Hoogtepunten:Composites Convention 2019
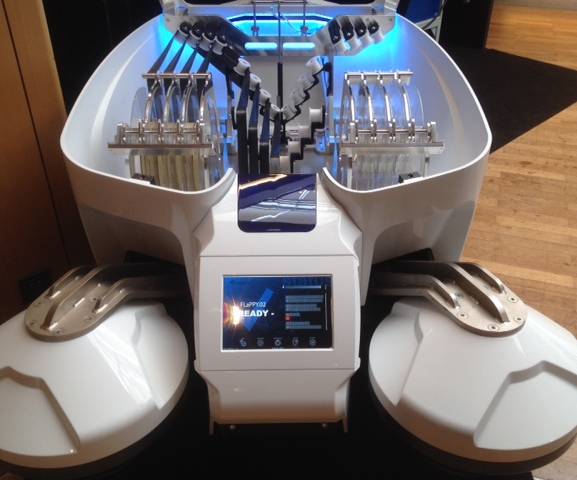
DLR's intrigerende naam Flappybot (Flexibele autonome productie-, plaatsings- en assemblagerobot) prototype is een radicale afwijking van de grote en dure statische machines die gebruikelijk zijn bij de productie van grote ruimtevaartcomponenten. Deze compacte autonome AFP-unit is ontworpen om direct over de mal te ‘rijden’. Bron | DLR
Als de composietenindustrie wil blijven groeien en haar concurrentievermogen wil verbeteren, moet ze de kansen benutten die digitalisering en automatisering met zich meebrengen. Op twee recente op lucht- en ruimtevaart gerichte conferenties in Duitsland werd gekeken naar wat de toekomst van de fabricage van composieten zou kunnen inhouden.
Een bezoek aan de fabriek van de toekomst in Stade
Future Factory for Composites was het thema van de Composites Convention van dit jaar in Stade, Duitsland, die van 12-13 juni werd gehouden. Gezamenlijk georganiseerd door CFK Valley e.V. (Stade, Duitsland) en Carbon Composites e.V. (Augsburg, Duitsland), trok het evenement een recordopkomst van bijna 450 mensen. Een sterke aanwezigheid in de VS was het resultaat van een samenwerking met het Utah Advanced Materials and Manufacturing Initiative (UAMMI, Kaysville, Utah, VS) als partnernetwerk en de Verenigde Staten als partnerland.
In de openingspresentatie, getiteld "Digitalisering:overgang van computerondersteunde productie naar menselijke automatisering", zei Dr. Jan Stüve, hoofd van het Centrum voor Lichtgewicht Productietechnologie van het Duitse Lucht- en Ruimtevaartcentrum (Deutsches Zentrum für Luft- und Raumfahrt; DLR; Stade, Duitsland) bood een voorproefje van het komende programma. Toekomstige fabriekstechnologieën die bij DLR in ontwikkeling zijn, omvatten meerdere samenwerkende robots die samenwerken om de productietijd te verkorten en digitale tweelingen van machines die procesoptimalisatie mogelijk maken. Een ander belangrijk gebied betreft mobiele autonome robots voor flexibele productiescenario's. Deze omvatten het prototype FlappyBot, een compacte vezelplaatsingseenheid die over de mal beweegt. Stüve waarschuwde voor de potentiële gevaren van overmatige automatisering en besprak hoe digitalisering zou betrek mensen opnieuw bij het productieproces.
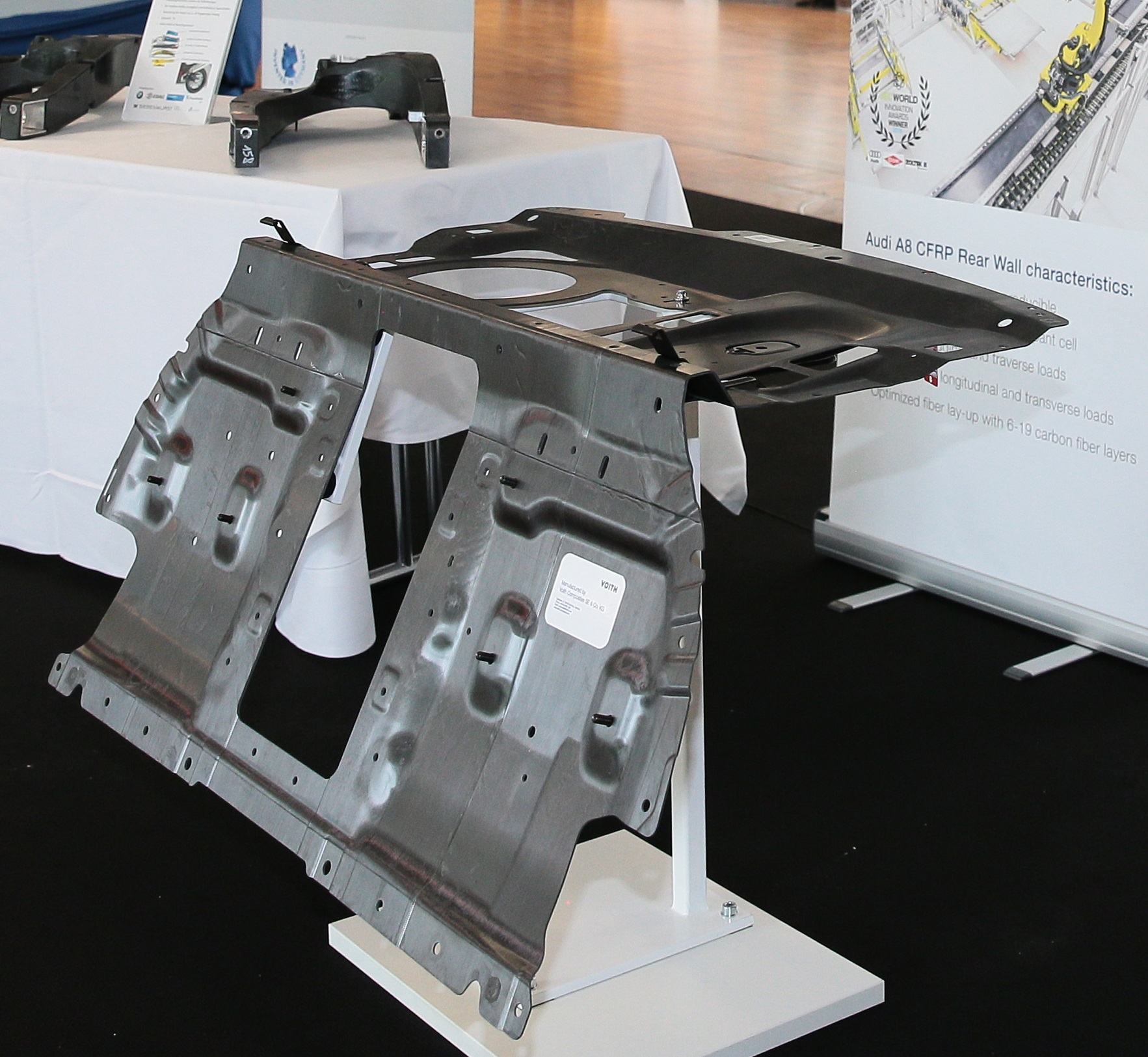
De Audi A8 CFRP-achterwand, het grootste onderdeel van de passagierskooi, wordt vervaardigd door Voith Composites in een sterk geautomatiseerd proces waardoor productievolumes van 65.000 onderdelen per jaar mogelijk zijn. Bron | CFK Valley
In een tweede keynote, "Rapid Manufacturing and Thermoplastic Composites - Trends and Technologies", nam Dr. Robert G. Bryant, senior materiaalingenieur bij het NASA Langley Research Center (Hampton, Va., VS), afgevaardigden weg uit de beslotenheid van de terrestrische fabriek in de richting van bouwen in de ruimte. Een langdurige menselijke aanwezigheid in de ruimte vereist als eerste stap beschutting en platforms. De ontwikkeling van steeds grotere raketten om steeds complexere structuren buiten de planeet te plaatsen is economisch niet duurzaam. Oplossingen vereisen fabricage in de buurt of op locatie. Het gebruik van een toolless advanced tape placement (ATP)-proces dat in-situ consolidatie van thermoplastische composietonderdelen mogelijk maakt, zou het antwoord kunnen zijn. Bij deze nieuwe techniek werken twee ATP-robots tegenover elkaar, de ene om de thermoplastische prepreg-tape af te zetten en de andere als gereedschap. Fabricage zonder gereedschap kan de kosten van lucht- en ruimtevaartproductie verlagen, de economie van ruimteverkenning verbeteren en andere marktsectoren ten goede komen (lees meer in "General Atomics Aeronautical development toolless thermoplasts composites process").
