Toyota Kata:een slanke strategie om gelijke tred te houden met het tempo van verandering
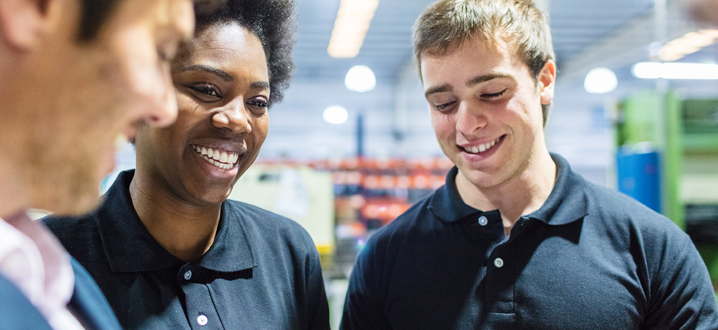
"Waarom duren onze omschakelingen zo lang?"
Als je deze vraag op de werkvloer hebt gesteld, werd je hoogstwaarschijnlijk met lege blikken aangekeken door je medewerkers. Open vragen als deze zijn overweldigend, dus medewerkers proberen snel antwoorden te vinden die het probleem niet echt aanpakken. Ze hebben geen aanknopingspunt om een antwoord te vormen.
Maar wat als je een vraag stelt met een specifiek, haalbaar doel?
"Welke stappen kunnen we nemen om de omsteltijd met 15 minuten te verkorten?"
U heeft uw medewerkers vervolgens een meetbaar doel meegegeven in de vorm van een vraag. Uw werknemers voelen zich misschien gesterkt om te antwoorden met enkele praktische suggesties voor incrementele wijzigingen, zoals het verminderen van installatiestappen of het combineren van werkstations. Dit kan op zijn beurt niet alleen de omsteltijd verkorten, maar ook de wachttijden en voorraden aanzienlijk elimineren.
Deze aanpak wordt vaak omschreven als Kaizen, of 'continue verbetering', dat de ruggengraat vormt voor lean manufacturing. Kaizen gebruikt de probleemoplossingscyclus Plan, Do, Check, Act (PDCA) om fabrikanten aan te moedigen kleine ideeën te gebruiken om grote problemen op te lossen, zoals kostbare, tijdrovende omschakelingen.
Deze methodologieën zijn de bouwstenen van Toyota Kata, een innovatieve, slanke manier van denken beschreven in het boek van Mike Rother, 'Toyota Kata:Managing People for Improvement, Adaptiveness and Superior Results'.
In wezen gaat Toyota Kata verder dan het oplossen van problemen en leert het management, ingenieurs en operators een nieuwe manier van denken om hun creatieve en wetenschappelijke denkvaardigheden te ontwikkelen om ze effectievere, slankere fabrikanten te maken. Deze benadering kijkt naar lean manufacturing als een cultuur, in plaats van een enkel proces.
Nu de productiewereld in een adembenemend tempo evolueert dankzij ontwikkelingen zoals kunstmatige intelligentie (AI), lacunes in arbeidsvaardigheden en het industriële internet der dingen (IIoT), biedt Toyota Kata kleinere fabrikanten een slanke strategie om hen te helpen groeien met deze ontwikkelingen . Het geeft werknemers de vaardigheden die ze kunnen gebruiken om voortdurend te verbeteren, aan te passen en ideeën te genereren voor een strategisch concurrentievoordeel.
Kleine stappen leiden tot grote resultaten voor fabrikanten
Toyota staat bekend als de meest succesvolle early adopter van Kaizen en de grondlegger van de "continue verbetering"-filosofie voor fabrikanten als onderdeel van zijn innovatieve Toyota Production System. Deze aanpak hielp het bedrijf voertuigen te creëren die bekend staan om hun betrouwbaarheid, terwijl productieverspilling, tijd en energiebronnen werden geëlimineerd. Toyota's "plan langzaam en handel snel"-filosofie hielp bij het ontstaan van de Prius hybride, die het bedrijf positioneerde als de leider in hybride technologie. Meer dan 80 jaar na de oprichting van het bedrijf is Toyota de grootste autofabrikant ter wereld.
Toyota Kata bouwt voort op Toyota's 'continue verbetering'-succesmodel, zodat andere fabrikanten van dit voorbeeld kunnen leren. Deze aanpak is steeds populairder geworden bij fabrikanten die verder willen gaan dan kortetermijnproductiedoelen om hun personeel in staat te stellen dagelijkse, duurzame procesverbeteringen door te voeren.
