Moleculaire dynamieksimulatie op het snijmechanisme in het hybride bewerkingsproces van monokristallijn silicium
Abstract
In dit artikel worden moleculaire dynamische simulaties uitgevoerd om het snijmechanisme te onderzoeken tijdens het hybride bewerkingsproces, gecombineerd met de thermische en trillingsassistenten. Een aangepast snijmodel wordt toegepast om het materiaalverwijderingsgedrag en de vorming van ondergrondse schade in één trillingscyclus te bestuderen. De resultaten geven aan dat tijdens het hybride bewerkingsproces het dominante materiaalverwijderingsmechanisme zou kunnen transformeren van extrusie naar afschuiving in een enkele trillingscyclus. Met een verhoging van de snijtemperatuur wordt het ontstaan en de verspreiding van scheuren effectief onderdrukt, terwijl de zwelling optreedt wanneer het dominante materiaalverwijderingsmechanisme afschuiving wordt. Het vormingsmechanisme van de ondergrondse schade in één trillingscyclus kan worden onderscheiden volgens de spanningsverdeling. Bovendien wordt het ontstaan van de vacatures in het werkstuk duidelijk naarmate de temperatuur stijgt, wat een belangrijk fenomeen is in het hybride bewerkingsproces.
Inleiding
Eenkristal silicium is een belangrijk halfgeleidermateriaal dat veel wordt gebruikt in infraroodoptica, micro-elektronica en opto-elektronische systemen vanwege zijn uitstekende optische en mechanische eigenschappen [1, 2]. Vanwege de hardheid en brosheid van monokristallijn silicium kunnen echter microscopisch kleine brosse breuken en ondergrondse schade ontstaan tijdens mechanische bewerking. Tijdens het microfreesproces kunnen door machinale bewerking veroorzaakte snijafwijkingen van het inwendige type worden gegenereerd in het werkstuk [3]. Bij bewerking met enkelkristaldiamant (SPDT) kan een beschadigde laag met een bereik van 200 tot 600 nm worden gevormd, afhankelijk van de verwerkingsparameters [4, 5]. Hoewel de ondergrondse schadelaag door slijpen en polijsten kan worden teruggebracht tot ongeveer 50 nm. De bewerkingsefficiëntie en het vermogen om complexe structuren te fabriceren zijn beperkt. Om deze problemen te overwinnen, zijn verschillende ondersteunende bewerkingstechnologieën voorgesteld en getest. Vooral het thermisch ondersteunde snijden (TAC) [6] en het trillingsondersteund snijden (VAC) [7] hebben veel aandacht getrokken vanwege hun buitengewone snijprestaties.
Voor brosse materialen zoals monokristallijn silicium kan de overgang van bros naar ductiel worden bevorderd wanneer de bewerkingstemperatuur wordt verhoogd. Tijdens het TAC-proces wordt het siliciumwerkstuk thermisch zacht gemaakt, waardoor de snijkrachten [8] en specifieke snij-energie [9, 10] afnemen. Ondertussen wordt het uitgloeien van de hogedrukfasen in de kubische siliciumfase duidelijk wanneer de bewerkingstemperatuur wordt verhoogd [11]. Met de juiste selectie van de bewerkingsparameters kan het gewenste bewerkte oppervlak met een hoge fasezuiverheid en lage ondergrondbeschadiging worden bereikt door TAC [12,13,14]. Naast TAC is vibratieondersteund snijden (VAC) een andere methode om een hoogwaardig oppervlak op monokristallijn silicium te verkrijgen. Deze techniek wordt al sinds de jaren zestig toegepast in de maakindustrie [15]. In de vroege ontwikkeling van deze technologie wordt alleen een lineaire trillingsbeweging in de nominale snijrichting toegepast bij het bewerken, wat lineair trillingssnijden (LVC) wordt genoemd. In 1994 werd de elliptische vibratie snijden (EVC) voorgesteld door Shamoto en Moriwaki [16]. Als volgt zijn de bewerkingsmogelijkheden van EVC op veel brosse materialen zoals silicium [17, 18], reactiegebonden siliciumcarbide [7], wolfraamcarbide [19, 20] en gehard staal [21] geverifieerd. Tijdens het EVC-proces kan de ondergrondse schade effectief worden onderdrukt, aangezien de tijdelijke snedediepte (DOC) veel kleiner is dan de nominale DOC [22]. Bovendien worden door de scheiding in elke trillingscyclus de contactoppervlakken tussen het snijgereedschap en het werkstuk blootgesteld aan het omringende gas of fluïdum, dat de gegenereerde snijwarmte afvoert. Daarom kunnen snijgereedschapslijtage zoals hechting en thermochemische reactie [23] effectief worden onderdrukt.
Om de bewerkbaarheid van brosse materialen verder te verbeteren, zijn experimenten met hybride bewerking (HM) uitgevoerd om de thermische en trillingsassistent te combineren [24, 25]. Het bleek dat bij het snijden van Inconel 718 met de HM-methode de machinaal bewerkte oppervlakteruwheid effectief kan worden verminderd [26]. Door experimenten en eindige-elementenmethode-simulaties (FEM) kan een substantiële daling van de snijkrachten en een superieure oppervlaktekwaliteit van titaniumlegeringen worden bereikt tijdens het HM-proces [27]. Deze resultaten demonstreren de haalbaarheid van de HM-methode bij het nauwkeurig bewerken van brosse materialen. Het is echter moeilijk om de fysieke variabelen tijdens het bewerkingsproces direct te observeren en te meten, omdat het snijgereedschap met een hoge frequentie trilt en de vervormingszone op hoge temperatuur is. Bovendien varieert de dikte van de tijdelijke materiaalverwijdering bij nanometrische oppervlaktefabricage gewoonlijk van sub-nanometers tot enkele nanometers. Daarom is de traditionele continuümweergave van het probleem zoals FEM twijfelachtig, aangezien de kwantummechanische effecten duidelijk worden.
