Composieten-intensief meesterwerk:2020 Corvette, Part 1
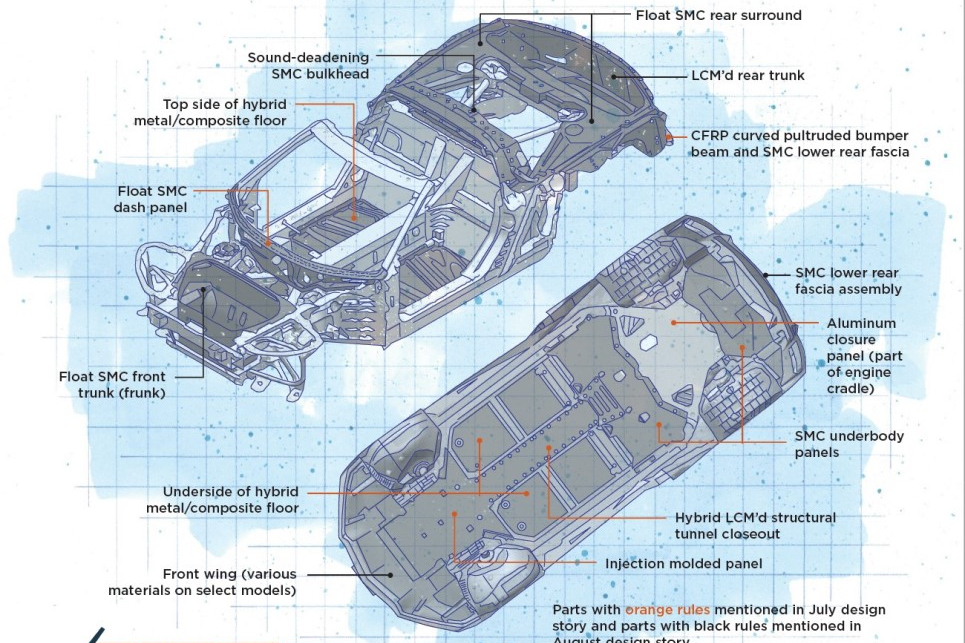
Lees voor deel 2 "Composieten-intensief meesterwerk:2020 Corvette, deel 2".
De langverwachte achtste generatie Chevrolet Corvette (C8) van General Motors Co. (GM, Detroit, Mich., V.S.), dat sinds de officiële onthulling op 18 juli 2019 lofbetuigingen oogstte, eerder dit jaar met de commerciële productie begon. De nieuwe Corvette Stingray cabrio's en coupés vallen niet alleen op vanwege hun schoonheid en het feit dat GM een high-performance, straatlegaal, middenmotorraketschip heeft geproduceerd vanaf minder dan $ 60.000 USD - een derde van de prijs van vergelijkbaar presterende middenmotor auto's, maar ze hebben ook een indrukwekkende reeks nieuwe en echt innovatieve composieten, die we hier en volgende maand in deel 2 zullen beschrijven.
Nieuwe engineconfiguratie verandert alles
GM Engineering ging naar het voorlopige ontwerp in de wetenschap dat ze aan een voertuig met middenmotor zouden werken - de eerste productie Corvette in acht generaties om die configuratie te dragen. "We hebben de architectuur van de voorste motor zo ver mogelijk ontwikkeld voor prestaties, dus het overschakelen naar een ontwerp met middenmotor was de volgende logische stap om een toch al geweldige auto te verbeteren en de segmentleider te zijn", legt Tadge Juechter, executive chief engineer van GM, uit. -Global Corvette . Uitgerust met het Z51-prestatiepakket, de 2020 Corvette Stingray kan in 2,9 seconden 0-60 mph (0-97 kmh) versnellen en topsnelheden bereiken van 194 mph (312 kmh). Het duwen van de motor naar de achterkant van het voertuig had invloed op veel dingen, waaronder het zwaartepunt van de auto, de relatieve positie van de inzittenden, de locatie van de transmissie en het ontwerp van de bodempanelen en opbergruimte in de kofferbak. Het ontwerp met middenmotor introduceerde ook hogere bedrijfstemperaturen en geluid in nieuwe delen van de auto.
