Naar digitale productie van slimme multimateriaalvezels
Abstract
Vezels zijn alomtegenwoordig en meestal passief. Opto-elektronica gerealiseerd in een vezel kan een revolutie teweegbrengen in meerdere toepassingsgebieden, waaronder biosynthetische en draagbare elektronica, omgevingsdetectie en energiewinning. De realisatie van hoogwaardige elektronica in een vezel blijft echter een veeleisende uitdaging vanwege de ongrijpbaarheid van een materiaalverwerkingsstrategie die het mogelijk zou maken om apparaten gemaakt in kristallijne halfgeleiders, zoals silicium, in een vezel te wikkelen in een geordende, adresseerbare, en schaalbare manier. De huidige fabricagebenaderingen van glasvezelsensoren zijn ofwel niet schaalbaar of beperken de keuze van halfgeleiders tot de amorfe, zoals chalcogenideglazen, die inferieur zijn aan silicium in hun elektronische prestaties, wat resulteert in een beperkte bandbreedte en gevoeligheid van dergelijke sensoren in vergelijking met een standaard silicium fotodiode. Onze groep onderbouwt een universele in-fiber fabricage van logische circuits en sensorische systemen analoog aan zeer grootschalige integratie (VLSI), die de opkomst van de moderne microprocessor mogelijk maakte. We ontwikkelen een veelzijdige hybride fabricagemethodologie die in-fiber materiaalarchitecturen assembleert die typisch zijn voor geïntegreerde micro-elektronische apparaten en systemen in silica, silicium en metalen op hoge temperatuur. Deze methodologie, genaamd "VLSI for Fibers" of "VLSI-Fi", combineert 3D-printen van preforms, een thermische trekking van vezels en post-draw assemblage van in vezels ingebedde geïntegreerde apparaten door middel van materiaalselectieve ruimtelijk coherente capillaire breuk van de vezelkernen. Wij zijn van mening dat deze methode een nieuwe klasse van duurzame, goedkope, doordringende vezelapparaten en sensoren zal opleveren, waardoor de integratie van stoffen met door mensen gemaakte objecten, zoals meubels en kleding, in het Internet of Things (IoT) mogelijk wordt. Bovendien zal het de innovatie op het gebied van 3D-printen stimuleren en de digitale fabricagebenadering uitbreiden naar het domein van de nano-elektronica.
Inleiding
Hoewel glasvezel getrokken vezels dateren uit de Romeinse tijd, werden de eerste functionele optische vezels in 1792 vervaardigd door de Franse gebroeders Chappe voor communicatiedoeleinden [1]. In 1842 toonde Jean-Daniel Colladon, een Zwitserse natuurkundige, aan dat licht intern door een waterstraal kan worden geleid [2]. Deze twee ontdekkingen leidden tot tientallen jaren van optische en materiaaltechnische verbeteringen die hebben geleid tot de efficiënte vezels van vandaag, die snelle telecommunicatie en gegevensopslag over kilometers afstand over de hele wereld mogelijk maken, zoals de 25.000 km lange trans-Pacific onderzeese kabel (TPC) voltooid in 1996 [3, 4]. Bovendien worden glasvezelsensoren (FOS) gebruikt voor een breed scala aan biomedische, olie- en gas-, maritieme, architecturale, chemische en ruimtevaarttoepassingen [5, 6].
De controle en verbeterde prestaties van lichtvoortplanting met behulp van fotonische kristallen vezels (PCF), ontwikkeld in 1996 door Philip Russel, opende de deuren voor onderzoek naar complexere interne functionele structuren van vezels [7,8,9]. Nieuwe microstructuren verwelkomden ook de integratie van materiële diversiteit in hun samenstelling [10, 11] om slimme vezels te ontwerpen voor elektronica [12], opto-elektronica [11], in-fibersynthese [13], microfluïdica [14], micro-elektromechanische systemen [15, 16], en biosynthetische interfacing [17]. Slimme vezels verschillen van traditionele vezels door een niet-traditionele functie die verder gaat dan optische communicatie en het typische gebruik van vezels in commerciële stoffen. Slimme vezels kunnen worden gebruikt voor esthetiek in elektronisch textiel door het gekleurde uiterlijk van de vezels te regelen als gevolg van optische interferentie in hun microstructuur [18] of om de prestaties te verbeteren, bijvoorbeeld in het geval van conventionele optische vezelgeleiders en diëlektrische spiegelvoering die lichtgeleiding mogelijk maakt door de lucht [19, 20].
Om een vezel functioneel te maken, moet deze bestaan uit materialen met verschillende elektronische eigenschappen, moet de architectuur specifiek zijn ontworpen om een bepaalde functie uit te voeren, en moeten de interne kenmerken worden verminderd op nanoschaal, ordes van grootte kleiner dan de kern van de huidige telecommunicatie vezels. Vezels worden meestal gemaakt door fabricagemethoden voor optische vezels, dat wil zeggen dat ze thermisch worden getrokken uit macroscopische cilindrische of kubusvormige staven die "voorvormen" worden genoemd. Het fabricageproces begint met een selectie van geschikte kern- en bekledingsmaterialen, zoals metalen, isolatoren en halfgeleiders. Zo werd in 2004 de eerste vezel met metaal-isolator-halfgeleiderstructuren ontwikkeld voor fotodetectie [21]. Materialen voor de voorvorm zijn zodanig gekozen dat hun viscositeit, μ , zijn vergelijkbaar bij trektemperatuur en vallen ongeveer in het venster van 4 < log(μ )[poise] < 6 Dit is nodig om afschuifstromen en capillaire instabiliteiten te voorkomen die anders de geometrie van de vezelinrichting zouden verstoren. Materialen waarvoor deze eis onbereikbaar is, zoals metalen of kristallijne halfgeleiders die erg dun zijn in hun vloeibare vorm tijdens het trekken van vezels, moeten worden beperkt tot kanalen met een lage aspectverhouding, met een geometrie die dicht bij evenwicht is.
De voorvorm, die in wezen een opgeschaalde versie van de vezel is, kan worden gebouwd met behulp van verschillende technieken, zoals het oprollen van vellen materiaal zoals een vloerkleed, het stapelen van gefreesde onderdelen zoals een puzzel of 3D-printen, zoals weergegeven in figuur 1a. (I) en besproken in deze review, en vervolgens geconsolideerd door een vacuüm sinteren. De voorvorm wordt vervolgens verwarmd in een oven en uitgerekt tot een vezel zoals een karamel of taffy (zie tekeningkegel in Fig. 1a (II)), terwijl de dwarsdoorsnede ervan behouden blijft op basis van de gegeven thermomechanische eigenschappen van een construct, zoals viscositeiten, interface energieën, onderlinge adhesie en differentiële thermische uitzetting (Fig. 1a (III)) [22]. Dit proces, in het geval van een 3D-geprinte voorvorm, wordt schematisch geïllustreerd in Fig. 1a. Een typische trek kan kilometers vezel opleveren met zeer fijne dwarsdoorsnedediameters op nanoschaal rond 5 nm [23, 24].