In de afgelopen jaren is simulatie van moleculaire dynamica (MD) op grote schaal toegepast in onderzoeken naar het ondersteunende bewerkingsproces vanwege de voordelen ervan bij het bestuderen van het nanometrische snijproces [28,29,30]. Gebaseerd op eerdere simulaties van TAC [31], wanneer de snijtemperatuur wordt verhoogd, wordt de anisotropie in de snijkracht, specifieke snij-energie en vloeispanning duidelijker. Ondertussen is de afschuifkracht in het werkstuk lager bij hogere snijtemperatuur, wat leidt tot smallere afschuifzones en grotere grootten van de afschuifvlakhoek [32]. Bovendien kan de materiaalverwijderingssnelheid worden verbeterd bij toenemende snijtemperatuur, aangezien er meer spanen worden gevormd [33]. Voor het EVC-proces is door MD-simulatie ontdekt dat de drukspanning en schuifspanning in het vervormingsgebied aanzienlijk kunnen worden verminderd in vergelijking met gewoon snijden [34], wat voordelig is voor het onderdrukken van ondergrondse schade. Bovendien laat het EVC-proces duidelijk zien dat de snijspanen dunner worden, wat resulteert in een toename van de verhouding tussen ongesneden spaandikte en gesneden spaandikte [35]. Verder is ontrafeld dat de trillingsparameters, waaronder amplitudeverhoudingen, trillingsfrequenties en faseverschillen, grote invloed hebben op de materiaalverwijderingsprestaties [34, 36].
Deze opmerkelijke prestaties hebben het begrip van het bewerkingsmechanisme voor het ondersteunende bewerkingsproces verbeterd. Om rekentijd en geheugen te besparen, zijn de simulatiesystemen echter meestal vrij klein. In eerdere simulaties van het EVC-proces waren de trillingsamplitudes en de nominale DOC minder dan 5 nm [22, 36]. Daarom is de tijdelijke materiaalverwijderingsdikte meestal minder dan 1 nm, wat het feitelijke materiaalverwijderingsproces niet nauwkeurig beschrijft. Bovendien zijn de MD-simulaties van het HM-proces niet gerapporteerd. Het mechanisme van het materiaalverwijderingsproces en de vorming van ondergrondse schade tijdens het HM-proces is nog onduidelijk. Daarom wordt in dit artikel MD-simulatie uitgevoerd om het snijmechanisme van het HM-proces te onthullen. Het klassieke snijmodel is aangepast zodat de trillingsparameters veel dichter bij de experimentele waarden liggen, de trillingsamplitude wordt bijvoorbeeld vergroot tot 40 nm met een nominale snijsnelheid van 3,125 m/s. Het materiaalverwijderingsmechanisme in één trillingscyclus en de invloed van verhoogde snijtemperatuur worden onderzocht. MD-simulatie wordt uitgevoerd door de beroemde Large-scale Atomic/Molecular Massively Parallel Simulator (LAMMPS) [37]. De nabewerkingssoftware OVITO [38] wordt gebruikt om de simulatieresultaten te analyseren.
Simulatiemethode
Details van het snijmodel
Figuur 1 toont het schematische diagram van het EVC-proces, dat oorspronkelijk is gepresenteerd door Shamoto et al. [39]. Het gereedschapstraject kan worden uitgedrukt als:
$$x\left( t \right) =A_{{\text{c}}} \sin \left( {2\pi ft} \right) - vt$$ (1) $$z\left( t \ rechts) =A_{{\text{d}}} \sin \left( {2\pi ft + \varphi } \right)$$ (2)waar x (t ) en z (t ) vertegenwoordigen de verplaatsing van het snijgereedschap in de x en z routebeschrijving. A c en A d zijn de trillingsamplitude in de nominale snijrichting (x richting) en de nominale DOC-richting (negatieve z richting). Parameters f , v , φ , en t vertegenwoordigen respectievelijk de trillingsfrequentie, nominale snijsnelheid, faseverschil en simulatietijd. De simulatietijd t ik staat voor de tijd van het punt P ik op het gereedschapstraject van Afb. 1.
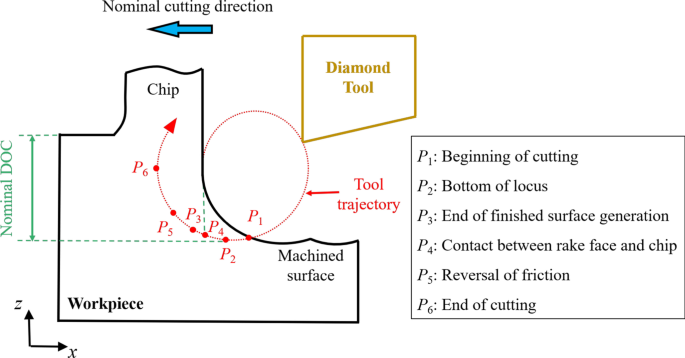
Het schematische diagram van het EVC-proces
Volgens de geometrische relatie [40] is de waarde van t 1 en t 3 kan worden bepaald door:
$$x\left( {t_{1} } \right){-}x\left( {t_{3} } \right) =2\pi v/\omega$$ (3) $$z\left( {t_{1} } \right){-}z\left( {t_{3} } \right) =0$$ (4)Dan, t 6 kan worden verkregen wanneer de transiënte bewegingsrichting van het diamantgereedschap evenwijdig is aan het snijvlak van het gereedschap:
$$\frac{{A_{{\text{c}}} \sin (2\pi ft_{6} ) + v}}{{A_{{\text{d}}} \sin (2\pi ft_ {6} + \varphi ) }} =\tan \gamma$$ (5)waar γ is de hellingshoek van het diamantsnijgereedschap.
