Typen onderhoud:een vergelijking
Soorten onderhoud
Het is bekend dat er elk jaar miljarden dollars verloren gaan door ongeplande downtime en slechte kwaliteit van activa. In een nooit eindigende strijd om deze statistiek te bestrijden, implementeren organisaties een van de verschillende soorten onderhoud, vaak een combinatie van twee of meer. Definities van de soorten onderhoud variëren in de branche, waardoor het nogal verwarrend kan zijn om zaken als preventief en voorspellend onderhoud te onderscheiden.
De meeste soorten onderhoud vallen onder twee hoofdcategorieën:preventief en correctief. Preventief onderhoud is wanneer u proactief taken en onderhoudsplannen initieert om storingen te voorkomen. Naast het voorkomen van storingen, kan preventief onderhoud tot doel hebben de gevolgen van een storing te minimaliseren of het risico van een storing te bepalen.
Correctief onderhoud gebeurt nadat de storing is opgetreden. Uw team zorgt er op dit moment in feite voor dat het middel weer werkt. Ter verduidelijking:correctief onderhoud kan opzettelijk worden uitgevoerd in de vorm van een onderhoudsstrategie van run-to-failure, die hieronder zal worden besproken.
Laten we eens kijken naar de meest voorkomende soorten onderhoud die in de productie- en procesindustrie worden gebruikt.
- Preventief onderhoud. Preventief onderhoud is een vaste routine van het periodiek inspecteren van apparatuur, het opmerken van kleine problemen en het oplossen ervan voordat ze grote problemen worden. Het belangrijkste doel van preventief onderhoud is nul downtime. Dit doel wordt nagestreefd met behulp van drie doelstellingen:de productieve levensduur van apparatuur verbeteren, kritieke apparatuurstoringen verminderen en productieverlies als gevolg van apparatuurstoringen minimaliseren.
Er zijn een aantal soorten onderhoud die binnen de categorie preventief onderhoud vallen. Deze omvatten:
- Onderhoud op basis van gebruik, die triggers gebruikt op basis van het daadwerkelijke gebruik van elk activum. Door het gebruik van bedrijfsmiddelen te volgen met apparatuurmonitors kunnen onderhoudsmanagers een preventief onderhoudsschema opstellen volgens vooraf ingestelde parameters.
- Voorgeschreven onderhoud lijkt sterk op preventief onderhoud, maar het maakt gebruik van machine learning-software zoals kunstmatige intelligentie (AI) en het internet der dingen (IoT) om preventieve onderhoudstaken te plannen.
Voor een diepgaand inzicht in de soorten preventief onderhoud, het ontwerpen van een preventief onderhoudsprogramma, preventieve onderhoudstools en meer, bekijk de link aan het begin van dit gedeelte.
- Voorspellend onderhoud. Voorspellend onderhoud is onderhoud dat de prestaties en conditie van apparatuur bewaakt tijdens normale bedrijfsomstandigheden om de kans op storingen te verkleinen. Vergelijkbaar met preventief onderhoud (sommige mensen categoriseren het zelfs als een vorm van preventief onderhoud) en nauw verwant aan condition-based maintenance (CBM) , ligt het doel van predictief onderhoud in de naam:eerst voorspellen wanneer storingen zouden kunnen optreden en vervolgens de storing voorkomen door middel van gepland correctief onderhoud.
Hoewel veel organisaties zowel voorspellend als preventief onderhoud toepassen (76 procent gebruikt preventief, terwijl 65 procent voorspellend gebruikt, volgens een recent onderzoek van Reliable Plant), zijn er een paar belangrijke verschillen. Het meest opvallende is dat preventief onderhoud niet het aspect conditiebewaking vereist dat voorspellend onderhoud vereist. Dit betekent dat bij voorspellend onderhoud gebruik wordt gemaakt van op omstandigheden gebaseerde technologieën zoals infraroodthermografie, akoestische monitoring, trillingsanalyse en olieanalyse. Een ander belangrijk verschil is dat preventief onderhoud het inspecteren en uitvoeren van onderhoud aan activa omvat, ongeacht of de apparatuur onderhoud nodig heeft (het onderhoudsschema is gebaseerd op een trigger). Voorspellend onderhoud niet.