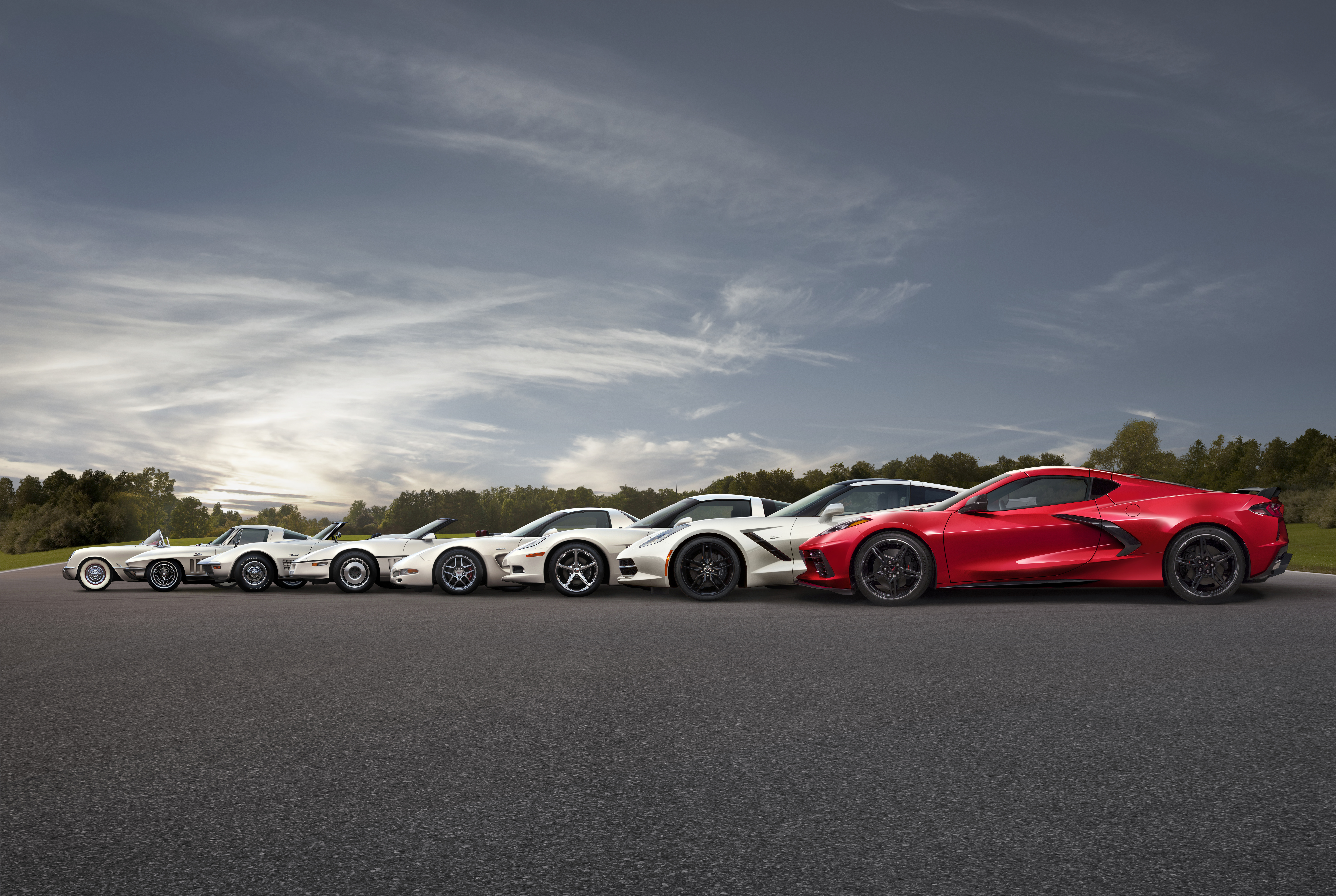
“Vanwege de middenmotor moesten we het anders doen”, legt Ed Moss, Corvette uit. groepsmanager carrosseriebouw. “Vanaf het begin hadden we zoveel discussies over hoe we de carrosseriestructuur moesten indelen. Op een gegeven moment lag alles op tafel terwijl we bespraken hoe elk systeem het beste kon worden ontworpen en gebouwd. We hebben bijvoorbeeld gedebatteerd over metaal versus composiet voor stuurhuizen. Als we de composiet stuurhuizen van de C7 hadden behouden, zouden we aan de scharnierpilaar [A-stijl] moeten hechten, die in een voertuig met middenmotor direct naast het voorwiel zit, waardoor er zeer weinig bagageruimte overblijft. We gingen daar met metaal. We hebben zelfs kort gesproken over metalen versus composiet carrosseriepanelen. Het zou echter economisch onhaalbaar zijn geweest om de stylinglijnen van de C8 in metallic kleuren te creëren.”
