Design spotlight:aanpassing van additief naar spuitgieten
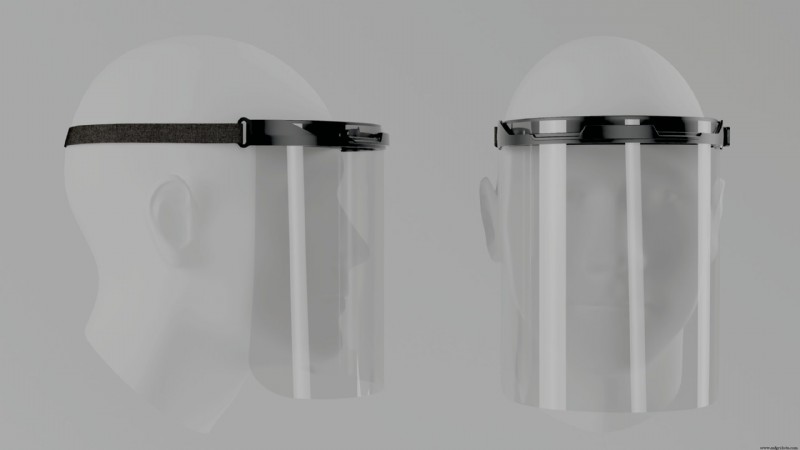
Toen de COVID-19-pandemie de Verenigde Staten trof, heeft ons team bij Fast Radius snel een aanzienlijk deel van onze additieve productiemogelijkheden omgezet in het produceren van gezichtsschermen. Tot op heden hebben we duizenden additief vervaardigde gelaatsschermen gemaakt en verzonden om eerstelijnswerkers te beschermen tegen het coronavirus. Het schild is herbruikbaar, extreem duurzaam, eenvoudig te monteren en comfortabel, maar de vraag heeft onze additieve productiecapaciteit ver overschreden.

Om ons product voor meer mensen beschikbaar te maken, hebben we besloten om de productie te verschuiven naar spuitgieten. Spuitgieten maakt het schild op twee punten toegankelijker; het stelt ons in staat een veel groter volume te produceren, en spuitgieten verlaagt de kosten van het product aanzienlijk vanwege lagere materiaalkosten en snellere productie.
In ons werk met klanten gebruiken we vaak additieve technologie om onderdelen te vervaardigen, terwijl we overgaan op spuitgietproductie. Ons eigen verhaal is een sterk voorbeeld van hoe we digitale productietechnologie kunnen gebruiken om een additief product voor spuitgieten opnieuw te ontwerpen.
Snelle ontwerp-iteratie met simulatietools
We moesten aanzienlijke wijzigingen aanbrengen in het additieve ontwerp van de "halo" (of hoofdband) van het schild om het geschikt te maken voor spuitgieten, terwijl ook de prestaties behouden blijven. We wisten dat de stijfheid moest worden geoptimaliseerd om de omstandigheden van dun staal te verminderen die gereedschapsbeschadiging tijdens het gieten kunnen veroorzaken. Omdat we wisten dat de stijfheid van de huidige halo goed werkte, simuleerden we de fluctuerende verplaatsing van de additieve halo en gebruikten die verplaatsing als doel voor de stijfheid van het spuitgegoten ontwerp.
Om de elementen die bijdragen aan stijfheid te begrijpen, hebben we Finite Element Analysis (FEA) gebruikt om de ontwerpvariabelen te lokaliseren die betere resultaten opleverden. We vertrouwden op het simulatiepakket binnen Autodesk 360, een tool die we voor verschillende doeleinden gebruiken, waaronder ontwerp, analyse en simulatie. We hebben zowel de kroon als de ribbelpatronen op de voorkant van de buitenring getest. Hoewel de ribbels wat stijfheid toevoegden, ontdekten we dat het toevoegen van hoogte aan de kroon een effectievere manier was om verplaatsing te minimaliseren.
