High Strength 3D Printing – Isotropic Fill Part 2
Bijwerken: Als je meer wilt weten over hoe verschillende vullingen je rol op verschillende manieren kunnen versterken en over de wetenschap erachter, kom dan op 21 juni om 11 uur EDT naar een webinar (registreer je hier)!
Opmerking van de schrijver:dit is het tweede bericht van onze tweedelige serie over het ontwerpen van de sterkst mogelijke onderdelen met Eiger's Isotropic Fiber-vultype, met koolstofvezel op de Mark Two. In ons vorige bericht is de achtergrond beschreven waarom we wapening printen in ons specifieke isotrope patroon - dit bericht behandelt hoe dat vultype het beste kan worden toegepast om de sterkste onderdelen te produceren met het meest efficiënte gebruik van onze 3D-printtechnologie van koolstofvezel.
We hebben eerder de basisprincipes van composietversterking besproken, evenals hoe verschillende vezeloriëntaties in Eiger kunnen worden toegepast. Nu is het tijd om de versterkingsefficiëntie te bespreken - 3D-printen van de sterkste onderdelen zonder onnodig gewicht of kosten. Het versterken van een laag met Eiger's Isotropic Fiber-vulling zal die laag sterker en stijfheid geven - maar heb je die sterkte daar echt nodig? We gaan je laten zien dat de locatie van een laag in relatie tot de belastingen die op het totale onderdeel worden uitgeoefend waarschijnlijk de belangrijkste overweging is bij het ontwerpen voor efficiënt gebruik van wapening bij 3D-printen met hoge sterkte.
Voordat we ingaan op het daadwerkelijk versterken van iets, is het belangrijk om te begrijpen hoe fysieke onderdelen reageren wanneer een kracht of belasting wordt uitgeoefend op hun externe geometrieën. Laten we als voorbeeld eens kijken naar een eenvoudig ondersteunde balk — een balk die aan beide uiteinden van onderen wordt ondersteund met één uiteinde vrij om te vertalen langs de x as, zoals in de afbeelding hieronder.
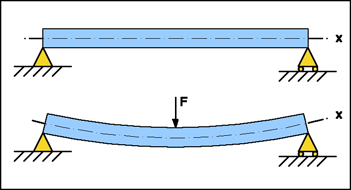
Als u een kracht uitoefent F naar de balk, zal de balk beginnen te buigen of naar beneden af te buigen, in een mate die afhangt van zowel de grootte van F als de geometrie en materiaaleigenschappen van de balk. Als je zou kijken naar de interne spanningen die worden gegenereerd door de kracht F in een representatief zijprofielgedeelte van de balk terwijl deze buigt, zou je zien dat de zijde van de balk die zich het dichtst bij de naar beneden wijzende belasting bevindt, compressie ervaart, terwijl de zijde van de balk die het verst weg is een gelijke kracht maar onder spanning ervaart.

In het bovenstaande diagram worden de interne buigspanningen beschreven σ over de dikte van de balk, waarbij een langere pijl aangeeft hoe groter de buigspanning. Het is meteen duidelijk dat de hoogste buigspanningen worden ontwikkeld aan de boven- en onderkant van de balk tijdens het buigen, waarbij de middellijn van de balk, de neutrale as genoemd, geen kracht ervaart. De tegenovergestelde richtingen van de pijlen aan weerszijden van de neutrale as geven de krachtrichting aan - compressie of spanning - die het gebied van de balk ervaart. Over het algemeen betekent dit dat als u optimaliseert voor uw gebruik van materiaal met hoge sterkte in een onderdeel dat buigt, u prioriteit moet geven aan het plaatsen van dat materiaal waar de hoogste krachten optreden - nabij het oppervlak van de balk. Dit simpele feit is de reden achter het ontwerp van I-balken en sandwichpaneelconstructie.
