Tractie verkrijgen met Markforged:Overmolding en 3D-geprinte wielen gieten
Noot van de redactie:deze gastpost is geschreven door Charles Guan, afgestudeerd aan MIT Werktuigbouwkunde en voormalig MIT Machine Shop &Design Instructeur. Hij is ook de bouwer van de robotrevisie op ABC's BattleBots. Hij werkt als technisch adviseur in robotica en transport, en wordt gesponsord door Markforged om deel te nemen aan BattleBots en andere robotica-competities. Bekijk zijn website en Equals Zero Robotics voor meer!
Wielontwerp
wielen. Met meer dan 6000 jaar geschiedenis achter de rug, zou je denken dat we ze nu perfect zouden hebben gekregen. Zoals ik tijdens BattleBots seizoen 2 op de harde manier ontdekte, is dit in veel opzichten verre van waar. Je kunt het wiel zelfs opnieuw uitvinden en het verkeerd doen. Ik ontwierp Overhaul 2.0 met een krachtig en stabiel vierkant platform met zeswielaandrijving met de bedoeling om snelheid in mijn voordeel te gebruiken bij het vangen van tegenstanders in de grijper. Ik koos de wielen op basis van wat ik wist:industriële zwenkwielen van gemiddelde hardheid met loopvlakken van thermoplastisch elastomeer (TPE) die sinds het begin in robotgevechten werden gebruikt. Het was onontgonnen terrein om 16 pk-motoren door deze wielen te plaatsen in een robot die is ontworpen om in 1 seconde 30 mph te bereiken.
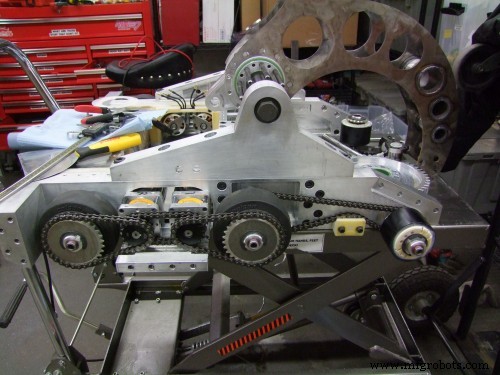
Dit werkte helemaal niet in mijn voordeel in de arena. De TPE-wielen begonnen uit elkaar te vallen en smolten letterlijk van de kracht die er doorheen werd geleid. Hun gladde loopvlak gleed over het losse puin en de deeltjes in de doos alsof de bot op ijs reed. Mijn 16 pk aan borstelloze aandrijfmotoren was daardoor vrijwel een totale verspilling. Als je mijn wedstrijd tegen Beta van het afgelopen seizoen bekijkt, zul je zien dat ik BattleBots voor een groot deel van de wedstrijd aanzag voor de D1 Grand Prix.
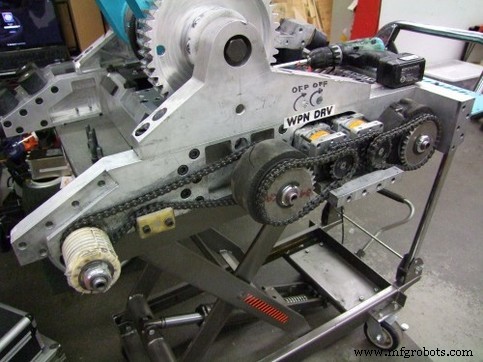
Na het BattleBots seizoen 2-toernooi bleef ik me afvragen over de volgende stappen. De wielen zouden moeten veranderen om de kracht van de bot op de grond te zetten. Hier begon ik onderzoek te doen naar gietbare rubbercompounds. Ik vond het niet erg om wat mallen te maken, het materiaal te gieten en dan aan iets anders te werken in de tijd die nodig is om uit te harden. Tijdens seizoen 2 van BattleBots had ik een aantal concurrenten – waaronder Beta – hun eigen urethaanwielen ter plaatse zien gieten.
