Extrusieproces:definitie, werkingsprincipe, typen, toepassingen, voordelen en nadelen [Opmerkingen bij PDF]
Op het gebied van werktuigbouwkunde is het Extrusieproces wordt veel gebruikt door de ingenieurs om een object te vormen met een vaste dwarsdoorsnede. Voor het maken van het object wordt de grondstof in een matrijs geduwd om het de gewenste vorm te geven.
De belangrijkste functie van dit proces is dat de brosse materialen gemakkelijk kunnen worden omgezet in het gewenste product, omdat bij extrusie alleen de schuifspanning en drukspanning optreden in het proces.
Er kan worden gesteld dat extrusie een semi-continu of zelfs een continu proces is dat kan worden gebruikt om warm of zelfs koud materiaal te vormen.
Wat is extrusie?
Extrusie is een vorm van metaalvormende bewerking waarbij matrijzen worden gebruikt om de vorm van het metalen stuk te veranderen met behulp van externe kracht die samendrukkend van aard is. Door dit proces kunnen we vrij gemakkelijk elk type complexe vorm maken.
Werkingsprincipe van extrusie:
De benodigde hoeveelheid kracht in het geval van het extrusieproces wordt gegeven door een plunjer of zuiger om de drukkracht te produceren. Het volgende is het werkingsprincipe van het extrusieproces:
- In het begin van het proces wordt een staaf of knuppel van een standaardmaat ontwikkeld door de fabrikant.
- Vervolgens wordt de knuppel verwarmd tot een hogere temperatuur in het geval van het hete extrusieproces en lange tijd bewaard bij kamertemperatuur om hem in de pers te duwen.
- De knuppel wordt door de plunjer in de pers naar de matrijs geduwd om de drukkracht te leveren.
- De matrijs is eerder vervaardigd in een vereiste vorm om het materiaal in de gewenste vorm te ontwikkelen. Hoge drukkracht helpt het materiaal om de gewenste vorm te bereiken.
- Ten slotte wordt het materiaal uit de pers gehaald en moet het daarna het afwerkingsproces doorlopen om de mechanische eigenschappen te verbeteren.
Soorten extrusie:
Extrusie kan grofweg in twee soorten worden ingedeeld, de ene is Hot Extrusion een andere is Koude extrusie . Deze bovengenoemde categorieën zijn ook onderverdeeld in categorieën, deze zijn als volgt:
Hete extrusie
- Voorwaartse extrusie
- Achterwaartse extrusie
Koude extrusie
- Voorwaartse extrusie
- Hydrostatische extrusie
- Hoer Extrusie
- Achterwaartse extrusie
- Impact extrusie
- Koude extrusie smeden
Dus laten we dieper in deze categorieën duiken.
Hete extrusie:
Ik hoop dat je al bekend bent met de naam van dit type "Hot extrusion". Hier in dit proces wordt het werkstuk of de knuppel verwarmd tot boven de herkristallisatietemperatuur, vervolgens wordt het in de container geladen en oefent de ram er kracht op uit.
Omdat het werkstuk al boven de herkristallisatietemperatuur wordt verwarmd, stroomt het vrij gemakkelijk door de matrijs en ook zeer nauwkeurig en effectief omgevormd.
De gebruikelijke materialen die bij dit type extrusie worden gebruikt, zijn magnesium, koper, staal, aluminium, nikkel, enz.
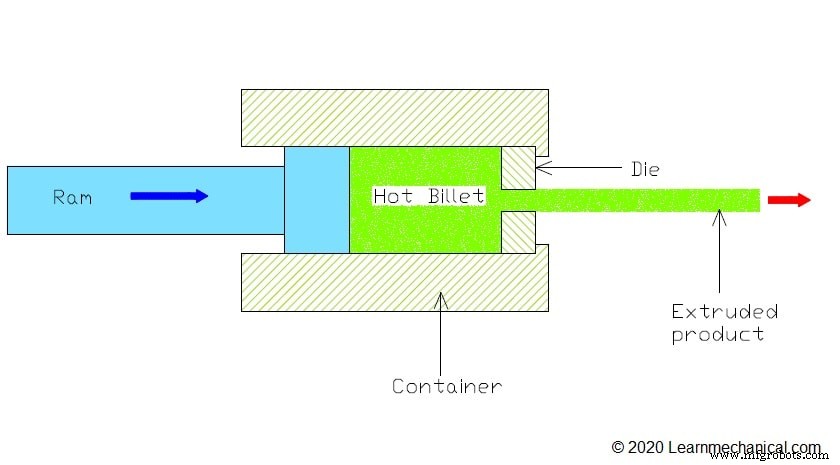
Koude extrusie:
In dit proces wordt het werkstuk op de normale kamertemperatuur gehouden, of je kunt zeggen onder de herkristallisatietemperatuur. Om een product door dit proces te extruderen, is een enorme hoeveelheid kracht nodig.