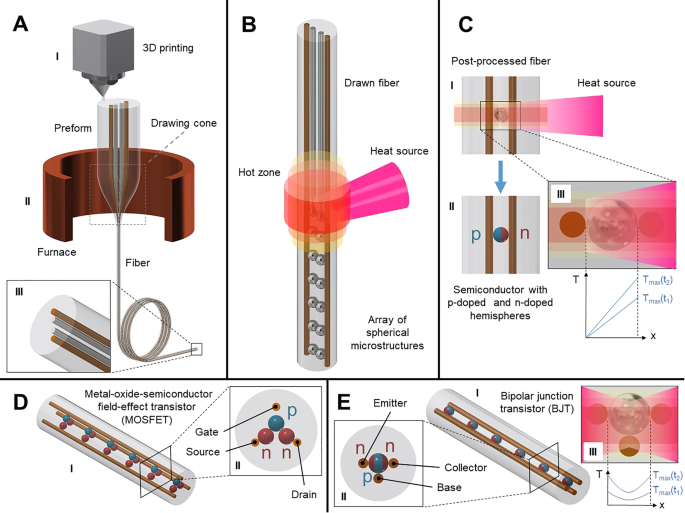
VLSI-Fi:Conceptuele schema's van de VLSI-Fi-techniek die de "2D + 1D + 0D"-benadering voorstelt. een De 3D-geprinte voorvorm a (I) wordt thermisch getekend a (II) in een lange, dunne vezel die de geometrie van de dwarsdoorsnede van de voorvorm (2D) behoudt. b Axiale patroonvorming van de vezel via ruimtelijk coherente, materiaalselectieve capillaire breuk (+1D), resulterend in de assemblage van aanvankelijk continue, afzonderlijke kernen in arrays van discrete apparaten die parallel in contact zijn. c Segregatiegestuurde controle van doping in halfgeleidende deeltjes na het uiteenvallen, waardoor de interne architectuur van een individueel apparaat kan worden gecontroleerd c (II) via thermische gradiënt c (III). d (I) Schematische illustratie van metaaloxide-halfgeleider veldeffecttransistor (MOSFET) via VLSI-Fi, waarbij de p-type en n-type halfgeleiders respectievelijk in blauw en rood worden weergegeven. De gouden doorlopende staven ingebed in een silicavezel fungeren als poort, bron en afvoer. De resulterende vezeldoorsnede wordt weergegeven in d (II). Evenzo, e (I) toont een schematische afbeelding van een bipolaire junctietransistor (BJT) gerealiseerd door VLSI-Fi, bereikt met botsende warmtebronnen van zowel de emitter- als de collectorzijde. De vezeldoorsnede e (II) toont de emitter, collector en basis van de BJT (continue staven ingebed in de vezel), met de p-type en n-type halfgeleiders van de npn-overgang respectievelijk in blauw en rood weergegeven
In een post-tekenstap, spelend op capillaire instabiliteiten, kan de vezel opnieuw vloeibaar worden gemaakt door verwarming om het uiteenvallen van de kernen mogelijk te maken op een ruimtelijk coherente materiaalselectieve manier, waardoor een axiale controle over de in vezels ingebedde structuren mogelijk wordt [25,26, 27] zoals geïllustreerd in Fig. 1b. Alternatieve technieken voor het axiaal patroontekenen van de kernen omvatten UV-blootstelling door fotomaskers in fotopolymere kernen, wat resulteert in niet-triviaal gevormde microdeeltjes [28]. Andere hybride-functionalisatietechnieken omvatten het coaten van de vezeloppervlakken met functionele materialen [10, 29] en opsluiting van een vezelbekleding door een trek [12] tot een reeks opto-elektronische apparaten vervaardigd door standaard complementaire metaaloxide-halfgeleider (CMOS) productie.
Vezels kunnen tot stoffen of netten worden geweven om een collectieve functionaliteit te bereiken die die van een individuele vezel overtreft [30]. Ontworpen door middel van biomimicry, kunnen vezels worden gevormd volgens de nuttige eigenschappen van de natuur om de functionaliteit van de stof te verbeteren, zoals hydrofobiciteit [31]. De vezels kunnen ook worden opgevat als syntheseplatforms voor goedkope materiaalproductie, zoals de omzetting van aluminiumkernen in silicium in met silica beklede vezels [13] of thermisch geïnduceerde fabricage van poreuze structuren door fasescheiding [32]. Vezels kunnen ook dienen voor externe en gedistribueerde signaaldetectie, zoals chemische detectie van gevaarlijke vluchtige stoffen in de omgeving [29]. De flexibiliteit in vezelontwerp is zodanig dat meerdere functionele modaliteiten in één vezel kunnen worden geïntegreerd voor complexe toepassingen zoals diepe spinocorticale stimulatie en monitoring bij muizen voor onderzoek naar neurodegeneratieve ziekten [33]. Deze voorbeelden laten een aantal van de verschillende domeinen zien waarin slimme vezels de natuurlijke oplossing zijn.
Motivatie
Hoewel vezels alomtegenwoordig zijn, blijft de integratie van hoogwaardige micro-elektronische systemen in een dunne vezel een grote uitdaging [11, 12]. Er zijn verschillende benaderingen voorgesteld om deze uitdaging aan te gaan, waarbij de inspanningen vooral gericht waren op materialen bij lage temperatuur. Hogedruk chemische dampafzetting (HPCVD) is bijvoorbeeld gebruikt om samengestelde halfgeleiders te integreren in microgestructureerde optische vezels (MOF's) [34], en om flexibele silicium p-i-n-junctievezels te creëren [35]. Als alternatief kan een CO2 laser werd gebruikt voor de herkristallisatie van SiGe-kern in silicavezels om hun elektronische eigenschappen te ontwikkelen [36]. Dergelijke benaderingen resulteren ofwel in apparaten met een beperkte elektronische bandbreedte, zoals het geval is bij chalcogenidematerialen, die intrinsiek amorf zijn of inherent niet-schaalbaar zijn.
Als zodanig heeft het Fibers and Additive Manufacturing Enabled Systems Laboratory (FAMES Lab) een techniek ontwikkeld en momenteel geïmplementeerd voor het regelen van de 3D-architectuur van vezels, die in deze review wordt beschreven. Aangezien de complexiteit van de uiteindelijke vezel correleert met de complexiteit van de dwarsdoorsnede van de voorvorm, maakt de fabricage in vrije vorm van voorvormen vezelapparaatfunctionaliteiten mogelijk die anders onbereikbaar zouden zijn. Bovendien is 3D-printen breed toegankelijk, waardoor het een kosteneffectief en gebruiksvriendelijk technologisch alternatief is voor traditioneel gebruikte methoden, waardoor een breed scala aan materialen mogelijk is, van thermoplasten tot materialen voor hoge temperaturen, evenals biomaterialen [37].
Bovendien heeft het FAMES-lab de mogelijkheid om materialen op hoge temperatuur te verwerken, naast het meer traditionele gebruik van thermoplasten in additieve fabricage, waardoor we kunnen profiteren van eigenschappen zoals de hoge elektronenmobiliteit in Si/Ge [38], evenals als het toekomstige gebruik van loodzirkonaattitanaat (PZT)/BaTiO3 composieten voor piëzo-elektrische toepassingen met grote piëzo-elektrische coëfficiënten in vergelijking met polymeren [39, 40] en hogere akoestische bandbreedte [41].
Met deze uitdagingen in het achterhoofd, stellen we optimalisatieoplossingen voor met behulp van additieve fabricage om snellere en complexere preformfabricage te bereiken, capillaire uiteenvalsimulaties om de axiale controle van de vezel te optimaliseren, en combinaties van onze vezels met tissue engineering. Deze strategieën maken het mogelijk om realistische biomedische platforms te creëren met biosensing- en biofunctionaliseringscapaciteiten voor in vitro geneesmiddelen- en behandelingsanalyse als een van de veelbelovende toepassingen voor glasvezelapparaten.
Concept
Om functionele vezels te realiseren, laten we ons inspireren door Very Large Scale Integration (VLSI) - een digitale ontwerp- en fabricagetechniek die in de jaren zeventig aanleiding gaf tot de moderne microprocessor. Deze techniek maakt gebruik van fotolithografie en chemische/thermische behandeling van blootgestelde delen van de halfgeleidende substraatwafel om de kenmerken van de geïntegreerde schakeling in deze laag (2D) te definiëren, terwijl de fabricage van een volledige schakeling vordert door het stapelen van dergelijke individuele lagen in de richting loodrecht op het wafeloppervlak (+1D). Bovendien kan de elektronische dotering van individuele componenten van het circuit (+0D) worden gecontroleerd door implantatie en thermische activering [42]. Onze benadering van vezels, genaamd "VLSI for Fibers" of "VLSI-Fi", is analoog:ten eerste definiëren additieve fabricage en thermische trekking van een voorvorm de geometrie van de dwarsdoorsnede van het vezelapparaat (2D); ten tweede kan de resulterende vezel later axiaal van een patroon worden voorzien (+1D), waardoor de assemblage van arrays van geïntegreerde discrete apparaten van aanvankelijk continue maar gescheiden kernen mogelijk wordt; en ten derde kan segregatiegestuurde structurering van individuele in-fiber-ingebedde apparaten (0D) worden uitgevoerd. Tabel 1 maakt een vergelijking tussen de twee technieken, waarbij de overeenkomst wordt benadrukt tussen elke graad van geometriecontrole die door elke techniek mogelijk wordt gemaakt ("2D + 1D + 0D"). De schema's van de beschreven stappen worden in detail getoond in Fig. 1, waar voorbeelden van mogelijke in-fiber-ingebedde apparaten kunnen worden gerealiseerd met behulp van de VLSI-Fi-techniek.
