Kernmaken in de gieterij
Kern ondersteunen complexiteit bij zandgieten
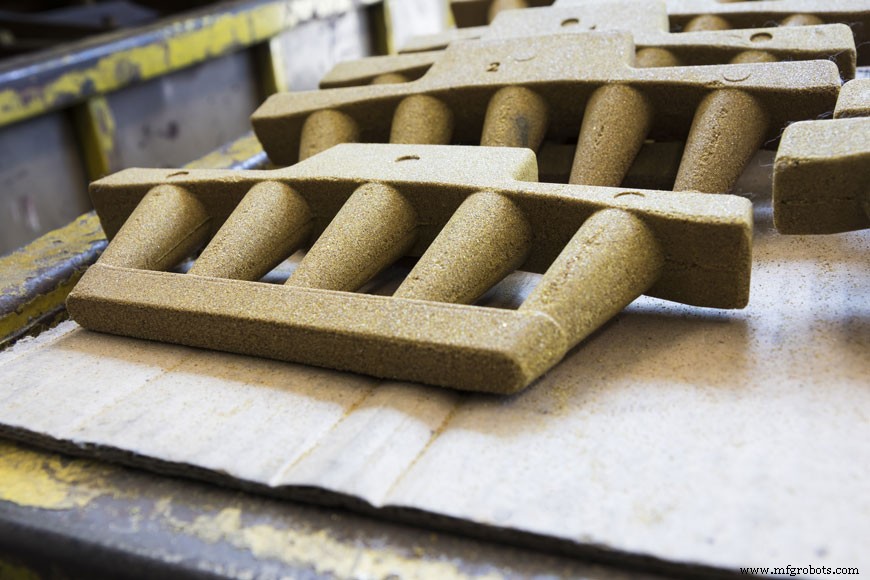
Wat is een kern in metaalgieten?
Een kern is een zand- of metalen inzetstuk dat wordt gebruikt om een deel van een gietstuk te vormen dat niet kan worden gevormd door het primaire verwijderbare patroon. Wanneer een patroon in zand wordt geperst en vervolgens wordt geëxtraheerd, laat het een holle indruk achter. Vloeibaar metaal vult deze leegte en koelt af. Kernen zijn gemaakt om meer complexiteit in het ontwerp mogelijk te maken. Goed geconstrueerde kernen creëren gaten of kamers in een gietstuk. Matrijzen voor automotoren kunnen tot vijf kernen bevatten om de kamers te creëren die nodig zijn voor de werking van een verbrandingsmotor.
Kernen kunnen ook helpen hoeken te creëren die met een patroon onmogelijk zouden zijn. Elke overhang boven een lege ruimte zou het onmogelijk maken om het patroon terug te trekken zonder de overhang te breken. In deze gevallen kan een kern worden gebruikt.
Gietstukken met interne kernen hebben meestal een opening in de buitenste schil van het vormstuk om de kern na het gieten te verwijderen, hoewel deze opening mechanisch kan worden afgesloten tijdens het afwerken.
Kernen gemaakt van zand zijn ontworpen om af te breken; interne kernen worden aan het einde van het proces letterlijk uit het gietstuk geschud. De "shakeout" -opening is ook handig voor de plaatsing van de kern. Elke plaats waar de kern de mal raakt, is een plaats waar gesmolten metaal niet kan stromen, dus om een consistente metaaldikte te krijgen, moet een kern de te vullen ruimte "overbruggen" zonder enige zijkanten te raken. Om dit te bereiken, is de kern normaal gesproken langer dan het gietstuk en wordt het op zijn plaats gehouden door groeven in het zand buiten het gietpatroon.