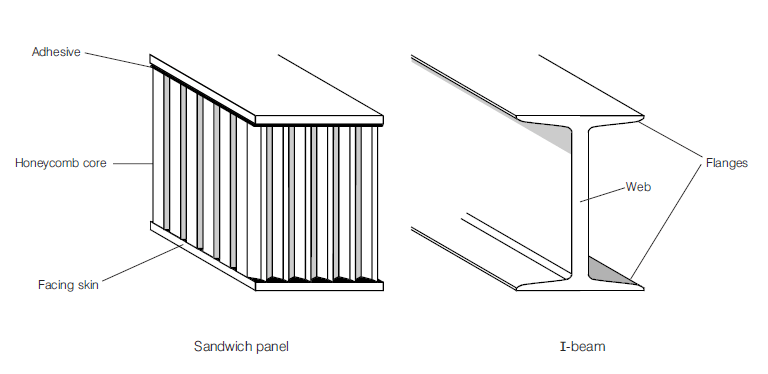
De ontwikkeling van zowel I-balken als sandwichpanelen is voortgekomen uit de wens om met een minimaal gewicht een zeer sterke, zeer stijfheidsplaat of balk te produceren. Zoals we hebben gezien, treden de grootste buigkrachten op aan de buitenoppervlakken van een balk, dus het toevoegen van materiaal met een hoge sterkte aan die oppervlakken zal de buigkrachten het best weerstaan. Nabij het midden van de balk dragen materialen met een hoge sterkte echter lang niet zo veel bij aan de algehele sterkte van de balk, omdat ze worden blootgesteld aan veel lagere krachten. Deze materialen voegen nog steeds dezelfde hoeveelheid gewicht toe, maar de algehele sterkte per gewichtsefficiëntie van gebieden nabij de neutrale as wordt echter sterk verminderd. De I-balkgeometrie is ontwikkeld om een metalen balk uit één materiaal met hoge sterkte en gewicht te bieden. De komst van geavanceerde materialen maakte de ontwikkeling mogelijk van een uit meerdere materialen bestaande sandwichpaneelconstructie, die de krachten die normaal door het I-balkweb (het verticale deel van de I-balk) worden geabsorbeerd, verdeelt over een veel groter gebied, en ook veel lichtere kernmaterialen die moeten worden gebruikt, omdat de betrokken krachten niet hoeven te worden geconcentreerd over een enkel web.
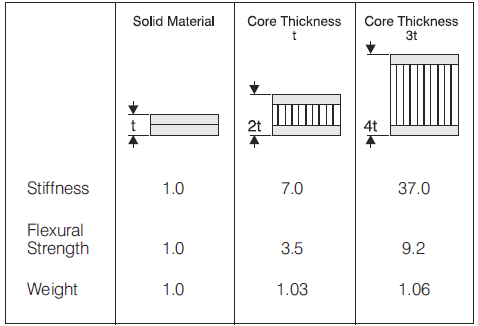
Superpositie van sandwichpanelen
Met al die theorie uit de weg, laten we een duik nemen in versterkende delen in Eiger. Standaard probeert Eiger een sandwichpaneel te genereren wanneer u glasvezel toevoegt op de externe 'Onderdeelweergave'-pagina die u voor het eerst tegenkomt bij het openen van een onderdeel uit uw Eiger-bibliotheek.
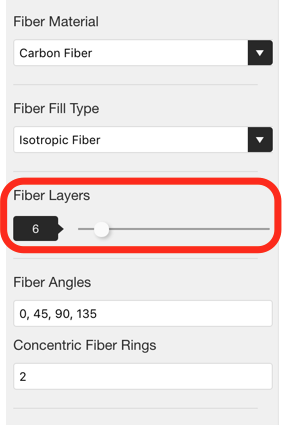
De helft van de waarde voor 'Vezellagen' die u hebt gekozen om aan een onderdeel toe te voegen, wordt automatisch toegevoegd aan de onderste lagen van het onderdeel boven de eerste vier (standaard) lagen die zijn geconfigureerd als massieve plastic vloerlagen, en de andere helft van de Vezellagen worden toegevoegd aan de bovenkant van het onderdeel, onder de bovenste vier (alweer standaard) lagen die zijn geconfigureerd als massieve plastic lagen. Dit algoritme werkt prima als het deel dat je probeert te versterken symmetrisch is rond een vlak evenwijdig aan het printbed, zoals het landingsgestel voor de Snotbot-drone die een team van Olin College heeft afgedrukt.