"Een echte uitdaging waarmee we werden geconfronteerd, was hoe we met luchtinductie moesten omgaan", herinnert Chris Basela, Corvette zich. hoofdingenieur carrosseriestructuur, die de noodzaak van een andere methode uitlegt om koellucht in en over de natuurlijk aangezogen, 495 pk sterke, 6,2-liter V8-motor te leiden, die 470 foot-pounds (637 Newton-meter) koppel genereert. "We hebben allerlei ontwerpen geprobeerd die de lucht dwongen om echt martelende paden te nemen, waardoor wervelingen en stromen ontstonden die we niet wilden. Het kostte veel iteratief werk met het aandrijflijnteam om het beste pad voor de luchtstroom te ontwikkelen, omdat de auto vrij moet kunnen ademen zonder beperking. We hadden ook toegang tot de luchtkast nodig en moesten rond de kofferruimte achterin werken. Een ander probleem was hitte en motorgeluid in het passagierscompartiment, omdat de inzittenden niet meer achter de motor zitten, maar er recht voor zitten. En we waren ons vooral bewust van de luchtkwaliteit in de cabine, aangezien de wetten in Europa en elders waren veranderd sinds de C7, dus we hebben heel hard gewerkt om VOS [vluchtige organische stoffen] te verminderen.”
"Zelfs uitzoeken hoe je assembleert de auto was een uitdaging”, voegt Moss toe. “Met het ontwerp met de motor voorin heb je een lange motorkap en een grote motorruimte, waardoor de machinist voldoende ruimte heeft om de auto vanuit de binnenkant te bouwen, zelfs als de voorbumperbalk al is vastgelast. Op de middenmotor Corvette , met zijn zeer korte clip aan de voorkant, houden we de voorkant van de auto open als het voertuig wordt uitgebouwd, en schroeven dan de voorbumper vast.”
"Het was nogal een evenwichtsoefening om de juiste vormen te krijgen, terwijl we ervoor moesten zorgen dat onze leveranciers de onderdelen en ons team in Bowling Green [GM's Kentucky-gebaseerde Corvette konden produceren. assemblagefabriek] ze zou kunnen assembleren”, vervolgt Basela. "Uiteindelijk was er maar één overdrachtscomposiet van de carrosserie van de C7 naar de C8." Dit was een sterke Klasse A, 1.2 soortelijk gewicht (SG) plaatvormmassa (SMC), ontwikkeld voor de 2016 Corvette en gebruikt in een verscheidenheid aan exterieurafsluitingen op het nieuwe voertuig.
Voertuigarchitectuur
Al vier generaties (C5-C8), Corvettes hebben een drielaagse, uit meerdere materialen bestaande carrosseriestructuur:het frame , meestal een mix van aluminium of staal - dit keer met een onderdeel van koolstofvezelversterkt composiet (CFRP); de lichaamsstructuur , dat grotendeels bestaat uit gebonden composiet om te profiteren van ontwerp- en productieflexibiliteit; plus vastgeschroefde closeouts (carrosseriepanelen), die zijn samengesteld sinds Covette's Juni 1953 debuut. Deze gelaagde hybride structuur zorgt niet alleen voor betaalbaar lichtgewicht in hoge productievolumes — vooral voor auto's van deze prestatieklasse — maar maakt het ook mogelijk om meerdere voertuigvarianten te produceren tegen een lage gereedschapsinvestering. Voor de huidige C8 is GM er zelfs in geslaagd om alle Klasse A composiet carrosseriepanelen (verlijmde binnen- en buitenkanten) op zowel het basismodel coupé als de cabriolet te produceren met slechts 20 gereedschappen.
