Een handleiding voor onderhoudsmanagers voor het maken en gebruiken van FMEA's
Een wrede ransomware-aanval trof de stad Atlanta in maart 2018. Het werd een van de duurste inbreuken in het afgelopen decennium. De openbare diensten werden verstoord. Afdelingen werden gedwongen om het essentiële papierwerk met de hand te doen. En het kostte het stadsbestuur $ 17 miljoen.
Toen het stof was neergedaald, was één ding duidelijk:de stad was niet voorbereid op deze ramp. Een audit die twee maanden voor de inbreuk werd uitgevoerd, vond 2.000 kwetsbaarheden in het IT-systeem van de stad. Het was een goede stap, maar het was too little, too late.
Wat er in Atlanta is gebeurd, is een waarschuwend verhaal met één grote les:risico kan nooit worden uitgesloten, maar het kan worden beheerd. Dit geldt met name voor het onderhoud. Uitval van apparatuur is onvermijdelijk. Maar weten hoe u de kans op mislukking kunt verkleinen en hoe u moet reageren als het gebeurt, is van cruciaal belang voor succes.
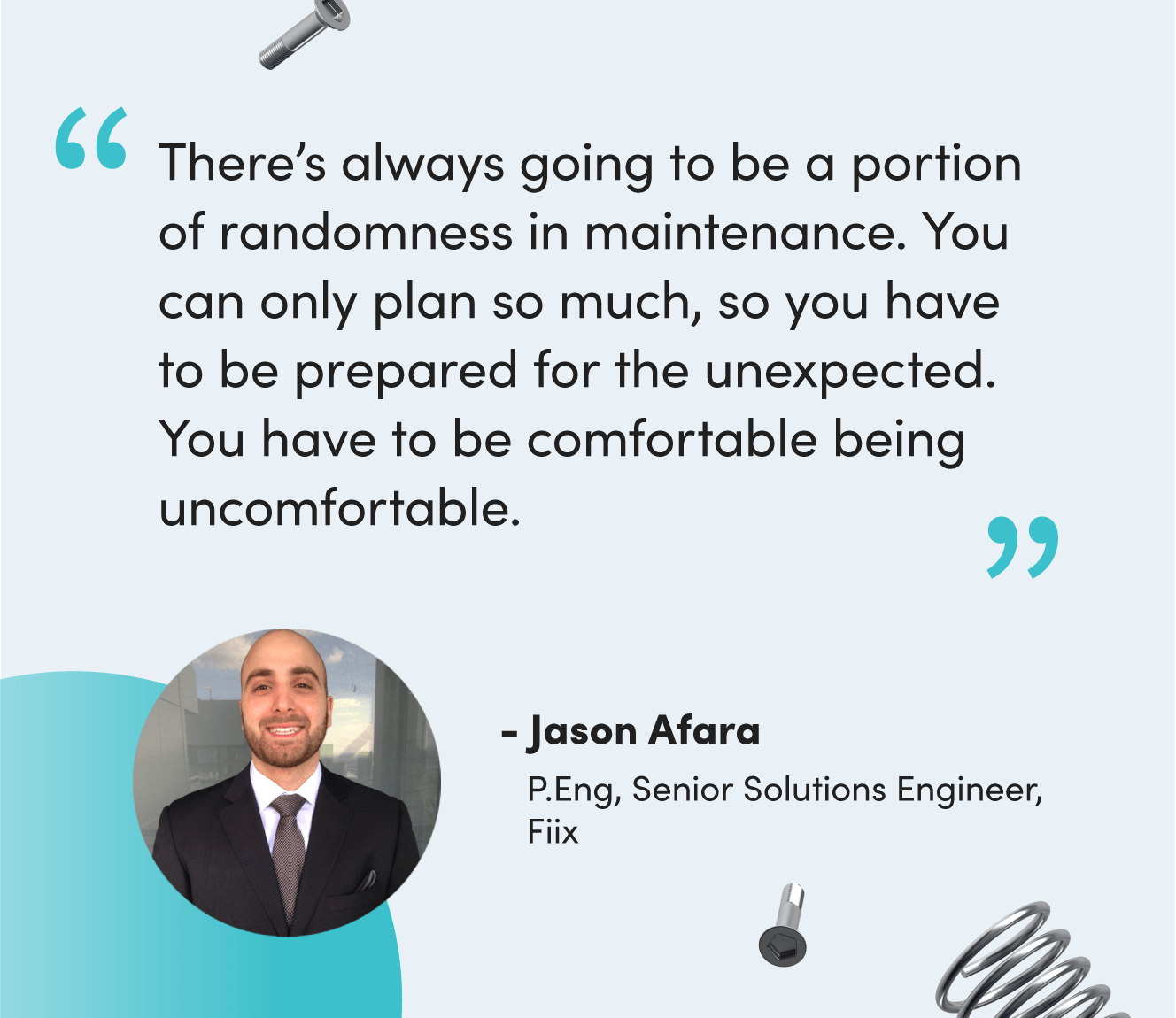
Een storingsmodus en effectenanalyse (FMEA) is een hulpmiddel om storingen te begrijpen en erop te anticiperen, zodat u de impact ervan kunt beperken. In dit artikel leer je:
- Wat een FMEA is
- De verschillende soorten FMEA's
- Een FMEA maken
- En hoe onderhoudsteams een FMEA kunnen gebruiken
Wat is een FMEA?