Duurzaamheid
Vooruitgang in de productie moet ook gepaard gaan met een vermindering van de milieu-impact. In die zin betoogde Jörg Spitzner, oprichter van Spitzner Engineers GmbH (Finkenwerder, Duitsland), in de volgende sessie dat om de klimaatdoelstellingen te halen, technologieën voor negatieve emissies nodig zijn. Het bedrijf van Spitzner beweert dat zijn gepatenteerde Blancair-windturbineconcept zowel de efficiëntie van de turbine verbetert als CO2 verwijdert uit de atmosfeer. Lucht wordt aangezogen in een filtermodule die op de gondel is gemonteerd, waar CO2 wordt gescheiden voor opslag en recycling bij de productie van synthetische brandstoffen en andere toepassingen. De gereinigde lucht wordt afgevoerd via openingen in de rotorbladpunten. Een video waarin het concept wordt uitgelegd, is beschikbaar op de website van Blancair.
De organisatoren van de sessie presenteerden ook een concept voor een slimme beoordeling van de eco-efficiëntie bij de productie van composieten (DLR), en geharde prepregs die buiten de autoclaaf op kamertemperatuur zijn gekomen met vuur, rook en toxiciteit (FST) (TCR Composites; Ogden, Utah, VS).
Empowerment door simulatie
De rest van de eerste dag van de conferentie ging de aandacht naar simulatie.
Dr. Lars Herbeck, chief technology officer bij Voith Composites (Garching, Duitsland), besprak hoe de Voith Roving Applicator-machine voor geautomatiseerde vezelplaatsing (AFP) de procesketen vereenvoudigt, waardoor een efficiënt geautomatiseerd voorvormproces met kortere cyclustijden mogelijk wordt. Hij schetste de structurele en processimulatie die werd uitgevoerd voor de geautomatiseerde productielijn die 65.000 componenten per jaar kan produceren voor de achterwand van de achterwand van koolstofvezelversterkte kunststof (CFRP) van de Audi A8.
Mark Bludszuweit van MET Motoren- und Energietechnik GmbH (Rostock, Duitsland) legde uit hoe simulatie inzicht biedt in de beste manier om onderdelen in een autoclaaf te laden, waardoor het uithardingsproces wordt geoptimaliseerd en de productiviteit wordt verhoogd. Een digitale tweeling die is ontwikkeld voor de grootste autoclaaf in de Stade-faciliteit van DLR, kan parallel lopen met het echte proces, of sneller om voorspellingen te doen van het gedrag van onderdelen.
Verdere onderwerpen voor virtuele procesontwikkeling betroffen het modelleren van SMC-processen (ESI Group; Chartres-de-Bretagne, Frankrijk) en processimulatie van sandwichpanelen om inzicht te krijgen in problemen met kernverplettering en prepreg-rimpels in de autoclaaf (Airbus Helicopters; Marignane, Frankrijk).
Wat betreft virtuele veiligheidsmodellering, besprak Jochen Rühl van Reichenbacher Hamuel GmbH (Dörfles-Esbach, Duitsland), onderdeel van Scherdel Gruppe, hoe een op simulatie gebaseerde benadering voor het beheer van stof en deeltjes die vrijkomen bij het bewerken van CFRP-onderdelen voordelen heeft opgeleverd voor klanten zoals als Airbus en Premium Aerotec (Augsburg, Duitsland). Bewerkingssimulaties en visualisatie van deeltjesverdelingen helpen fabrikanten om te voldoen aan de strengere gezondheids- en veiligheidswetgeving en verbeteren de bewerkingsresultaten, evenals verminderde machinestilstand en onderhoud, wat zich uiteindelijk vertaalt in lagere kosten per onderdeel.
De simulatiesessie toonde ook een door Boeing gesponsord project over virtuele kostenmodellering van composietproductie, rekening houdend met de complexe interacties tussen ontwerp, productie en financiën om kostenfactoren te identificeren (Massachusetts Institute of Technology; Cambridge, Mass., VS), en een concept voor digitale fabrieksplanning op basis van simulatieve modellering van optimale waardeketens van composieten (Fraunhofer IGCV; Augsburg, Duitsland).
