De evolutie van additieve composieten
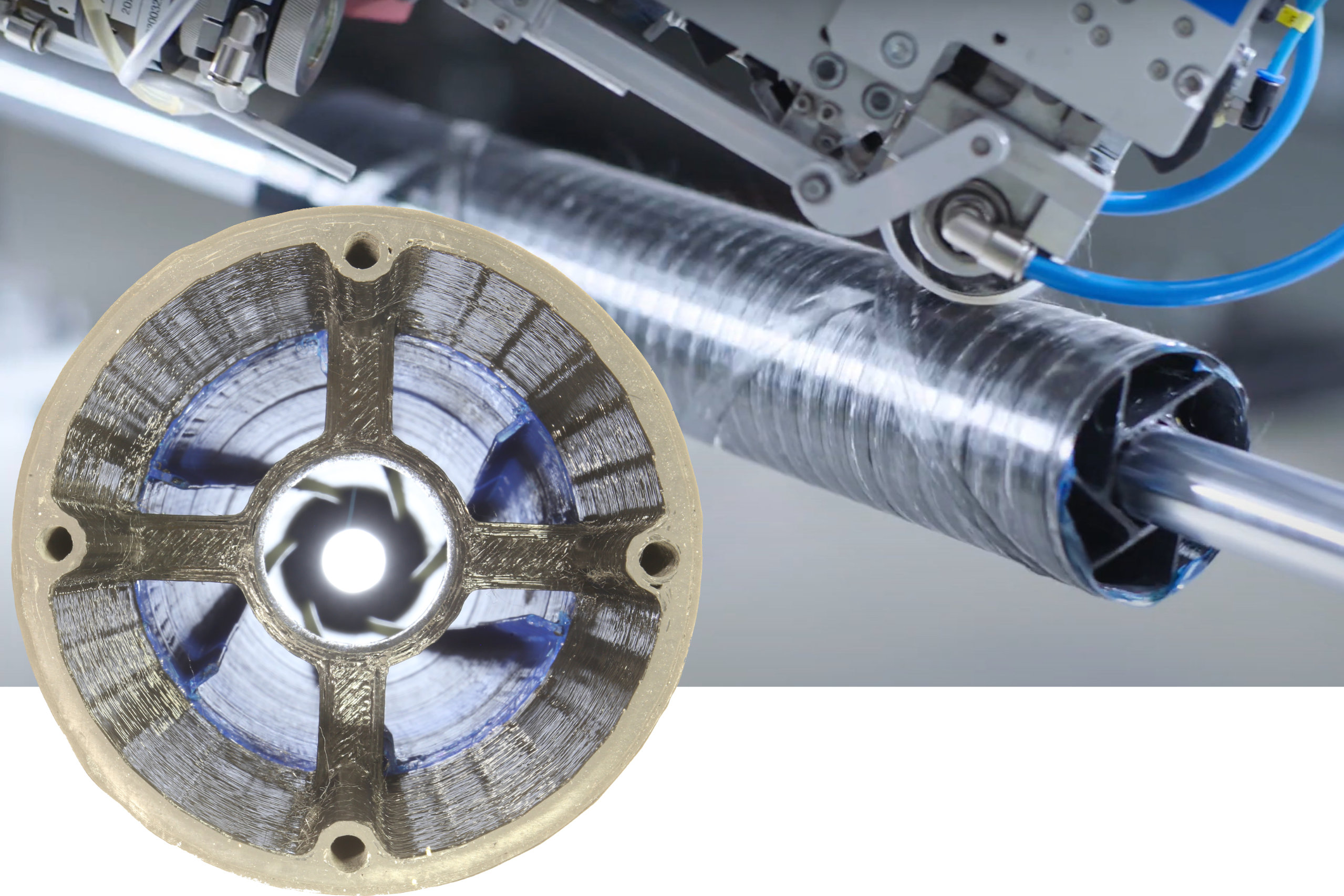
In oktober 2020, CW rapporteerde over 3D-printen van composieten met continue vezels en leverde een landschap van de technologieën die worden ontwikkeld, evenals een classificatie van de gebruikte processen. Dit laatste werd bijgedragen door Alexander Matschinski, onderzoeksmedewerker en expert voor Additive Manufacturing aan de TU München en de leerstoel voor Carbon Composites (Lehrstuhl für Carbon Composites, of LCC, München, Duitsland).
