Alcoa streeft naar uitmuntendheid op het gebied van betrouwbaarheid

Als je niet tegen de hitte kunt, kun je beter geen werk zoeken bij de vestiging van Alcoa Primary Metals in het zuiden van Indiana.
Vuurspuwende potlijnen en met gesmolten metaal gevulde smeltkroezen kunnen de omgevingstemperatuur van de productievloer tot bijna drie cijfers drukken. Warmte straalt zichtbaar af van machines. Zweetstroompjes druppelen langs de wangen en ruggen van de arbeiders. Frequente pauzes voor water en Gatorade zijn een noodzaak.
Het is een fysiek veeleisende omgeving, maar de echte hitte waarnaar in de eerste paragraaf wordt verwezen, heeft meer te maken met de positie van deze specifieke fabriek in de aluminiumsmeltindustrie. Deze locatie, onderdeel van Alcoa's enorme Warrick Operations, werd eind jaren vijftig gebouwd en begon in het begin van de jaren zestig met de productie van ruw aluminium voor de blikplaatindustrie.
Het is een oude fabriek in een leeftijds- en technologiegevoelige industrie. In 1980 waren er 33 Amerikaanse smelterijen. Nu zijn dat er 13. Slechts 6 procent van de aluminiumcapaciteit in de wereld zal dit jaar worden geproduceerd in smelterijen van meer dan 50 jaar oud. De klok tikt.
Voeg aan deze status toe:
-
25 procent van het personeelsbestand van de fabriek komt momenteel in aanmerking voor pensionering door leeftijd of dienstjaren;
-
de door de fabriek betaalde lonen behoren tot de hoogste in de industrie; en,
-
een paar jaar geleden waren de onderhoudskosten van deze smelter per metrische ton geproduceerd aluminium de op één na hoogste in het wereldwijde Alcoa-systeem.
Voel je de hitte? Elke medewerker van deze fabriek doet dat. Maar in plaats van te wachten op een ondergang die aanstaande leek, is het onderhouds- en operationele personeel naar voren getreden en actie ondernomen.
"We moeten de knoop doorhakken als we deze levensstandaard willen behouden en deze fabriek in leven willen houden", zegt Alcoa Business System-manager van smelten, Mark Keneipp. “Dit is de nieuwe realiteit. Je moet er gewoon mee dealen.”
Het begint met een blik in de spiegel.
“Onze uitdaging was en is om ondanks onze hoge leeftijd kostendekkend te zijn”, zegt Keneipp. “We zitten niet meer aan de voorkant van de leeftijdscurve. We moeten een horizon van 15 tot 20 jaar hebben om kapitaal aan te trekken binnen Alcoa. Als het 25 tot 30 jaar is, zou dat geweldig zijn. Om dat te doen, moeten we ons voortdurend bewijzen als een slanke, kostenconcurrerende, stabiele en efficiënte fabriek.”
Dit is geen omgeving voor de zwakken. Maar door hard werken en doorzettingsvermogen zijn er voldoende beloningen.
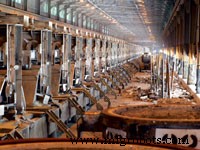
Time-out voor bellen
De inspanningen om de aanwezigheid van Alcoa Primary Metals in de productiegemeenschap in het zuiden van Indiana te ondersteunen, begonnen op bedrijfsniveau.
In 1997 begon Alcoa CEO Alain Belda de principes van Toyota Production System (TPS) naar de 250 wereldwijde locaties van zijn bedrijf te brengen.
Rodney Cunningham, manager productie aluminiumfabriek (links), procescoördinator Larry York en senior stafprocesingenieur Brian Audie staat in een lege aluminiumtank op het terrein van Alcoa's Warrick Operations. De locatie gebruikte traditioneel vier van dergelijke tanks als opslagvaten voor aluminiumoxide, een belangrijk ingrediënt in het aluminiumsmeltproces. Initiatieven op het gebied van slanke productie en kritisch denken hebben ertoe geleid dat de fabriek is ingekrompen tot twee tanks, waardoor het bedrijf een grote som geld heeft bespaard.
TPS is een lean manufacturing-filosofie die is gebaseerd op 'just-in-time'-productie, afvalverwijdering en snelle probleemoplossing. De smelter in Indiana deed echter een belangrijke ontdekking bij de implementatie van het systeem.
"TPS en flow en lean werken niet als je onstabiele, onvoorspelbare apparatuur hebt", zegt Keneipp.