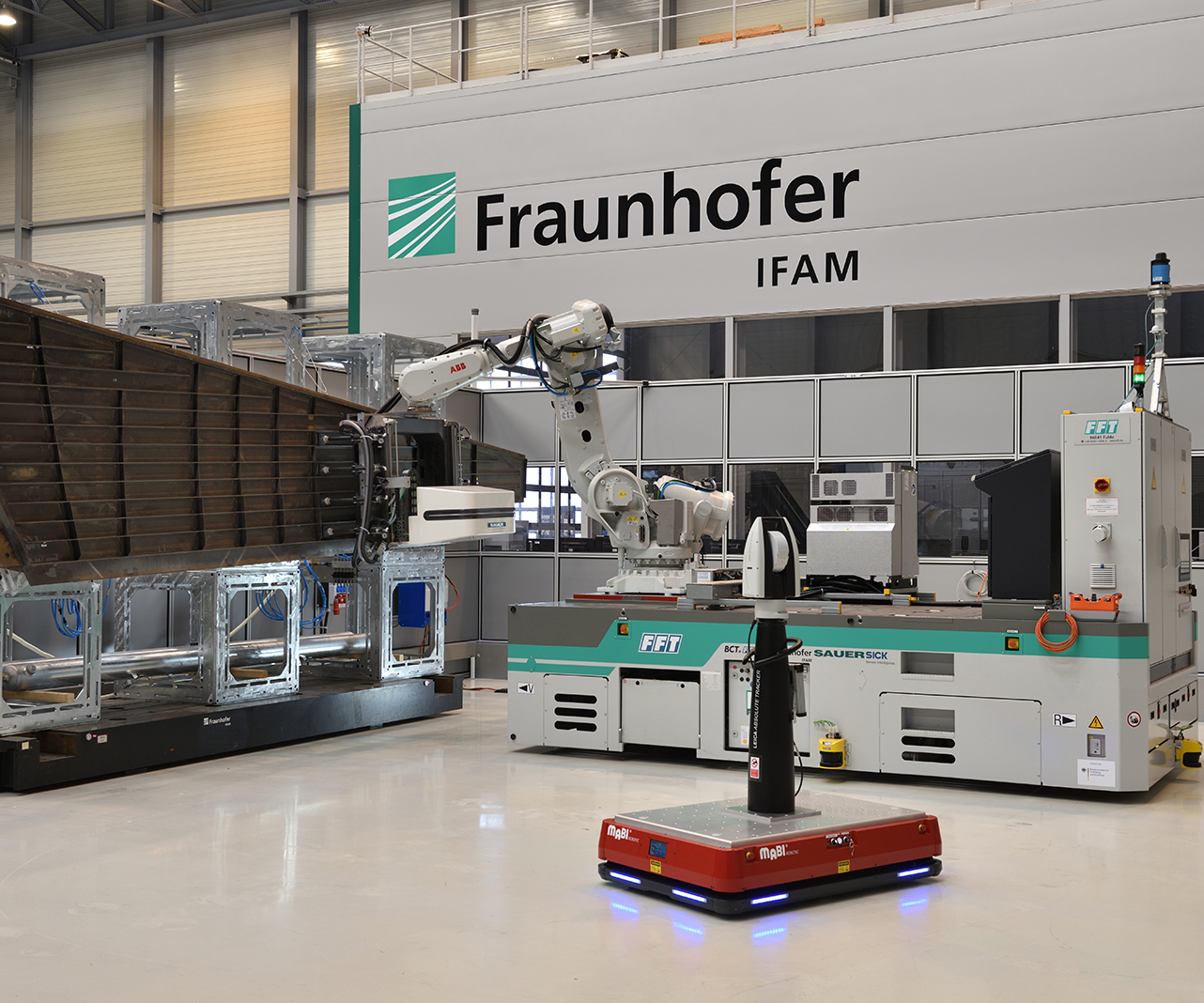
Het mobiele bewerkingsconcept MFBast18 is samengesteld uit een automatisch geleide voertuig, robot en draagbare CNC-machine en biedt een verhoogde productiviteit bij de productie van grote CFRP-vliegtuigonderdelen. Bron | Fraunhofer IFAM
Prijswinnaars
Dit jaar deelden twee projecten de CFK Valley Innovation Award en het prijzengeld van €7.500.
De eerste plaats (en € 4.500) ging naar het MBFast18-project voor mobiele robotsystemen, dat een op AGV’s gebaseerd mobiel CNC-bewerkingssysteem ontwikkelde voor grote CFRP-vliegtuigonderdelen.
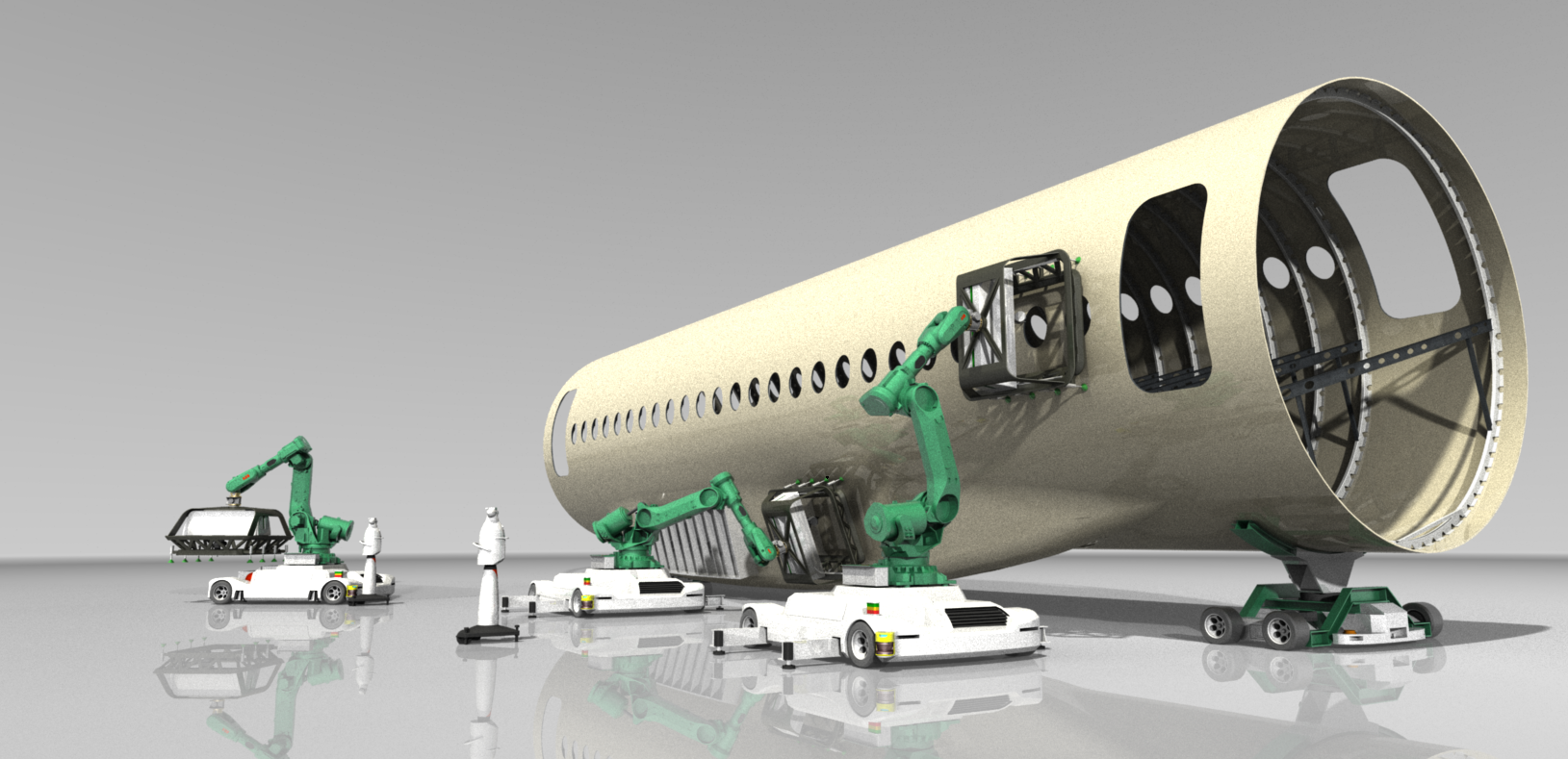
Bron | Fraunhofer IFAM
Vergeleken met de huidige dure, statische bewerkingssystemen voor grote vliegtuigconstructies, maken kleinere mobiele robotsystemen flexibele productie en hogere productiviteit mogelijk.
