Top gasrecycling hoogovenproces
Top gasrecycling hoogovenproces
Op het gebied van de productie van ruwijzer (HM) door hoogovens (BF), is de meest veelbelovende technologie om de uitstoot van CO2 (kooldioxide) aanzienlijk te verminderen de recycling van CO (koolstofmonooxide) en H2 (waterstof) uit de gas dat de BF-top verlaat. Het CO- en H2-gehalte van het bovenste BF-gas heeft de potentie om als reducerende gaselementen te werken, en daarom wordt hun recirculatie naar het BF beschouwd als een effectief alternatief om de BF-prestaties te verbeteren, het gebruik van C (koolstof) en H2 te verbeteren, en de uitstoot van CO2 te verminderen. Deze 'top gas recycling' (TGR) technologie is voornamelijk gebaseerd op het verlagen van het gebruik van fossiel C (cokes en kolen) met het hergebruik van de reductiemiddelen (CO en H2), na verwijdering van de CO2 uit de top BF gas. Dit leidt tot een lagere energiebehoefte. Vanwege de voordelen van een hoge productiviteit, een hoge PCI-snelheid (poederkoolinjectie), een laag brandstofverbruik en een lage CO2-uitstoot, enz.. , wordt het TGR-BF-proces beschouwd als een van de veelbelovende ijzerproductieprocessen in de toekomst.
In TGR-BF wordt zuurstof (O2) in de BF geblazen in plaats van hete lucht om stikstof (N2) in het bovenste BF-gas te verwijderen. Een deel van het bovenste BF-gas dat CO en H2 bevat, wordt opnieuw gebruikt als reductiemiddel in het BF. CO2 uit het BF-topgas wordt opgevangen en vervolgens opgeslagen. Er zijn verschillende recyclingprocessen voorgesteld, geëvalueerd of praktisch toegepast voor verschillende doeleinden. Deze processen onderscheiden zich door (i) met of zonder CO2-verwijdering, (ii) met of zonder voorverwarmen, en (iii) de plaats van injectie.
Het concept van de TGR-BF (Fig 1) omvat veel technologieën, waaronder (i) injectie van reducerende top-BF-gascomponenten CO en H2 in de schacht- en haardblaaspijpen, (ii) het verlagen van het verbruik van fossiele C-input door lagere cokes snelheid, (iii) gebruik van zuiver O2-gas in plaats van hete lucht bij de haardblaaspijp (verwijdering van N2 uit het proces), en (iv) terugwinning van zuiver CO2 uit het bovenste BF-gas voor ondergrondse opslag.
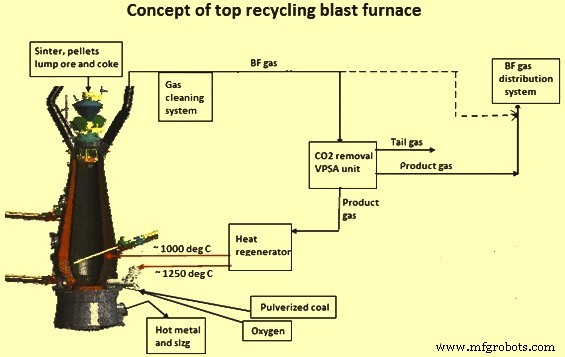
Fig 1 Concept van TG-BF
Het concept van topgasrecycling is experimenteel getest in de experimentele BF (EBF) van de LKAB in Lulea, Zweden. De EBF werd aangepast en er werd een gasscheidingsinstallatie gebouwd op basis van VPSA-technologie (vacuum pressure swing adsorptie) in de buurt van de EBF.
Geschiedenis van BF-topgasrecycling
Om de snelheid van het reductiemiddel te verlagen en de productiviteit van de BF te verhogen, zijn in de twintigste eeuw verschillende nieuwe concepten geïntroduceerd, gebaseerd op het conventionele BF-proces.