Efficiënt, gestroomlijnd en kosteneffectief fabrieksonderhoud en de betrouwbaarheid van machines moeten voorop staan.
Om zijn punt te illustreren, biedt Keneipp een diagram aan dat 'de onderhoudsijsberg' wordt genoemd. Boven het water zijn directe onderhoudskosten gekoppeld aan materialen, arbeid, overuren, contractdiensten en overhead en voordelen. Onder de oppervlakte liggen indirecte kosten die verband houden met uitvaltijd, installatie en opstarten, gemiste schema's, overtollige voorraad, crisisbeheer, noodaankopen en een algemeen rimpeleffect op de productie.
"De indirecte componenten worden gegijzeld door de onstabiele apparatuur en processen van een fabriek", zegt hij.
Al deze verspilling vervuilt het systeem en drijft zowel de exploitatie- als de onderhoudskosten op.
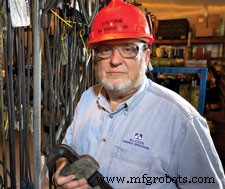
In 2002 had deze smelterij totale onderhoudskosten van meer dan $35 miljoen. Zijn "pijnlijk hoge" verhouding van meer dan $ 137 aan onderhoudskosten voor elke metrische ton geproduceerd aluminium (zie "Alleen de feiten" voor jaarlijkse tonnage) plaatste het op een na laatste onder de Alcoa-smeltfabrieken wereldwijd. Het wereldwijde gemiddelde in 2002 was $ 90 per ton.
Deze Alcoa-fabriek en haar leiders hadden twee opties.
“De fabrieksmanager, Royce Haws, zei dat we onze kosten gingen verlagen. Het was geen optie om te blijven waar we waren. Het zou gaan gebeuren”, zegt Keneipp. "We kunnen het op een slimme of kortzichtige manier doen. Als je bijziend bent, zijn dat enge dagen. Het is moeilijk om kapitaal in de fabriek aan te trekken om de dingen te doen die moeten worden gedaan als u onderhoud uitstelt. Niemand voelt zich goed bij die aanpak. Dat is een motivatie voor mensen om iets beters te zoeken.”
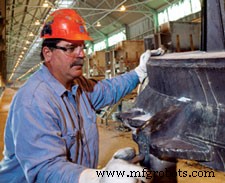
De golven vangen
Als je het nu nog niet geraden hebt, koos de Alcoa-fabriek voor de slimme aanpak om de onderhoudskosten te verlagen. Onderhoudsleiders werkten begin 2003 samen met consultants van Life Cycle Engineering (LCE) en de Ron Moore Group om een aanpak te ontwikkelen, het Reliability Excellence Process, dat in drie 'golven' werd ingezet. Het proces is gebaseerd op de overtuiging dat een geformaliseerd, goed gedefinieerd partnerschap noodzakelijk is tussen onderhoud en operaties. In dit partnerschap is Operations eigenaar van de apparatuur en heeft het een primair belang bij betrouwbaarheid. Maintenance is een gelijkwaardige partner die zich inzet om tijdige en effectieve methoden, vaardigheden, expertise en ondersteuning te bieden.
"Dat is een grote verandering", zegt inspecteur van betrouwbaarheidstechniek Joseph Motz. “Vroeger was het een silo-omgeving waar veel met de vinger werd gewezen.”
Gesmolten metaal wordt uit een smeltkroes gegoten
in de Ingot-afdeling van de Alcoa-fabriek.
Enkele voorbeelden:
Een telefoniste heeft een mogelijk probleem opgemerkt. Er was geen reparatie gepland of gemaakt. De automaat ging kapot. Wie was de schuldige?
Of er kwam onderhoud opdagen voor een preventief onderhoud van twee uur. Terwijl hij in de machine zat, ontdekte hij extra problemen en voltooide hij de PM-taak acht uur later, wat gevolgen had voor de output. Wie was de schuldige?
Het antwoord in deze gevallen was zowel onderhoud als operaties.
"We moesten ons realiseren dat we allemaal in hetzelfde team zitten", zegt Motz. “We zijn hier allemaal om aluminium te maken. Als we in verschillende richtingen gaan en niet samenwerken, werkt het proces niet.”
Golf 1 in de benadering met drie golven begon in juni 2003.