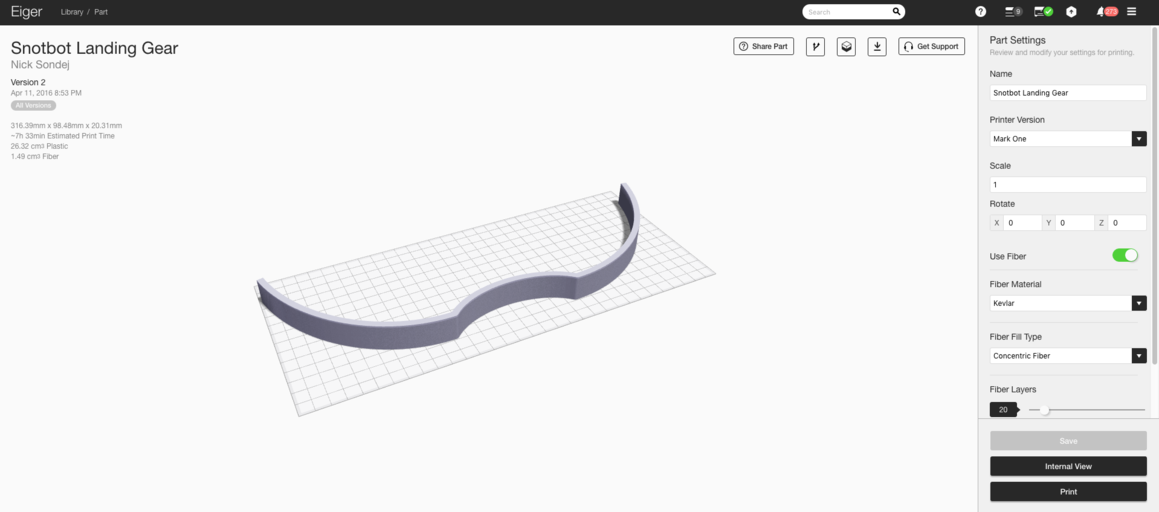
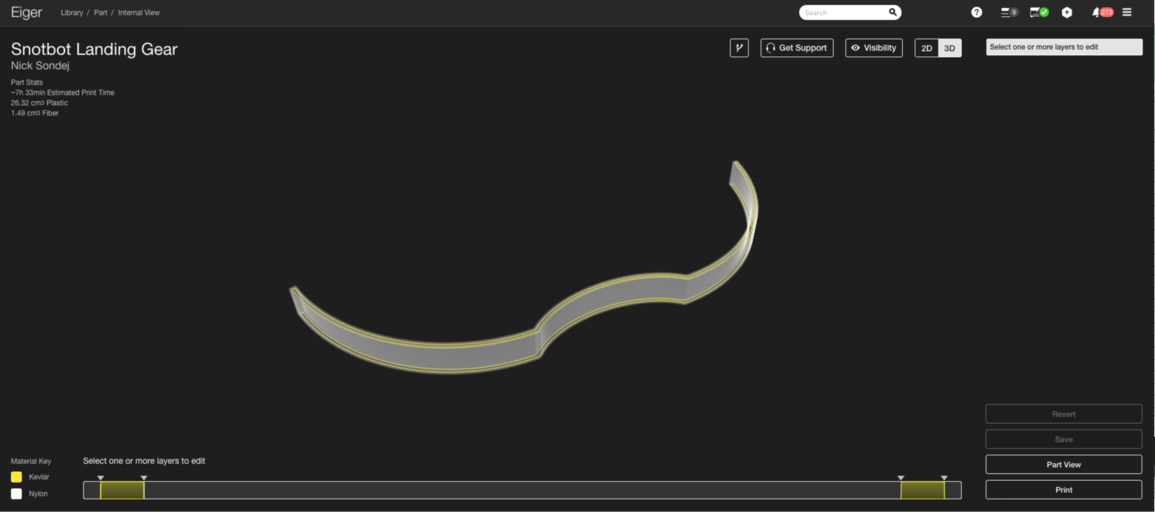
Zoals je op de bovenstaande foto's kunt zien, heeft het algoritme 10 lagen Kevlar-wapening aan de boven- en onderkant van het onderdeel toegevoegd. Aangezien het onderdeel symmetrisch is rond een XY-vlak, resulteerde het standaard vezellaagalgoritme in het gewenste gedrag, sandwichpaneelversterking.
