De beste manieren om gootsteenvlekken in spuitgieten te voorkomen en te repareren
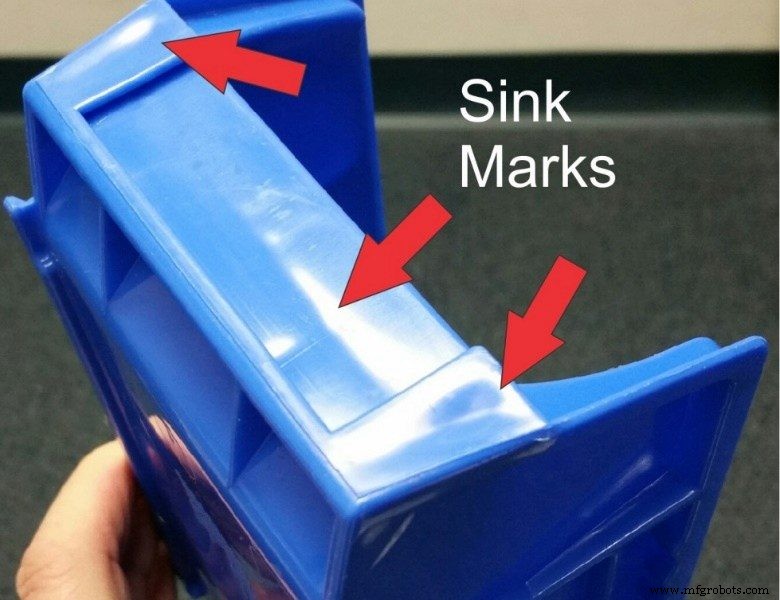
Spuitgieten is een geweldig productieproces voor het maken van esthetische rapid prototyping en kunststof productieonderdelen. Maar als er geen strikt controlesysteem voor het productieproces is, kunnen er defecten zijn in de kunststof vormdelen, zoals gootsteenmarkeringen.
Dus, wat is een zinkmarkering bij spuitgieten? Waarom gebeurt dit en hoe voorkom je ze als fabrikant? Blijf lezen terwijl we je antwoorden geven op deze vragen en belangrijke dingen die je moet weten over zinkvlekken.
Wat is gootsteen in spuitgieten?
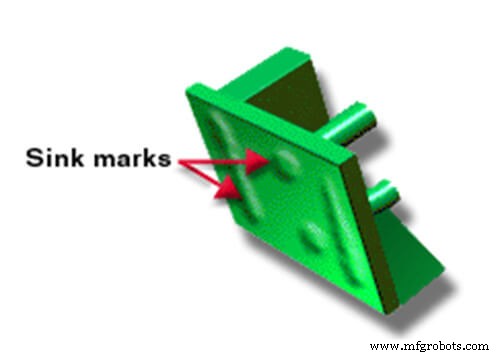
Zinkmarkering is een defect op het oppervlak van spuitgegoten onderdelen met variaties in wanddikte . Met andere woorden, spuitgietsporen komen voor op dikkere delen van gegoten onderdelen en dit defect lijkt meer op een kuiltje of groef op het oppervlak. Als een deel van een product dikker is, betekent dit dat het meer delen bevat. Bovendien verlengen deze dikkere gebieden hun koeltijd. Daarentegen koelt het buitenste gedeelte van het plastic onderdeel dat in contact komt met het vormstaal vaak erg snel af.
Bijgevolg veroorzaakt dit verschil in afkoeltijd tussen het buitenste gedeelte van het gegoten onderdeel en het interieur het defect. Hoe? Als de moleculen in het dikkere deel van het prototype beginnen af te koelen, trekken ze samen, waardoor het buitenste deel naar binnen trekt, waardoor een zinkvlek ontstaat. Als het buitenste deel echter sterk genoeg is, veroorzaakt deze samentrekking in plaats daarvan een leegte.
De mate van zichtbaarheid van een spoelbak is afhankelijk van de diepte, de kleur van het product en de textuur. Het is echter belangrijk op te merken dat kleine verzakkingen vaak zichtbaar zijn vanwege hun vermogen om licht in verschillende richtingen te reflecteren.