"Golf 1 was Ron Moore", zegt Keneipp. “We hebben hem erbij gehaald om met belangrijke fabrieksleiders te praten. Hij daagde de eeuwenoude paradigma's uit. ‘Je moet meer een asset-owner-filosofie aannemen.’ ‘Je verspilt geld.’ Hij schudt de boel wakker en opent ogen.”
Wave 2 arriveerde in augustus met een volledige Reliability Excellence-beoordeling door LCE. Gedurende een periode van twee weken heeft het bedrijf uitgebreide interviews gehouden met 90 operationele en onderhoudsmedewerkers (per uur en salaris), evenals met de fabriekscontroller.
De informatie leidde tot:
-
een financiële analyse waarin de geschatte waarde voor het dichten van de hiaten naar uitmuntendheid in betrouwbaarheid wordt gedetailleerd in vergelijking met de implementatiekosten (gepresenteerd als een berekening van het rendement op de investering);
- een voorlopig masterplan dat de processen en methodologieën schetste die nodig zijn om de hiaten te dichten.
"We wilden naar onze huidige toestand kijken en een doeltoestand identificeren", zegt Keneipp. "De kloof tussen die twee is je pijn of winst. Is het de moeite waard om de kloof te overbruggen? Dat moesten we aan het senior management bewijzen. We moesten bewijzen dat het verdiensten was om geld in de oude fabriek te steken.
"Gezien alle feiten, was het verstandig om zo snel mogelijk geld goedgekeurd te krijgen om verder te gaan."
Golf 3 begon in september. Operationele en onderhoudsleiders:
-
het masterplan geïmplementeerd
-
heeft alle werknemers geïnformeerd over hun nieuwe rollen en verantwoordelijkheden met betrekking tot het vergroten van de betrouwbaarheid van apparatuur
-
workshops gegeven over de juiste technieken om de betrouwbaarheid te verbeteren
-
vastgelegde gedefinieerde processen en effectieve voortgangsmetingen
“Dit is niet gemakkelijk. Niets van dit alles is ", zegt Rodney Cunningham, productiemanager van potroom. “Maar als je management commitment hebt en een partnership tussen onderhoud en exploitatie, dan vergroot je de kans op succes. Zonder die dingen ga je het niet redden."
De lat hoger leggen
Het vaststellen van definities op verschillende gebieden heeft geleid tot verbeteringen. Een primaire focus was om te definiëren "wat is mogelijk?" en "wat is vooruitgang?"
Een antwoord kwam in het accepteren van de algehele effectiviteit van apparatuur (OEE) als een belangrijke fabrieksbrede maatstaf. OEE volgt bronnen van bedrijfsverlies, waaronder de beschikbaarheid, prestaties en kwaliteit van apparatuur, en wordt uitgedrukt als een percentage van optimale prestaties.
"Het wordt in feite bepaald door een aantal beste prestaties uit het verleden", elektrodeproductiemanager Tom Svoboda. “Je hebt het zien gebeuren. Het was niet fictief of hypothetisch. Of de apparatuur die maand buitengewoon draaide of u er echt bovenop zat, het gebeurde. De vraag is:als je het in die ene periode hebt gedaan, waarom zou je het dan niet altijd kunnen doen?”
Gebruikmakend van een sportanalogie om het belang van 100 procent OEE te illustreren, als een hoogspringer normaal 6 voet 6 inch springt maar een persoonlijk record van 7 voet vestigt, wat specifiek leidde tot deze top 100 procent prestatie. Heeft hij anders getraind? Veranderde hij zijn dieet voorafgaand aan de meet? Had hij andere schoenen aan? Hij legde letterlijk de lat hoger. Wat kan worden geleerd en wat kan worden gedaan om dat doel keer op keer te bereiken?
Onderhoud en operaties werkten samen om topprestaties te definiëren voor fabrieksfuncties (bijvoorbeeld anodemontage), processen (ontladen van erts), resultaten (schroot) en individuele apparaten (ringoven). Bij het verzamelen van deze informatie werd vastgesteld dat er $ 8,3 miljoen aan jaarlijkse kostenbesparingen mogelijk waren als gevolg van het behalen van OEE-doelen.
Met de achtergrondinformatie werden huidige toestanden gedefinieerd en doelcondities vastgesteld. Activiteiten – werkprojecten waarbij gebruik werd gemaakt van lean manufacturing-tools zoals Kaizen en Continuous Improvement – vonden plaats. De voortgang werd gemeten en geanalyseerd. En er werden tastbare voordelen berekend.