Al in de jaren 1920 werd een concept ontwikkeld voor de injectie van het hete reducerende gas in de BF. Het lagere gasvolume uit de blaasmonden in de oven moest worden gecompenseerd door de injectie van voorverwarmd reducerend gas bij 1000°C met 27% CO, 33% H2 en 26% N2 in de onderste schachtzone. Hierdoor bleek slechts 30% van de cokes (toen 345 kg/tHM) nodig te zijn voor het BF-proces. In het midden van de jaren 60 werd dit idee opnieuw opgepakt in België en in het begin van de jaren 70 werden de eerste proeven uitgevoerd bij een BF met een diameter van 4,6 m in Cockerill-Seraing in België. Een specifieke hoeveelheid van 400 N cum/tHM gereformeerd gas dat voorverwarmd was tot 1000°C werd in de onderste schacht van de BF geïnjecteerd. Er werd een vervangingsverhouding van 0,22 kg tot 0,26 kg cokes per N cum reducerend gas waargenomen.
Verdere onderzoeken werden vanwege de hoge kosten van aardgas om economische redenen niet uitgevoerd. Aan het eind van de jaren zeventig werd in Duitsland begonnen met de ontwikkeling van een nieuw proces waarbij koude zuivere O2, brandstof en gerecycled gas op twee tuyere-niveaus werden geïnjecteerd. Op basis van dit idee werd in 1984 in Canada een proces ontwikkeld voor een conventionele BF zonder tweede rij blaasmonden. Het belangrijkste kenmerk van dit concept was de injectie van steenkool ter vervanging van de cokes. Beide concepten werden nooit gerealiseerd en eindigden alleen als een studie.
Bijna tegelijkertijd werd dit idee verder gebruikt door NKK in Japan, waar een tweede rij blaaspijpen in het midden van de schacht werd geïnstalleerd. In deze tuyeres werd voorverwarmd reducerend gas, bestaande uit hergebruikt topgas zonder CO2-verwijdering, geïnjecteerd. Het gas werd verwarmd door gedeeltelijke verbranding met zuurstof. Koude O2, kolen en koud gerecycleerd topgas werden in de blaaspijpen van de haard geïnjecteerd. NKK testte het proces in een experimentele BF met 3 blaaspijpen, een binnenvolume van 3,9 kubieke meter en een haarddiameter van 0,95 m. De koleninjectiesnelheid zou kunnen worden verhoogd tot 320 kg/tHM, terwijl de cokessnelheid zou kunnen worden verlaagd tot 350 kg/tHM. Het tekort aan stookgas in de geïntegreerde staalfabriek vanwege de recycling van het top-BF-gas stopte de ontwikkeling van dit proces, omdat de prijs van elektrische energie en aardgas hoog was in Japan.
De eerste commerciële exploitatie van een BF met topgasrecycling werd eind jaren tachtig uitgevoerd in 12 campagnes door RPA Toulachermet in Rusland bij BF nummer 2 met een nuttig volume van 1033 cum. In dit volledig cokes BF-procesconcept werd heet topgas en bijna CO2-vrij samen met pure O2 in de haardblaaspijpen geblazen. Het koolzuurvrije topgas werd in hete fornuizen verwarmd tot 1200 deg C. Met dit nieuwe proces werd bijna 250.000 ton ruwijzer (HM) geproduceerd. Het laagst bereikte cokesgehalte was 367 kg/tHM, vergeleken met de referentie van 606 kg/tHM, wat een verlaging van het cokesgehalte van 239 kg (39 %). Tijdens deze campagnes werden ernstige tuyere-burnouts gezien, wat leidde tot veranderingen in het ontwerp van de tuyere. Moeilijkheden met het CO2-reinigingssysteem stopten het proces uiteindelijk. Rekening houdend met deze achtergrondonderzoeken is in 2004 het concept van ULCOS (ultra-low carbon di-oxide steelmaking) TGR-BF ontwikkeld.
Ontwikkeling van ULCOS TGR-BF
Het ontwikkelwerk is in twee fasen uitgevoerd. In de eerste ontwikkelingsfase, die liep van 2004 tot 2009, kreeg het proces de naam ‘ULCOS nieuw hoogovenproces’. Tijdens deze fase zijn drie nieuwe procesconcepten ontwikkeld en getest. In de tweede fase die begon in 2009 en die werd genoemd als 'ULCOS topgasrecycling hoogovenproces', werden twee extra ULCOS TGR-BF-campagnes uitgevoerd.