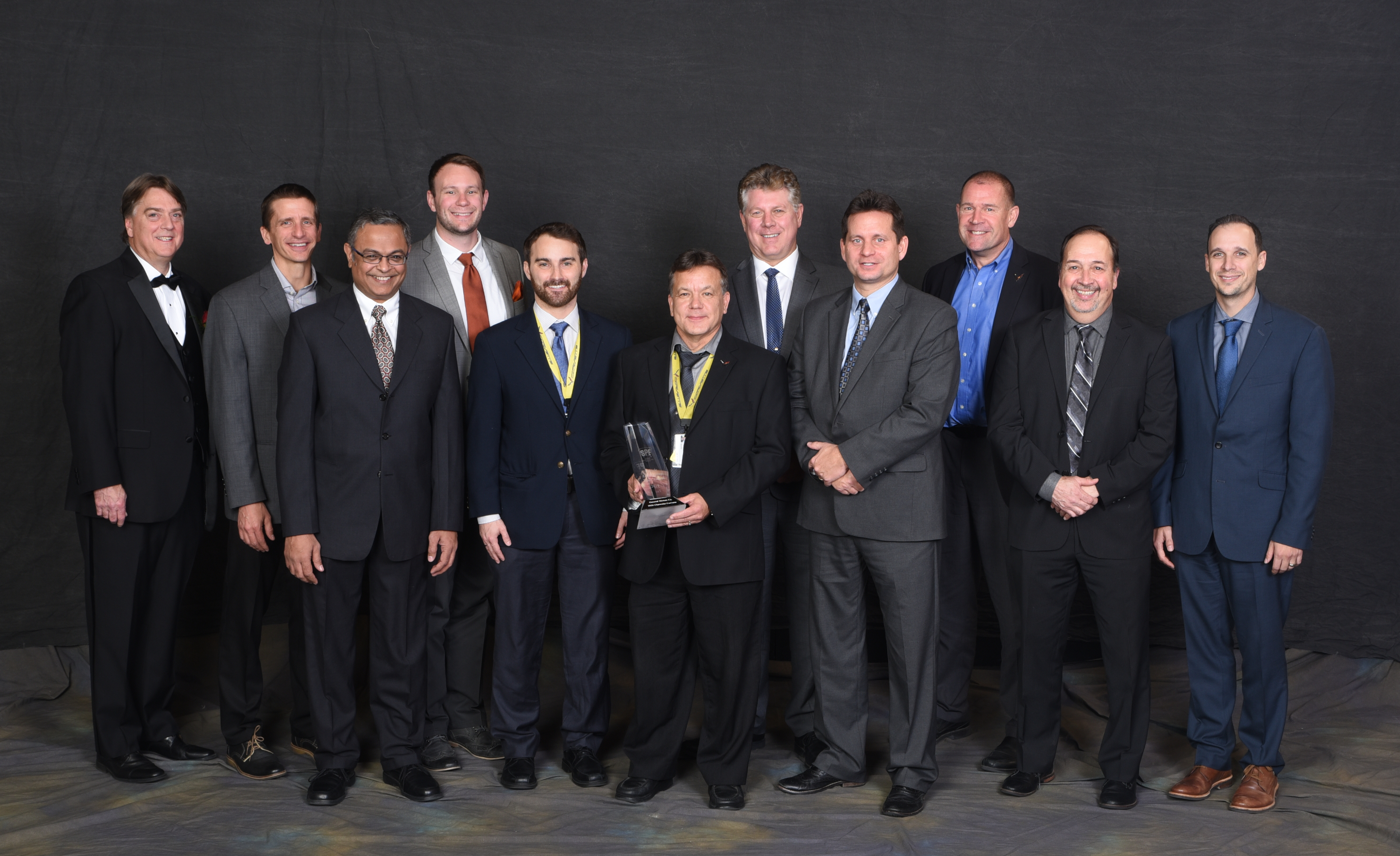
Bovendien, Corvettes zijn altijd ontworpen met een open-dakarchitectuur, of het nu gaat om cabrio's of coupés met vaste of verwijderbare dakpanelen. Omdat voertuigen met open dak over het algemeen minder stijf zijn dan voertuigen met vaste daken, een belangrijk aandachtspunt voor elke Corvette’ De techniek is altijd om een zo stijf mogelijke basis te creëren om de ophanging en besturing te verbeteren. Historisch gezien, tunnels (huisvesting van transmissies en aandrijfassen op voertuigen met motor voorin) hebben de Corvette gedomineerd carrosseriestructuren en zijn belangrijke factoren geweest voor het bereiken van een hoge torsiestijfheid. In het geval van de nieuwe Corvette GM bereikte een nog hogere stijfheid. Met het dak verwijderd, is het koetswerk van de C8 53,78% stijver dan een benchmark met een krachtige middenmotor, 29,27% stijver dan een tweede krachtige middenmotorconcurrent en 13,79% stijver dan de C7. Twee composietonderdelen hebben een belangrijke bijdrage geleverd aan de stijfheid van het voertuig:één rechtstreeks bevestigd aan de framestructuur (achterbumperbalk) en een andere bevestigd aan de bodemplaat (onderste tunnelafsluiting).
