Interview met een expert:Spencer Wright van pencerw.com en nTopology

Bijna iedereen die betrokken is bij de productiewereld heeft ooit de blog of de productie-nieuwsbrief van Spencer Wright gelezen. Spencer is een jarenlange expert op het gebied van workflows voor de productie van metalen additieven en hoofd van research &partnerships bij nTopology. Spencer was zo vriendelijk om met RP Platform om de tafel te gaan zitten om zijn achtergrond in zowel AM als conventionele productie te bespreken, zijn huidige werk bij het ontwerpen van geoptimaliseerde workflows en hoe hij het vakgebied in de nabije toekomst ziet evolueren.
Hoe raakte u oorspronkelijk geïnteresseerd in 3D-printen?
Ik raakte geïnteresseerd in het printen van metaal, gewoon omdat het cool klonk!
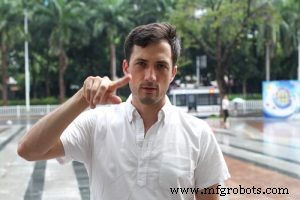
Mijn achtergrond ligt in de traditionele productie. Ik ben een projectmanager, productmanager, een behoorlijk fatsoenlijke mechanische ontwerper ... Ik heb een aantal jaren aangepaste fietsframes gebouwd. Daarna werkte ik in een prototyping-winkel waar we elektromechanische assemblages ontwikkelden, dus ik deed wat ervaring op met het ontwerpen van embedded systemen.
Ik verhuisde in 2012 naar New York en deed een stap terug en dacht na over waar ik me op wilde concentreren, terwijl ik bleef werken aan conventioneel vervaardigde spullen. Maar ik was op zoek naar iets anders. Destijds waren Makerbot en Shapeways erg groot in de hardwarescene van New York. Beiden zijn echt interessante bedrijven, maar met een achtergrond in mechanische dingen - structurele, functionele dingen - werd ik nieuwsgierig en hoorde over een aantal verschillende metaalprinttechnologieën. Dit was rond dezelfde tijd dat GE Morris overnam, wat hier in de VS veel ophef maakte. Ik raakte bevriend met een aantal mensen die in een strategiebedrijf met de naam Undercurrent werkten, dat op dat moment veel met GE werkte, en uiteindelijk fulltime bij hen terechtkwam.
Het was door dat werk dat ik me bewust werd van metaalpoederbedfusie. Er was veel marketing over hoe 3D-printen X, Y en Z zou veranderen, maar ik dacht:"Laten we hier wat context krijgen". We hebben extreem stabiele productieprocessen. We hebben extruderen, we hebben gieten, we hebben smeden, we hebben machinale bewerkingen... Dit zijn industrieën van meerdere miljarden dollars. Hoe verhoudt metaaldruk zich daarmee?
Dus ik begon het te onderzoeken en ontdekte dat deze printers ongeveer $ 1 miljoen kosten, wat veel geld leek in vergelijking met een CNC-frees. Dus de vraag was:"Wat kunnen ze afdrukken?" De bouwplatforms waren ongeveer zo groot als een broodtrommel, dus wat is een hoogwaardig onderdeel dat in een broodtrommel past en zou kunnen profiteren van een laag gewicht of een aantal interessante ontwerpelementen?
Het grootste deel van de metaaldrukindustrie tegenwoordig bestaat uit onderdelen voor ruimtevaart, of medische implantaten, of olie en gas, maar het antwoord dat ik bedacht was fietsonderdelen. Het is eigenlijk een geweldige industrie, omdat mensen veel geld zullen betalen voor iets dat net iets lichter is of iets beter past. Als je een onderdeel kunt printen dat er echt uniek uitziet, dat is duidelijk futuristisch, daar houden mensen van.
Ik wist niets van de technologie af, maar ik wist hoe ik onderdelen moest ontwerpen, ik wist hoe ik onderdelen moest vinden en ik wist hoe ik vragen moest stellen. Dus ik gebruikte die drie vaardigheden (en het feit dat ik een blog en een nieuwsbrief had, wat een groot gat in de markt was) en bleef eraan werken. Ik ontwierp en printte onderdelen, schreef erover en het werd gewoon een ding. Terwijl ik aan dingen werkte, kreeg ik steeds meer telefoontjes uit het niets van mensen in bedrijven als Siemens en Philips, die hier veel beter in zijn dan ik. Het zorgde ervoor dat mijn stem naar buiten kwam en het gaf me toegang tot mensen bij deze bedrijven, zodat ik vragen kon stellen en erachter kon komen wat ze doormaakten.