Hieronder staat een grafiek die laat zien hoe condition-based onderhoud zich verhoudt tot voorspellend en proactief onderhoud. Hier is voorspellend onderhoud een van de twee kanten die voortkomen uit CBM:een proactieve kant die zich richt op het vinden van de oorzaak van een storing en een voorspellende kant die zich concentreert op de faalsymptomen en storingen.
Klik op de link aan het begin van dit gedeelte voor meer informatie over voorspellend onderhoud, voorspellende onderhoudstechnologie en meer.
- Betrouwbaarheidsgericht onderhoud (RCM). Betrouwbaarheidsgericht onderhoud is het proces van het identificeren van potentiële problemen met uw apparatuur en het bepalen wat u moet doen om ervoor te zorgen dat die activa op maximale capaciteit blijven produceren. Met andere woorden, u analyseert storingen om de juiste onderhoudsmethoden en aangepaste onderhoudsschema's voor elk afzonderlijk activum te vinden.
Betrouwbaarheidsgericht onderhoud wordt soms verward met preventief onderhoud, maar er is één belangrijk verschil:preventief onderhoud is niet selectief zoals RCM, waardoor het minder efficiënt is. Aangezien RCM elk activum afzonderlijk bekijkt, wordt de inefficiëntie verminderd door onderhoudstaken toe te wijzen die zijn afgestemd op elk apparaat.
Betrouwbaarheidsgericht onderhoud maakt gebruik van een algemene workflow in vier stappen:kies het activum, evalueer het activum, bepaal het type onderhoud en herhaal het proces. Beoordelingscriteria voor het implementeren van een RCM-programma stellen zeven vragen:
- Hoe goed moet dit apparaat presteren?
- Op welke manieren kan dit apparaat defect raken?
- Wat veroorzaakt elke storing?
- Wat gebeurt er als er een storing optreedt?
- Waarom is elke mislukking belangrijk?
- Welke taken (proactief) moeten worden uitgevoerd om te voorkomen dat deze storingen optreden?
- Wat moet er gebeuren als er geen geschikte preventieve taak kan worden gevonden?
Klik op de link aan het begin van dit gedeelte om meer te lezen over op betrouwbaarheid gericht onderhoud, inclusief het implementeren van RCM, praktijkvoorbeelden van organisaties die een RCM-programma hebben geïmplementeerd, en meer.
- Totaal Productief Onderhoud (TPM). Totaal productief onderhoud is het proces waarbij machines, apparatuur, medewerkers en ondersteunende processen worden gebruikt om de integriteit van de productie en de systeemkwaliteit te behouden en te verbeteren. Het doel van een TPM-programma is om de algehele effectiviteit van apparatuur (OEE) te verbeteren door kleine, multidisciplinaire teams te vormen die zich bezighouden met kerngebieden zoals preventief en autonoom onderhoud, training van machinebedieners en de standaardisatie van werkprocessen. Totaal productief onderhoud richt zich op alle afdelingen binnen een organisatie en zorgt voor een efficiënt en effectief gebruik van de productiemiddelen.
Totaal productief onderhoud wordt meer als een proces dan als een programma beschouwd, maar ook als een proces ter verbetering van de bedrijfsvoering dan als een volledig onderhoudsprogramma. Het is ook geen quick fix, want het duurt jaren om maximaal te profiteren van een hoogwaardig TPM-proces; u kunt echter onmiddellijk resultaten zien.
Totaal productief onderhoud omvat lean manufacturing en de 5-S-systeemtechnieken uit de internationaal geaccepteerde benchmark die bestaat uit acht pijlers:autonoom onderhoud, gerichte verbetering, gepland onderhoud, kwaliteitsonderhoud, vroegtijdig apparatuurbeheer, training en opleiding, veiligheid, gezondheid en milieu, en TPM in administratie.