Het MD-model is aanwezig in Fig. 2. Het monokristallijne siliciumwerkstuk is ingesteld als vervormbaar lichaam. Terwijl het diamantgereedschap wordt beschouwd als een star lichaam, aangezien de gereedschapsslijtage in deze simulatie kan worden verwaarloosd. De morfologie van het werkstuk in het klassieke snijmodel wordt hervormd volgens het gereedschapstraject in de vorige vibratiecyclus, rekening houdend met de gereedschapsrandradius. Het traject van het gereedschap kan worden bepaald zoals geïllustreerd in figuur 2b. P o en P b zijn het middelpunt en het onderste punt van de gereedschapsrandcirkel. Wanneer het gereedschapskanteffect wordt beschouwd, wordt het transiënte oppervlakgeneratiepunt P c varieert langs de gereedschapsrand tijdens de gereedschapsbeweging. Het eigenlijke afgewerkte oppervlak wordt gegenereerd door de omhullende lijn van de snijkant van het snijgereedschap. Als het traject van P b wordt uitgedrukt door Vgl. (1) en (2), het traject van P c kan worden berekend via [41]:
$$x_{{\text{c}}} \left( t \right) =A_{{\text{c}}} \sin \left( {2\pi ft} \right) - vt - r\sin \theta \left( t \right)$$ (6) $$z_{{\text{c}}} \left( t \right) =A_{{\text{d}}} \sin \left( { 2\pi ft + \varphi } \right) + r(1{-}\cos \theta \left( t \right))$$ (7)waar
$$\sin \theta \left( t \right) =\frac{{z^{{\prime }} (t)}}{{\sqrt {x^{{\prime }} (t)^{2 } + z^{{\prime }} (t)^{2} } }}$$ (8) $$\cos \theta \left( t \right) =\frac{{ - x^{{\prime }} (t)}}{{\sqrt {x^{{\prime }} (t)^{2} + z^{{\prime }} (t)^{2} } }}$$ (9 )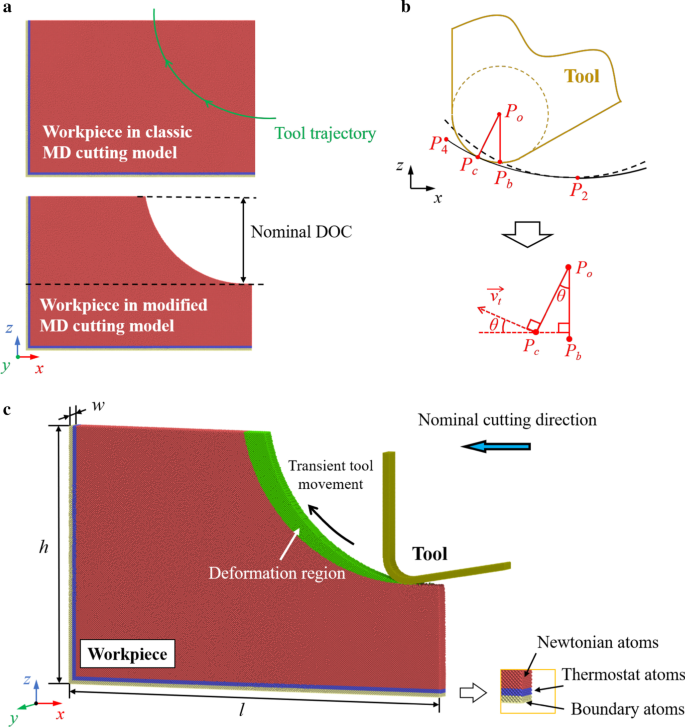
Schema van het MD-snijmodel. een Wijziging van het werkstuk. b Bepaling van het gereedschapstraject. c De morfologie van het gewijzigde MD-model. Groene atomen vertegenwoordigen het vervormingsgebied in één trillingscyclus
Siliciumatomen zijn onderverdeeld in drie groepen:grensatomen, thermostaatatomen en Newtoniaanse atomen. De grensatomen worden in hun gebalanceerde positie gefixeerd om het werkstuk tijdens de simulatie vast te houden. De thermostaatatomen worden op omgevingstemperatuur gehouden om de gegenereerde snijwarmte af te voeren, terwijl Newtoniaanse atomen de tweede wet van Newton volgen.
Details van de simulatieparameters staan vermeld in Tabel 1. De lengte l en hoogte h waren vastbesloten om voldoende afstand te bewaren tussen de snijzone en de vaste grenzen. De periodieke randvoorwaarde wordt toegepast langs de y richting om bulksilicium na te bootsen. De nominale snijrichting, gereedschapshark/spelingshoek en faseverschil werden bepaald onder verwijzing naar de experimentele opstelling [42]. De trillingsamplitude en nominale DOC worden vergroot om de experimentele schaal te benaderen met acceptabele simulatiekosten. Ondertussen werden, om de dikte van het verwijderde materiaal (groene atomen in figuur 2c) te garanderen, de snelheidsverhouding en de trillingsfrequentie ingesteld op respectievelijk 40 en 500 MHz. Daarom werd de nominale snijsnelheid bepaald op 3,125 m/s. Bovendien worden simulaties met verschillende snijtemperaturen uitgevoerd om het effect van thermische assistent op het snijmechanisme te onthullen. De snijtemperatuur wordt verhoogd van 300 tot 1200 K, wat realiseerbaar is tijdens TAC-achtige laserondersteunde bewerking [4, 11].
In dit aangepaste model wordt alleen de snijfase tijdens de vibratiecyclus gesimuleerd en worden de tijdstappen opgeslagen wanneer het werkstuk wordt gescheiden met snijgereedschap. Daarom kan de rekenkracht worden geconcentreerd op het tijdelijke snijproces. Het belangrijkste is dat het proces van tijdelijke materiaalverwijdering nauwkeurig kan worden beschreven. Een vergelijking tussen het aangepaste model en het klassieke MD-model wordt weergegeven in tabel 2.
Potentiële functie
In MD-simulatie is het belangrijk om een robuust potentieel aan te nemen om de interactie tussen atomen te beschrijven. Voor monokristallijn silicium hebben wetenschappers veel mogelijkheden ontwikkeld, zoals de gemodificeerde embedded-atom-methode (MEAM) [45], Stillinger-Weber (SW) [46], Tersoff [47] en ladingsgeoptimaliseerde veellichamen (COMB) [ 48] potentiëlen. Van deze potentiëlen heeft het analytische obligatie-orderpotentieel (ABOP) voorgesteld door Erhart en Albe [49] steeds meer aandacht getrokken. Het is een potentiaalfunctie met drie lichamen die het vormen en verbreken van bindingen mogelijk maakt tijdens de bewerkingssimulatie. Volgens eerdere onderzoeken [50] kan de ABOP zowel dimeer- als bulkeigenschappen van silicium nauwkeurig beschrijven. Ondertussen zijn de mechanische eigenschappen van silicium gemaakt door de ABOP goed consistent met de experimenten [31], wat belangrijk is in MD-simulaties van machinale bewerking op nanoschaal. Daarom wordt in dit artikel het ABOP-potentieel toegepast om de silicium-silicium- en koolstof-koolstof-interacties te beschrijven. Ondertussen wordt de interactie van silicium-koolstof beschreven door het Morse-potentiaal, waarvan is bewezen dat het een efficiënt potentieel is in snijsimulatie op nanoschaal [51, 52]. De Morse-potentiaalfunctie kan worden uitgedrukt als:
$$E_{{\text{Si - C}}} \left( {r_{ij} } \right) \, =D_{{\text{M}}} \left[ {{\text{e}} ^{{ - 2a(r_{ij} - R_{{\text{M}}} )}} - 2{\text{e}}^{{ - a(r_{ij} - R_{{\text{ M}}} )}} } \rechts]$$ (10)waar D M , een, en R M vertegenwoordigt respectievelijk de cohesie-energie, de elasticiteitsmodulus en de evenwichtsafstand tussen atomen. De parameters voor Morse-potentiaal is [53]:D M = 0,435 eV, a = 46.487 nm −1 , R M = 0.19475 nm.