Het MBFast18-systeem maakt gebruik van een 4,6 meter lang autonoom platform gebouwd door FFT Produktionssysteme GmbH &Co. KG (Fulda, Duitsland), navigatie- en veiligheidssensoren geleverd door SICK AG (Waldkirch, Duitsland), en een 5-assige CNC-machine van SAUER /DMG MORI (Suhl en Bielefeld, Duitsland). Een mobiele lasertracker ontwikkeld door het Fraunhofer Institute for Manufacturing Technology and Advanced Materials (IFAM; Stade, Duitsland) positioneert de robot nauwkeurig. De boorunit, met een werkoppervlak van maximaal 0,5 vierkante meter, wordt met vacuümgrijpers op het onderdeel geklemd; boorposities worden berekend en doorgegeven aan de machine met behulp van software die is ontwikkeld door BCT GmbH (Dortmund, Duitsland). Dit concept is ook toepasbaar op handling- en assemblageactiviteiten en andere industrieën zoals windenergie en spoor.
Bekijk een video over het MBFast18-project:
De tweede plaats ging naar de start-up Hyconnect GmbH (Hamburg, Duitsland) voor zijn FAUSST metaal-composiet verbindingstechnologie. Het bedrijf richt zich in eerste instantie op de scheepsbouwsector, waar het samenvoegen van composieten aan metaal een grote belemmering vormt voor een bredere acceptatie van composieten. De FAUSST-oplossing maakt gebruik van een hybride weefsel bestaande uit kettinggebreid glas en metaalvezels waarmee metalen en composieten mechanisch stevig kunnen worden verbonden. De metaalvezelzijde is verbonden met een stalen profiel dat kan worden gelast aan metalen constructies, en de andere zijde is gelamineerd aan het composietcomponent. De gepatenteerde technologie zou het ontwerp- en verlijmingsproces aanzienlijk versnellen. De eerste prototypetoepassingen worden momenteel getest.
Bekijk een inleiding tot het deelnameproces van FAUSST:
Activering door automatisering
Op dag twee werd het bekroonde MBFast18-project in meer detail onderzocht in presentaties van Christoph Brillinger, projectmanager bij Fraunhofer IFAM, en Dr. Gregor Graßl van FFT, die de uitdagingen bespraken bij het ontwikkelen van slimme proces- en fabriekscontrolesystemen voor operaties met meerdere robots . Jerome Berg, stafingenieur bij Northrop Grumman Innovation Systems (Clearfield, Utah, VS), beschreef de geautomatiseerde productie van Airbus-stringers in de faciliteit van het bedrijf in Utah met behulp van een intern ontwikkeld AFP-proces, en Uwe Lang van Evonik Resource Efficiency GmbH (Darmstadt , Duitsland) introduceerde "Sandwich Technology 4.0", een geautomatiseerde productietechnologie voor hoge productiesnelheden die gebruik maakt van het ROHACELL-schuimkernmateriaal van het bedrijf. Een sterk geautomatiseerd voorvormproces voor een neuslandingsgesteldeur van een vliegtuig is gedemonstreerd in een samenwerking met DLR en Airbus' technologiehub CTC GmbH (Stade, Duitsland).
Bekijk een video van het voorvormproces:
Felix Hünecke, hoofd bedrijfsontwikkeling bij ABSOLUTE Reality GmbH (Hamburg, Duitsland), maakte een reis naar virtual reality en liet zien hoe 3D-modellen van gebouwen kunnen worden gemaakt, bewerkt en aangevuld met afbeeldingen, documenten en video's om virtuele omgevingen te creëren die kunnen worden overal ter wereld bekeken. Het bedrijf maakte een 3D-rondleiding door een DLR-productiehal in Stade.
Maak een wandeling door de productiehal van DLR:
Felix Schreiber, CEO, ARK Group (Aken, Duitsland), besprak de proces- en kostenvoordelen van gestructureerde machinegegevens in een geautomatiseerde productielijn voor harsoverdrachtgieten (RTM), terwijl Sascha Backhaus van CTC GmbH modulaire automatisering in de fabricage van composieten en de Hybr -iT-project, dat teams ontwikkelt waarin mensen en robots samenwerken met op software gebaseerde assistentiesystemen.
Geen enkele gebeurtenis over de toekomstige fabriek zou het onderwerp kunstmatige intelligentie (AI) kunnen negeren, en Amir Ben-Assa, CMO van Plataine (Waltham, Mass., VS) besprak de kansen en uitdagingen van het implementeren van AI in de productie van composieten. Hij presenteerde praktische toepassingen van AI, van waarschuwingen (bijvoorbeeld productievertragingen of kwaliteitsproblemen) tot aanbevelingen (bijvoorbeeld geoptimaliseerde materiaalkeuze). Op AI gebaseerde digitale assistenten op Google Glass zouden een andere mogelijkheid kunnen zijn, door 'handsfree' gebruikersinteractie met AI op de productievloer en realtime audio- en visuele presentatie van waarschuwingen te bieden.
