Composieten 4.0:digitale transformatie, adaptieve productie, nieuwe paradigma's
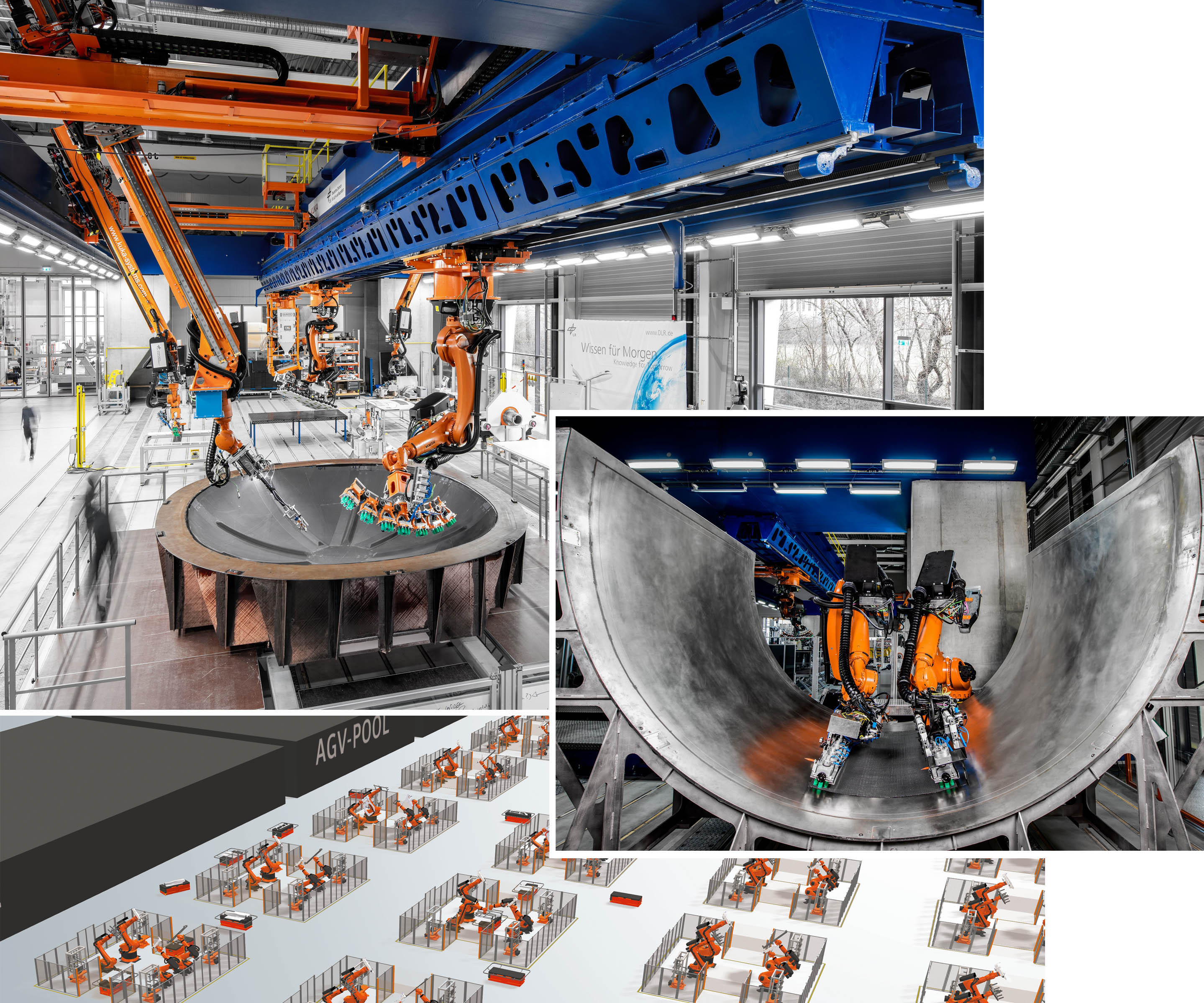
Composites 4.0 is een klein sterrenstelsel in het universum van Industrie 4.0, de digitale transformatie in hoe goederen en diensten worden ontworpen, geproduceerd, geleverd, geëxploiteerd, onderhouden en ontmanteld. Voor de fabricage van composieten is het doel om automatisering, sensoren en data, 5G-communicatie, software en andere continu evoluerende digitale technologieën te gebruiken om producten en processen efficiënter, intelligenter en adaptiever te maken.
Fabrikanten van composieten doorlopen deze digitale transformatie langs een spectrum. De eerste stappen zijn onder meer inline inspectie en geoptimaliseerde processen die afval en kosten verminderen en tegelijkertijd de kwaliteit en opbrengst van onderdelen verhogen. Meer geavanceerde oplossingen werken in de richting van intelligente, autonome productie die niet alleen agile is, maar reageert op en zelfs anticipeert veranderende markten en klanteisen.
"Composites 4.0 is geen doel, maar een hulpmiddel", legt Dr. Michael Emonts uit, directeur van het AZL Aachen Center for Integrative Lightweight Production aan de RWTH Aachen University (Aken, Duitsland), wiens iComposite 4.0-project een adaptieve procesketen met potentieel om de kosten van een autovloerpan met 50-64% te verlagen.
"Er is een verschil tussen gewoon dingen digitaal maken en digitale transformatie die de processen achter uw bedrijf daadwerkelijk verandert en nieuwe kansen en bedrijfsmodellen opent", stelt Christian Koppenberg, directeur van Dynexa, producent van composietonderdelen (Laudenbach, Duitsland).
"Composites 4.0 gebruikt niet alleen robots", stelt Dr. Michael Kupke, hoofd van het Duitse Aerospace Center's (DLR) Center for Lightweight Production Technology (ZLP, Augsburg), dat een met kunstmatige intelligentie [AI] uitgeruste werkcel heeft ontwikkeld waar collaboratieve robots kunnen overschakelen van het produceren van composiet achterdrukschotten naar romppanelen zonder herprogrammering of omscholing. “Het is de technologie die ervoor zorgt dat je de robots geen les hoeft te geven, want daar is geen businesscase voor. Composites 4.0 is meer dan alleen efficiëntie verhogen en kosten verlagen. Het is een verandering in hoe bedrijven denken over en omgaan met productie die zal bepalen welke bedrijven overleven en welke niet.”
Adaptieve preforming, RTM
“Het idee van het iComposite 4.0-project was om preforms te maken van kosteneffectieve rovings en tows door droge, lange glasvezels (25-30 millimeter) te combineren, gespoten en vervolgens versterkt met een raster van unidirectionele (UD) koolstofvezels via geautomatiseerde vezelplaatsing (AFP)”, legt Emonts uit. "De gekozen demonstrator, een achterbak onder de vloer van het voertuig, werd eerder gemaakt met duurder textiel dat ook meer dan 60% afval produceerde."