Resultaten en discussie
Snijprestaties
Bij gewoon snijden kan het dominante materiaalverwijderingsmechanisme sterk worden beïnvloed door de onvervormde spaandikte [54]. Met een kleine onvervormde spaandikte is extrusie het dominante materiaalverwijderingsmechanisme. De metallische stabiele fase (Si-II) kan worden gegenereerd door de hogedrukfaseovergang (HPPT), die de ductiele vervorming van silicium mogelijk maakt. Wanneer de onvervormde spaandikte wordt vergroot, kan materiaal voornamelijk worden verwijderd via een afschuifproces. Tijdens het EVC-proces kan het materiaalverwijderingsmechanisme, aangezien de onvervormde spaandikte constant varieert, in één trillingscyclus van extrusie naar afschuiving transformeren. Afbeelding 3 toont de snapshots van de snijsimulatie bij 300 K. De kristalstructuur van het werkstuk wordt bepaald door de common-buuranalyse (CNA) [55]. Deze analyse vindt atomen die zijn gerangschikt in een kubusvormig of hexagonaal diamantrooster. De niet-diamantstructuur in figuur 3c, e bevat voornamelijk de amorfe fase (a-Si), Si-II en andere defecte atomen [56]. Deze structuren zijn onstabiel en zullen na het snijden veranderen in a-Si. Uit Fig. 3b, c kan worden afgeleid dat materiaal voornamelijk wordt verwijderd door extrusie in de eerste snijfase. Een voorbijgaand stagnatiepunt kan worden waargenomen nabij de snijkant van het snijgereedschap. Net als bij gewoon snijden, worden materialen in het vervormingsgebied door het stagnatiepunt verdeeld in spanen en gecomprimeerd materiaal. Naarmate het snijgereedschap voortschrijdt, wordt de niet-vervormde spaandikte vergroot. Afschuifvlakken en polykristallijne korrels worden gegenereerd in het werkstuk, wat aangeeft dat afschuiving het dominante materiaalverwijderingsmechanisme wordt.
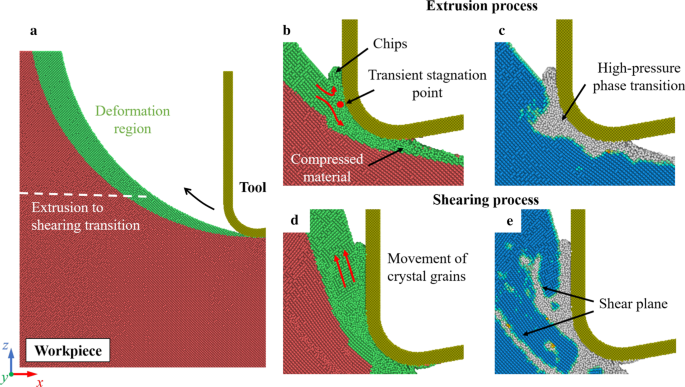
Overgang van het materiaalverwijderingsmechanisme. een Illustratie van het vervormingsgebied. b , d Extrusie- en knipproces. c , e Identificatie van de kristalstructuur in het werkstuk. Blauwe atomen vertegenwoordigen de kubische diamantstructuur, terwijl de grijze atomen zich in de niet-diamantstructuur bevinden
Afbeelding 4 toont de morfologie van het werkstuk bij verschillende snijtemperaturen. Bij 300 K kunnen duidelijke barsten en breuken in het werkstuk worden waargenomen tijdens de opwaartse beweging van het gereedschap. Voor bros materiaal zoals monokristallijn silicium zou de opwaartse beweging van het gereedschap leiden tot het afscheuren van materialen en defecten in het werkstuk achterlaten, wat in EVC als een specifiek probleem wordt beschouwd [42]. Hoewel deze scheuren kunnen worden verwijderd door verdere trillingscycli, zal de bewerkingsstabiliteit worden beïnvloed door de onregelmatigheid van het werkstukoppervlak. Wanneer de snijtemperatuur wordt verhoogd, wordt het ontstaan en de verspreiding van scheuren effectief onderdrukt. Uit Fig. 4d wordt geen duidelijke breuk gedetecteerd wanneer de snijtemperatuur stijgt tot 1200 K. Er wordt echter waargenomen dat bij 900 K en 1200 K zwelling van het bewerkte oppervlak duidelijk wordt wanneer het materiaalverwijderingsmechanisme verandert in afschuiving. Er kan worden geconcludeerd dat naarmate er meer kristalkorrels worden gegenereerd in de afschuiffase, de zwelling kan worden veroorzaakt door de rotatie van deze kristalkorrels bij hoge temperatuur.