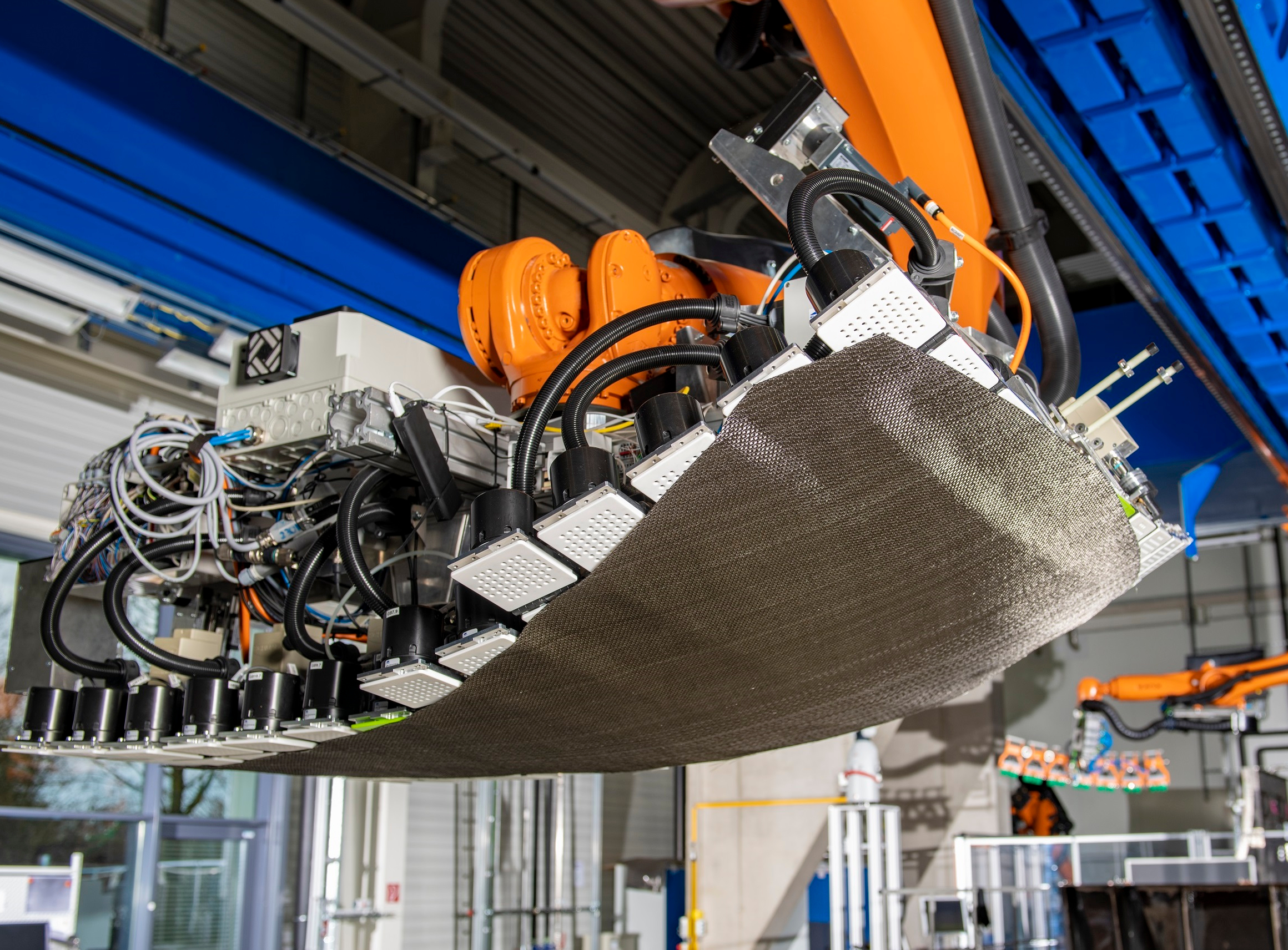
De multifunctionele robotcel van ZLP Augsburg is ontworpen om de ontwikkeling van geïntegreerde processen voor het vervaardigen van grote composietcomponenten op industriële schaal mogelijk te maken. Bron | DLR
Verdere onderwerpen waren:
- Glasvezeldetectie voor intelligente procesbewaking in grote composietstructuren (MT Aerospace AG; Augsburg, Duitsland);
- Een intelligent besturingssysteem voor de geautomatiseerde productie van composieten (National Composites Centre, Bristol, VK);
- Een op modellen gebaseerd kwaliteitscontrolesysteem voor het thermovormen van kleine componenten (Faserinstitut Bremen e.V.; FIBRE, Bremen, Duitsland);
- Een proces voor het persgieten van discontinue vezelversterkte thermoplasten voor vliegtuigtoepassingen, gebaseerd op flexibele automatisering en schaalbaar tot grote onderdelen (ACT Aerospace; Gunnison, Utah, VS);
- Een isotherm RTM-proces dat kortere cyclustijden biedt voor de productie van grote hoeveelheden CFRP-onderdelen (Airbus Helicopters)
- Grootschalige productie van complexe, hoogwaardige thermoplastische profielen van koolstofvezel voor stutten, pijpen en aandrijfassen met behulp van bijna netvormige tape-preforms en injectievormen (herone GmbH; Dresden, Duitsland). Lees meer over herone en dit proces in "Injection-forming for high-performance, unitized thermoplastische structuren."
10 jaar vooruitgang in Augsburg
In een apart evenement, tijdens het 5e colloquium over productietechnologie van de DLR op 15 mei, kwamen bijna 200 gasten samen in het Centrum voor lichtgewicht productietechnologie (Zentrum für Leichtbauproduktionstechnologie, ZLP) in Augsburg. Het evenement vierde het 10e jaar van ZLP in Augsburg, waar vandaag ongeveer 60 medewerkers zich richten op automatisering en digitalisering van de composietproductie.
