ULCORED-proces
ULCORED-proces
ULCORED is een proces voor directe reductie (DR) dat DRI (direct gereduceerd ijzer) produceert in een schachtoven, hetzij uit aardgas (NG) of uit reducerend gas verkregen door vergassing van steenkool. Afgas uit de schacht wordt teruggevoerd in het proces nadat koolstofdioxide (CO2) is afgevangen, die de DR-fabriek in een geconcentreerde stroom verlaat en naar de opslag gaat. De DRI-stap produceert een vast product dat vervolgens wordt gesmolten met behulp van een elektrische boogoven (EAF). Het proces is voornamelijk in 2006 ontworpen door een team onder leiding van LKAB, Voest-alpine en MEFOS.
Het doel van het ULCORED-proces was het verminderen van het NG-verbruik dat nodig is om DRI te produceren. Dit werd bereikt door de traditionele hervormingstechnologie te vervangen door partiële oxidatie (POx) van NG. In combinatie met het CCS-apparaat kan ULCORED de CO2-uitstoot met 70% verminderen in vergelijking met het gemiddelde in de BF-route.
Het concept van het ULCORED-proces omvat het scheiden van CO2 uit het procesgas. Het wordt gekenmerkt door een inspanning om een op gas gebaseerd DR-proces over te nemen op een minimale uitstoot van broeikasgassen (BKG), met behulp van CO2-afvang- en opslagtechnologie (CCS) en tegelijkertijd op een minimaal gebruik van energie. Het proces is zo ontworpen dat de extractie en opslag van CO2 mogelijk is. Het proces is daarom ook afhankelijk van CCS met een vergelijkbare in-process capture.
Het proces is gebaseerd op het gebruik van een shifter om het koolmonoxide (CO) gas uit de as om te zetten in waterstof (H2) samen met een CO2-verwijderingseenheid. Dit opent een nieuwe innovatieve evolutie van het procesconcept.
De belangrijkste kenmerken van het ULCORED DR-proces omvatten (i) het gebruik van zuurstof (O2) in plaats van lucht, resulterend in een afgas van bijna 100 % CO2 dat alleen hoeft te worden gecomprimeerd, (ii) er zijn mogelijkheden om de behoefte aan NG met 15% tot 20%, en (iii) steenkool, biomassa, bioafvalvergassing en H2 kunnen worden gebruikt als alternatief voor NG.
Het concept van ULCORED is om te voldoen aan de vraag naar verminderde CO2-uitstoot met behulp van op ijzererts en gas gebaseerde directe reductie voor DRI-productie. Het concept omvat het gebruik van 100 % zuurstof (O2), POx in plaats van reformers, shifter voor de productie van CO2-vrij reductie/overtollig gas en het reductiemiddel is ofwel aardgas of syngas uit kolen/biomassavergassing. In plaats van aardgas kan ook reductiegas worden gebruikt dat wordt geproduceerd door de vergassing van steenkool.
ULCORED DR-proces op basis van NG
De belangrijkste kenmerken van het ULCORED DR-proces op basis van NG zijn (i) geen reformer, (ii) geen verwarming en (iii) hoge druk. Door de hoge druk is er minder gassnelheid in de DR-schacht, minder fluïdisatie en minder fijne deeltjes die de DR-schacht verlaten. Door de hoge druk zijn er ook kleinere CO2-verwijderings- en POx-eenheden nodig en is er minder stroom nodig voor de recyclecompressor.
De originaliteit van het concept is het gebruik van O2 in plaats van lucht, waardoor er geen of weinig stikstof (N2) in het gas zit. De reforming vindt plaats door een POx-eenheid voor het conditioneren van het reductiegas (Fig 1). De technologie vervangt de conventionele reforming van aardgas door gedeeltelijke oxidatie van het gas om het verbruik van aardgas te verminderen dat nodig is om DRI te produceren. De POx-reactie die plaatsvindt is CH4 + 0,5O2 =CO + 2H2 met delta H =– 8,6 Kcal/mol.
