A Maintenance Manager's Guide to Reliability Centered Maintenance (RCM)
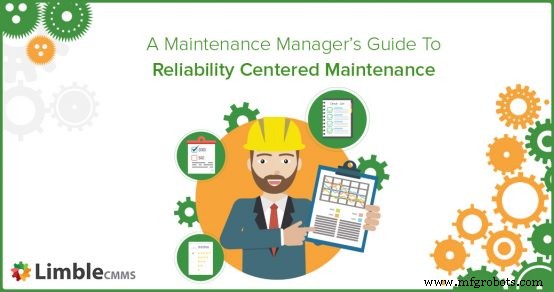
Twijfelt u of uw apparatuur wel of niet zo goed werkt? Vraagt u zich af of u manieren kunt vinden om de productiviteit te verbeteren en de onderhoudskosten te verlagen door uw onderhoud te optimaliseren? Dan wilt u misschien onderzoek doen naar Reliability Centered Maintenance (RCM) .
Wat is op betrouwbaarheid gericht onderhoud?
Er wordt veel jargon gebruikt als het gaat om Reliability Centered Maintenance – maar simpel gezegd – RCM is een gestructureerd proces dat problemen identificeert die, wanneer ze worden opgelost, de productiviteit van uw apparatuur en bedrijfsmiddelen verhogen en tegelijkertijd de onderhoudskosten verlagen. Betrouwbaarheidsgericht onderhoud is niet per se een onderhoudsmethode, het zijn evaluatiecriteria om te bepalen welke onderhoudsmethoden het beste werken voor elk stuk machine.
Als het correct wordt gedaan, kan RCM de resultaten van uw bedrijf enorm beïnvloeden.
Ebsco rapporteerde een investeringsrendement van 63% na het starten van een op betrouwbaarheid gericht onderhoudsprogramma.
Hoe de RCM-analyse uit te voeren
Als u een Reliability Centered Maintenance-analyse wilt uitvoeren, is er een standaardreeks vragen om u te helpen. Deze vragen worden gesteld door SAE (Society of Automotive Engineers), de regelgevende organisatie op het gebied van RCM en andere technische normen. De onderstaande vragen worden vermeld als onderdeel van de JA1011-standaard van SAE.
We hebben die vragen genomen en vereenvoudigd in deze gids met een echt vorkheftruckvoorbeeld
Vraag 1: Wat zijn de functies en bijbehorende gewenste prestatienormen van het actief in zijn huidige operationele context (functies)?
Wat een mondvol. Maak je geen zorgen, we zullen het voor je opsplitsen.
A) Voordat we die vraag beantwoorden, moeten we selecteren welke apparatuur u gaat analyseren met RCM.
Wanneer u beslist met welk apparaat u moet beginnen, moet u overwegen welk apparaat het meest waardevol is en de meeste pijn voor uw organisatie veroorzaakt wanneer deze uitvalt.
Hierdoor kunt u de grootste beloning voor uw inspanningen oogsten.
B) We moeten het gedeelte "functies en bijbehorende gewenste prestatienormen" uitzoeken.
Simpel gezegd, wat doet het geselecteerde apparaat en wat is de gewenste prestatie? Raadpleeg uw productieteam voor productiviteitsgegevens om inzicht te krijgen in de hoogste productiviteitsniveaus van het apparaat.
C) We moeten het gedeelte "in de huidige operatiecontext (functies)" uitzoeken.
Om de huidige gebruikscontext van het apparaat te begrijpen, moet u uw CMMS raadplegen voor gegevens over onderhoudswerkzaamheden. Als u geen CMMS heeft, kunt u deze gegevens wellicht terugvinden in uw papieren administratie. Als u deze nummers op geen van beide locaties kunt vinden, kan ander onderhoudsbeheer u wellicht helpen.
Uw antwoord kan er ongeveer zo uitzien:
Vorkheftruck #3 kan 18 pallets per uur verplaatsen op piekniveaus. Momenteel is de Mean Time Between Repair (MTBR) 800 uur met een gemiddelde uitvaltijd van 6 uur. Als we onze heftruck 40 uur per week laten draaien, ervaren we elke 20 weken (800/40) een kritieke storing en verliezen we de mogelijkheid om 108 pallets (18 pallets * 6 uur) te verplaatsen. Op basis van gegevens van uw CMMS of andere onderhoudsmanagers zou een heftruck een MTBR van 1200 uur moeten hebben. Als we onze MTBR met %50 kunnen verhogen tot de gemiddelde MTBR, krijgen we de mogelijkheid om elke 20 weken 54 extra pallets te verplaatsen.