Framestructuur
Het frame van de C8 is grotendeels van aluminiumlegering met één CFRP-onderdeel dat is ontwikkeld om te voldoen aan GM's strikte dollar-per-kilogram-doelen. Het frame van de C7 was daarentegen volledig van aluminium en de C6 was grotendeels van staal.
Het enige composietonderdeel dat rechtstreeks op het frame is gemonteerd en dat met de body-in-white (BIW) meegaat door het elektroforetische roestlaagproces (dat GM ELPO noemt), is een unieke achterbumperbalk van CFRP. Dit onderdeel helpt het frame te verstevigen en draagt bij aan de prestaties bij een aanrijding van achteren. Zijn gebogen vorm — mogelijk dankzij een nieuw proces genaamd radiuspultrusie, ontwikkeld door Thomas GmbH + Co. Technik + Innovation KG (TTI, Bremervörde, Duitsland) — stelt hem in staat om de stijlkenmerken van de achterkant te evenaren en in een beperkte pakketruimte te passen, terwijl de dimensionale integriteit nauw blijft. naar de warmte van de motorruimte. Als het eerste gebogen, gepultrudeerde onderdeel van de auto-industrie (zie ons volledige artikel over dit onderdeel in het CW-nummer van mei 2020), werd de holle, tweekamerige balk geproduceerd door Shape Corp. (Grand Haven, Mich., VS) op apparatuur die werd ontwikkeld en gebouwd door TTI. De balk weegt slechts 1,3 kilogram en is voorzien van een gelijmd/vastgeschroefd trekhaakoog dat een uittrekkracht van 25 kilonewton kan leveren.