Chaplets voor kernondersteuning
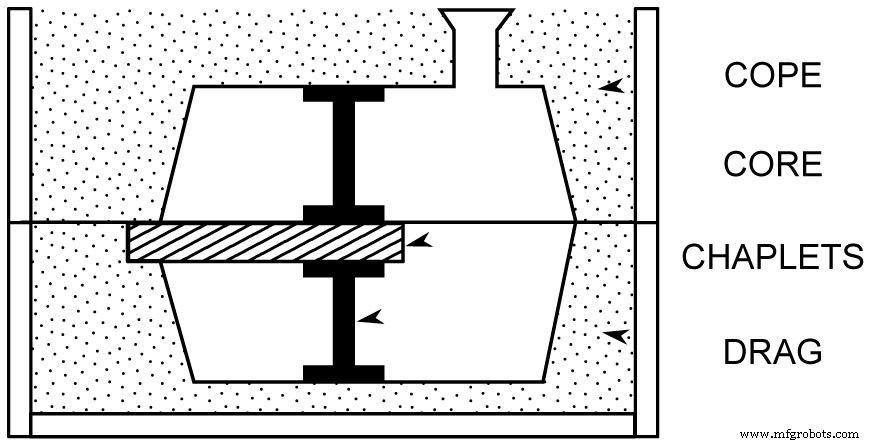
Als de kern erg lang is, of als er maar één rand uit de mal kan steken, dan chaplets worden gebruikt om de kern op zijn plaats te verankeren. Kroontjes zijn vaak gemaakt van hetzelfde metaal als het gietstuk, omdat een deel van het kroontjesmetaal in het gietstuk zelf wordt verwerkt. Om stevig te hechten aan de rest van het gietstuk, moet het oppervlak van de rozenkrans smelten, maar eerst moet het de kern ondersteunen. Het ontwerpen van rozenkransen is daarom een lastig metallurgisch proces dat zoveel mogelijk wordt vermeden, omdat er altijd de mogelijkheid is om zwakte of gietfouten te introduceren bij het gebruik van een rozenkrans.
Maar chaplets zijn soms de enige manier om bepaalde structuren in een gietstuk te creëren. Zandkernen hebben de neiging om op het vloeibare metaal te drijven, soms zo hoog dat ze breken. Chaplets die boven en onder zijn geplaatst, kunnen helpen de kern in de juiste positie te houden. Het bovenste kroontje moet sterker zijn, om de druk van metaal en gas die in de mal omhoogduwen, tegen te gaan.
Zand maken met kracht
De neiging van de kern om te drijven is een van de redenen waarom een nauwkeurig begrip van de mechanische sterkte van het kernzand belangrijk is. Tests van schuif- en treksterkte die worden uitgevoerd op kernzand zijn vergelijkbaar met de tests die worden onderzocht in ons artikel over gieterijzand. Als de afschuifsterkte van het zand lager is dan die van de druk die wordt gecreëerd door het vloeibare metaal dat de mal vult, kan de kern splijten en een vervorming in het gietlichaam veroorzaken.
Bindmiddelen vormen een groot deel van het kernzandproductieproces. Groene zandkernen zijn gemaakt van standaard vochtige vormzandmengsels en een bindmiddel, zoals dextrine. Kernen van dit type zijn erg kwetsbaar en kunnen worden gemaakt met een prieel of binnendraden om het hanteren te vergemakkelijken. Droge zandkernen bevatten geen water. Ze zijn gemaakt van kwartszand en een bindmiddel om het oppervlak te verharden.
