Expert Interview:Lithoz's CEO Dr. Johannes Homa over de staat van keramisch 3D-printen
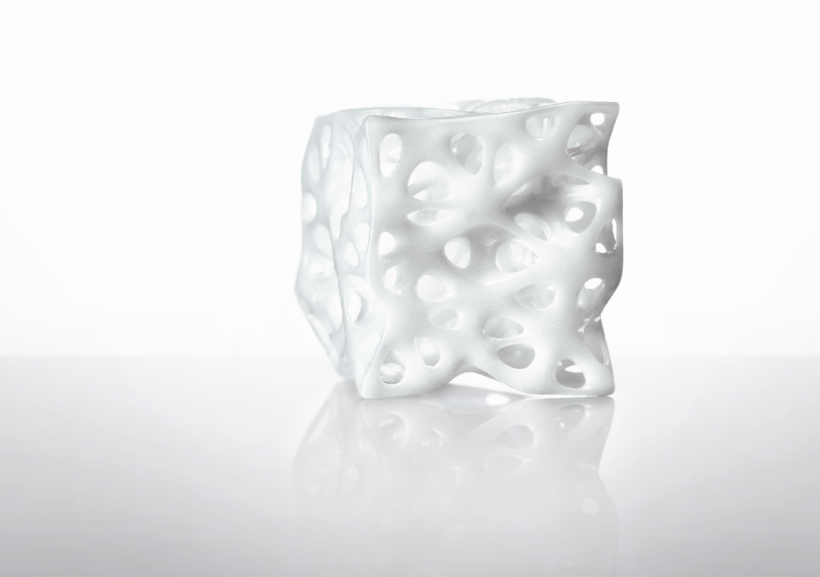
Keramiek 3D-printen is nog een relatief nieuwe technologie voor additieve fabricage. Ondanks zijn nieuwigheid vindt keramisch 3D-printen zijn weg naar veel industrieën, van medische en tandheelkundige tot lucht- en ruimtevaart en luxegoederen.
Momenteel ontwikkelt slechts een handvol bedrijven 3D-printtechnologie voor keramiek. Een van die bedrijven is de Oostenrijkse fabrikant Lithoz.
We spraken met de CEO en oprichter van Lithoz, dr. Johannes Homa, om de huidige staat van keramisch 3D-printen, enkele van de opwindende toepassingen en de voordelen van 3D-printen als digitale productietechnologie te bespreken.
/>
Kun je ons iets vertellen over Lithoz en je missie als bedrijf?
Lithoz is een technologieleverancier voor het 3D-printen van hoogwaardig keramiek, wat inhoudt dat we machines, software en materialen ontwikkelen en verkopen voor het 3D-printen van keramiek.
We zijn duidelijk de wereldmarkt- en technologieleider op dit gebied.
Naast technologieontwikkeling ondersteunen wij onze klanten ook op het gebied van applicatieontwikkeling.
Noch de AM-gemeenschap noch de keramische industrie was gewend aan keramiek 3D-printen. We steunen beide partijen zoveel we kunnen.
Hoe ben je ertoe gekomen om Lithoz op te richten?
De technologie is in 2006 ontwikkeld aan de Technische Universiteit van Wenen, in samenwerking met een tandheelkundig bedrijf Ivoclar Vivadent AG.
Toen bereikten we in 2010 een doorbraak:we waren in staat om keramiek in 3D te printen met dezelfde materiaaleigenschappen als in de conventionele vormtechnologie. Deze mijlpaal moedigde ons aan om Lithoz voort te zetten als een bedrijf voor 3D-printen van hoogwaardig keramiek.
Kun je iets meer vertellen over de technologie die Lithoz heeft ontwikkeld?
Onze technologie is gebaseerd op een fotopolymerisatieproces, dat sterk lijkt op conventionele stereolithografie. Het verschil is dat met onze technologie de keramische deeltjes worden gedispergeerd in een lichtgevoelige hars.
Tijdens het drukproces wordt dit composietmateriaal door licht laag voor laag gestold. Het deel dat uit onze 3D-printer komt, wordt een green body genoemd, wat betekent dat het nog geen afgewerkt product is.
Het groene lichaam moet een warmtebehandeling ondergaan waarbij een deel in een gespecialiseerde oven wordt gebakken. Technisch gezien ontbinden en sinteren we het onderdeel om de gewenste eigenschappen van een keramisch onderdeel te bereiken.
Tijdens het ontbinden verbrandt u het bindmiddel en sintert u het keramiek tot volledige dichtheid. Het onderdeel ondergaat krimp, maar dit is een normaal verschijnsel bij keramische vormprocessen.