Ik wist niets van het ontwerpen van banden en wielen, noch van gieten en gieten. Over een schot in het donker gesproken! Gelukkig had ik in de zomer een aantal vertegenwoordigers van Smooth-On-bedrijven op de Detroit Maker Faire in het nauw gedreven en uitgebreid met hen gesproken over hun gedachten over welke van hun producten geschikt waren voor het maken van tractiewielen. Smooth-On is een bedrijf dat zich voornamelijk richt op het maken en gieten van speciale effecten, kostuums en rekwisieten - niet voor industrieel gebruik. Hun distributeurs zijn echter landelijk, dus hun materialen zijn zeer gemakkelijk verkrijgbaar voor experimenten - op slechts 15 minuten rijden van Boston. De missie:leer de workflow van het gieten van hars door aangepaste wielen te produceren voor een schaalmodel van 30 pond van Overhaul dat ik destijds aan het ontwerpen was voor een wedstrijd in de herfst van 2016.
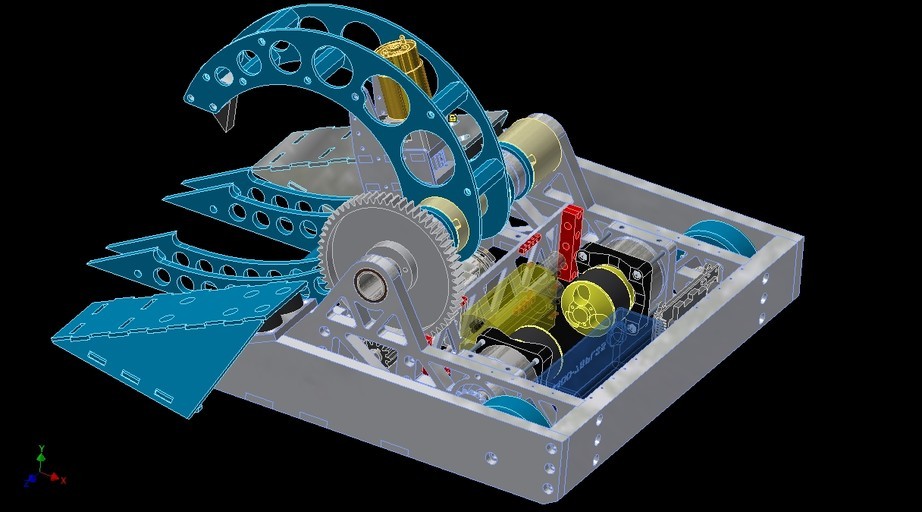
De mal ontwerpen
De vertegenwoordigers wezen me op twee materialen met een gunstig hoge scheurweerstand en treksterkte, de Reoflex- en Simpact-serie. Deze twee eigenschappen zijn wenselijk in een wielcompound, waar het rubber constant door de dikte van het loopvlak wordt geschoven en over de grond wordt gesleept. Ik kreeg een monster van ReoFlex 50 in handen (voor een durometer van 50 A, die redelijk zacht is als een schoenzool) en begon met het ontwerpen van de mal en de naaf.
