Composieten maken nieuwe vliegende speedboot mogelijk
De wereldwijde elektrificatie van transport is een ongelijke evolutie, die tegelijkertijd mogelijk wordt gemaakt en wordt belemmerd door de talloze krachten die de technologische ontwikkeling beheersen en van invloed zijn op alles, van auto's en onbemande vliegtuigen tot spoorvervoer en zeevaartuigen. Deze stimulerende/belemmerende krachten zijn onder meer snel rijpende maar zware batterijen, overheidstoezicht dat zich soms traag aanpast, principes van zwaartekracht en wrijving, strikte veiligheidseisen voor passagiers, angstige verzekeraars en ongelijke ontwikkeling van lichtgewicht materialen.
Toch maken materiaal-, verwerkings-, hardware- en software-innovaties producten mogelijk die slechts een paar jaar geleden ondenkbaar waren, en er is misschien geen beter voorbeeld hiervan dan de Zeven , een nieuwe volledig elektrische, high-range, volledig composiet foiling speedboot die wordt vervaardigd door Candela Boats (Lidingö, Zweden) met behulp van harsmatrixoplossingen van Sicomin Epoxy Systems (Châteauneuf les Martigues, Frankrijk).
Hoe we hier zijn gekomen
Candela Boats werd in 2014 opgericht door CEO Gustav Hasselskog die, hoewel een ingenieur van opleiding, eerder als consultant en in de consumentenchemicaliënmarkt had gewerkt. Naar eigen zeggen had Hasselskog "verveeld" met de zakelijke werkwereld en besloot hij dat hij meer zinvol werk wilde vinden. In 2014 zegde hij zijn baan op en in die zomer trok hij zich met zijn gezin terug in een huis op een van de archipels rond Stockholm, Zweden.