Experimentele sectie
In deze sectie beschrijven we eerst ons werk aan het 3D-printen van polycarbonaatvoorvormen, gevolgd door recente ontwikkelingen in 3D-glasprinten met behulp van stereolithografie. Vervolgens benaderen we de axiale patroonvorming van de vezels via een ruimtelijk coherente, materiaalselectieve capillaire breuk, die de assemblage van aanvankelijk continue, afzonderlijke kernen mogelijk maakt in arrays van discrete apparaten die parallel worden gecontacteerd. Ten slotte stellen we de toepassing van onze biointerfacing-vezels voor, gecombineerd met tissue engineering om levensvatbare weefselgroei in vitro te volgen. Functies worden mogelijk gemaakt door gebruik te maken van in-fiber microfluïdische kanalen om cellen en signalerende biochemicaliën en draden van vormgeheugenlegeringen voor bewegingscontrole te gebruiken, en piëzo-elektrische elementen om de omgeving in kaart te brengen door middel van ultrasone golven.
Tekening van 3D-geprinte preforms
Zoals eerder vermeld, zijn conventionele fabricagetechnieken voor voorvormen, zoals dunne-film-rollen en stapelen-en-ruw [10], beperkt in het produceren van complexe geometrische structuren, nemen een aanzienlijke hoeveelheid tijd in het vezeltrekproces in beslag en vereisen geschoolde arbeid en dure apparatuur. 3D-printen lost deze problemen op met behulp van oplosbaar ondersteunend materiaal en het deels geautomatiseerde en gebruiksvriendelijke proces. Dit maakt het printen van zeer complexe geometrieën met gemak in relatief korte tijd mogelijk.
Om de invloed van de afdrukhoek van polycarbonaat (Hatchbox 3D) preforms te beoordelen, werden cilindrische en vierkante staven geprint met behulp van een Prusa i3 MK2 FDM-printer met één kop. De temperaturen van de extruder en het printbed waren ingesteld op respectievelijk 235°C en 105°C en de printer was ingesteld om 100% infill-preforms te produceren met een mondstuk van 0,35 mm. De oriëntatie van de lagen in de voorvorm hangt af van de horizontale oriëntatie van het onderdeel ten opzichte van het printbed, en wanneer de voorvorm tijdens het thermisch trekken in de oven wordt ingebracht, wordt de warmtestroom beïnvloed door de laagoriëntatie. Om te testen welke oriëntatie het meest geschikt was voor thermisch trekken, werden voorvormen met 0°, 15°, 30°, 45° en 90° oriëntaties gedrukt. Alle hoeken werden gemeten tussen de lengteas van de voorvorm en de horizontale as. De 3D-geprinte preforms ondergingen het thermische trekproces in een oven met drie temperatuurzones van 90 °C, 100 °C en 200 °C. Voor de cilindrische preforms was de thermische trek succesvol onder hoeken 0° en 45°. De voorvormen van 90° mislukken altijd door delaminatie van de laag.
We waren ook in staat om met succes niet-evenwichtsstructuren te tekenen, zoals een vierkante staaf met een geïmproviseerd vulpatroon zoals weergegeven in Fig. 2a (I), waarbij in plaats van het rechtlijnige vulpatroon, de opvulling ook was ingesteld om de omtreklijnen te volgen en te printen in geordende structuur. Het trekken van de voorvorm op vierkante basis van 0° was succesvol, en hoewel deze enigszins vervormd was, was de vezel nog steeds in staat om de vorm van de voorvorm te behouden. Vezels met afmetingen zo laag als 40 m × 60 m werden met succes getrokken en worden getoond in figuur 2a, zonder delaminatie van lagen. Bovendien werden alle lagen goed geconsolideerd. Een voorbeeld van een vezeldoorsnede wordt getoond in Fig. 2a (IV), en afbeeldingen van een vezel voor en na het gloeien worden getoond in Fig. 2a (V) en 2a (VI), respectievelijk, waar we zien dat de gegloeide vezel bereikt optische transparantie, die in toekomstig werk zal worden gekenmerkt. Uit deze experimenten concluderen we dat de meest succesvolle preforms de preforms zijn die op 0° zijn gedrukt, terwijl 90° altijd delamineert tijdens het trekproces. De consolidatie van lagen in de thermisch getrokken vezels verbeterde naarmate de oriëntatiehoek van de 3D-geprinte preform afnam.
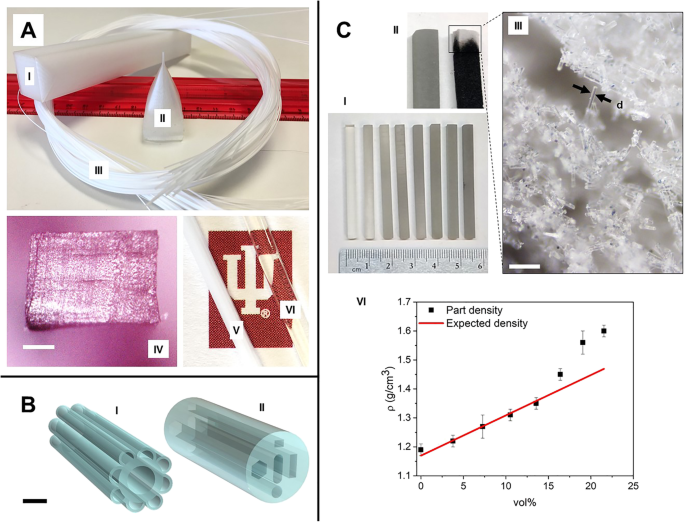
3D-geprinte preforms:a (I) 3D-geprinte voorvorm van polycarbonaat met vierkante basis. een (II) Tekenkegel. een (III) Resulterende polycarbonaatvezel na thermisch trekken. een (IV) Vezeldwarsdoorsnede na het trekproces, zonder delaminatie van de laag. De doorsnede is rechthoekig vanwege de niet-isotrope porositeit van het opvulpatroon (schaalbalk 200 m). een (V) Getrokken vezel voor het gloeien. een (VI) Getrokken vezel na gloeien met schijnbare optische transparantie. b CAD-modellen van Glass preforms, met succes gerealiseerd in natronkalkglas met zeer nauwkeurige 3D-printing op basis van extrusie. b (I) Structuur bootst blauw tarantulahaar na. b (II) Preform-model met niet-evenwichtige dwarsdoorsnedegeometrie (schaalbalk 1 cm). c (I) Vierkante glasmonsters met toenemende glasvulling (van links naar rechts), bedrukt met SLA-techniek. c (II) Detail van glasmonster voor het bakken (links) en tijdens het bakken (rechts). In de laatste is het mogelijk om de zwarte verkleuring te zien die het gevolg is van de verkoolde harsresten, terwijl de punt een witte kleur vertoont nadat deze resten zijn uitgeroeid. c (III) Beeld onder de microscoop van het vervaagde gedeelte (schaalbalk 200 m), waar de witte verkleuring het resultaat is van de natuurlijke kleur van de samengeperste gemalen vezels in een onderling verbonden poreuze structuur. Bovendien correleert de nominale breedte van de glasvezel, in de afbeelding aangegeven met d, met de verwachte waarden van 16 m (#38 Fiber Glas). c (IV) Een plot van de bedrukte glasvoorvormen dichtheden (ρ ) als functie van de volumefractie van glasvezels gemengd met hars, samen met de gemiddelde dichtheid van het printmateriaal
3D-printen van glazen preforms
Naast thermoplasten hebben glazen, waaronder gesmolten kwarts, belangrijke wetenschappelijke en technische toepassingen in optica, communicatie en elektronica [43]. Gestructureerde silicavezels kunnen meerdere toepassingen ten goede komen, bijvoorbeeld kleurloze kleuring van stoffen voor mode, fotonische kristalvezels voor optisch-chemische detectie of single-mode vezels voor telecommunicatie en het scherp concentreren van licht. Deze vezels worden over het algemeen vervaardigd door middel van een tweestapsproces:de fabricage van de voorvorm en het thermisch trekken van de voorvormen tot een vezel. Hoewel het trekproces relatief eenvoudig en goedkoop is, vereist de fabricage van voorvormen op dit moment een behandeling per geval en voor elke specifieke voorvormconfiguratie moet een afzonderlijke technologie worden ontwikkeld en toegepast.