Kunt u enkele voorbeelden delen van de toepassingen die met uw technologie zijn bereikt?
We zijn actief in drie verschillende branches. De eerste is medisch, waar we resorbeerbare en niet-resorbeerbare implantaten en medische hulpmiddelen hebben. Zo zijn er sinds 2017 resorbeerbare implantaten in gebruik. Niet-resorbeerbare implantaten zijn daarentegen bio-inert, wat inhoudt dat ze niet reageren met het menselijk lichaam.
Bovendien is de warmtegeleiding van keramiek vrij laag. Een ander voordeel van keramische implantaten in vergelijking met metalen implantaten is dat mensen geen pijn voelen wanneer ze in direct zonlicht staan of wanneer ze een warme douche nemen.
De derde medische toepassing zijn medische apparaten, waarbij je een aantal isolerende, niet-magnetische eigenschappen van het keramiek nodig hebt. Keramiek is ideaal voor de medische industrie omdat het bio-inert is en geen allergische reacties veroorzaakt, zoals bij metalen of kunststoffen wel het geval kan zijn.
Een ander gebied waar we ons op richten is het gieten van kernen voor turbinebladen. Turbinebladen hebben een intern koelsysteem om het blad tijdens bedrijf af te koelen. Met de groeiende trend om de efficiëntie te verhogen door de temperatuur te verhogen, zijn de ontwerpen van dergelijke koelsystemen geavanceerder geworden.
Het niveau van verfijning betekent dat de ontwerpen niet meer kunnen worden gespuitgiet, waardoor een nieuwe productieaanpak nodig is om ze te kunnen produceren. Additive manufacturing blijkt een ideale oplossing voor deze kernen.
Een ander aandachtsgebied voor ons is technisch keramiek. Dit zijn geavanceerde keramische materialen die in alles worden gebruikt, van satellietcomponenten, zoals spiegelhouders en radiofrequentiecomponenten, tot werktuigbouwkundige onderdelen, bijvoorbeeld voor textielmachines en halfgeleidermachines.
Dit betekent dat er een breed scala aan toepassingen is voor onze technologie, waaronder luxegoederen.
Kan deze technologie ook worden gebruikt met metalen?
Dat is een goede vraag.
Onze filosofie is dat we onze technologie aanpassen aan het poeder en niet andersom.
Het betekent dus dat we onze technologie konden aanpassen aan metalen. We waren zo succesvol dat we zelfs een spin-out van het bedrijf hebben gemaakt.
Nu is er een bedrijf genaamd Incus, en het doet 3D-metaalprinten met behulp van een fotopolymerisatiebenadering. Met deze technologie kan het hoge resoluties, goede mechanische eigenschappen en hoge precisie bereiken, waardoor onderdelen vergelijkbaar zijn met metalen spuitgietonderdelen.
Wat is de huidige staat van keramisch 3D-printen in termen van begrip van de technologie?
Keramisch 3D-printen is een van de jongste technologieën in 3D-printen, dus de kennisbasis is nog niet zo goed ontwikkeld.
Dat gezegd hebbende, ontving ik vandaag een e-mail van een klant die een ontmoeting had met hun C-level executive die verrast was dat het potentieel voor het 3D-printen van keramische onderdelen in hun bedrijf groter was dan voor metalen onderdelen .
We zien dat er veel toepassingen zijn, maar keramiek AM is nog niet zo bekend in de 3D-printindustrie.
Dit begint echter te veranderen. Mensen hebben gezien dat er beperkingen zijn met kunststoffen en metalen, die kunnen worden overwonnen door keramiek.
Hoe zou u een bedrijf adviseren dat de mogelijkheden van keramisch 3D-printen of 3D-printen onderzoekt? meer in het algemeen, maar weet niet waar te beginnen met het toepassen van de technologie?
Dit is een heel moeilijke vraag omdat de businesscase meestal niet zomaar op je bureau ligt. De eenvoudigste manier om aan de slag te gaan, is door 3D-printen voor prototypes te verkennen. Op deze manier kunt u beginnen met het leren van de technologie.
Vervolgens ga je met klanten praten en je portfolio bekijken om te bepalen welke onderdelen zinvol zijn voor 3D-printen. De grootste uitdaging is om een onderdeel te vinden dat geschikt is voor additieve productie. Vanuit een ontwerpperspectief zou dit onderdeel zeer geavanceerd moeten zijn en idealiter niet door andere technologieën kunnen worden geproduceerd.
Als je het eenmaal hebt gevonden, heb je een concurrentievoordeel. Kortom, het is niet alleen laaghangend fruit waarnaar u op zoek bent, maar het is een project dat u in uw bedrijf opzet. En het moet eerder van bovenaf komen en niet van onderaf.