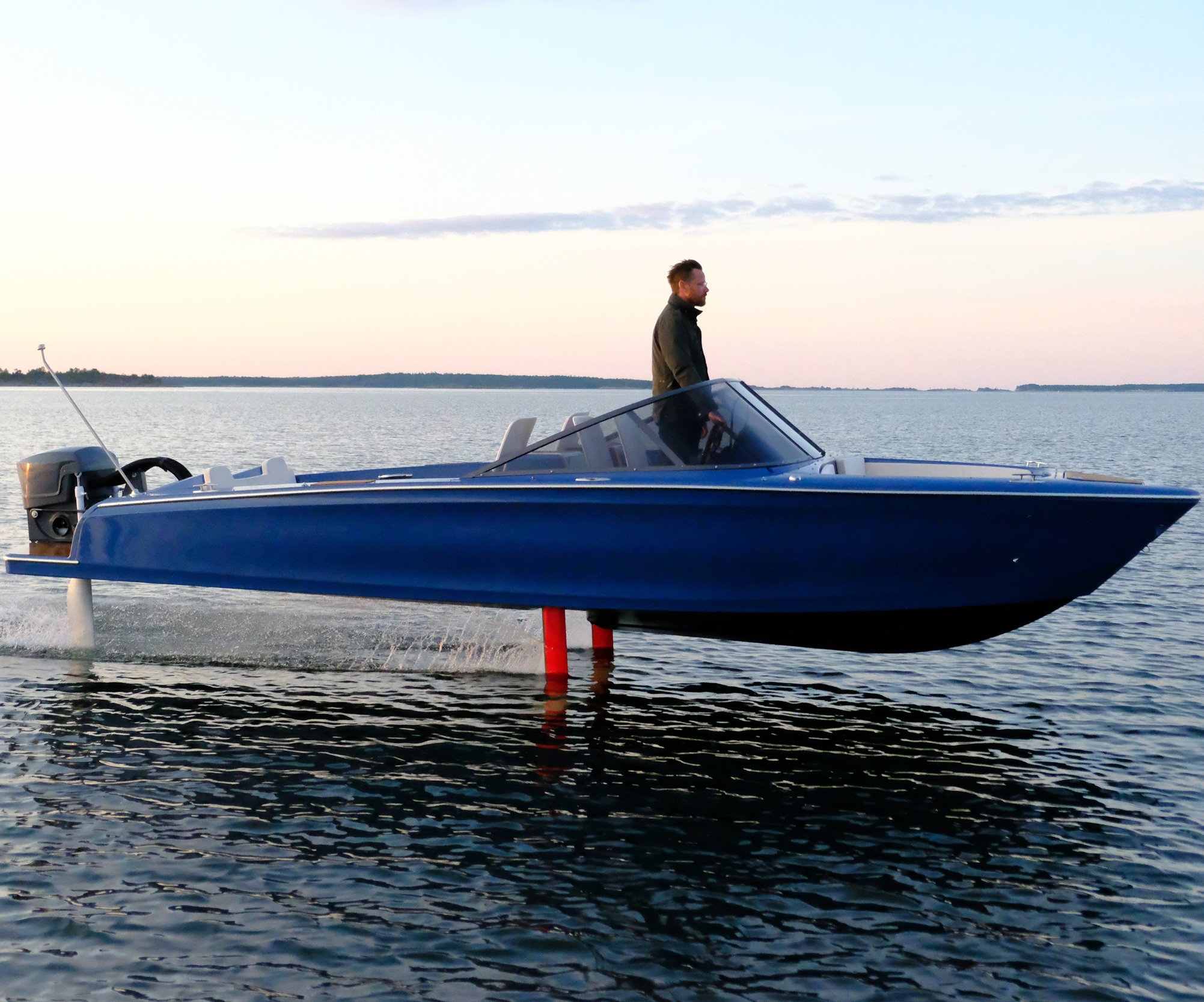
"We hadden een boot van 25 voet met een V-8-motor", herinnert Hasselskog zich, eraan toevoegend dat om overal naartoe te gaan en alles te krijgen een boottocht naar Stockholm nodig was, die minstens $ 50 per reis kostte. "Het voelde een beetje raar om zoveel geld uit te geven aan een boot", zegt hij. Hasselskog begon te rekenen en vroeg zich af wat er nodig zou zijn om de recreatievaart efficiënter te maken. "Wat ik ontdekte", zegt hij, "is dat het onderwerp niet is behandeld om boten efficiënter en elektrisch te maken."
Hasselskog begon de recreatieve maritieme markt verder te bestuderen. Hij bestudeerde batterij- en elektrische voortstuwingstechnologie en bepaalde wat nodig zou zijn om een planerende boot een bereik van ten minste 50 zeemijl te geven - een doel dat hij redelijk achtte. Tot nu toe werd de toepassing van volledig elektrische voortstuwing in planerende vaartuigen geplaagd door een gebrek aan vermogen en een gebrek aan bereik, voornamelijk vanwege de wrijving op het wateroppervlak die een boot moet overwinnen. Verder vereist het vergroten van het bereik of het vermogen in een planerende boot de toevoeging van batterijen, wat ook het gewicht en, bij uitbreiding, de weerstand verhoogt. Kortom, het was niet mogelijk om een planerende boot efficiënter te maken, ontdekte Hasselskog. “Een planerende boot is een doodlopende weg. Efficiënter kun je het niet maken', zegt hij. "Foilen is de enige manier." Dus Hasselskog verkocht het zomerhuis van de familie op de archipel en in 2014 werd Candela Boats geboren.