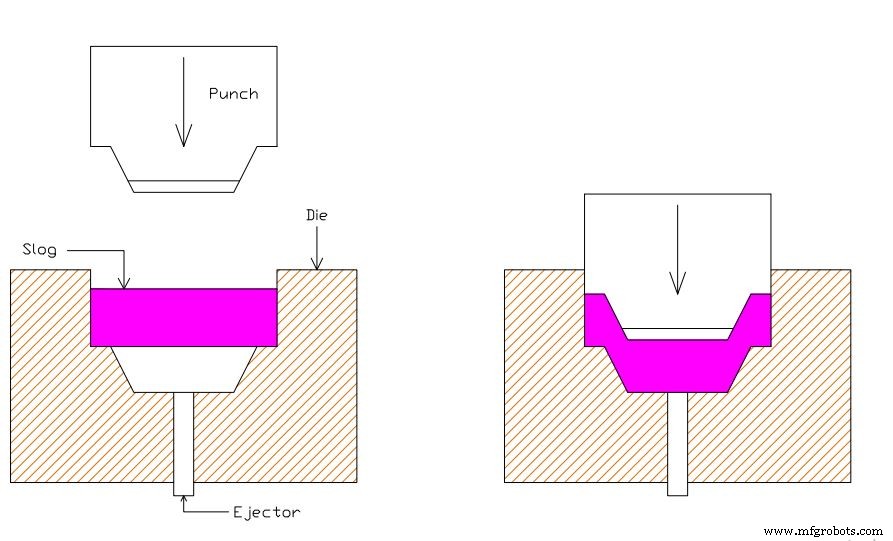
Indirecte extrusie:
In dit proces is de richting van de kracht die wordt uitgeoefend door de ram en de richting van het geëxtrudeerde metaal aan de andere kant. Dit type extrusie wordt ook wel backward extrusie genoemd.
Het belangrijkste voordeel van deze manier van extrusie is dat het de wrijving relatief vermindert. Ook kunnen we door dit proces metaal met een relatief kleinere diameter extruderen.
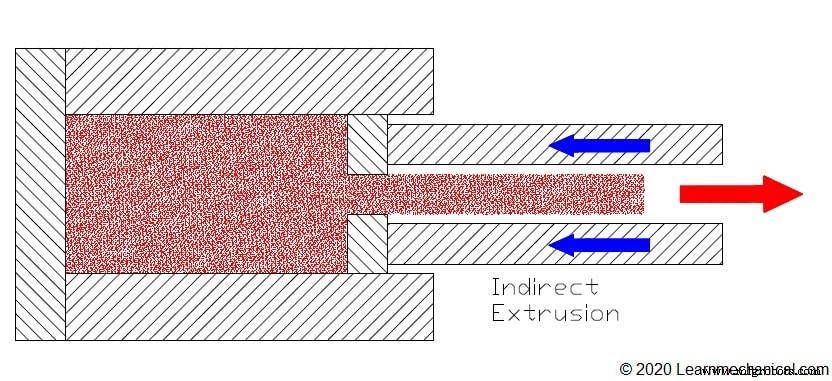
Directe extrusie:
Bij dit extrusieproces is de richting van de ram en de richting van het geëxtrudeerde metaal in dezelfde richting. Deze wijze van extrusie wordt ook wel voorwaartse extrusie genoemd.
Het grote voordeel van dit proces is dat we door dit type langere werkstukken kunnen extruderen.
