Evoluerende AFP voor de volgende generatie
Als geautomatiseerde vezelplaatsing (AFP) en geautomatiseerde tape-legging (ATL) de fabricageprocessen waren die een wijdverbreide toepassing van composieten in de Boeing 787 en Airbus A350 mogelijk maakten, dan zal het ook AFP/ATL zijn die de weg wijst voor de volgende generatie commerciële vliegtuigen, nu op tekentafels. Het verschil deze keer? Beoordeel.
Boeing schat dat de wereld tegen 2037 meer dan 31.000 nieuwe vliegtuigen met één gangpad nodig zal hebben om aan de vraag van passagiers te voldoen. Airbus voorspelt een behoefte aan meer dan 28.000 enkelgangsvliegtuigen tegen 2037. Beide bedrijven overwegen vervanging van hun enkelgangers - de 737 (Boeing) en de A320 (Airbus). Van beide bedrijven wordt verwacht dat ze composieten aanzienlijk gebruiken in elk nieuw vliegtuig dat ze ontwikkelen. Beide bedrijven vertellen hun toeleveringsketens dat ze voor deze vliegtuigen productiesnelheden van 60-100 vliegtuigen per maand verwachten, met de nadruk op 100. De categorie met één gangpad vertegenwoordigt voor beide bedrijven ongeveer twee derde van de totale wereldwijde vraag, wat betekent dat de productieomgeving die is ontwikkeld voor vliegtuigen met één gangpad, wordt in de nabije toekomst de standaardproductieomgeving voor aerocomposieten.
Dit alles betekent dat automatiseringstechnologie nu moet worden ontwikkeld als het wil voldoen aan de kwaliteits- en productiesnelheidseisen van vliegtuigen van de volgende generatie. Niets van dit alles gaat verloren bij Electroimpact (EI, Mukilteo, Wash., U.S.) senior engineer Todd Rudberg. Rudberg en EI betraden de composietenwereld in 2004 toen het bedrijf AFP-technologie ontwikkelde voor de fabricage van de 787 Section 41 voorste rompsectie, vervaardigd door Spirit AeroSystems (Wichita, Kan., V.S.). EI ging vervolgens AFP- en ATL-systemen produceren voor de fabricage van andere 787-constructies, A350-constructies, motorconstructies en, meest recentelijk, Boeing 777X-vleugelliggers. Nu kijkt Rudberg naar de toekomst van de vliegtuigproductie van de volgende generatie en ziet hij kansen voor AFP om te verbeteren. Aanzienlijk.
De kansen, zegt Rudberg, zijn duidelijk als je naar de gegevens kijkt. EI heeft zelfs verschillende statistieken ontwikkeld om het bedrijf te helpen begrijpen wat zijn machines goed doen en wat het kan verbeteren. Ten eerste ziet Rudberg, wanneer hij over het AFP-landschap van 2019 kijkt, talloze bedreigingen voor de huidige AFP-technologie, waaronder ATL, handoplegging, platte ladingen van geweven stoffen en, natuurlijk, aluminium.
De AFP-statistieken die Rudberg ontwikkelde, zijn afkomstig van een volledig productiedemonstratieproject (FPD) waarvoor EI vier preproductie-builds heeft uitgevoerd. Gegevens van een van die builds, uitgevoerd in februari 2019 met "standaard" EI AFP-technologie, onthulden een aanzienlijke uitdaging in het gebruik van de machine, waarbij de gebruikstijd van de machine in een van de zeven emmers viel:
- Laserprojectie:30%
- Rennen:27%
- Inspectie:22%
- Pauze:10%
- Door de operator veroorzaakte stop:6%
- Foutherstel:3%
- Afbeelding:2%
Op een andere manier bekeken, met de huidige technologie, is er één operatie met toegevoegde waarde in AFP (run), waarbij al het andere wordt beschouwd als operaties zonder toegevoegde waarde. De verhouding tussen waarde- en niet-waarde-operaties is dus 1:3. "De industrie wil echt 3:1, en ik ook", zegt Rudberg, "en ik zou dit graag gedaan willen hebben voordat ik met pensioen ga." Het doel is simpelweg om de tijd te verminderen die wordt verbruikt door niet-waardetoevoegende operaties.