In 2004 was $ 2,4 miljoen aan verbeteringen gekoppeld aan OEE-winsten.
Verder kijken en actie ondernemen leidden ook tot lagere onderhoudskosten in de smelterij. In het eerste jaar na de start van het betrouwbaarheidsinitiatief daalden de kosten met $ 1,9 miljoen, van een basisbedrag van $ 32 miljoen tot $ 30,1 miljoen. In 2004 daalde het cijfer nog eens $ 700.000. De verhouding van onderhoudskosten per geproduceerde ton daalde ook tot $ 109 in 2004.
Het Plan op 'Gepland'
Er is ook een grote inspanning geleverd om elementen van onderhoud beter te definiëren. Met name in dit door de operator geleide betrouwbaarheidssysteem:"hoe wordt het werk gepland?" en "hoe wordt het werk gedaan?"
“Terugkijkend hielden we onszelf voor de gek door te denken dat we gezond waren”, zegt onderhoudsmanager Danny Reyes. “Veel van onze oude statistieken klopten niet meer. We dachten dat ons 'percentage gepland en gepland werk' 85 procent was en ons 'percentage PM voltooiing' 90 procent."
LCE informeerde de fabriek dat het de verkeerde definities gebruikte.
"Het 'percentage gepland en gepland werk' was eigenlijk gewoon 'percentage gepland'. De planning was zeer beperkt", zegt Reyes. “Het was het naleven van de planning. Waarschijnlijk was 10 procent van die banen gepland.”
Een 35-tegen-1 verhouding van ambachtspersoneel (140) tot planners (vier) was de kern van het probleem.
“Het werkte niet zo goed”, zegt onderhoudsplanner Larry McCubbins. “Er was weinig tijd om te plannen. Je werd een planner, en daar was je niet zo goed in.'
Een reactieve omgeving gedijt in deze setting. "We deden de 'aanpak voor huisonderhoud'", zegt Keneipp. “Zo pakken jij en ik projecten op zaterdagochtend aan. Het is echt ongepland en inefficiënt.”
De fabriek heeft sindsdien drie planners toegevoegd voor een totaal van zeven, wat een beter beheersbare verhouding van 20-op-1 oplevert.
"Dat maakt het voor deze jongens mogelijk om het werk op te zetten, te organiseren, te plannen, in te plannen met productiecentra, ervoor te zorgen dat alle onderdelen aanwezig zijn, ervoor te zorgen dat de apparatuur niet werkt en dat de tijd wordt toegewezen", zegt onderhoudsinspecteur van smelting. Scott Deon.
Andere sleutels tot een betere planning:
-
Een formeel document schetst nu de componenten van een geplande taak (zie zijbalk op pagina 14). "De arme vier planners die we hadden, probeerden alles te doen, deden de dingen niet op dezelfde manier", zegt Deon. "Dit nieuwe formaat standaardiseert nu hoe het werk moet worden uitgevoerd."
-
Een formeel, beveiligd gebied wordt nu door de planners gebruikt voor jobkitting. In het verleden werden benodigde onderdelen en materialen stuk voor stuk naar een bouwplaats gestuurd. De stapel kan weken blijven liggen totdat alle items zijn aangekomen. Tijdens de wachttijd was het niet ongebruikelijk dat onderdelen of gereedschappen werden verplaatst, verloren of gebruikt voor een andere klus.
“Terwijl de planner de klus plant, bestelt hij al het materiaal en laat het hier afleveren ', zegt McCubbins. “Als alles voor de klus er is, verzamelen we het op een paar pallets. De ambachtslieden komen dan en nemen het mee naar de bouwplaats en voeren het werk uit.” -
Effectieve communicatie.
“Vroeger dacht ik dat ik wist wat mensen wilden. Dit proces heeft me geleerd dat ik dat niet deed", zegt McCubbins. “Ik wist niet wat ze wilden en wat goed voor hen was. In het verleden plande ik de klus en stelde ik geen vragen.”
Voegt Deon toe:“Met de gedeelde verantwoordelijkheid met de productie weten we nu welke klus eerst komt. De persoon die de apparatuur bezit, moet weten wat het belangrijkste is. Vroeger, ik denk niet dat we gissen. Maar waren we 100 procent? Waarschijnlijk niet.” -
Gerichte, effectieve wekelijkse vergaderingen.
