Belangrijke kenmerken van het walsen van walsdraad
Belangrijke kenmerken van het walsen van walsdraad
Walsdraad wordt normaal gesproken gewalst in een hogesnelheidswalserij, waar de staaltemperatuur hoger is dan 1000 ° C, de maximale walssnelheid 120 meter per seconde (m/s) overschrijdt en de geproduceerde rollen walsdraad tot 10 kilometer (km) lang kunnen zijn . Tijdens het walsen van walsdraad worden gewoonlijk 25 tot 30 passages genomen in een continue walserij.
Walsdraad is een materiaal dat een zeer brede toepassing kent. Van componenten voor de auto-industrie, bandenkoord, elektroden, verbindingselementen zoals bouten en moeren, veren, draad en draadproducten, stalen versterkingen, enzovoort, alles is gebaseerd op walsdraad. Dat is de reden waarom walsdraad normaal gesproken is ontworpen met veelzijdigheid in het achterhoofd. Omdat de molen een energie-intensieve molen is, wordt het noodzakelijk dat de optimale oplossingen worden opgenomen in het molenontwerp zonder afbreuk te doen aan de flexibiliteit. Alle maten, materialen en legeringen moeten efficiënt en met een hoge productiviteit in de walsdraadfabriek worden geproduceerd.
Walsdraad moet voldoen aan de eisen van de gebruikers van walsdraad op het gebied van oppervlakte- en interne kwaliteit, evenals fysieke, chemische, mechanische en metallurgische eigenschappen. Walsdraad ondergaan nabewerkingen zoals trekken, smeden of machinale bewerking in de gewenste vormen en warmtebehandeling om het product de gewenste sterkte te laten bereiken. Het walsdraad moet dus in staat zijn om goede prestaties van de geproduceerde onderdelen te garanderen, waar ze ook worden gebruikt, en tegelijkertijd goed verwerkbaar te zijn in verschillende stadia van de nabewerking.
De gebruiker van walsdraad heeft drie basisvereisten, namelijk (i) het elimineren of vereenvoudigen van een of meer van de secundaire of tertiaire verwerkingen om de productiviteit te verbeteren en de verwerkingskosten te verlagen, (ii) om de functionaliteit te verbeteren, d.w.z. om de levensduur te verlengen, om het gewicht te verminderen, of andere voordelen te brengen aan het eindproduct waarvoor het walsdraad wordt gebruikt, en (iii) het gebruik van milieubelastende stoffen tijdens nabewerkingsprocessen te elimineren.
Om te voldoen aan de steeds strengere eisen van de consument, moet de walsdraadwals over de algemene capaciteiten van walsdraad beschikken vanuit de verschillende gezichtspunten, namelijk (i) het verbeteren van de maatnauwkeurigheid, (ii) het implementeren van maatvrij walsen (d.w.z. walsen). producten van verschillende afmetingen zonder rollen te verwisselen), (iii) verbetering van de productiviteit door het verwisselen van rollen te versnellen (verkorting van de tijd voor het wisselen van rollen) en (iv) verbetering van de kwaliteit van het productoppervlak door het voorkomen van oppervlaktedefecten tijdens transport in het rolproces.
Walsdraadfabriek wordt verondersteld niet alleen de materialen te leveren, maar moet ook walsdraad leveren om te voldoen aan de vereisten voor de lange daaropvolgende verwerking die ze ondergaan in de secundaire en tertiaire processen totdat de eindproducten zijn geproduceerd. Aangezien de eindproducten in veel gevallen als vitale onderdelen in verschillende industriële gebieden worden gebruikt, zijn er bovendien eisen aan procesrationalisatie in geïntegreerde samenwerkingen met klanten. Daarom moet de molen niet alleen in staat zijn om te voldoen aan de kwaliteitseisen van de gebruikers, maar ook om te voldoen aan hun productiviteit, opbrengst, flexibiliteit en productiekostenvereisten tijdens de daaropvolgende verwerking. Een hoog maalrendement samen met een adequate productkwaliteit is van het grootste belang voor de beheersing van de productiekosten.