De Composites 4.0-transformatie vereiste integratie van het vezelspuiten, vezelafzetting en daaropvolgende harsoverdrachtgietprocessen (RTM), zodat ze op elkaar reageerden en werden aangepast op basis van de kwaliteit van het onderdeel gemeten tussen de stappen (Fig. 1). "We gebruikten een machine vision-systeem van Apodius GmbH [Aken, Duitsland] met een optische lasersensor en een cameramodule om de oppervlaktetopologie van de gespoten voorvorm te karakteriseren", zegt Emonts. “Apodius paste de software aan om het percentage vezels in elke richting te analyseren. De iComposite 4.0-lijn vergeleek dit met het digitale ontwerp en besloot of het aan de mechanische vereisten voldeed. Zo ja, dan heeft het het standaard UD-raster toegepast voor wapening. Zo nee, dan besliste het waar extra UD-vezellagen moesten worden geplaatst.”
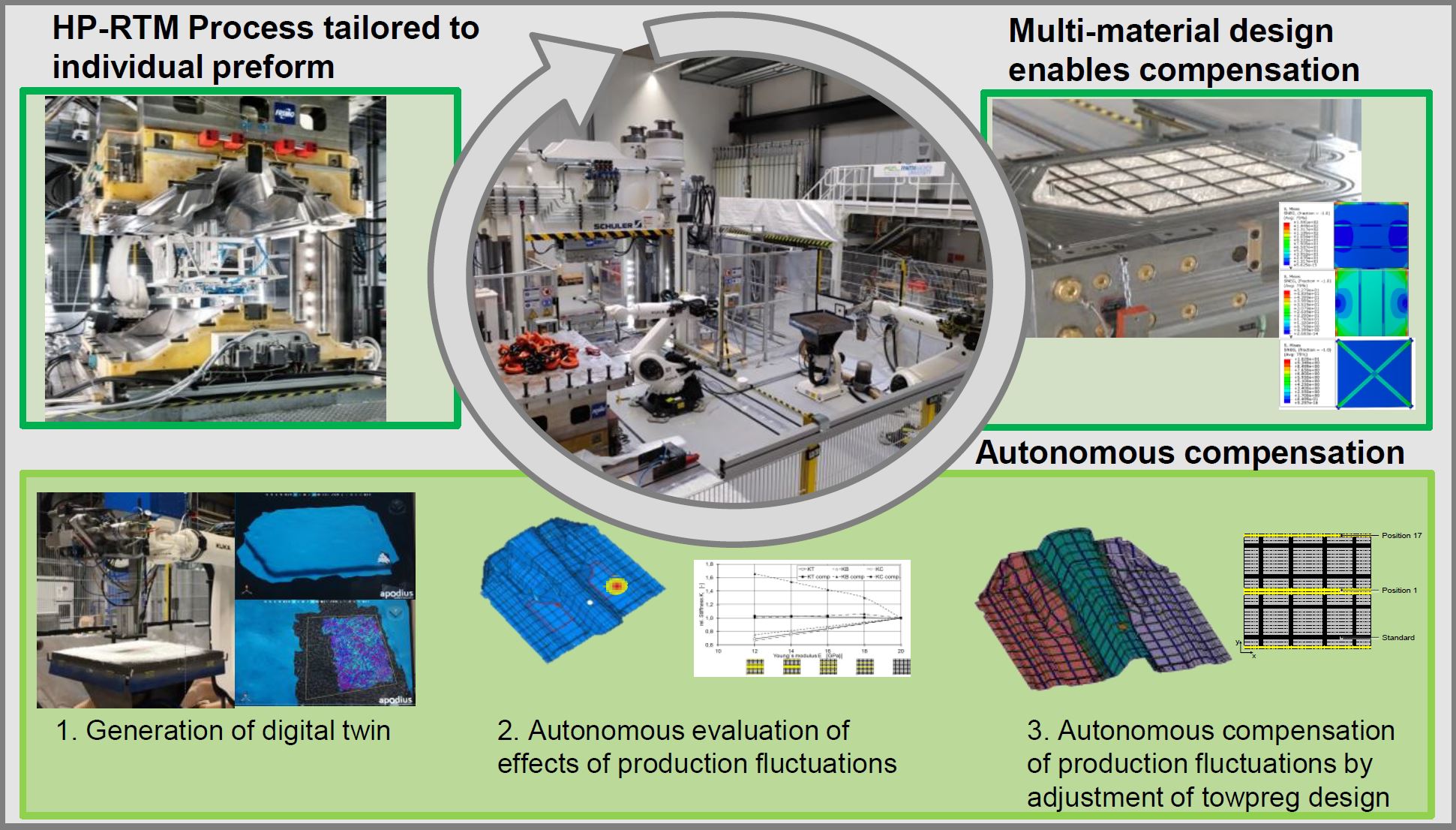
Deze extra UD-lagen kunnen er echter toe leiden dat de dikte en geometrie van onderdelen de toleranties overschrijden. "Daarom", legt hij uit, "hebben we de voorvormlijn gecombineerd met een adaptief RTM-proces dat, indien nodig, de onderdeeldikte aanpaste door de druk op bepaalde delen van de pers te verhogen." Ook dit was geautomatiseerd, met als doel interventie van de lijnoperator te vervangen, maar het vereiste wel simulatie van de prestatie van het onderdeel met behulp van meetgegevens en standaard FEA-software.
"Momenteel wordt de simulatie van de mechanische eigenschappen van het onderdeel offline uitgevoerd", zegt Emonts. “We hebben een database met proces- en onderdeelvariaties gegenereerd, algoritmen gemaakt om op elke variatie te reageren en deze via FEA gevalideerd. Dus, op basis van de variaties die door de lijn werden gemeten, gaven de algoritmen deze opdracht om een geschikte beperking uit te voeren. Om de lijn in-situ adaptief te maken, zou de volgende stap het toevoegen van machine learning zijn.” Ondertussen voert AZL tal van Composite 4.0-projecten uit, waaronder zelfgeoptimaliseerde productie van hybride thermoplastische composieten en spuitgegoten onderdelen met geïntegreerde verstijving van op tape gebaseerde op maat gemaakte blanks.