Een storingsmodus en effectenanalyse, of FMEA, identificeert en documenteert alle manieren waarop een apparaat kan falen en de mogelijke impact van deze storingen. Het schetst:
- Foutmodi voor afzonderlijke componenten
- De gevolgen van falen op productiviteit en veiligheid
- Een plan om deze problemen te voorkomen of erop te reageren
Het bouwen van FMEA's is een belangrijk onderdeel van op betrouwbaarheid gericht onderhoud (RCM).
Er zijn drie hoofddoelen van een FMEA:
- Voorkom toekomstige storingen door de kans op veelvoorkomende en kritieke storingen te verkleinen met behulp van gepland onderhoud en standaard operationele procedures
- Verkort de reactietijden, verminder de uitvaltijd en verbeter de gezondheid en veiligheid wanneer activa defect raken
- Geef prioriteit aan preventief en correctief onderhoud in niet-noodsituaties
Wat zijn de verschillende soorten FMEA?
FMEA's kunnen worden onderverdeeld in subtypes op basis van het type risico dat ze beoordelen en de impact die ze hebben. Hier is een kort overzicht van elk type FMEA:
- FFMEA (functionele storingsmodus en effectenanalyse) :Een FFMEA analyseert de risico's die het functioneren van een systeem beïnvloeden. Het doel van een FFMEA (ook wel een systeemfoutmodus en effectenanalyse genoemd) is om deze fouten te voorkomen voordat ze zich voordoen.
- DFMEA (ontwerpfoutmodus en effectenanalyse) :Een DFMEA beoordeelt de risico's van een asset in de ontwerpfase. Het doel van deze analyse is om potentiële problemen met een activum te vinden en te corrigeren voordat het wordt ingezet om de betrouwbaarheid te vergroten, de hoeveelheid onderhoud te verminderen en de levensduur van het activum te verlengen.