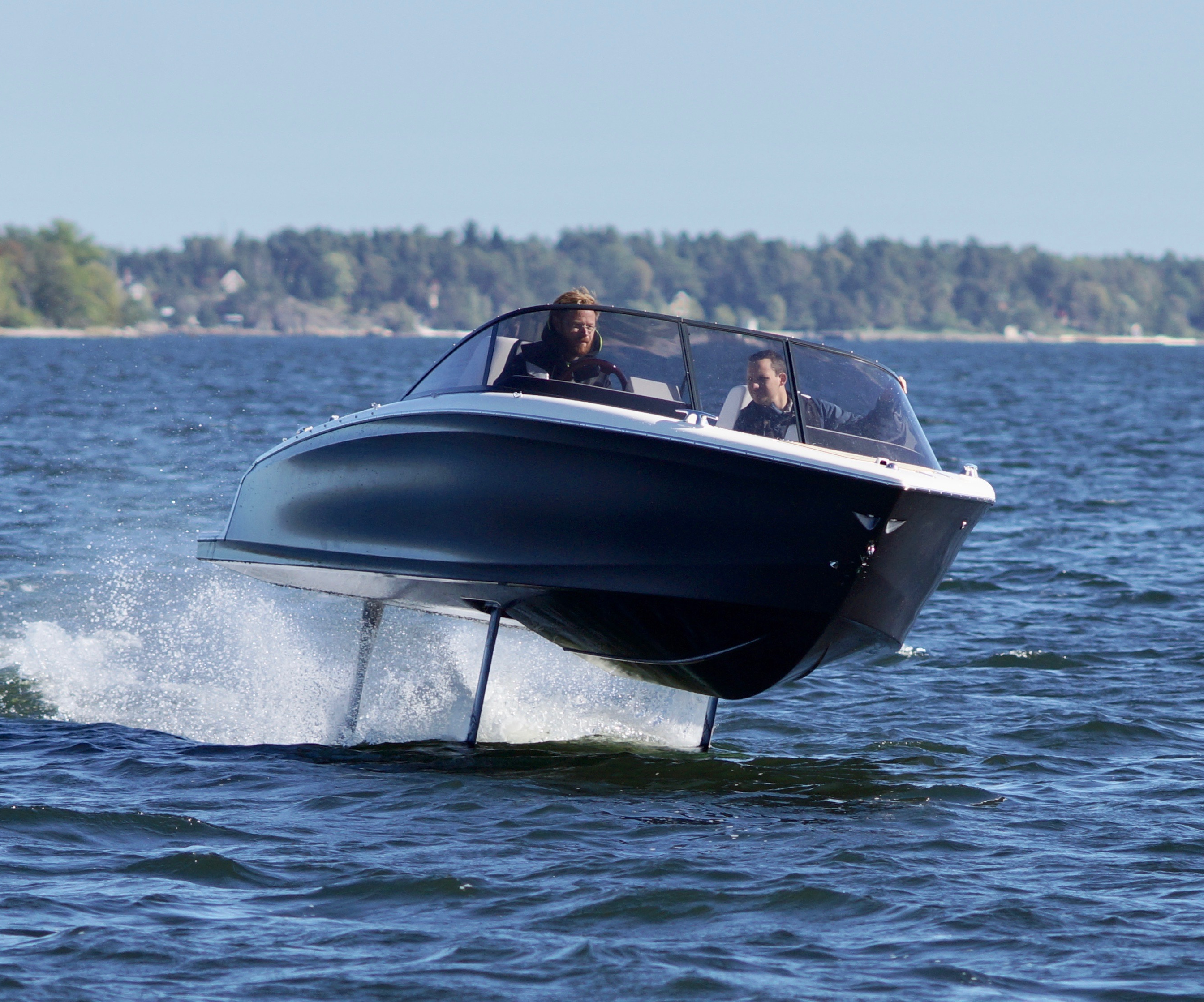
Verijdelen is inherent onstabiel vanwege de complexe thermodynamica die erbij betrokken is. Candela Boats ontwikkelde een geavanceerd systeem van sensoren en bedieningselementen om de folies te manipuleren en een soepele, veilige rit te garanderen. Bron | Candela-boten
Foilen is niet voor bangeriken
De primaire uitdaging van foilen ligt in de inherente instabiliteit van een boot die door en over beweegt water, maar niet op het wateroppervlak. Een folie - of, beter gezegd, een draagvleugelboot - is een vleugelachtige structuur die aan de onderkant van een bootromp is bevestigd. De folie gaat loodrecht op de vaarrichting door het water en geeft, volgens dezelfde principes van vliegtuigvluchten, met een bepaalde snelheid voldoende lift om de boot volledig uit het water te tillen. De wrijving van de romp wordt dus geëlimineerd, waardoor folieweerstand en lucht de enige weerstanden blijven.