Figuur 2b toont natronkalkglas preform computer-aided design (CAD) modellen die met succes met hoge precisie zijn gerealiseerd in op extrusie gebaseerde printtechnologie, vergelijkbaar met de producten beschreven door het bedrijf Micron3DP [44]. Dit materiaal heeft veelbelovende optische eigenschappen, vooral bij lange golflengten zoals IR [45], waardoor het een interessante kandidaat is voor de fabricage van vezels met nieuwe optische functionaliteiten. Het voorvormmodel getoond in Fig. 2b (I) bootst de structuur van het blauwe tarantulahaar na, vergelijkbaar met de structuur gepresenteerd in [46], en in Fig. 2b (II) bevat de voorvormdwarsdoorsnede niet-evenwichtsgeometrieën en is dus vatbaar voor hervormen als gevolg van minimalisering van de oppervlaktespanning. Deze modellen zijn ontworpen en gerealiseerd als een verificatie van de mogelijkheid om complexe, niet-evenwichtige voorvormdoorsneden te bereiken.
Aangezien de bekledingsstructuur mechanische integriteit aan de vezel verschaft tijdens het trekproces, omdat het is samengesteld uit het meest viskeuze materiaal, zijn onze inspanningen tot nu toe gericht geweest op dit onderdeel van de vezel, waar we uiteindelijk streven naar het behoud van de geometrie van de dwarsdoorsnede van de voorvorm. Op de lange termijn willen we extrusietechnieken voor meerdere materialen ontwikkelen, waardoor we meerdere materialen monolithisch in dezelfde print kunnen integreren. Als alternatief is het mogelijk om de structuur te vullen met poedervormige materialen zoals Si of Ge. De gevulde structuur kan vervolgens worden gesinterd om de voorvorm te verkrijgen. Gumennik et al. hebben een vergelijkbare benadering beschreven [47].
Als er interesse is om een vezel te produceren met natronkalkglas als kernmateriaal, zou een eenvoudige benadering zijn om een voorvorm met hangende kern te printen. Vezels met hangende kernen zijn van belang voor verschillende toepassingen, waaronder detectie [48] en verliesarme terahertz-geleiding [49], en worden meestal gerealiseerd met polymeren [49]. Bij dit type vezelgeometrie wordt de kern ondersteund door stutten die hem verbinden met de buitenste laag. Na het tekenen worden deze structuren verkleind tot afmetingen in de orde van grootte van de betreffende golflengte, op een manier dat voor het geleide licht het effect dat van een hangende kern is. Monro et al. hebben gesuspendeerde kernvezels gerapporteerd in verschillende materialen zoals silica en bismutglas [48]. Ze bieden ook een reeks voorbeelden van detectietoepassingen van deze vezels, met name in biologische en chemische detectie, wat de levensvatbaarheid van deze vezelgeometrieën bevestigt.
Nieuwe benaderingen voor op stereolithografie gebaseerde 3D-printen van glas met behulp van aangepaste harsen zijn ontworpen met behulp van foto-uithardbare silica nanocomposiet [50]. Hier stellen we een methode voor waarbij glasvezelvoorvormen worden vervaardigd door 3D-printen op basis van kant-en-klare commerciële harsen, waardoor het een kosteneffectieve en eenvoudigere methode is om 3D-geprinte glazen onderdelen te bereiken met behulp van stereolithografie (SLA). De SLA-printer (Form 2 van Formlabs) werkt met een laser met een golflengte van 405 nm om de hars via de bodem van het vat te verknopen terwijl het gebouwde platform stapsgewijs laag voor laag stijgt.
Om prints op glas te verkrijgen, gebruiken we een mengsel van commerciële heldere hars (Formlabs FLGPCL04 Clear) met 0,79 mm (1/32") borosilicaatglasvezels (#38 Fiber Glast) voor het drukproces. Dit zorgt voor een uitstekende controle van de uiteindelijke afdrukmateriaalsamenstelling en flexibiliteit bij het bereiken van de gewenste eigenschappen van de vezel. De glasvezels werden gedispergeerd in heldere hars met behulp van een magnetische roerder. Het glas wordt in kleine stappen toegevoegd en na elke toevoeging ongeveer 3 min gehomogeniseerd. Voor het drukproces, de printer was ingesteld op de open modus om het gebruik van onze aangepaste hars mogelijk te maken. Kubusvormige voorvormen met de afmetingen 4 × 4 × 50 mm werden geprint in een oriëntatie van 90°. Na het printen werden de onderdelen ondergedompeld in isopropanol gedurende 10 min om overtollig hars te verwijderen en nagehard met UV-licht gedurende 30 min bij 60 ° C. Voorvormen van uitgehard glas met toenemende volumeverhouding van glasvezels gemengd in de drukhars (van links naar rechts) worden getoond in Fig. 2c (I).
De preforms worden vervolgens nabewerkt om de resterende hars te ontbinden en de glasdeeltjes te sinteren, wat resulteert in een geheel dat uit glas bestaat. De effecten van deze processen op de preform worden geïllustreerd in Fig. 2c (II), waar we een preform zien na uitharding (links) en na het bakproces (rechts). In de laatste is het mogelijk om de zwarte verkleuring te zien die het gevolg is van het bakken in een verassingsoven, terwijl de punt een witte verkleuring vertoont na het ontbinden. Fig. 2c (III) toont een afbeelding die onder een microscoop wordt genomen van een voorvorm vóór het sinteren, waar te zien is dat alle hars inderdaad uit het onderdeel is gebakken, wat resulteert in een onderling verbonden structuur die alleen door de glasvezels wordt gevormd. Verschillende parameters moeten worden gecontroleerd, zoals baktemperatuur en verwarmingsprofiel, om chemische reacties en krimp te beheersen. De thermische ontbinding van het bindmiddel werd bereikt met behulp van een verassingsoven. De resulterende bruine delen werden gesinterd in een hoge temperatuur buisoven. Het sinteren werd uitgevoerd bij een temperatuur van 1300 °C en een druk van 5 × 10 −2 mbar, volgens het voorgeschreven protocol in [51]. Een bewaarfase bij 800°C werd ingesteld om moleculair gebonden water en oppervlaktegebonden silanolgroepen te verdampen. Sinteren onder vacuüm verbetert de optische transparantie omdat het de opsluiting van lucht in het sinterglasgedeelte vermindert [52].
Na de nabewerking worden het volume en het gewicht van de onderdelen gemeten om de dichtheid te verkrijgen. Dit wordt vervolgens vergeleken met de gemiddelde dichtheid van het afdrukmateriaal - samengesteld uit het mengsel van uithardbare hars en glasvezel - dat wordt berekend door ρ gemiddelde = ρ hars (1 − χ v ) + ρ glas (χ v ), waar ρ hars = 1.17 g/cm 3 is de dichtheid van de uitgeharde heldere hars, ρ glas = 2.55 g/cm 3 is de dichtheid van de gemalen glasvezels, en χ v is de volumeverhouding van de glasvezels die in de hars zijn gemengd.
De resultaten worden getoond in Tabel 2 en grafisch in Fig. 2c (IV), waar we de dichtheid van de bedrukte onderdelen weergeven voor verschillende volumeverhoudingen van glasvezel in de hars, vergeleken met de gemiddelde dichtheid van het afdrukmateriaal. We zien dat, voor lagere volumeverhoudingen van glas gemengd in de hars, de verkregen resultaten binnen de verwachte vallen. Bij hogere glasconcentraties zien we echter een afwijking van het lineaire gedrag van de ideale dichtheid. Dit kan worden toegeschreven aan de sedimentatie tijdens de afdruk, die significant wordt bij deze volumeverhoudingen, waardoor in die afdrukken effectief hogere glasconcentraties worden geproduceerd. Het printproces vindt plaats op de bodem van de tank, waar de glasconcentratie als gevolg van sedimentatie tijdens het printen constant toeneemt. Het begint vanaf (en hoger) de initiële uniforme concentratie die op de berekende curve zou moeten vallen.