De implementatie van TPM omvat vijf fasen:
- Identificeer een proefgebied
- Herstel apparatuur in de beste bedrijfsconditie
- OEE meten
- Grote verliezen aanpakken/verminderen
- Gepland onderhoud implementeren
Klik op de link aan het begin van dit gedeelte om meer te lezen over TPM, inclusief de acht pijlers van TPM, hoe het te implementeren, hoe een TPM-proces te ondersteunen en meer.
- Autonoom onderhoud. Autonoom onderhoud is een onderhoudsstrategie die bestaat uit het trainen van operators om hun apparatuur continu te bewaken, aanpassingen te doen en kleine onderhoudstaken uit te voeren om de efficiëntie te verhogen. Dit wordt gedaan in plaats van onderhoudstechnici toe te wijzen aan regelmatig gepland onderhoud, zodat ze meer belangrijke en dringende onderhoudstaken kunnen uitvoeren.
Autonoom onderhoud heeft twee kernprincipes:het voorkomen van verslechtering van apparatuur door een goede werking en het in een "als nieuw"-staat brengen en houden van apparatuur door middel van restauratie en goed beheer. Dit vereist dat operators vaardigheden beheersen, zoals het detecteren van afwijkingen door de componenten van de machine te begrijpen, verbeteringen aan te brengen, kwaliteitsproblemen te identificeren en uit te zoeken wat de kwaliteitsproblemen veroorzaakte.
Het implementeren van autonoom onderhoud omvat zeven stappen:het vergroten van de kennis van de machinist, de eerste reiniging en inspectie van de machine, het wegnemen van de oorzaak van verontreiniging en het verbeteren van de toegang, het ontwikkelen van normen voor smering en inspectie, inspectie en bewaking, het standaardiseren van visueel onderhoud en continue verbetering.
Klik op de link aan het begin van dit gedeelte voor een meer diepgaande kijk op autonoom onderhoud, hoe het te implementeren en te onderhouden.
- Run-to-failure-onderhoud (RTF). Run-to-failure-onderhoud is een ongepland, reactief type onderhoud dat meestal een bewuste strategie is die is ontworpen om de kosten te minimaliseren. Organisaties kunnen ervoor kiezen om een RTF-plan aan te nemen voor zaken als wegwerpmiddelen (machines met wegwerponderdelen die bedoeld zijn om te worden uitgewisseld in plaats van gerepareerd), niet-kritieke middelen zoals gereedschap, duurzame middelen of middelen die niet onderhevig zijn aan slijtage of waarschijnlijk niet zullen falen onder normale bedrijfsomstandigheden, of activa die willekeurige faalpatronen vertonen die niet kunnen worden voorspeld.
Het voorbehoud bij RTF-onderhoud is dat het een goed beoordelingsvermogen vereist. Weten wanneer iets een groothandelsfout moet worden genoemd in plaats van het te repareren, maakt deel uit van de vaardigheden die bij RTF-onderhoud horen. Het kan enig risico met zich meebrengen, aangezien activa niet worden gecontroleerd, waardoor de organisatie in de loop van ongeplande downtime staart wanneer er iets kapot gaat.
Wanneer RTF echter wordt geïmplementeerd op de juiste activa met een slimme planning voor het omgaan met onvermijdelijke storingen, kan RTF tijd en geld besparen door ononderbroken apparatuur niet te vervangen.
Machine-onderhoud en het menselijk lichaam parallel
Als het gaat om soorten onderhoud, technieken en kosten, kunnen de primaire soorten onderhoud worden vergeleken met het menselijk lichaam om een momentopname te krijgen van de equivalente taak "lichaamsonderhoud". De onderstaande tabel gebruikt een voorbeeld van een stroomopwekkingsmiddel en vergelijkt dit met het menselijk hart.