Maar wat gebeurt er als uw onderdeel niet voldoet aan de hierboven beschreven symmetrievoorwaarde? In dat geval biedt het standaardalgoritme niet de versterking die u zoekt, zoals in het geval van het motorremhendelgedeelte dat we vaak gebruiken als krachtdemonstratie op beurzen.
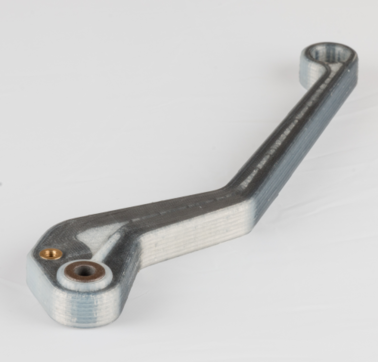
Zoals u kunt zien in de onderstaande schermafbeelding, voegt het standaardvezelalgoritme vezels toe aan de onderkant van het onderdeel, maar voegt het geen vezels toe waar het nodig is aan de bovenkant van het onderdeel om het sandwichpaneel te voltooien, omdat de kleine verhoogde rand waar het brons bus wordt ingedrukt, waardoor het onderdeel asymmetrisch is. We willen de vezels eigenlijk verder weg van de bovenste laag van het onderdeel dan van de onderkant van het onderdeel om een zo groot mogelijk sandwichpaneel te produceren.
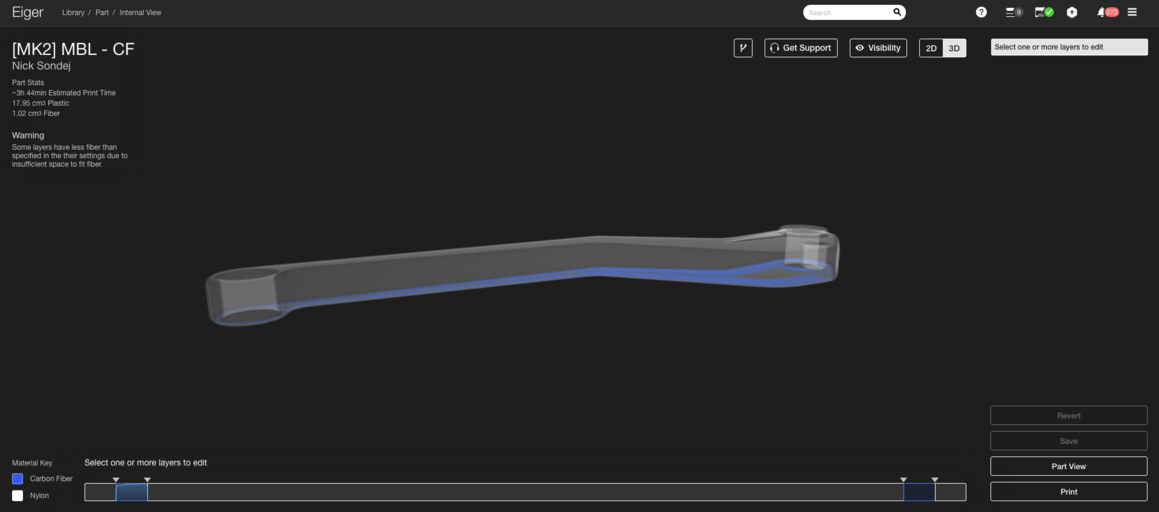
Dit brengt ons bij de eerste algemene richtlijn voor het versterken van de sterkste onderdelen op uw Markforged-printer - probeer eerst de grootste sandwichpanelen te maken die u in een onderdeel kunt maken, door Isotropische vezelvulling te gebruiken met een of twee concentrische ringen in lagen met de meeste afstand van elkaar hen.