- PFMEA (procesfoutmodus en effectenanalyse) :Een PFMEA zoekt mogelijke storingen binnen een proces op. Het verschil tussen een PFMEA en andere soorten FMEA's is dat het zich richt op wat er mis kan gaan tijdens de werking en het onderhoud van een systeem.
- FMECA (foutmodus, effecten en kritische analyse) :Een FMECA (of kriticiteitsanalyse) analyseert zowel faalwijzen als het risiconiveau dat met die faalwijzen gepaard gaat.
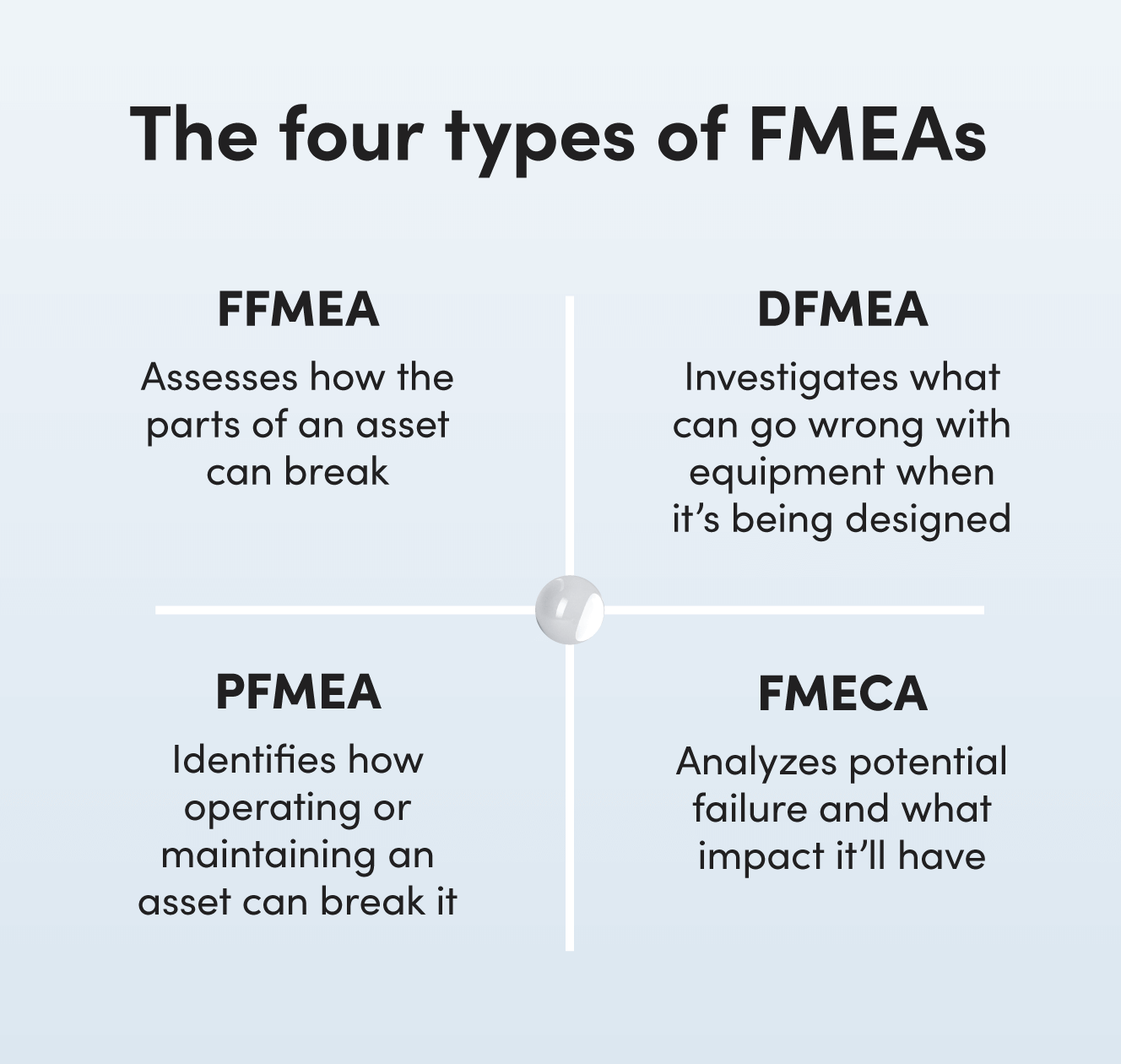
Wat is het verschil tussen een storingsmodus en een storingscode?
Een storingsmodus is een fout of defect waardoor een systeem niet goed werkt. Een voorbeeld van een storingsmodus op een transportband met variabele snelheid kan een vastgelopen lager zijn. Een gebroken lager zorgt ervoor dat de transportband langzamer gaat werken of niet meer werkt.
Een storingscode is een storingsmodus die wordt weergegeven door een alfanumerieke tag. Storingscodes worden vaak gebruikt in CMMS-software als een manier om informatie snel over te brengen en om storingen te sorteren of te rapporteren. Foutcodes worden meestal ondersteund door drie stukken contextuele informatie. Een voorbeeld van een storingscode ziet er als volgt uit:
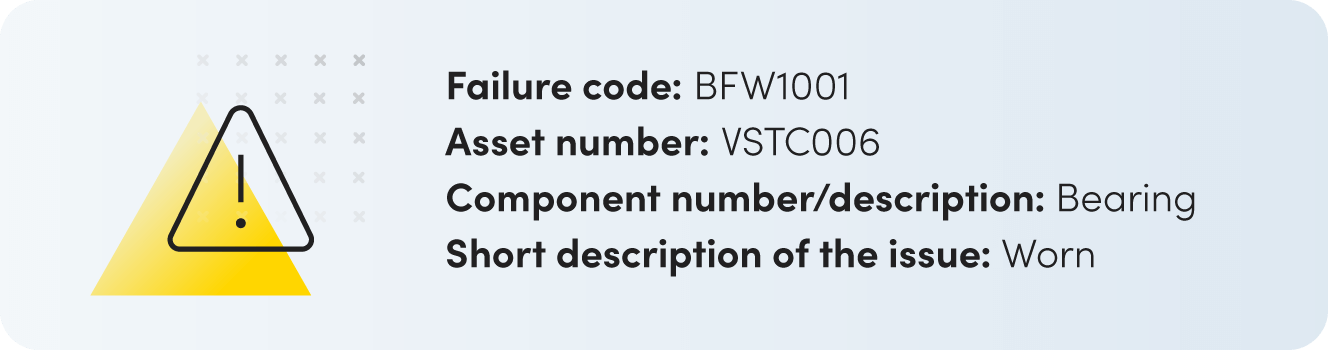
Wat is het verschil tussen FMEA en FRACAS?
Een faalmodus en effectenanalyse schetst mogelijk falen, de oorzaken en de impact ervan. Het is een proces dat mogelijke toekomstige incidenten en hun waarschijnlijke hoofdoorzaken opsomt. Het is een proactieve maatregel.
Een storingsrapportage-, analyse- en corrigerende actiesysteem (FRACAS) is een closed-loop rapportagesysteem dat reeds opgetreden storingen analyseert. Het onderzoekt mislukkingen uit het verleden om erachter te komen waarom ze zijn gebeurd en welke impact ze hadden, zodat ze in de toekomst kunnen worden voorkomen. Het is een reactieve maatregel.
