Foutdetectie en diagnose bij het onderhoud van apparatuur
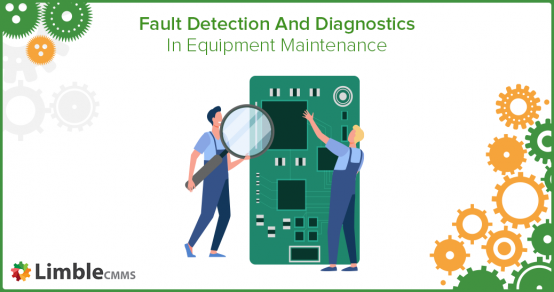
Het begrijpen van apparatuurstoringen en het ontwikkelen van strategieën om deze te detecteren en te diagnosticeren, is een van de belangrijkste elementen van apparatuuronderhoud.
Het doel van dit artikel is om een overzicht te geven van foutdetectie en diagnose zoals deze worden toegepast om het onderhoudsproces van apparatuur te verbeteren en de betrouwbaarheid van activa te vergroten.
Het verhaal achter foutdetectie en diagnose
In het begin was het onderhoud van apparatuur beperkt tot het repareren van defecte activa en het uitvoeren van basis routineonderhoud op basis van vaste tijdsintervallen. Onderhoudsprofessionals hadden niet proactiever kunnen zijn, zelfs als ze dat zouden willen. Hun vermogen om gegevens over de gezondheid en prestaties van apparatuur te verzamelen, op te slaan en te analyseren, was simpelweg te beperkt.
Door consistente verbeteringen in op microprocessors gebaseerde besturingen, automatisering, realtime data-acquisitie en systemen zoals Fault Detection and Diagnostics (FDD), is de manier waarop we apparatuuronderhoud uitvoeren echter aanzienlijk veranderd.
FDD in apparatuuronderhoud
Het doel van Fault Detection and Diagnostics in de context van apparatuuronderhoud is het optimaliseren van de onderhoudskosten en tegelijkertijd het verbeteren van de betrouwbaarheid, beschikbaarheid, onderhoudbaarheid en veiligheid (RAMS) van de apparatuur.
De FDD functioneert door het continu monitoren en analyseren van conditiebewakingsgegevens en het detecteren van eventuele afwijkingen (indien aanwezig). De datasets over de toestand van de apparatuur worden vervolgens verwerkt door foutdiagnose-algoritmen, soms ingebouwd in de apparatuur zelf, om storingswaarschuwingen voor de operators van de apparatuur te produceren en tijdige onderhoudsinterventie mogelijk te maken.
In sommige gevallen zijn de algoritmen geavanceerd genoeg om zelfs acties voor het inperken van storingen te initiëren om de storing zelf automatisch te corrigeren en de apparatuur in zijn gezonde staat te herstellen.
Belangrijkste elementen van het foutdetectie- en diagnosesysteem
De FDD bevat, zoals de naam al aangeeft, de detectie en diagnose van apparatuurstoringen. De diagnose van de storing kan worden onderverdeeld in storingsisolatie en -identificatie.
De storingsevaluatie wordt vaak toegevoegd binnen de reikwijdte van FDD omdat het helpt om de ernst van de storing op de systeemprestaties te begrijpen - een belangrijk aspect van onderhoudsbeheer.
Niettemin moet het foutdetectie- en diagnosealgoritme voor alle apparatuur ten minste de vier belangrijkste processen bevatten die hieronder worden vermeld (deze kunnen ook een niet-lineair proces vormen, op voorwaarde dat sommige stappen tegelijkertijd plaatsvinden):
We moeten elk element in meer detail bespreken om echt te begrijpen hoe foutdetectie en diagnose werken.
1. Foutdetectie
Foutdetectie is het proces waarbij de aanwezigheid van een fout in apparatuur wordt ontdekt voordat deze zich manifesteert in de vorm van een storing. Het is de belangrijkste fase van FDD omdat alle stroomafwaartse processen afhankelijk zijn van de nauwkeurigheid ervan.
Als de apparatuur niet in staat is om de juiste storingsmodus te ontdekken (of als de detectie niet correct is en valse alarmen veroorzaakt), dan zal de isolatie, identificatie en evaluatie ook niet effectief zijn.
Er zijn twee hoofdbenaderingen voor foutdetectie:
- Modelgebaseerde foutdetectie: Het wordt uitgevoerd door middel van wiskundige modellering van signalen en processen.