Zero-defect CFRP wingskins
Het ZAero-project (zie "Zero-defect fabricage van composietonderdelen") is een ander belangrijk Composites 4.0-project, dat in 2016 van start ging. Het was gericht op het verhogen van de productiviteit voor grote koolstofvezelversterkte kunststof (CFRP) structuren zoals wingskins. Defecten zouden worden verminderd door gebruik te maken van geautomatiseerde inline-inspectie met ofwel prepreg AFP of Danobat's (Elgoibar, Spanje) geautomatiseerde plaatsing van droog materiaal (ADMP, zie "Bewijs van levensvatbaarheid van droge stoffen, infusie voor grote aerostructuren"). Procesbewaking tijdens harsinfusie of prepreg-uitharding zou de uithardingstoestand voorspellen en de cyclustijd verkorten. De verzamelde proces- en defectgegevens werden met FEA gebruikt om de prestaties van onderdelen te voorspellen. Dit werd vervolgens ingevoerd in een beslissingsondersteunend hulpmiddel voor het aanpakken van geïdentificeerde defecten. Er werd een part-flow-simulatie voor CFRP-wingkins ontwikkeld die, wanneer deze in deze tool werd ingevoerd, hielp bij het optimaliseren van een herbewerkingsstrategie (Fig. 2). Tegenwoordig worden veel van dergelijke onderdelen tijdens de fabricage herwerkt, maar pas na NDI. Eerdere herbewerking en verbeterde procescontrole waren inderdaad de doelstellingen van het ZAero-project, evenals de redenen voor de beoogde 15% hogere productiesnelheid, 15-20% reductie in productiekosten en 50% minder afval.
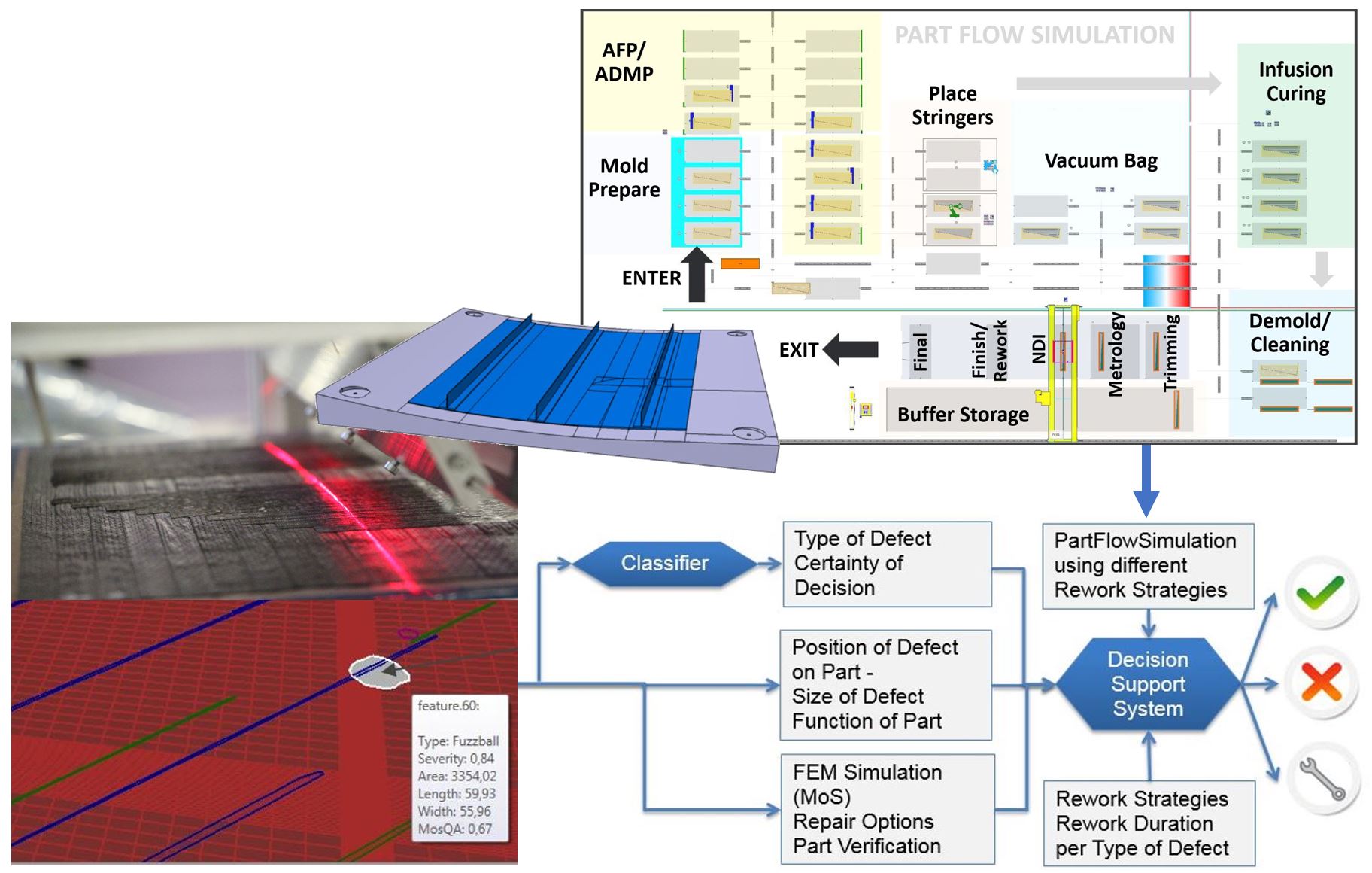
Bij de laatste beoordeling van september 2019 bereikte de prepreg AFP-sensor, ontwikkeld door projectleider Profactor (Steyr, Oostenrijk), niet alleen geautomatiseerde inline-inspectie, maar kon ook worden gebruikt om onderdelen ter plaatse te corrigeren. "Deze sensor kan de standaarddefecten detecteren, zoals gaten, overlappingen, FOD, fuzzballs en verdraaide kabels, evenals vroege en late sneden van elke kabel", zegt Dr. Christian Eitzinger, hoofd machinevisie voor Profactor. Een ontbrekende sleep kan automatisch worden gecorrigeerd door een extra sleep precies daar te plaatsen waar deze is weggelaten. De machine moet echter worden gestopt om fuzzballs of een verwrongen kabel te verwijderen. “Een database gebouwd met behulp van de 3D Experience van Dassault Systèmes (Parijs, Frankrijk) voor CATIA stelt ons in staat om de effecten op de prestaties van het onderdeel te berekenen op basis van de grootte, vorm en het type defect. Het verwerken van alle defecten in een laag duurt slechts enkele seconden. De machinist bepaalt vervolgens welke defecten er mogen blijven en wat er moet worden gerepareerd.”
Voor de bewaking en controle van het infusieproces heeft Airbus (Toulouse, Frankrijk) via dochteronderneming InFactory Solutions (Taufkirchen, Duitsland) drie sensoren ontwikkeld die de temperatuur, de uithardingstoestand en het harsstroomfront meten (zie "Sensoren voor het bewaken van het harsinfusiestroomfront". ) "We hebben deze geïntegreerd met CATIA 3D Experience en hebben aangetoond dat de gegevens betrouwbaar kunnen worden verkregen en toegevoegd aan de digitale thread van elk onderdeel", zegt Eitzinger. (Zie online zijbalk "Composites 4.0:Digital thread vs. digital twin".)