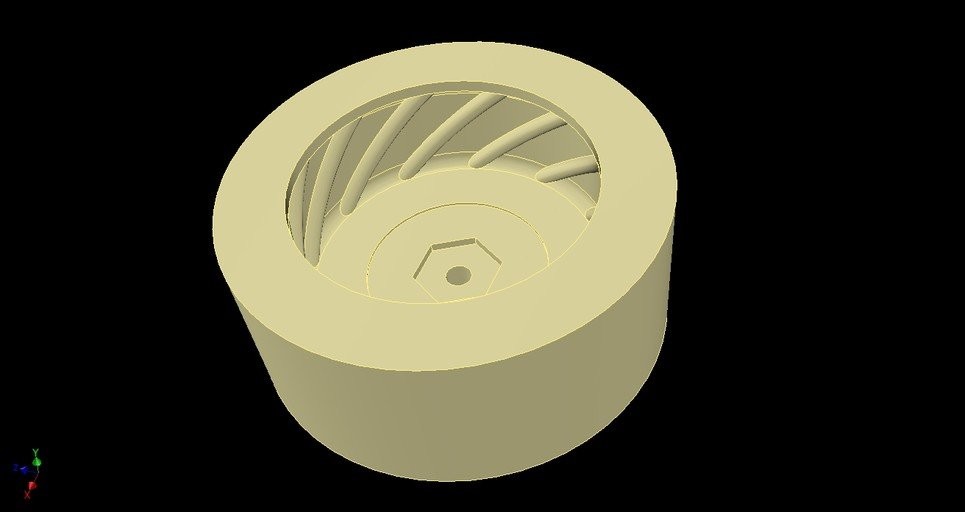
Na de prestaties van Overhaul in de doos, was ik er vrij zeker van dat er een soort vuilopruimingsfunctie op het oppervlak van het wiel nodig was. Hoewel we niet proberen water te kanaliseren of door modder te klauwen zoals bij autobanden, was er nog steeds los afval en verfvlokken uit de arena zelf om mee te kampen. Om te beginnen heb ik een eenvoudig spiraalvormig loopvlakpatroon gemaakt. Dit was op geen enkele manier geoptimaliseerd - ik wilde nu gewoon snel naar de vormfase gaan. Ik dacht dat de spiraalvormige groeven de neiging zouden hebben om vuil naar de zijkant weg te duwen, weg van het contactvlak. De exacte oriëntatie en het aantal groeven is natuurlijk nog steeds een onzekere wetenschap als je ooit banden hebt gekocht.
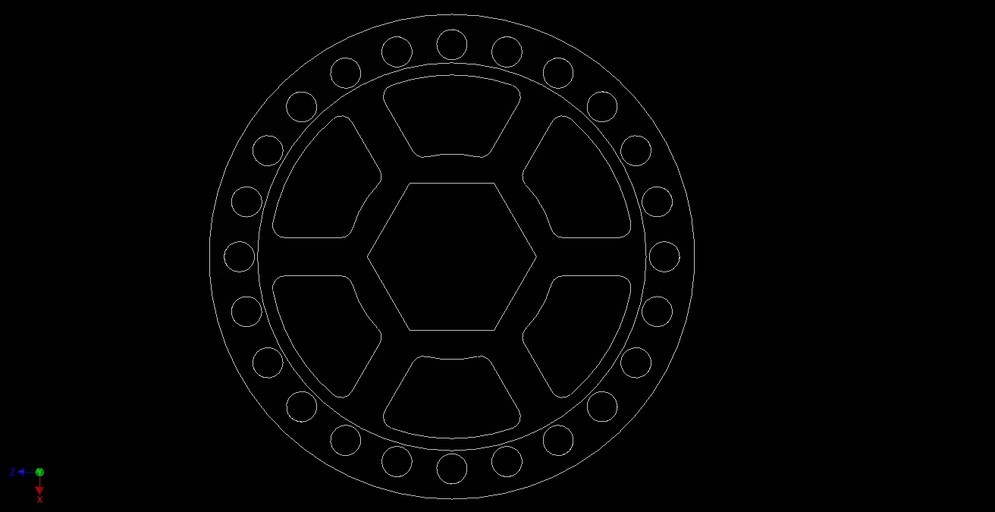
Vervolgens stond ik voor de taak om de wielnaaf te ontwerpen. Ik nam een kijkje in mijn doos met scooter- en skateboardwielen voor inspiratie. Ze hadden allemaal een gemeenschappelijk kenmerk:doorlopende gaten of sleuven waar het urethaan omheen en in stroomde. Ik was er erg op gebrand om ervoor te zorgen dat het loopvlakmateriaal op de naaf kon blijven, zelfs als de hechting mislukt. Ik heb een vrij eenvoudige cilindrische naaf gemodelleerd, maar met veel doorgaande gaten in een taps toelopende centrale rib om een maximale oppervlakte en doorsnede te geven waar het urethaan aan kan blijven kleven. Ik koos voor Onyx boven gewoon nylon voor de naaf vanwege de hogere stijfheid en sterkte, rekening gehouden met hechtingseigenschappen. Door de verhoogde stijfheid zou ik de wielnaaf lichtgewicht kunnen maken, terwijl de hars beter zou hechten aan de microscopisch ruwe textuur van Onyx dan glanzend nylon.