CW werkt opnieuw samen met LCC, maar deze keer om te kijken naar het grotere landschap van Additive Composite Manufacturing (ACM), met name processen die worden ontwikkeld op de interface tussen conventionele composieten en additive manufacturing (AM). "We zien steeds meer technologieën die buiten onze classificaties voor continu 3D-printen van vezels vallen, maar in plaats daarvan geautomatiseerde composietproductie combineren met AM en nieuwe oplossingen bieden die tot nu toe niet mogelijk waren", merkt LCC-onderzoeker Thomas Wettemann op.
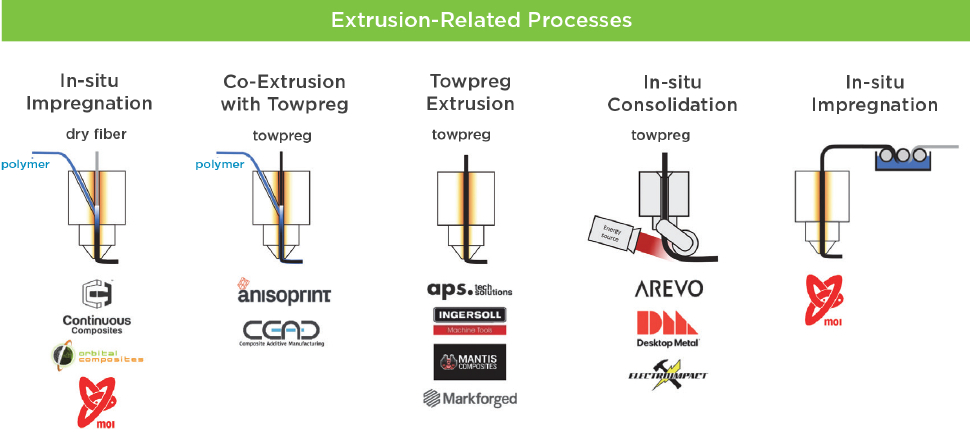
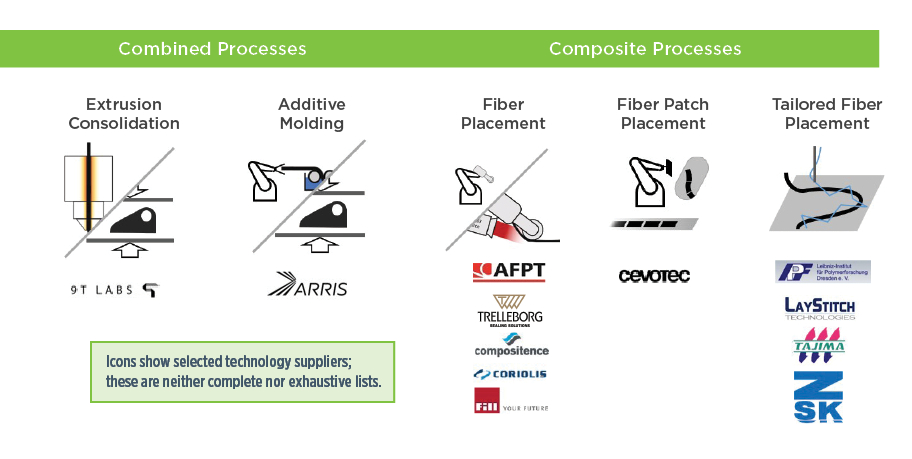
LCC zelf vervaagt de grenzen tussen traditionele processen en 3D-printen door geautomatiseerde vezelplaatsing (AFP) en filamentwikkeling (FW) te combineren met op extrusie gebaseerde ACM (zie "Toekomstige composietproductie - AFP en additieve productie"). "We gaan ook over van traditionele extrusie van thermoplasten naar 3D-printen met thermosets door technologieën aan te passen die we hebben ontwikkeld voor harsoverdrachtsgieten [RTM] en te combineren met ultrasone trillingen”, zegt Dr. Swen Zaremba, plaatsvervangend hoofd van LCC. Tegelijkertijd werkt LCC aan het ontwikkelen van standaarden voor ACM en het verbeteren van haar materialen en processen.