Oorzaken en oplossingen van gootsteenvlekken bij spuitgieten
Het produceren van onderdelen door middel van spuitgieten omvat het injecteren van gesmolten materiaal in een mal. Binnen de mal stolt het materiaal tot de gewenste delen. Vervolgens wordt het uitgeworpen.
Spuitgietsporen komen vaak voor wanneer de dikte van het in de mal geïnjecteerde onderdeel te groot is voor de gebruikte hars. Er zijn echter andere oorzaken van zinkvlekken. Laten we nu eens kijken wat de oorzaak is en hoe we verzakkingen bij spuitgieten kunnen verminderen.
Sink Marks Oorzaak 1:Onjuiste smelttemperatuur
Het gebruik van een verkeerde temperatuur bij het smelten van een hars kan leiden tot zinkvlekken op het oppervlak van het afgewerkte plastic. Vaak zijn de verzakkingen het gevolg van de lage temperatuur van het inzetstuk, en als dit het geval is, kan het verhogen van de temperatuur deze problemen oplossen.
Om dit te voorkomen, past u de smelthars aan binnen het door de fabrikant aanbevolen temperatuurbereik. Controleer de smelttemperatuur voordat u de hars in de mal injecteert.
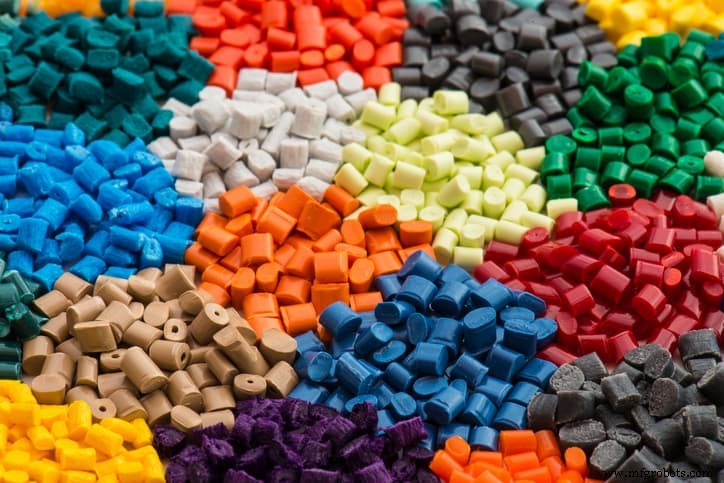
Sink Marks Oorzaak 2:Lage inpak- en bewaartijd
Wanneer de inpak- en houdtijd te kort is, kan dit ook putten op de oppervlakken van producten veroorzaken. Idealiter zou de inpak- en houdtijd lang moeten zijn. Dit zorgt voor een goede afdichting van de onderdeelpoort, waardoor het binnenkomen en verlaten van kunststofhars uit de vormholte wordt voorkomen. Als de poortafdichting niet goed plaatsvindt, zal de kunststofhars de holte verlaten wanneer deze wordt gelegd om te rusten.
Om verzakkingen te voorkomen, moet u deze lang genoeg vasthouden om ervoor te zorgen dat de poort stolt na het vullen van de mal. Dit zou helpen voorkomen dat gesmolten materiaal de mal verlaat, waardoor putten worden voorkomen. Met andere woorden, waar een markering of depressie optreedt in de buurt van de poort, helpt het verlengen van de pack- en hold-tijd om deze uit te roeien.
Sink Marks Oorzaak 3:Onjuiste pak- of houddruk
Onjuiste verdeling van de houddruk is een andere reden waarom spoelbakken op gegoten onderdelen verschijnen. Dat wil zeggen dat het toepassen van de juiste verpakkingsdruk op verschillende delen van het product helpt om het in vorm te houden.
Om verzakkingen of krimp te voorkomen, varieert een typische druk in de vormholte van 8000-15.000 psi. De regel hierbij is dat de pak- of houddruk 50-70% van de injectiedruk moet zijn.
De beste manier om druk uit te oefenen is door de dikte te meten. Dientengevolge vereisen dikke vormsecties meer plastic en druk dan minder dikke secties om vorm te behouden.