In het geval van de motorremhendel hierboven, betekent dit dat u de bovenste laaggroep naar beneden moet verplaatsen totdat er vezels boven op het hendellichaam lopen, zoals te zien is in de volgende afbeelding.
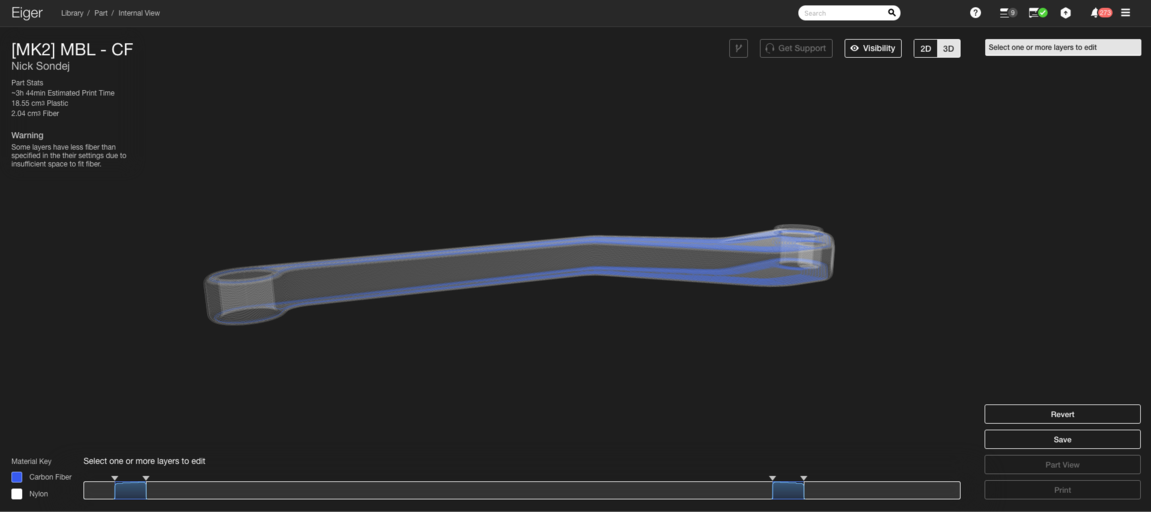
Wat gebeurt er als je meerdere, mogelijk overlappende regio's hebt die rijp zijn voor sandwichpaneelconstructie, zoals in deze crankarm uit het ontwerp van 2016 van het UW-Madison Human Powered Vehicles Team?
