Een totaal productief onderhoudsplan (TPM) implementeren
De succesvolle en duurzame implementatie van Total Productive Maintenance (ook bekend als TPM) zou een belangrijke zorg moeten zijn voor elke gewetensvolle fabrieksmanager of productieleider. TPM leidt tot minder uitvaltijd, minder stops en storingen en een kleinere kans dat producten tijdens het fabricageproces kwaliteitsgebreken vertonen.
Waarom is TPM zo'n effectief hulpmiddel? Kortom, want bekwame operators die een actieve rol spelen bij het inspecteren en onderhouden van hun eigen apparatuur, zullen altijd bijdragen aan een betere productie en betrouwbaarheid van de apparatuur.
In de loop der jaren hebben onderzoeken de positieve correlatie tussen de implementatie van een TPM-programma en de algehele productieprestaties bevestigd. Sommige bevindingen geven aan dat een bedrijf verloren productie met ongeveer 20% kan verminderen door een volledig productief onderhoudsplan uit te voeren. Toch rijst er een belangrijke vraag:hoe kan een bedrijf TPM effectief implementeren ? De volgende informatie zal op die vraag ingaan.
Wilt u geld besparen op onderhoudskosten?
Hier vindt u meer nuttige bronnen en onderzoekspapers.
Wat is het totale productieve onderhoud
Ter vergelijking:elk TPM-programma omvat minimaal 8 kernconcepten die een grote rol spelen bij het bepalen van het uiteindelijke succes van het initiatief. Deze 8 concepten zijn:
-
Autonoom onderhoud
Dit fundamentele element van TPM is gericht op het trainen en in staat stellen van onderhoudspersoneel, zoals machinebedieners, om het routineonderhoudsbeheer zelf uit te voeren. -
Gerichte verbetering
Deze pijler van TPM verwijst naar proactieve onderhoudstechnieken:een huidig proces op een holistische manier onderzoeken en manieren identificeren om het te verbeteren. -
Gepland onderhoud
Een gepland onderhoudsprogramma maakt gebruik van historische downtime-gegevens en voorspellende analyses om belangrijke onderhoudstaken te plannen rond waarschijnlijke uitvalpercentages of verwachte inactiviteitstijden. -
Kwaliteitsbehoud
Het kwaliteitsonderhoudsproces is ontworpen om ervoor te zorgen dat de daadwerkelijke onderhoudstaken die worden uitgevoerd, op efficiënte wijze de algemene doelstellingen van foutdetectie, defectpreventie en kwaliteitsborging bereiken. -
Vroeg apparatuurbeheer
Door gebruik te maken van feedback van operators met praktische ervaring, zorgt vroegtijdig apparatuurbeheer ervoor dat het ontwerp van nieuwe apparatuur de levensduur, toegankelijkheid en productiviteit van de machine optimaliseert. -
Training
Elk TPM-programma moet een element van training en opleiding bevatten voor zowel operators als managers. -
Veiligheid en gezondheid
Alle TPM-processen moeten rekening houden met veiligheids- en gezondheidsfactoren om een veilige werkomgeving voor operators en andere werknemers te bevorderen. -
TPM-georiënteerd beheer
Afgezien van puur mechanische overwegingen, zal een goed ontworpen TPM-programma ook rekening houden met administratieve functies zoals orderverwerking en planningsbeheer, en zoeken naar manieren om deze te verbeteren ter ondersteuning van de productievloer.