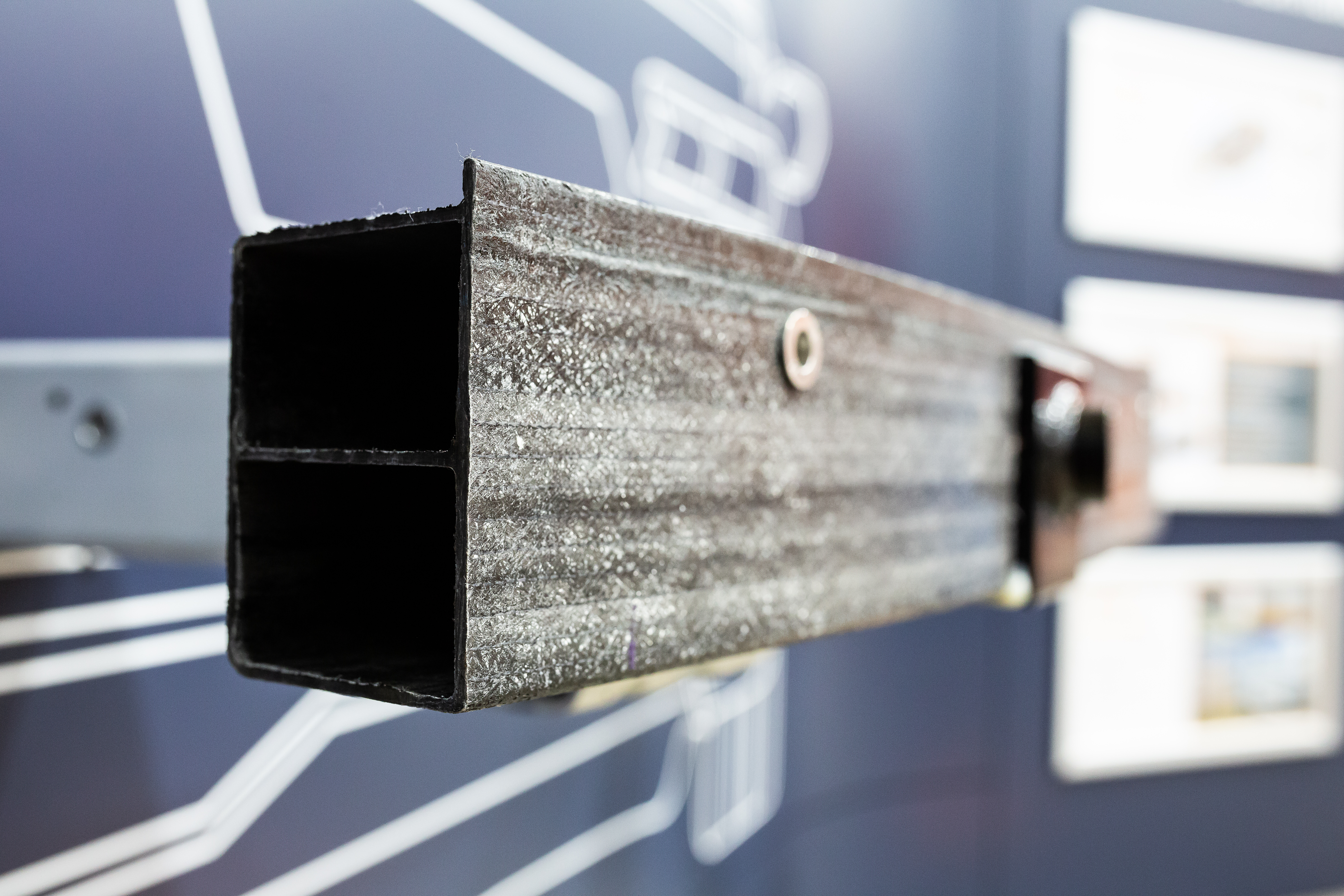
Lichaamsstructuur:deel A
Vrijwel alle carrosseriecomponenten van de C8 zijn van composiet en worden aan het frame gehecht en/of vastgeschroefd nadat dit ELPO heeft ondergaan. Opmerkelijke composietonderdelen op dit niveau zijn onder meer structurele bodemafsluitingen en de vloer - die we in dit nummer zullen behandelen - en voor- en achterkoffers, inductiekanalen en de achterste omlijsting en het schot - die we zullen behandelen, samen met carrosseriepanelen en bekleding , volgende maand.
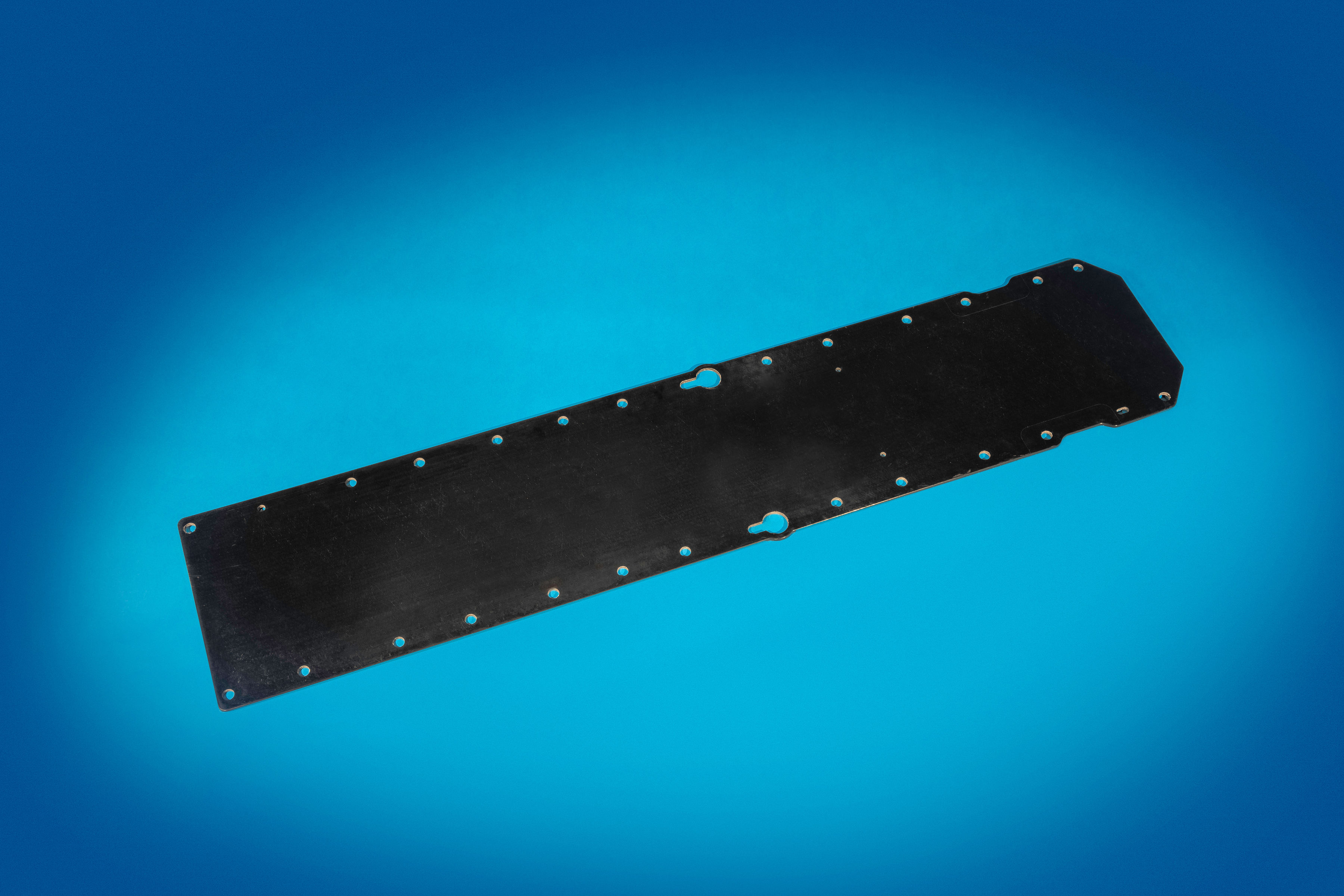
De verwijderbare structurele afsluiting van de onderste tunnel op de C8, die fungeert als toegangsdeur, draagt voor meer dan 10% bij aan de torsiestijfheid van het voertuig en fungeert als primair laadpad tijdens een crash. Dit hybride composiet paneel bestaat uit drie lagen glasvezel preform. Deze bestaan uit continue/geweven en gehakte/willekeurige vezels met een vezelvolumefractie van 38% (FVF), met sluiers toegevoegd aan de boven- en onderlaag op elke stapel voor een verbeterde oppervlakteafwerking. Glazen preforms zijn doorschoten