Tijdens de ontwikkeling werden warmte- en massabalansmodellen en een 3-D axi-symmetrisch model van de BF gebruikt voor de berekening van de hoofdgegevens en de innerlijke toestand van het proces voor de selectie van de beste bedrijfsparameters. Er zijn vier alternatieven gedefinieerd en onderzocht op de mogelijk haalbare C-besparing en de haalbaarheid om het BF onder deze nieuwe concepten te laten draaien. De conclusie was dat de alternatieven 1, 3 en 4 bij een hoog poederkoolinjectieniveau een fossiele C-besparing van 21% of hoger moeten kunnen realiseren. Alternatief 2 werd afgewezen vanwege de lage verwachte C-besparing en de noodzaak van de uitdagende technologie om het recyclegas in twee stappen eerst in een recuperator te verwarmen en vervolgens verder te verwarmen door middel van partiële oxidatie. Alle alternatieven omvatten CO2-verwijdering en de injectie van CO-rijk productgas in de schoorsteenpijpen, het gebruik van zuivere O2 en de injectie van steenkool samen met het reducerende gas. In alle alternatieven werd in de toekomst het gebruik van biomassa, gedeeltelijk gereduceerd erts en waterstofrijk gas als een mogelijkheid overwogen.
In alternatief 1 (Fig 2) wordt het ontkoolde productgas koud geïnjecteerd met zuivere O2 en steenkool bij de haardblaaspijpen en heet bij de schachtblaaspijpen. Een kritiek punt in dit alternatief was de kleine stroomsnelheid van het koude gas op het niveau van de blaasmond, wat leidde tot kleinere toevoerkanalen en hogere vlamtemperaturen in vergelijking met het normale BF-proces. Ook was een nieuw blaasmondontwerp nodig vanwege de kleine gasstroomsnelheden.
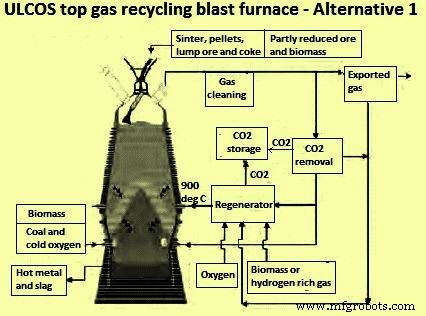
Fig 2 ULCOS top gasrecycling hoogoven – alternatief 1
In alternatief 3 (Fig 3) werd het ontkoolde productgas samen met O2 en steenkool heet geïnjecteerd in de normale schoorsteenblaaspijpen. Om een hoge koolstofbesparing te bereiken, was het noodzakelijk om te werken met een lage RAFT (raceway adiabatic flame temperature) en tegelijkertijd met een hoge koleninjectiesnelheid.
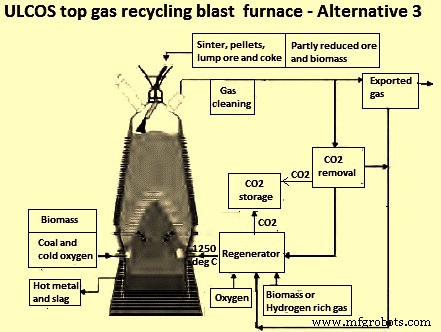
Fig 3 ULCOS top gasrecycling hoogoven – alternatief 3
In alternatief 4 (Fig 4) werd het ontkoolde productgas heet geïnjecteerd bij de haardblaaspijpen en heet bij de onderste schacht. De temperatuur van het gerecyclede gas varieerde van kamertemperatuur tot 1250 ° C.