Let op, er is een nog breder ACM-landschap dat bestaat uit gehakte met vezels gevulde filamenten die zijn geëxtrudeerd met behulp van fused deposition modeling (FDM), poedervormige vezelmaterialen die zijn verwerkt met behulp van selectieve lasersintering (SLS) en zeer op maat gemaakte onderdelen met behulp van magnetisch georiënteerde vulstoffen en digitale lichtverwerking (DLP), de laatste ontwikkeld door Fortify (Boston, Mass., VS). Deze processen produceren inderdaad composietonderdelen en openen nieuwe markten en toepassingen, maar deze discussie blijft binnen het domein van continue vezelversterking.
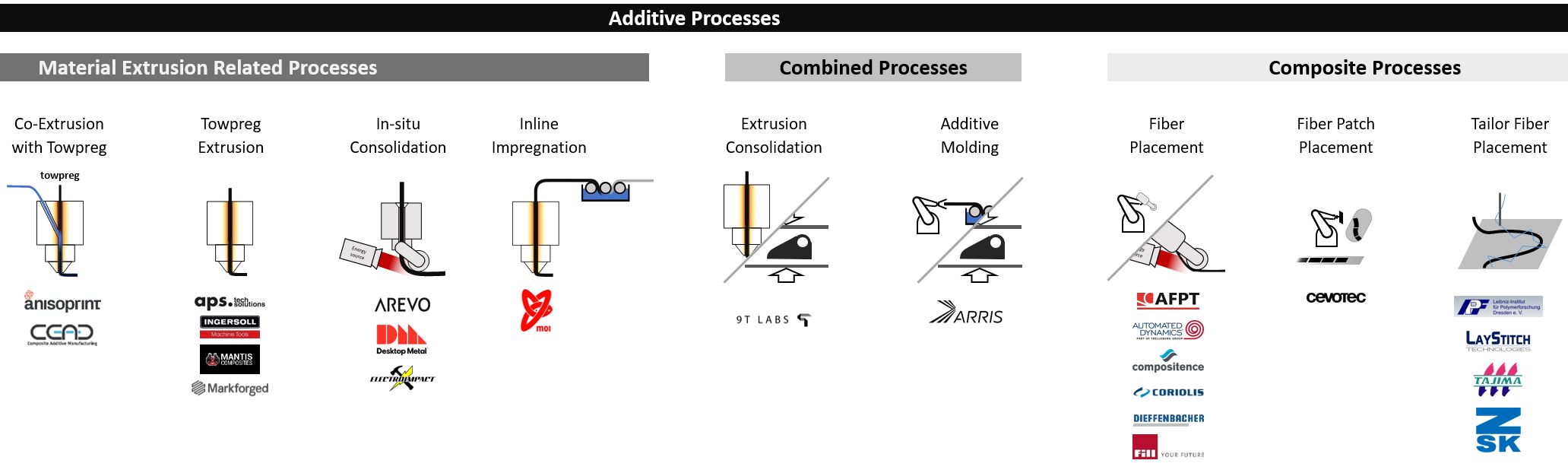
Wat is ACM?
"Meestal hebben we deze discussie eerst, evenals de motivatie om deze nieuwe technologieën te ontwikkelen", zegt Zaremba. Zoals uitgelegd door Wettemann in een SAMPE-presentatie van januari 2019, is de motivatie een kosteneffectieve productie die verder gaat dan massaproductie - inclusief een partijgrootte van één - die ook hulpbronnen bespaart, verspilling minimaliseert of elimineert en milieu- en klimaatvriendelijk is. "Het biedt ook een manier om de procesketen van composieten volledig digitaal te maken", voegt hij eraan toe. "Het is de eerste stap op weg naar decennia van verandering."
Belangrijke componenten van de LCC-definitie van ACM zijn onder meer:
- Lange procesketens teruggebracht tot één punt "verwerking in een doos"
- Globale consolidatie/polymerisatie vervangen door lokale materiaalbehandeling en terugkerende warmtebehandeling
- Gereedschapsloze productie
“ACM concentreert wat voorheen lange verwerkingsketens waren tot min of meer één punt, een soort fabricage in een doos”, zegt Zaremba. Dus, voegt Matschinski eraan toe, "u verwerkt de materialen en geeft het onderdeel zijn vorm in die doos en zonder vormgereedschap." Beiden zijn het erover eens dat de "doos" een zeer grote ACM-cel kan zijn, bijvoorbeeld de SCRAM-cel die in 2020 door Electroimpact (Mukilteo, Wash., VS) is onthuld. "ACM kan ook buiten een enkele doos worden gebruikt", zegt Zaremba, "bijvoorbeeld ons werk om lokale versterking en kleinere functies toe te voegen aan grotere AFP-onderdelen."