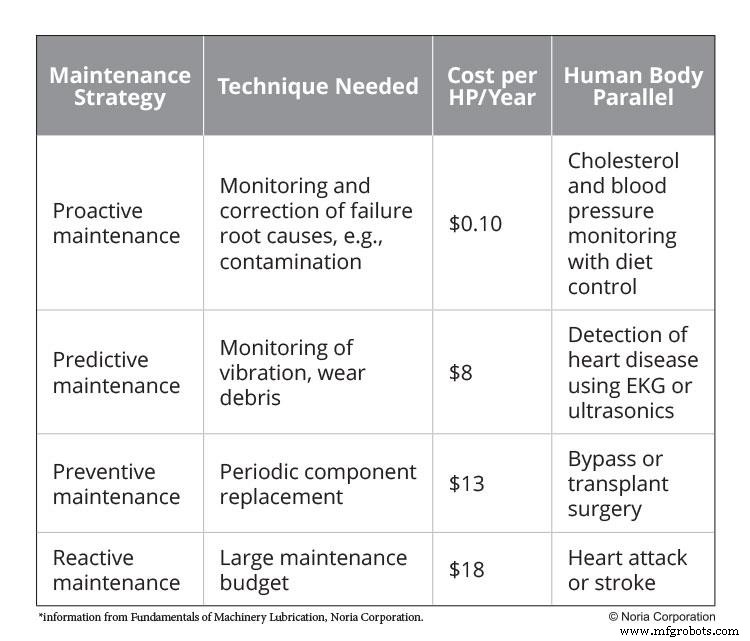
Soorten onderhoudstriggers
Onderhoudstriggers kunnen worden ingesteld en gebruikt bij meerdere soorten onderhoud. Breakdown-triggers worden gebruikt bij run-to-failure- of reactieve onderhoudsplannen. Voorspellend onderhoud gebruikt zaken als op tijd gebaseerde triggers in de vorm van waarschuwingen om te proberen een storing te voorkomen. Andere triggers die zullen worden besproken, zijn triggers op basis van gebeurtenissen, gebruik en omstandigheden.
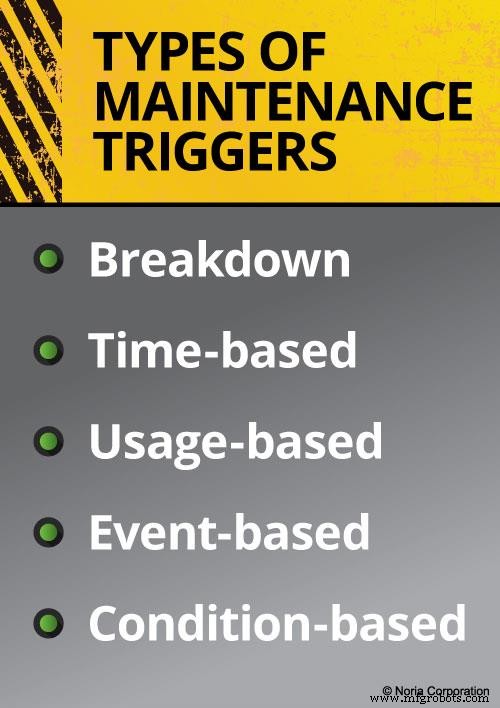
- Uitsplitsingstriggers. Zoals eerder vermeld, worden storingstriggers gebruikt bij run-to-failure of reactieve onderhoudsprogramma's. Wanneer een activum niet meer werkt, wordt een waarschuwing geactiveerd, waarmee een onderhoudswerkorder wordt gepland om het activum te repareren en in de normale bedrijfstoestand te brengen.
Storingstriggers zijn meestal alleen nuttig wanneer een organisatie een groep goedkope, eenvoudig te vervangen apparatuur heeft en vervangende onderdelen en eenheden op voorraad heeft die gemakkelijk en gemakkelijk kunnen worden verwisseld, waardoor uitvaltijd zo veel mogelijk wordt geminimaliseerd. Het gebruik van afbraaktriggers is vergelijkbaar met een kat-en-muisspel; het niet hoeven plannen van onderhoud zorgt voor een minder duur onderhoudsbudget, maar het betekent ook dat u te allen tijde reserveonderdelen en apparatuur beschikbaar moet hebben, evenals personeel om problemen op te lossen. Het aanhouden van aandelen op deze manier druist in tegen lean-principes zoals Just in Time (JIT), die zijn ontworpen om de voorraad te verminderen.