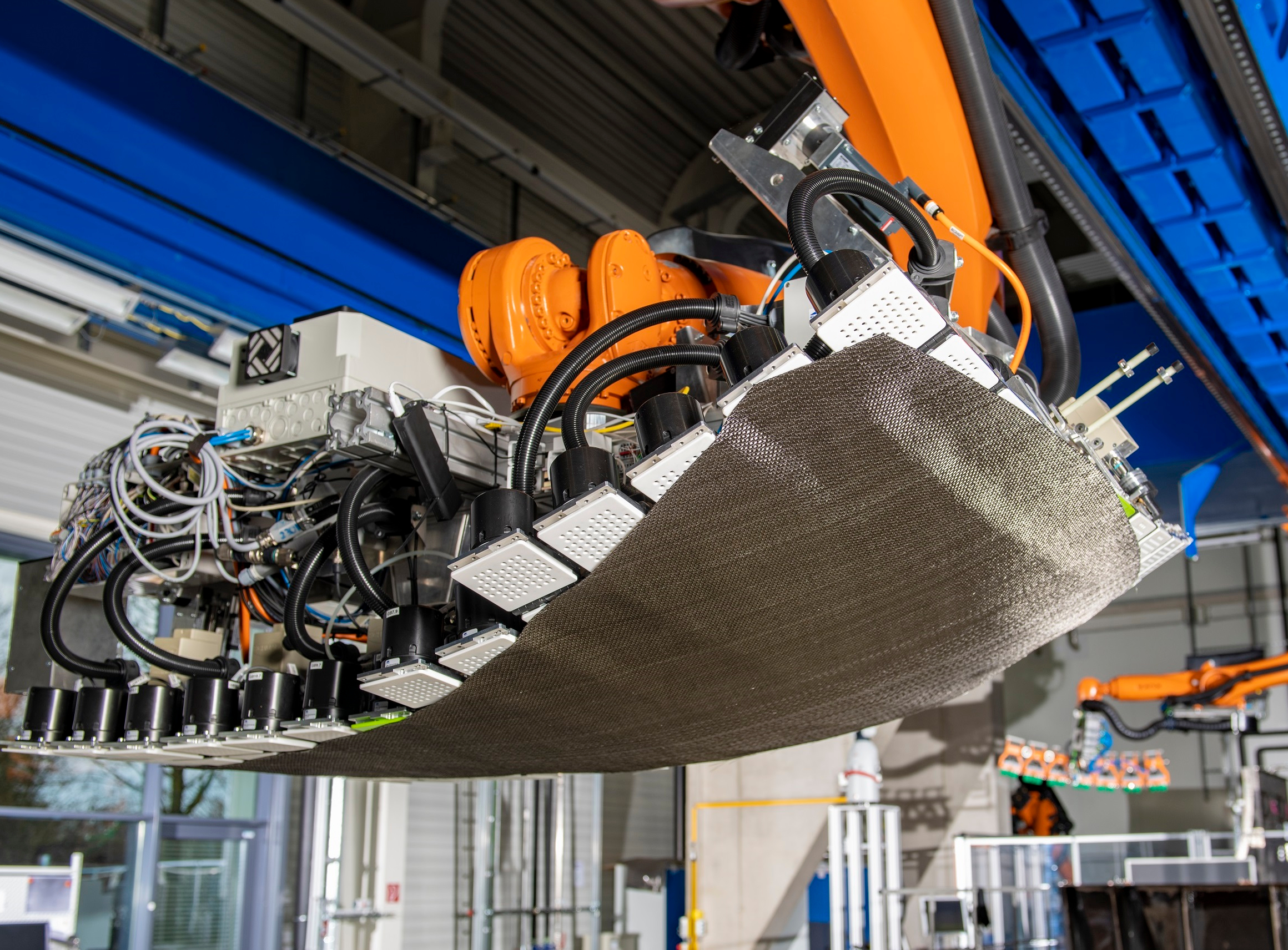
Een robotgrijper voor geautomatiseerd draperen, onderdeel van het geïntegreerde productieproces van ZLP Augsburg voor structurele componenten op ware grootte. Bron | DLR
De dag begon met twee presentaties van de University of British Columbia (UBC; Vancouver, Canada), die in 2016 een samenwerking aanging met DLR. Prof. Dr. Anoush Poursartip, mededirecteur van UBC's Digital Learning Factory Initiative, introduceerde het concept van een leerfabriek voor composieten geïnspireerd op medische academische ziekenhuizen. De leerfabriek voor composieten, die zich op de Okanagan-campus van UBC zal bevinden, zal worden ontworpen om onderzoek en onderwijs te integreren met industriële activiteiten. Een digitale tweeling die wordt gehost bij UBC Vancouver, zal gegevens van de fysieke fabriek combineren met simulatie om de productieprocessen van lucht- en ruimtevaartcomposieten te optimaliseren. Vervolgens bespraken prof. dr. Homayoun Najjaran van UBC en Marian Körber van DLR de optimalisatie van complexe productieprocessen in een virtuele omgeving, en hoe UBC's expertise op het gebied van machine learning-technieken en kunstmatige intelligentie wordt gebruikt om de tijd en kosten van de ontwikkeling van robotsystemen bij DLR te verminderen . Er werd een diepgaande leermethode gebruikt om de robotgrijper van ZLP te trainen voor geautomatiseerd draperen, een belangrijk onderdeel van de geautomatiseerde procesketen van de fabriek in Augsburg voor het vervaardigen van grote CFRP-onderdelen. De grijper met 127 zuigmodules met variabele zuigkracht herkent en pakt gesneden materiaal op; de modules nemen de geometrie aan die nodig is om ze op hun plaats in de mal te draperen.