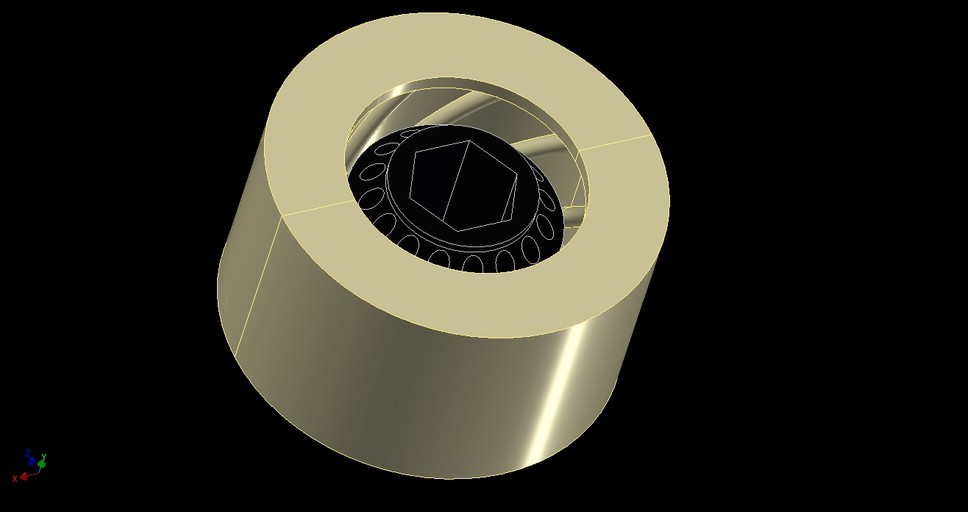
Omdat de Tiny Overhaul ook wat kleinere voorwielen nodig zou hebben, heb ik de parametrische functies van Autodesk Inventor gebruikt om snel een 2-inch model te genereren. Deze mal had een vrij smal gebied om doorheen te gieten, dus ik was geïnteresseerd in hoe het materiaal zich zou gedragen.
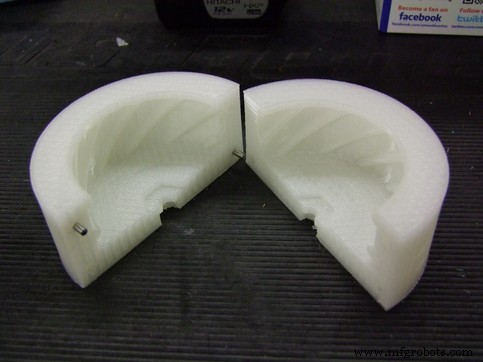
Ik heb een testmal geprint met gewoon niet-versterkt nylon op de Mark Two. De mal was erg schaars - 4 muren en 4 dak- en vloerlagen, maar slechts 25% vulling, gedrukt op de grofste laaginstelling van 0,2 mm. Ik heb de gaten van de registratiespeld in de helften gemodelleerd om uitlijning te garanderen.