Uit tabel 2 kunnen we zien dat bij 21,54 vol% gemalen glasvezels infill-onderdelen, de gemeten dichtheid 1,61 g/cm was 3 , wat betekent dat de werkelijke volumeverhouding 31,88 vol% is. Tijdens het experimentproces kregen we een monster met een werkelijke vulling van 34,78 vol% gemalen glasvezel. Dit resultaat was niet ver verwijderd van de 37,5 vol% silica-infill die werd vervaardigd door Kotz et al. [53], waar een aangepaste hars werd ontwikkeld, in tegenstelling tot de commerciële hars die we in dit werk gebruiken. Toekomstige richtingen voor dit werk zijn onder meer warmtebehandelingsprocedures, sinteren van onderdelen en de studie van de mechanische en optische eigenschappen van de resulterende onderdelen.
Coherente materiaalselectieve capillaire afbraak en segregatiecontrole van doping
Als een voorvorm eenmaal thermisch is getrokken, is het resultaat een lange, dunne vezel waarin de dwarsdoorsnede behouden blijft, zoals weergegeven in figuur 1a (III). In het geval van een vezel met een of meer kernen, kunnen deze axiaal van een patroon worden voorzien via een ruimtelijk coherent, materiaalselectief capillair opbreekproces [26], weergegeven in Fig. 3. Terwijl het Tomotika-model de vorming van periodieke instabiliteiten in een oneindige, gelijkmatig verwarmde cilinder van vloeistof, rekening houdend met de effecten van de omringende vloeistof [55], het voortplanten van Rayleigh-instabiliteiten introduceert het concept van voorwaartse voortplanting [56]. Hoewel er in de literatuur verschillende voorbeelden van wiskundige behandelingen van capillaire instabiliteiten te vinden zijn, zoals in Liang et al. [57], zijn deze werken vooral gericht op isotherme regimes, die in ons geval niet van toepassing zijn. Bovendien heeft ons geval een extra complicatie van het verspreiden van thermische gradiënt en dus gradiënt van viscositeit. Als zodanig is het waarschijnlijk dichter bij het marginale instabiliteit-criteriumgestuurde proces, zoals vermeld in Powers et al. [56]. Door zowel onze computationele als experimentele resultaten te combineren, willen we een wiskundig model opstellen voor het uiteenvallen van vezels via axiale thermische gradiëntverschijnselen.
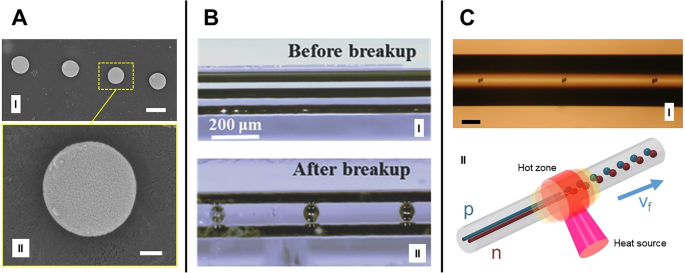
Capillaire breuk:a (I) Vezelsectie met Si-bollen gevormd door capillaire breuk (schaalbalk 0,5 m). een (II) Afbeelding met één bol die de vormkwaliteit weergeeft (schaalbalk 100 nm), van Gumennik et al. [26]. b (I) Voorbeeld van een metaal-halfgeleider-metaal fotodetecterend apparaat in een enkele silicavezel vóór b (I) en na b (II) uiteenvalproces, van Wei et al. [54]. c (I) Opbreken van een dubbelkernige vezel in bi-sferische clusters (schaalbalk 100 m), van Gumennik et al. [26]. c (II) Schematische weergave van het proces getoond in c (I), met p- en n-type kernen weergegeven in respectievelijk blauw en rood
De huidige fase van simulatie van capillair uiteenvallen richt zich op het stationaire regime. We zijn geïnteresseerd in het analyseren van hoe instabiliteiten zich voor het eerst ontwikkelen in een aanvankelijk stationaire vezel die wordt onderworpen aan een thermische gradiënt. Dit proces is analoog aan de eerste stap van de capillaire uiteenvalexperimenten uitgevoerd door Gumennik et al. [26], waarbij een silicavezel met een 4 μm dikke Si-kern door de hete zone van een waterstof-zuurstofvlam wordt gevoerd met stromen van respectievelijk 0,3 en 0,1 L/min. Hoewel de maximaal haalbare temperatuur met dit type toorts kan oplopen tot 2800 °C, moet de maximale temperatuur die de vezel ervaart onder het Silica kookpunt van 2230 °C liggen.
Considering that the flame width is between 3 and 3.5 mm and that the fiber has a diameter of about 300 μm, it is easy to understand why it is not feasible to experimentally measure the temperature gradient to which the fiber is exposed. Furthermore, the dynamic nature of the breakup process and the fact that it involves multiple materials with varying emissivities further adds to the complexity of the problem, while the fiber’s high aspect ratio and sharp viscosity ratios render the numerical simulation of the full Navier-Stokes equations computationally challenging.
In our simulations (using COMSOL Multiphysics® 5.3a, with its Microfluidics and Heat Transfer modules) shown in Fig. 4a, we assume an axisymmetric fiber with radius r fiber = 140 μm, composed of a thin Silicon core (r core = 2 μm) enclosed in a Silica cladding. Initial heat-transfer simulations showed that a fiber length of 15 mm is sufficient to ensure that the fiber extremities remain at room temperature, thus avoiding influence from the boundaries to the breakup process. Through the sweep of different parameters such as heat source length and distance to the fiber surface, as well as power, we can observe the changes produced in the breakup behavior, thus collecting information about the temperature gradient. Also of importance are the breakup period and speed, parameters which can be compared to experimental results and used for the refinement of the simulations.
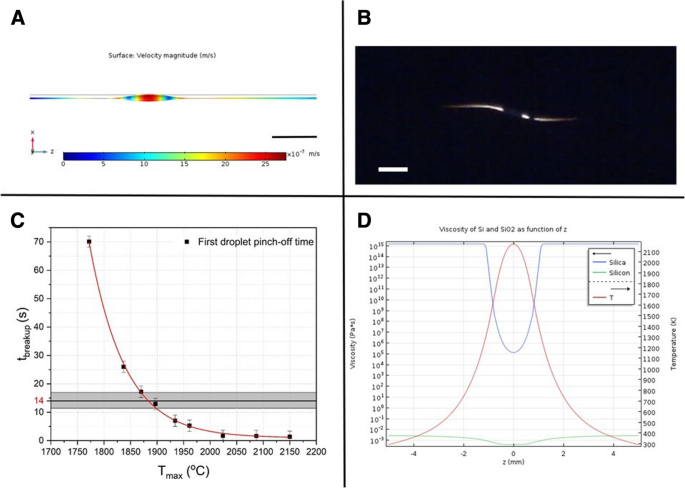
Capillary breakup simulations:a Image of the simulated Si core during the first droplet formation, right before the pinch-off for T max = 1900 °C. Color scale represents surface velocity (scale bar = 50 μm). b Snapshot of fiber breakup experiment recording just after the first droplet pinch-off, indicating a breakup time of 14 ± 3 s (scale bar = 60 μm). c Breakup time t breakup for different values of T max . The exponential dependence of t breakup on T max is evident, a behavior that is expected due to the dependence of t breakup on the core’s viscosity, which in turn depends exponentially on the temperature. The shaded rectangle encompasses the temperature range compatible with this breakup time-scale. d Si core and SiO2 cladding viscosities as a function of axial position, with temperature pro le over-imposed, for T max = 1900 °C
The simulations are performed in two steps:first, the steady-state temperature profile is calculated for different heat source powers, in order to achieve the desired maximum temperature T max . The results are then exported to a time-dependent fluid-flow simulation, where the Navier-Stokes equation is solved with time steps of 0.05 s, from 0 s until the first droplet pinch-off (t breakup ), which is dependent on T max , as can be seen in Fig. 4c, where t breakup is plotted for different values of T max . It is possible to observe that t breakup has an exponential dependence on T max , which is expected since t breakup is proportional to the core’s viscosity, which in turn is exponentially dependent on the temperature.