"Vastgoedeigenaren zitten de vergaderingen voor en planners/planners van gebiedsonderhoud zijn de facilitators", zegt Keneipp. “Als het een planningsgesprek is, overleggen we hoe we dat gaan doen. Als het een planningsvergadering is, stellen we de planning op.”
Ook met betrekking tot de manier waarop het werk wordt gedaan, heeft de fabriek stappen ondernomen om de geschiedenis van de apparatuur te documenteren en de instructies voor onderhoudstaken te standaardiseren.
"Vroeger kon je records krijgen, maar toen stopte de documentatie", zegt Dan Decastra, energietechnicus van gelijkrichterstations. “Dus hebben we een locatie op de server gemaakt en zijn we begonnen met documenteren. Voor dit station hebben we een 'bad boy'-lijst gemaakt. We hebben de grote problemen eruit gehaald en zijn daar begonnen. Nu kun je teruggaan naar 2001 en een geschiedenis zien van de luchtschakelaars, contacten, transformatoren en de skids.”
Betrouwbaarheidsingenieur Jonathan Fulton voegt eraan toe:“Misschien kan een derde van ons onderhoudspersoneel morgen met pensioen gaan als ze dat zouden willen. Dat is een enorme potentiële aansprakelijkheid voor ons. En het is moeilijk om van buitenaf een kwaliteitsvakman te krijgen. Om dit aan te pakken, standaardiseren we werkprocessen en ontwikkelen we materieelhistorie. Door dit te doen, kunnen we mensen met technische expertise snel op de hoogte brengen.”
Aantekeningen wieg
Een laatste voorbeeld van verbetering is hoe de fabriek beter definieerde wie onderhoudsproducten koopt en hoe geld wordt besteed aan gereedschappen en verbruiksmaterialen.
In het verleden kocht diverse onderhoudspersoneel in de smelterij het handgereedschap, elektrisch gereedschap, veiligheidsproducten, reinigingsmiddelen, goederenbehandelingsproducten en honderd andere benodigde artikelen. Gekochte producten werden ondergebracht in gedecentraliseerde gereedschapswiegjes rond de faciliteit en in een groot aantal niet-officiële bewaarplaatsen (kluisjes, kisten en hokjes).
“Terwijl de fabriek steeds verder uitbreidde, kwamen er gebieden bij. Ze hadden een kleine groep en iemand deed de bestelling en ze verzamelden hun voorraden hier en daar”, zegt algemeen monteur Dick Day. "We gaven veel geld uit om deze satellietkribben te voeden. Ze werden niet beheerd. Mensen kochten dingen, maar het was niet echt toegankelijk.”
Als een monteur een bepaald gereedschap nodig had, zocht hij ernaar. Het was ergens in de buurt. Als hij het niet kon vinden, zou hij er een bestellen. Dat gekochte gereedschap zou kunnen verdwijnen voordat het hem bereikte. Het leidde tot verspillende en overbodige uitgaven.
Om dit aan te pakken, werd een gecentraliseerde wieg gebouwd en werden alle items van de satellietwieg en het hokje naar dit beveiligde, omheinde gebied gebracht.
De waardeloze kwam binnen.
"We realiseerden ons dat we veel verouderde spullen hadden - iets voor een apparaat dat we misschien 10 jaar geleden hebben weggehaald", zegt Keneipp.
En het waardevolle kwam binnen.
“Het was verbazingwekkend wat er allemaal uit het houtwerk kwam. Iemand bracht een kast met meer dan $ 38.000 aan pompen en vijzels erin, "zegt Day, die de hoofdbediende van de centrale wieg werd. “We begonnen te gebruiken wat we hadden. Voor sommige materialen hoefden we een jaar lang niets te bestellen.”
Vandaag is Day verantwoordelijk voor de inkoop van deze onderhoudsgerelateerde producten. Hij ontvangt de aankopen, slaat de artikelen op en verdeelt ze indien nodig.
"We weten wat we hebben en waar het zich bevindt", zegt hij.
Day heeft ook een minimum/maximum-systeem gecreëerd voor een verscheidenheid aan producten en is begonnen met het standaardiseren van merken voor elektrisch gereedschap en lasbenodigdheden.
"Met elektrisch gereedschap hebben we grotendeels gestandaardiseerd op DeWalt en we zijn zwaar in hun draadloze gereedschappen", zegt hij. "Voor lasbenodigdheden hebben we onze draadaanvoerpistolen en de vervangende onderdelen voor die pistolen gestandaardiseerd."
