Wegversperringen verwijderen om nieuw geïnstalleerde slijpprocessen te optimaliseren
Over het algemeen doorlopen nieuwe lijnen met een hoog volume die complexe onderdelen produceren die slijpprocessen omvatten, zoals een automotor of een blad en schoep van een vliegtuigmotor, verschillende stadia van de aanschaf van machines tot de daadwerkelijke productie, zoals weergegeven in figuur 1. Als deze regels een proces bevatten dat wordt beschouwd als "hoog risico ' het wordt gepland met 'ontwikkelingstijd' als onderdeel van de evaluatie en aankoop van de molen (stappen 4 en 5) door testen en verfijning. Dit is een effectieve strategie en vermindert de problemen die gepaard gaan met het starten van een programma aanzienlijk, maar kan tijdrovend en duur zijn; heel vaak zijn werkstukmonsters niet eens beschikbaar of zijn prototypes onderhevig aan verdere ontwerpwijzigingen. In dergelijke gevallen of voor componentontwerpen die verschillend zijn, maar niet radicaal anders van bestaande ontwerpen wordt "optimalisatietijd" zelden gepland voorafgaand aan de daadwerkelijke machinekwalificatie.
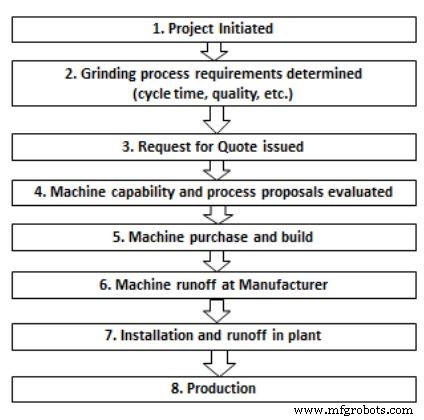
Wanneer machines zijn gekwalificeerd en geïnstalleerd met "niet-radicaal" ” processen, ligt de focus op onderdeelkwaliteit en cyclustijd. Wielspecificaties kunnen heel goed worden gekozen om de hoogste kwaliteit te garanderen te midden van onzekerheden van het nieuwe onderdeelontwerp en hun impact op het houden van onderdeeltoleranties aan vaak strengere CpK-specificaties dan vereist voor productie. Bovendien worden vanwege de kosten of beschikbaarheid vaak slechts 50 of 100 onderdelen geleverd voor kwalificatie, waardoor het opzetten van een stabiel proces op lange termijn twijfelachtig is. Er is doorgaans niet veel tijd of componenten om de gereedschaps- of schuurkosten per onderdeel te optimaliseren. Na de installatie neemt in veel gevallen een "if it ain't broken, don't fix it"-houding het over en lopen de processen vast. Optimalisatie wordt zelden geprobeerd.
Het is daarom erg belangrijk dat de "extra stap" van optimalisatie wordt beschouwd als een laatste "audit" van het proces. Meestal kan deze stap gewoon een procesaanpassing zijn, zodat herkwalificatie van het hele proces niet nodig is, maar af en toe kunnen er voldoende kansen worden ontdekt die grote veranderingen in de cyclus- en/of wielspecificatie rechtvaardigen. Er zou een kosten-batenanalyse worden uitgevoerd om te bepalen of er een meer substantiële procesverandering moet worden doorgevoerd.
Er zijn verschillende redenen waarom een gebrek aan "optimalisatietijd" suboptimale processen kan veroorzaken:
- Cyclussen kunnen acceptabel functioneren in de machine, maar zijn niet 'wielvriendelijk'. d.w.z. de levensduur van het wiel kan minder dan optimaal zijn
- Wieltechnologie evolueert. Schattingen gemaakt op bestaande technologie zijn mogelijk niet optimaal voor nieuwe technologie
- Subtiele variaties in onderdeelconfiguratie, machineontwerp en kwaliteitseisen maken procesoptimalisatie erg moeilijk buiten de productielijn. Dit komt omdat de productielijn veel onderdelen biedt en een omgeving met echte variaties en metrologie. Deze twee eigenschappen vormen een test voor de 'robuustheid' van het 'geoptimaliseerde' proces.