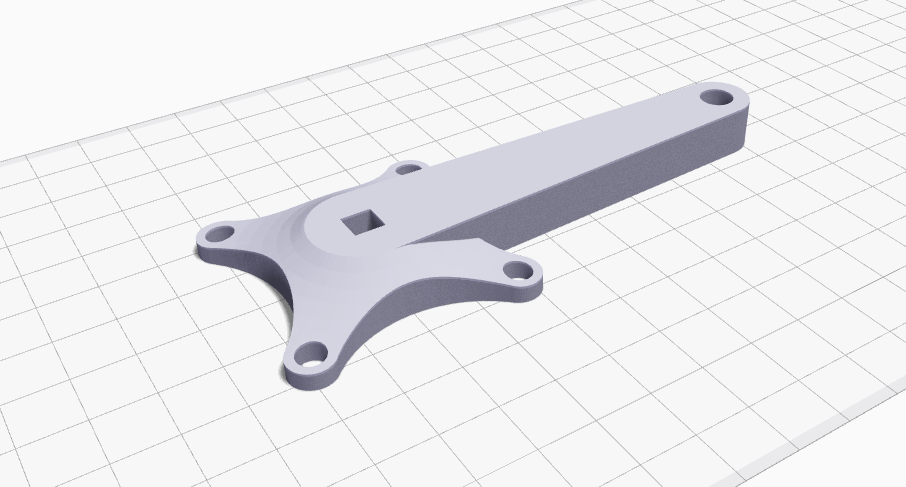
Er zijn duidelijk meerdere regio's die sandwichpanelen kunnen worden - er is de boven- en onderkant van de arm zelf (het langere deel van de structuur), evenals de boven- en onderkant van de vierpuntige flens die ook baat zou hebben bij composietversterking . Omdat bouten door alle vier de gaten worden geleid, zou de toevoeging van vezels beter bestand zijn tegen de spanningskegels die door de bouten worden geproduceerd. Hoewel je misschien een grondige (en langdurige) laadsimulatie kunt uitvoeren om de beste plaatsen te vinden om glasvezel toe te voegen, is het het gemakkelijkst (en waarschijnlijk het meest efficiënt) om gewoon te beginnen met het bouwen van sandwichpanelen. Eerst laten we het standaardvezelalgoritme vier lagen Isotrope vezelvulling toevoegen aan de boven- en onderkant van het onderdeel.
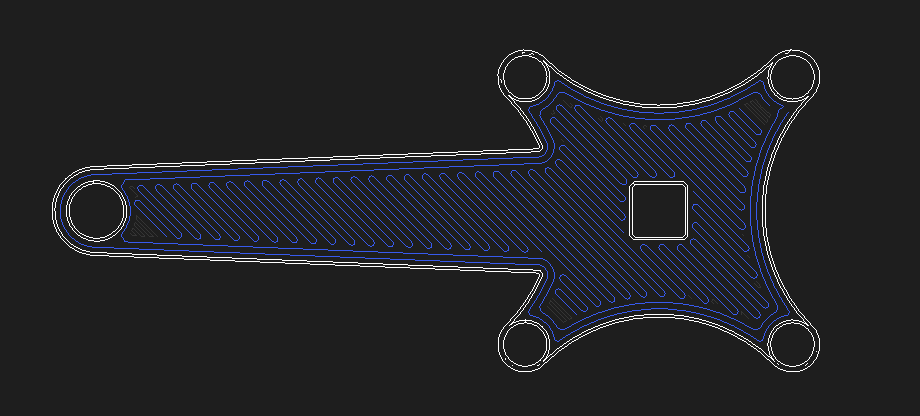
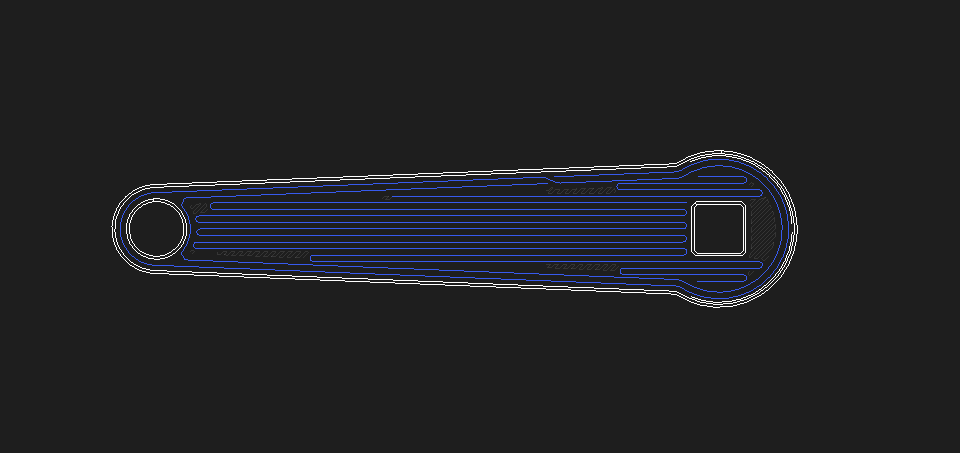
Deze twee lagen hebben zeer verschillende dwarsdoorsnede-oppervlakken, wat niet helemaal ideaal is (het is het beste om te proberen om 'huid'-lagen van sandwichpanelen te hebben met een ongeveer gelijke dwarsdoorsnede als de geometrie het toelaat), maar om het grootst mogelijke sandwichpaneel in de Dit betekent dat deze crankarm beter bestand is tegen de grote buigbelastingen van het been van een fietser.