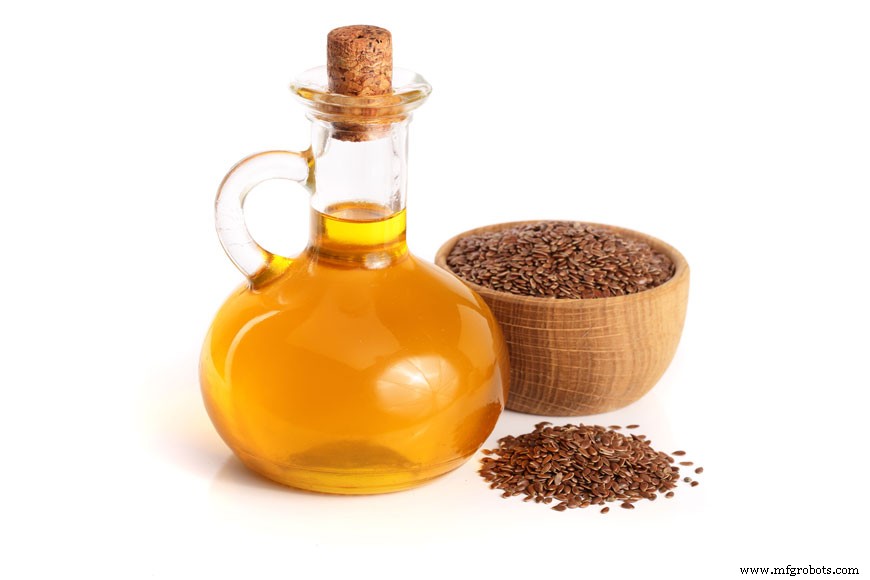
Vanaf de jaren tachtig vond er een transitie plaats in de technologie van kernbindmiddelen. Al honderden jaren kernolie was de traditionele kernbinder - en wordt nog steeds een deel van de tijd gebruikt. Lijnolie gemengd met kleinere hoeveelheden hars en een verdunner, zoals hoogwaardige kerosine, zou worden toegevoegd aan droog gietzand om kernzand te creëren. Additieven zoals maïsmeel, dextrine, bijproducten van papierfabrieken of eiwitbinders kan worden toegevoegd om de kern te versterken. Deze zouden meestal verbranden in de hoge hitte van het gieten, waardoor de kern instortte en gemakkelijk eruit kon worden geschud. Andere traditionele bindmiddelen waren onder meer koolteerpek en petroleumpek, bijzonder stabiel voor grote kernen. Hout en gomhars werd traditioneel ook gebruikt om de samenvouwbaarheid van de kern te verbeteren, hoewel deze harsen de neiging zouden hebben om te klonteren bij hitte en vochtigheid. Veel van deze traditionele verbindingen zijn vervangen door synthetische opties, zodat de gewenste eigenschappen behouden blijven, maar de uitdagingen worden weggenomen.
Moderne gieterijen hebben daarom schonere kernproductieprocessen die een betere luchtkwaliteit ondersteunen en gemakkelijker te implementeren zijn op de gieterijvloer. Deze synthetische "chemical set"-kernen bieden verschillende voordelen, waaronder bakken op lage temperatuur, gemakkelijk instorten tijdens het uitschudden en minder uitgassen tijdens het proces van het maken van de kern.
Tegenwoordig zijn de meest gebruikte kernbinders kunststoffen van het ureum - en fenol-formaldehyde groepen en furaanharsen . Er zijn drie categorieën harsbindmiddelprocessen: koude zetting , cold-box/gasgehard , en warmharden methoden.
Koude stand processen beginnen uit te harden nadat het laatste additief in het zand is geroerd, zoals cement dat doet. Het zijn chemisch zelfinstellende processen. Gebruikelijke voorbeelden zijn furaanharsen en fenol-formaldehydeharsen die door zuur worden gekatalyseerd. Ze beginnen uit te harden nadat sulfonzuur in het zand is geroerd. Timing is belangrijk voor deze processen:het zand kan niet zo langzaam hard worden dat het de productie verstoort, en ook niet zo snel dat het moeilijk is om de reactie te beheersen.
Cold-box of gasgeharde processen voer een gas in de kerndoos in dat chemisch reageert om het kernbindmiddel te harden. Zand verrijkt met furaanharsen of epoxy's kan bijvoorbeeld worden uitgehard door SO2 toe te voegen. . Waterglas, of natriumsilicaat, kan worden gehard met behulp van de CO2 proces.