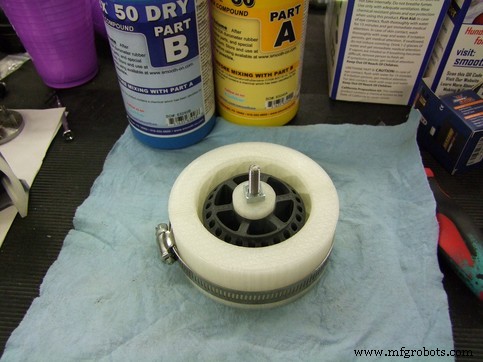
De mal gieten
De malhelften zijn ontworpen om bij elkaar te worden gehouden met een enkele gewone slangklem. Binnenin zit de wielnaaf op een adapterbus om hem gecentreerd in de mal te houden, en deze adapterbus heeft een doorgaand gat naar de onderkant van de malhelften, zodat ik een borgmoer en bout verticaal kan draaien om de onderkant af te dichten van de wielnaaf tegen de mal. Voordat ik dit in elkaar zette, heb ik de malhelften gecoat met spray-on mal release.

Op advies van vrienden die meer ervaring hadden met gieten en gieten, leende ik een vacuümpot om alle luchtbellen uit de gemengde hars te trekken. Smooth-on adverteert hun harsen als "minimaliseren van ingesloten lucht", maar kijkend naar het mengsel dat overkookte, bleek dat dit minder dan effectief was. Opgesloten luchtbellen zouden de integriteit van het loopvlak van het wiel verminderen, omdat dit veel onderbrekingen in het materiaal zou veroorzaken. Ik heb de beker met gemengd materiaal ontgast in plaats van de hele mal met vloeibare hars in de kamer te plaatsen, omdat alle lucht in de malhelften als ze hol worden bedrukt, ze waarschijnlijk zou vervormen of zelfs zou lekken en langzaam naar buiten zou borrelen.
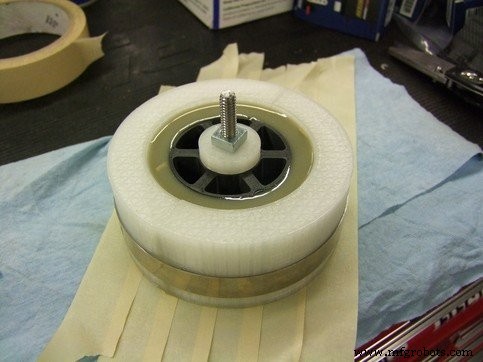
Het duurde ongeveer 2 minuten om de 3-inch wielvorm te gieten - ik hield de mengbeker net genoeg gekanteld om een continue vloeistofstroom te behouden, zodat de hars op de bodem kon zakken en zich niet ophoopte of over de vorm kroop. Door de hars "zijn waterlijn te laten vinden" voorkom je dat er grote luchtbellen in het onderdeel blijven zitten.
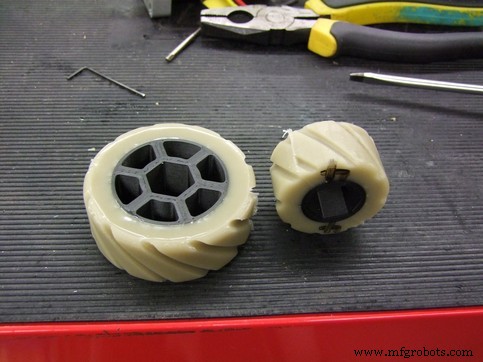
Ik schonk zowel een 3 "wiel als een 2" wiel als een startbatch. Nadat de eerste twee wielen in ieder geval solide waren geworden, was het tijd om wat productie aan te gaan. Ik heb extra mallen geprint zodat ik 4 of meer wielen tegelijk kon schenken - een van mijn mengbekers was perfect voor twee 3″ wielen en twee 2″ wielen, dus dat werd de standaard.
Het uithardingsproces
De meeste harsfabrikanten adviseren een aanvankelijke langzame uitharding bij kamertemperatuur en daarna het materiaal daarna te verwarmen om de polymeerverknopingen meer te versterken. In de datasheet van Reoflex 50 staat bijvoorbeeld dat het materiaal 4 tot 8 uur moet worden verwarmd tot 65 graden Celsius. Ik gebruikte een verwarmde kamer van ongeveer 70 graden Celsius:de nieuwe wielen die voortkwamen uit deze door warmte versnelde kuur waren absoluut taaier en veerkrachtiger om aan te raken.