De productiecapaciteit van een walsdraadfabriek is afhankelijk van ofwel de volumeproductie van enkele standaardproducten ofwel van een gediversifieerde productmix bestaande uit walsdraad met een groot aantal staalsoorten en gespecialiseerde productkwaliteiten.
Een walsdraadwalserij heeft in principe (i) verwarmingsfaciliteiten nodig om het uitgangsmateriaal (knuppel) tot walstemperaturen te verwarmen, (ii) walsfaciliteiten bestaande uit walsinstallaties met rollen, blokken, geleiders en beschermers, (iii) leggen, warmtebehandeling en oprolapparatuur, en (iv) transport- en behandelingsapparatuur. Alle apparatuur moet nauw samenwerken met een controle op roltemperaturen, tijdverlies, snelheidsverlies, kasseien, niet-conform product en kwaliteitsafwijkingen die leiden tot omleiding of zelfs afwijzing.
Vereisten van een moderne walsdraadwals
Er zijn verschillende belangrijke parameters (Fig 1) voor het walsen van walsdraad in een walsdraadmolen. Een moderne walsdraadwals is over het algemeen ontworpen om te werken met de filosofie van de 'overall equipment Effectiveness' (OEE). De OEE-waarde van de molen is de waarde die wordt verkregen door het gebruik van de molen, de efficiëntie van de molen en de opbrengst van de molen te vermenigvuldigen. De bezettingsgraad van de molen is de beschikbare bedrijfstijd gedeeld door de geplande productietijd en uitgedrukt in een percentage. Het rendement van de molen is de looptijd gedeeld door de beschikbare bedrijfstijd van de molen en uitgedrukt in een percentage. De molenopbrengsttijd is de tijd om het belangrijkste product te produceren gerelateerd aan de looptijd. De productopbrengst wordt uitgedrukt als het gewicht van de geaccepteerde rol gedeeld door het gewicht van de knuppels en uitgedrukt in percentage.
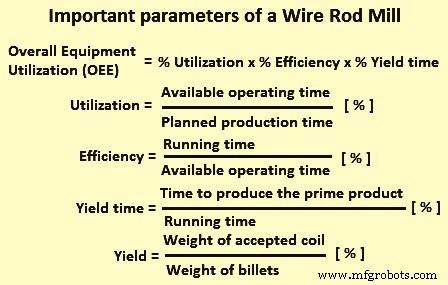
Fig 1 Belangrijke parameters van een walsdraadfrees
Walsdraadmolens hebben normaal gesproken een lagere OEE dan andere soorten molens vanwege de hogere uitvaltijd voor het wisselen van rollen en het wisselen van standaards en groef- en geleidingsaanpassingen tijdens het verschuiven van de producten. De OEE van de molen kan worden verbeterd als deze uitvaltijd kan worden verminderd.
De theoretische productiecapaciteit van een molen is de capaciteit die kan worden verkregen zonder enig verlies, d.w.z. met 100 % benutting, 100 % efficiëntie en 100 % opbrengst. De werkelijke capaciteit is echter afhankelijk van het OEE-niveau van de fabriek. Als het OEE-niveau van de fabriek 60% is, dan is de productiecapaciteit van de fabriek 60% van de theoretische capaciteit. Het OEE-niveau in een ultramoderne walsdraadwals met een goed gedefinieerde geoptimaliseerde wals is normaal gesproken op het niveau van 80 %.
De kosten van slechte kwaliteit in de walsdraadfabriek worden over het algemeen bepaald als de som van inspectiekosten en afkeuringen/omleidingen van walsdraad als gevolg van interne en externe defecten. Voor een goed presterende molen kan dit ongeveer 10% zijn. Het kan tot 30% stijgen in een walsdraadfabriek met een gediversifieerde productmix bestaande uit walsdraad met een groot aantal kwaliteiten en gespecialiseerde productkwaliteiten.