Heethardend methoden zijn afhankelijk van de introductie van warmte om het kernzand in te stellen. Lijnzaadkernolie , het traditionele kernbindmiddel, wordt gezet met een heet uithardingsproces. In het shell-proces , hoeft de gieterij niet aan chemie te doen:zand komt voorgemengd of gecoat uit de verdeler en de chemicaliën in het zand zorgen ervoor dat het een harde schaal vormt tijdens het bakken. Meestal hoeven deze niet helemaal te genezen. Hotbox en warm-box methoden gebruiken furaan- of fenolharsen en een katalysator zuur-zout die uitharden wanneer de kerndoos wordt verwarmd. (Ze verschillen alleen in het type hars en de temperatuur die nodig is om in te stellen.)
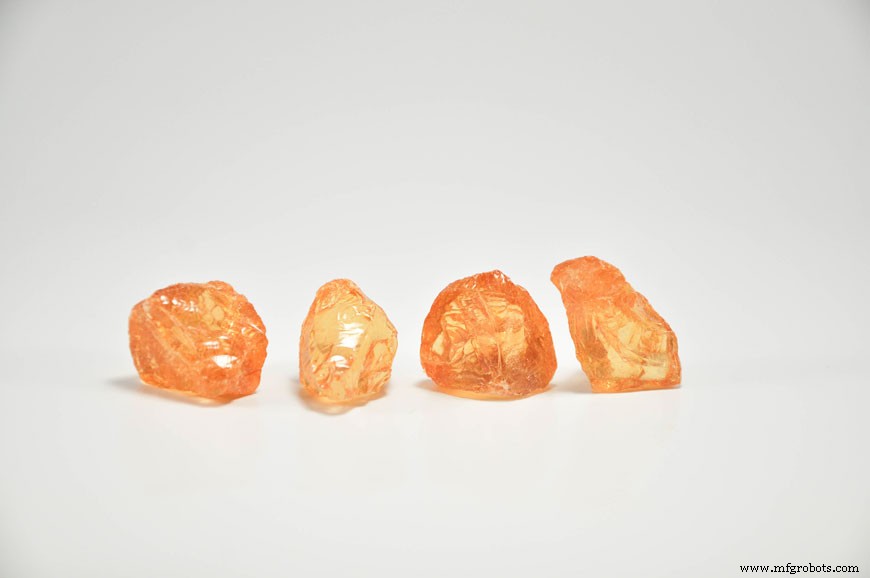
Methoden voor het maken van kernen
Kernen worden gemaakt met veel van dezelfde methoden die worden gebruikt voor zandvormen. Bovendien, kernblazers en schroeftoevoermachines worden gebruikt.
Kernblazers forceer zand in de kerndoos met perslucht van ongeveer 100 lb/in 2 . Ze kunnen worden gebruikt voor het maken van alle soorten kleine en middelgrote kernen. De geproduceerde kernen zijn zeer uniform en er worden hoge productiesnelheden bereikt.
Schroefaanvoer machines worden gebruikt om platte kernen te extruderen, meestal cilindrisch. Het kernzand wordt door een matrijs op een kernplaat geduwd. Het gebruik van deze machines is beperkt tot de productie van voorraadkernen:de lange, geëxtrudeerde cilinder die door de machine wordt gemaakt, wordt gebakken en vervolgens op de gewenste lengtes gesneden.
Kerndrogers zijn als cakevormen omdat ze de vorm van een kern ondersteunen terwijl deze zich in de kernoven bevindt bakken. Dit zijn meestal lichte skeletijzeren of aluminium dozen, waarvan de interne vorm nauw aansluit bij het kopgedeelte van de kern. Kernen die zouden afbrokkelen of waarvan delen zouden afbreken wanneer ze op een vlakke plaat worden geplaatst, gaan door de oven in een kerndroger.