Folies kunnen verschillende vormen aannemen, maar in alle gevallen moeten ze een vlak vlak oppervlak bieden dat eerst door de waterkant gaat. En, net als een vliegtuigvleugel, kan de aanvalshoek van een foil in het water worden aangepast om de lift te vergroten of te verkleinen. Folies kunnen ook op verschillende waterdiepten worden ingezet, maar de diepte heeft invloed op de efficiëntie. Relatief ondiepe, oppervlakte-piercing foiling is bijvoorbeeld stabieler, maar minder efficiënt. Dieper foilen is efficiënter maar minder stabiel.
Hoe dan ook, "vliegen" over water biedt een heel andere hydrodynamische omgeving dan die waarmee een planerende boot op het wateroppervlak wordt geconfronteerd. Uit het water en rijdend op foils, gedraagt een boot zich heel anders - gewichtsverdeling, draaien, windweerstand en turbulent water moeten zorgvuldig worden beheerd.
Foiling-technologie, hoewel meer dan 100 jaar oud, werd tot nu toe voornamelijk gebruikt in grote racejachten en sommige passagiersveerboten. Foiling-racejachten worden doorgaans bemand door grote bemanningen die goed zijn opgeleid om een dynamische, snel bewegende foiling-structuur te beheren. Foiling-veerboten vertrouwen op oppervlakte-piercing foiling, wat, zoals opgemerkt, stabieler is.
Hasselskog besloot zijn speedboot zo efficiënt mogelijk te maken en koos daarom voor diepe foils . De uitdaging zou zijn om een diep verijdelende boot gemakkelijk, naadloos en veilig te laten werken, ongeacht wie er aan het stuur zit. Om dit te doen zou de ontwikkeling nodig zijn van een ongekend verijdelend controlesysteem en een bootstructuur die niet alleen lichtgewicht is, maar ook specifiek ontworpen is. voor foilen.
De perfecte folie bouwen
De Zeven is 7,7 meter lang, 2,4 meter breed, weegt 1.300 kilogram en heeft een capaciteit van zes personen. Het maakt gebruik van twee folies, waarvan de grootste ongeveer 2 meter van de voorkant van de boot wordt ingezet. Het ontwerp van de primaire folie is relatief eenvoudig:twee stutten gaan door de romp het water in en hechten haaks op een folie van 2,35 meter lang, 200 millimeter breed en 25 millimeter dik. De