- Op kennis gebaseerde foutdetectie: Het is een methode die gebruikmaakt van historische gegevens over de prestaties van apparatuur.
Modelgebaseerde foutdetectie
Bij modelgebaseerde detectie definiëren we een reeks technische regels die zijn geschreven in overeenstemming met fysieke wetten die de relaties van subsystemen en componenten binnen de apparatuur definiëren. Telkens wanneer de regel wordt overtreden, kan het algoritme de fout detecteren en een foutdiagnose uitvoeren.
Een voorbeeld van modelgebaseerde foutdetectie is het gebruik van tijddomeinreflectometrie (TDR) om fouten in ondergrondse kabels te detecteren. In TDR wordt het signaal over de testkabel verzonden en ontvangen nadat het is gereflecteerd vanaf het foutpunt.
Als de kabel een discontinuïteit of hoge impedantie heeft, wordt het deel van het signaal teruggekaatst naar de testapparatuur of ontvanger. Door de signaalterugkeertijd en de snelheid van het gereflecteerde signaal te analyseren, kan de testapparatuur de aard van fouten in de kabel detecteren als een open circuitfout of een kortsluitingsfout.
Een ander eenvoudig, op regels gebaseerd detectievoorbeeld komt van de serie-operatie van flessenvul-, dop- en verpakkingssysteem op een transportbandsysteem. Er kan een eenvoudige regel worden vastgesteld die de hiërarchie van processen aangeeft, zoals:
- de fles kan pas worden afgesloten als de flessen met vloeistof zijn gevuld
- de flessen kunnen alleen worden verpakt als ze zijn gevuld en afgedekt
In het geval van een storing in het mechanisme voor het afdekken van flessen, zal het algoritme de binnenkomende verstoring in het verpakkingssysteem detecteren. Het zal de verpakkingsoperator ruim van tevoren op de hoogte stellen. De nodige voorbereidingen kunnen getroffen worden om operationele verliezen aan de verpakkingszijde van de transportband tot een minimum te beperken.
Op kennis gebaseerde foutdetectie
Om op kennis gebaseerde foutdetectie te laten werken, moeten we eerst een basislijn vaststellen. Dit wordt gedaan door de parameters van apparatuurprestaties op te halen zoals spanning, stroom, trilling, temperatuur, druk en andere relevante procesvariabelen - terwijl de apparatuur onder normale omstandigheden werkt.
Het doel is om de apparatuurhandtekening onder normale operaties te ontwikkelen.
Daarna worden dezelfde parameters continu opgehaald en gecorreleerd met de "gezonde" handtekening om de afwijking vast te leggen via een statistische analyse-interface - patroonherkenning via machine learning of een kunstmatig neuraal netwerk.
We kunnen deze techniek gebruiken om motorlagerstoringen te voorspellen door middel van sensorische gegevens die zijn verzameld van het lager en de motor in het algemeen.
De grote hoeveelheid data die in de loop van de tijd is verzameld – procesgeschiedenis – kan worden geanalyseerd met behulp van een statistisch algoritme. Dit helpt ons de impact te begrijpen van de verschillende omstandigheden waaraan de motor wordt blootgesteld, zoals thermische classificatie, mechanische belasting of andere bedrijfsomstandigheden die zich in speciale omstandigheden voordoen.
Het algoritme correleert vervolgens de impact van deze omstandigheden op de verslechtering van de lagergezondheid en voorspelt het uitvalpercentage en de gezondheidstoestand van de algehele motor.
Op basis van deze gegevenshandtekeningen kan de analyse worden gemaakt om de toekomstige gezondheid van de apparatuur te voorspellen. Bovendien kunnen de nodige alarmen worden geactiveerd en foutdiagnose worden uitgevoerd, zodat de operator/technicus passende maatregelen kan nemen.
Dezelfde gegevens kunnen worden gebruikt om een voorspellende onderhoudsstrategie vast te stellen voor de resterende levensduur van de motor.
2. Foutisolatie
Het doel van het foutisolatieproces is om de fout te lokaliseren tot het laagste onderdeel dat kan worden vervangen. In sommige toepassingen gaan foutdetectie en isolatie hand in hand; het kunnen natuurlijk aparte modules van het proces zijn. Dit komt omdat de processen voor het detecteren en lokaliseren van de fout in principe op hetzelfde moment plaatsvinden, beide gedaan door het Fault Detection and Isolation (FDI) algoritme.