The relevant parameters used in these simulations are listed in Table 3. Preliminary simulations indicate that the phase transition of the Si core has no significant influence on the steady-state temperature pro le obtained, neither on the subsequent fluid-flow simulations since, in the entire region where the capillary instabilities occur, the temperature is higher than the melting point of Si. Therefore, in order to maintain the model as less computationally intensive, we simulate a core of liquid Si as a first approximation. Moreover, although a fully coupled heat-transfer and fluid-flow simulation is preferable, we consider that the effects of coupling bring second-order corrections to the solution and thus can be neglected at this stage. An image of the simulated core during the first droplet formation, right before the pinch-off, is shown in Fig. 4a, for T max = 1900 °C. A plot of the densities of silica and silicon, as a function of the axial position (in the simulation, the z-axis) for this particular simulation, is presented in Fig. 4d, with the temperature profile over-imposed.
Our results allow us to define the ranges of viscosities for which the time scales for breakup are comparable to those observed experimentally, thus assessing qualitatively the temperature profile imposed on the fiber. Fig. 4b shows a snapshot of a fiber breakup experiment recording just after the first droplet pinch-off, at the frame corresponding to t = 39 s. Since the resolution of the images before this frame is not ideal, judging on the basis of the symmetry of the breakup behavior, it is possible to assess that the pinch-off of the first droplet occurs at t = 35 ± 3 s, which translates to a breakup time after the temperature steady-state regime is achieved, of 14 ± 3 s. The shaded rectangle in Fig. 4c encompasses the temperature range compatible with this breakup time-scale, from which we can infer that the maximum temperature to which the fiber is exposed is 1885 ± 15 °C. With the collection of statistics on the breakup behavior in the future, we aim to develop a procedure for the temperature measurement of the process, which is otherwise unattainable by conventional means [26, 58, 59].
Moreover, segregation-driven control of doping in post-breakup semiconducting particles is attainable, allowing to control an individual device’s internal architecture. It is possible to control the structure of a single sphere, as was demonstrated by Gumennik et al. [47] shown in Fig. 5. When the droplet is exiting the flame, it experiences a thermal gradient:it is colder on the end distant from the flame, and consequently, it is expected to solidify laterally, starting from the colder side. If the sphere is doped with a material that is more soluble in a liquid than in a solid, this dopant will be repelled into the liquid as the solidi cation front propagates, collecting predominantly on the hot side. This effect is shown schematically in Fig. 1c and can be used to synthesize structured particles, composed for example of Ge-rich Si, (as shown in Fig. 5):Starting with 50:50 Si-Ge mixture in the fiber core, after the breakup the sphere will solidify, such that the Ge is extruded into the melt as the solidi cation evolves, leading to anisotropic distribution and resulting in axially oriented Janus particle heterojunctions [47]. This method can be extremely useful in assembling complex fiber-embedded devices such as heterojunctions, as shown in Fig. 1d and e.
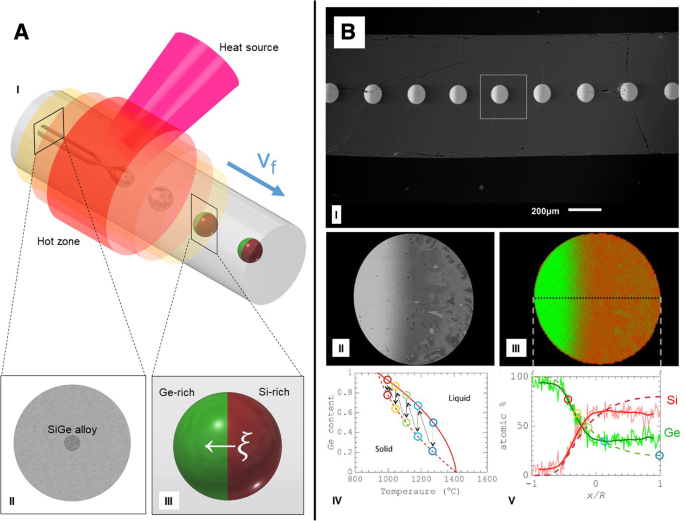
Segregation control of doping:a (I) Schematic illustration of the segregation-driven control of doping in post-breakup semiconducting particles. Details:cross section of a Ge-rich Silicon continuous core in silica fiber a (II) and post-breakup schematic drawing of doping-segregated sphere, or Janus particle, with the Ge-rich side indicated in green a (III). b (I) Scanning Electron Microscope image in backscattered mode of the fiber, polished along its axis, showing an array of Janus particles. b (II) Detail of single Janus particle cross section. b (III) Energy-dispersive X-ray spectroscopy (EDS) map of Janus particle, indicating non-homogeneous distribution of Ge along the cross section, from overlaid maps of Si (in red) and Ge (in green). b (IV) Si-Ge equilibrium phase diagram, liquidus (solid line), and solidus (dashed line). b (V) SiGe atomic content distribution along the dashed line in b (III). (From Gumennik et al. [47])
Biomedical Application
Fiber technology is frequently utilized in various biomedical applications as chemical, biological, and physical sensors. Fiber-embedded sensors have been designed to monitor physical parameters such as stresses, temperature, pressure, and humidity or chemical parameters such as pH level, oxygen concentrations, and carbon dioxide concentrations [60]. Fiber bundles are beneficial to embed multiple sensors together in a single system and in increasing signal reception levels, resulting in higher signal-to-noise ratios. Lightness, flexibility, and unique optical properties are the main characteristics that lead the demand for fiber sensors in biomedical studies. To meet clinical usage requirements, preforms must be fabricated from biocompatible, non-toxic, and chemically inert materials to prevent immune reaction from the patient. Examples of smart fiber development include a neural fiber probe composed of a polymer and metal core composition that enables flexibility and bending stiffness of the neural probe as it provides in vivo optogenetic stimulation and delivers drugs as an input in order to record feedback electrical and physiological output signals [33]. Another example is a fiber integrating microfluidic principles with complex cross-sectional geometries and meter-long microchannels which analyzes cell separation by dielectrophoresis (DEP). Live and dead cells are separated by inertial and dielectrophoretic forces by sheathless, high-throughput microfluidic cell separator which contains conductive materials in the microchannels [14]. The following strategies show a new array of possibilities where smart fibers can be used in biological interfacing.
Consider an artificial gut that can serve as a bioactivity testing platform at the microscale and at the macroscale. With today’s progress in tissue engineering, a variety of functionalities can be integrated in bioink-coated fibers co-extruded using a bioprinter for tissue fabrication, as shown in Fig. 6(I). Traditionally, bioprinting research aims at creating tissue grafts for regenerative medical practice and does so by carefully designing the hydrogel (Fig. 6(II)) with the appropriate nutrition and signaling molecules for the type of cells required based on the application (Fig. 6(III)). Tissue engineering is very challenging to study as the whole biology of the system completely changes microseconds after the experiment has been launched. Monitoring and regularly tuning a tissue’s maturation remains very complex.