Er is ook één overkoepelende AFP-statistiek die uitleg behoeft:gemiddelde strips voor falen (MSBF). Dit is het gemiddelde aantal glasvezelkabels dat tussen plaatsingsfouten is geplaatst. Hoe groter dit aantal, hoe betrouwbaarder de machine en het proces natuurlijk. De FPD-build van februari, zegt Rudberg, had een MSBF van 5365.
De doelen
Als we de operatie van AFP nader bekijken, zegt Rudberg, heeft EI directe controle over slechts drie operaties:run, foutherstel en inspectie. En daar richt het bedrijf zijn inspanningen op. Dat gezegd hebbende, wijst Rudberg erop dat de vliegtuigbouwer ook een rol te spelen heeft, met name bij het verminderen van kwaliteitsinspecties, pauzes en door de operator veroorzaakte stops. "We moeten ons realiseren dat de looptijden erg laag zijn geworden omdat machines erg snel zijn", zegt hij, "en alles wat geen toegevoegde waarde heeft, heeft een enorme impact op uw gebruik. Het blijkt dus een teamsport te zijn. Niet alleen de OEM — ik — moet het beter doen, de vliegtuigbouwer heeft ook enige verantwoordelijkheid.”
Voor de fabricage van vliegtuigen van de volgende generatie wil Rudberg de MSBF verhogen tot>20.000, de looptijd verhogen tot 77% en laserprojectie, door de operator veroorzaakte stop en beeld volledig elimineren. Hoe? Rudberg identificeert drie technologische gebieden die deze overgang kunnen vergemakkelijken:servo-aangedreven korven, 100% in-process inspectie en gegevensbeheer, of EI 4.0.
Alle drie zijn beoordeeld door EI in een reeks recente FPD-projectbuilds na die eerste build in februari. Gegevens uit het FPD-project zelf bewijzen dat EI op de goede weg is. Rudberg zegt dat het gebruikte AFP-systeem - genaamd MuSCLE - 1.500 pk piekvermogen, 0,5 G acceleratie/vertraging, een neerlegsnelheid van 4.000 inch/minuut, een kopdraaitijd van 1 seconde, een spar-hoeksnelheid van 120 graden/seconde en 6.000 MSBF behaalde. (behaald in productie).
De conversie naar servomotor-creels, en weg van servo-pneumatische korven, zegt Rudberg, is gedaan om de snelheid van het plaatsen van de sleep, de nauwkeurigheid van de plaatsing van de sleep, de controle van de trekspanning en de algehele betrouwbaarheid van de constructie te verhogen. Het bedrijf heeft de afgelopen twee jaar gewerkt aan een compacte servoaandrijving die op de EI modulaire kop kan worden geïnstalleerd. De resultaten van de technologie zijn tot dusver veelbelovend; testresultaten:15.000 MSBF, 87% hogere optelsnelheid, 36% hogere snijsnelheid, betere nauwkeurigheid bij het plaatsen van het uiteinde. Verder bewees EI dat het servomotor-creelsysteem kan worden gebruikt om droge koolstofvezels te plaatsen.
De sleutel voor inspectie is het "in-process" gedeelte. EI beschikt al over inspectietechnologie, ontwikkeld met Aligned Vision (Chelmsford, Mass., VS) en ingezet op de 777X-vleugelproductielijn die laser- en vision-technologie gebruikt om te controleren op ronden, gaten, kreukels, fouten bij de eindplaatsing en vuil van vreemde voorwerpen ( FOD). Dit systeem bestaat echter onafhankelijk van het AFP-systeem en vereist een duidelijk gezichtsveld om te kunnen werken - wat betekent dat de AFP-kop moet worden verplaatst. Rudberg en EI hebben een nieuw inspectiesysteem ontwikkeld, RIPIT genaamd, dat een integraal onderdeel is van de AFP-kop en de plaatsing van vezels inspecteert zodra deze zich voordoet.