Wettemann merkt echter op:"we zien nu voorbeelden van de hele procesketen van composieten in een geautomatiseerde lijn of cel, maar dit is niet wat we zouden definiëren als ACM." De SCRAM-cel daarentegen heeft het vermogen om materiaal te verwerken en vorm te geven zonder gereedschap door een in-situ consolidatie (ISC) thermoplastische AFP-kop te combineren met een fused filament fabricage [FFF, een andere term voor FDM] 3D-printkop. "Voor ons was deze in-situ consolidatie met behulp van AFP inderdaad het begin van ACM bij de LCC, omdat je de uitgeharde/geconsolideerde composieten maakt terwijl je plaatsing of lay-up uitvoert", zegt Zaremba.
Dit brengt ons bij het tweede belangrijke punt in de LCC-definitie van ACM. "Vroeger had je altijd een globale consolidatiestap en idealiter dezelfde materiaalbehandeling en geschiedenis voor het onderdeel zoals het werd gegoten in een autoclaaf, oven, verwarmd gereedschap of pers", legt Zaremba uit. "Met ACM voeren we deze warmtebehandeling en consolidatie op lokale basis uit terwijl we het onderdeel bouwen."
Wettemann wijst erop dat ISC een toegangspoort bood van geautomatiseerde composietproductie tot de wereld van AM, "maar dit stelt ook echte uitdagingen voor de materialen en verwerking, omdat deze lokale materiaalbehandeling ook een terugkerende warmtebehandeling is. Merk op dat we in het begin alleen spuitgietmaterialen aanpasten voor 3D-printen. Maar toen beseften we dat het niet echt geoptimaliseerd is voor FFF-afdrukken. Dus begonnen bedrijven materialen voor hun printsystemen aan te passen om het hoofd te bieden aan de terugkerende verwarming en afkoeling van de harsen, en ook aan de vereiste snelheid en de noodzaak om lagen aan elkaar te hechten en kromtrekken te voorkomen. Dat laatste is ook de reden waarom steeds meer bedrijven continue vezels proberen op te nemen.”
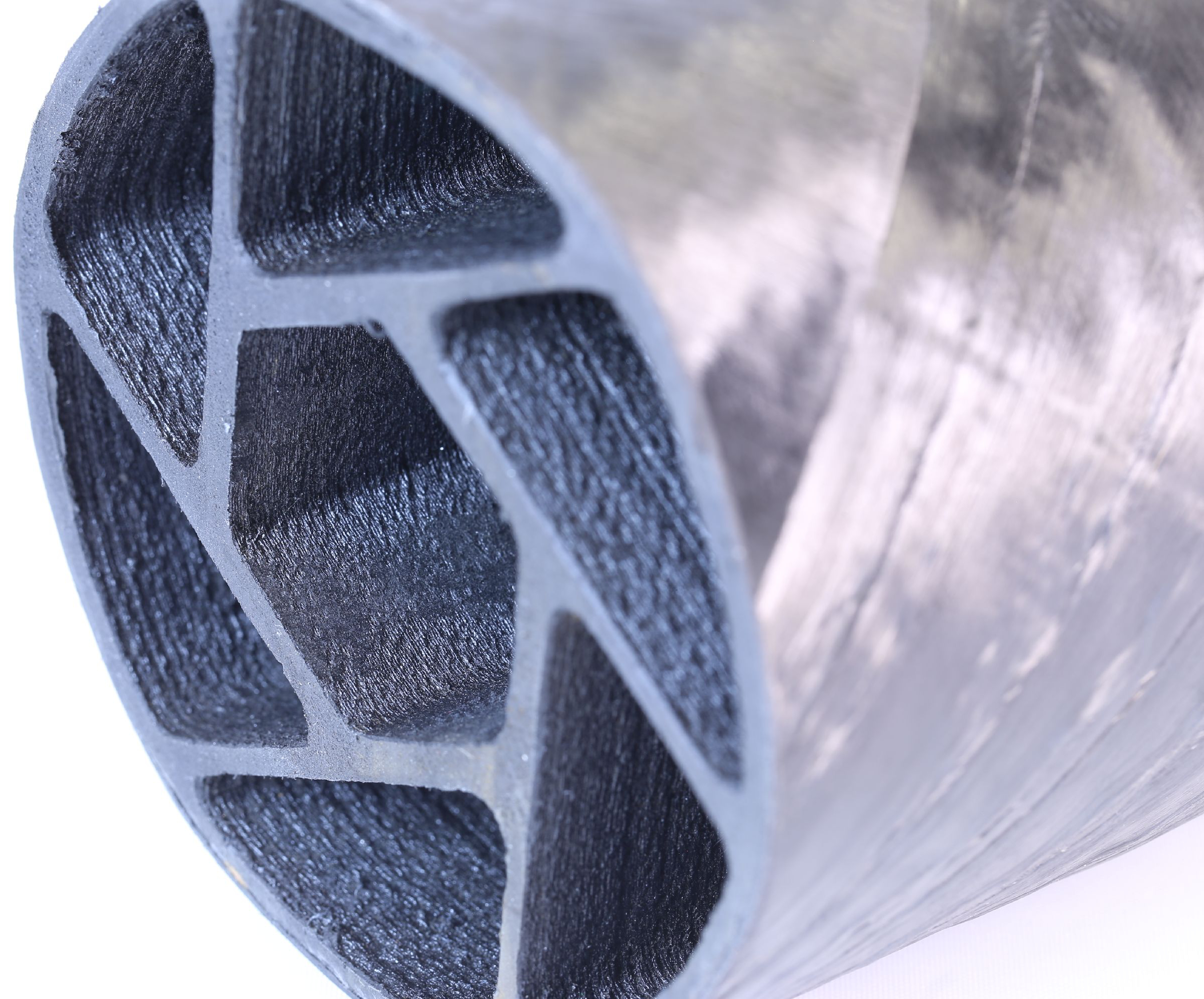
Het integreren van continue vezels levert echter ook problemen op. “Dat is een van de redenen waarom we ons tot ACM aangetrokken voelden”, zegt Zaremba. “3D-printprocessen beloofden veel resultaten, maar de resultaten leverden niet de kwaliteit op die we verwachten voor bijvoorbeeld structurele of ruimtevaarttoepassingen. We zagen een kloof tussen geavanceerde composieten die continue vezels gebruiken en wat AM-technologieën kunnen bieden. LCC wil deze werelden samenbrengen en het beloofde potentieel realiseren, maar ook technologieën combineren om tot nieuwe oplossingen te komen.”