Aangezien dit defect het gevolg is van krimp wanneer materiaal zoals de plastic hars in dikke gebieden samentrekt tijdens het drogen, kan het helpen om voldoende plastic in dikke gebieden te krijgen met de juiste druk om het uit te roeien.
Zakvlekken Oorzaak 4:Hoge schimmeltemperatuur
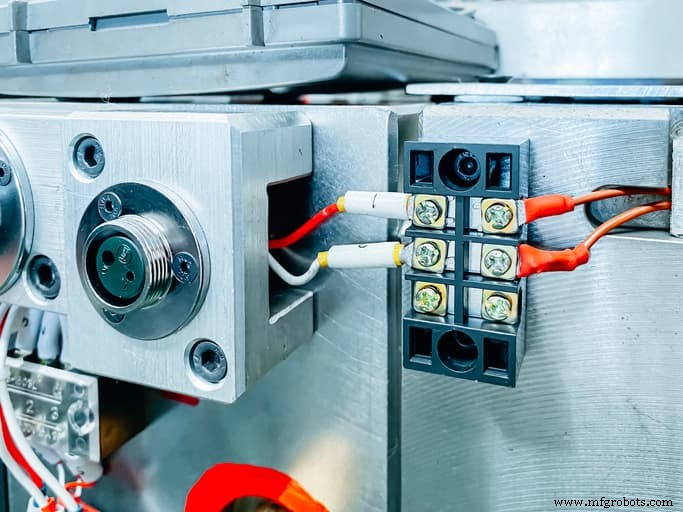
Niet de aanbevolen schimmeltemperaturen gebruiken (die tussen 80-120 o . liggen Celsius) kan leiden tot deze depressie. Een te hoge temperatuur kan de poort ervan weerhouden om goed en op tijd af te sluiten. Om dit op te lossen, gebruikt u het juiste temperatuurbereik van de mal en zorgt u voor correct sanitair.
Hieronder vindt u de aanbevolen spuitgiettemperatuur voor gewone kunststof:
Plastic materiaal | Temperatuur spuitgieten (C°) | Matrijstemperatuur (C°) |
LDPE | 160-260 | 50-70 |
POM | 200-210 | >90 |
ABS | 210-275 | 50-90 |
PP | 250-270 | 50-75 |
PS | 180-280 | 10-40 |
PVC-rigide | 180-210 | 30-50 |
PVC-zacht | 170-200 | 15-50 |
HDPE | 260-300 | 30-70 |
PC | 280-320 | 80-100 |
TPR | 120-250 | 50-70 |
PA66 | 260-290 | 70-120 |
PMMA | 210-240 | 50-70 |
PA6 | 240-260 | 70-120 |
Sink Marks Oorzaak 5:Onjuiste onderdeelgeometrie
Onjuiste onderdeelgeometrieën en malontwerp kunnen er ook voor zorgen dat deze depressies ontstaan. Het is belangrijk op te merken dat de ribben en nokken de meest voorkomende plekken zijn waar zinkvlekken voorkomen. Hieronder staan een paar manieren om spuitgietdefecten te verhelpen veroorzaakt door geometrie.
Evenwichtsribbe en wanddikte
Het creëren van een balans tussen ribbe en wanddikte zou de neiging van deze markeringen om zich te vormen te verminderen. Vermijd het verhogen van de hoogte van de ribbe tot de dikte van de muur. Omdat dit kan leiden tot een toename van het aantal vervormingen of defecten op het plastic.
Houd er ook rekening mee dat gesmolten plastic, net als andere vloeistoffen, met weinig of geen weerstand langs het pad stroomt. Daarom zouden minder dikke gebieden het eerst vollopen tijdens de kunststofinjectie. Nadat dit gedeelte vol is, begint het gesmolten plastic het ribgedeelte te vullen.
Gebruik een geleidelijke helling van 7 graden aan de basis van de rib
Om vervorming en onvolkomenheden te minimaliseren, is een geleidelijke helling van 7 graden aan de basis van de ribbe noodzakelijk. Het gebruik van deze hellingmethode werkt alleen als de poort zich in de buurt van het gebied bevindt. Deze helling zorgt voor een geleidelijke stijging van het gesmolten materiaal dat in de mal wordt geïnjecteerd, waardoor vlekken en vervormingen op het oppervlak worden voorkomen.