Dit geeft je een goed beeld van waar je zou kunnen verbeteren.
Als u niet alle gegevens kunt vinden, is dat goed. Bouw het zo goed mogelijk uit.
Vraag 2: Op welke manieren kan het zijn functies niet vervullen (functionele storingen)?
Nu we weten waar we zijn en het gewenste resultaat dat we hopen te bereiken, moeten we de bron van de storingen (storingen) identificeren.
Kijk met dat in gedachten door uw administratie of denk na over de recente storingen en wat de oorzaak kan zijn.
Als u een vorkheftruck als voorbeeld gebruikt, kan uw antwoord er ongeveer zo uitzien:
- Menselijke fout
- Vork storing
- Motorstoring
Vraag 3: Wat veroorzaakt elke functionele storing (storingsmodi)?
U kunt voortbouwen op de vorige lijst met mislukkingen om uit te breiden en vraag 3 te beantwoorden:
- Menselijke fout – veroorzaakt door slechte training
- Defecte vork - veroorzaakt door slecht onderhoud en/of slecht gedrag van de bestuurder
- Motorstoring – veroorzaakt door slecht motoronderhoud (olie verversen enz.)
Vraag 4: Wat gebeurt er wanneer elke storing optreedt (storingseffecten)?
Deze vraag is vrij eenvoudig:uw antwoord moet de negatieve effecten weerspiegelen van de storingen die u hebt beschreven. Het kan er ongeveer zo uitzien – Failure Mode and Effects Analysis (fmea)
- Menselijke fout – ongevallen (breuk, morsen, menselijk letsel), productiviteitsdaling, enz.
- Defecte vork - schade aan apparatuur, levenscyclus, ongevallen (breuk, morsen, menselijk letsel), hogere arbeids- en reparatiekosten, productiviteitsdaling, enz.
- Motorstoring – schade aan apparatuur, hogere arbeids- en reparatiekosten, productiviteitsdaling, enz.
Vraag 5: Op welke manier is elke mislukking van belang (gevolgen van mislukkingen)?
Dit lijkt erg op de vorige vraag, hoewel je het opsplitst in de negatieve effecten omdat een storing meerdere negatieve effecten kan hebben.
- Hogere arbeids- en reparatiekosten – $ 25 per uur en gemiddeld $ 500 aan onderdelen
- Apparatuurschade - $ 800 per incident als gevolg van verkorting van de levensduur van de vorkheftruck
- Productiviteitsdaling – $300 per uur door productieonderbreking
- Ongevallen (breuk, morsen, menselijk letsel) – Mogelijke veiligheidsschendingen, letsel van werknemers en beschadigde goederen. Potentieel duizenden dollars per incident.
Door dit op te splitsen in werkelijke cijfers, kunt u de kosten die gepaard gaan met storingen inschatten en voorspellen.
Stel dat er een motorstoring is opgetreden die een uitvaltijd van 6 uur heeft veroorzaakt. De totale rekening zou $ 150 zijn voor arbeid, $ 500 voor onderdelen, $ 800 vanwege een kortere levensduur en $ 1800 voor productiviteitsdaling. Dit komt neer op maar liefst $ 3250 voor een enkele storing aan een enkel apparaat .
Vraag 6: Wat moet er worden gedaan om elke mislukking te voorspellen of te voorkomen (proactieve taken en taakintervallen)?
Hier komen we tot de kern waarom RCM belangrijk is. Kunt u preventief of voorspellend onderhoud uitvoeren om die grote onverwachte kosten en onderbrekingen te voorkomen? Is het het waard, en zo niet, moet je dan een run-to-failure-strategie gebruiken?
Wat had er, aan de hand van het voorbeeld in vraag 5, kunnen worden gedaan om de uitsplitsing van $ 3250 te voorkomen?
Nadat uw technicus het probleem heeft opgelost, weten ze wat de storing heeft veroorzaakt. Als u de oorzaak van de storing kent, kunt u onderhoud plannen en plannen om meer storingen te voorkomen.
Laten we bijvoorbeeld zeggen dat een verstopt filter schade aan de motor heeft veroorzaakt die tot de storing heeft geleid. Nu weten we wat we moeten doen. Vervang het filter op de vorkheftruck elke 3 maanden samen met het verversen van de olie, zodat de lucht vrij door de motor van de vorkheftruck kan stromen, wat moet voorkomen dat deze verslechtert en kapot gaat.