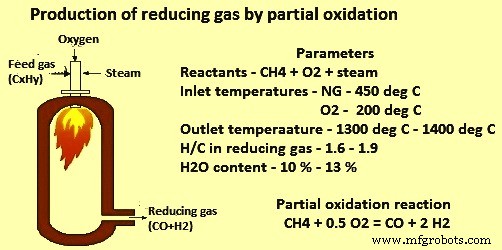
Fig 1 Vermindering van de gasproductie door gedeeltelijke oxidatie
De pilot unit voor de partiële deoxidatie is bij Linde getest in twee campagnes met een nieuw ontworpen brander voor H2-rijk voedingsgas. Er werd een buisreactor met voorverwarmd gas (60% H2 en 40% CH4) gebruikt. De conclusies van de pilot unit tests waren:(i) De brander en reactor konden probleemloos werken, (ii) een stabiele vlam zonder noemenswaardige geluidsproductie kon worden verkregen, (iii) de productie van roet zal naar verwachting lager zijn dan 300 mg /N cum tot 460 mg/N cum nat gasvolume, en (iv) door de atmosferische druk was het CO2- en CH4-gehalte hoger dan de voorcalculaties op basis van verondersteld evenwicht. Een hogere werkdruk tot 7 kg/sq cm kan dit gehalte verminderen.
De DR-as heeft een tegenstroom van reducerend gas dat bij de blaaspijpen wordt geïnjecteerd en ijzererts wordt van bovenaf koud toegevoerd. De oven wordt bedreven bij een druk van 6 kg/cm2 en een temperatuur van ongeveer 900°C. Het asafvoergas bevat waarschijnlijk voornamelijk CO, CO2, H2 en H2O.
Het afgas van de as, dat voornamelijk CO, CO2 en H2O bevat, wordt door een shifter (een- of tweetraps) geleid die CO omzet in H2. Het gebruik van een watergasshifter resulteert in een hoog H2-gehalte in de reductieschacht. De watergasverschuivingsreactie is CO (g) + H2O (g) <–> CO2 +H2. Vrijwel alle CO in het afgas van de schacht wordt naar H2 verplaatst en de CO2 wordt verwijderd in de CO2-verwijderingseenheid. Een verhoogde productie van overtollig gas verhoogt de stroomvraag voor de CO2-verwijderingsinstallatie en de O2-productie. Het berekenen van het juiste niveau van overtollig gas is een iteratief proces. Geschatte niveaus van overtollig gas zullen om deze reden hoger zijn. Het geschatte overschot van 2,2 giga calorieën per ton DRI zal naar verwachting de extra stroomvraag compenseren. Dit kan worden bereikt door een omleiding van wat gas rechtstreeks naar de shifter. De hoeveelheid omgeleid gas wordt bepaald op basis van de eigenschappen van het reductiegas in de reductieschacht. Vanwege de toegenomen gasvolumes in het systeem hebben de shifter en CO2-verwijderingsunits extra investeringen nodig.
In de shifter-eenheid is de CO-verschuivingsreactie exotherm, en evenwicht bevordert de CO-omzetting bij een hoge stoom-tot-gasverhouding en lage temperaturen, terwijl het niet wordt beïnvloed door druk. In een adiabatisch systeem wordt de haalbare CO-slip bepaald door de uitgangstemperatuur. Omzetting in een enkel bed van katalysator is evenwichtsbeperkt en naarmate de reactie vordert, beperkt de hoge temperatuur uiteindelijk verdere reactie. Deze beperking kan worden overwonnen met een tweetraps systeem bestaande uit een verschuiving van hoge temperatuur gevolgd door verschuiving van lage temperatuur, met koeling tussen de bedden. Een lage bedrijfstemperatuur geeft het gunstigste thermodynamisch evenwicht en dus de minimale slip van CO. De meeste moderne H2-fabrieken hebben koelsystemen stroomopwaarts van de lagetemperatuur-shiftreactor om te kunnen werken dicht bij het dauwpunt van het procesgas. Er moet een veiligheidsmarge boven het dauwpunt worden gebruikt om te zorgen voor volledige verdamping van waterdruppels die zich in de koeler kunnen vormen.