De laatste van driedelige demonstranten was een subsectie van de bovenste vleugelafdekking met drie stringers (zie online zijbalk "ZAero-projectupdate"). Voor dit onderdeel werd de beslissingsondersteunende tool van Profactor live gedemonstreerd bij partner FIDAMC (Madrid, Spanje), verbonden met de deelstroomsimulatie - gebaseerd op Siemens PLM (Plano, Texas, VS) Tecnomatix Plant Simulation-software - die draait op de Profactor-server in Oostenrijk. Naast het bouwen van een defectdatabase, voerde ZAero experimenten uit met machine learning. Handmatig ontworpen, generatieve computermodellen gecombineerd met diepe neurale netwerken gedetecteerde en geclassificeerde defecten, waardoor een percentage van 95% correcte classificatie van verschillende regio's (gap, overlap, sleep, fuzzball) in echte ADMP-bewakingsgegevens wordt bereikt, zelfs wanneer kunstmatig gecreëerde defectgegevens werden gebruikt voor de diepe netwerktraining (analoog aan hoe ultrasone testsystemen worden gekalibreerd op een reeks opzettelijke defecten).
"We zullen zeker een volgende fase nastreven", zegt Eitzinger. Ondertussen commercialiseert Profactor modulaire sensoren voor vezeloriëntatie en defecten tijdens geautomatiseerde layup. InFactory Solutions biedt ook zijn AFP- en harsinfusiesensoren aan, en vezelplaatsingspartners Danobat en MTorres (Torres de Elorz, Navarra, Spanje) verkopen nu hun apparatuur met geïntegreerde inline-inspectie.
Dynexa's digitale transformatiereis
Dynexa is een fabrikant van composiet onderdelen die gespecialiseerd is in CFRP buizen en assen. “We hebben altijd geprobeerd alles te digitaliseren”, zegt directeur Koppenberg. “We hebben handmatige en analoge processen al afgeschaft en alles grotendeels geïntegreerd in ons ERP-systeem [enterprise resource planning]. Maar hoe doen we dit in de maakindustrie? We begrepen dat alles wat we in een werknemersprotocol of -procedure stoppen een code is, en dit is een basis voor digitale transformatie. Maar waar wordt het opgeslagen? Op een lokale server, in de cloud of in de machine? We zouden vijf mensen vragen en zeven antwoorden krijgen over wat we moeten doen.” (Zie online zijbalk, "Composieten 4.0:waar te beginnen?")
Gelukkig had de Duitse regering een programma opgezet voor universiteiten om gratis Industrie 4.0-advies te geven aan kleine en middelgrote ondernemingen (MKB). Dynexa begon te werken met het Darmstadt “Mittelstand (SME) 4.0” Competence Center. “Ze zeiden dat we ons geen zorgen moesten maken over de digitale architectuur, maar meer moesten kijken naar wat je moet meten en hoe je dat moet doen”, herinnert Koppenberg zich. "We hebben één proces gekozen dat aanzienlijke handmatige metingen omvatte, waarbij we wisten dat we problemen hadden met kwaliteit, tijd en kosten."
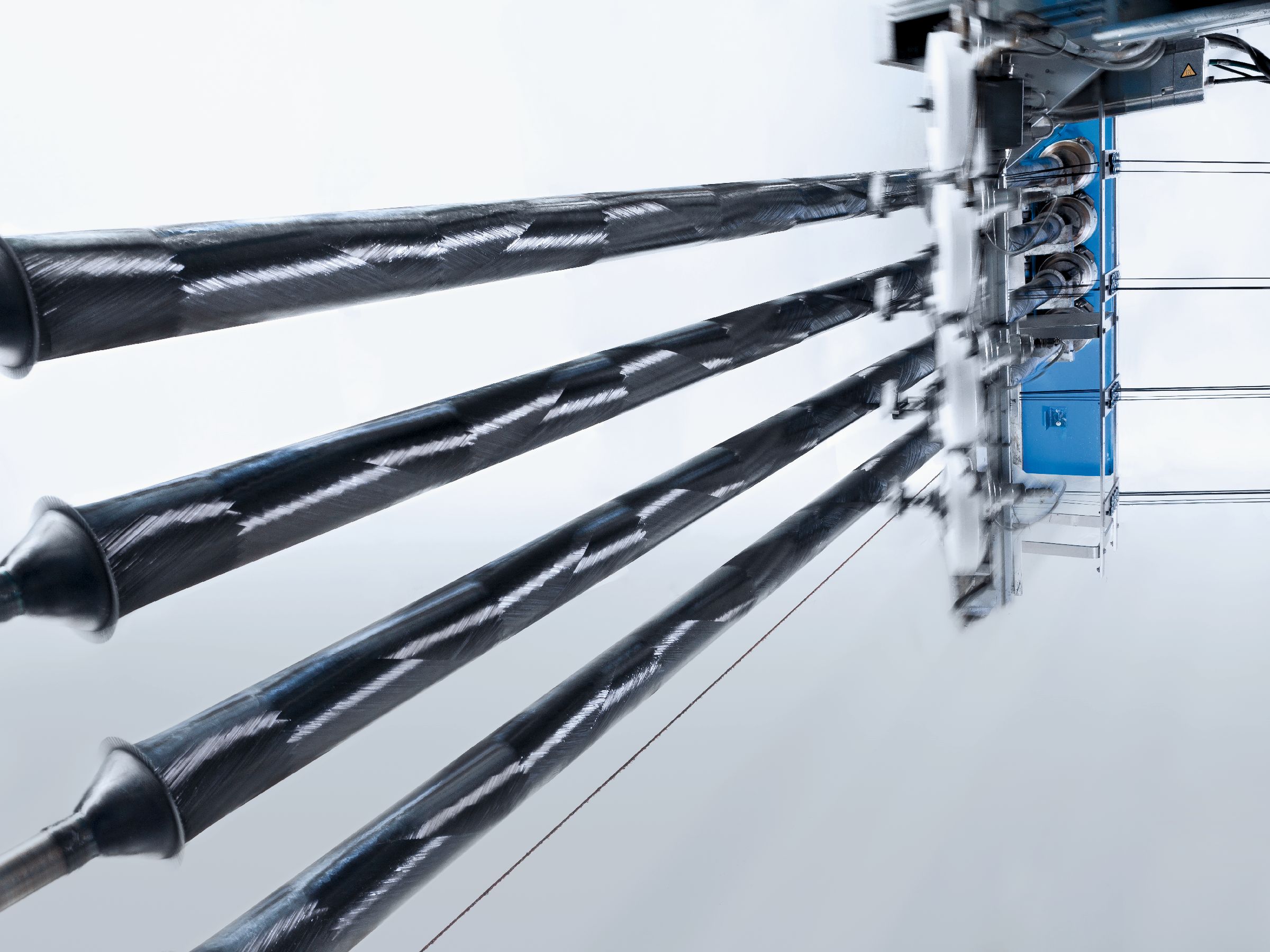
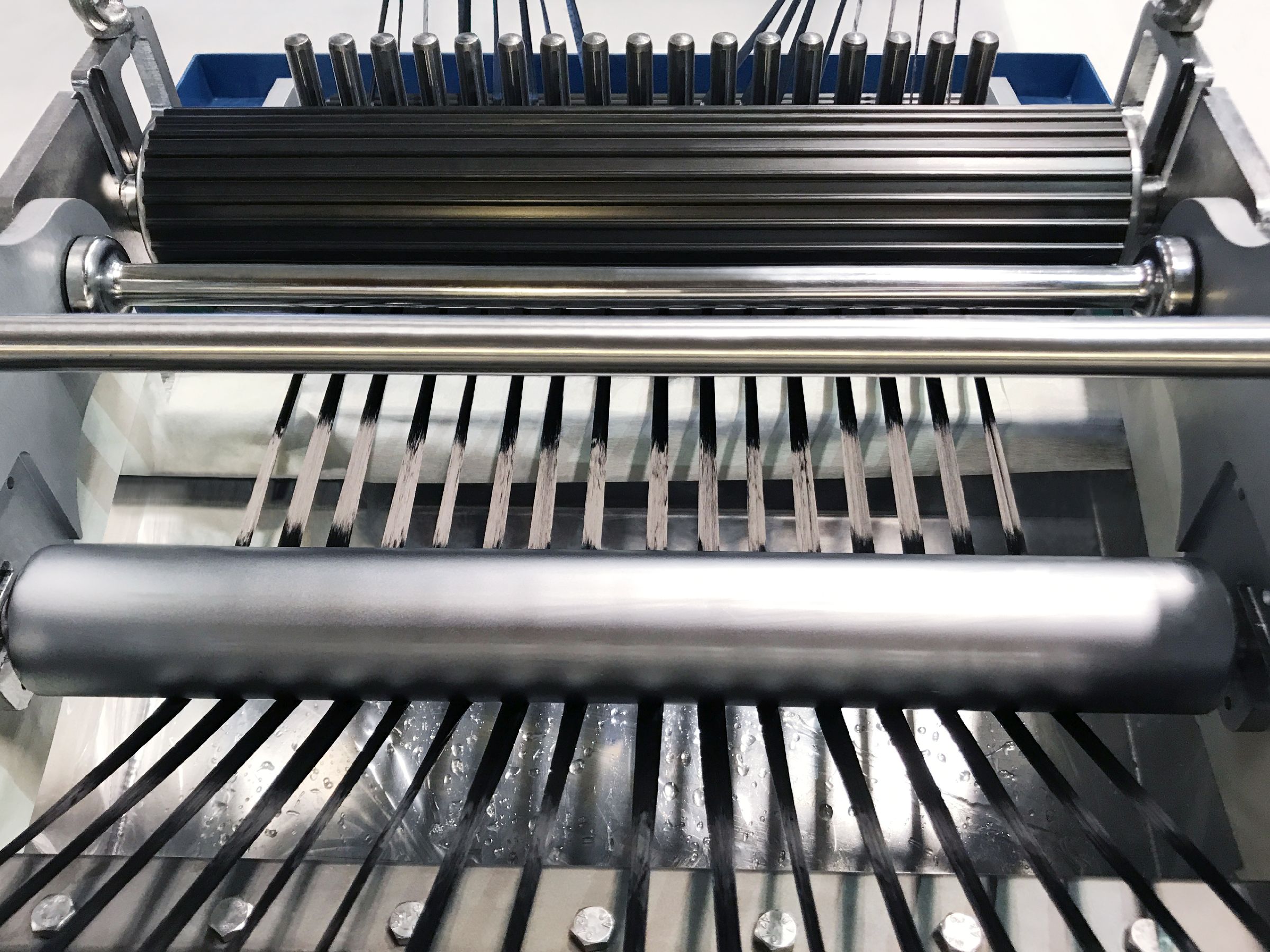