In een moderne walsdraadfabriek staat productiviteit en kwaliteit centraal. Hoge bezetting, efficiëntie en opbrengst geven een hoge productiviteit. Maar een hoge productiviteit op zich is niet de enige factor voor het succes van een walsdraadwalserij. Het moet producten produceren die waarde toevoegen aan de klanten en ze krijgen walsdraad van hoge kwaliteit die de betalingen die ze voor het walsdraad doen waard zijn.
De productiviteit en het gebruik van de molen is afhankelijk van de uitvaltijd in de molen, veroorzaakt door verschillende redenen, waaronder de molenlay-out en de productmix. In de molen wordt de opbrengst van knuppels tot het eindproduct in alle stappen geregistreerd en het volgen van het materiaal in de molen volgt de verliezen op die in de molen plaatsvinden. De belangrijkste categorieën van de verliezen die in de fabriek plaatsvinden, zijn (i) tijdverliezen in de tijd, (ii) snelheidsverliezen, (iii) verliezen door kasseien, (iv) verliezen als gevolg van kwaliteitsafwijkingen, (v) verliezen door molens stilstandtijd, (vi) verliezen als gevolg van omleiding/afwijzing van walsdraad tijdens inspectie in de afwerkingszijde van de fabriek, en tijdverlies als gevolg van waardeverhogende operaties in het geval van productie van gespecialiseerde walsdraadproducten.
Flexibiliteit van de molen
In een walsdraadwals wordt staal (staaf) verwarmd tot boven de herkristallisatietemperatuur en door verschillende groeven van de walsen in de walserij geleid. Gangbare ontwerpen voor rollen die in walsdraadmolens worden gebruikt, zijn diamantvierkant, diamant-diamant, doospassages, vierkant-ovaal, vals rond-ovaal en rond-ovaal. In de walsdraadwalsen wordt normaal gesproken vrijgewalst op maat, wat betekent dat walsdraad van elke afmeting kan worden gewalst zonder de beperkingen van de pasafmetingen van de walsen die in de wals worden gehouden. Dit wordt ook wel de flexibiliteit van de serie genoemd. Bovendien maakt de vereenvoudiging van het doorgangsschema van een bovenstroomse walserij het mogelijk de frequentie van het wisselen van de wals aanzienlijk te verlagen. Hoe groter het bereik van de productafmetingen die met dezelfde rollen kunnen worden gerold (vrij bereik), des te groter is het effect van een verminderde frequentie van het wisselen van de rol. De maat freerolling is niet beperkt tot de eindwalserij. Het kan ook worden toegepast op de voorbewerkingsmolen.
Om de productiviteit te verbeteren, ligt de focus op het minimaliseren van de stilstand van de walsdraadwals. De effectiviteit van een dergelijke focus wordt gewoonlijk verbeterd door de tijd en noodzaak voor het verwisselen van rollen te verminderen wanneer nieuwe definitieve afmetingen en nieuwe staalsoorten en vormen moeten worden vervaardigd. Dit wordt bereikt door het werkbereik, ook wel flexibiliteit van de serie genoemd, te verbeteren. Verbeterde flexibiliteit wordt bereikt wanneer een groot aantal verschillende staalsoorten met verschillende vormen en afmetingen worden gewalst met een minimale wijziging van het walsschema. Elke staalsoort wordt gekenmerkt door zijn specifieke manier van materiaalstroom, zoals verschillende spreiding, bij het passeren van de rolspleet. Ook de opstarttijd en de wachttijd voor de juiste walstemperatuur, afhankelijk van de daadwerkelijke staalsoort, moeten worden verkort. Verschillende verwarmingscycli veroorzaken echter nog steeds te hoge uitvaltijden, wanneer een breed scala aan kwaliteiten moet worden gewalst. Om te voldoen aan de huidige markteisen, waaronder kleinere partijen en talrijke staalsoorten, is het een noodzaak geworden dat de moderne walsdraadwalserijen een hoge mate van flexibiliteit vertonen.