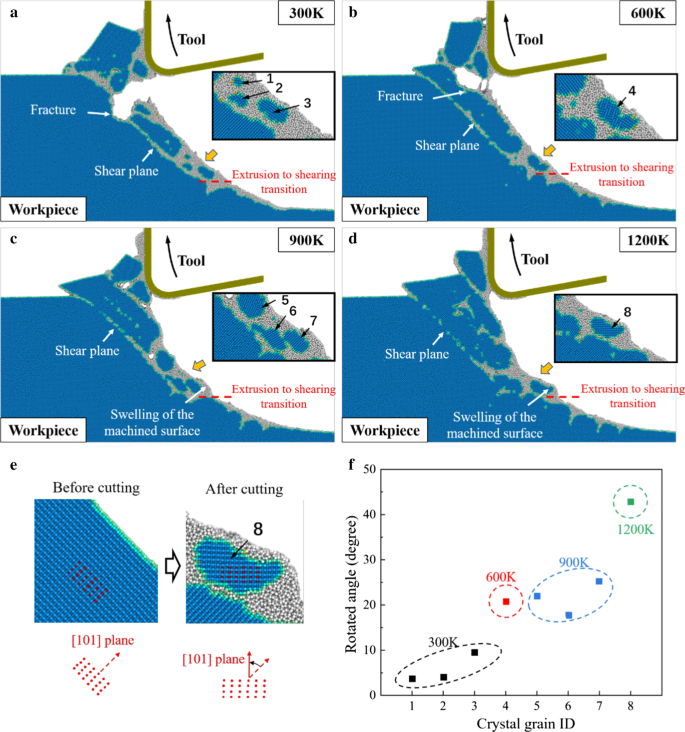
Werkstukmorfologie van het HM-proces bij a 300 K. b 600 K. c 900 K. d 1200 K. Blauwe atomen vertegenwoordigen de kubische diamantstructuur, terwijl de grijze atomen een niet-diamantstructuur hebben. e Bepaling van de rotatiehoek van kristalkorrels. v De rotatiehoek bij toenemende snijtemperatuur
Voor een duidelijke beschrijving van deze rotatie worden de coördinaten van 24 gemarkeerde atomen (rode atomen) in de kristalkorrels gebruikt om de gemiddelde rotatiehoek te berekenen, zoals geïllustreerd in figuur 4e. De rotatiehoek van 8 kristalkorrels (genummerd in Fig. 4a-d) is samengevat in Fig. 4f. Opgemerkt kan worden dat de rotatiehoek duidelijk groter wordt bij verhoogde temperatuur. Tijdens het HM-proces kan de viscositeit van a-Si sterk worden verlaagd bij hoge temperatuur en wordt de optrekkende beweging van werkstukatomen bevorderd door de opwaartse beweging van het gereedschap. Daarom wordt de atomaire stroom in het werkstuk verbeterd en kan de rotatie van de kristalkorrels worden vergemakkelijkt, wat leidt tot zwelling van het bewerkte oppervlak. Om de rotatie van kristalkorrels te beperken, moet het verwarmingsvermogen worden gecontroleerd om oververhitting van het werkstuk te voorkomen. Bovendien moeten de trillingsparameters zorgvuldig worden gekozen, bijvoorbeeld een kleinere nominale snijsnelheid en een hogere trillingsfrequentie moeten worden toegepast om de vorming van kristalkorrels te onderdrukken en de zwelling door verdere trillingscycli te verwijderen. Zoals geïllustreerd in Afb. 5, met de juiste trillingsparameters, P 1 kan zich in de extrusiefase bevinden en het uiteindelijke bewerkte oppervlak wordt gegenereerd door extrusie zonder te zwellen.
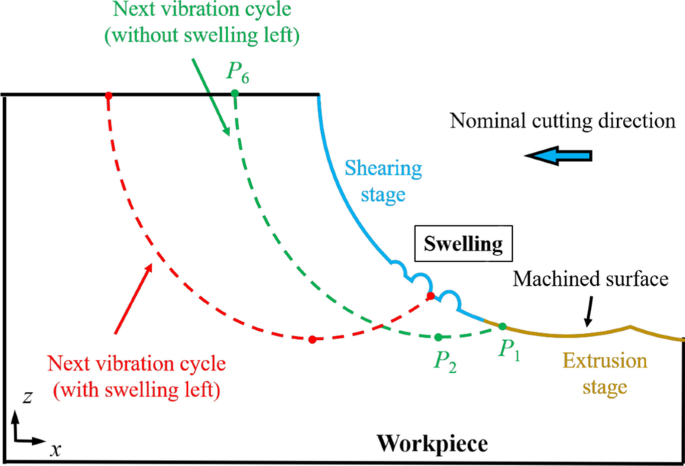
Eliminatie van zwelling in HM-proces
Stressveld in werkstuk
Om het snijmechanisme tijdens het HM-proces verder te onderzoeken, werd de spanningsverdeling in het werkstuk berekend. In MD-simulatie kan de hydrostatische spanning worden uitgedrukt als:
$$\sigma_{{{\text{hydrostatic}}}} =\, (\sigma_{x} + \sigma_{y} + \sigma_{z} )/3$$ (11)waar σ x , σ j , en σ z , zijn spanningstensoren van LAMMPS-uitvoergegevens.
De hydrostatische spanningsverdeling tijdens extrusie- en afschuiffasen wordt getoond in Fig. 6. En de piekwaarden van de spanningen in de druk- en trekgebieden werden gemarkeerd. Met de gereedschapsbeweging varieert het contactpunt tussen gereedschap en werkstuk langs de gereedschapskantcyclus, wat resulteert in de beweging van het drukgebied van de gereedschapskant naar het spaanvlak. Volgens eerdere rapporten zou de HPPT van monokristallijne siliciumfase (Si-I) naar Si-II kunnen optreden bij drukken vanaf 10-12 GPa [57, 58]. In de snijsimulatie bij 300 K bereikte de maximale drukspanning in de extrusie- en afschuiffase respectievelijk 18,1 GPa en 17,6 GPa. Dit resultaat geeft aan dat de ductiele Si-II-fase kan worden gegenereerd tijdens het snijden en dat de HPPT nog steeds bestaat in de afschuiffase. Bovendien concentreert de trekspanning zich in de extrusiefase voornamelijk in de buurt van het contactgebied tussen het flankvlak van het gereedschap en het bewerkte oppervlak als gevolg van de hechting van siliciumatomen en het oppervlak van het gereedschap. Naarmate het gereedschap verder gaat in de afschuiffase, wordt het trekgebied vergroot en neemt de trekspanningsconcentratie in het ondergrondse werkstuk aanzienlijk toe, wat wordt veroorzaakt door de optrekkende beweging. Wanneer de snijtemperatuur wordt verhoogd, wordt de plastische vervormbaarheid van monokristallijn silicium verbeterd en wordt de interne spanning in het werkstuk verminderd. Naarmate de temperatuur stijgt van 300 tot 1200 K, nam de maximale drukspanning af met 16,6% en 25% in de extrusie- en afschuiffase. Ondertussen, hoewel de trekspanningsconcentratie in het ondergrondse werkstuk nog steeds duidelijk is, is de piekwaarde van de trekspanning blijkbaar met meer dan 30% verminderd. Er is gemeld dat de breuktaaiheid van monokristallijn silicium effectief kan worden verhoogd bij hogere temperaturen [59]. Daarom kunnen scheuren en breuken veroorzaakt door het afgescheurde effect als gevolg van opwaartse beweging van het gereedschap effectief worden onderdrukt.