Dynexa maakt gebruik van een nat filamentwikkelproces. (Zie "Composiet uitgaande as klaar voor testgrond in auto's.)" Een belangrijke stap is het opnemen van hars, waarbij de droge vezel op een verdichtingsrol wordt geleid die uit het harsbad oprolt. Tegen de verdichtingsrol zit een rakel die de hoeveelheid hars bepaalt die moet worden gecombineerd met het droge filament voordat het wordt gewikkeld. "Als we te veel hars opnemen, kunnen we de gespecificeerde buisdiameter overschrijden", zegt Koppenberg, "maar met te weinig hars lopen we het risico onder de minimaal toegestane diameter te vallen."
“Zonder meten weet je pas de uiteindelijke diameter na uitharding, als alle waarde is geïnvesteerd”, merkt hij op. “Dus de operator moet de machine stoppen, het onderdeel meten, opschrijven en dan opnieuw starten. Door jarenlange ervaring weten we wat de dikte van het laminaat moet zijn in elke fase van het wikkelen. De operator vergelijkt dus de meting en stelt de rakel zo nodig af om de harsopname te corrigeren, maar dit is erg handmatig en is afhankelijk van de vaardigheid en ervaring van de operator."
Om dit te digitaliseren sprak Dynexa met talloze laser- en camerafabrikanten. "Ze zouden zeggen:'we hebben de oplossing', maar dan kon niemand het laten werken", merkt Koppenberg op. Het team van de Universiteit van Darmstadt maakte het gebruik van een camera echter mogelijk door de correcties uit te zoeken die nodig waren vanwege bepaalde fysieke factoren, zoals lichtreflectie van het natte oppervlak. "Nu hebben we de wikkelmachine aangesloten op het meetapparaat, dat op een zeer gestandaardiseerde manier werkt", voegt hij eraan toe.
Het team ontwikkelde een database met correctietabellen en beslissingsalgoritmen waarmee de filamentwikkelmachine weet wat het doel moet zijn voor elke fase van de specifieke buis die wordt gewikkeld. "Als de invoer van het meetapparaat laat zien dat de harsopname niet is waar hij zou moeten zijn", legt Koppenberg uit, "reageert de filamentwikkelmachine door de rakel aan te passen om het weer in de specificaties te brengen zonder te stoppen met opwinden om te meten."
Elke wikkelmachine heeft nu het digitale meetsysteem, en een ethernetkaart. "Het duurste onderdeel was het installeren en leiden van de kabels naar de server", grapt Koppenberg, "maar nu kunnen we met elke machine praten en alle gegevens verzamelen." En er is nog een voordeel. “Vroeger programmeerden operators aan de machines, maar toen we ze eenmaal op de server hadden aangesloten, kunnen we programmeren op elke desktop- of laptopcomputer. Dit heeft de uitvaltijd verder verminderd en een ander productieknelpunt weggenomen.”
Dankzij deze eerste digitale stap heeft Dynexa haar procesbeheersing, kwaliteit en efficiëntie kunnen verbeteren, waardoor ze kosteneffectiever is geworden. Het heeft ook geleid tot verdere transformatie.