Hij doet zijn huiswerk en vindt innovatieve manieren om kosten te besparen.
Een paar voorbeelden zijn:
Handschoenen :"Vroeger kochten we een merk handschoenen met een klein lipje erop voor $ 12 per paar. Dat moest iedereen hebben', zegt hij. "Je zou dezelfde handschoenen met een beetje elastiek erin kunnen kopen voor $ 2,67 per paar. Mensen vonden ze leuk.'
Hydraulische olie :"We kochten het per gallon voor $ 8 per stuk. Door het in bulk te kopen, besparen we nu $ 3 per gallon. Ik giet de olie in herbruikbare kannen die 57 cent per stuk kosten.”
Acetyleenslang :“Vroeger kochten we het voorverpakt op een spoel. Nu kopen we het op een rol van 500 voet en snijden we af wat de persoon nodig heeft. We besparen 25 procent.”
Day zegt dat het allemaal gezond verstand is.
"Ik zie het als mijn geld", zegt hij. "Als dit mijn bedrijf is, zou ik het zo runnen."
Ze laten zweten
Door hard werken, partnerschap, eigendom en innovatief denken is deze Alcoa-smeltfabriek stabieler, slanker, voorspelbaarder, betrouwbaarder en kostenconcurrerender geworden.
OEE-kostenvoordelen zijn $ 4,4 miljoen op jaarbasis voor 2005 tot nu toe vergeleken met het basiscijfer van 2003.
De onderhoudskosten van 2005 tot nu toe bedragen $ 27,1 miljoen op jaarbasis en weerspiegelen een daling van $ 4,9 miljoen ten opzichte van het basiscijfer van 2003.
De onderhoudskosten voor het tweede kwartaal van 2005 bedroegen $ 96 per geproduceerde ton en het is de bedoeling dat in de nabije toekomst $ 87 wordt behaald.
Een LCE-follow-upbeoordeling plaatste de fabriek in de categorie "proactieve omstandigheden" en er wordt gewerkt aan verbetering in de categorie "excellentie".
Er is optimisme en momentum.
"Toen ik 15 jaar geleden werd aangenomen, zeiden we:'We zijn oude technologie. We kunnen niet concurreren met sommige van de modernere faciliteiten'", zegt Fulton. “Voor mij is de beloning dat we concurreren en een hogere efficiëntie hebben. We produceren beter met onze 40 of 50 jaar oude technologie dan op locaties die 10 of 20 jaar geleden zijn gebouwd.”
Hoewel de hitte voor deze plant nooit helemaal weg zal gaan, doet ze er alles aan om de concurrentie te laten zweten.
Wat zijn de kenmerken van een geplande taak?
-
Er is een nauwkeurige schatting van de tijd voor de taak, zodat de supervisor een redelijke verwachting zou hebben wanneer hij of zij de taak zou kunnen toewijzen.
-
Er is een nauwkeurige schatting van de benodigde middelen in termen van ambachtspersoneel, reparatie-/vervangingsonderdelen, gereedschappen, ondersteunende apparatuur, enz.
-
Alle benodigde informatie (blauwdrukken, vergunningen, veiligheidsgerelateerd, etc.) wordt verkregen.
-
Opeenvolging van taakstappen, procedures en instructies om het werk te volbrengen zijn vastgelegd.
-
Alle benodigde onderdelen en materialen zijn uitgerust.
-
Als een ingebouwde controle om een geplande kwaliteit van het werk te garanderen, moet u periodiek de aard van het werk bespreken met een supervisor en/of de vakman die is toegewezen om het werk te voltooien. Zorg ervoor dat er een volledig begrip is van de reikwijdte van het werk en dat het werkpakket compleet is.
Onderhoud en reparatie van apparatuur
- Wat is betrouwbaarheidscultuur?
- Wat is de rol van de betrouwbaarheidsingenieur?
- Een Whirlpool Reliability Revolution
- Onderhoud en betrouwbaarheid beste prestaties
- De nr. 1 sleutel tot betrouwbaarheidssucces
- Betrouwbaarheidsgerichte verkoop?
- Hoe versnelt uitmuntende betrouwbaarheid de voordelen van Lean?
- Familiegerichte betrouwbaarheid
- Toeleveringsketenbeheer:verder gaan dan uitmuntende betrouwbaarheid
- Waarom uitmuntende betrouwbaarheid essentieel is voor veiligheid
- Betrouwbaarheid is een groen initiatief