Voorbeelden:
De maalcyclus afgebeeld in figuur 2 is verzonden vanuit de OEM die in een fabriek is geïnstalleerd en is momenteel in productie. Deze cyclus werkt prima en produceert acceptabele onderdelen, maar is niet "wielvriendelijk".
De wielonvriendelijkheid van deze cyclus is te wijten aan de grote piek (kracht/kracht) aan het begin van de cyclus. Wielslijtage is evenredig met het kwadraat van de slijpkracht, hoge krachten zorgen ervoor dat het wiel snel slijt. In dit geval zou het verminderen van Fast Feed en het verhogen van Medium Feed de levensduur van de wielen verlengen met behoud van de cyclustijd en de kwaliteit van de onderdelen.
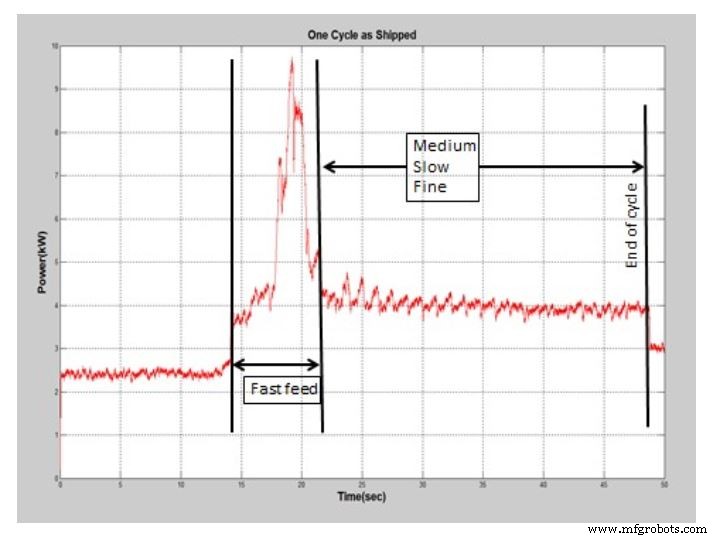
Een cyclus in het proces van optimalisatie
In een recent ongebruikelijk geval stemde de fabrikant ermee in om het maalproces 'in situ' te optimaliseren. Aanvankelijk werd de maalcyclus gewijzigd om deze "wielvriendelijker" te maken, zoals hierboven besproken. In dit geval was de vriendelijkere cyclus ook ~5 sec korter dan de initiële cyclus.
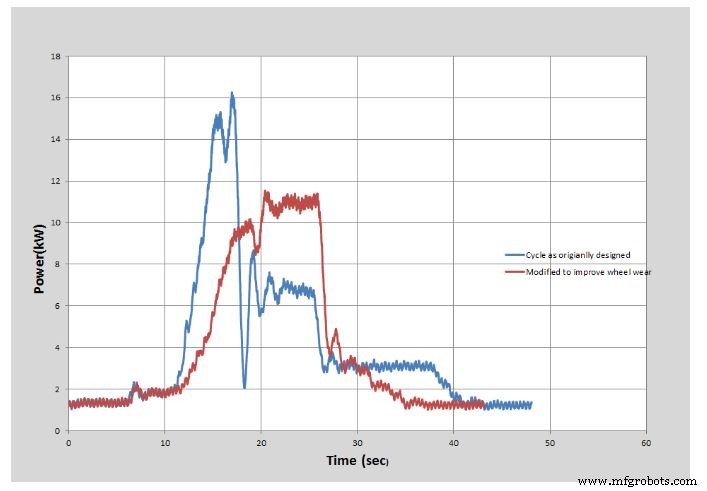
Nadat de aangepaste cyclus enkele weken was uitgevoerd om de kwaliteit van de onderdelen te valideren, werd het aantal onderdelen per jurk verhoogd van 8 naar 20 en werd de diepte van de jurk verlaagd van 0,03 mm naar 0,02 mm. Dit proces loopt nu ongeveer 6 weken zonder noemenswaardige verandering in de kwaliteit van de onderdelen. Hieronder ziet u een overzicht van de kostenbesparingen per jaar.