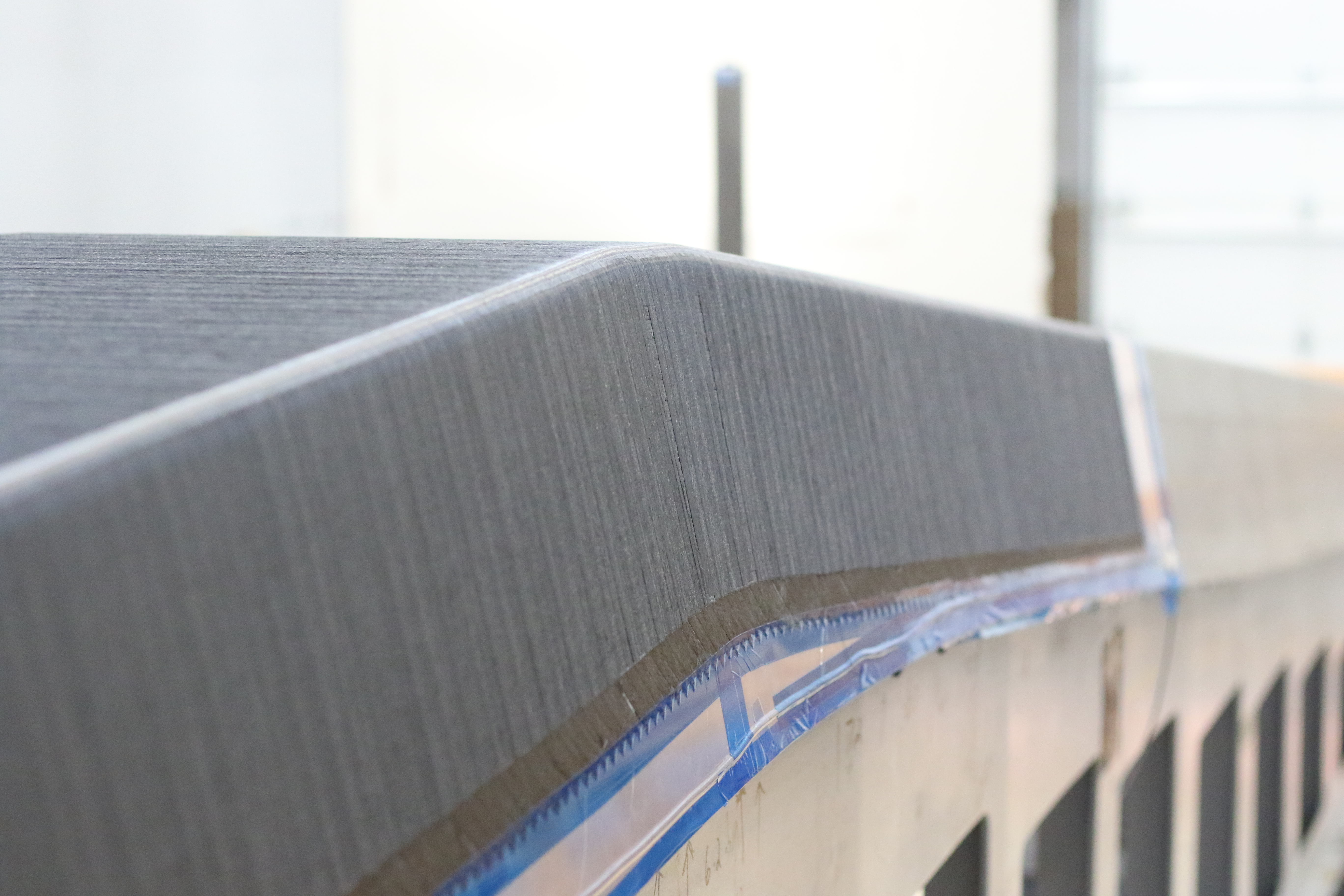
Aangezien Boeing en Airbus productieprocessen voor composieten buiten de autoclaaf overwegen, zal het vermogen van AFP-systemen om droge koolstofvezels efficiënt te plaatsen van cruciaal belang zijn. Deze demonstratorspar toont droge vezels geplaatst door een Electroimpact-systeem. Bron | Elektro-impact
EI zal de aard van de technologie achter RIPIT niet onthullen, behalve om te zeggen dat het niet laser- of vision-gebaseerd is. In ieder geval zegt Rudberg dat tests van het systeem aantonen dat het in staat is om in realtime sleepslippen tot ±0.030 inch te detecteren, plaatsing toe te voegen tot ±0.050 inch en plaatsing tot ±0.050 inch te verminderen. Verder zegt Rudberg:"We hebben veel proeven gedaan om RIPIT-gegevens te correleren met het bestaande Boeing-gekwalificeerde vision-systeem [Aligned Vision-systeem gebruikt op 777X] en we krijgen correlatie."
De waarde van gegevensbeheer, zegt Rudberg, ligt in het vermogen van de systemen van EI om fabrikanten te helpen duidelijker te zien hoe goed het AFP-proces werkt. Daartoe heeft EI software voor gegevensvisualisatie ontwikkeld - EI 4.0 - die niet alleen inzicht biedt in hoe een bepaalde machine presteerde (op basis van MSBF) tijdens een bepaalde build, maar ook in hoe individuele slepen en sequenties presteerden. Kortom, de software helpt de operator precies te zien waar in de AFP-kop het probleem zich bevindt. "Dus we zullen deze EI 4.0 gebruiken om aan te geven waar ze [operators] moeten gaan kijken in het AFP-hoofd om wijzigingen aan te brengen", zegt Rudberg.