Het maken van FMEA's voor onderhoud is een belangrijk onderdeel van het bouwen van een FRACAS. In feite is het de eerste stap van het proces. Een FMEA is een basislijn voor zowel falen als team- en apparatuurprestaties. Op basis van deze informatie kunt u beslissingen nemen, zoals welke rapporten u moet maken of welke fouten u moet targeten.
Hoe u FMEA's kunt gebruiken voor onderhoud
Er zijn drie manieren waarop onderhoudsteams een storingsmodus en effectanalyse kunnen gebruiken:
- Een preventief onderhoudsschema maken dat de kans op uitval van activa verkleint en middelen optimaliseert
- Als voorbereiding op noodonderhoud, zodat activa snel kunnen worden gerepareerd en uitvaltijd tot een minimum kan worden beperkt
- Voorrang geven aan correctief onderhoud en onderhoudsachterstand
FMEA's gebruiken om een preventief onderhoudsschema op te stellen
Er zijn drie manieren waarop u FMEA's kunt gebruiken om een preventief onderhoudsprogramma van wereldklasse uit te voeren:
- Nieuwe taken voor preventief onderhoud maken
- Geef prioriteit aan preventief onderhoud
- Preventief onderhoud optimaliseren
Download deze sjabloon om een preventief onderhoudsschema te maken
De eerste stap bij het maken van een preventief onderhoudsprogramma is begrijpen welke storingen kunnen optreden en hoe vaak deze optreden. Een FMEA schetst deze informatie. Als er bijvoorbeeld een nieuwe asset wordt ontworpen, stelt een FMEA u in staat om erachter te komen welke PM's nodig zijn om mogelijke faalwijzen te voorkomen en hoe vaak deze moeten worden uitgevoerd. Zo kun je de input in kaart brengen die nodig is voor het maken van nieuwe PM's, inclusief wie aan het werk wordt toegewezen, wat het werk in gang zet, wat het gaat kosten en hoe lang het duurt.
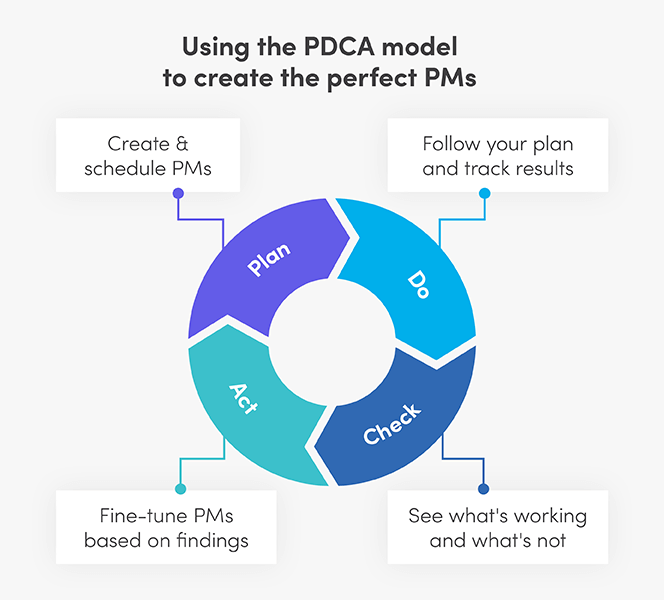
Het succes van uw preventief onderhoudsprogramma hangt af van zowel het aantal storingen dat u ontdekt en stopt als de impact van die storingen. Als u 100 kleine storingen voorkomt, maar niet de vijf of zes storingen opvangt die uw bedrijf miljoenen dollars kosten, is uw programma gebrekkig. Een FMEA heeft alle informatie die je nodig hebt om PM's te prioriteren en de meest waarschijnlijke en storende storingen aan te pakken.
Hoewel FMEA's u een basis geven voor het maken van een preventief onderhoudsschema, zullen uw plannen niet eeuwig duren. Uw operatie verandert voortdurend. Je PM-schema moet mee veranderen. Door werkorder- en reparatiegeschiedenissen te gebruiken om FMEA's bij te werken, kunt u uw planning optimaliseren en gelijke tred houden met andere wijzigingen. Een storingsmodus komt bijvoorbeeld niet zo vaak voor als u had voorspeld. Deze gegevens kunnen ertoe leiden dat u de frequentie van de PM verlaagt die bedoeld is om deze storingsmodus te voorkomen. U kunt die middelen dan gebruiken voor een andere onderhoudstaak.
