Shell Molding:proces, toepassing, voor- en nadelen
Er zijn verschillende gietprocessen die worden gebruikt in de verwerkende industrie. Al deze processen hebben hun eigen voor- en nadelen, waardoor ze geschikt zijn voor specifiek gieten. Shell moulding, ook wel shell mould casting genoemd, is een van de meest geschikte casting proces voor complexe en andere dunne secties. Dit proces geeft een hoge nauwkeurigheid en een betere oppervlakteafwerking. Een van de grote voordelen van dit gietproces, waardoor het geschikt is voor verschillende gietindustrieën, is dat het eenvoudig kan worden geautomatiseerd. Al deze voordelen maken dit proces veelzijdig en gemakkelijk toepasbaar voor elke bedrijfstak.
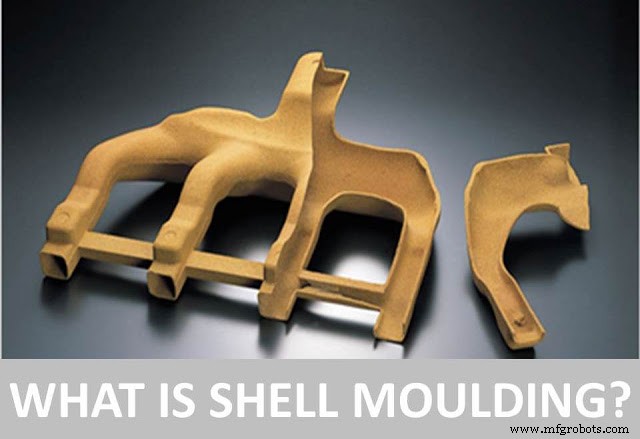
Shell-vormgietproces maakt gebruik van een mal zoals een schaal, die is gemaakt door het mengsel van zand en hars. Deze mal is licht van gewicht en heeft een hoge sterkte waardoor hij geschikt is voor automatisch gieten. Dit proces is geschikt voor zowel ferro- als non-ferrogietwerk, maar wordt vooral gebruikt voor staal.
In dit artikel zullen we het hebben over het vormproces van de schaal, de voor- en nadelen en de toepassing ervan.
Laten we beginnen met de discussie.
Shell Molding-proces:
Proces:
Shell molding omvat verschillende stappen. Deze worden hieronder gegeven
#Step 1:Maken van een metalen patroon
De eerste en belangrijkste stap in elk gietproces is patroon maken. Patroon is een replica van het eindproduct. Het kan gemaakt zijn van hout, plastic, metaal enz. Shell molding gebruikt een metalen patroon samen met alle patroontoeslag . Dit patroon is gemaakt door aluminium of gietijzer. Een van de grote voordelen van het gebruik van een metalen patroon is dat het zeer nauwkeurig gieten geeft en kan worden gebruikt voor meervoudig gieten.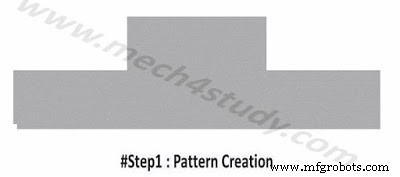
#Step 2:Verwarming van patroon
Het metalen patroon dat door een ander gietproces is gecreëerd, wordt nu verwarmd op een temperatuurbereik tussen 180 - 250 graden Celsius. Deze verwarming is essentieel, waardoor het met hars gemengde silica stolt wanneer het erop wordt gegoten. Na verwarming wordt een klein laagje smeermiddel (Mosltly Silicon) over het metalen patroon gespoten, waardoor het metalen patroon gemakkelijk van de schaal kan worden verwijderd.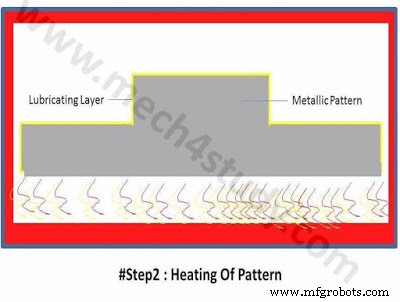
#Step 3:Shell Mould Creation
Deze stap is een grote stap in dit gietproces. Deze stap kan verder worden onderverdeeld in de volgende stappen.- Patroon wordt over een stortbak geklemd. Nu wordt dit geheel met de voorkant naar beneden gedraaid. Een mengsel van zand en hars wordt in de stortbak gedaan. Meestal wordt fijn groen zand gebruikt voor het mengsel. li>
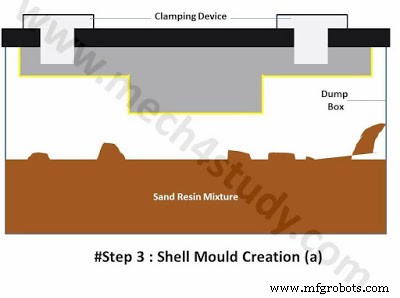
- Nu is dit hele samenstel omgekeerd, waardoor het harsmengsel over het verwarmde patroon kan vallen. Een laag van het mengsel, die in direct contact staat met het patroon, wordt hard en vormt een schaal. De dikte van shell is meestal afhankelijk van de temperatuur van het patroon en de tijdsduur van het contact.