Met behulp van deze software is het mogelijk om MSBF grafisch weer te geven voor een verscheidenheid aan machinefuncties en om probleemvezelkabels en bijzonder uitdagende sequenties te identificeren. De software meet en rapporteert ook andere machine-activiteiten die het gebruik kunnen aantasten. Met behulp van deze tools voor gegevensbeheer kon EI de bouwtijd voor de OPS optimaliseren en verminderen van meer dan 50 minuten tot iets minder dan 40 minuten. Andere tools zijn onder meer vergelijkingen van schakelprestaties en vergelijkingen van laaghoeken.
"Ik geloof echt dat het gebruik van 75% een realistisch doel of verwachting is", stelt Rudberg. “Maar er is teamwork voor nodig, er is organisatorisch initiatief en follow-up van de vliegtuigbouwer nodig, er is onze verbeterde technologie voor nodig, er is beter preventief onderhoud en voorspellend onderhoud nodig, en betere hulpmiddelen om het celgebruik te analyseren en machineprestaties.”
Hars
- Industrie 4.0 en het IoT:markttrends voor de komende jaren
- Augmented reality – The next big thing voor HR?
- DARPA werkt aan nieuwe generatie materialen voor hypersonische voertuigen
- Nieuwe kristallen voor de volgende generatie displaytechnologieën
- Hoe u zich kunt voorbereiden op de volgende verstoring van de toeleveringsketen
- Vijf regels voor de volgende supply chain-crisis
- Merchandising in de cloud is de volgende must-have voor de detailhandel
- Materiaal voor de volgende generatie slimme sensoren
- COVID-19:vraag naar de volgende generatie slimme fabrieken
- Waar volgt de automatiseringsrevolutie?
- Stikstofproductie in de lucht- en ruimtevaartindustrie