- Tijdgebaseerde triggers. Misschien zijn de meest gebruikte onderhoudstriggers tijdgebaseerd. Deze zijn gekoppeld aan onderhoudsplanningssoftware zoals een geautomatiseerd onderhoudsbeheersysteem (CMMS) en alarmeren op basis van een vooraf ingesteld tijdsinterval. Op tijd gebaseerde triggers worden gebruikt in voorspellende en preventieve onderhoudsprogramma's voor eenvoudige taken zoals het smeren van tandwielen of het plannen van een inspectie. Wanneer een activum bijvoorbeeld een looptijd van 14 dagen bereikt, wordt er een waarschuwing geactiveerd om het te laten onderhouden. Buiten een productieomgeving zou een op tijd gebaseerde trigger elke drie maanden de luchtfilters van uw verwarming, ventilatie en airconditioning (HVAC) vervangen.
- Op gebruik gebaseerde triggers. Net als bij op tijd gebaseerde triggers, zijn op gebruik gebaseerde triggers afhankelijk van een vooraf bepaalde statistiek op basis van het gebruik van het betreffende activum, ongeacht de tijdsperiode. In tegenstelling tot op tijd gebaseerde triggers, die volgens de regels van de machine worden uitgevoerd, betekent op gebruik gebaseerde triggers dat een asset pas onderhoud krijgt als het een bepaalde hoeveelheid service heeft voltooid.
Net zoals uw auto elke 5.000 mijl een olieverversing krijgt, kan elke machine die tijd- of hoeveelheidbeperkte bewerkingen uitvoert, worden ingesteld met een op gebruik gebaseerde trigger. Meterstanden kunnen worden toegevoegd aan een CMMS en worden gebruikt om waarschuwingen in te stellen wanneer een gewenste hoeveelheid of waarde is bereikt. Op gebruik gebaseerde triggers zijn een geweldige manier om apparatuur te onderhouden die onderhevig is aan onregelmatige dienstregelingen en worden meestal gebruikt met programma's voor voorspellend of preventief onderhoud.
- Op gebeurtenissen gebaseerde triggers. Gebeurtenistriggers kunnen worden gebruikt om te reageren op apparatuur of faciliteiten en deze te beoordelen nadat een gebeurtenis zoals brand of overstroming heeft plaatsgevonden. De noodzaak om controles van het elektrische systeem en de infrastructuur na een overstroming te plannen en uit te voeren, kan bijvoorbeeld worden aangestuurd door een CMMS, waarbij het systeem het onderhoudsteam op de hoogte stelt van dergelijke taken. Hoewel op gebeurtenissen gebaseerde triggers plaatsvinden nadat een gebeurtenis heeft plaatsgevonden, zijn ze mogelijk niet allemaal direct verbonden met de gebeurtenis zelf. De meeste op gebeurtenissen gebaseerde triggers fungeren als vervolgcontroles op een gebeurtenis.
- Op conditie gebaseerde triggers. Op voorwaarden gebaseerde triggers worden gebruikt op basis van een beoordeling van een individueel activum. De beoordeling wordt gebruikt om te bepalen of het acceptabel is dat het activum blijft draaien of dat er onderhoud nodig is. Dit is een meer diepgaande optie omdat onderhoudspersoneel praktische kennis van het activum moet hebben om een weloverwogen beslissing te nemen over de toestand ervan.
De conditie van de apparatuur kan ook op afstand worden beoordeeld. Sensoren die op een asset zijn geplaatst om parameters zoals temperatuur, trillingen en geluid te bewaken, kunnen worden gebruikt als door omstandigheden geactiveerde waarschuwingen. Als een sensor bijvoorbeeld een temperatuurpiek opmerkt die een vooraf bepaald bereik overschrijdt, wordt een waarschuwing verzonden om een inspectie te plannen.
Moderne onderhoudstechnologie
Een van de belangrijkste factoren voor fabrikanten om uit te blinken in operationeel onderhoud, is het gebruik van de gegevens die door moderne technologie worden geleverd. Om dit te doen, is er vrijwel geen nieuwe onderhoudsoplossing nodig om bedrijfsmiddelen, medewerkers en processen georganiseerd en naadloos te laten werken.