folie - ook wel een omgekeerde ∏-foil genoemd - staat loodrecht op de rijrichting. De foil stutten worden door een motor aangedreven om op en neer te bewegen om de foil te laten zakken en op te tillen. Wanneer de boot niet aan het foilen is, wordt de foil volledig ingetrokken, gelijk met de bootromp. Bij foiling snelheden wordt de foil in het water ingezet tot een maximale diepte van 550 millimeter.
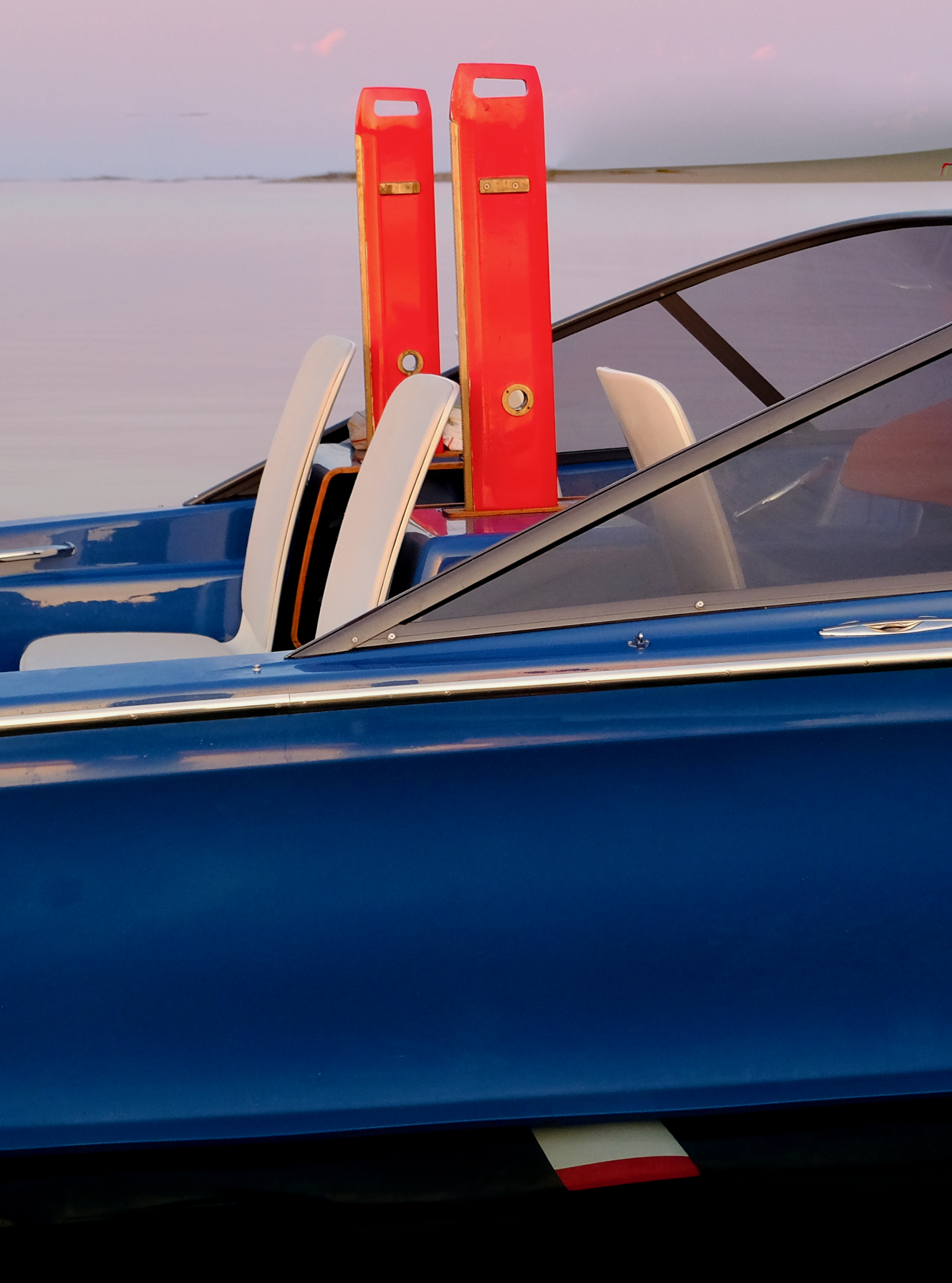
Wanneer de Zeven niet in de foiling-modus is, de twee oranje stutten die aansluiten op en de foil activeren om deze gelijk met de romp te trekken. De wit met oranje folie is hier net onder de romp en net boven het waterniveau zichtbaar. Bron | Candela-boten
Aan de achterkant van de boot zit een tweede, kleinere T-foil die ook als roer fungeert. Het is bevestigd aan een elektromotor van 55 kilowatt die een aandrijfas in het roer aandrijft die een propeller aan het uiteinde van het roer laat draaien. De motor wordt aangedreven door oplaadbare batterijen, die zich in het voorste gedeelte van de romp bevinden, om voor balans te zorgen wanneer de boot vaart. De Zeven begint te foilen met 14-15 knopen, vaart met 22 knopen, heeft een maximale snelheid van 30 knopen en een bereik van 50 zeemijl.
Teodor Hällestrand, productmanager bij Candela Boats, zegt dat de foliesteunen en folies koolstofvezel/epoxy-composieten zijn en een belangrijke ontwerptechnische uitdaging vormden. Om de controle te bieden die nodig is voor een soepele rit, moest Candela de foil kunnen aanpassen aan veranderende bootomstandigheden. Dit vereist een zeer dynamisch sensor / regelsysteem in combinatie met een zeer responsieve folie. "De folie is recht, maar we wilden hem in het water kunnen draaien, afhankelijk van snelheid, rolhoek, hellingshoek en gierhoek", zegt Hällestrand. "We kunnen begrijpen hoe de boot is gepositioneerd en vervolgens de oriëntatie aanpassen om de rit zo soepel mogelijk te laten verlopen." Dit wordt bereikt door het besturingssysteem, dat de stutten dynamisch aanpast om ofwel de aanvalshoek van de folie te veranderen of om de folie te draaien, met name om te draaien.