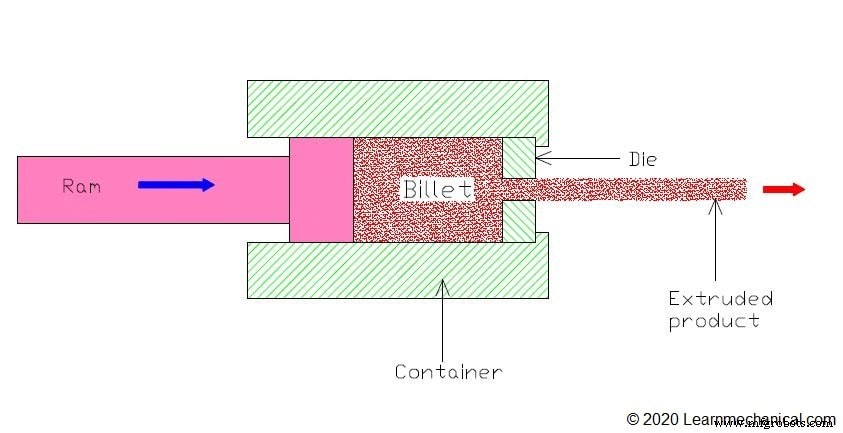
Hydrostatische extrusie:
Bij dit type extrusie gebruiken we vloeistof om de knuppel onder druk te zetten. Eerst wordt een knuppel in de container geladen, dan vullen we de container met vloeibare, meestal ricinusolie, dan wordt de container gesloten, behalve één kant van de container, die een ram en zuiger bevat.
Om de bewerking soepel te houden, wordt de knuppel conisch gehouden zodat deze gemakkelijk door de matrijs kan.
Dus wanneer we de machine starten, oefent de ram een grote hoeveelheid druk uit op de vloeistof en wordt deze overgebracht naar de knuppel. Door de vloeistof onder hoge druk vindt er een plastische vervorming plaats in de knuppel en deze komt uit aan de andere kant van de matrijs en krijgt de vorm van de matrijs.
Het belangrijkste voordeel van dit proces is dat er zeer weinig wrijvingskracht in actie komt omdat er geen contact is tussen de containerwand en de knuppel.
Hydrostatische extrusie geleidt gewoonlijk bij kamertemperatuur.
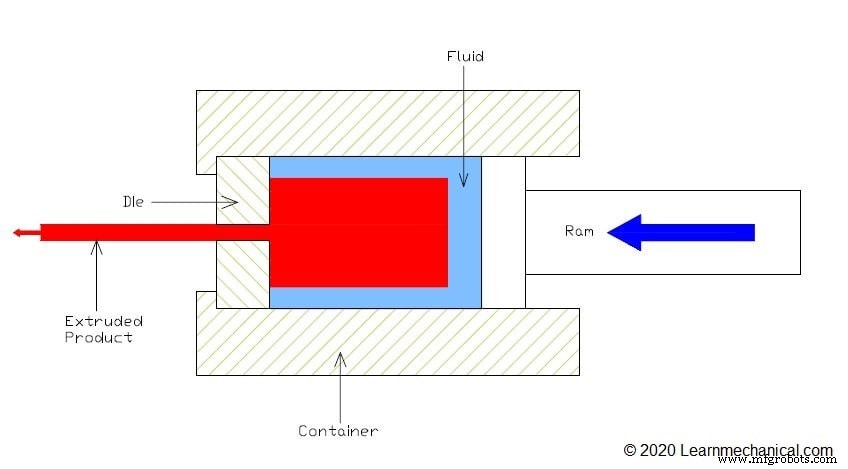
Hooker extrusie:
Dit is een vrij populair extrusieproces, waarbij dunwandige naadloze koperen of aluminium buizen worden geproduceerd.
Eerst wordt de knuppel of de plano in de container geplaatst, een pons wordt de kracht op het werkstuk uitgeoefend en maakt het werkstuk in een komvorm.
In de volgende stap oefende een langere pons opnieuw de kracht uit in de beker en maakte het een lang cilindervormig product en de dikte, zoals gewoonlijk, nam ook af.
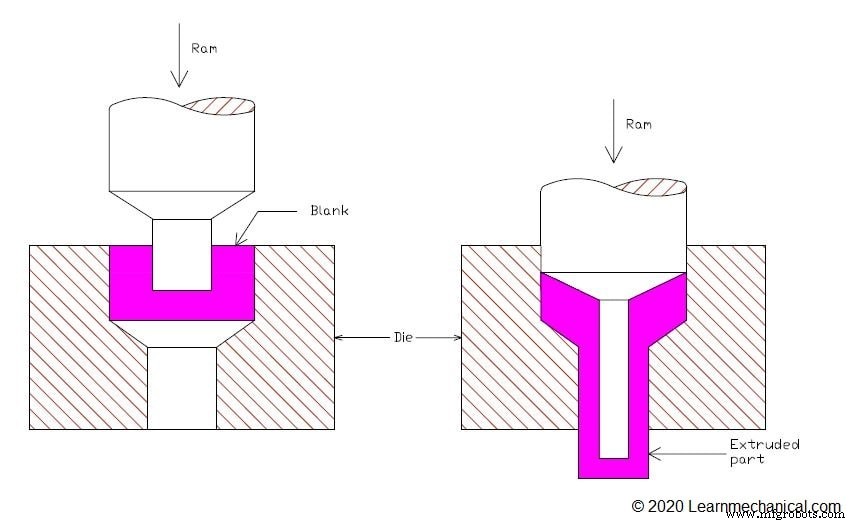
Impact extrusie:
Hier in dit proces wordt een pons met zeer hoge snelheid op het werkstuk geslagen om een impactbelasting te produceren. Het kan elk type zijn, zoals vooruit, achteruit en zelfs beide.