Samensmelten van twee werelden
LCC ziet veel van dergelijke nieuwe oplossingen, bijvoorbeeld het Additive Molding-proces dat is ontwikkeld door Arris Composites (Berkeley, Californië, VS) en de Fusion Bonding-cel voor 3D-printen die is ontwikkeld door 9T Labs (Zürich, Zwitserland), die beide van hoge kwaliteit zijn. volumeprocessen. "Geen van deze processen geeft het uiteindelijke onderdeel vorm binnen het additieve proces, maar gebruik een soort mal en een tweede stap in die mal", zegt Matschinski. “Dit past dus niet in onze definitie van ACM. Beide bieden echter interessante oplossingen die traditionele composietproductie en AM-technologieën combineren.”
"9T Labs gebruikt zeker 3D-printers", merkt Wettemann op, "maar om een voorvorm te maken die vervolgens wordt verwerkt in een gedigitaliseerd vormproces om lichtgewicht thermoplastische composietcomponenten te creëren die volledig nieuw zijn en markten aanspreken die voorheen geen composiettechnologie konden gebruiken. ” Hier verwijst hij naar het doel van 9T Labs om metalen te vervangen in onderdelen waar spuitgieten niet genoeg prestaties kan leveren. “Bij LCC hebben we ook onderzocht hoe we eindeloze vezels in het spuitgieten kunnen introduceren, maar het is vrij moeilijk om een precieze positionering van eindeloze vezels in het injectieproces te maken.” Daarentegen biedt de technologie van 9T Labs een schijnbaar eenvoudig te implementeren productiemethode voor hoogwaardige onderdelen.
Arris Composites heeft een andere benadering, maar bereikt een enigszins vergelijkbaar doel, zij het met het streven naar deelvolumes die een orde van grootte hoger liggen. "We maken niet alleen een hoogvolumeproductie van continue vezelonderdelen mogelijk, maar voegen ook multifunctionaliteit toe die dynamische onderdeelconsolidatie mogelijk maakt", zegt Riley Reese, medeoprichter en CTO van Arris Composites. "We hebben bijvoorbeeld een assemblage van 17 componenten in een enkel onderdeel veranderd, terwijl we de sterkte hebben vergroot en eigenschappen zoals radiotransparantie hebben toegevoegd. We zijn kostenconcurrerend met compressievormen - bijvoorbeeld SMC [sheet molding compound] - maar met de prestaties van continue vezels."