De oplossing is niet altijd even duidelijk als het vervangen van een filter, maar door de RCM-analyse te doen, kunt u de gegevens verkrijgen om de beslissing te nemen of middelen besteden aan preventief onderhoud is de moeite waard om storingen te voorkomen . Als dat niet het geval is, voldoet een run-to-failure (reactieve) strategie wellicht het beste aan uw behoeften.
Vraag 7: Wat moet er gebeuren als er geen geschikte proactieve taak kan worden gevonden (standaardacties)?
Deze vraag klinkt verwarrender dan het is.
Hier is een andere manier om het te verwoorden:
Als u geen preventieve of voorspellende onderhoudsplannen kunt implementeren om het probleem op te lossen, is er dan nog iets dat u kunt doen?
Zeker daar dit. Er is alleen een beetje creatief denken voor nodig.
Laten we bijvoorbeeld zeggen dat u een oude vorkheftruck heeft en u besluit dat de beste keuze zou zijn om hem te laten draaien totdat hij doodgaat. U kunt de productiestilstand voorkomen die wordt veroorzaakt wanneer de vorkheftruck uiteindelijk defect raakt door een proces in te voeren om een vorkheftruck te huren of een vorkheftruck van een andere afdeling te lenen, zodat u geen productiviteit verliest. Het bedenken van deze oplossingen is vaak het beste wanneer u brainstormt met andere mensen in uw team (d.w.z. technici, management, productiepersoneel, andere afdelingen).
Dit is een situatie waarin de onverwachte storing niet echt zo onverwacht is, dus u kunt de oplossing van tevoren voorbereiden.
Hoe kan uw bedrijf veranderingen doorvoeren op basis van RCM-analyse?
Zodra u de bovenstaande vragen heeft beantwoord, is het tijd om wijzigingen door te voeren op basis van de resultaten van uw RCM-analyse.
Vanaf hier bepaal je welk plan nodig is. Hier is een overzicht van enkele van de meest voorkomende onderhoudsstrategieën en hoe deze te implementeren.
Run-to-failure/reactief onderhoud
Definitie: De apparatuur repareren als deze defect raakt.
Voorbeeld: Als u wacht tot uw printplaat defect raakt voordat u een technicus stuurt om deze te repareren, vertrouwt u op correctief onderhoud. Dit soort onderhoud is meestal het duurst, maar nooit helemaal te vermijden. Dat gezegd hebbende, correctief onderhoud heeft zijn tijd en plaats en dankzij uw Reliability Centered Maintenance-analyse weet u wanneer u het op de juiste manier moet gebruiken.
Preventief onderhoud
Definitie: Werk dat regelmatig op een geplande basis wordt uitgevoerd om de kans op uitval van apparatuur te verkleinen. Preventief onderhoud wordt uitgevoerd terwijl de apparatuur nog in werkende staat is om onverwachte storingen te voorkomen.
Preventief onderhoud kan tot 545% rendement opleveren. Hier leest u hoe u uw eigen plan kunt implementeren:
Stap 1. Selecteer machines die regelmatig onderhoud nodig hebben en hoge vervangings-/reparatiekosten hebben. Het plannen van preventief onderhoud aan deze bedrijfsmiddelen levert uw bedrijf het meeste rendement op.
Stap 2. Bepaal een onderhoudsschema op basis van de vereisten van het activum
Hoe vaak heeft elke machine routinematige preventieve zorg nodig? – Deze informatie is te vinden in de handleiding van de machine. Als u de handleiding niet kunt vinden, gaat u naar de website van de fabrikant, aangezien deze meestal een exemplaar online heeft staan.
Stap 3. Verzamel relevante informatie van je collega's en leidinggevenden. Mogelijk moet u met leden van het productieteam of ander personeel spreken om een goed idee te krijgen van hoe u het beste een preventieplan kunt implementeren en wanneer u de apparatuur het beste kunt onderhouden.
Stap 4. Voer uw preventief onderhoud uit. Nu moet u beslissen of u uw plan handmatig wilt uitvoeren of dat u een CMMS-systeem wilt implementeren dat de processen kan automatiseren.
Zodra het preventieve onderhoudsplan soepel loopt, kunt u langzaam andere activa toevoegen die baat hebben bij een goed preventief onderhoudsschema. Voordat u het weet, staat al uw apparatuur in uw preventief onderhoudsplan en begint u de voordelen te zien.