We moeten ook de flens versterken met de vier gaten die deze krukarm met de eigenlijke kruk verbinden. We concentreren ons alleen op de flens, we hebben de onderkant ervan al versterkt toen we het algehele onderdeel in de eerste stap versterkten, we hoeven alleen maar een groep lagen te versterken van ongeveer 25 lagen in het onderdeel, waar de flens eindigt. Maar als we daar een lagengroep toevoegen, hebben we drie afzonderlijke vezellagen. We hebben het alleen gehad over sandwichpanelen met twee composiethuiden, één aan elke kant - hebben we een van de sandwichpanelen verpest?
Dit brengt ons bij onze tweede richtlijn:ons concept van 'sandwichpanelen' is niet alleen additief, en we kunnen een sandwichpaneel over een grotere of kleinere leggen, waarbij de composiet 'huid'-laag van de vorige sandwich opnieuw wordt gebruikt.
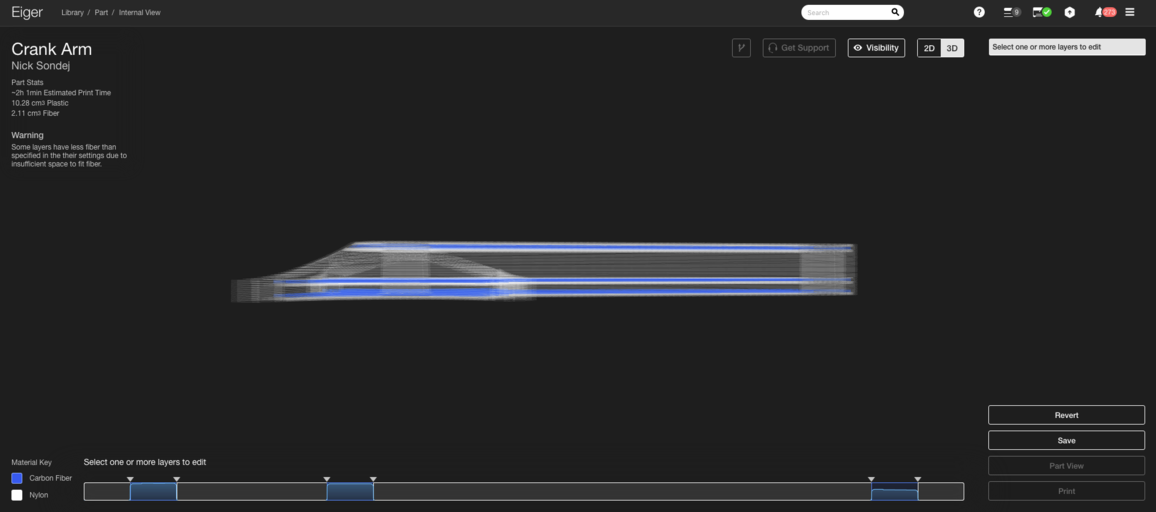
Dit resulteert dus in de configuratie in de afbeelding hierboven, met een dunner sandwichpaneel dat de krukarmflens versterkt en een dikker sandwichpaneel dat het totale deel versterkt. Beide sandwichpaneeluitvoeringen gebruiken de koolstofversterkingslaaggroep aan de onderkant van het onderdeel als hun onderste huidlaag.