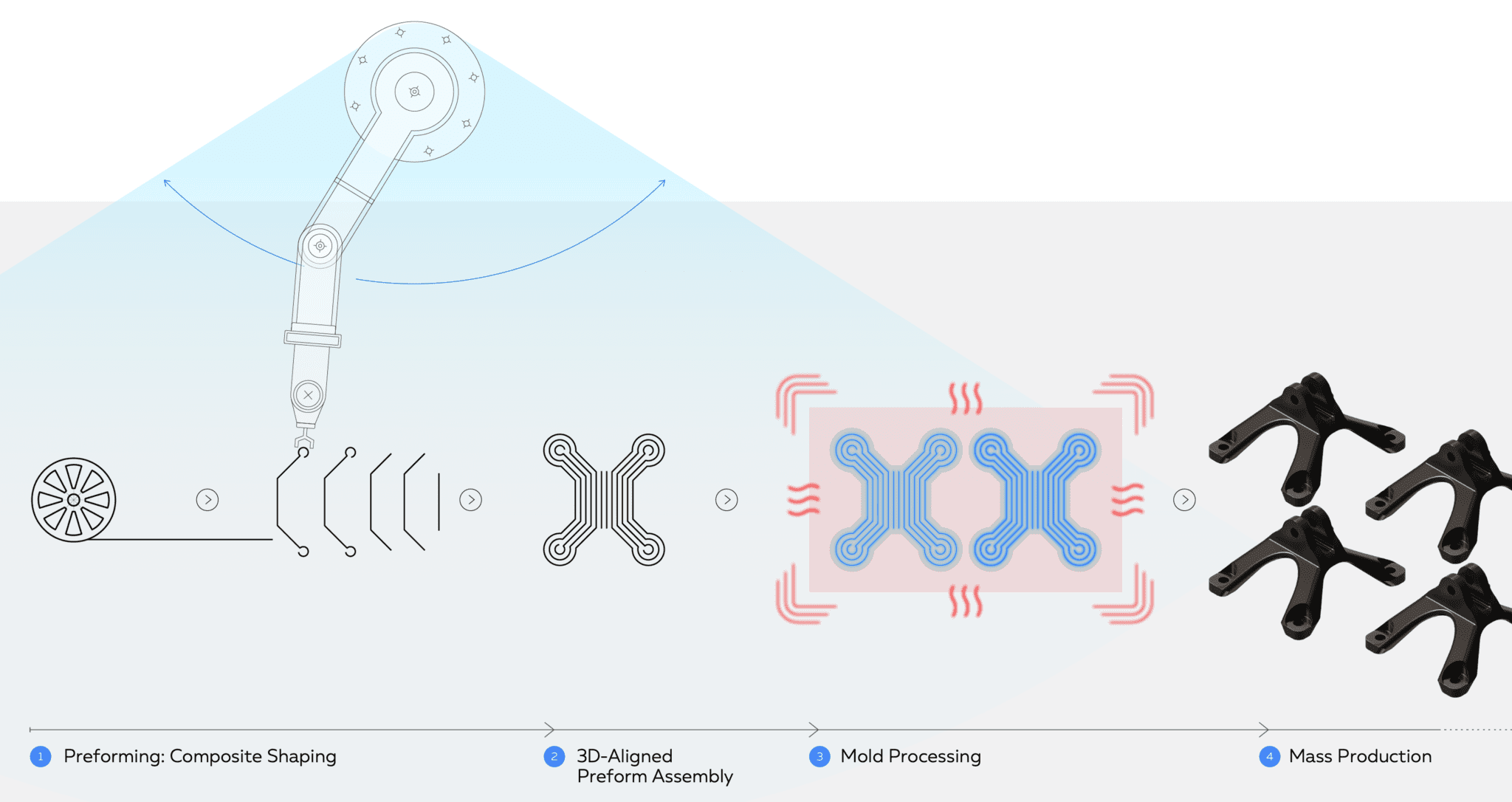
Directe vs. indirecte ACM
Terugkomend op LCC's definitie van ACM, erkent het derde belangrijke onderdeel het debat tussen productie met en zonder vormgereedschap. "Directe Bij benaderingen komt de uiteindelijke vorm van de afdruk - ik heb nooit gereedschap", zegt Wettemann. “Het voordeel is dat we volledig vrij zijn van gereedschapsfabricage. Zolang we mallen hebben, hebben we het over indirecte processen, of we hebben het over de meer conventionele fabricage van composieten, die vervolgens wordt ondersteund door AM-technologieën.”