Hasselskog zegt:"We moeten de frontfolie kunnen verdraaien of een andere aanvalshoek kunnen bieden." Al deze acties gebeuren onder belasting, zegt hij, "dus we hebben een materiaal nodig met een lage torsiestijfheid, maar met een hoge buigstijfheid." Het resultaat is een "redelijk uitgebreid lay-upplan" dat gebruik maakt van unidirectionele (UD) koolstofvezeltapes (voornamelijk ±45 graden) om de vereiste stijfheid en buigmogelijkheden te bieden. De folie maakt gebruik van standaard modulus koolstofvezel van verschillende leveranciers en doordrenkt met SR1710 epoxyhars geleverd door Sicomin Epoxy Systems. De folie wordt bij kamertemperatuur uitgehard, gevolgd door een naharding van 40°C.
Niet je gemiddelde romp
Nergens is Zeven ’s afwijking van de ontwerpnormen voor planerende boten duidelijker dan in de romp – zowel in ontwerp als techniek. Het meest opvallend is het feit dat, hoewel het een standaard V-vormige, golfbrekende romp heeft aan de voorkant van de boot, de romp vlak is van de voorste foils tot aan het achterste. Hasselskog wijst hiervoor op verschillende redenen.
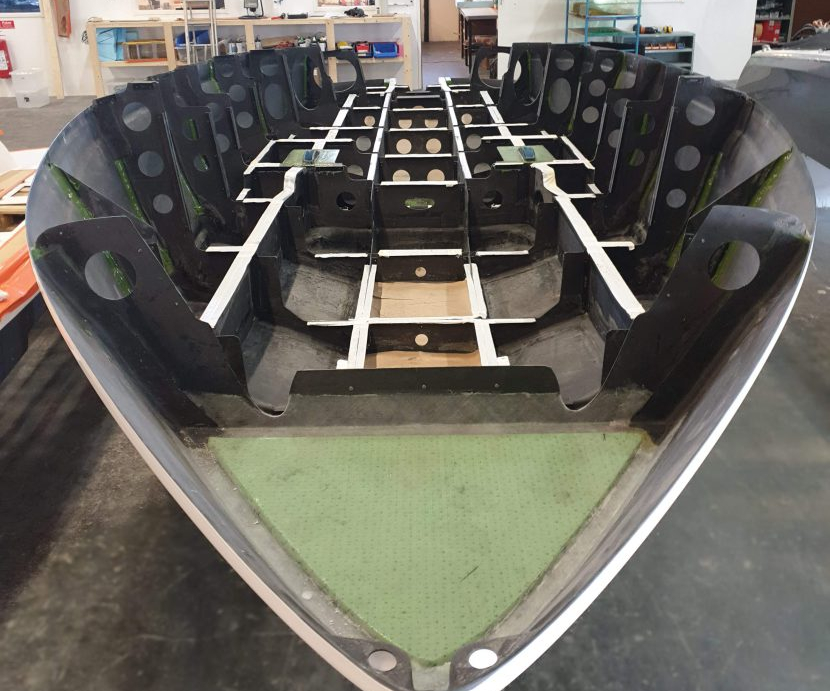
Het interieur van Seven 's romp toont de stringers en ribben die zijn gesneden uit koolstofvezel/epoxy composietlaminaten en vervolgens op hun plaats zijn gehecht met zelfklevende en mechanische bevestigingsmiddelen. Deze architectuur stelt Candela Boats in staat om snel rompen te assembleren en biedt flexibiliteit om zich aan te passen aan ontwerpwijzigingen. Bron | Candela-boten
Ten eerste, zegt hij, hebben we "alleen de V-vorm nodig om de golven te doorboren." Het beschermt ook de foils als de boot niet aan het foilen is. Ten tweede vereenvoudigt het afvlakken van de helft van de romp de fabricage en bespaart het veel gewicht. Ten derde, zegt hij, maakt de vlakke bodem de boot ongelooflijk stabiel op het dok voor het in- en uitstappen. "Het is als een binnenschip", merkt hij op.