Het wordt over het algemeen gedaan bij kamertemperatuur, d.w.z. koude extrusie.
Als we producten nodig hebben zoals een beker, tandpastahoes of een hol gedeelte, doen we over het algemeen achterwaartse extrusie, wat een vrij populair effectextrusieproces is.
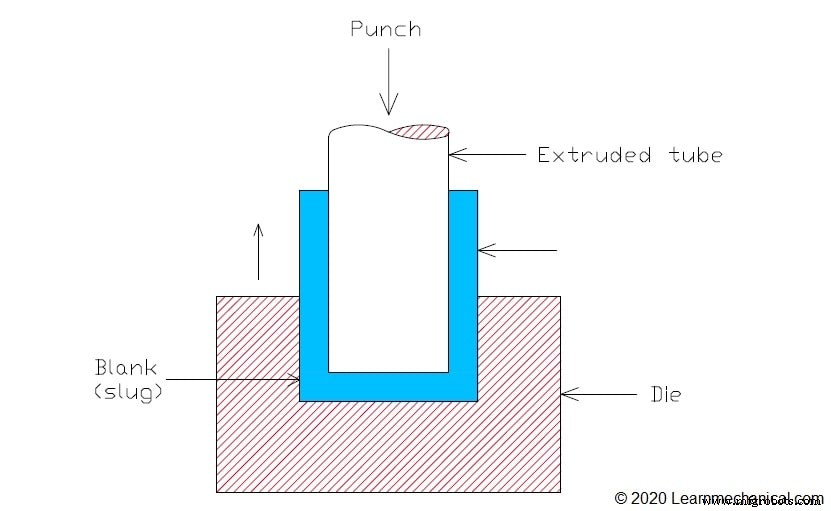
Koude extrusie smeden:
Koud extrusie smeden is een achterwaarts extrusieproces. Het proces van Cold Extrusion smeden is hetzelfde als van Impact Extrusion. In dit proces is de beweging van de pons of ram iets langzamer dan Impact Extrusion. Naarmate de kracht die op de plano wordt uitgeoefend geleidelijk toeneemt, is de lengte van het geëxtrudeerde product vrij kort, maar de dikte is groter.
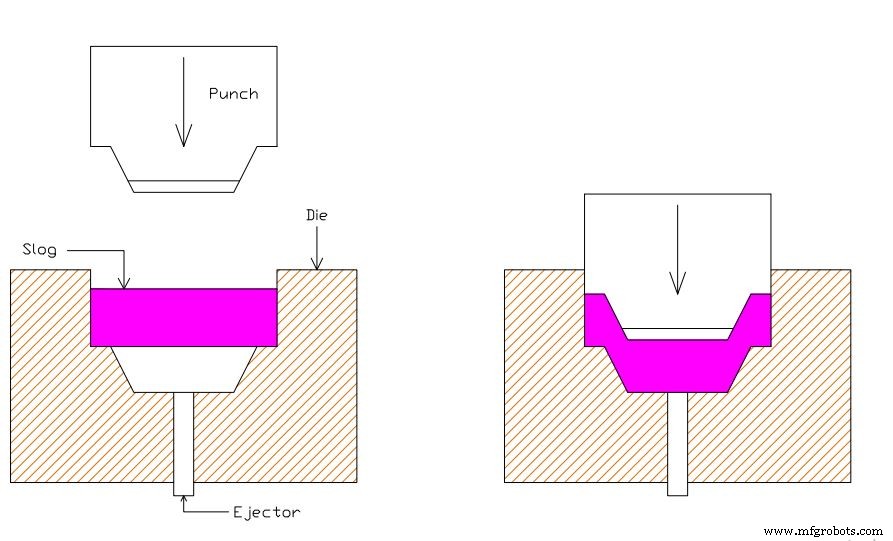
Toepassingen van het extrusieproces:
- Het extrusieproces wordt voornamelijk gebruikt bij de vorming van holle buizen en het kan worden gebruikt in de productie-industrie. Afgezien daarvan wordt door fabrikanten rekening gehouden met het extrusieproces voor het maken van instantvoedsel en snacks. In het geval van voedselverwerking wordt een extrusieproces gebruikt om het product te verwarmen en een vloeibaar stadium van het product te ontwikkelen. Ook bij het koken wordt tegenwoordig het extrusieproces gebruikt dat mengen, scheren, scheiden, koelen, verwarmen enzovoort omvat. Voor het verwijderen van het vocht uit de producten en ook voor het inkapselen van materiaal wordt door producenten ook rekening gehouden met het extrusieproces.