Wettemann merkt op dat dergelijke hybride benaderingen helpen bij het aanpakken van factoren zoals consolidatie en tooling die de kosten en tijd van de traditionele fabricage van composieten verhogen. "We zagen ontwikkelingen bij het Digital Manufacturing and Design Centre van de Singapore University of Technology en bij Mikrosam [Prilep, Macedonië] van 2015 tot 2017, waar geautomatiseerde robots werden ontwikkeld om geavanceerde composietonderdelen te produceren in een AFP-achtig proces, maar zonder gereedschap", zegt hij. verklaart. "Dus dit gaat richting ACM in die zin dat beide benaderingen erin zijn geslaagd om digitale productie in de vrije ruimte zonder gereedschap te maken, maar verdere ontwikkeling is nog steeds nodig. Het verminderen van de behoefte aan gereedschap is essentieel, want dat geeft ons ook nieuwe mogelijkheden voor zowel het vervaardigen van composietcomponenten als het soort componenten dat gemaakt kan worden.” Bijvoorbeeld, de zeer organische belastingspaden die worden gegenereerd door topologie-optimalisatie en generatieve ontwerpsoftware streven inderdaad naar de efficiëntie van biologische structuren zoals botten en bomen, maar ze zijn erg moeilijk te vervaardigen met continue vezels.
Toekomstige ontwikkelingen bij LCC
"Bij de directe productie van onderdelen zien we hetzelfde dat u in uw landschap laat zien, dat de lijnen vervagen en dat we overgaan op een veel meer hybride productieaanpak", zegt LCC-onderzoeker Patrick Consul (zie "3D-printen van CFRP mallen voor RTM flaperon, exoskeletten en meer”). Eerder dit jaar voltooide zijn team de eerste proeven van een hybride benadering die materiaalextrusie en gerichte energiedepositie [DED] combineert met behulp van een op laser gebaseerde prototypemachine om te printen op voorgeconsolideerde laminaten en zeer grote 3D-prints zonder een verwarmde kamer. "We werken ook aan het combineren van ACM met frezen en AFP, die echt goed passen omdat ze allemaal afhankelijk zijn van gecompliceerde toolpaths", zegt hij. "De overgang tussen hen wordt vrij eenvoudig en je hebt niet veel extra training nodig." Zo wordt de procesketen verkort, gedigitaliseerd en vereenvoudigd.
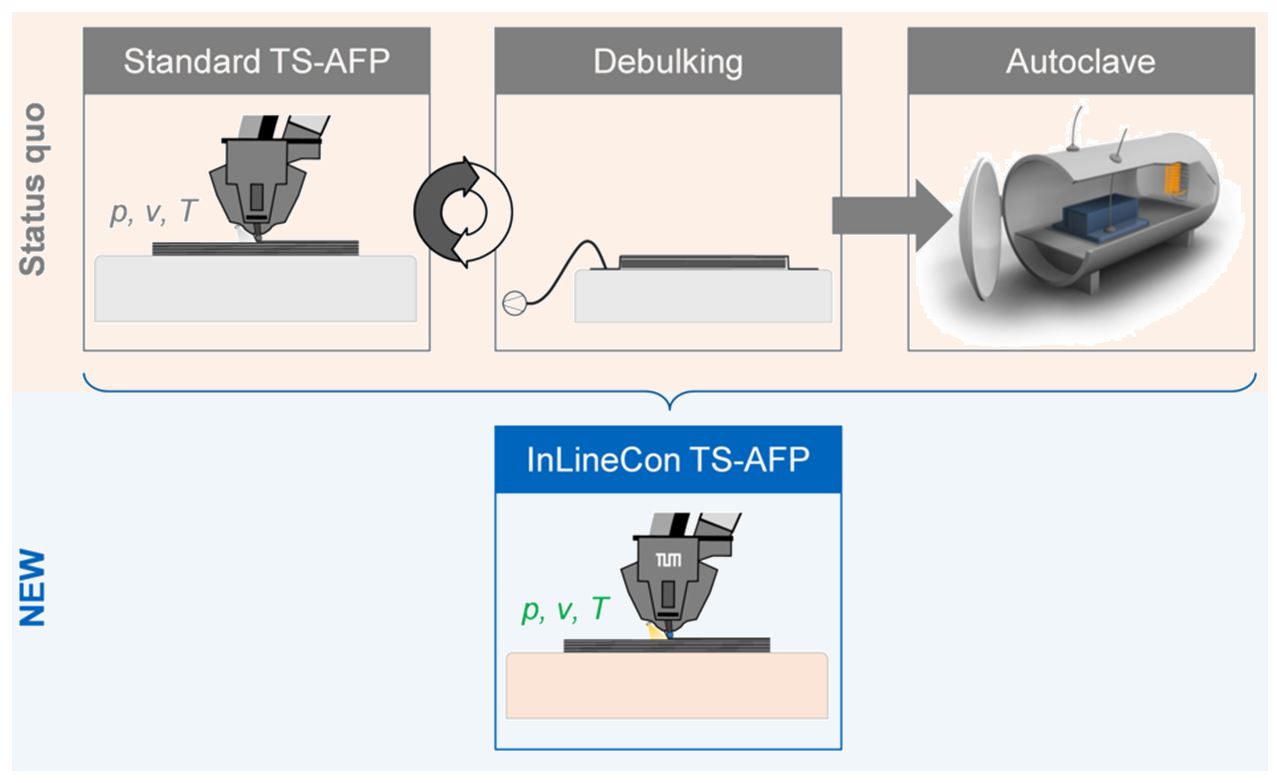