Technologische vooruitgang komt het meest voor in condition-based monitoring in de vorm van proactief en voorspellend onderhoud. Bij dit soort onderhoud kunnen technologieën zoals olieanalyse, trillingsanalyse, thermografie en motorstroomanalyse helpen bij het bepalen van de hoofdoorzaken en storingssymptomen, voordelen zoeken zoals verlenging van de levensduur van de machine en vroege foutdetectie, en het aantal en de impact van storingen verminderen.
De huidige technologische revolutie in de maakindustrie heeft geleid tot minder fouten en defecten, een geoptimaliseerde productie en lagere arbeidskosten. Geautomatiseerde sensoren die machines continu kunnen bewaken, behoren tot de grootste verbeteringen. Ze kunnen niet alleen worden gebruikt voor meerdere soorten onderhoud, maar ze kunnen ook een enorme hoeveelheid gegevens genereren die kunnen worden geanalyseerd en gebruikt om processen te verbeteren.
CMMS-oplossingen kunnen helpen om al deze gegevens te benutten en te integreren met vier belangrijke aspecten voor een moderne strategie voor onderhoudstechnologie:voorspellend onderhoud gebruiken, focussen op gegevens en het IoT, inventaris beheren en cycli verbeteren voor blijvend succes.
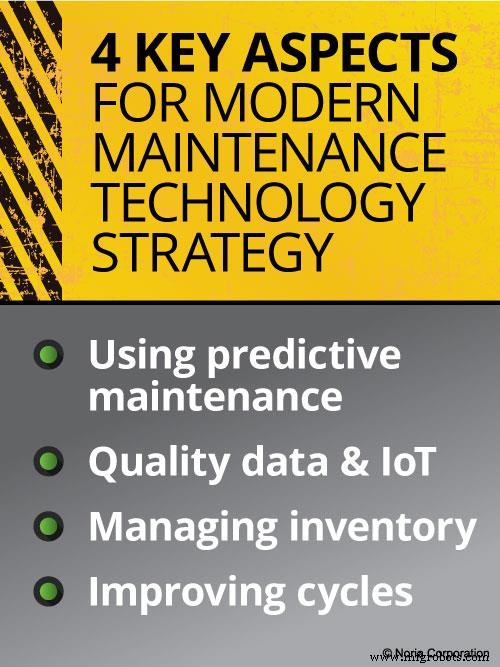
- Voorspellend onderhoud gebruiken: Hoewel preventief onderhoud een goede manier is om te voorkomen dat u loopt te falen en de uitvaltijd te verminderen, is de volgende stap het implementeren van voorspellend onderhoud om de gegevens die uw machines genereren efficiënt te verzamelen en te analyseren.
- Kwaliteitsgegevens en het IoT: Het is belangrijk om een CMMS te hebben dat de enorme hoeveelheid data aankan die in uw fabriek wordt geproduceerd. U wilt gegevens integreren van standaard zelf-geïnstalleerde sensoren tot ingebouwde sensoren en alles daartussenin. Dit betekent meestal dat je op zoek moet naar een CMMS met een IoT-strategie, zodat je niet getrouwd bent met één type hardware.
Het IoT wordt gebruikt om gegevens die zijn verzameld van bedrijfsmiddelen op de fabrieksvloer draadloos te integreren in een CMMS dat door de hele organisatie wordt gebruikt. Hiervoor moeten eerder besproken triggers en waarschuwingen worden ingesteld om automatisch werkorders te maken zonder menselijke tussenkomst.
- Voorraad beheren: Uit een recent onderzoek van Plant Services bleek dat bijna 29 procent van de respondenten een achterstand van drie tot vier weken had met onderhoudstaken. Altijd een reactieve benadering van onderhoud doen, zorgt er alleen maar voor dat uw achterstand groeit, wat betekent dat uw activa niet het juiste onderhoud krijgen dat ze nodig hebben. Door achterstallige taken in een CMMS bij te houden, kunt u problemen, oorzaken en oplossingen identificeren en kunt u een meer proactieve cultuur omarmen om de achterstand te verminderen.