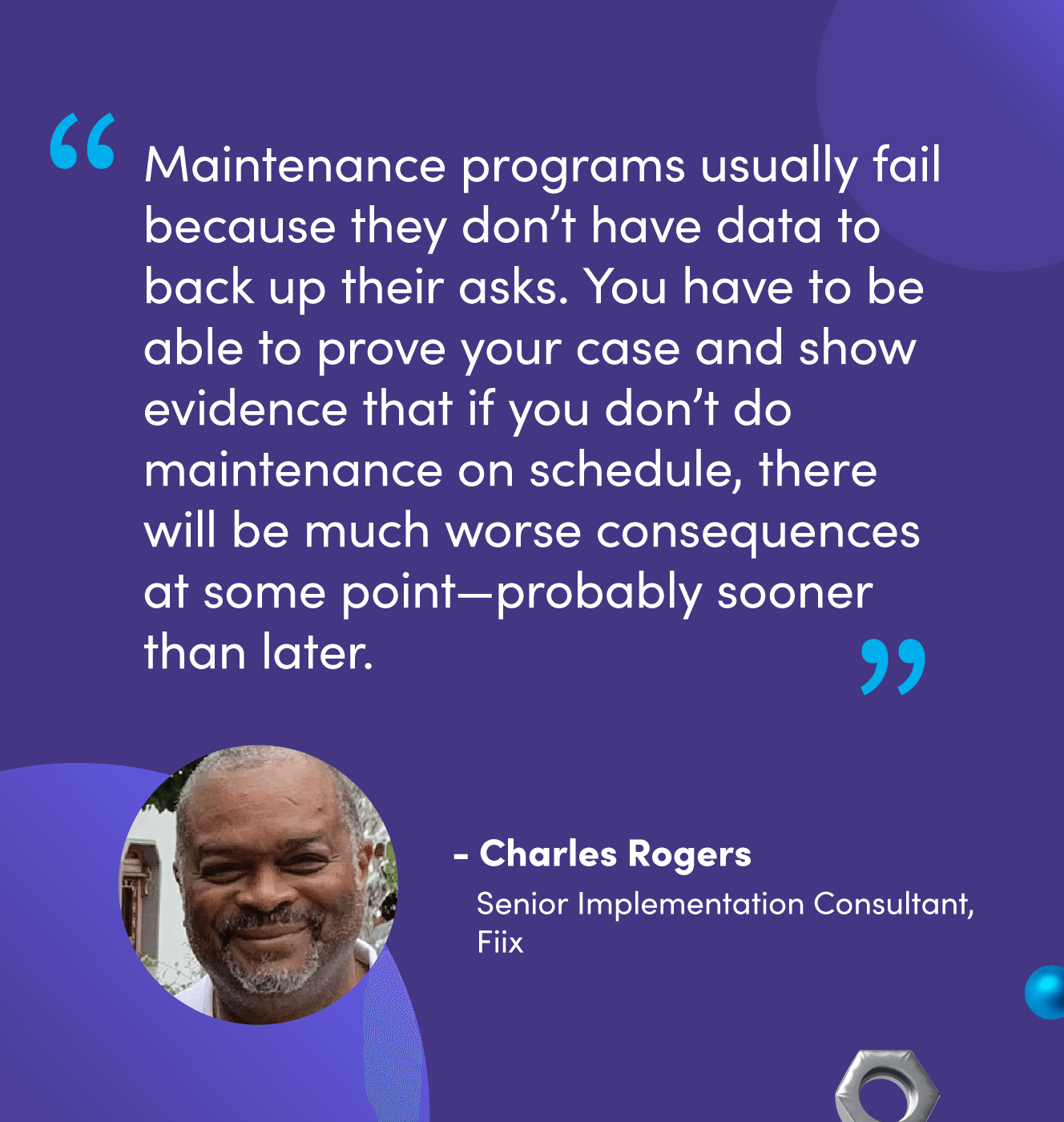
FMEA's gebruiken om voor te bereiden op noodonderhoud
Geen enkele hoeveelheid onderhoud zal een storing volledig elimineren. U kunt het beste plannen voor storingen met een hoog risico en grote impact, zodat uw team ze in één uur kan oplossen in plaats van twee. Een FMEA is een waardevol instrument om deze noodmaatregelen te treffen.
Begin met te kijken naar storingen die de grootste impact hebben en het vaakst voorkomen. Kies uit deze lijst faalwijzen die moeilijk te detecteren zijn. Je zult eindigen met faalwijzen die moeilijk te herkennen zijn en de grootste puinhoop veroorzaken. Stel een noodplan op voor deze storingen.
Uw noodplan moet alle informatie bevatten die de respons- en reparatietijden verkort. Het moet ook rekening houden met gezondheid en veiligheid. Dit kan het volgende omvatten:
- Onderdelen samenstellen om de tijd te besparen die nodig is voor het ophalen van kritieke reserveonderdelen en persoonlijke beschermingsmiddelen (Download een sjabloon voor onderdelenkitten)
- Een gedetailleerde takenlijst maken of tips voor probleemoplossing
- Diagrammen, handleidingen, foto's en andere visuele hulpmiddelen aan werkorders toevoegen
- Een lijst schetsen van technici of aannemers die de reparatie kunnen voltooien
- Een manier vinden om snel met technici te communiceren, zoals CMMS-software
FMEA's gebruiken om prioriteit te geven aan correctief onderhoud en onderhoudsachterstand
Het vroegtijdig detecteren van een storing is nuttig, maar het betekent niets als u geen proces heeft om die storing snel en effectief te corrigeren. Een FMEA helpt je dit proces op te bouwen.