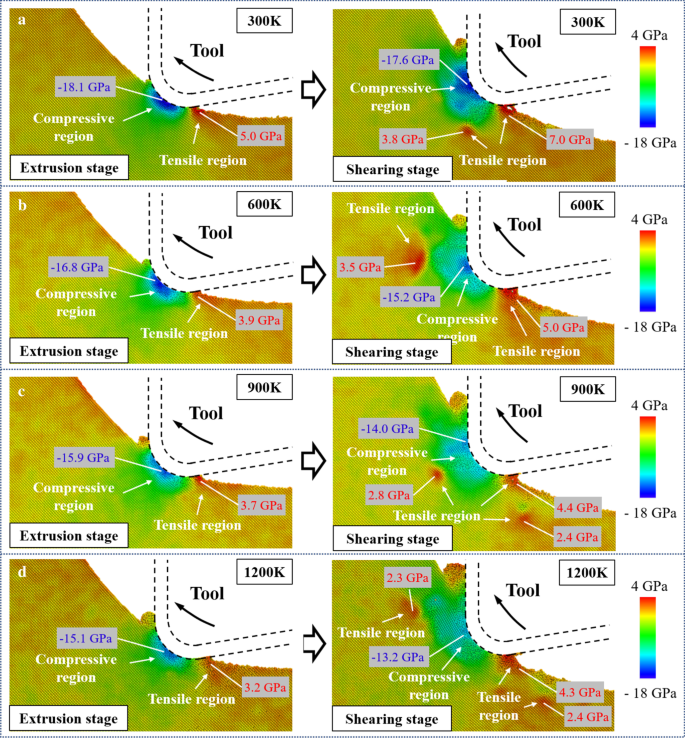
De hydrostatische spanningsverdeling bij:a 300 K. b 600 K. c 900 K. d 1200 K
Monokristallijn silicium heeft een Face Center Cubic (FCC) kristalstructuur met 12 slipsystemen. Op basis van de gereedschapsbeweging zijn de belangrijkste slipsystemen voor afschuifvervorming de (111)/[\(\stackrel{\mathrm{-}}{1}\)01] en (1\(\stackrel{\mathrm{-) }}{1}\)1)/[\(\stackrel{\mathrm{-}}{1}\)01] systemen. Daarom is de opgeloste schuifspanningscomponent τ s in het (111)/[\(\stackrel{\mathrm{-}}{1}\)01] slipsysteem wordt berekend. Zoals geïllustreerd in Fig. 7, is de opgeloste schuifspanningscomponent τ s in de richting M van het glijvlak N kan worden berekend door middel van stress tensoren door:
$$\tau_{{\text{s}}} =a_{1} a_{2} \sigma_{x} + b_{1} b_{2} \sigma_{y} + c_{1} c_{2} \sigma_{z} + \left( {a_{1} b_{2} + a_{2} b_{1} } \right)\tau_{xy} + \left( {a_{1} c_{2} + a_{2} c_{1} } \right)\tau_{xz} + \left( {b_{1} c_{2} + b_{2} c_{1} } \right)\tau_{yz}$$ (12)waar a 1 , b 1 , c 1 zijn de richtingscosinus van de normaalrichting van het vlak N terwijl a 2 , b 2 , c 2 zijn de richtingscosinus van de sliprichting M . Terwijl τ xy , τ xz , en τ yz zijn de schuifspanningstensoren van LAMMPS-uitvoergegevens.
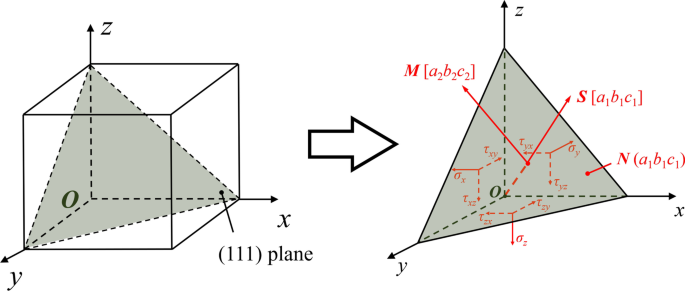
Illustratie van de stress tensoren
De verdeling van de opgeloste schuifspanning τ s wordt getoond in Fig. 8. Het gebied met positieve τ s wordt gedefinieerd als het afschuifgebied omdat de slipbeweging langs de [\(\stackrel{\mathrm{-}}{1}\)01]-richting wordt bevorderd, wat de materiaalverwijdering door middel van afschuiving vergemakkelijkt. Terwijl de regio met negatief τ s wordt beschouwd als het schadegebied omdat de slipbeweging de voorkeur heeft in de tegenovergestelde richting, wat leidt tot de vorming van ondergrondse schade in het werkstuk. In de extrusiefase is de spanning in het afschuifgebied kleiner dan die in het schadegebied. Onder het bewerkte oppervlak kan schade aan de ondergrond worden veroorzaakt door afschuifvervorming [60]. Als de beweging van het snijgereedschap, wordt de schuifspanning langs de [\(\stackrel{\mathrm{-}}{1}\)01] richting geleidelijk verhoogd, waardoor de materiaalverwijdering overgaat van extrusie naar afschuiving. Bovendien, aangezien de positie van het schadegebied omhoog beweegt langs de gereedschapsbeweging, kan de gegenereerde schade worden verwijderd door een verdere vibratiecyclus en zal deze niet in het werkstuk achterblijven. Wanneer de temperatuur wordt verhoogd van 300 K tot 1200 K, nam de schuifspanning in het schadegebied af met respectievelijk 36,1% en 42,4% in de extrusie- en afschuiffase. Daarentegen is door de opwaartse beweging van het gereedschap de afname van de schuifspanning langs de [\(\stackrel{\mathrm{-}}{1}\)01] richting in de afschuiffase veel minder duidelijk. De kritische opgeloste schuifspanning (CRSS) voor slipbeweging kan worden uitgedrukt als [61]:
$$\tau_{{\text{c}}} \left( T \right) =C\varepsilon^{1/n} \exp \left( \frac{U}{nkT} \right)$$ (13 )waar U en ε vertegenwoordigen de activeringsenergie van de glijbeweging en de reksnelheid. Parameters n en C zijn materiële constanten. Er kan worden geconcludeerd dat de CRSS duidelijk kan worden verlaagd met toenemende temperatuur. Daarom kan de afschuifvervorming in de [\({\overline{\text{1}}}\)01] richting worden vergemakkelijkt bij verhoogde temperatuur.