Voor een meer gedetailleerde gids over hoe u een strategie voor preventief onderhoud met succes implementeert, raadpleegt u onze How to Switch from Reactive Maintenance to Preventive Maintenance or How To.
Voorspellend onderhoud
Definitie: Bepaalt de staat van apparatuur terwijl deze in gebruik is door middel van hardware en software die is ontworpen om functionaliteit of afwijkingen te meten. Het rendement op de investering wordt behaald door precies te weten wanneer services nodig zijn en alleen apparatuur te onderhouden wanneer dat nodig is. Indien correct geïmplementeerd, is voorspellend onderhoud zeer kosteneffectief.
Onafhankelijke onderzoeken van het ISI (Instituut voor Wetenschappelijke Informatie) hebben aangetoond dat voorspellend onderhoud de preventieve onderhoudstaken met 15% kan verminderen en een algemeen effect op de uitvaltijd van 1-2% heeft.
Voorbeeld: Stel dat u warmtebeeldapparatuur gebruikt om te bepalen wanneer printplaten gerepareerd moeten worden. Met visuele inspecties worden problemen zoals oververhitting van de printplaat niet opgespoord. Dit is voorspellend onderhoud omdat u de apparatuur alleen repareert wanneer deze moet worden gerepareerd, in plaats van te vertrouwen op timing of gebruik via een preventief onderhoudsplan.
Stappen om voorspellend onderhoud te implementeren:
Voor voorspellend onderhoud is hard- en software nodig. In ons bovenstaande voorbeeld zijn een warmtebeeldcamera en warmtebeeldsoftware nodig om te bepalen of de printplaten moeten worden gerepareerd. Investeringen in hard- en software kunnen vaak kostbaar zijn. Gelukkig zijn er in het hele land bedrijven voor voorspellend onderhoud ontstaan die redelijk betaalbaar zijn.
Als u bereid bent om de nodige hardware- en software-investeringen te doen, zorg dan voor een lijst met apparatuur waarop u voorspellend onderhoud wilt implementeren. Doe daarna wat onderzoek online of door contact op te nemen met de fabrikant om erachter te komen wat u nodig heeft om voorspellend onderhoud voor dat apparaat toe te passen.
Bovendien kan het installeren van sensoren op uw apparatuur en het synchroniseren ervan met uw CMMS de totale kosten aanzienlijk verlagen, hoewel de initiële investering nog steeds groot is.
Als uw CMMS over de juiste integraties beschikt, kan het communiceren met de sensoren en u laten weten wanneer en hoe vaak u deze voorspellende onderhoudstaken moet uitvoeren.
Raadpleeg onze gids Wat is een CMMS-systeem en hoe werkt het voor een diepgaande kijk op wat een CMMS is.
Tot slot
Reliability Centered Maintenance kan u helpen inzien hoe belangrijk de beslissingen over het onderhoud van uw bedrijfsmiddelen zijn. Deze beproefde analysemethode helpt uw bedrijf tijd, geld en middelen te besparen, wat op zijn beurt uw winst zal verbeteren.
Als je geïnteresseerd bent in het verbeteren van je onderhoudsactiviteiten, bekijk dan Limble CMMS om te zien hoe we je kunnen helpen.
2 Reacties
-
Edward J Turk 9 september 2018, 17:09
Vergelijk RCM met voorspellend onderhoud voor mij.
Bedankt Ed
Reply -
David 20 september 2018, 13:55
Voorspellend onderhoud is een gestructureerd proces of methode waarin RCM zijn theorie van toenemende productiviteit van apparatuur en bedrijfsmiddelen toepast. Het is alsof je het afslaan op een kruispunt vergelijkt met autorijden.
Reply
Onderhoud en reparatie van apparatuur
- Gids voor productie-KPI's
- Wat is betrouwbaarheid?
- Weg met onderhoud. Verbeter de betrouwbaarheid.
- Wat is betrouwbaarheidscultuur?
- Conditiegebaseerd onderhoud:een complete gids
- Betrouwbaarheid:het draait niet allemaal om onderhoud!
- Onderhoud en betrouwbaarheid beste prestaties
- Details zijn belangrijk voor onderhoud en betrouwbaarheid
- Familiegerichte betrouwbaarheid
- 5 sleutels om de betrouwbaarheid van apparatuur te behouden
- Hoe Reliability Centered Maintenance (RCM) te implementeren