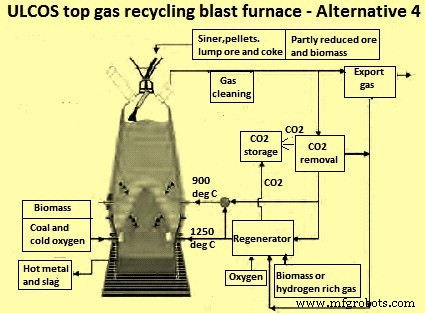
Fig 4 ULCOS top gasrecycling hoogoven – alternatief 4
In alternatieven 1 en 4 wordt ook productgas via schachtmondstukken geïnjecteerd. De verschillen zijn de gasinjectietemperatuur en de positie van de injectiepunten. In alle gevallen werd het minste deel van het gas verwarmd in een regeneratief systeem. De verwachte fossiele C besparing voor alternatief 1 was 21% bij een kolengehalte van 170 kg/tHM, alternatief 3 was 24% bij een kolengehalte van 180 kg/tHM en alternatief 4 was 25% bij een kolengehalte van 150 kg/tHM .
Wiskundige modellering van de omstandigheden van de toevoerkanalen en vergassingstests werden vervolgens uitgevoerd en zowel laboratorium- als proefschaalonderzoeken werden gedaan voor het ontwerp en de engineering van de blaaspijpen onder de beperkingen van gelijktijdige injectie van gerecycleerd gas, zuivere O2 en poederkool. De geometrie van de blaaspijp is verbeterd op basis van de resultaten van de berekeningen om hotspots en storingen tijdens bedrijf te voorkomen en om een voldoende impuls van de gasstroom te behouden om een loopbaan met voldoende diepte te vormen.
Campagnes van het TGR-BF-proces in de experimentele BF
Het doel van de proeven was om de werking van de EBF aan te tonen in een volledige TGR-modus met pure O2 en PCI bij de haardblaaspijpen. Dit is gedaan onder de drie gedefinieerde alternatieven. De ijzerlast bestond uit 30 % korrels en 70 % sinter. De productiesnelheid van HM werd op een constant niveau van 1,5 ton per uur gehouden en het PCI-tarief werd gevarieerd van 130 kg/tHM tot 170 kg/tHM. Tijdens de verschillende proefperiodes is het volume van het gerecyclede topgas gemaximaliseerd om een maximale fossiele C-besparing te realiseren. De resultaten verkregen tijdens de proeven in EBF werden vervolgens vergeleken met modelberekeningen.
Alternatief 3 en alternatief 4 zijn in 2007 getest, tijdens de eerste campagne na een conventionele opstart. Alternatief 3 is in het najaar van 2009 op optimalisatie getest in de tweede campagne, gevolgd door een test van alternatief 1. In de derde en laatste campagne in 2010 lag de focus op alternatief 4 bij 900 graden C. Alternatief 4 werd beschouwd als een voorkeursalternatief voor het vervolg ULCOS BF demonstratieproject op industriële schaal. De grens van 900 ° C voor de temperatuur van het opnieuw geïnjecteerde gas is ingesteld om problemen met de reductie van silica door H2 van de vuurvaste materialen te voorkomen.
Tijdens elke campagne werden in-situ metingen van temperatuur en gassamenstelling evenals monsters van het lastmateriaal genomen van de EBF met de twee in-burden sondes. Om het gedrag van het lastmateriaal onder de nieuwe bedrijfsomstandigheden te onderzoeken, werden vlak voor de stopzetting van de campagne manden met verschillende sinter- en pelletmaterialen in de EBF geladen. Deze manden werden teruggewonnen uit de EBF tijdens de dissectie van de oven na het blussen met stikstof. Dit was gedaan tijdens de campagnes in 2007 en 2010. In de tweede campagne in 2009 kon alleen de quench worden uitgevoerd vanwege een onvoorbereid einde van de campagne vanwege een probleem in het EBF-laadsysteem en werden er dus geen manden geladen.