Hoe TPM te implementeren
Hoewel een TPM-programma moet worden aangepast aan specifieke bedrijfsbehoeften en omstandigheden, zijn er 7 basisstappen om TPM te implementeren, zoals hieronder vermeld:
1. Kondig plannen voor TPM-implementatie aan
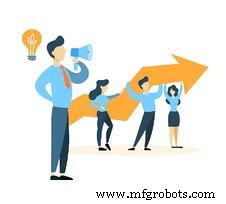
2. Identificeer een gebied voor een pilot TPM-programma
U kunt zich concentreren op een apparaat dat het gemakkelijkst te verbeteren is, of een productiegebied dat problematisch is gebleken en moet worden gerepareerd om de winstgevendheid snel te verbeteren. Identificeer in deze eerste fase van het TPM-proces doelen die SMART zijn:specifiek, meetbaar, haalbaar, realistisch en getimed.3. Concentreer u op het herstellen van gerichte apparatuur in uitstekende werkconditie
Zodra uw proefgebied is geïdentificeerd, legt u een basisstandaard vast voor de huidige productiviteit. Organiseer en definieer uw plan voor TPM-implementatie . Gebruik de 5S-methodiek (Sort, Set, Shine, Standardize, Sustain). Richt u eerst op het uitvoeren van een autonoom onderhoudsprogramma en geef waar nodig training aan operators van apparatuur. Net zoals een auto-eigenaar een aanzienlijk bedrag kan besparen op reparatiekosten door basis routine-onderhoud uit te voeren, zo kunnen ook bedrijven de levensduur van de machine verlengen en mechanische problemen vroegtijdig opsporen door hun machinisten regelmatig deel te laten nemen aan basisonderhoudsprocedures4. Begin met het meten van de algehele effectiviteit van apparatuur (OEE)
Hoe u ook besluit om OEE bij te houden, het is absoluut noodzakelijk dat ongeplande stoptijden worden gedocumenteerd en voor elk voorval een reden wordt gegeven. Geef een categorie op voor "onbekende oorzaak" of "niet-toegewezen stoptijd" voor gevallen waarin de operator niet zeker is van de oorzaak van de stop. Na verloop van tijd zal dit u helpen om eerst te identificeren belangrijke verliesoorzaken, die op hun beurt leiden tot stap #5: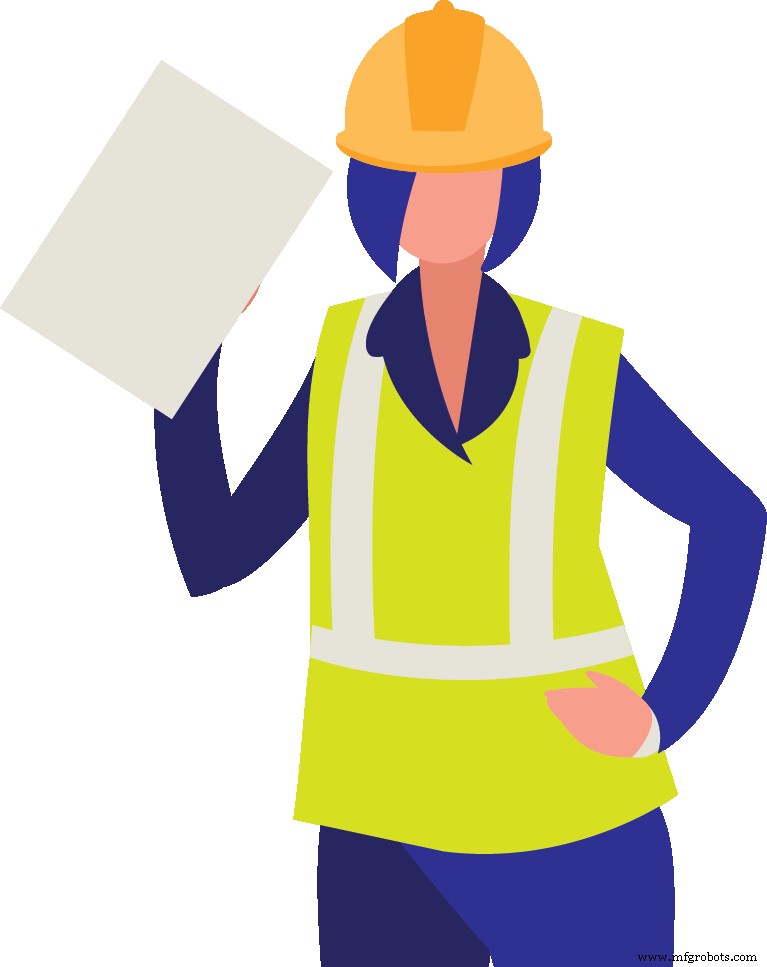
5. Oorzaken van groot verlies aanpakken
In deze stap moet u een multifunctioneel team van ongeveer 4 tot 6 medewerkers aanwijzen om één belangrijke oorzaak van downtime te onderzoeken. . Dit team zal een plan maken om de oorzaak van het verlies weg te nemen en een geplande stoptijd plannen om dit initiatief uit te voeren. Als uw grote verliezen bijvoorbeeld het gevolg zijn van frequente vulleropstoppingen, zal dit team de huidige operatorprocessen en reparatieopties onderzoeken, een plan maken om de opstoppingen te stoppen en vervolgens tijd plannen om het plan in actie te brengen. Zodra de aangewezen actie is voltooid, meten ze de OEE in de toekomst en herstarten ze het proces indien nodig.