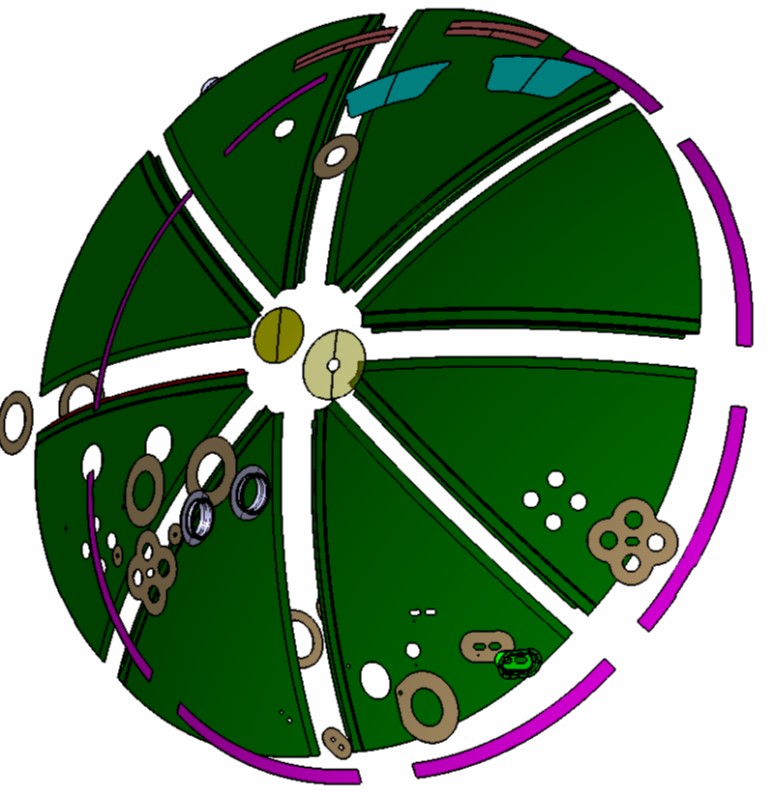
De thermoplastische composietcomponenten voor Premium Aerotec's achterste drukschotontwerp worden samengevoegd met behulp van een weerstandslastechniek die is ontwikkeld bij ZLP Augsburg. Bron | Premium Aerotec
Thermoplastische technologieën zijn een ander aandachtspunt voor ZLP Augsburg. Ralph Männich en Alexander Sänger van Premium Aerotec GmbH hebben een project geschetst om 's werelds eerste thermoplastische achterste drukschot (RPB) voor vliegtuigen met één gangpad te ontwikkelen. Het bedrijf werkt samen met ZLP Augsburg, Toray Advanced Composites en het Institute for Composite Materials (IVW) aan een ontwerp dat bestaat uit acht CFRP-segmenten met geïntegreerde stringers die zijn verbonden met behulp van een door ZLP ontwikkelde weerstandslastechnologie. Geautomatiseerde processen met korte cyclustijden maken productie in hoge volumes mogelijk. De voltooiing van de technologie (tot TRL 6) is gepland voor 2020 en de implementatie is gepland voor 2021/2022. Tijdens de Paris Air Show in juni toonde Premium Aerotec een 1:1-demonstrator voor een vliegtuig uit de Airbus A320-serie. Vergeleken met de huidige A320-drukschotten gemaakt van geklonken aluminium componenten, zou het thermoplastische onderdeel dezelfde mechanische eigenschappen bieden met een gewichtsbesparing van 10-15% en een vermindering van de productietijd met 50%. In de volgende lezing gingen Dr. Stefan Jarka en Manuel Endraß van DLR door met het thema thermoplastisch lassen en gingen dieper in op de verbindings- en NDT-mogelijkheden van ZLP Augsburg en zijn rol in het RPB-project.
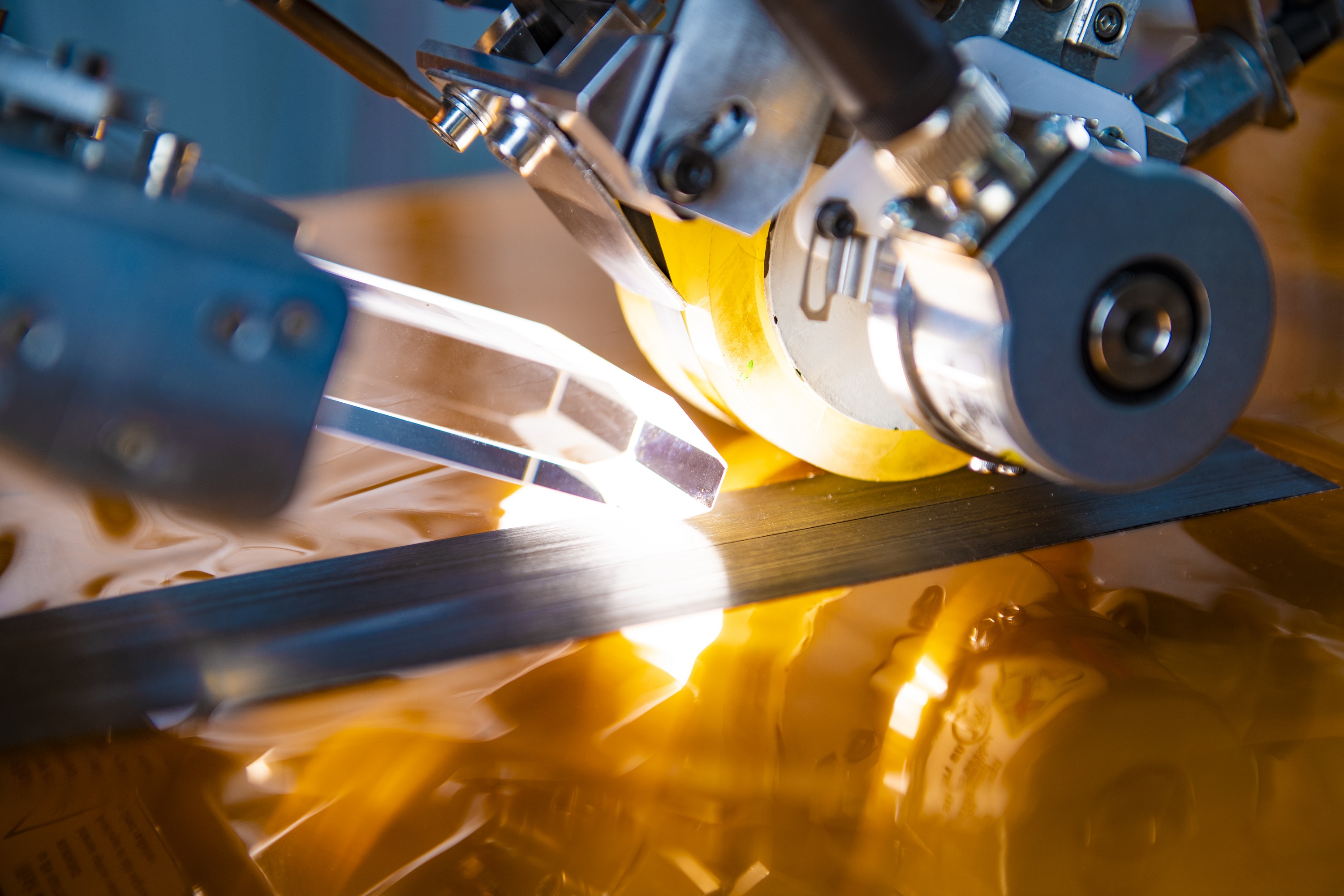
ZLP Augsburg onderzoekt op flitslampen gebaseerde in-situ AFP van thermoplastische composieten, een oplossing met gepulseerde energie die de veiligheidsbehuizingen elimineert die nodig zijn voor op laser gebaseerde AFP. Bron | DLR
Ook in de ruimtevaart bieden thermoplastische composieten kansen. Presentaties van Ralf Hartmond, MT Aerospace AG en Lars Brandt, projectmanager voor ruimtegerelateerde toepassingen bij DLR, schetsten de ontwikkeling van een met koolstofvezel versterkte thermoplastische boventrap voor de volgende generatie Ariane raketwerper. Brandt gedetailleerd het werk van DLR over materiaalscreening voor de tank voor vloeibare waterstof (LH2 ) tank - waar koolstofvezel PEEK en low-melt (LM) PAEK veelbelovend zijn - en ontwikkeling van een in-situ thermoplastisch composiet AFP-proces om een lean additive manufacturing-benadering mogelijk te maken. ZLP vergelijkt een nieuw flitslamp-geassisteerd in-situ AFP-proces met traditionele laser-ondersteunde AFP.