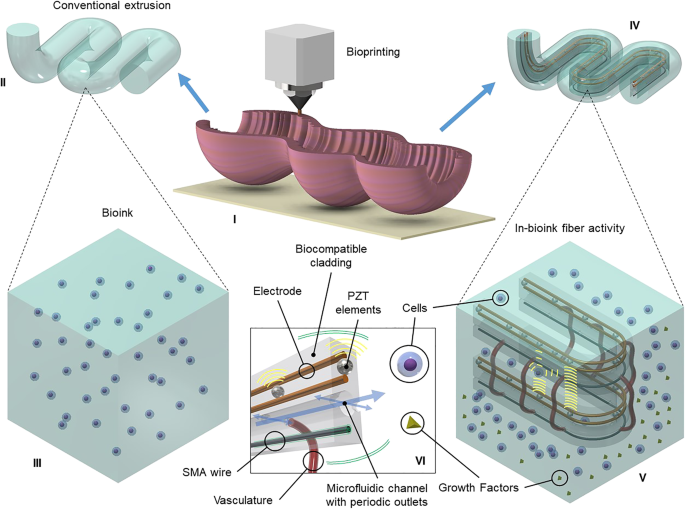
Biological interfacing. (I) Three-dimensional bioprinting of a tissue. (II) Standard microextrusion of bioink. (III) Conventional bioink with cells suspended in hydrogel. (IV) Novel coaxial microextrusion of biointerfacing fiber coated in bioink. (V) Close-up view of fiber where biointerfacing occurs:epithelial cells and vascular epithelial growth factors are excreted from different microchannels and result in cellular self-assembled vasculature between two orifices; piezoelectric elements measure surrounding cell density by ultrasound; and shape memory alloy wires provide peristaltic motion in the tissue. (VI) Visualization of biointerfacing fiber and its components
We propose here a solution by introducing smart fibers in the design (Fig. 6(IV)) to provide a better understanding of the climate and environmental growth. The embedded fiber holds multiple functionalities (Fig. 6(VI)) such as inducing vasculogenesis, ultrasonic imaging, peristaltic movement, and microfluidic flow. Control of the microenvironment takes place via the fiber hooked to syringe pumps and wired to an analytical software. The features of this application (Fig. 6(V)), including pilot experimental data, are detailed in the next subsections.
The Extracellular Matrix and Vasculature
Tissue engineering is widely explored with the increase of artificial tissue needs [61, 62], and the ability to bioprint realistic tissue has an important role to play in tomorrow’s drug and treatment development [63, 64]. One of the biggest challenges is the design of the extracellular matrix (ECM), composed of proteins, growth factors, and other biomolecules, that guide the cell’s contribution to the tissue [65]. Naturally, the ECM gives purpose and structure to the cells, and its extraction typically works by decellularizing tissue and recycling or reusing the ECM for a new cellular construct. The ECM comes in the form of solvents, hydrogels, biopolymers, bioceramics, aerogels, or foams to provide biodegradable or resorbable structure to the tissue [66]. Due to tissue engineering’s high complexity in defining the specifics of the biosystem—mechanical properties, scaffold dissolvability or absorption rates, initial cell types, nutrition, density and ratios, growth factors introduction, and its resulting bioactivity and tissue self-assembly—it is vital to assess the behavior of different types of naturally produced ECM or artificially developed biomaterials in the presence of interacting cells. Moreover, viable tissue requires an organized vascular system that supplies nutrition and oxygen to the tissue for the health and growth of cells. Vascularization provides the natural microfluidic feed of biochemicals to initiate proliferation, specialization, interactions, and motion. The vascular network is formed by vasculogenesis, arteriogenesis, and angiogenesis. Vasculogenesis develops its network through the differentiation and division of endothelial stem cell [67]. Angiogenesis forms new sprouts from existing vessels that are formed in the early embryonic vasculogenesis stage [68].
In-Fiber Microfluidic Feed
Microfluidic conduits with periodic microchannels for content delivery can be used to weave microfluids to specific locations in tissue constructs. The liquefaction front at the boundary of the hot zone defines the droplets’ pinch-off location as described previously. Multiple cores can therefore be broken up in a spatially coherent manner. For example, a silica fiber including a platinum and a silicon core can become a fiber tube with multiple outlets, by inducing the silicon core into an array of spheres and then thinning the fiber using hydrogen fluoride, etching the silicon spheres with potassium hydroxide and etching the platinum core with regal water. An example of the result is shown in Fig. 6(V). The flexibility of fibers allows the microfluidic feed to be integrated in multiple ways in tissue construct. In Fig. 6(IV), the microfluidic channels are used to provide the necessary cell type and growth factors to initiate vascularization and angiogenesis as the tissue reaches maturity.
Biomaterial and Biochemical Testing
In parallel to fiber development, a new testing platform (Fig. 7a (I)) was designed to analyze vascularization and cell-to-cell interactions in the presence of growth factors (Fig. 7a (II)). The platforms were printed in high resolution at an orientation of 30 from biocompatible resin by stereolithography (Formlabs’ Form 2 and Dental LT Clear resin). The print result, shown in Fig. 7a (III), was assembled with two glass capillary tubes with outer diameters of 1.8 mm and 1.0 mm where biological agents are fed. Initial trials will assess diffusion parameters of biochemicals and the growth of cellular colonies in various biocompatible materials. These platforms are designed to be single-use. In 2 h, 24 testing wells can be printed at a relatively low cost. The distance between each capillary outlet of two parallel fibers can be adjusted between 100 and 400 m to investigate the optimum vasculogenesis range that is accepted around 200 m [67]. The medium of interaction in the well’s chamber will first host commercial bioinks (Cellink, USA), one containing sodium alginate and nanofibrillar cellulose and the other containing gelatin methacryloyl, before developing our own in-house biomaterials. The glass capillary tubes shown in Fig. 7a (I) will eventually be replaced by the microfluidic fiber shown in Fig. 6a (V) which will be discussed in the next section.
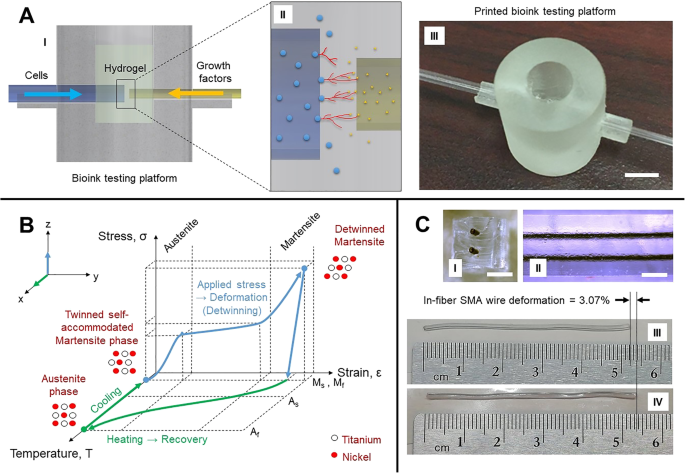
Pilot experiments for biointerfacing:a (I) Cross section of biotesting well showing fluidic feed. een (II) Example of the interaction of epithelial cells (blue circles on the left) with vascular endothelial growth factors (yellow dots on the right) resulting in vasculogenesis excreted by the cells (red lines in the center). een (III) Printed testing platform in biocompatible resin (scale bar = 5 mm). b Temperature-stress-strain graph of the shape memory effect. c (I) Cross section of in-fiber SMA wires (scale bar = 1 mm). c (II) Side view of in-fiber SMA wires (scale bar = 1 mm). c (III) 5.2-mm segment of an in-fiber SMA wire in contraction after being heated at 80 °C. c (IV) 5.36-mm segment of extended in-fiber SMA wire at room temperature
Peristaltic Motion
Shape memory alloy (SMA) wires are lightweight, non-corrosive, and cost-efficient actuating materials for refined applications in a variety of applications such as prosthetic biomimicry [69], self-expandable surgical implants [70], and aerospace engineering [71].
SMAs are metal compounds known for their shape memory effect and pseudoelasticity. Although such properties are typically found in nickel-titanium, these properties can be found in a range of different other metal alloys. Figure 7(b) shows the shape memory effect in terms of temperature, stress, and strain. As shown, at low temperatures, the SMA in its martensite solid state can be deformed by mechanical force, and when thermally induced, goes through a non-diffusive molecular reordering, converting to an austenite solid state. When cooled, the material will return to its initial martensite form, hence the shape memory effect. This thermal cycle is defined by four temperatures, the starting and finishing martensite and austenite temperatures (M s, M f , A s , and A f ), which specifies the start and end of transition periods between states. When the SMA is deformed in as martensite, the molecular de-ordering is defined as detwinning, and it allows the material to experience elongation, which is particularly useful for actuation applications. Essentially, the shape memory effect cycle can occur hundreds of times for an average elongation of 6% and contraction [72], hence its nickname “muscle wire” for its close similarity to muscular myofibrils.