Denk bijvoorbeeld aan het voorbeeld van TDR-testen voor ondergrondse kabels. Het geretourneerde pulssignaal van de kabel geeft tegelijkertijd de aanwezigheid en de locatie van de fout aan door tijd en snelheid van het geretourneerde pulssignaal.
Een belangrijk aspect van foutisolatie is dat de fout moet worden gelokaliseerd op het laagste onderdeel dat kan worden vervangen . Dit wordt gedaan om de nauwkeurigheid van isolatie te verbeteren en de impact van downtime te verminderen.
In het geval van het eerder toegelichte voorbeeld van het flessentransportsysteem, moet de detectie de locatie van de storing kunnen lokaliseren, zoals de storing van de controlekaart in het flesafsluitmechanisme.
Als de detectie alleen wijst op een storing op hoog niveau in de transportband, is dat niet echt nuttig voor de technicus die de diagnose uitvoert - er zijn meerdere systemen op dezelfde transportband die mogelijk defect zouden kunnen raken.
De informatie die het reparatieproces echt zal versnellen, is de exacte locatie van de fout kennen.
3. Foutidentificatie
Het doel van foutidentificatie is om de onderliggende storingsmodus te begrijpen, de grootte van de fout te bepalen en de oorzaak ervan te vinden. Foutdiagnosemethoden kunnen verschillen, maar de te volgen stappen zijn over het algemeen hetzelfde.
De onderliggende faalmodus begrijpen
Een diepgaand begrip van de faalmodus vereist werk:
- we moeten analyseren hoe de fout zich op verschillende tijdstippen gedraagt
- zodat we de tijdvariante signatuur van de faalmodus kunnen ontwikkelen
- en classificeer het in verschillende categorieën
De grootte van de fout bepalen
Ongeacht de toegepaste foutdetectiemethode, speelt de grootte of omvang van de fout een belangrijke rol bij het bepalen van het gewenste niveau van fouttolerantie dat in het ontwerp van de apparatuur moet worden ingebouwd.
Als de foutomvang laag is, moet het systeem de fout alleen nog een extra tijd kunnen verdragen totdat de fout vanzelf is verholpen. Het perfecte voorbeeld is het toestaan van tijdelijke overstroom in elektrische apparaten, zolang dat geen significante invloed heeft op de prestaties van de apparatuur.
Als de foutomvang echt hoog is, is een andere methode vereist:technici moeten actieve of passieve redundanties gebruiken om de fouttolerantie op hun apparaten te verbeteren.
Oorzaken vinden
Het foutdetectie- en diagnosealgoritme vormt de kern van een goed foutdiagnosesysteem. Het is gebaseerd op machine learning-principes en kan worden gebruikt om anomalieën te identificeren in de gegevensstromen die afkomstig zijn van de apparatuur, en de oorzaak erachter te bepalen.
Het identificeren van sommige faalwijzen is heel eenvoudig, terwijl andere een uitdaging kunnen zijn en uitgebreide wiskundige berekeningen vereisen.
Laten we als voorbeeld een driefasige AC-inductiemotor met hoog voltage en hoog vermogen gebruiken.
Vaker wel dan niet, zijn de onderliggende faalwijzen mechanisch van aard en geassocieerd met het roterende deel van de motor:kortgesloten rotorwikkelingen, lagerdefecten en defecte rotor. Omdat de rotor een snel bewegend onderdeel is, kan er geen sensor rechtstreeks op worden geïnstalleerd.
De geavanceerde FDD-algoritmen kunnen worden gebruikt om gezonde motorstatorterminalstroomsignaturen te produceren en deze te vergelijken met huidige handtekeningen onder defecte omstandigheden.
Bij het breken van rotorstaven is de puls die wordt geproduceerd in de statorstroom bijvoorbeeld tweemaal de frequentie van de motorstatorstroom. Er is een indirecte correlatie tussen het mechanisch breken van rotorstaven en de fluctuaties in de statorstroom.
Dergelijke opkomende trends worden geanalyseerd door foutdetectie- en diagnostische algoritmen en kunnen worden gebruikt om mogelijke hoofdoorzaken te vinden die in realtime worden afgeleid en weergegeven in live dashboards.