Veranderende paradigma's voor composieten
"We bevinden ons in een stapsgewijs proces om onze klanten een nieuw ecosysteem te bieden", zegt Matthias Bruckhoff, hoofd verkoop en marketing bij Dynexa. Hij geeft een voorbeeld:“In Amazon kun je zien wat je wanneer hebt gekocht en nieuwe producten voorgesteld. Vroeger namen we de eisen van de klant en reageerden we binnen een paar dagen met behulp van onze berekeningen en engineeringtools. Dit komt nu online. Onze klanten zullen producten bekijken en binnen enkele minuten berekenen wat ze nodig hebben, wat ze kosten en wat ze leveren. Dit is niet nieuw, maar het is voor onze branche. Net zoals we onze machinebedieners hebben vrijgemaakt om zich te concentreren op meer machines en taken op een hoger niveau, zullen we ons technische team nu vrijmaken om zich te concentreren op meer gespecialiseerde en geavanceerde producten."
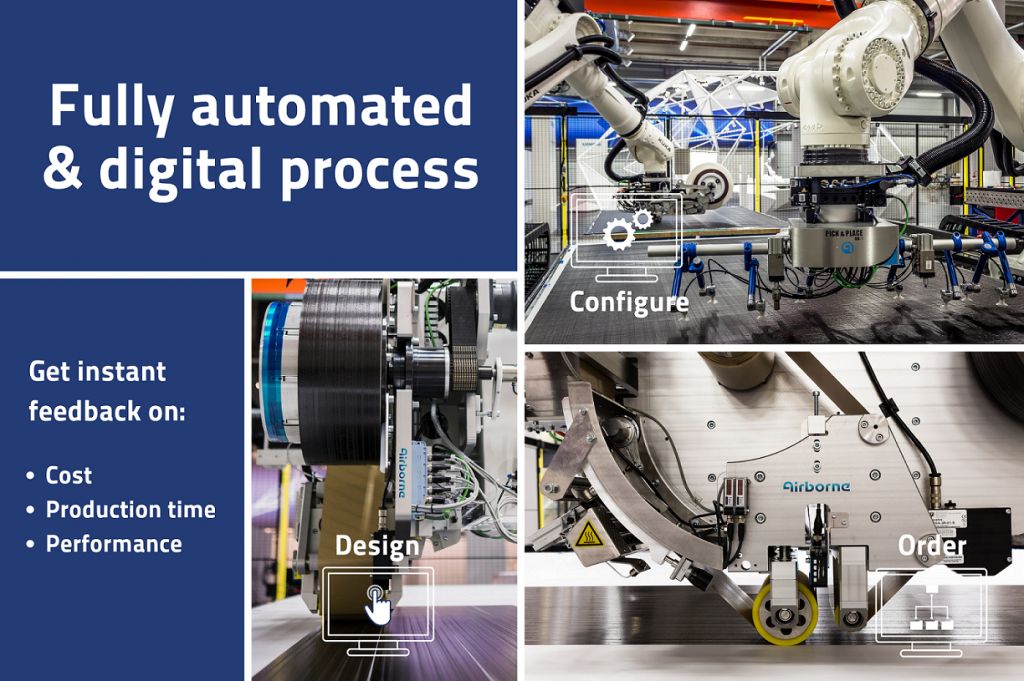
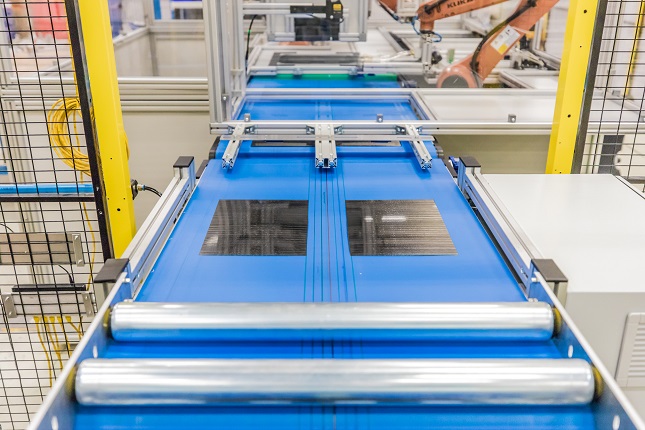
Airborne (Den Haag, Nederland) lanceerde in september 2019 zijn On-demand Manufacturing Portal voor geautomatiseerde productie van composieten (zie "Airborne lanceert portal voor composietprinten"). Met behulp van deze tool voeren klanten ontwerpen in op het webgebaseerde platform. Het systeem maakt vervolgens on-the-fly de machinecode aan en bepaalt de productieduur en -kosten. Producten kunnen vervolgens worden aangepast en, eenmaal besteld, geproduceerd in een geautomatiseerde productiecel. Het portaal werd gelanceerd met behulp van Airborne's Automated Laminating Cell (ALC) om thermoset prepreg te verwerken. Het zal worden uitgebreid naar andere processen, bijvoorbeeld de productielijn voor hoogvolume thermoplastische composieten (TPC) die is ontwikkeld voor de Specialties-divisie van SABIC (Riyadh, Saoedi-Arabië).
"Dit portaal is een belangrijke bouwsteen van hoe we de digitale toekomst van composietproductie zien", zegt Marcus Kremers, Chief Technology Officer bij Airborne. “Vijf jaar geleden zijn we overgestapt van een bedrijfsmodel voor de productie van onderdelen naar het helpen van klanten met automatisering en digitalisering. We ontwikkelen een portfolio van oplossingen die het klanten gemakkelijk maken om met composieten te bouwen.” Dit portfolio omvat de ALC, geautomatiseerde honingraatoppotten, geautomatiseerde ply-kitting en de hoogvolumelijn met TPC-tapes, de Digital Composites Manufacturing Line (DCML) genoemd door SABIC en Falcon door Airborne. Dit laatste is een voorbeeld van de maatwerkoplossingen van Airborne. "We integreren onze kennis van composietmaterialen en onderdelenproductie in deze geautomatiseerde systemen, zodat de klanten geen specialisten hoeven te zijn", zegt Kremers.
Airborne heeft drie businessmodellen:koop de automatisering, huur hem of laat hem bij Airborne werken via manufacturing as a service (MaaS). Geautomatiseerde luchtcellen hebben sensoren en inline inspectiesystemen die waarschuwingen genereren op basis van een database met defecten en toleranties die door de klant zijn gedefinieerd. "De Falcon-lijn heeft zeer lage toleranties voor visuele kwaliteitsgebreken", merkt Kremers op, "maar onze automatisering voor de lucht- en ruimtevaart wordt meer gedreven door structurele toleranties. We zijn ook voortdurend bezig met het verbeteren van onze technologieën om zelflerend en zelfaanpassend te zijn. Onze volgende softwareversie voor het leggen van ALC-tapes zal bijvoorbeeld in staat zijn om defecten te identificeren en het productieprogramma direct aan te passen.”