met twee lagen preforms gemaakt met Toray (Tokyo, Japan) T700 12K standaardmodulus koolstofvezel in de vorm van NCF biaxiaal weefsel met 21% FVF en een vinylester (VE) matrix. De closeout wordt geproduceerd door Molded Fiber Glass Co. (MFG, Ashtabula, Ohio, V.S.) met behulp van het eigen PRiME-proces (Prepositioned Reinforcement zorgend voor Manufacturing Excellence), een soort vloeibaar compressiegieten (LCM).
Afgezien van een enkele aluminium close-out bij de achterwielen die deel uitmaakt van de motorsteun, bestaan de overige bodempanelen uit geperst SMC of spuitgegoten thermoplasten. Deze panelen verminderen onder meer de turbulentie en luchtweerstand van de bodem, verbeteren het brandstofverbruik en houden vocht, stof en stenen uit de motor en aandrijflijn van het voertuig. Verder vormen ze de dimensionale basis voor meerdere buiten- en binneninterfaces.
De lage dichtheid maar structurele SMC-panelen bevatten nieuwe formuleringen (in dit geval 40% FVF gehakte glasvezel / onverzadigde polyester (UP) hars) ontwikkeld door MFG. Het materiaal wordt "drijvend" SMC genoemd omdat de dichtheid van elk paneel kleiner is dan 1,0 (gemiddelde SG=0,97) en dus in water kan drijven. MFG produceerde alle structurele SMC- en LCM-onderdelen op de auto.