Een bijzonder aspect van een walsdraadmolen is het gebruik van een flexibel roldoorlaatontwerp, of flexibele groeven met een hoog werkbereik. Door gebruik te maken van flexibele roldoorgangen, kan het walsen in dezelfde groeven worden uitgevoerd voor een breed scala aan eindproducten, simpelweg door de rolafstand te veranderen. Zo kan het wisselen van groeven worden vervangen door een eenvoudige verschuiving van de rolspleet en dit vermindert de uitvaltijd voor het wisselen van het ene product naar het andere. Er is een sterke onderlinge afhankelijkheid tussen de flexibiliteit van het ontwerp van de roldoorgang, het gebruik van de molen en de opbrengst.
Door gebruik te maken van een flexibel roldoorgangsontwerp kan een belangrijk deel van de verliezen in de molen worden verminderd. Een flexibel roldoorlaatontwerp minimaliseert het risico van overvulling van de groeven en het ontstaan van kasseien tijdens het wisselen van staalsoort. Een flexibel roldoorlaatontwerp heeft ook voordelen voor productontwikkeling wanneer er behoefte is aan introductie van nieuwe maten of staalsoorten. Ook kan een belangrijke verbetering van de waardeverhogende looptijd worden bereikt met een flexibel roldoorlaatontwerp.
Productiviteit van de fabriek
De walsdraadmolen kan gecombineerd worden met een staafmolen door voor het afwerkblok een koelbeduitlaat te hebben. Dit wordt normaal gesproken gedaan om de capaciteit van de bovenstroomse walserij te benutten. Wanneer de rollen in het walsdraadblok worden verwisseld, produceert de bovenstroomse wals staven om de totale stilstand van de wals te verminderen.
Moderne walsdraadwalserijen zijn over het algemeen enkelstrengs walserijen. In het geval van een meerstrengige wals wordt een tweede tussenwals op elk van de strengen geïntroduceerd om de invloed van verandering in het aantal gelijktijdig inwalsen van strengen te verminderen. De tweede tussenwals kan de vorm hebben van een voorbewerkingsblok. Het kan ook de vorm hebben van een walsblok met drie rollen. Het belangrijkste kenmerk van de driewalswals is zijn vermogen om de variaties in afmeting tussen de drie gegroefde walsen, die de gehele omtrek van een walsrol rollen, te onderdrukken en daardoor de spreiding te verminderen in vergelijking met een conventionele twee-hoge walserij. Deze tussenmolen staat bekend als appreteermolen waarbij het vormgeven door middel van lage reductie wordt gedaan. Dit helpt bij het hebben van een familierolfilosofie stroomopwaarts in de molen, waardoor de resettijd wordt verkort.
Om de freessnelheid en daarmee de freesproductiviteit te verhogen, wordt na een conventioneel afwerkingsblok een reduceer-/maatfrees (RSM) geïnstalleerd. De integratie van een RSM na het conventionele afwerkingsblok verbetert de freesproductiviteit op kleine formaten aanzienlijk (tot 60%). Zijn extreme precisie is bewezen in vele installaties. Verder resulteert dit in combinatie met walsen bij zeer lage temperatuur in een meer verfijnde microstructuur die aanvullende secundaire processen kan elimineren. De RSM biedt zowel productiviteits- als kwaliteitsverbeteringen van het eindproduct, terwijl tegelijkertijd de bedrijfskosten worden verlaagd en de kwaliteit van het walsdraadproduct wordt verhoogd. Het biedt plaats aan een ontwerp met een enkele rolgang vanaf stand 1 in de voorbewerkingsgroep tot en met de laatste stand van het afwerkingsblok. Omdat het hetzelfde ontwerp voor een enkele doorgang mogelijk maakt, kan een hoge maalefficiëntie worden gehandhaafd zonder rekening te houden met de uiteindelijke productgrootte.
Spanningen tussen staanders worden normaal gesproken zoveel mogelijk vermeden bij het walsen van walsdraad, omdat anders de kop- en staarteinden buiten de tolerantie vallen omdat de vrije uiteinden niet onder spanning kunnen worden gerold. Dit feit kan resulteren in overvolle groeven en einddefecten zoals vinnen. In het hogesnelheidsblok zonder draaiing met vaste overbrenging, worden spanningen tussen de staanders gebruikt om stabiele rolomstandigheden te bereiken. Wanneer er spanningen tussen de staanders worden uitgeoefend op de opgerolde baar, worden de groeven ingesteld om de vereiste tolerantie te geven.