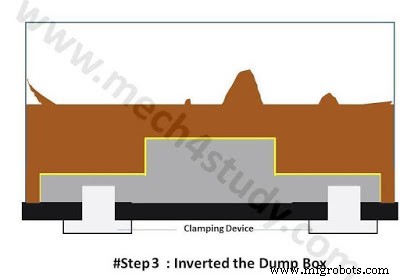
- Nu is de dumpbox weer omgekeerd, waardoor extra zandharsmengsel kan worden verwijderd.
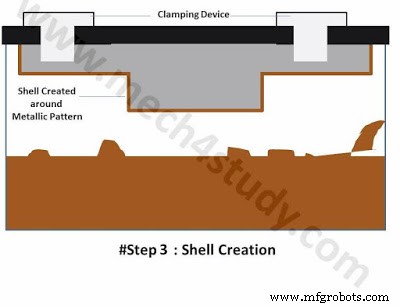
- Daarna wordt het metalen patroon uit de dumpbox verwijderd en wordt de schaal ervan gescheiden. De andere helft van de mal wordt ook gemaakt met dezelfde techniek.
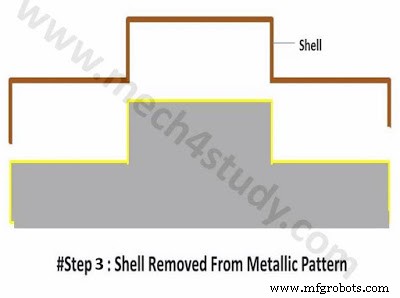
#Step 4:Matrijsmontage
Deze stap assembleert alle schelpen die zijn gemaakt door het gieten van de schelp. De al vereiste schaal werd in een kolf geassembleerd en ondersteund door een bakmateriaal. Alle wenselijke onderdelen zoals kernen, runner, riser etc. zijn eraan bevestigd.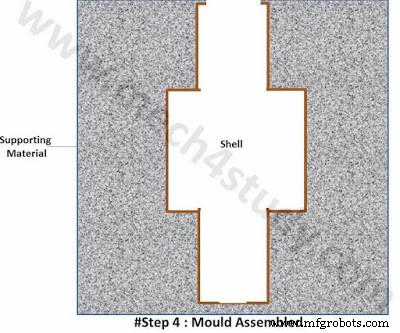
#Step 5:Casting-formatie
Nu is de holte gevuld met een gesmolten metaal en laten stollen. Na het stollen wordt het gegoten metaal verwijderd door de schaal te breken. Het door dit proces gevormde gietstuk is zeer nauwkeurig en goed afgewerkt. Over het algemeen is er geen verdere bewerking nodig.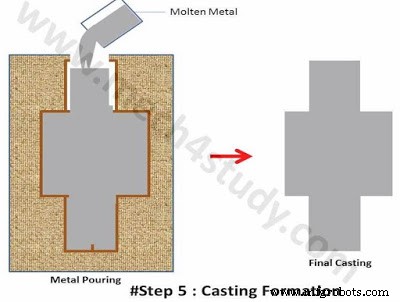
Voor- en nadelen:
Voordelen:
- Dunne en complexe secties kunnen gemakkelijk worden gecast.
- Hoge maatnauwkeurigheid en goede oppervlakteafwerking.
- Eenvoudig geautomatiseerd.
- Het kan worden bediend door een semi-ervaren operator.
- Geen verdere bewerking nodig.
Nadelen:
- Speciaal metaalpatroon vereist, wat het duur maakt voor grote gietstukken.
- Het is niet geschikt voor productie in kleine batches.
- Schildpadden zijn minder doorlatend in vergelijking met groenzandschimmel.
- Grootte en gewichtsbeperking.
Toepassing:
De meeste industriële producten zoals versnellingsbak behuizing, drijfstang, kleine boten, vrachtwagenkappen, cilindrische kop, nokkenas, kleplichaam enz. Worden gemaakt door schaalgieten.Dit heeft alles te maken met het gietproces van schaalvormen, de voor- en nadelen en de toepassing ervan. Als je vragen hebt over dit artikel, stel ze dan door te reageren. Als je dit artikel leuk vindt, vergeet dan niet om het op sociale netwerken te delen. Schrijf u in op onze website voor meer informatieve artikelen. Bedankt voor het lezen.
Productieproces
- Niet-traditioneel bewerkingsproces:vereisten, typen, voor- en nadelen
- Elektronenstraalbewerking:principe, werking, uitrusting, toepassing, voor- en nadelen
- Schuurstraalbewerking:principe, werking, uitrusting, toepassing, voor- en nadelen
- Ultrasoon verspanen:principe, werking, uitrusting, toepassing, voor- en nadelen
- Ultrasoon lassen:principe, werking, uitrusting, toepassing, voor- en nadelen
- Elektrochemische bewerking:principe, bewerking, uitrusting, toepassing, voor- en nadelen
- Elektroslaklassen:principe, werking, toepassing, voor- en nadelen
- Thermietlassen:principe, werking, uitrusting, toepassing, voor- en nadelen
- Solid State-lasproces:principe, typen, toepassing, voor- en nadelen
- Wrijvingsroerlassen (FSW):Principe, werking, toepassing, voor- en nadelen
- Spuitgietmachine:constructie, werking, toepassing, voor- en nadelen