6. Proactief onderhoud implementeren
In deze stap ligt je focus op het voorkomen van storingen of stoptijden. Identificeer belangrijke "pijnpunten" die apparatuurstoringen kunnen veroorzaken en maak een schema voor preventief onderhoud met regelmatige tussenpozen. Stel ten slotte een feedbackproces in waarmee u de effectiviteit van uw programma voortdurend kunt controleren. Dit feedbacksysteem kan onderhoudslogboeken, maandelijkse of tweemaandelijkse audits en gegevensverzameling van thermografie en/of trillingsanalyse omvatten.
7. Implementeer zo nodig specifieke TPM-concepten
Zo moet vroeg materieelbeheer een rol gaan spelen bij het ontwerpen en/of installeren van nieuwe machines voor de productievloer. Misschien moet het ontwerp van nieuwe apparatuur worden geoptimaliseerd met verbeterde toegankelijkheid, eenvoudigere reinigings- of smeerprocedures of de toevoeging van veiligheidsvoorzieningen. Aan de andere kant, als er inkoopproblemen zijn of vertragingen bij het verwerken van werkorders, moet u deze administratieve knelpunten zo snel mogelijk aanpakken.TPM benutten om onderhoudsbeheer te verbeteren
Totaal productief onderhoud is een belangrijk element om productieverliezen door uitvaltijd te verminderen. Een effectief TPM-programma kan werknemers in staat stellen proactieve maatregelen te nemen voor het onderhoud van vitale machines; hierdoor zal productieapparatuur een langere functionele levensduur hebben. TPM-implementatie helpt ook om kwaliteitsgebreken en suboptimale looptijden te verminderen.
Er zijn veel tools op de markt beschikbaar, zoals Enterprise Asset Management-platforms en gerelateerde programma's, die bedrijven kunnen helpen bij de implementatie van TPM. In de uiteindelijke analyse, hoewel een volledig productief onderhoudsplan enige inspanning vereist voor een goed ontwerp en uitvoering, zijn de voordelen hiervan de investering zeker waard!
Onderhoud en reparatie van apparatuur
- Uw TPM-plan in daden omzetten:een stapsgewijze handleiding
- Hoe u het onderhoud proactief kunt houden
- Totaal productief onderhoud implementeren
- Vodcast:een inleiding op totaal productief onderhoud
- Een elektrisch onderhoudsprogramma samenstellen
- Unilever breidt Total Productive Maintenance-programma uit met behulp van Informance
- Hoe fabrieksmanagers regelmatig machineonderhoud kunnen plannen
- Totaal productief onderhoud en industrieel IoT
- Hoe Reliability Centered Maintenance (RCM) te implementeren
- Totaal productief onderhoud:een prestatiehefboom?
- Inzicht in totaal productief onderhoud (TPM)