Rond die tijd ben ik uiteindelijk op zoek gegaan naar iets anders in mijn carrière. Ik besloot me fulltime te concentreren op productie- en ontwerpworkflows, dus nu werk ik bij nTopology, dat ontwerpsoftware maakt voor industrieel 3D-printen. Het meeste van wat ik doe, is uitzoeken hoe onze software in de rest van de gereedschapsketen past. Hoe traceren we de workflows van onze klanten gedurende deze hele cyclus en maken we die ervaring beter?
Het lijkt alsof je achtergrond in traditionele productie betekent dat je 3D-printen op een veel organischere manier benadert dan veel mensen doen:beginnen met een probleem en 3D-printen identificeren als het juiste hulpmiddel om het op te lossen. Bent u het daarmee eens?
Ja zeker. Ik zal opmerken dat het tegelijkertijd mijn interesse is om de juiste technologie voor de baan te gebruiken. Ik ben constant aan het sleutelen aan ontwerpprojecten. Ik print er een aantal, maar ik CNC er ook een paar. Ik krijg wekelijks mensen die me een e-mail sturen met de mededeling dat ze een bedrijfsidee hebben en dit in 3D willen printen. Mijn vraag is altijd:"Waarom wil je het afdrukken?"
Dit is echt uniek aan het printen van vandaag, en ik denk dat de technische pers misschien niet geweldig werk heeft geleverd door vast te stellen waarom iemand ooit een gedrukt onderdeel zou willen. Er zijn veel verhalen die zeggen:"We gaan X drukken en het zal geweldig zijn", maar ik denk dat de pers er niet goed in is geweest om zich af te vragen hoe dat voor iemand een voordeel zou zijn. Als ik iets zoek, maakt het me niet uit of het gedrukt is. Het maakt consumenten niet uit of dingen worden geprint en het maakt bedrijven zeker niet uit. Waar ze om geven, is of dit product beter presteert, minder kost of gemakkelijker verkrijgbaar is.
Het komt erop neer dat printen voor de overgrote meerderheid van de onderdelen geen goede oplossing is. Voor iets dat lichter moet zijn, is dat het geval, omdat u interne doorgangen kunt opnemen en de montage kunt vereenvoudigen. Dat zijn echte voordelen. Voor mij was het het uitzoeken van die toepassingen en de heuristieken die we kunnen gebruiken om naar een industrie te kijken en erachter te komen of het een goede gok is voor afdrukken.
Mijn advies aan mensen is:probeer uw aanvraag niet in druk te persen. Er zijn echt goede dingen om af te drukken en daar moeten we ons op concentreren.
Wat zouden hiervan de laatste tijd goede voorbeelden zijn?
We werken in een paar primaire industrieën. In al deze verschillende industrieën ontwerpen we roosterstructuren [lichtgewicht] die de exacte mechanische eigenschappen hebben die onze klanten willen.
De grootste is de ruimtevaart - raketten en ruimteschepen - waar de regelgeving erg ingewikkeld is. Er zijn grote vragen over hoe je onderdelen inspecteert en zorgt dat ze bijvoorbeeld na X aantal vlieguren nog goed zijn. Lucht- en ruimtevaart heeft de strengste eisen, dus als je daaraan kunt voldoen, kun je meestal ook voldoen aan de behoeften van andere industrieën!
We hebben ook een grote aanwezigheid in medische implantaten, waar de ontwerpbehoeften heel verschillend zijn, maar nog steeds zeer sterk gereguleerd zijn. We werken ook samen met veel consumententechnologiebedrijven, die onderdelen maken die op een bepaalde manier energie opnemen. Schoenenbedrijven zijn er erg open over, maar er zijn andere sportkledingbedrijven die dingen als opvulling onderzoeken. Wanneer iemands lichaam ergens tegenaan botst, wil je die energie absorberen, zodat het niet naar hun botten wordt overgebracht. Schuim is daar prima in, maar je kunt verschillende structuren gebruiken om energie naar buiten af te voeren, in plaats van via de pad.