Afhankelijk van de stoomverhouding kan de lagetemperatuur-shiftreactor in staat zijn te werken bij een temperatuur zo laag als 190°C zonder zorg voor condensatie. In het concept passeert het topgas een hoge en lage temperatuur shifter met daartussen warmteterugwinning. De shifter voor hoge temperatuur zet 97,2% van de CO om en de shifter voor lage temperatuur voltooit de conversie naar 99,5%. De warmtewisselaar verwarmt het gerecyclede gas en de capaciteit wordt berekend op basis van een ingesteld temperatuurverschil aan de warme kant van 50 graden C. Een overmaat aan warmte in de warmtewisselaar produceert stoom naar het stoomnetwerk via een condensor/reboiler.
De CO2-verwijderingseenheid wordt gebruikt om de CO2 uit gas te verwijderen, waarbij een H2-rijk reductiegas wordt geproduceerd dat wordt teruggevoerd naar het proces. De CO2-verwijderingseenheid wordt bepaald door een verdeling voor het CO2-verwijderingsrendement, H2- en N2-terugwinning. De twee CO2-verwijderingsprocessen die kunnen worden gebruikt, zijn het vacuümdruk-swing-adsorptieproces (VPSA) of het aminewasproces. De keuze van de CO2-verwijderingseenheid (VPSA of amine) hangt af van de lokale vereisten. Als er een stoomoverschot is, kan de energievragende CO2-stripping worden uitgevoerd met stoomenergie in de fabriek in plaats van elektriciteit die nodig is voor de VPSA. Beide technologieën hebben voor- en nadelen die verder moeten worden geanalyseerd. Beide technologieën werken met het ULCORED concept. Er is ook een mogelijkheid om een pressure swing adsorptie (PSA) te gebruiken voor CO2-verwijdering in plaats van een VPSA-eenheid vanwege de reeds hoge druk die in het proces beschikbaar is.
Het type proces dat wordt geselecteerd, is van invloed op het processtroomschema en de lay-out. Het VPSA-proces vereist, inclusief cryogene techniek en compressie tot een druk van 110 kg/cm², 260 kWh vermogen per ton afgevangen CO2. In het geval van een amine-scrubberproces, met hoogwaardige amines (geactiveerde methyldiethanolamine, aMDEA), vereist het volledige proces (aminen en compressie tot een druk van 110 kg/cm²) ongeveer 1,6 ton lagedrukstoom en 160 kWh vermogen per ton CO2 gevangen.
Het deel van het gereinigde H2-rijke gas dat N2 bevat, wordt uit het proces afgevoerd om N2-ophoping in het reductiegas tegen te gaan. Het aftapgas is een waardevol gas dat kan worden gebruikt voor de productie van stoom of verwarming binnen het systeem.
Het stroomschema van het ULCORED-proces op basis van aardgas wordt gegeven in figuur 1.
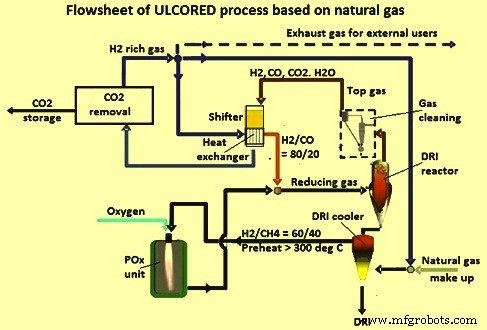
Fig 2 Stroomschema van ULCORED-proces op basis van aardgas
ULCORED DR-proces op basis van kolenvergassing
De meest CO2-besparende optie met ULCORED is het gebruik van een kolenvergasser die syngas produceert voor de DR-installatie en CO2-arm H2-gas voor alle gebruikers van de installatie. Dit concept kan zowel voor bestaande systemen als voor achteraf aangebrachte systemen worden aangepast.