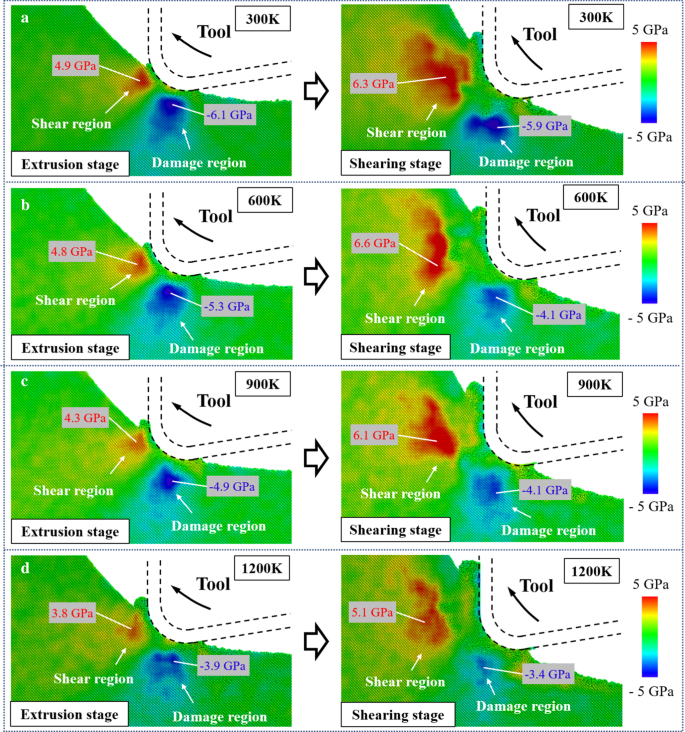
De opgeloste schuifspanningsverdeling bij:a 300 K. b 600 K. c 900 K. d 1200 K
Faseovergang
Wanneer de snijtemperatuur wordt verhoogd, kan de faseovergang van silicium sterk worden beïnvloed. De relaxatie van het a-Si en de overgang naar Si-I kan worden bevorderd bij een geschikte temperatuur [62]. In Fig. 4 wordt het schadepatroon in de werkstukken smaller bij hoge temperatuur. Een gedetailleerde observatie van het schadepatroon bij het snijden bij 1200 K is te zien in Fig. 9a. Er wordt waargenomen dat de gegenereerde schade in het vervormingsgebied gedeeltelijk wordt hersteld na het snijden, wat aangeeft dat de overgang van de niet-diamantstructuur naar Si-I heeft plaatsgevonden. En er worden meer Si-I-atomen gegenereerd wanneer de snijtemperatuur stijgt, zoals weergegeven in figuur 9b. Verder is het geconstrueerde oppervlaktegaas (rode kleur) [63] van het machinaal bewerkte werkstuk bij 1200 K aanwezig in Fig. 9c. Opgemerkt wordt dat er enkele vacatures worden gevormd in het ondergrondse werkstuk. Omdat de atomen in de Si-I-fase dichter op elkaar zijn gepakt, zou de overgang naar Si-I een krimp van het materiaal kunnen veroorzaken, wat vacatures in het werkstuk veroorzaakt. Het volume van de vacatures bij verschillende temperaturen wordt berekend en weergegeven in figuur 9d. Opgemerkt wordt dat bij kamertemperatuur bijna geen vacatures worden gegenereerd. Hoewel een duidelijke toename van de vacatures kan worden gedetecteerd wanneer de snijtemperatuur wordt verhoogd tot 900 K en 1200 K.
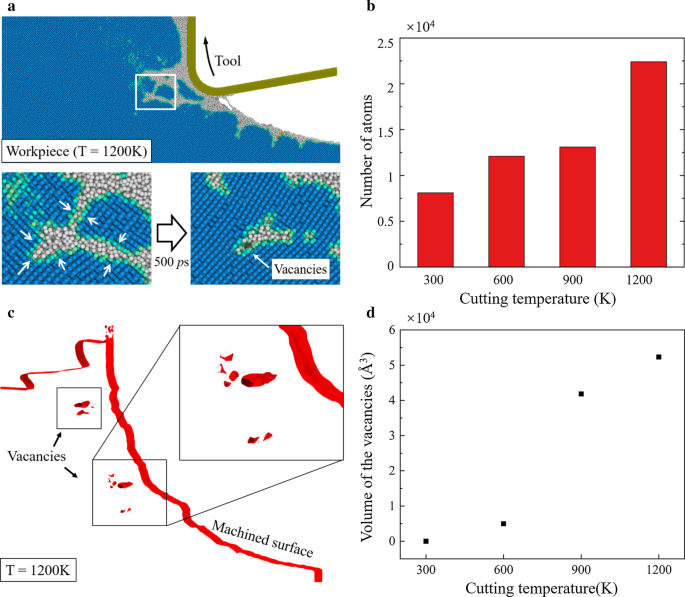
Ontspanningsproces en vacatures in werkstuk. een Momentopname van het schadepatroon van het werkstuk bij 1200 K. b Aantal atomen getransformeerd van de niet-diamantstructuur in Si-I-fase. c Geconstrueerd oppervlaktegaas van het werkstuk bij 1200 K. d Het volume van de vacatures bij verschillende temperaturen
Verdere analyse van de vacatures is te zien in figuur 10. Een materieel element onder het machinaal bewerkte oppervlak wordt gekozen om het genereren van vacatures te volgen. Het aantal atomen in de niet-diamantstructuur en de spanningsevolutie van het materiële element zijn aanwezig. Er wordt geconcludeerd dat tijdens het snijproces het materiaalelement eerst wordt samengedrukt en vervolgens trekspanning ondervindt als gevolg van de opwaartse beweging van het gereedschap. Ondertussen kunnen twee pieken van de schuifspanning worden waargenomen bij 300 K, aangezien de schuifspanning in het schadegebied toeneemt naarmate het snijgereedschap passeert. Wanneer de snijtemperatuur wordt verhoogd, is de afname van de schuifspanning duidelijker dan trekspanning. Bij 1200 K is de tweede piek van de schuifspanning bijna verdwenen, terwijl trekspanning dominant wordt in het materiële element tijdens het relaxatieproces.