Aan de binnenkant van de romp heeft Candela echter gewerkt om de Zeven . te maken niet alleen structureel gezond, maar ook aanpasbaar aan een efficiënte, relatief hoge productiesnelheid. Hällestrand zegt dat de romp qua ontwerp vergelijkbaar is met de romp van een vliegtuig - een huid rond een rooster van stringers en ribben. Net als de folie is de romp doordrenkt met dezelfde UD-koolstofvezel en SR1710-epoxy, vervaardigd op composietgereedschap dat ook met SR1710 is gemaakt. Rompdikte onder de waterlijn is 3 millimeter; rompdikte boven de waterlijn is 2 millimeter.
Marc Denjean, exportmanager bij Sicomin, zegt dat de SR1710 een hoogwaardig epoxysysteem is dat "ver bovengemiddelde mechanische eigenschappen" biedt. Sicomin biedt ook een in-mold epoxy high-build primer, wat betekent dat de romp uit de mal wordt gehaald om te worden geverfd.
Om de stringers en ribben te bouwen, begint Candela met 3 millimeter dik massief laminaat met koolstofvezel/epoxy doordrenkte panelen en bewerkt ze vervolgens CNC in vorm, afhankelijk van waar in de romp het laminaat wordt geplaatst. Om de rompstructuur te bouwen - stringers en ribben - worden deze gesneden vormen vervolgens geassembleerd en aan elkaar en aan de romp bevestigd met lijmverbindingen en mechanische bevestigingsmiddelen.
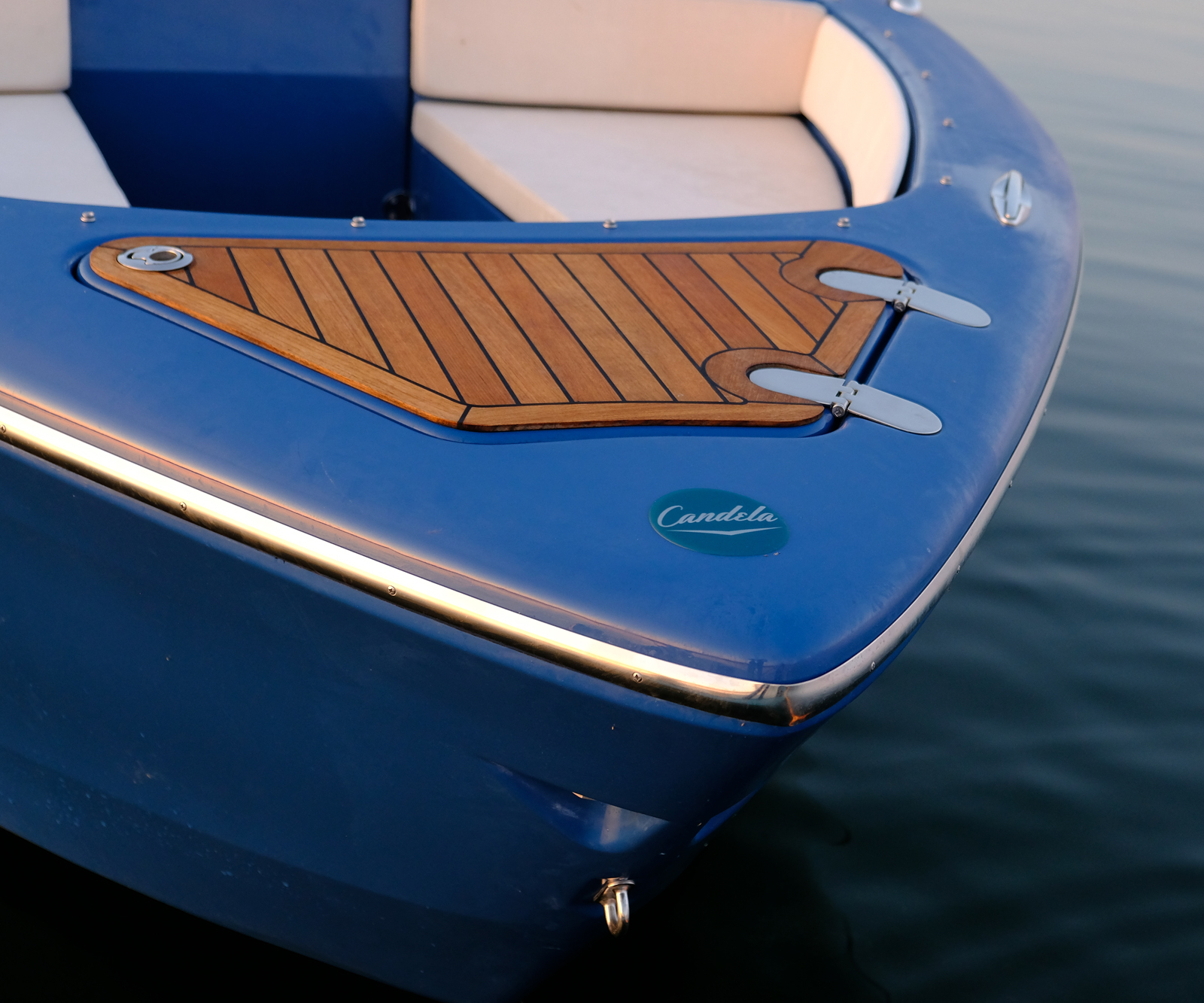
Het batterijpakket van de Seven bevindt zich in het voorste gedeelte van de romp, om de broodnodige balans te bieden wanneer de boot in de foiling-modus is.
Bron | Candela-boten
Dit ontwerp- en fabricageproces van laminaat, op maat gesneden en gemonteerd, is volgens Hasselskog zeer efficiënt gebleken en stelt Candela Boats in staat om de rompstructuur in slechts 40 uur te bouwen. Het stelt het bedrijf ook in staat om gemakkelijk interne structuren aan te passen aan ontwerpwijzigingen zonder de kosten en tijd die nodig zijn om mallen aan te passen. "Het is eenvoudig op te schalen, wijzigingen aan te brengen of een nieuwe structuur te bouwen door simpelweg de bewerkingscode te wijzigen", zegt hij.