Vindt u dat er veel leercurves zijn wat betreft de workflows van bedrijven, vooral wanneer er meerdere softwareplatforms bij betrokken zijn?
Deze zijn behoorlijk ingewikkeld. Soms merk ik dat ik tegelijkertijd $ 50.000 aan technische software op mijn computer heb staan! Het goede nieuws is dat waar je ook aan werkt, of het nu raketonderdelen of schoenen zijn, het kaliber van de software dat we zien meestal vrij gelijkaardig is. Er zijn een half dozijn CAD-programma's die onze klanten doorgaans gebruiken, en daarnaast zijn er een handvol verschillende analysepakketten en productiesoftwareplatforms.
Hoewel er verschillen zijn, lijken de algemene vereisten erg op elkaar. Dit zijn serieuze engineeringbedrijven met serieuze behoeften, dus je moet traceerbaarheid behouden, je moet voldoen aan de regelgeving, je moet documentatie hebben en je moet analyseresultaten kunnen traceren, wat lastig kan zijn.
De realiteit is dat hoewel de wereld van engineeringsoftware relatief volwassen is, productiesoftware dat niet is. De pakketten die bedrijven gebruiken (voornamelijk Autodesk Netfabb en Materialise Magics) bestaan nog niet zo lang, in het grote geheel der dingen. Elk jaar worden ze bijgewerkt met behoorlijk significante verschillen. Bovendien heb je bestandsformaten die voortdurend veranderen, dus het kan ingewikkeld worden.
Wat ziet u als het antwoord om dit alles te stroomlijnen?
Op dit moment is onze focus om dit proces zo soepel mogelijk te laten verlopen. Uiteindelijk is het gebied waar we dat het meest kunnen beïnvloeden, binnen onze software, Element. We kunnen die ervaring geweldig maken. Binnen deze branche is dat lastig. Wat zijn de bestandsindelingen die u gaat gebruiken om van CAD naar Element naar uw buildprocessor te gaan? Op dit moment is het STL, wat een rommelige bestandsindeling is.
Lattice-structuren kunnen miljoenen balken hebben. Wanneer u STL gebruikt, beschrijft u het oppervlak van die structuur met driehoeken. Voor elke balk heb je minimaal misschien tien driehoeken, hoewel we in de meeste gevallen vinden dat het beter is om ten minste 50 driehoeken te gebruiken. Met een miljoen stralen betekent dit bestandsgroottes die gewoon krankzinnig zijn.
Het is gewoon niet praktisch om geometrie op die manier te beschrijven, en dus gebruiken we binnen Element helemaal geen mozaïekpatroon. We gebruiken een grafiekstructuur, dus elke straal gaat van de ene knoop naar de andere. Elke knoop heeft een X-, Y- en Z-locatie en een straal die eraan is toegewezen. De liggers verbinden dan die knopen. Met een relatief kleine hoeveelheid informatie kunnen we ontwerpen laten zien die veel, veel balken hebben. We maken op die manier ontwerpen binnen onze software, daarna gebruiken we een open-source bestandsspecificatie waarmee je ze kunt exporteren en je eigen slicers en oriëntatiehulpmiddelen kunt gebruiken.
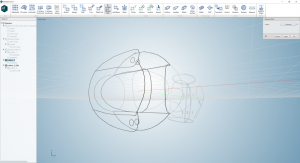
We werken eraan om dit te integreren in de 3MF-bestandsstandaard. Het doel is om een veel eenvoudigere bestandspresentatie te hebben om roosters te communiceren. Dit betekent op zijn minst dat als je een bestand moet e-mailen, je geen 20 minuten wacht voordat het is geüpload. De bestandsoverdracht is eenvoudiger en de weergave is een stuk eenvoudiger, omdat de vereenvoudigde geometrie betekent dat uw CPU niet zo hard werkt. Die voorstelling kunnen we ook prima snijden. We kunnen dit ook rechtstreeks in uw FEA-software importeren, zodat we straalanalyse kunnen uitvoeren - wat veel gemakkelijker is dan het gebruik van vaste elementen.
Hoe ziet u de acceptatie van dit nieuwe bestandsformaat?