Het op kolen gebaseerde concept is gebaseerd op de productie van reducerend gas met behulp van bestaande kolenvergassingstechnologie en koude ontzwaveling (op basis van bestaande technologie) of heetgasontzwaveling. Het concept maakt gebruik van O2 in plaats van lucht en omvat CO2-opslag. Het hoge H2-gehalte in de reductieschacht wordt bereikt door een watergasshifter. Overtollig H2-gas wordt geleverd aan de andere gebruikers van de installatie.
Kolenvergassing is een bekende techniek en zal naar verwachting een van de toekomstige procestechnieken voor energieconversie worden na uitputting van de olie- en gasreserves. Er zijn verschillende technologieën ontwikkeld voor het vergassen van steenkool. Er zijn verschillen tussen de technologieën, maar ze werken over het algemeen met een relatief hoge C-conversie-efficiëntie, meestal meer dan 80%. Een groot voordeel bij kolenvergassing is de mogelijkheid om het syngas (zoals zwavel, kwik etc.) efficiënt te reinigen voor gebruik.
Aangezien de schachtoven voor de productie van DRI werkt op een druk van 6 kg/sq cm, wordt de gasdruk van de vergasser verlaagd door een expansieturbine die ook vermogen terugwint (van 30 kg/sq cm naar 6 kg/sq cm).
Het ULCORED DR-proces kan eenvoudig worden geïntegreerd met een kolenvergassingsinstallatie, waarbij de voordelen van de originaliteit van het procesconcept worden meegenomen. Steenkool wordt geleverd aan de kolenvergassingsinstallatie. Zwavel wordt uit het syngas verwijderd door zowel warme als koude ontzwaveling. Het schone syngas wordt gemengd met gereinigd H2-rijk recyclegas, voorverwarmd in de DRI-koeler of uit de warmtewisselaar tussen de hogetemperatuur- en lagetemperatuurverschuiver.
Er zijn drie verschillende manieren om de vergasser te integreren met het ULCORED DR-proces. De vergasser kan worden geïntegreerd als een koud syngas of op een manier waarbij de thermische energie in het hete gas van de vergasser wordt gebruikt. In figuur 3 zijn drie verschillende opstellingen weergegeven. De mogelijkheid om overtollig H2 voor het systeem te produceren wordt mogelijk gemaakt door het gereinigde syngas rechtstreeks naar de shifter-units om te leiden.
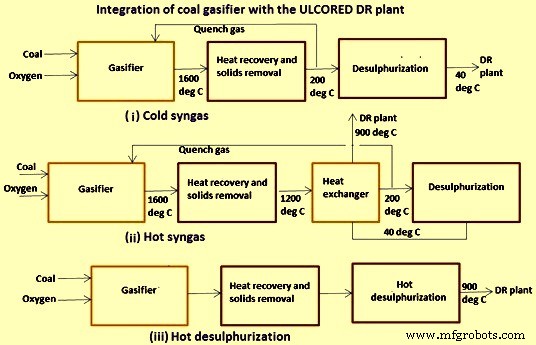
Fig 3 Integratie van kolenvergasser met de ULCORED DR-fabriek
Zuurstof wordt voornamelijk verbruikt in de kolenvergasser, maar ook vóór de schacht, in een kleine POX, wat zorgt voor een juiste temperatuur van het reductiegas. Verschoofd gas is gas dat moet worden omgeleid naar de shifter om de juiste samenstelling van het reductiegas te verzekeren, d.w.z. het verhogen van de H2-hoeveelheid. CO2 verwijderd is de hoeveelheid CO2 die wordt afgescheiden van de hoofdprocesstroom in het CO2-verwijderingsproces. Het stroomschema van het op steenkool gebaseerde ULCORED-proces wordt getoond in figuur 4.