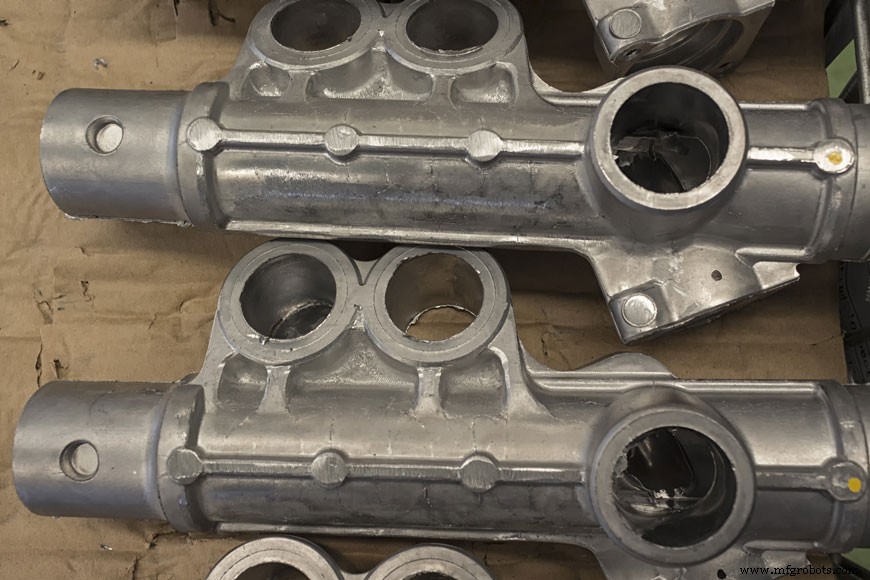
De kern plaatsen
Nadat een kern is uitgehard, wordt deze vaak met de hand afgewerkt. Langs de scheidingslijnen van de kerndoos kunnen er "vinnen" worden gearchiveerd. Soms worden kernen in meerdere delen gemaakt, als de benodigde vorm groter is dan de kerndozen en ovens die voorhanden zijn. Na de uithardingsfase wordt een gesegmenteerde kern samengesteld. Wanneer de kernen glad en samengevoegd zijn, worden ze in rekken geplaatst om te wachten op gebruik in de mal.
Kernen worden bijna altijd zorgvuldig geplaatst door gieterijarbeiders in plaats van door een machine ingebracht. Chaplets, indien aanwezig, gaan eerst naar beneden in de weerstand en dan wordt de kern geplaatst. De gieter zorgt ervoor dat de kern goed in de mal zit en vrij is van gebreken. Alle benodigde rozenhoedjes worden op de kap geplaatst en als alles er goed uitziet, wordt de kap over de sleep geplaatst en vastgeklemd.
Kerns creëren flexibiliteit bij zandgieten
Het kunnen maken en plaatsen van zandkernen is een essentieel onderdeel van het gietproces.
In sommige gevallen is de kern nodig voor het nut van het laatste onderdeel:buizen, motoren en andere mechanische apparaten moeten vaak hol zijn om te kunnen werken. Voor decoratieve artikelen kunnen kernen ook de totale metaalkosten verlagen. Vooral bij het gieten in ijzer kunnen kernen het gewicht van een eindproduct aanzienlijk verminderen. Waar de mechanische sterkte van massief staal nodig is, kan dit ongepast zijn. In andere omstandigheden is een kern echter een goede ontwerpoverweging, zelfs als dit niet noodzakelijk is voor de functie van het product.
Vorige post:GieterijzandmetaalgietprocesVolgende post:Smelten en gieten
Productieproces
- Zand
- Het belang van kerncompetenties
- De basisprincipes van statorkernlaminering in uw apparatuur
- Cyber-fysieke systemen:de kern van Industrie 4.0
- Wat zijn de verschillende soorten zandstraalzand?
- Zandgiettoepassingen voor de markt voor zwaar materieel
- Zandgieten versus spuitgieten:wat zijn de verschillen?
- Zandgiettoepassingen voor de automobielmarkt
- Wanneer kies je het harszandgietproces
- De werking van een verwarmingskern begrijpen
- Lake Erie Crushers – De toekomst van zand en grind