Op de langere termijn is de visie om het on-demand portaal uit te breiden om de productiecapaciteit voor composietonderdelen te verzamelen, verdeeld over meerdere bedrijven en regio's. Kremers citeert Protolabs (Maple Plains, Minn., V.S.), dat in slechts een dag on-demand spuitgegoten, plaatwerk, CNC-gefreesde of 3D-geprinte prototypes levert. Evenzo biedt de online app van Plyable (Oxford, V.K.) matrijzen voor het vervaardigen van composieten, met materialen variërend van polyurethaanplaat tot staal, inclusief composiet en 3D-geprinte gereedschappen. “Dat is een andere manier om de waardeketen in te richten”, zegt Kremers. "We maken de machines en software die dit mogelijk maken voor composietonderdelen."
AZL Aachen streeft dit doel ook na met zijn Ultra-Fast Consolidator Machine, ontwikkeld om in minder dan vijf seconden meerlaagse TPC-laminaten te produceren. Het werd in 2019 op de markt gebracht en maakt gebruik van Conbility (Aken, Duitsland) robot-, laserondersteunde AFP-applicators en 25 millimeter brede UD-tapes, evenals een stukstroomprincipe - state-of-the-art in de high-speed printindustrie - om TPC-laminaten te produceren, eenvoudig geplakt of volledig geconsolideerd, in verschillende diktes, met lokale versterkingen. "Onze visie is om schaalbare machines te bieden die online platforms mogelijk maken", zegt Emonts. “Lijnen kunnen meerdere stations hebben, elk met meerdere AFP-applicators. De klant voert de vereisten in en krijgt opties voor plybook, kosten en levering. Eenmaal voltooid, communiceren de applicators met elkaar om de productie te organiseren, niet met de operator. Dit is een volledig intelligente productie van composieten op maat.”
Automatisering van de automatisering
De belangrijkste focus van de ZLP is de geautomatiseerde productie van CFRP-structuren. "Automatisering voor slechts één onderdeel of programma is moeilijk te rechtvaardigen", merkt Florian Krebs, ZLP-teamleider voor flexibele automatisering op. “Als je echter verder gaat dan taakspecifieke machines naar een automatiseringsplatform dat herconfigureerbaar is met bijna geen extra instellingen, heb je nu een zakelijke oplossing. Hoe flexibeler het platform, hoe sneller het rendement op de investering.”
De werkcel die wordt getoond in de openingsafbeeldingen is ontworpen als onderdeel van het ZLP-project PROTEC NSR om een familie van onderdelen te bouwen die dezelfde procesroute volgt:pick-and-place lay-up van droge non-crimp stoffen en harsinfusie (zie online zijbalk "Nee businesscase voor het aanleren van robots"). "Dit proces is ontworpen voor het achterste drukschot van de Airbus A350, maar je zou op deze lijn ook een romppaneel of een vleugelkap kunnen maken omdat de stappen vergelijkbaar zijn", zegt Krebs.
"Om flexibele automatiseringsplatforms te bereiken, zijn bepaalde technologiestenen nodig, waaronder algoritmen voor de robots, evenals sensoren en het begrijpen van de gegevens die ze produceren", zegt Kupke. "De PROTEC NSR-productielijn is bijvoorbeeld ontworpen met het oog op maximale modulariteit - alle modules zijn onderling met elkaar verbonden om een zelfconfigurerend, -corrigerend en -optimaliserend systeem te demonstreren, schaalbaar in omvang en complexiteit."
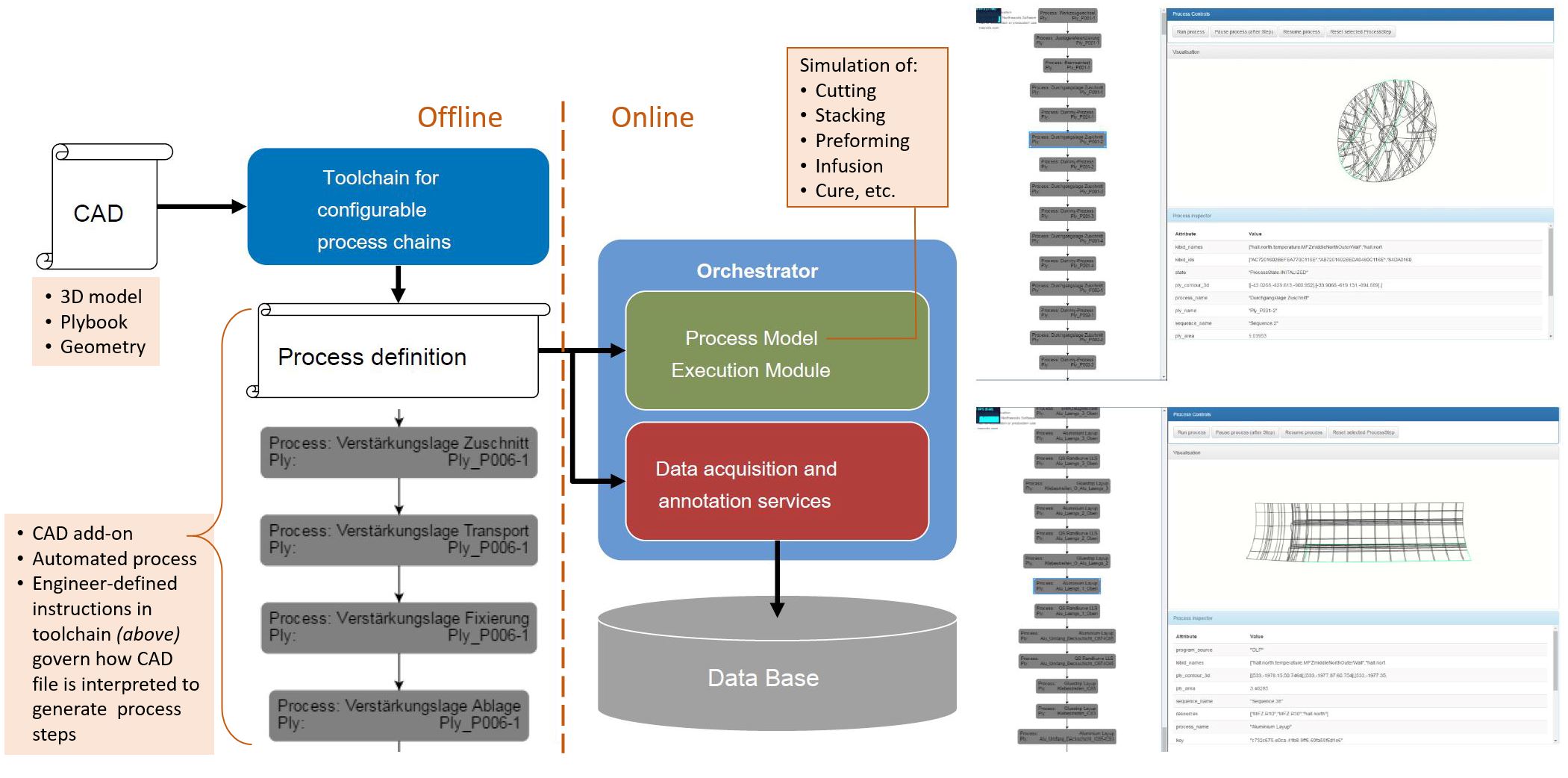
Hij legt de modules uit zoals getoond in Fig. 5, waaronder CAD-model, procesdefinitie, procesmodel dat simulatie en uitvoering van het proces mogelijk maakt, fabricage-uitvoeringsmodule, sensoren om gegevens te verkrijgen, software om de gegevens te annoteren en database voor opslag.