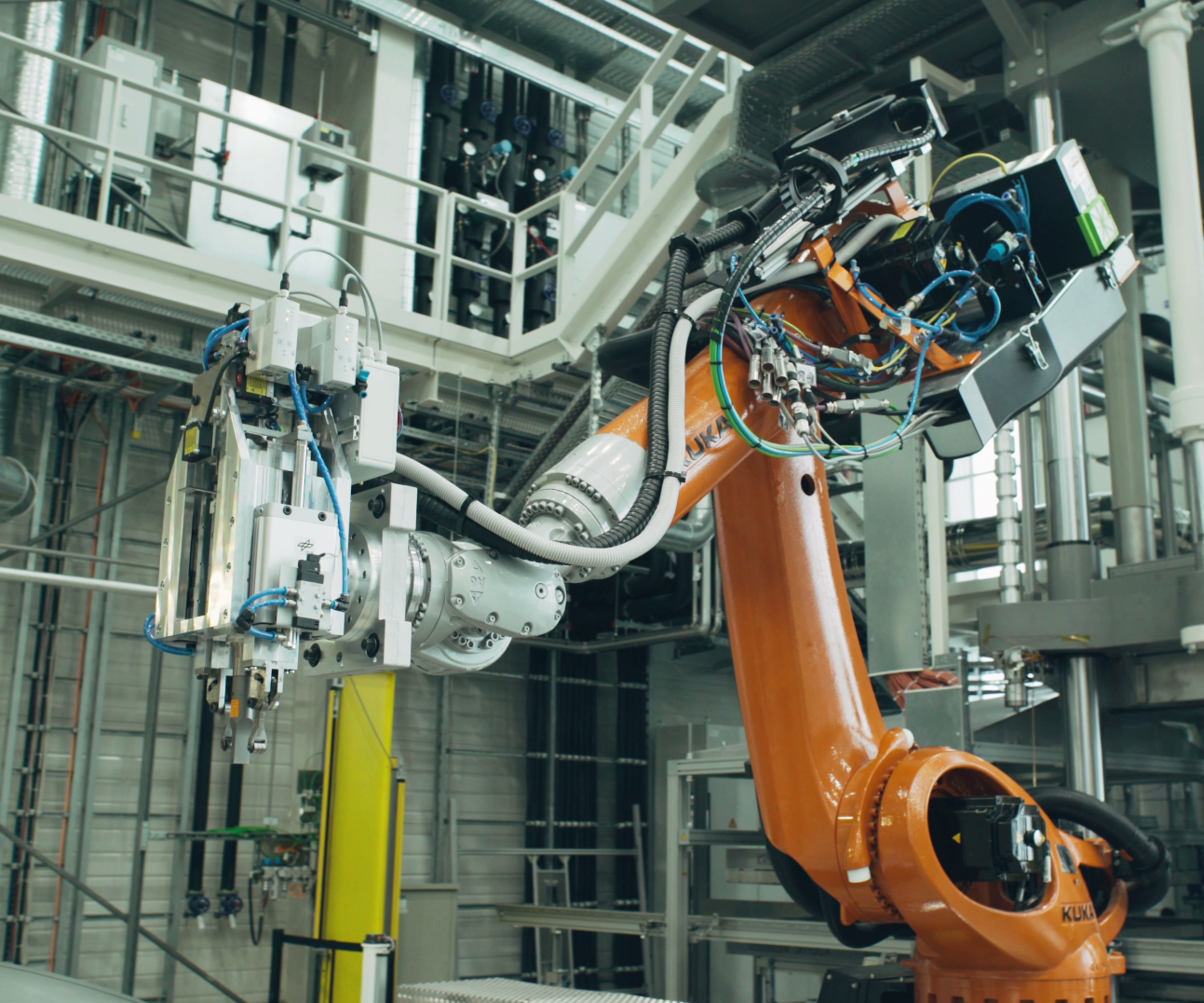
Verbindingstechnologieën zullen de sleutel zijn tot de succesvolle introductie van thermoplastische composieten in toekomstige ruimtevaarttoepassingen. ZLP in Augsburg heeft een op een robot gebaseerd continu ultrasoon lassysteem ontwikkeld dat bestaat uit een eindeffector gemonteerd op een KUKA QUANTEC KR210-robot op een lineaire baan van 7 m. Dit is bewezen op componenten zoals een verstijfd romppaneel en een achterste drukschot. Bron | DLR
De dag werd afgesloten met een tot nadenken stemmende keynote van Prof. Dr. Michael Kupke, hoofd van ZLP Augsburg, getiteld "Digitalisering en flexibele productie". Hij vroeg of de opkomst van de digitale platformeconomie kansen of risico's biedt voor composietproducenten, en wees erop dat IT een kerncompetentie aan het worden is en moet worden behandeld als een concurrentievoordeel dat waarde toevoegt in plaats van als een kostenpost. Hij zei ook dat er een voortdurende paradigmaverschuiving plaatsvindt van gedetailleerde planning naar zelforganisatie (lean productie) en automatisering in combinatie met digitalisering. AI, zegt hij, maakt autonome, flexibele productie mogelijk. Kupke concludeerde echter dat het essentieel is om menselijke vaardigheden, die essentieel zijn voor besluitvorming en procesverbetering, te waarderen en te integreren.
Hars
- 4 brandende vragen voor additieve productie in 2019
- 25 belangrijke mijlpalen voor de productie van additieven in 2019
- 3 productievoorspellingen voor 2019
- Top 10 ontwikkelingen op het gebied van composietproductietechnologie
- Composite fabricage:de fabricage van composietmaterialen
- Meer van JEC World 2019
- JEC World 2019 preview:SABIC
- Mensen in composieten – januari 2019
- Automatiseringstechnologie benadrukt veiligheid, flexibele productie
- 2019:Productievoorspellingen
- Best practices voor productiemarketing voor 2019