De eerste stap is het identificeren van faalwijzen met een hoge ernstscore (dwz activa die uw bedrijf het meeste kosten als ze defect raken). Er moeten zo snel mogelijk corrigerende maatregelen worden genomen op deze apparatuur. Met deze lijst kunt u trainingsmateriaal en reactieplannen maken, zodat iedereen weet hoe te reageren op mislukkingen.
U kunt een vergelijkbare aanpak hanteren bij het prioriteren van onderhoudsachterstanden, op één extra stap na. Na het rangschikken van uitgesteld werk op ernst, kijk naar overgebleven werk op faalfrequentie. Vergelijk dit met hoe laat het werk is. Als een storingsmodus een frequentie heeft die groter is dan het aantal gemiste inspecties, moet dit werk prioriteit krijgen omdat de kans op falen groter is.
Deze gratis sjabloon helpt u bij het prioriteren van uw onderhoudsachterstand
Hoe maak je een FMEA
Het onderstaande FMEA-sjabloon helpt u risico's in uw bedrijf te herkennen en actie te ondernemen om dit te voorkomen.
Download hier uw eigen FMEA-sjabloon
Maar eerst, hier leest u hoe u gegevens voor uw FMEA kunt krijgen
Goede FMEA's zijn afhankelijk van goede data. Zonder data bouwt u uw onderhoudsprogramma op giswerk en aannames. Maar hoe vind je de benodigde informatie voor een FMEA? De drie onderstaande bronnen geven je een goede basis:
- OEM-richtlijnen:dit is uw startpunt. Deze richtlijnen geven je een basis voor het invullen van een FMEA als je geen andere gegevens hebt.
- Interviews met operators en technici:profiteer van de ervaring van degenen die elke dag met apparatuur werken. Ze geven u inzichten die u nergens anders kunt vinden, bijvoorbeeld als een onderdeel twee keer zoveel smering nodig heeft als gesuggereerd of als de frequentie van een storing is toegenomen omdat de machinespecificaties zijn gewijzigd.
- Werkordergegevens:uw werkorders laten zien hoe apparatuur presteert en zijn een geweldige bron van informatie voor het aanpassen en verbeteren van uw FMEA's. Zoek naar veelvoorkomende storingen, welke acties zijn ondernomen om de hoofdoorzaak te vinden en op te lossen, wat een reparatie vertraagde en hoe gemakkelijk het was om een storing te detecteren.
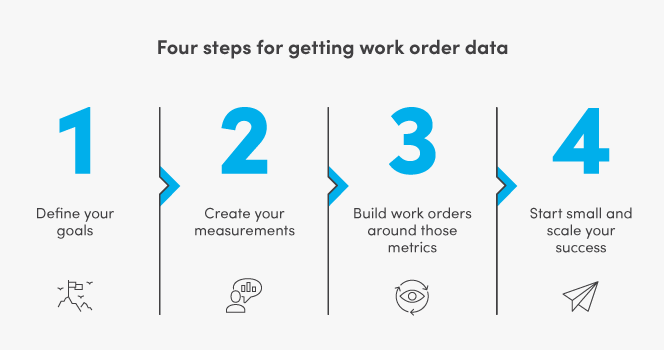
Geen van deze bronnen werkt alleen. Combineer ze om een volledig beeld te krijgen van hoe uw apparatuur werkt, hoe deze kan falen, de impact van een storing en wat er aan gedaan moet worden.
Een FMEA-sjabloon
1. Identificeer activacomponenten
Documenteer elke activacomponent die kan breken of verslechteren. De componenten van een bottellijn kunnen bijvoorbeeld tandwielkasten, motoren, tandwielen, lagers en mondstukken zijn.
Begin met uw meest kritische apparatuur en werk van daaruit verder. Dit is een goed moment om duidelijke naamgevingsconventies en een activahiërarchie te maken als je deze nog niet hebt.
2. Identificeer mogelijke faalwijzen
Het is tijd om te identificeren hoe die componenten kunnen falen. Als een enkel onderdeel meerdere storingsmodi heeft, vermeld dan elke storingsmodus dienovereenkomstig. De faalwijzen van een lager kunnen bijvoorbeeld een verkeerde uitlijning, corrosie of vervuiling zijn.
3. Maak een lijst van mogelijke effecten van falen
Beschrijf het resultaat van een storing en hoe dit de productie en de veiligheid van het personeel beïnvloedt. Een slecht uitgelijnd lager zal bijvoorbeeld een leiding afsluiten totdat deze kan worden vervangen (ongeveer drie uur), met een potentieel verlies van 1.800 eenheden.