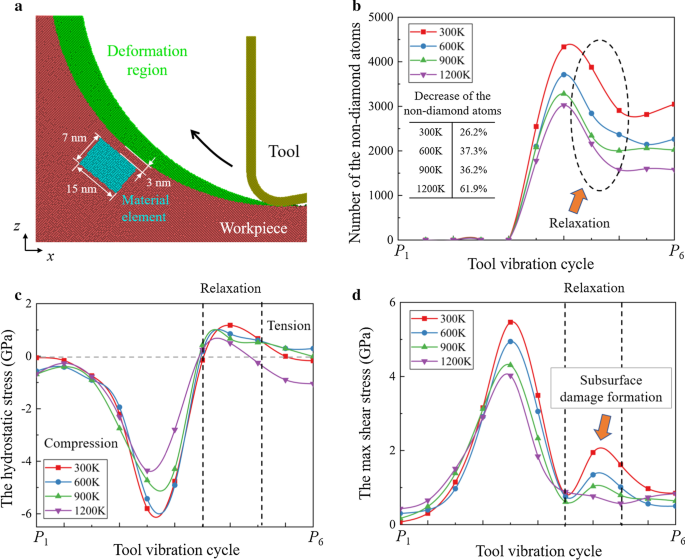
Ontspanning tijdens het HM-proces. een Illustratie van het materiële element. b Statistieken van de atomen in niet-diamantstructuur in het materiële element. c , d Stress evolutie van het materiële element
Om het effect van trekspanning op het vormingsproces van de vacatures te onderzoeken, werden relaxatiesimulaties van bulksiliciummonsters uitgevoerd. Zoals weergegeven in figuur 11a, bestaat het initiële model uit 40% Si-I-atomen en 60% a-Si-atomen, die wordt gegenereerd door de smelt-quench-methode [64]. De grootte van het model is 21,7 nm × 8,1 nm × 26,1 nm in x , j , en z direction, which contains 230,400 atoms. The initial interface between crystal and non-crystal region is set as (001) crystal plane. Periodic boundary condition is applied in three dimensions to mimic bulk materials. The constructed surface mesh of the relaxed model is present in Fig. 11b. Furthermore, to quantify the vacancies, the solid volume fraction is calculated as the ratio of the solid material volume and the total volume of the simulation sample, as shown in Fig. 11c. It is observed that when temperature is increased, the solid volume fraction decreased obviously under tensile stress. Therefore, to suppress the vacancies, the desired cutting temperature in HM process should be lower than that in ordinary TAC. Meanwhile, the vibration parameters should be optimized to reduce the tensile stress in subsurface workpiece.
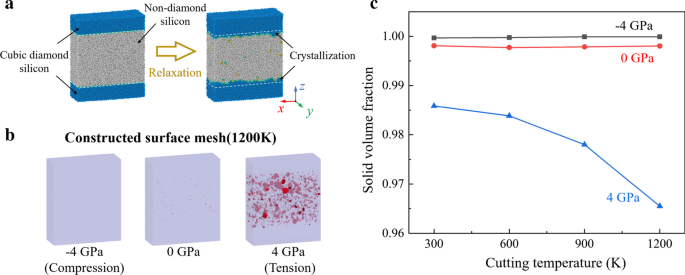
Relaxation simulation of silicon. een Scheme of MD relaxation simulation. b The surface mesh of the relaxed model at 1200 K. c The solid volume fraction curves
Conclusies
In this paper, MD simulation is carried out to investigate the cutting mechanism of hybrid machining (HM) process. A modified cutting model is applied to reveal the material removal behavior and subsurface damage formation in one vibration cycle. The main conclusions were as follows:
- (1)
During HM process, the dominant material removal mechanism could transform from extrusion to shear in a single vibration cycle. With an increase of the cutting temperature, the generation and propagation of cracks can be effectively suppressed. However, the swelling appears when the dominant material removal mechanism becomes shearing, which is caused by the rotation of the crystal grains in workpiece.
- (2)
Based on the stress analysis, the dominant formation mechanism of the subsurface damage in one vibration cycle can be distinct. In the extrusion stage, the subsurface damage can be generated by the shear stress in the damage region. While in the shearing stage, tensile stress becomes dominant in subsurface damage formation. When the cutting temperature is increased, although the tensile stress concentration in the subsurface workpiece is still obvious, the peak value of the stresses is apparently decreased, which effectively suppress the cracks and fractures in workpiece.
- (3)
When the cutting temperature is increased, less subsurface damage is generated in the workpiece. However, due to the tensile stress, some vacancies can be generated in the workpiece when the cutting temperature is increased. Therefore, the desired cutting temperature during HM process should be lower than that in ordinary TAC and the vibration parameters should be set carefully to suppress the vacancies in the subsurface workpiece.
Beschikbaarheid van gegevens en materialen
The datasets used and analyzed in the current study can be obtained from the corresponding authors upon reasonable request.
Afkortingen
- TAC:
-
Thermal assisted cutting
- VAC:
-
Vibration assisted cutting
- LVC:
-
Linear vibration cutting
- EVC:
-
Elliptical vibration cutting
- DOC:
-
Depth of cut
- HM:
-
Hybrid machining
- FEM:
-
Finite element method
- MD:
-
Moleculaire dynamiek
- LAMMPS:
-
Large-scale Atomic/Molecular Massively Parallel Simulator
- MEAM:
-
Modified embedded-atom method
- SW:
-
Stillinger–Weber
- COMB:
-
Charge optimized many-body
- ABOP:
-
Analytical bond-order potential
- Si-II:
-
Metallic stable phase
- HPPT:
-
High-pressure phase transition
- CNA:
-
Gemeenschappelijke buuranalyse
- a-Si:
-
Amorphous phase
- Si-I:
-
Single-crystal silicon phase
- FCC:
-
Face Center Cubic
- CRSS:
-
Critical resolved shear stress
Nanomaterialen
- Wat is het fabricageproces van snijgereedschappen?
- Typen en classificatie van bewerkingsprocessen | Productiewetenschap
- Wat zijn de belangrijkste stappen in het bewerkingsproces?
- Het belang van smering bij het bewerken van mechanische onderdelen
- De precisie en het proces van lasersnijtechnologie begrijpen
- Aanvoersnelheid versus snijsnelheid:begrijp het verschil
- Het verschil tussen conventioneel en niet-conventioneel bewerkingsproces
- Het draaiproces bij CNC-bewerking begrijpen
- Een overzicht van het kunststofbewerkingsproces
- Voorbereiding op de prototypes voor het productieproductieproces
- Voordelen van het lasersnijproces