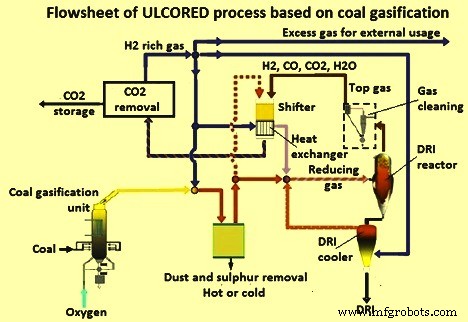
Fig 4 Stroomschema van het ULCORED-proces op basis van kolenvergassing
Het gebruik van een kolenvergasser en een shifter in het systeem maakt het mogelijk om een deel van het syngas rechtstreeks naar de shifter te leiden, waardoor meer gas wordt gegenereerd dan nodig is voor de directe reductie-installatie. Deze functie maakt het mogelijk om een CO2-arme brandstof voor de staalfabriek te genereren. Het maakt het mogelijk om één CO2-bron uit het systeem te hebben, waardoor het in principe mogelijk is om alle CO2 die in het staalproductiesysteem wordt gegenereerd af te vangen en op te slaan.
Huidige status van ULCORED DR-proces
Er zijn diepgaande fundamentele modelstudies voor het ULCORED DR-proces voltooid. Deze modelstudies omvatten pelletschaalmodellen, schachtmodellen en procesmodellen door stroomschemasimulaties. De modelstudies hebben geholpen bij het fundamentele begrip van het DR-proces, inclusief de dynamiek ervan. De stroomschemamodellering heeft geholpen bij het optimaliseren van de proceslay-out om te passen bij het ULCORED DR-proces in een staalfabriekomgeving. Verschillende benaderingen die tijdens de modelleringsstudies werden gevolgd, hebben vergelijkbare resultaten opgeleverd. Deze studies hebben een geloofwaardige basis gecreëerd voor de evaluatie van het concept in verschillende scenario's. Materiaalbalancering, massabalancering, energiebalancering en CO2-emissieberekeningen zijn uitgevoerd voor I ton koude DRI-output met 92 % metallisatie en 2,76 % C.
Een van de interessante opties is een ULCORED DR-fabriek voor de productie van LRI (minder gereduceerd ijzer) en een conventionele of N2-vrije hoogoven (BF) om het ruwijzer (HM) te produceren met een extra besparing van CO2-uitstoot. LRI is een alternatieve keuze in plaats van DRI gezien de succesvolle tests die zijn uitgevoerd in de LKAB-experimentele BF. De LRI-test met een DR-product verminderd tot slechts 65% metallisatiegraad reageerde zeer positief in de BF met opmerkelijk stabiele ovenconditie en een laag cokesverbruik dat lager was dan 200 kg/tHM.
De uitkomst van deze onderzoeken is dat het ULCORED DR-proces een 'quick fix' kan zijn voor een brownfield-verbetering van de CO2-emissies, vooral daar waar aardgas relatief goedkoop is. In het geval van een geïntegreerde staalfabriek met BF-route, kan LRI een keuze zijn gezien de succesvolle tests die zijn uitgevoerd in de LKAB-experimentele BF.
Het ULCORED DR-proces moet eerst in een pilot worden getest, een stap die gebruik kan maken van de mogelijkheid van de EDRP-oven (experimentele directe reductie-piloot), die LKAB van plan is de komende jaren op te richten als aanvulling op haar experimentele BF in Lulea, Zweden. De specificaties van de EDRP zijn (i) 1 ton ijzer per uur productie, (ii) recirculatie van topgas, (iii) werkdrukbereik van 0 kg/sq cm tot 8 kg/sq cm in de schachtoven, (iv ) gasstroom in het bereik van 1700 N cum tot 3100 N cum per uur, en (v) temperatuur van de schachtoven in het bereik van 900 ° C tot 1050 ° C.
ULCORED zal waarschijnlijk een kandidaat zijn om bestaande installaties voor directe reductie aan te passen, zodra de levensvatbaarheid ervan is aangetoond op proef- en vervolgens op demonstratieschaal, wat ook 10 tot 15 jaar of langer zou duren.
Productieproces