“Aan de linkerkant van dit diagram maak je een plan. De uitvoeringsmodule voert dat plan vervolgens uit”, zegt Kupke. “Tijdens de processtappen verkrijgen we data van alle betrokken machines en processen, bijvoorbeeld de snijplotter, de robots, het gebouw (temperatuur, druk, vochtigheid), de camera’s tijdens pick-and-place, etc. We analyseren de data real-time tijdens het proces en ook de verzamelde data automatisch annoteren met meta-data om deze in te voeren in de database, die de basis vormt voor de digitale tweeling van het proces. Het belangrijkste punt van de digitale tweeling is om één centrale repository te hebben, één bron van waarheid. Het CAD-model en de procesdefinitie van elk onderdeel maken deel uit van de enige bron van waarheid.”
Met deze modules op hun plaats werkt de lijn autonoom met een druk op de knop. Uit het CAD-model, het productieplan en de camera's leiden de robots af welk gesneden stuk het volgende is en zoeken het op de tafel (bijvoorbeeld uit 100 andere gesneden stukken). "Ze beslissen hoe ze de grijpers configureren om het op te pakken en in de tooling te leggen, en weten waar ze het moeten plaatsen." Op basis van het productieplan bepalen de robots elk begin-/eindpad voor alle processtappen en weten ze wanneer ze klaar zijn. "Meestal worden deze paden door een mens aangeleerd", merkt Kupke op. “Maar in ons systeem wordt elk pad automatisch, botsingsvrij en in realtime gedefinieerd. Als u het CAD-model of de procesdefinitie wijzigt, passen de robots zich aan zonder extra leerinspanningen. Maar wat als je het onderdeel helemaal verandert? Met dit soort automatisering zou je die verandering heel snel kunnen doorvoeren. Dit is de weg naar flexibel produceren. Het is onze rol bij ZLP om deze weg te effenen door technologische bouwstenen te ontwikkelen en aan elkaar te koppelen.”
Kans en ontologie
De COVID-19-pandemie heeft de waarde van flexibele productie duidelijk gemaakt. Het heeft ook een steeds onvoorspelbare zakelijke omgeving gecreëerd. "In de afgelopen twee tot drie jaar is alles vluchtiger geworden", merkt Dynexa's Bruckhoff op. “Onze klanten willen heel snel antwoorden, om zo op hun klant te kunnen reageren. Door ons nieuwe online ecosysteem aan te bieden, maken we de hele supply chain concurrerender.”
Dit wordt goed erkend door de luchtvaartindustrie. "We hebben een digitale basis nodig voor productielijnen en hele sites die zowel horizontale als verticale integratie mogelijk maakt", zegt Marc Fette, voorzitter van de technische afdeling Aerospace Technologies van de VDI - The German Association for Engineers en COO voor Composite Technology Center (CTC, Stade, Duitsland), een R&T-dochteronderneming van Airbus. CTC-projecten in Composites 4.0 omvatten het volgen van materiaal en activa, collaboratieve robots, geavanceerde procesketens en meer. Maar Fette benadrukt de noodzaak van ontologie - een terminologie en gemeenschappelijk protocol voor digitale communicatie en gegevensuitwisseling. (Zie de online zijbalk "Composites 4.0-architectuur en ontologie".)
"Je hebt een holistisch netwerk nodig voor alle machines en productiesystemen in een bepaalde fabriek", legt hij uit, "maar dit moet zich ook uitstrekken tot de hele waardecreatieketen, inclusief disciplines zoals engineering, inkoop, logistiek en materialen en procescertificering , aan de ene kant. Anderzijds moeten alle stakeholders, zoals leveranciers, worden meegewogen en betrokken bij dit veranderingsproces. We zien veel pilootprojecten, maar als je in detail kijkt, ontbreekt het nog aan een strategie voor een holistische aanpak per bedrijf of productieketen.”
Hij vervolgt:“We hebben een zeer groot, wereldwijd netwerk van leveranciers en zij hebben dezelfde eisen om als een digitaal verbonden supply chain te opereren. De meeste van onze leveranciers zijn KMO's die werken voor zowel vliegtuigfabrikanten, Airbus als Boeing. Als er geen discussie is over een gemeenschappelijke standaard, dan geef je deze uitdagingen door aan de leveranciers. Ze kunnen het zich hoogstwaarschijnlijk niet veroorloven om te voldoen aan twee sets van verschillende standaarden voor al hun machines, inclusief documentatie, het beoordelen van gegevens, cyberbeveiliging, enz.”
Fette geeft toe dat dit grote ideeën zijn en zegt dat vliegtuig-OEM's plannen maken om deze uitdagingen aan te gaan. "Maar er zijn veel van dit soort obstakels, en het is echt complex, waarbij niet alleen technologie betrokken is, maar ook sociale, economische, ergonomische en juridische kwesties - het is mentaal een veranderingsproces. We staan nog maar aan het begin. Maar om te slagen, moeten we begrijpen dat deze nieuwe systemen afhankelijk zijn van mensen en dat deze mensen aan boord moeten zijn, niet alleen bij OEM's, maar in het hele wereldwijde netwerk."
“Markets are becoming more fragmented across all industries and everyone is facing a paradigm shift,” notes ZLP’s Krebs. “Many people don’t see that as an opportunity,” adds Kupke, also of ZLP. But those who do see that opportunity envision democratized access to composites enabled by Composites 4.0, and with that, a much broader market, including applications that we are only beginning to conceive.
Hars
- Het optimaliseren van digitale transformatie in CPG-productie
- Strategie voor digitale transformatie vereist een nieuwe benadering van talent
- Datagestuurde digitale transformatie stuwt Airbus naar nieuwe hoogten
- Hoe verandert het nieuwe tijdperk van digitale transformatie de nutssector?
- Evonik bouwt nieuwe productiefaciliteit PA12
- Plan voor succes in digitale transformatie
- Wat is digitale transformatie in productie?
- 7 aanjagers van digitale transformatie
- Digitale transformatie-uitdagingen in de maakindustrie
- Transformatie van digitale productie:een goede voornemen voor het nieuwe jaar
- GE Digital:een doorlopend digitale transformatietraject