Eerlijk gezegd maak ik me er niet zo'n zorgen over. We hebben eerder horten en stoten gezien in bestandsformaten, maar voor ons is er zo'n duidelijk voordeel aan dit formaat dat ik vermoed dat het heel snel zal veranderen. De meeste afdrukbestandsindelingen gebruiken nog steeds driehoeken, wat betekent dat de geometrische representatie allemaal binnen hetzelfde paradigma bestaat. 3MF heeft ook driehoekige geometrie (het is om een aantal andere redenen een beter formaat), maar we voegen daar een compleet andere representatie aan toe, zodat we hetzelfde deel kunnen weergeven met een veel kleiner bestand. Ik vermoed dat de voordelen daarvan veel groter zullen zijn dan de moeilijkheden.
Ziet u maatwerk voor de specifieke behoeften van klanten als een sleutelfactor voor succesvolle software voor AM?
Ja en nee. Wij zijn een productbedrijf. We verkopen een product dat we hebben gebouwd voor de meest veeleisende gebruikers en proberen hier de best mogelijke versie van te maken. Een consistente aanpak van problemen maakt de ervaring aanzienlijk beter. Voor de meer marginale CAD-toepassingen is wat vaak gebeurt, is dat een klant zegt:"We zijn dol op de functies, maar we zouden echt willen dat er overal contextmenu's waren". Het CAD-bedrijf wil de verkoop echt, dus geven ze hen de contextmenu's. Binnen een paar maanden krijg je overal contextmenu's, ze werken goed en ze krijgen een grote uitverkoop.
Over een jaar komt er iemand anders langs en zegt:"We houden van je software, maar we willen echt een beter mapsysteem met opdrachten, omdat de contextmenu's niet echt werken voor onze technici". Het CAD-bedrijf besteedt daar zes maanden aan, en dan heb je twee manieren om precies hetzelfde te doen. Wat je uiteindelijk krijgt is een stukje software dat schizofreen is.
We hebben de neiging om de voorkeur te geven aan een enkele interactie. Elke nieuwe functie die we introduceren, wordt op dezelfde manier aangepakt en is consistent in de hele workflow. We luisteren naar wat onze klanten echt nodig hebben en bedenken iets dat past in ons raamwerk voor het beheren van interacties, maar ook in die behoeften.
Maar daar komt nog bij dat de behoefte aan flexibiliteit in workflows zeker een punt is. Met het nieuwe bestandsformaat hebben we het zo geschreven dat het voor iedereen heel gemakkelijk is om het te pakken, te manipuleren en te begrijpen wat er aan de hand is.
Hoe zit het met het stroomlijnen van AM-workflows? Welke manieren heb je gevonden om de algehele processen strakker te maken en het aantal verbroken verbindingen te verminderen?
Dat is moeilijk. Uiteindelijk, als je naar onze ruimtevaartgebruikers kijkt, stuiter je constant tussen verschillende dingen. Zelfs met een relatief eenvoudig onderdeel, krijg je een onderdeelnummer, dan versie 2, versie 3 etc. en het explodeert als het ware. Een ding dat we hebben gedaan, is om meerdere versies van hetzelfde ontwerp in één bestand toe te staan. Je kunt in verschillende richtingen uitwijken, maar houd dat allemaal binnen hetzelfde eigenlijke bestand, wat enigszins helpt.
Uiteindelijk is interoperabiliteit echter belangrijker dan stroomlijnen. We hebben veel nagedacht over het maken van een eenvoudigere versie van Element als plug-in voor andere CAD-software, maar dan werken we met de geometriekernel en gebruikersinterface van iemand anders. Het op maat maken van die dingen is moeilijker dan het doen in je eigen stukje software. Kies je daarnaast voor de meest populaire CAD-software en bouw je daarvoor? Kies jij degene die je klanten gebruiken?
Dus voorlopig hebben we ervoor gekozen om onze flexibiliteit te behouden. U importeert in onze software, maar we zullen dat proces zo eenvoudig mogelijk maken. We weten dat als we het meeste werk in onze software houden, we een goede gebruikerservaring kunnen garanderen.
Hoe ziet u dit alles in bredere zin evolueren?
Ik ben enthousiast over het steeds volwassener worden van metaalprinten. Mensen hebben een eeuw van metaal snijden onder onze riem. We hebben dit veel gedaan en we zijn er goed in. Het is herhaalbaar en betrouwbaar, dus ik hoef niet te weten op welke machine een onderdeel is gemaakt. Bij metaalprinten is dat helemaal anders. Het is niet zo herhaalbaar, dus als ik met hetzelfde bestand naar verschillende fabrikanten ga, zullen ze het op verschillende manieren opbouwen en krijgen we een ander resultaat. Ik hoor mensen praten over hoe we meer materialen of snelheid nodig hebben, en die dingen zijn belangrijk, maar wat ik echt wil is volwassenheid. Dat is waar ik erg enthousiast over ben.