Op dit punt is het onderdeel al extreem sterk, maar omdat fietscrankarmen worden onderworpen aan nogal wat gecompliceerde torsiebelastingspatronen, gaan we nog een vezellaag toevoegen. Dit komt omdat schuifspanningen kunnen worden veroorzaakt door bepaalde uitgeoefende torsiebelastingen. In tegenstelling tot buigspanningen, hebben schuifspanningen een maximale grootte op de neutrale as of het middenvlak van een onderdeel, en aangezien het moeilijk te voorspellen is of de krukarm aan deze belastingsomstandigheden zal worden blootgesteld, is het het gemakkelijkst om gewoon nog een composietlaaggroep toe te voegen rond het middenvlak van de crankarm.
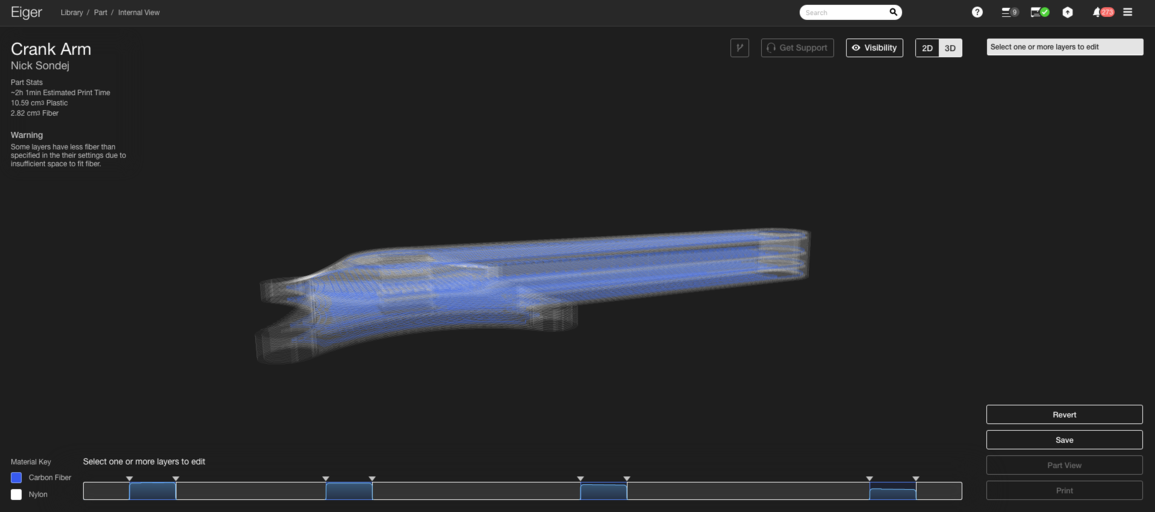
Dit resulteert in de uiteindelijke configuratie die te zien is in de bovenstaande afbeelding - met vier afzonderlijke groepen vezels die een reeks sandwichpanelen creëren. Dit is een van de sterkste configuraties die we kunnen produceren, met behoud van een algeheel lichtgewicht onderdeel.
Samenvattend zijn onze drie richtlijnen voor 3D-printen met hoge sterkte met behulp van vezelversterking:
Deze richtlijnen zijn niet onfeilbaar en er zullen altijd uitzonderingen zijn, maar ze zijn een geweldige plek om te beginnen bij het ontwerpen van je sterkste onderdelen.
Zelf een onderdeel verstevigen? Leer vandaag nog meer over de Mark Two!
3d printen
- Stressvrije reiniging voor FDM-afdrukken
- Waarom CT-scanning een belangrijk onderdeel wordt van succesvol 3D-printen
- Hoe 3D-printtechnologie een belangrijk onderdeel wordt van Industrie 4.0
- 6 belangrijke ontwerpoverwegingen voor 3D-metaalprinten
- Is 3D-printen klaar voor de productie van eindonderdelen?
- 3D-printen en prototypen
- Multibody STL-bestanden maken voor 3D-printen
- Hoe u uw model positioneert voor 3D-printen
- Hoge snelheid 3D-printen voor productie in kleine batches
- 3D-printen met hoge snelheid met AION500MK3
- 3D-printtechnologieën (deel 2)