LCC stimuleert ook de hybride benadering door technologieën te combineren die zijn ontwikkeld voor RTM en 3D-printen. "Het resultaat is vergelijkbaar met uitharden in een oogwenk, maar we wilden afstappen van UV-uithardende harsen omdat ze een beetje te duur zijn als je grotere onderdelen wilt bouwen", legt Zaremba uit. "In plaats daarvan gebruiken we een nieuwe ultrasone mengtechniek die we hebben ontwikkeld voor RTM en passen deze nu aan voor gebruik in een typische extruder met goedkope, snel uithardende epoxy's die zijn ontwikkeld voor de auto-industrie."
Matschinski legt deze technologie verder uit:"We gebruiken de ultrasone trillingen om de epoxyhars bijna onmiddellijk te mengen en uit te harden terwijl we de geïmpregneerde vezel tijdens het printen afzetten." Hoe verschilt dit van de ultrasone trillingen die worden gebruikt door het DLR Institute of Composite Structures and Adaptive Systems in Braunschweig, Duitsland (zie "De kosten van 3D-printmaterialen met continue vezels verlagen")? Matschinski legt uit:"DLR gebruikt de ultrasone trillingen om de infiltratie van een thermoplastische matrix in de gespreide vezels te verbeteren om doorlopende vezelversterkte 3D-printerfilamenten te creëren, die vervolgens worden geprint met behulp van conventionele materiaalextrusie. We gebruiken ultrasoon voor het uitharden van een continu vezelversterkt thermohardend filament.”
“Organisaties als Arris Composites, 9T Labs en onze teams hier bij LCC zijn bijvoorbeeld interessant omdat ze zowel wortels en medewerkers hebben uit de composietenwereld als uit de AM-wereld”, zegt Wettemann. “Ze komen samen om nieuwe technologieën te creëren die ons nu kunnen helpen om ons weg te halen van een toekomstige economie die mogelijk beperkt is in hulpbronnen en groei en die worstelt met de klimaatcrisis. Ze bieden een pad naar de benodigde oplossingen.”
Hars
- 3D-printen versus additieve productie:wat is het verschil?
- De waarde van additieve productie in de auto-industrie
- De evolutie van industrieel onderhoud
- Additive manufacturing gaat de volgende fase in zijn evolutie in bij de AHO
- Is hybride productietechnologie de toekomst van additieve productie?
- Rapid Prototyping:de evolutie van 3D-printen
- De evolutie van onderhoudspraktijken
- SAMPE 2018 keynote blikt op de toekomst van composieten
- De evolutie van medische materialen
- De evolutie van medische machines
- De evolutie van 3D-zicht