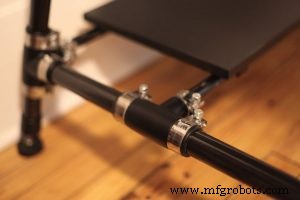
We hebben veel moeite gedaan om ontwerpbeperkingen in onze software in te bouwen. Als je iets ontwerpt in Photoshop, heeft het een kleurenpalet dat je op je ontwerp toepast. Ze laten je geen kleuren kiezen zoals ultraviolet, omdat je ze niet kunt zien, dus het heeft geen zin om iets op die manier te ontwerpen! Met CAD-software is het eenvoudig om dingen te ontwerpen die niet maakbaar zijn. Onze belangrijkste focus is om onze gebruikers te helpen begrijpen wat wel en niet te produceren is en om die intelligentie in de software in te bouwen, zodat ze realtime feedback krijgen over hoe hun ontwerp wordt afgedrukt.
Het is echt moeilijk voor ons om dat te doen in een wereld waar niet alleen machines onderdelen anders printen, maar de fabrikanten ook geen specificaties publiceren over wat er kan worden geprint. Wat ik echt wil, is dat machinefabrikanten API's publiceren die je feedback geven over bedrukbaarheid en aangeven waar de probleemgebieden zijn.
Tot slot, wat zie je als de 'next big thing' in de komende vijf jaar?
Het is geen sexy antwoord, maar ik ben op zoek naar een betrouwbaarder, meer herhaalbaar, stabieler proces. Of ik wil op zijn minst een flow waarin mensen gekke dingen kunnen doen, maar die betrouwbare bouwtijden biedt om daar een solide basis voor te bieden.
Ik denk dat het goed is om te zien dat meer machinefabrikanten meer integratie met onderdelenfabrikanten ontwikkelen en hun eigen servicebureaus openen. Ze gaan meer leren over het printen van onderdelen en hopelijk zullen ze die intelligentie in hun machines invoeren. Tegelijkertijd zien we dat machinefabrikanten nauwer worden gekoppeld aan software.
Er is een ding dat Conway's Law wordt genoemd en dat zegt dat bedrijven de neiging hebben om systemen te bouwen die een facsimile zijn van hun eigen organisatiestructuur. Als u bijvoorbeeld een onderdeel hebt met een printplaat die is bevestigd aan spuitgieten en het werktuigbouwkundige team zich in een ander gebouw bevindt dan het engineeringteam voor embedded systemen, dan valt de PCB van het spuitgegoten onderdeel. .
Het redelijke gevolg hiervan is dat als u een naadloze end-to-end-workflow wilt, u deze teams nauwer moet integreren. Laat ze in hetzelfde gebouw werken en elkaar tegen het lijf lopen bij de waterkoeler! Dat meer bedrijven deze verschillende rollen bij elkaar brengen, is iets wat ik heel graag zie.
www.pencerw.com
3d printen
- Interview met een expert:professor Neil Hopkinson, directeur 3D Printing bij Xaar
- Interview met een expert:Philip Cotton, oprichter van 3Dfilemarket.com
- Interview met een expert:Dr. Alvaro Goyanes van FabRx
- Interview met een expert:Dr. Bastian Rapp van NeptunLab
- Interview met een expert:Ibraheem Khadar van Markforged
- Jigs en armaturen:6 manieren om de productie-efficiëntie te verbeteren met 3D-printen
- Interview met expert:Duncan McCallum, CEO van Digital Alloys over Joule Printing en de toekomst van Metal 3D Printing
- Expertinterview:Nanoe CEO Guillaume de Calan over de toekomst van keramisch 3D-printen
- Expert Interview:Ultimaker President John Kawola over de toekomst van 3D-printen
- Motorsport, Performance Racing en 3D Printing:een interview met Revannth Murugesan van Carbon Performance
- Interview met experts:Sintavia President Doug hedges op het bereiken van serieproductie met 3D-metaalprinten