Het kan in het begin moeilijk zijn om het volledige potentieel van AM te zien. Elk bedrijf dat 3D-printen toepast, moet enige moeite doen om dit potentieel uit te graven. Maar als u eenmaal een geschikt gebruiksscenario heeft gevonden, zal dit vele deuren voor u openen.
Wat zijn enkele van de uitdagingen bij het 3D-printen van keramiek?
Een probleem waarmee we vaak worden geconfronteerd, is dat mensen onderdelen willen 3D-printen, die al goed ingeburgerd zijn in conventionele vormtechnologieën. Als gevolg hiervan zijn ze verrast dat additive manufacturing doorgaans duurder is dan meer conventionele technologieën.
Wat moet worden begrepen, is dat het reproduceren van een traditioneel vervaardigd onderdeel met behulp van 3D-printen het in de meeste gevallen niet goedkoper zal maken.
Een andere uitdaging is dat we materiaalwetenschappelijke problemen niet kunnen oplossen met behulp van additive manufacturing. AM is slechts een vormtechnologie. Het lost geen problemen op voor sinteren, wat verplicht is voor keramische verwerking.
Het is bijvoorbeeld eenvoudig om keramische onderdelen van meerdere materialen in 3D te printen. Maar het zou dan een uitdaging zijn om deze materialen te co-sinteren. Ik denk dat dergelijke overwegingen soms worden onderschat.
Een recent rapport van SmarTech Analysis staten dat de groei van keramisch 3D-printen grotendeels zal worden aangedreven door de productie van eindonderdelen. Wat vind je daarvan?
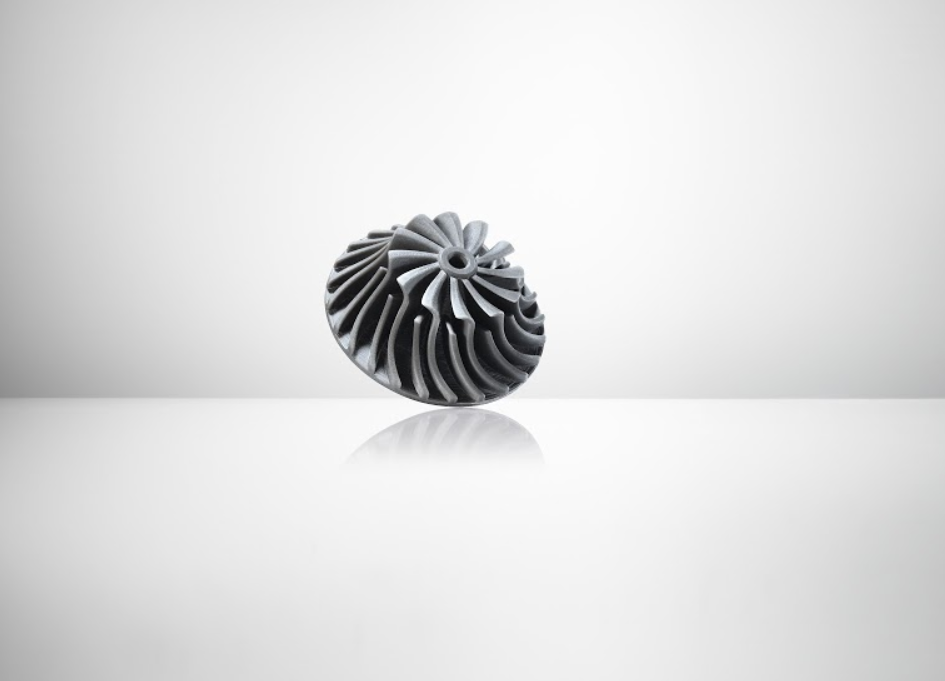
Ik ben het er helemaal mee eens. Toen we 10 jaar geleden begonnen, had niemand een idee van hoogwaardig keramisch 3D-printen. En nu zien we zoveel toepassingen waar zelfs wij niet van op de hoogte waren.
Ik ben ervan overtuigd dat keramiek de materialen van de toekomst zijn en we staan nog maar aan het begin van deze reis. In de afgelopen 10 jaar hebben we moeten laten zien en bewijzen dat 3D-printen ook mogelijk is met keramiek, en nu beginnen mensen te profiteren van deze technologie.
Wat ik ook denk dat mensen zijn Nu beginnen te beseffen is dat digitale technologie, zoals AM, een oplossing kan zijn voor lockdowns, dankzij digitale inventarisaties die mogelijk zijn met de technologie.