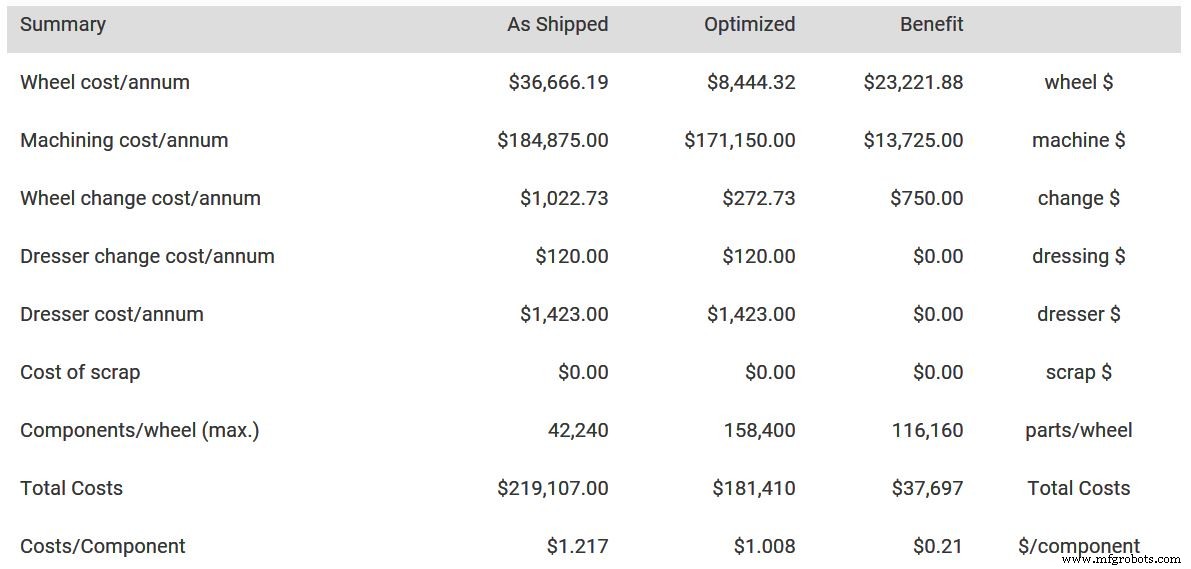
Strategie voor optimalisatie
De oplossing, zoals geïllustreerd in het tweede voorbeeld, is om tijd en onderdelen te plannen in de vroege productiefasen (tussen stap 7 en 8 in figuur 1) om samen met de machinebouwer en het applicatie-engineeringteam aan procesoptimalisatie te werken. . Tijdens deze fase moet op zijn minst apparatuur voor het bewaken van het vermogen worden gebruikt om te helpen bij de evaluatie en ontwikkeling van de cyclus. Met deze extra stap kan het proces worden gecontroleerd op stabiliteit bij langere onderdeelseries die problemen aan het licht kunnen brengen en/of kansen voor verbeteringen kunnen bieden.
De potentiële opbrengst van deze stap is groot, aangezien verbeteringen/kostenbesparingen die in deze fase worden gemaakt, gedurende de hele levenscyclus van het project van kracht zullen zijn.
Eerder vermeld op Norton Abrasives
Shop onze selectie Norton-rasterwielen op MSCdirect.com.
Industriële technologie
- Uitbouwen van operationele standaarden en processen
- Airbus introduceert de fabriek van de toekomst
- Foutmodi van apparatuurbetrouwbaarheidsprocessen
- Het optimaliseren van productieactiviteiten op uw werkvloer
- Slijpschijven:fabricage en kwaliteit | Industrieën | Metallurgie
- De waardevolle rol van procesautomatisering bij het nastreven van ESG
- FASMET- en FASTMELT-processen voor het maken van ijzer
- Wat is honen? - Definitie, proces en hulpmiddelen
- Hoe bedrijfsprocesbeheer te implementeren?
- Oppervlakteslijpdiensten:proces en precisie
- Grondbeginselen van OD-slijpen