Boss-ontwerp
Bij het ontwerpen van een naaf waarbij de ring door minimale spanning zou gaan, moet de buitendiameter het dubbele zijn van de binnendiameter. Dit type naafontwerp zou zinkvlekken helpen verminderen. Aan de andere kant, als de naafring veel spanning zou doorstaan als er zwaardere belastingen worden uitgeoefend, moet de buitendiameter tweeënhalf keer de binnendiameter zijn.
Het dunnere basisgebied rond de baas
Het is het beste om te voorkomen dat het basisgebied rond de baas dunner wordt. Deze praktijk, die tegenwoordig gebruikelijk is, maakt de constructie zwak. Als gevolg hiervan zou de naaf sterke ribben nodig hebben voor ondersteuning die bijgevolg de materiaalstroom tijdens het injecteren onderbreken, wat resulteert in verzakkingen in het plastic.
Klein mondstukgat
Als het mondstuk verstopt raakt of het mondstukgat van de vormmachine klein is, kan een gebrek aan druk een vlek op het plastic veroorzaken. Daarom is de beste manier om dit soort defecten op plastic te voorkomen, het reinigen of vervangen van de spuitmond van de injectiemachine om de ideale injectiesnelheid te krijgen.
DFM helpt putten in kunststof spuitgieten te voorkomen
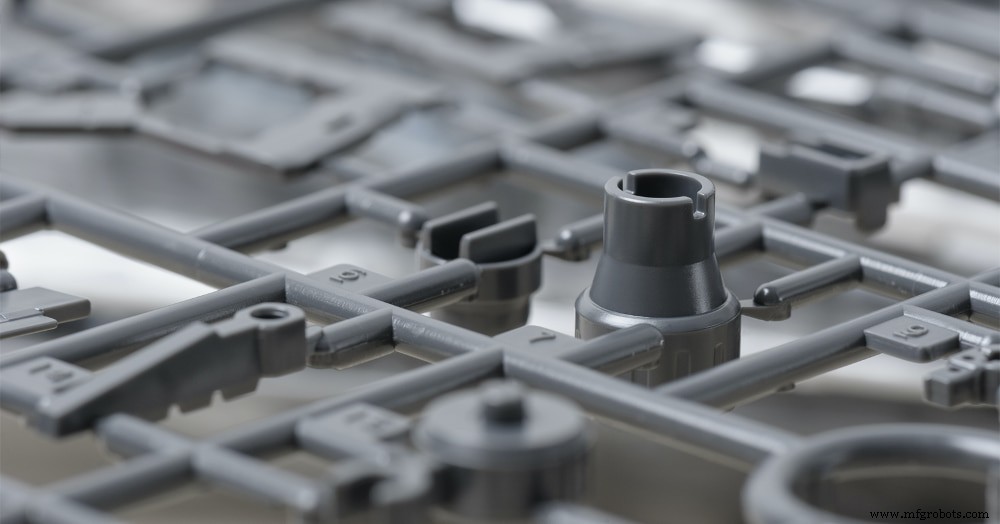
Ontwerpen voor fabricage of maakbaarheid omvat het ontwerpen van een component of onderdeel, zodat het gemakkelijker is om meer van dat onderdeel te produceren. Dit proces omvat een reeks ontwerprichtlijnen die de industrie aanbeveelt voor een betere productie en het ontwerp van onderdelen.
Door ontwerp voor maakbaarheid toe te passen in de ontwerpfase, worden verzakkingen van vormdelen voorkomen. Deze productiefase is ook het ideale moment om deze defecten aan te pakken, aangezien dit tegen minimale kosten gebeurt. Dit proces omvat ook het gebruik van gespecialiseerde simulatieprogramma's voor malstroom. Het doel van het gebruik van dit programma is om het proces van spuitgieten te simuleren. Deze simulatie in 3D toont stroming, kromtrekken, warmteflux en details van de volledige mal.