4. Ernstscore
Dit is een meting van de impact van een storing op productie en veiligheid. Het wordt gescoord op een schaal van 1 tot 10, waarbij 1 een gebeurtenis met een lage impact is en 10 een gebeurtenis met een hoge impact. Houd rekening met de staat van het activum bij het scoren. Een auto waarvan de band bijvoorbeeld klapt bij lage snelheid, zal kleine stuurproblemen ondervinden, maar een klapband bij hoge snelheid is veel gevaarlijker.
Bereken de ernstscore van een item met deze kritische analysesjabloon
5. Lijst mogelijke oorzaken
Maak een lijst van alle mogelijke redenen waarom een storing kan zijn opgetreden. Ga verder dan een directe oorzaak. Er kan bijvoorbeeld een gecorrodeerd lager optreden omdat de benodigdheden verkeerd waren gelabeld of de instructies onduidelijk waren, wat leidde tot onjuiste smering.
Kom tot op de bodem uit met deze handige (en gratis!) root cause analysis tempalte
6. Verwachte frequentiescore
Dit is een maatstaf voor hoe vaak een storingsmodus voorkomt. Het wordt gescoord op een schaal van 1 tot 10 waarbij 1 staat voor een gebeurtenis die zelden voorkomt en 10 voor een gebeurtenis die zeer vaak voorkomt.
7. Lijst huidige procescontroles
Documenteer alle getroffen maatregelen om een storing te voorkomen of op te sporen. Procescontroles kunnen wekelijkse preventieve onderhoudsinspecties, maandelijkse vervanging van onderdelen en het gebruik van sensoren omvatten om gevaarlijk hoge trillingsniveaus te detecteren.
8. Detectiescore
Dit aantal bepaalt hoe gemakkelijk het is om een probleem te detecteren voordat het een totale mislukking veroorzaakt. Het wordt gescoord op een schaal van 1 tot 10. Een score van 1 wordt gegeven aan een gebeurtenis die nooit kan worden gedetecteerd. Een gebeurtenis die bijna elke keer kan worden gedetecteerd, wordt een score van 10 gegeven. Een lekke band kan bijvoorbeeld soms in een vroeg stadium worden gedetecteerd, zodat deze een 5 krijgt. Een afgebroken voorruit wordt vaak veroorzaakt door onvoorspelbare gebeurtenissen, wat betekent dat deze moeilijk te detecteren is en een 9 zou scoren.
9. Risico prioriteit nummer
Het risicoprioriteitgetal berekent faalwijzen die de grootste impact hebben en het best te voorkomen zijn. Om de RPN te vinden, vermenigvuldigt u de ernst, frequentie en detectiescores. Als een storingsmodus bijvoorbeeld een ernstscore van 8, een frequentiescore van 5 en een detectiescore van 10 heeft, zou de RPN 400 zijn. Hoe hoger het getal, hoe meer middelen er moeten worden ingezet om die storing te voorkomen.
10. Bepaal de aanbevolen actie
Stel een plan op om de kans op falen te verkleinen of de kans op vroege detectie te vergroten. Dit kan zijn het verhogen van de frequentie van PM's op een onderdeel of het investeren in conditiebewakingsapparatuur.
FMEA's beheren
FMEA's zijn levende documenten die regelmatig moeten worden herzien en bijgewerkt. Hier zijn enkele gebeurtenissen die een beoordeling van een FMEA kunnen veroorzaken:
- Er is een nieuw activum ontworpen of geïnstalleerd in uw instelling
- Een nieuwe technicus of operator voegt zich bij het team
- Er is een wijziging aangebracht in de bedrijfsmodus van een machine (dwz deze wordt vaker uitgevoerd of de specificaties zijn gewijzigd)
- Er komt vaker een storingsmodus voor
- Er is nieuwe technologie geïmplementeerd waarmee u storingen gemakkelijker kunt detecteren of voorkomen
- U vindt een nieuwe storingsmodus of reden voor een bestaande storing
- De impact van faalveranderingen (dwz er wordt een nieuw product geproduceerd met duurder materiaal)
Zowel onderhouds- als operationeel personeel moet worden betrokken bij het wijzigen en aanvullen van een storingsmodus en effectanalyse. De diversiteit aan perspectieven en ervaringen met apparatuur helpt hiaten in uw FMEA's te voorkomen.