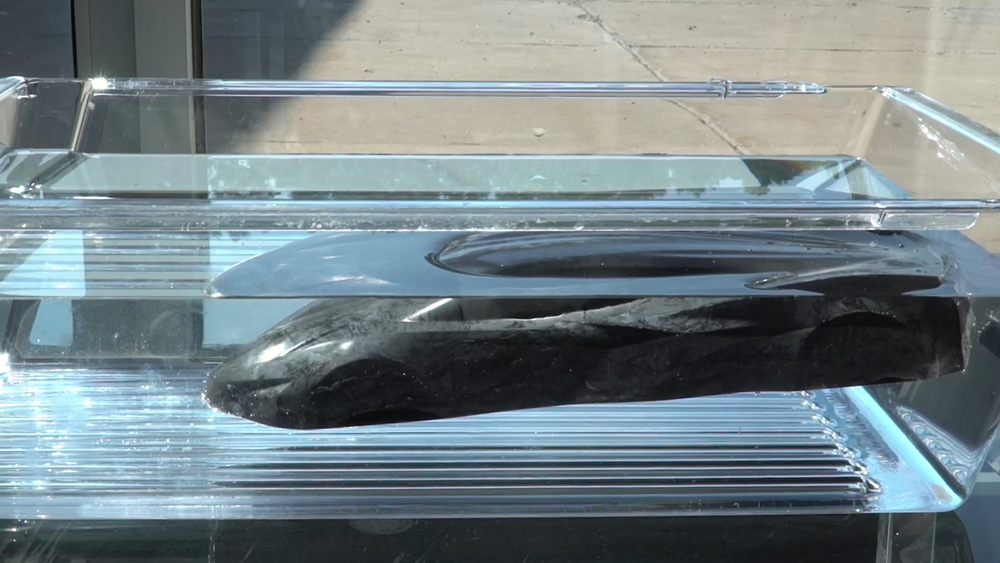
Het voertuig heeft ook een hybride vloer die is geoptimaliseerd voor torsiebuiging en bescherming tegen zijdelingse botsingen (waarbij de rockerpanelen en de tunnel waarop het is aangesloten) worden betrokken. Vloerpanelen zijn voorzien van naar de cabine gericht gestempeld aluminium dat is gehecht aan platen van 1,5-SG-composiet aan de wegzijde (60 gew.% continu en geweven glasvezel/VE) geproduceerd via het PRiME-proces. Alvorens beide lagen warm te hechten met Pliogrip 9100 polyurethaan structurele lijm van Ashland Global Holdings Inc. (Wilmington, Del., V.S.), reinigt en bereidt MFG de materialen voor.
Alle composietonderdelen die rechtstreeks aan het C8-frame zijn gehecht, worden eerst onderworpen aan laserablatie, een proces ontwikkeld door GM, MFG en Adapt Laser Systems LLC (Kansas City, Mo., VS) voor de 2016 Corvette, en aangepast van een composietenindustriemethode voor het reinigen van mallen. Laserablatie vervangt handmatig schuren en reduceert arbeid, tijd en kosten, elimineert stof en verbetert de herhaalbaarheid. Laserpad, aanvalshoek en energieniveau kunnen worden aangepast voor het materiaal en de geometrie van elk onderdeel. Om de productieflexibiliteit te maximaliseren, is de hele onderkant, inclusief de vloer, verbonden met het frame en zichzelf via lijmen en schroeven.
In het augustusnummer van CW gaan we verder met de innovatie van composieten op de nieuwe Corvette , hervat met extra componenten op het niveau van de carrosseriestructuren en afwerking met externe sluitingen (carrosseriepanelen), plus extra bekleding en upgrades. Zie deel 2.
Hars
- 10 voordelen van cloud computing in 2020
- De toekomst van 3D-printen:12 belangrijke inzichten van AMFG's AM Landscape Digital Conference 2020 (deel 1)
- De toekomst van 3D-printen:12 belangrijke inzichten van AMFG's AM Landscape Digital Conference 2020 (deel 2)
- Onderhoudsleiderschap, deel 3
- Inleiding tot harmonischen:deel 1
- Duurzaamheid in productie - deel 3
- 2020-trends en uitdagingen beïnvloed door Covid-19:deel I
- Draaien is optioneel
- Wat is een onderdeelnummer?
- Bewerking van kleine onderdelen
- Cilindriciteit in GD&T