Tijdens de simulatie controleren de ingenieurs die toezicht houden op het project met behulp van een checklist op problemen met het ontwerp, inclusief zinkmarkeringen. Als er problemen zijn, brengen ze de nodige wijzigingen aan in het ontwerp, inclusief het gebruikte materiaal en de mal. Ze herhalen dit proces totdat de checklist is voltooid en problemen zijn verholpen.
Het algemene doel van DFM is om producten met minimale fouten te vervaardigen en de productkwaliteit te verhogen voor een optimale klanttevredenheid. Trouwens, het niet volgen van deze ontwerpgids voor spuitgieten tijdens de productie van kunststof onderdelen leidt dit vaak tot vermijdbare kosten als gevolg van matrijsmodificatie en herontwerp.
RapidDirect – Uw beste spuitgietpartner
Bent u op zoek naar de beste plaats voor uw spuitgietservices zonder gootsteensporen? Denk aan RapidDirect! We bieden de beste kwaliteit tijdens zowel prototyping als productie op ware grootte.
Bovendien bieden we onze klanten gratis DFM-analyses om ervoor te zorgen dat defecten zoals een zinkvlek het uiterlijk van uw product niet aantasten.
We zijn grote fans van perfectie, daarom volgen we alle DFM-standaardrichtlijnen om ervoor te zorgen dat uw productonderdelen meer dan perfect zijn. Dus waar wacht je op? Bezoek RapidDirect vandaag nog om uw project een kickstart te geven.
Veelgestelde vragen
Wat veroorzaakt holtes bij spuitgieten?Leegte treedt op wanneer er een verschil is in de afkoelsnelheid tussen de buitenste en binnenste delen, vooral wanneer de buitenste laag van het product afkoelt vóór de binnenste laag. Dit verschil zorgt ervoor dat de binnenste laag krimpt, loskomt van de andere laag, waardoor een leegte ontstaat.
Hoe voorkom je verzakkingen en holtes?
De belangrijkste manieren waarop u putten en holtes in een ontwerp kunt voorkomen, zijn onder meer:
a. Zorg ervoor dat de smelttemperatuur optimaal is.
b. Ervoor zorgen dat de pack-and-hold-druk ideaal is.
c. Vermijd overmatige schimmeltemperatuur.
d. Zorg voor het gebruik van het juiste materiaal en matrijsontwerp.
Hieronder vindt u manieren waarop u stroomlijnen kunt verwijderen en voorkomen;
a. Verhoog de injectiesnelheid, druk of temperatuur van het materiaal.
b. Waar de wanddikte toeneemt, rond de hoeken van de mal in die regio's af.
c. Zorg voor een goede afstand tussen vormpoorten en vormkoelvloeistof.
d. Verhoog de stroomsnelheid door de diameter van de spuitmond te vergroten.
Conclusie
Weten wat de oorzaak van zinkvlekken is, is de eerste stap om ze te voorkomen en op te lossen. Er zijn veel redenen waarom zinkvlekken optreden, van houdtijd en druk tot maltemperatuur en smelttemperatuur. Een manier om te voorkomen dat deze depressie uw gegoten onderdelen vervormt, is door DFM te gebruiken bij de productie.
Ook als u op zoek bent naar een ideaal bedrijf voor uw spuitgietbehoeften tegen een betaalbare prijs, denk dan aan RapidDirect.
Hars
- Injection Molded Part Design Part 2:Sink Marks
- Voor- en nadelen van thermohardend spuitgieten
- Hoge viscositeit PEEK voor spuitgieten en extrusie
- PPSU voor injectie-rek- en extrusieblaasvormen en spuitgieten van flessen
- PHA-gebaseerde harsen voor geblazen gegoten films, spuitgieten en thermovormen
- Beste van...Beste praktijken in spuitgieten
- 8 manieren om downtime te voorkomen en toch geld te besparen
- Wat zijn spuitgietfouten en hoe u ze kunt voorkomen:10 defecten aan kunststof onderdelen
- Beste kunststof spuitgietmaterialen
- Efficiënte en kosteneffectieve services voor kunststof spuitgieten
- Hoeveel kosten spuitgieten en hoe kunt u dit inschatten?