Een beknopte handleiding voor totaal preventief onderhoud
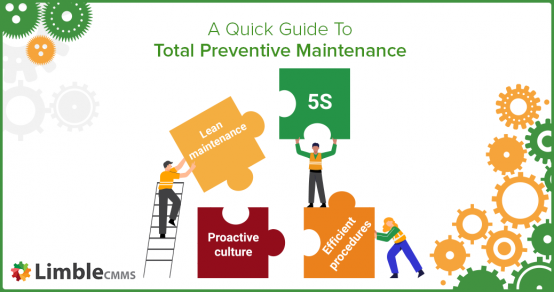
In een echt efficiënte organisatie kan de zorg voor activa niet de enige verantwoordelijkheid zijn van het onderhoudsteam. Totaal preventief onderhoud onderkent dat en biedt een kader om de onderhoudsverantwoordelijkheden over de hele productievloer uit te breiden.
Een toenemend aantal fabrikanten probeert TPM te implementeren in een poging de bedrijfskosten te verlagen, uitvaltijd te verminderen en OEE te verbeteren. Laten we eens kijken waarom.
De essentie van totaal preventief onderhoud (TPM)
Totaal preventief onderhoud staat voor een georganiseerde, gestandaardiseerde en gestructureerde aanpak van preventief onderhoud. Het unieke van TPM is dat het machineoperators in staat stelt om elementaire onderhoudsverantwoordelijkheden op zich te nemen. Het idee is dat mensen die de apparatuur bedienen kunnen worden bijgeschoold om routineonderhoudstaken uit te voeren op "hun" machines.
Totaal preventief onderhoud wordt gebruikt als synoniem voor totaal productief onderhoud. Ze delen hetzelfde acroniem - TPM.
TPM is eind jaren vijftig ontwikkeld door Seiichi Nakajima. Het schetst een robuust raamwerk dat wordt weergegeven door de 5S-basis en acht pijlers die u in de onderstaande afbeelding kunt zien.
Elke implementatie van totaal productief onderhoud is gedoemd te mislukken als het niet is gebouwd op een sterke basis, wat wordt bereikt door de 5S-methodologie toe te passen.
Het 5S-systeem schetst best practices die werknemers moeten volgen om verspillende acties te elimineren, gemeenschappelijke procedures te standaardiseren en ervoor te zorgen dat de werkomgeving altijd schoon en georganiseerd is.
Als dat er is, kan de organisatie beginnen met het implementeren van de pijlers. Elke pijler is gericht op het optimaliseren van een specifiek onderdeel van de onderhoudsoperatie of kwaliteitsmanagement. Dit leidt tot het creëren van een bedrijfsbrede proactieve onderhoudscultuur en de ontwikkeling van efficiënte preventieve onderhoudsprocedures .
Stoppen bij autonoom onderhoud
Het uiteindelijke doel van de implementatie van TPM is om een organisatie zo dicht mogelijk bij een perfecte productie te brengen:nul defecten, nul storingen, nul ongevallen en nul afval. Het bereiken van dat niveau kan jaren van voortdurende verbetering vergen.
Veel organisaties zijn niet klaar voor een dergelijk engagement. Ze kunnen echter nog steeds profiteren van het kernidee van TPM:operators betrekken bij het onderhoud van apparatuur. Dat wordt gedaan door de eerste pijler van totaal productief onderhoud te implementeren, genaamd autonoom onderhoud .
Bij autonoom onderhoud nemen machinebedieners de verantwoordelijkheid voor basisonderhoudstaken zoals visuele inspecties, veiligheidscontroles, reiniging en smering. Dit maakt onderhoudstechnici vrij om zich te concentreren op complexere onderhoudstaken.
Raadpleeg onze gids over autonoom onderhoud voor meer informatie over de implementatie ervan.
Voor- en nadelen van het gebruik van TPM
Succesvolle implementatie van totaal preventief onderhoud:
- vermindert het aantal uitval van apparatuur en productievertragingen
- vermindert het aantal defecte producten en verbetert de algehele effectiviteit van de apparatuur
- standaardiseert het werk volgens de best practices uit de branche
- leidt tot slanke productieprocessen en onderhoudsactiviteiten met minimale verspilling; slanke productie
- verlaagt de operationele en onderhoudskosten
- vergemakkelijkt het delen van kennis en best practices door de hele organisatie
Operatorfouten zijn de hoofdoorzaak van veel apparatuurstoringen. Door machinebedieners verantwoordelijk te maken voor de bedrijfsmiddelen waarmee ze werken, wordt het aantal storingen veroorzaakt door verkeerd gebruik van apparatuur aanzienlijk verminderd.