Kwaliteit draadstang
Walsdraad wordt in verschillende toepassingen gebruikt. In veel van de toepassingen zijn de kwaliteitseisen van het walsdraad zeer streng. Inferieure kwaliteit van het walsdraad verhoogt de defecten/omleidingen van de eindproducten en heeft ook een nadelige invloed op de opbrengsten bij de klanten, wat ontevredenheid bij de klanten veroorzaakt.
Aangezien walsdraadwalsen een energetisch walsen is, is het altijd noodzakelijk dat het walsen van defecte walsdraadrollen tot een minimum wordt beperkt. Soms, wanneer het defect in de knuppel vrij groot is, kan het zelfs kasseien in de molen veroorzaken. Aangezien de lengte van het walsdraad vanaf een knuppel erg lang is, vergt kwaliteitsborging over de gehele lengte van het walsdraad na het walsen tijd en inspanning. Om deze reden is de kwaliteitscontrole van knuppels (het uitgangsmateriaal voor het walsen) van groot belang. De defecte knuppels moeten worden geïdentificeerd, gescheiden en verwijderd door middel van knuppelinspectie. De knuppels moeten zowel op oppervlaktegebreken als op inwendige gebreken worden gecontroleerd. Kleine oppervlaktedefecten kunnen worden verwijderd door de knuppel te slijpen (conditioneren).
De belangrijkste eigenschappen die aan walsdraad (vooral in dun walsdraad) worden gevraagd, zijn de hoge productiviteit bij secundaire bewerking en de hoge sterkte na het definitieve trekken. De hoge productiviteit betekent het minimaliseren van draadbreuk tijdens het trekken en bundelen of ideaal geen breuk, hogere directe trekbaarheid en goede trekbaarheid onder zware trekomstandigheden zoals hoge treksnelheid. Deze steeds geavanceerdere eisen van klanten door strenge normen toe te passen op kwaliteitscontrole-items zoals niet-metalen insluitsels, segregatie, ontkoling, mechanische eigenschappen en microstructuur.
Normaal gesproken zijn er drie hoofdvereisten voor het walsdraad voor veel toepassingen. Dit zijn (i) hogere sterkte, (ii) eliminatie of vereenvoudiging van de nabewerking, en (iii) minder gebruik van milieubelastende stoffen. Een hogere staalsterkte is vereist vanwege kostenreductie bij de gebruikers en vele andere redenen. Aangezien walsdraad aan de kant van de gebruiker verschillende soorten secundaire bewerkingen ondergaan, zoals smeden, trekken en machinale bewerking, evenals warmtebehandeling voor gloeien, afschrikken, temperen,
enz., vandaar dat eisen vanuit het oogpunt van kostenreductie, energiebesparing en milieubehoud dringend aandringen op eliminatie of vereenvoudiging van warmtebehandeling en machinale bewerking (zoals bijna net of spaanloze vormgeving).
Beheersing van niet-metalen insluitsels, precipitaten, transformatie en metallografische structuur is een belangrijke metallurgische maatregel voor de verbetering van de eigenschappen van walsdraad. Het beheersen van niet-metalen insluitsels is een van de belangrijkste kiemtechnieken voor sterkteverhoging van verenstaal, verlenging van de levensduur van lagerstaal en verwijdering van lood uit vrijsnijdend staal, enz. Controle van de structuur en vorm van oxiden en sulfiden is effectief in het realiseren van de gewenste eigenschappen van deze staalsoorten.
In een walsdraadfabriek zijn er geen compromissen als het gaat om het nauwkeurig voldoen aan de gespecificeerde eigenschappen van het spoelmateriaal. Hier speelt het gecontroleerde koeltransportsysteem (CCC) een sleutelrol. De constante hoge kwaliteit in de hele walsdraadrol moet worden gecontroleerd.