- Cyclus verbeteren: Door gebruik te maken van gegevens van een gemoderniseerde installatie op de fabrieksvloer en deze te integreren via een CMMS, bent u op weg om uw onderhoudscyclus te verbeteren, besparingen te realiseren en de efficiëntie te verhogen.
Moderne trends in onderhoudstechnologie
- Industrieel internet der dingen: Zoals eerder besproken, is het internet der dingen, en meer specifiek het industriële internet der dingen (IIoT), een moderne vorm van geautomatiseerde gegevensverzameling door het gebruik van een netwerk van draadloze sensoren. Tegenwoordig zijn goedkope, multifunctionele sensoren gemakkelijker verkrijgbaar dan ooit. Ze kunnen worden geconfigureerd in verschillende sensornetwerken op meerdere industriële activa en worden gebruikt om automatisch onderhoudsgegevens te verzamelen. Dit elimineert de noodzaak voor dure en tijdrovende handmatige gegevens, die vatbaar zijn voor menselijke fouten.
- Augmented Reality (AR): Onderhoud en training op afstand beginnen te profiteren van AR dankzij de mogelijkheid om instructies op afstand aan te bieden. Door deze maatwerkaanpak kunnen onderhoudstaken worden aangepast aan het inzicht en vaardigheidsniveau van de medewerker. Augmented reality kan training vergemakkelijken die wordt gegeven door een leverancier van apparatuur of hoger onderhoudspersoneel via een cyberpresentatie die laat zien hoe een taak moet worden uitgevoerd.
Hoewel het nog steeds een opkomende trend is, wint het gebruik van AR voor training aan populariteit vanwege de toenemende complexiteit van industriële apparatuur. Augmented reality kan de last verlichten van onderhoudspersoneel dat probeert om gelijke tred te houden met variaties in nieuwe apparatuur, inclusief technologisch geavanceerde mogelijkheden die bij elk activum horen. Er zijn al verschillende leveranciers die grootschalige AR-oplossingen aanbieden voor onderhoudstaken en IIoT-providers die AR leveren als onderdeel van een gebundeld pakket.
- Maintenance as a Service (MaaS): MaaS is een vrij nieuw paradigma voor de onderhoudswereld. Het gaat in wezen om het leveren van onderhoudsdiensten op aanvraag. Met MaaS kan een leverancier een exploitant van een installatie in rekening brengen op basis van de onderhoudsdiensten die hij/zij daadwerkelijk gebruikt in plaats van een vast servicetarief. Dit doen leveranciers door grote hoeveelheden data te verzamelen en te verwerken, via de cloud op te slaan en op basis van deze data taken in te plannen. Diensten omvatten:
- de levensduur van een asset voorspellen of inzicht bieden in optimale onderhoudsintervallen;
- het leveren van servicehandleidingen, video's en virtual reality (VR) en interactieve AR-ondersteuning;
- configureren van informatietechnologie (IT) en andere systemen binnen een fabriek op basis van analytische resultaten; en
- met gedetailleerde statistieken en rapporten over machines.
Vroege stadia van MaaS-programma's beginnen beschikbaar te worden gemaakt door leveranciers. ThyssenKrupp-liften worden nu geleverd met een proactief onderhoudsprogramma dat problemen voorspelt voordat ze zich voordoen en de juiste personen op de hoogte stelt om een inspectie uit te voeren. BMW is ook van plan om MaaS in de nabije toekomst naar de consument te brengen, met programma's die autobezitters laten weten wanneer ze het beste onderhoud aan hun voertuigen kunnen laten uitvoeren.
Onderhoud en reparatie van apparatuur
- Verschil tussen preventief versus voorspellend onderhoud
- Preventief onderhoud optimaliseren met een CMMS
- Preventief onderhoud versus voorspellend onderhoud:terug naar de basis
- Preventief onderhoud:een overzicht
- Preventief onderhoud
- Preventieve onderhoudssoftware gebruiken voor productie
- Gepland preventief onderhoud (PPM) uitvoeren
- Werkopdrachten voor preventief onderhoud plannen
- Belangrijkste voordelen van software voor preventief onderhoud
- Wat is preventief onderhoud?
- 5 soorten onderhoud om te weten