Natuurlijk is het niet allemaal zonneschijn en regenbogen. De bovengenoemde voordelen kunnen niet worden bereikt zonder het overwinnen van bepaalde uitdagingen:
- willekeurige implementatie van TPM-programma's kan leiden tot grote operationele verstoringen en kan veel interne middelen verspillen voor onbeduidende winst
- de organisatie heeft een goed doordacht plan nodig met duidelijke mijlpalen en verantwoordelijkheden
- Iedereen meekrijgen met het idee kan veel verandermanagement vergen
- een investering vooraf voor training van werknemers, onderhoudssoftware en consultants kan nodig zijn
De reikwijdte van de totale training voor preventief onderhoud
Er moet een sterk totaalprogramma voor preventief onderhoud worden ontworpen om medewerkers de organisatorische veranderingen te laten bijbenen.
Wanneer de processen zijn uitgewerkt, moet het bedrijf standaard operationele procedures maken/bijwerken en deze toevoegen aan een bedienings- en onderhoudshandleiding (als ze die gebruiken).
Vanwege de aard van het TPM-proces zal de meeste training gericht zijn op machinebedieners en onderhoudspersoneel. Training kan worden uitgevoerd door een combinatie van klassikale training en on-the-job (OJT) training. Dit zorgt voor een mooie balans tussen theoretische en praktische kennis.
Enige training kan ook vereist zijn voor managers die verantwoordelijk zijn voor het proces. Gelukkig kun je met een simpele Google-zoekopdracht genoeg online TPM-cursussen vinden. Afhankelijk van de cursus maak je kennis met basis- en geavanceerde concepten die nodig zijn om een lean onderhouds- en productieomgeving in te richten. En een soort TPM-certificering halen.
Tot slot kunnen bedrijven voor hulp terecht bij TPM-consultants. Zij zullen u door het hele proces begeleiden door seminars te organiseren, werknemers op te leiden en samen met uw interne team verspilling te elimineren en de onderhoudsprogramma's en -procedures te verbeteren.
Vertrouwen op software voor preventief onderhoud
CMMS-software is de beste manier om elk type preventief onderhoudswerk te beheren. Voor een meer holistische benadering kunnen moderne CMMS-oplossingen ook worden geïntegreerd met een bestaand ERP-systeem.
Er zijn zoveel manieren waarop CMMS kan worden gebruikt om onderhoudsactiviteiten te optimaliseren. In de context van totaal preventief onderhoud:
- wordt gebruikt voor het plannen, volgen en organiseren van alle onderhoudsbronnen (werk, arbeid, gereedschap)
- biedt directe toegang tot procedures, checklists, veiligheidsrichtlijnen en andere belangrijke documenten
- houdt een gedetailleerd overzicht van de onderhoudsgeschiedenis van alle fysieke activa, die nodig is om slimme onderhoudsbeslissingen te nemen
- helpt u bij het volgen en voorspellen van MRO-voorraad die nodig is om een evenwichtige voorraad te behouden
- helpt u op de hoogte te blijven van uw onderhoudsuitgaven
- kan worden geïntegreerd met conditiebewakingssensoren en voorspellende analyses voor het uitvoeren van CBM of voorspellend onderhoud
Als u geïnteresseerd bent in het testen van Limble CMMS, heeft u drie opties:
- START EEN GRATIS 30-DAAGSE PROEF
- VRAAG EEN DEMO AAN
- PROBEER ONZE ZELFDEMO (leidt u naar een testomgeving waar u kunt spelen met de functies van Limble)
Staan achter continue verbetering
Organisaties die niet willen veranderen worden weggegooid door de marktwerking. TPM is niet voor elke organisatie de juiste oplossing, maar veel van de lean principes die het predikt zijn dat wel.
Op het absolute minimum moeten we allemaal streven naar continue verbetering. Of het nu iets groters is, zoals het implementeren van een digitale onderhoudsoplossing, of iets kleins, zoals het updaten van bestaande standaard operationele procedures - het maakt niet echt uit - zolang we maar vooruitgaan.
De eenvoudigste manier om onderhoudsactiviteiten te verbeteren, is door moderne CMMS-software te implementeren. Als u geïnteresseerd bent in hoe Limble CMMS de digitale transformatie van uw onderhoudsafdeling een vliegende start kan geven, kunt u altijd contact met ons opnemen.
Onderhoud en reparatie van apparatuur
- Verschil tussen preventief versus voorspellend onderhoud
- Een gids voor het implementeren van totaal productief onderhoud
- Gids voor productie-KPI's
- Preventief onderhoudsprogramma:een gids in acht stappen voor het opstellen van een PM-plan
- Preventief onderhoud versus voorspellend onderhoud:terug naar de basis
- Preventief onderhoud:een overzicht
- Preventief onderhoud
- Onderhoud:resultaten op lange of korte termijn?
- Conditiegebaseerd onderhoud:een complete gids
- Typen onderhoud:een vergelijking
- Wat is preventief onderhoud?