This unique characteristic was first reported by Alden Greninger and Victor Mooradian in 1938 [73], can also be triggered by magnetic field energy [74], namely ferromagnetic shape memory alloys (FSMA), and can be found in polymers (SMP) as well [75]. Today, SMA’s mechanical fatigue and fracture, elasticity, and thermodynamics have been characterized well experimentally [76] and mathematically [77], and its behavior has been modeled [78].
Although the shape memory effect allows for nice contraction behavior of a material, for appropriate robotic applications, the motion needs to be reversable. Typically, an SMA is set in tandem with an opposite mechanism, such as springs, electric drives, elastic bands, or simply another SMA wire. Furthermore, the assembly changes whether it is a linear or rotatory actuation and if the opposing contractions of the actuation are equal. Although wires are thin and weak alone, they can be bundled together to reach the desired force and keep its shape memory effect response time. SMA wires can also be coiled around a capstan to provide greater elongation over shorter distances. Various strategies have been reviewed and chosen for specific applications [79]. The thermal induction is typically best controlled by powering the SMA wire and varying the input current of the order of hundreds of milliamperes. Cooling can be done naturally or by including heat sinks and ventilation.
Fiber drawing technology allows us to play on different material characteristics and to provide to an SMA wire an elastic coating that helps preserve the disorder state of the SMA fiber. As shown in Fig. 7c (I) and c (II), a fiber can be drawn with multiple embedded SMA wires. Styrene-ethylene-butylene-styrene (SEBS) was chosen as the surrounding structure to the SMA wires. SEBS is a copolymer elastomer that can withstand the drawing temperature of 80 °C. While preliminary results show that the actuation can work but with lower efficiency than bare SMA wires, the back-and-forth motion through heating (Fig. 7c (III)) and cooling (Fig. 7c (IV)) cycles is observed for a deformation of approximately 3.07%. More research is required to optimize the setup, but this early stage of experimentation in-fiber SMA actuation shows promising outlooks. The wires were physically pulled and heated using a hot plate to prove the concept. Heating by current would allow speeding up the shape memory effect and controlling better the heat’s diffusion through the fiber. The 5.35-mm wire was measured to have a diameter of 0.11 mm and a resistance of 18.2 was recorded across the fiber segment. To provide a frame of reference, according to SMA wire manufacturers (Dynalloy, Inc.), a 0.1-mm-thick wire made of nickel and titanium requires approximately 200 mA of current for a 1 s contraction. Controlling each wire individually would allow for directional movement, and adding more SMA wires to the design would allow multi-directional motion and greater contraction strength. Moreover, if ferromagnetic SMA wires were used, the control of the motion could become locally controllable via tuning of the interacting magnetic field. Additionally, the FAMES Lab’s drawing tower having the ability to rotate a preform as it is drawing into a fiber enables the possibility to manufacture spring-like structures of SMA wires in the fiber which allows for greater deformation, similar to commercially available SMA springs. Clearly, varieties of strategies are enabled with in-fiber SMA wires.
Biosensing
Biosensors are developed in a wide variety of ways. They can be designed label-based or label-free to detect specific expressions from biological elements such as cells, bacteria, hormones, proteins, DNA, and more [80, 81], from sampling blood, urine, saliva, sweat, or tears. Psychophysiological conditions can be observed from real-time biofeedback such as blood pressure, electrodermal activity, skin conductance, respiration and heart rates, and more [82, 83]. Bioimaging has been done by optical imaging, ultrasound, magnetic resonance frequency, computed tomography, near-infrared spectroscopy, quantum dot probing, and by many more techniques [84].
In optical fiber research, previous biosensing fibers have been fabricated relying on silicon photonic crystal detection of biological radiation [85]. Photonic crystal technology has been used before to monitor in label-free real-time cellular morphology and survival [86]. Such progress in biophotonics has led to hollow-core microstructured fibers visible under magnetic resonance imaging (MRI) [87]. The hollow core allows the propagation of the optical radiations along the fiber over very long distances. The geometry of the hollow fibers varies to tune the photonic bandgaps and dispersion of different detected wavelengths. The inner walls of these hollow tubes are coated with oppositely charged polyelectrolytes and magnetite nanoparticles which are used as contrast agents for MRI. Such design therefore enables new biomedical precision diagnosis opportunities, for example, in the observations of neural activity in vivo [87, 88].
Ultrasonography technology enables us to observe density of cells in liquid or gel in a non-intrusive manner [89, 90]. Ultrasonic probes typically function according to the piezoelectric effect (generation of electricity from applied stress), which was first discovered by Jacques and Pierre Curie in 1880 [91]. The inverse piezoelectric effect (deformation of a piezoelectric crystal from an applied electric field) was induced mathematically by Gabriel Lippmann in 1881 [92] and later in 1916, Chilowsky Constantin and Paul Langevin developed ultrasonic submarine detection for World War I military applications [93]. Thereon, sonar applications have been diverse, such as underwater imaging and fish-finding [94, 95] and energy harvesting [96, 97].
The piezoelectric elements convert electrical energy to and from mechanical energy and transmit sound waves between each other. All frequency and bandwidth parameters require precise regulation, and good energy transmission requires good acoustic and damping matching impedances. Two fibers with integrated piezoelectric elements, designed as pulsing emitter and receiver, can create an ultrasonic waveguide between each other to measure density over the wave’s trajectory. This fiber enables us to sense the microstructures of the environment as the tissue reaches maturation. The piezoelectric elements are created by capillary breakup from a PZT core for example. PZT elements have an acoustic impedance of 33.7 × 10 6 kg/m 2 s with a resonance frequency below 25 MHz. The produced spheres are lined with conductive electrodes to a transducer. This setup provides the feedback in a control system to better adjust microfluidic and motion feed. The in-fiber ultrasonic imaging of the microenvironment clearly helps understand how the tissue environment behaves over time.
Conclusies
We have formulated the concept of VLSI for fibers (VLSI-Fi)—a combination of liquid-phase processing techniques in microelectronic materials forming a toolbox for fabrication of high-performance devices and systems in fibers and textiles. Our experimental work focuses on a set of demonstrations substantiating our control over narrower aspects of VLSI-Fi, such as preform 3D printing, in-fiber circuit assembly by material-selective spatially coherent capillary instability, and segregation-driven doping control at the level of an individual fiber-embedded device. We envision that VLSI-Fi will enable realization of product in multiple technological areas, one of which is fabrication of active biomimetic scaffolds for engineered tissues with realistic microstructures.
Beschikbaarheid van gegevens en materialen
Not applicable.
Afkortingen
- BJT:
-
Bipolar junction transistor
- CAD:
-
Computer-aided design
- CMOS:
-
Complementary metal-oxide-semiconductor
- DEP:
-
Dielectrophoresis
- ECM:
-
Extracellular matrix
- EDS:
-
Energy-dispersive X-ray spectroscopy
- FAMES Lab:
-
Fibers and Additive Manufacturing Enabled Systems Laboratory
- FOS:
-
Fiber optic sensors
- FSMA:
-
Ferromagnetic shape memory alloys
- HPCVD:
-
High-pressure chemical vapor deposition
- IoT:
-
Internet of Things
- MOF:
-
Microstructured optical fibers
- MOSFET:
-
Metal-oxide-semiconductor field-effect transistor
- MRI:
-
Magnetic resonance imaging
- PCF:
-
Photonic crystal fiber
- PZT:
-
Lead zirconate titanate
- SEBS:
-
Styrene-ethylene-butylene-styrene
- SLA:
-
Stereolithography
- SMA:
-
Shape memory alloy
- SMP:
-
Shape memory polymers
- TPC:
-
Trans-Pacific undersea cable
- UV:
-
Ultraviolet
- VLSI:
-
Very large-scale integration
- VLSI-Fi:
-
Very large-scale integration for fibers
Nanomaterialen
- Het optimaliseren van digitale transformatie in CPG-productie
- GE opent slimme fabriek in Alabama
- Een volwassenwording voor de digitale draad in slimme productie
- Gegevensgestuurde productie-uitdagingen
- Wat is digitale transformatie in productie?
- Gebruikmaken van digitale technologie in de productie
- De digitale fabriek:slimme productie stimuleert industrie 4.0
- GE Digital:productie transformeren met Smart MES
- Slimme productie van Autodesk
- Digitale productie:de industrie van morgen
- Wat is slimme productie?