In dit opzicht speelt het CCC-systeem een belangrijke rol voor de verwerkingskwaliteit van walsdraadproducten, het bereiken van de gewenste uniformiteit en metallurgische en mechanische eigenschappen. Het controleert nauwkeurig de variaties in de treksterkte rond de ring op snel gekoelde producten tot een standaarddeviatie binnen 1% van de gemiddelde treksterkte.
Het CCC-systeem is door een juiste keuze van het koelregime geschikt voor de productie van alle conventionele staalsoorten en ook voor speciale productkwaliteiten met alternatieve koelmodi. Het optimaliseert ook de verwerking van koolstof- en gelegeerde staalsoorten bij gebruik in combinatie met de RSM voor walsen bij lage temperatuur en gecontroleerde koeling, wat een zeer goede combinatie van eigenschappen en dimensionale controle oplevert.
Het CCC-systeem vergemakkelijkt de verwerking in een breed scala van omstandigheden, waaronder zowel snelkoelende als langzaamkoelende modi binnen één enkel systeem. Dit vermogen stelt de walsdraadwalserij in staat om een breed spectrum van gewoon koolstofstaal en gelegeerd staal te produceren, evenals roestvrij staal en andere speciale kwaliteiten. Het CCC-systeem resulteert in verbeterde as-rolled rod-eigenschappen van de walsdraad, die de productie van meer kwaliteiten in een direct bruikbare toestand mogelijk maakt, en stroomafwaartse processen, zoals sferoïdiserend gloeien, verminderen of elimineren.
Thermo mechanisch walsen (TMR) in de walsdraadmolen verfijnt de uiteindelijke korrelgrootte als gevolg van dynamische herkristallisatie. Gecombineerd met de uiteindelijke in-line waterkoeling en de superieure gecontroleerde koeling op het CCC-systeem, speelt TMR een belangrijke rol bij het bepalen van de uiteindelijke producteigenschappen. Dit is met name gunstig voor laaggelegeerde en middelgelegeerde staalproducten die vervolgens tijdens de downstream-verwerking worden gesferoïdiseerd en gegloeid. Het vermogen om de korrelgrootte sterk te beheersen, beïnvloedt ook de daaropvolgende transformatie naar harde producten zoals bainiet en martensiet door de starttijd en temperatuur van de transformatie te verschuiven. TMR kan dus directe stroomafwaartse koude bewerking minimaliseren en gloeitijden verkorten.
De combinatie van verwerking op een CCC-systeem en lage walstemperaturen biedt de mogelijkheid om de hardbaarheid in sommige kritieke soorten walsdraad te verminderen. Dit bevordert uiteindelijk de ferrietvorming en vertraagt de evolutie naar bainiet en martensiet. De verfijnde korrelgrootte die door TMR wordt bereikt, verbetert de diffusie tijdens warmtebehandeling en kan resulteren in kortere warmtebehandelingstijden en temperaturen. Voor die staven die niet met warmte zijn behandeld, verhogen de verfijnde en complexe structuren de trekopname tijdens koude vervorming, wat verschillende voordelen oplevert, zoals (i) verminderde treksterkte tijdens het rollen, (ii) verbeterde stroomafwaartse respons en (iii) meer werk hardbaarheid. De verbeteringen komen voort uit korrelverfijning en microstructurele controle. De goede beheersing van het koelproces bij het CCC-systeem in combinatie met de verminderde hardbaarheid van de walsdraad maakt het proces zeer stabiel en verkleint de kans op vorming van ongewenste harde fasen.
Productieproces
- Deegrol
- Tiara
- Prikkeldraad
- Rollende alarmrobot
- MOSMusic
- Arduino 3D-draadbuigmachine
- Belangrijkste kenmerken van een moderne bar- en lichtsectiemolen
- Belangrijkste kenmerken van een moderne walsdraadmolen:
- Belangrijkste kenmerken van een moderne Hot Strip Mill
- Walsproces voor staal
- Koudwalsen van staal