Het komt erop neer
In overeenstemming met de oorspronkelijke visie van Hasselskog, is de efficiëntie van de Seven is moeilijk te verslaan — hij is 4-5 keer energiezuiniger dan een vergelijkbare planerende boot op gas en zet 90% van zijn chemische energie om in mechanische energie. Verder zijn de eigendomskosten van de Seven is volgens Candela 95% minder dan een planerende boot op gas.
Het bedrijf heeft 190 bestellingen voor de Zeven, en het verwacht in 2020 40 boten te assembleren. Hasselskog zegt dat Candela momenteel alleen een bootontwerper en -assembleur is. De fabricage van composietstructuren wordt gedaan door derden, maar Hasselskog zegt dat Candela dat werk in huis kan halen, omdat het de productieprocessen wil optimaliseren en uiteindelijk de ecologische voetafdruk van het bedrijf wil verkleinen. "We moeten onze kosten verlagen en dat betekent efficiënter produceren", zegt Hasselskog. "We zijn er nog niet, maar we gaan de goede kant op."
Hars
- CompositesWorld SourceBook 2022
- Composites Evolution toont hoogwaardige prepregs, nieuwe thermoplastische UD-tapes
- Problemen oplossen met thermovormen van thermoplastische composieten
- De evolutie van additieve composieten
- Thermoplastische composieten:structurele bumperbeugel
- Gebruiksvriendelijke kits maken reparatie van composietstructuren in het veld mogelijk
- Composieten als versterkingen voor het lichaam
- Moi Composites introduceert 3D-geprinte glasvezelboot
- UMaine Composites Center ontvangt $ 500.000 om botenbouwers te helpen bij het integreren van 3D-printtechnologie
- Thermoplastische composieten lassen
- Hoogwaardige composieten in Israël