Kun je iets meer vertellen over hoe digitale technologieën en 3D-printen kan ondersteuning bieden aan bedrijven?
Tijdens de COVID-19-crisis is er een lockdown geweest van bepaalde leveranciers. Bij spuitgieten bijvoorbeeld heeft een leverancier het gereedschap in huis en als je een onderdeel opnieuw wilt produceren, ga je naar je leverancier en vraag hem om meer onderdelen voor je te vervaardigen en hij zal dat in een normale omgeving doen.
Maar de situatie met COVID-19 maakt de wereldwijde toeleveringsketen nu veel kwetsbaarder en verstoord. Veel bedrijven kunnen hun leveranciers niet bereiken of de leveranciers kunnen geen onderdelen produceren.
Aan de andere kant, bij additive manufacturing is het enige gereedschap dat u gebruikt de machine zelf. De machine kan hier in Europa zijn, of de Verenigde Staten, in Azië, in principe overal, en u hoeft alleen maar de gegevens naar de machine over te dragen en het onderdeel onmiddellijk af te drukken, zonder gereedschap.
Natuurlijk moet je het onderdeel kwalificeren voor AM, maar over het algemeen geeft de technologie je veel meer flexibiliteit.
Een ander punt is dat het digitale karakter van AM je in staat stelt om ontwerpbestanden in virtuele opslag op te slaan, in plaats van een fysieke inventaris, en ze on demand af te drukken.
Hoe ziet u de evolutie van het 3D-printen van keramiek in de komende jaren?
Ik denk dat er een groot potentieel in het verschiet ligt. Dat gezegd hebbende, moet keramische AM, in tegenstelling tot andere AM-technologieën, vanaf het begin voldoen aan de eisen van een hoogwaardig onderdeel.
Want als je een keramisch onderdeel nodig hebt, moet het dezelfde materiaaleigenschappen hebben als bij conventionele productie, ook al is het maar een prototype. Dat komt omdat je het zou gebruiken in een ruwe omgeving, zoals hoge temperaturen of een corrosieve omgeving.
Als je een visueel prototype wilt hebben, zou je het niet van keramiek maken, maar van plastic. Je wilt altijd functionele prototyping hebben met keramiek AM, dus vanaf het begin waren we bezig met de productie van partijgrootte één.
Wat brengt het komende jaar voor Lithoz?
We zien twee verschillende gevolgen van de pandemie voor ons bedrijf.
Ten eerste hebben we gezien dat een kleinere groep van onze klanten een pauze nam in additive manufacturing en zich op andere dingen concentreerde.
In een andere groep zien we meer bedrijven die nu op zoek zijn naar veel meer in additief, vanwege de voordelen van digitale productietechnologie, zoals digitale opslag en de mogelijkheid om hun toeleveringsketen te stabiliseren.
Hoewel de huidige situatie slecht is voor de wereldeconomie, zie ik dat bedrijven nu het potentieel van additive manufacturing beseffen, omdat mensen anders gaan denken en digitale productietechnologieën beschouwen als een middel om deze problemen op te lossen.
Voor Lithoz denken we niet dat deze crisis een grote impact zal hebben op onze omzet en omzet. De toekomst ziet er heel rooskleurig voor ons uit.
We hebben veel projecten lopen die we momenteel niet kunnen onthullen. Ze zullen in de toekomst verschijnen en mensen zullen zeer verrast zijn over wat er al mogelijk is met keramisch 3D-printen.
3d printen
- Interview met een expert:Dr. Bastian Rapp van NeptunLab
- Expertinterview:Felix Ewald, CEO van DyeMansion
- Interview met expert:Duncan McCallum, CEO van Digital Alloys over Joule Printing en de toekomst van Metal 3D Printing
- Expertinterview:Nanoe CEO Guillaume de Calan over de toekomst van keramisch 3D-printen
- Expert Interview:Ultimaker President John Kawola over de toekomst van 3D-printen
- Interview met expert:Simon Fried, medeoprichter van Nano Dimension over de opkomst van 3D-printen voor elektronica
- Interview met expert:CEO van PostProcess Technologies over het oplossen van het knelpunt in de nabewerking voor additieve productie
- Expert Interview:Jabil's Rush LaSelle over de toekomst van additieve productie
- Interview met expert:Nanci Hardwick, CEO van MELD Manufacturing, over het benutten van het potentieel van de productie van metaaladditieven
- Interview met experts:Andy Kalambi, CEO van RIZE, over het duurzaam en schaalbaar maken van industrieel 3D-printen
- Interview met expert:Carl Fruth, CEO van FIT AG over het bereiken van radicale innovatie met additieve productie