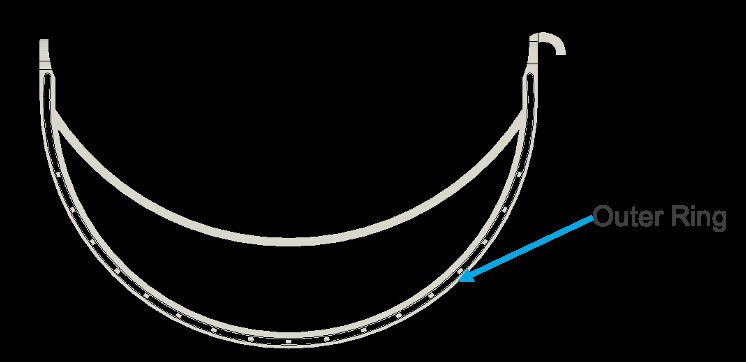
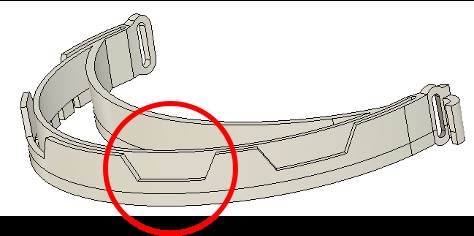
Het toevoegen van hoogte aan de kroon kan echter leiden tot slechte gereedschapscondities (dun gereedschapsstaal) tussen de buitenste en middelste ringen. De sleuf waarin het schild zelf wordt geplaatst, is erg dun - zo dun als één tot twee millimeter; hoe groter de secties in de kroon, hoe dunner staal nodig zou zijn voor het gereedschap, waardoor de kans groter is dat het gereedschapsstaal beschadigd raakt tijdens het gieten.
We moesten de optimale kroonhoogte vinden die dun staal zou verminderen met behoud van stijfheid in de buitenste ring van de halo. Om dit te bepalen, hebben we 16 simulaties uitgevoerd, waarbij we het ontwerp iets hebben aangepast om de prestaties elke keer te verbeteren. In deze fase van het ontwerpproces hadden we ons doel al bereikt en hadden we veel ontwerpen met een vergelijkbare of betere verplaatsing dan de additieve halo.
Snelle prototyping met HP Multi Jet Fusion (MJF)
Uit de concepten die we simuleerden, kozen we er drie om te printen met HP MJF, aangezien dat de technologie is die we gebruikten om onze originele additieve halo te produceren. Normaal gesproken zou het drie dagen duren voordat een MJF-onderdeel voldoende is afgekoeld om bruikbaar te zijn, maar ons team van productie-ingenieurs heeft de constructie zo ingepakt dat we onze onderdelen de volgende dag in huis hadden.
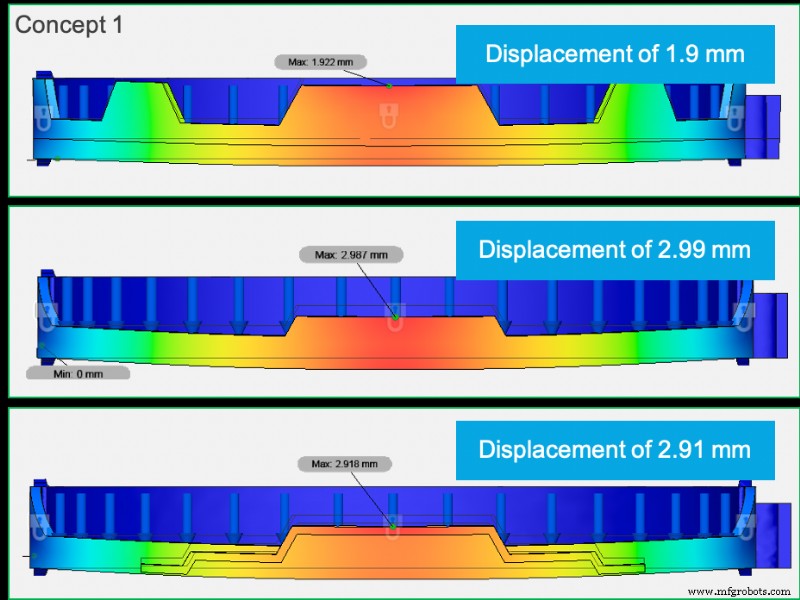
Het operationele team van de Fast Radius-fabriek in Chicago droeg de drie concepthalo's en vergeleek ze met de originele additief vervaardigde versie om comfort en montagegemak te vergelijken. Concept 10 (zie hierboven, derde ontwerp) accepteerde het schild het gemakkelijkst, maar ze stelden verschillende aanpassingen voor om het comfort te verbeteren en de montage te vergemakkelijken. Het resulterende ontwerp (zie hieronder) werd gebruikt om het spuitgietgereedschap te produceren dat de volgende versie van onze gelaatsscherm-halo zal maken.