In Arkansas had Almatis Premiun Alumina eerdere ervaring met het werken met lean-tools en het gebruik van die tools in de traditionele benadering van puntoplossingen, wat leidde tot duidelijke verbeteringen en positieve resultaten. De uitdaging was om continu te verbeteren. Het bedrijf was geïnteresseerd in het revitaliseren van zijn lean-inspanningen en het nastreven van duurzaamheid. Almatis nam voor hulp contact op met de Arkansas Economic Development Commission – Manufacturing Solutions (AEDC-MS), het MEP-centrum in Arkansas.
AEDC-MS probeerde een programma op te zetten dat gericht was op verbeteringen op het gebied van de proceskosten door middel van verlaging van de proceskosten. Een team van 18 mensen identificeerde, beheerde en benutte kansen binnen het productieproces. AEDC-MS leidde acht uur Lean 101-training, inclusief introducties tot de Verbeter Kata. Vervolgens gebruikte het team leiderschapscoaching om zich te concentreren op individuele verantwoordelijkheden, de neiging van de mens om zich tegen verandering te verzetten en blootstelling aan het wetenschappelijke proces van continue verbetering. Zestien uur Value Stream Mapping werd gebruikt om in te spelen op de behoeften van een specifieke productielijn en kantooractiviteiten. Er werd extra tijd besteed aan het managementteam van Almatis om ervoor te zorgen dat ze klaar waren voor de levering van Kata. Een driedaagse Toyota Kata-sessie leidde tot een besparing van $ 12.000/maand in de eerste twee dagen van implementatie, wat een volledig rendement op de investering opleverde binnen de eerste 30 dagen van verbetering.
Andere behaalde resultaten waren onder meer:
- $ 2,5 miljoen aan meer of behouden omzet over een jaar
- 160 nieuwe of behouden banen
- $200.000 aan kostenbesparingen
- $ 475.000 aan nieuwe investering
Hoe Toyota Kata te integreren in uw faciliteit
Om kleine en middelgrote fabrikanten te helpen lean-succes te behalen, zoals Almatis en Toyota, heeft het MEP National Network TM heeft een Toyota Kata-overzicht ontwikkeld:Toyota Kata:de vaardigheden ontwikkelen om te gedijen in de constant veranderende markt van vandaag.
Dit overzicht benadrukt dat, hoewel kleinere fabrikanten misschien niet het niveau van strategische middelen hebben zoals de kolossale Toyota, ze dezelfde methodologieën van Toyota Kata kunnen toepassen, waaronder:
- Nieuwe gewoontes ontwikkelen en mensen anders laten denken over problemen en doelen
- Een manier van werken, en van samenwerken
- Wetenschappelijk denken gebruiken als ingrediënt om teams en organisaties effectiever en succesvoller te maken
- Ontwikkelen van een cultuur van continu leren en verbeteren op alle niveaus door bewust te oefenen
Implementatie van Toyota Kata begint met de toepasselijke naam Starter Kata. Starter Kata richt zich op kleine protocollen en processen die, wanneer ze vroeg en vaak worden toegepast, productiemedewerkers helpen sneller te leren en hen te leren meer samen te werken. De twee belangrijkste elementen van Starter Kata zijn Verbeter Kata en Coaching Kata, zoals aangegeven in het bovenstaande Almatis-voorbeeld.
De Verbeter- en Coaching Kata helpt medewerkers:
- Begrijp de richting of uitdaging
- Begrijp de huidige toestand
- Stel de volgende doelvoorwaarde vast
- Experimenteer naar de doelconditie
Door Toyota Kata te integreren als onderdeel van uw best practices op het gebied van productie, kunnen uw medewerkers met succes obstakels overwinnen en meer zelfvertrouwen en wetenschappelijk denken ontwikkelen om problemen op te lossen.
Het MEP National Network's overzicht van Toyota Kata is een eerste stap om uw personeel in staat te stellen wendbaarder te worden, zodat ze nieuwe manieren kunnen vinden om afval te verminderen, nieuwe technologieën te ontwikkelen en zich aan te passen aan deze nieuwe veranderingen in de steeds groter wordende competitieve wereld van productie .
Industriële technologie
- Lean continue verbetering – belangrijke drijfveren voor continue verbetering
- Het potentieel voor het integreren van visuele data met het IoT
- Het is tijd voor verandering:een nieuw tijdperk aan de rand
- Marketingdoelen vs. Marketingstrategie:wat is het verschil
- Een effectieve klinische leveringsstrategie opstellen voor het postpandemische landschap
- De risico's, beloningen en technologie voor een sterke direct-to-consumer-strategie
- 5 tips voor het bijhouden van elektronica-onderhoud
- Wat is 5S? Een uitleg van de elementen van 5S voor een lean-cultuur
- Maxim brengt intelligentie naar de edge met nieuwe module voor Industrie 4.0
- De 8 verspillingen van Lean Manufacturing
- De uitdaging van de 5S-methode voor de industrie 4.0