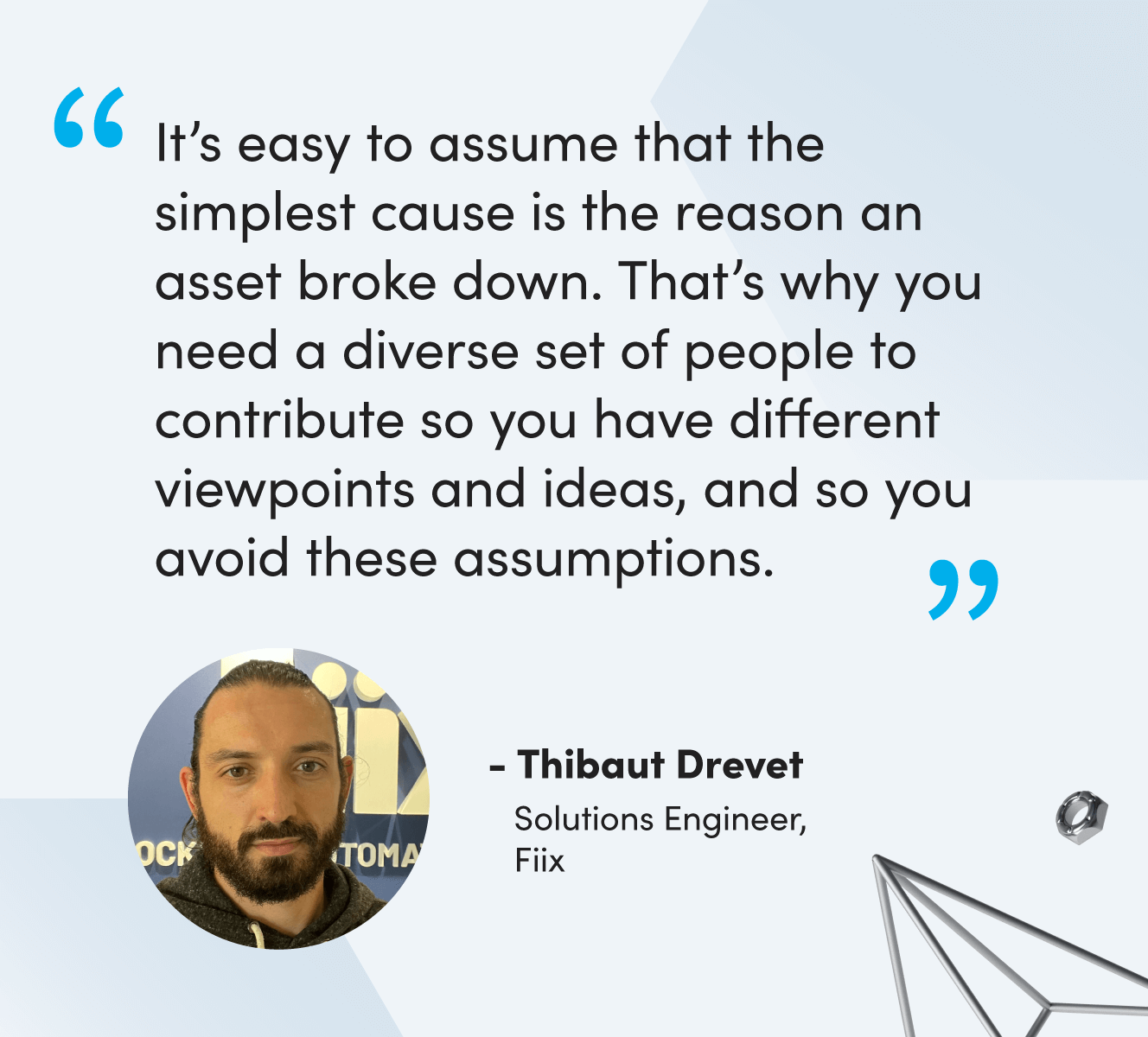
FMEA's zijn een langetermijninvestering in succes
Een storingsmodus en effectenanalyse is geen pleister of een hulpmiddel voor probleemoplossing. Het is een continue activiteit met als doel falen waar mogelijk te voorkomen en de effecten ervan te verzachten wanneer dat niet het geval is. Het is een hulpmiddel voor planning en een beveiliging tegen financiële verliezen en veiligheidsrisico's.
Hoewel het creëren van FMEA's een aanzienlijke tijdsinvestering met zich meebrengt, zal het u op de lange termijn terugbetalen door u te helpen vooruit te plannen, reactief onderhoud te voorkomen en het succes van uw team te volgen.
Onderhoud en reparatie van apparatuur
- Hoe u het onderhoud proactief kunt houden
- Beknopte handleiding voor de ontwikkeling en uitvoering van PM
- Onderhoud en betrouwbaarheid beste prestaties
- Details zijn belangrijk voor onderhoud en betrouwbaarheid
- Houd het onderhoud eenvoudig:gebruik zintuigen en gevoeligheid
- 5 oorzaken van apparatuurstoringen (en wat u kunt doen om dit te voorkomen)
- Tijd is geld:tips voor het gebruik van onderhoudssoftware om tijd te besparen en efficiënter te besteden
- Vereenvoudig storingsrapportage bij onderhoud
- Een gids voor onderhoud en onderdelen van skiliften
- Uw gids voor bediening en onderhoud van kranen
- 4 onderhoudstips om de levensduur en ROI van apparatuur te verlengen