Tijdens de campagnes werden monsters uit de cohesieve zone teruggevonden en de grootte en vorm van de racebaan gemeten voor verder onderzoek. De campagnes werden gestart met een week conventionele BF-normaal bedrijf (heteluchtstraal) met sinter, eerst voor verwarming en thermische stabilisatie en vervolgens voor het vaststellen van een referentie voor conventioneel BF-bedrijf. Na de referentie is een stop gemaakt voor het afkoppelen van de blower en het aansluiten van het productgas op de pebble heaters (regeneratoren). De opstart in de TGR-BF-modus werd gedaan door een kunstmatige explosie bestaande uit koude O2 uit de lansen en hete N2 uit de kiezelverwarmers. In progressieve stappen werd de N2 uit de kiezelstralers vervangen door koolzuurvrij topgas (productgas).
Resultaten van de campagnes van ULCOS TGR-BF
De eerste conclusie die uit de campagnes naar voren kwam is dat het mogelijk is om het ULCOS TGR-BF proces te bedienen. Tijdens de campagnes met het nieuwe proces waren er geen veiligheidsgerelateerde problemen. De werking van de VPSA-eenheid, de tweede belangrijke faciliteit, verliep soepel en zonder grote storingen. De EBF in combinatie met de VPSA-eenheid werkte heel goed tijdens de campagnes.
Er moet echter worden opgemerkt dat de werking van de VPSA-eenheid werd beïnvloed door de veranderingen in de samenstelling van het topgas en het volume van het gas uit de EBF. Daarom moesten beide eenheden in een zeer nauwe relatie worden geëxploiteerd. De maximale verhouding gerecycleerd topgas die tijdens de campagnes werd bereikt, lag rond de 90%.
Tijdens de campagnes van het TGR-BF-proces werd een stabiele werking van de BF ervaren met een soepele afdaling van de last en was het gemakkelijk om de thermische stabiliteit te behouden. Het rendement van het gas in de BF-schacht was stabiel tijdens de verschillende alternatieven en er was een goede gasverdeling zoals blijkt uit de metingen van de in-burden-schachtsondes. Tijdens de campagnes waren er echter enkele apparatuurstoringen waardoor de EBF tijdens de operatie onder de nieuwe procesomstandigheden moest worden stopgezet. Enkele lange onderbrekingen waren nodig om terug te keren naar de operatiestap van de 'conventionele operatie' met kunstmatige hete straal van koude O2 en warme N2. De kleine onderbrekingen vereisten alleen het stoppen van de gasinjectie en het toevoegen van wat extra cokes en/of kolen.
Na opstarten met N2, wanneer er geen top-BF-gas beschikbaar is, kan het productgas binnen ongeveer 1 uur weer worden gerecycled. Alle problemen werden zoals voorspeld opgelost en de thermische stabiliteit van de BF kwam nooit ernstig in gevaar. Gedurende de campagne hebben de opgedane ervaring en het toegenomen vertrouwen het mogelijk gemaakt om het EBF-herstel geleidelijk sneller te maken (op productieniveau). Telkens tijdens het wisselen van alternatieven (3 naar 4, 3 naar 1) werd de BF ongeveer 8 uur stilgelegd voor het maken van de nodige gasaansluitingen op de schachtblaaspijpen en het wisselen van haardblaaspijpen.
Uit de experimenten op laboratoriumniveau bleek dat het conventionele belastingsmateriaal geen probleem zou zijn voor het nieuwe proces. Dit werd bevestigd tijdens de campagnes. Er waren geen specifieke procesproblemen gerelateerd aan de eigenschappen van de belastingsmaterialen. De resultaten van zowel sondes als uitgravingsmonsters hadden het reductieprofiel van een in het centrum werkende oven aangetoond, wat een laag reductieniveau aan de muur en een hoger reductieniveau in het ovencentrum is voor zowel sinter- als pelletsmonsters. Trommeltesten op de uitgravingsmonsters hadden een desintegratiegedrag vertoond dat vergelijkbaar was met dat van een conventioneel BF-proces dat overeenkwam met de laboratoriumtests. Uit het belastingtestwerk kon worden geconcludeerd dat de belastingseigenschappen zoals gebruikt in de huidige conventionele BF geen probleem lijken te vormen voor het ULCOS TGR-BF-proces.