Het gebruik van dergelijke foutidentificatie-algoritmen heeft de hoeveelheid tijd die technici nodig hebben om problemen met apparatuur op te lossen en de oorzaak van de storingen te achterhalen, aanzienlijk verminderd. Automatische diagnose van hoofdoorzaken heeft enorm bijgedragen aan het verminderen van de uitvaltijd van apparatuur, het verbeteren van de gemiddelde reparatietijd en het verbeteren van de algehele betrouwbaarheid van de installatie.
4. Foutevaluatie
Zodra de faalwijzen en de bijbehorende hoofdoorzaken zijn geïdentificeerd, is de volgende stap het evalueren van de impact van dat fouttype op de algehele prestaties van het systeem.
We moeten rekening houden met factoren zoals:
- de impact van de storing op de omgeving en de rest van het systeem
- de impact van de fout op de systeemveiligheid
- het financiële verlies als gevolg van downtime
- de noodzaak om beslissingen te nemen over kapitaalvervanging (in het geval dat de ernst van de storing voldoende is om de vervanging van apparatuur te rechtvaardigen in plaats van deze te repareren)
via GIPHY
Foutevaluatie is een belangrijk onderdeel van het algehele proces omdat het doel is om de ernst van de fout te begrijpen . Dit helpt betrouwbaarheidsingenieurs om validatie te bieden en het risico op storingen te berekenen, die beide een grote impact zullen hebben op onderhoudsvereisten, aanbevelingen en optimalisatie.
Het resultaat van de FDD voor één apparaat zou bijvoorbeeld de snel toenemende uitvalpercentages kunnen impliceren. De impact van die fout kan echter minimaal zijn op de algehele systeemprestaties, waardoor het algehele risico matig is. In dit geval kan de minder stringente onderhoudsstrategie, zoals run-to-failure of preventief onderhoud, voldoende zijn om het risico te beheersen.
Foutdetectie en diagnose voor een ander apparaat kunnen wijzen op het toenemende uitvalpercentage, samen met de grote impact van een storing op de algehele systeemprestaties. In dit geval moet ondanks de hoge kosten het strengste programma voor voorspellend onderhoud worden toegepast. Dit komt omdat de hogere onderhoudskosten gerechtvaardigd zijn om grote gevolgen te voorkomen die veel duurder zullen zijn.
Onderhoud optimaliseren met FDD
Kortom, foutdetectie en diagnose spelen een beslissende rol bij het optimaliseren van het onderhoudsregime voor elk apparaat, gedurende de hele levenscyclus.
Met de komst van snelle computertechnologieën, big data-verwerking en geavanceerde leeralgoritmen, is traditionele foutdetectie geëvolueerd naar automatische foutbeheersystemen die niet alleen fouten detecteren, maar ook de hoofdoorzaak identificeren en corrigerende maatregelen implementeren om herhaling in de toekomst te voorkomen.
Een dergelijke automatisering van een reeks handmatige processen heeft betrouwbaarheids- en onderhoudsingenieurs in staat gesteld voorspellingen toe te passen over de gezondheid van apparatuur, toekomstige apparatuurprestaties af te leiden en optimale onderhoudsintervallen vorm te geven.
Het enige dat ze nog hoeven te doen, is hun geautomatiseerde onderhoudsbeheersoftware (CMMS) opstarten, de toestand van hun kritieke bedrijfsmiddelen volgen en de juiste onderhoudswerkzaamheden plannen.
Onderhoud en reparatie van apparatuur
- De evolutie van industrieel onderhoud
- Laat risico en uw apparatuur uw onderhoudsstrategie bepalen
- Menselijke gezondheidszorg en onderhoud van apparatuur:eventuele verbindingen?
- Onderhoud en betrouwbaarheid beste prestaties
- Nieuw boek helpt productie en onderhoud te transformeren
- Details zijn belangrijk voor onderhoud en betrouwbaarheid
- 5 sleutels om de betrouwbaarheid van apparatuur te behouden
- 5 oorzaken van apparatuurstoringen (en wat u kunt doen om dit te voorkomen)
- 3 sleutels voor verhuur en onderhoud van industriële apparatuur
- Tips voor motoronderhoud om uw zwaar materieel en machines te beschermen
- Bescherm zwaar materieel met deze reinigings- en onderhoudstips voor de winter