- Om het ontwikkelen van kant-en-klaar materiaal wordt echter een koud extrusieproces gebruikt . Zo worden bijvoorbeeld pastasoorten vervaardigd met behulp van een koud extrusieproces. Dit soort producten zijn verwerkt met een laag vochtgehalte waardoor de levenscyclus van producten wordt verlengd en het ook handiger is om klanten te bedienen.
- Bovendien worden farmaceutische producten ook ontwikkeld met behulp van het extrusieproces . Polymere filters, nanoporeuze goederen worden gevormd door het extrusieproces. Het maakproces van medicijnen heeft zowel een warm als een koud extrusieproces. Om de oplosbaarheid van producten en de biologische beschikbaarheid te vergroten, wordt het hete extrusieproces gebruikt. In dit proces wordt rekening gehouden met een hoge hoeveelheid druk, hitte en agitatie door fabrikanten.
- Daarnaast wordt in ruwbouw het aluminium extrusieproces gebruikt . Dit proces omvat deuren, ramen etc. In de auto-industrie wordt het extrusieproces ook gebruikt om het gewenste type materiaal te vormen door gebruik te maken van brosse materialen.
- Ten slotte kan worden gezegd dat het extrusieproces veel wordt gebruikt om plastic materialen te maken .
Voordelen van extrusieproces:
Extrusie heeft verschillende voordelen, namelijk:
- Het extrusieproces wordt veel gebruikt om binnen de kortste tijd een complex profiel van materialen te creëren in vergelijking met andere metaalvormende processen.
- Het extrusieproces is erg handig om met brosse en ductiele materialen te werken.
- De mechanische eigenschappen die kunnen worden ontwikkeld door het extrusieproces zijn zeer nauwkeurig en verbeteren de levenscyclus van producten.
Nadelen van extrusieproces:
Enkele nadelen van extrusie worden hieronder opgesomd:
- De tijdsbesteding van dit proces is erg hoog.
- De installatiekosten in de beginfase zijn ook erg hoog.
- De hoeveelheid drukkracht die nodig is voor het extrusieproces is ook erg hoog, en daarom moet de operator ervoor zorgen dat de plunjer op de juiste manier in de pers wordt bevestigd.
Conclusie:
Dit gaat dus allemaal over het extrusieproces in details.
Ik hoop dat je dit artikel interessant vindt.
Als dat zo is, voel je dan vrij om deze bron te delen met je vrienden of je favoriete sociale-mediagroepen. Je enige aandeel is echt merkbaar.
Industriële technologie
- Hoonproces:definitie, onderdelen of constructie, werkingsprincipe, voordelen, toepassing [Opmerkingen bij PDF]
- Lapproces:definitie, werkingsprincipe, typen, materiaal, voordelen, toepassing [Notities bij PDF]
- Rake Angle:definitie, belang en typen (positief, negatief, nul) [Opmerkingen bij PDF]
- Quick Return Mechanism:definitie, typen, werkingsprincipe, toepassingen, voordelen, nadelen [Opmerkingen bij PDF]
- Elektronenstraallassen:definitie, constructie, werking, toepassingen, voordelen en nadelen [Opmerkingen bij PDF]
- Plasmabooglassen:principe, werking, apparatuur, typen, toepassing, voor- en nadelen
- Solid State-lasproces:principe, typen, toepassing, voor- en nadelen
- Explosielassen:principe, werking, typen, toepassing, voor- en nadelen
- Wrijvingslassen:principe, werking, typen, toepassing, voor- en nadelen
- MIG-lassen:principe, werking, apparatuur, toepassingen, voor- en nadelen
- Wat is TIG-lassen:principe, werking, uitrusting, toepassingen, voor- en nadelen