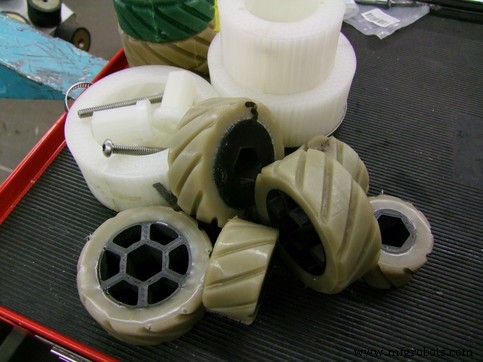
Het resultaat na een week experimenteren was een half dozijn van elke maat wiel. Ik had mijn voorraad ReoFlex 50 doorgenomen, dus ik besloot dat dit een goede plek was om te stoppen en ervoor te zorgen dat de wielen echt in competitie werkten voordat ik meer geld aan materiaal uitgaf. Ik kwam de afgelopen dagen in een mooie cyclus terecht - ik zou de vormen gieten zoals het laatste wat ik 's avonds deed voordat ik wegging, ze' s morgens uit de vorm halen en ze vervolgens in de loop van de dag bakken.
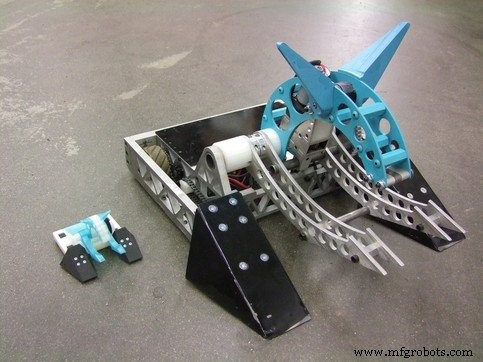
En zo zien ze eruit als ze in de bot zijn geïnstalleerd. Als je geïnteresseerd bent in de ontwikkeling van "30-Haul", zoals we het noemden, kun je de build-thread bekijken op mijn website.
Dus wat nu? Nu ik het productieproces heb verkend en een basisontwerp voor me heb, is het tijd voor de echte wetenschap. Blijf op de hoogte voor deel II van deze serie, waar ik wielen van verschillende samenstellingen probeer te maken en hun tractie test op een geverfde stalen vloer. Voor nu, dit is hoe deze wielen eruit zagen na een paar harde rijwedstrijden!
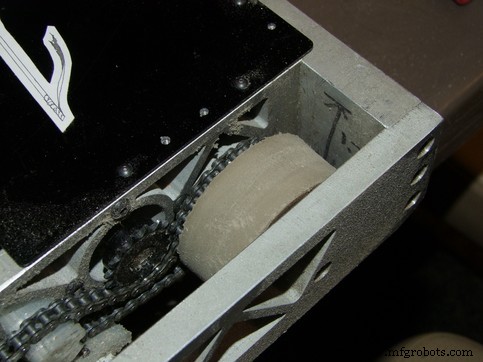
Lees meer over Markforged-printers en hoe ze bij uw toepassingen passen!
3d printen
- Interview met een expert:Spencer Wright van pencerw.com en nTopology
- 3D-geprinte onderdelen afwerken met… kleurpotloden?
- Interview met een expert:Ibraheem Khadar van Markforged
- Stratasys werkt samen met GrabCAD en e-Xstream
- Stratasys blaast MakerBot nieuw leven in met de methode
- Zandgieten met FDM-technologie
- Betere kwaliteitscontrole met 3D-geprinte onderdelen
- Blijf jezelf vast met functionele 3D-geprinte onderdelen!
- De Go Kart opnieuw vormgeven met 3D-geprinte onderdelen
- Grip krijgen met een 3D-geprint stuur
- Prototyping en productie op korte termijn met spuitgieten