Uiteindelijk zal het overschakelen van additive manufacturing naar spuitgieten de halo veel toegankelijker maken voor degenen die het nodig hebben. We hebben de prijs met 55% kunnen verlagen.
Toen we begonnen met het maken van additieve halo's, voldeden we aan een vraag die we niet konden voorspellen. Toen duidelijk werd dat we ons product toegankelijker konden maken, hebben we ons additiefontwerp voor spuitgieten aangepast en een gereedschap in slechts drie dagen in productie genomen.
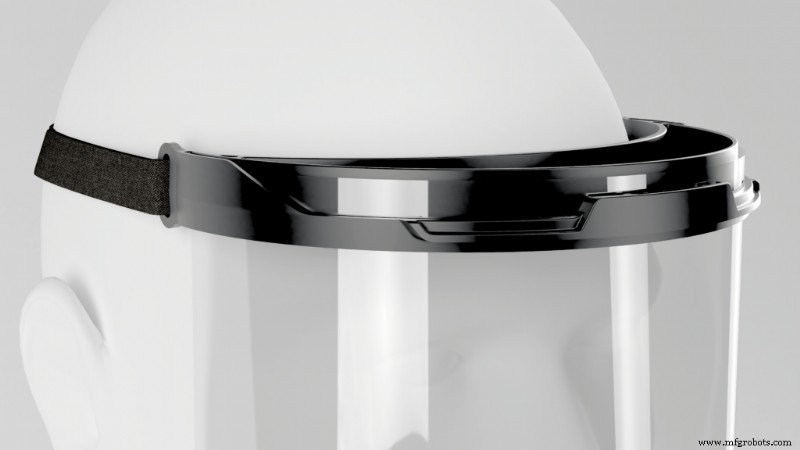
Ons team werkte de klok rond om dit belangrijke product op de markt te brengen. We hebben deze opmerkelijke tijdlijn bereikt, grotendeels dankzij simulatiesoftware, digitale productie en ons flexibele werkmodel. Deze pandemie heeft ons gedwongen om flexibeler te worden met productontwikkelingscycli, een trend waarvan we denken dat deze zich lang na de pandemie zal voortzetten.
Klaar om uw onderdelen te maken met Fast Radius?
Start uw offerteIndustriële technologie
- Wat is reactie-spuitgieten?
- Gegoten versus spuitgieten
- Thermovormen versus reactie-spuitgieten (RIM)
- Spuitgieten versus reactie-spuitgieten (RIM)
- Gietvormen versus reactie-spuitgieten
- Ontwerptips voor gietvormen
- Ontwerpservices van Protocase:6 tips
- Spuitgietpoortontwerp:een ultieme gids voor kunststofproductie
- Aluminium spuitgieten in productproductie
- Trekhoek voor spuitgieten:ontwerpgids en beste praktijken
- Waarom u ontwerp nodig heeft voor productie in spuitgieten