De resultaten die werden behaald tijdens de ULCOS TGR-BF-campagnes waren zeer bemoedigend wat betreft de besparing van de C (kolen en cokes). De proeven van alle drie de campagnes hadden een aanzienlijke verlaging van de snelheid van het reductiemiddel aangetoond, die werd bereikt door de injectie van het ontkoolde bovenste BF-gas. Tijdens de drie campagnes daalde de kolen- en cokes-input van circa 530 kg/tHM naar 400 kg/tHM, wat een aanzienlijke besparing van de C betekent. De CO2-input werd teruggebracht van 470 kg/tHM tot circa 350 kg/tHM, wat resulteerde in een C-besparing van ongeveer 25%.
Hoewel alternatief 1 niet volledig kon worden onderzocht vanwege de vroege stopzetting van de tweede campagne, bedroeg de maximale vermindering van de C-input via cokes 21% in vergelijking met de referentieperiode bij conventionele BF-operatie. Voor dit alternatief is een nieuwe tuyere-technologie ontwikkeld. Het blaaspijpontwerp bestond uit coaxiale pijpen waarbij de binnenpijp werd gebruikt voor de injectie van de poederkool en de buitenpijp voor de injectie van O2. De drie geïnstalleerde blaaspijpen werkten erg goed en na demontage werd geen schade of slijtage waargenomen. De VPSA kon tot 88% van het BF-topgas recyclen.
Wat betreft alternatief 3 zou het C-verbruik in de eerste campagne tot 15 % kunnen worden verminderd met een topgasrecyclingratio van ongeveer 72 %. De resultaten van dit alternatief waren lager (ongeveer 15 %) dan verwacht op basis van de warmte- en massabalansberekeningen (24 %), aangezien dit de eerste ervaring was met de topgasrecyclingmodus en het proces niet was geoptimaliseerd. In de tweede campagne waren de resultaten van dit alternatief veel beter, toen de maximale reductie in C-invoer van ongeveer 25% werd bereikt met een topgasrecyclingratio tot 90%.
Bij alternatief 4 werd een C-besparing van 24% behaald bij een topgasrecyclingratio van 90%. In termen van cokes- en kolenverbruik was er een besparing tot 123 kg/tHM in het nieuwe proces (alternatief 4) in vergelijking met de referentieperiode. Uit deze resultaten kon een goede correlatie worden bepaald tussen de hoeveelheid geïnjecteerd gas (CO+H2) en de vermindering van het reductiemiddel. De C-aanvoer via cokes en kolen zou gemiddeld met 17 kg kunnen worden verminderd per 100 N cum ingespoten gas (CO+H2).
De campagnes van EBF hebben bewezen dat het mogelijk is om een BF-proces uit te voeren op een veel lager verbruiksniveau van fossiele C in vergelijking met het verbruik van het huidige BF. Een C-besparing tot 25% werd bewezen door de injectie van het reducerende gedecarboniseerde topgas. Dit is een significante daling in vergelijking met het huidige best bediende BF-proces. In feite wordt verwacht dat de toepassing van BF-TGR-technologie op moderne BF zal leiden tot een vermindering van het C-verbruik van het huidige niveau van ongeveer 405 kg C/tHM tot een niveau van ongeveer 295 kg C/tHM.
VPSA-eenheid heeft stabiel gefunctioneerd. Het was opgevallen dat de VPSA-eenheid 97% van het topgas uit de BF kon behandelen. De gemiddelde volumefractie van CO2 in geïnjecteerd gas was ongeveer 2,67 % en het terugwinningspercentage van CO was 88 %, waarmee werd voldaan aan de eisen van kwantiteit en kwaliteit. In combinatie met VPSA- en CCS-eenheden kan de CO2-emissie die door het TGR-BF-proces wordt verminderd, oplopen tot 1270 kg/tHM, wat goed is voor 76 % van de totale CO2-emissies in het ijzerproductieproces. 24% van de verminderde CO2 was afkomstig van gasrecycling en de overige 52% werd ondergronds getransporteerd en opgeslagen door CCS.
Procesmatig kan worden gesteld dat de ULCOS-bewerking stabieler is dan de conventionele BF-bewerking, wat betreft de temperatuur en kwaliteit van de HM. Dit lijkt voornamelijk te wijten te zijn aan de lagere invloed van de oplossing-verliesreactie die verband houdt met de veel lagere niveaus van directe reductiesnelheid (DRR). De laagst waargenomen waarde van deze DRR is 5 %. Er was geen indicatie in de bedrijfsresultaten dat dit daadwerkelijk de minimumwaarde was die in ULCOS TGR-BF kon worden bereikt. De kwaliteit van HM werd grotendeels beïnvloed door de werking van ULCOS TGR-BF. Vooral werd een substantiële afname van het siliciumgehalte (groter dan 1% absoluut) en een correlatieve toename van het C-gehalte waargenomen. Er moet echter worden opgemerkt dat het siliciumgehalte in conventionele BF-werking veel lager is (ongeveer 0,5% in conventionele BF tegen ongeveer 2,0% in de EBF), en daarom mag niet zo'n grote verandering worden verwacht tijdens de toepassing van de ULCOS BF-TGR-proces op industriële schaal.
De testcampagnes van ULCOS TGR-BF hebben aangetoond dat het nieuwe TGR-BF-proces haalbaar en eenvoudig te bedienen is. Het kan worden bediend met een goede veiligheid, een hoog rendement en een sterke stabiliteit. De testcampagnes hebben bewezen dat het mogelijk is om de EBF-werking te verschuiven tussen 4 bedrijfsmodi (conventioneel, alternatieven 1, 3 en 4). Het bewees ook dat het mogelijk is om het BF-proces en de gasscheidingsinstallatie VPSA in een gesloten kringloop te laten werken. De verkregen C-besparingen kwamen overeen met de voorspellingen uit de stroomschemaberekeningen. De tests gaven ook aan dat conventionele belastingsmaterialen sinter, pellet en cokes geschikt zijn voor het ULCOS TGR-BF-proces.
Op basis van de ervaring van EBF-campagnes zijn de items die aandacht vereisen voor een veilige en duurzame industriële toepassing van het ULCOS TGR-BF-proces:(i) het risico op gaslekkage op mondstukniveau kan vereisen dat het mondstukniveau fysiek gescheiden is van het giethuis voor brandbeveiliging, (ii) risico op lekkage door buigen van flenzen bij hoge temperaturen, (iii) verlenging van de schoorsteen van hete kachels/kachel om giftig gas in de omgeving te voorkomen, (iv) voor het voorkomen van storingen in de opstartfase , operationeel personeel moet worden getraind met kunstgas tijdens de werkingstest, (v) optimale injectieparameters zijn belangrijk om ophoping/verstopping bij de mondstukneus te voorkomen, (vi) belang van individuele straalstroomregeling naar de blaasmonden om ophoping te voorkomen van overmatige O2 en poederkool in de blaaspijp in geval van verstopping, (vii) de keuze van vuurvaste materialen en fabricage van vuurvaste voorwerpen moeten worden gewijzigd en het gebruik van C-stalen ankers moet indien mogelijk worden vermeden, alternerend eze materialen worden gebruikt dan C-staal, of staal gecoat met aluminiumoxide, en (viii) het is belangrijk om metaalstof te vermijden door een zorgvuldige selectie van metalen onderdelen.
De testresultaten hebben aangetoond dat alternatief 4 het beste effect van emissiereductie had en werd geselecteerd als eerste keuze voor de proef op industriële schaal BF in de volgende fase.
Productieproces
- Hoogovenprocesautomatisering, meet- en controlesysteem
- Opwekking en gebruik van hoogovengas
- Gebruik van colanoot in een hoogoven
- Verpulverde koleninjectie in een hoogoven
- Hoogoven onregelmatigheden tijdens bedrijf
- Hoogoven koelsysteem
- Hoogoventoplaadsystemen
- Chemie van de ijzerproductie door hoogovenproces
- Vuurvaste bekleding van hoogoven
- Cokesovengasinjectie in een hoogoven
- Gaslasproces begrijpen