Aflevering 33:Ethan Escowitz, Arris Composites
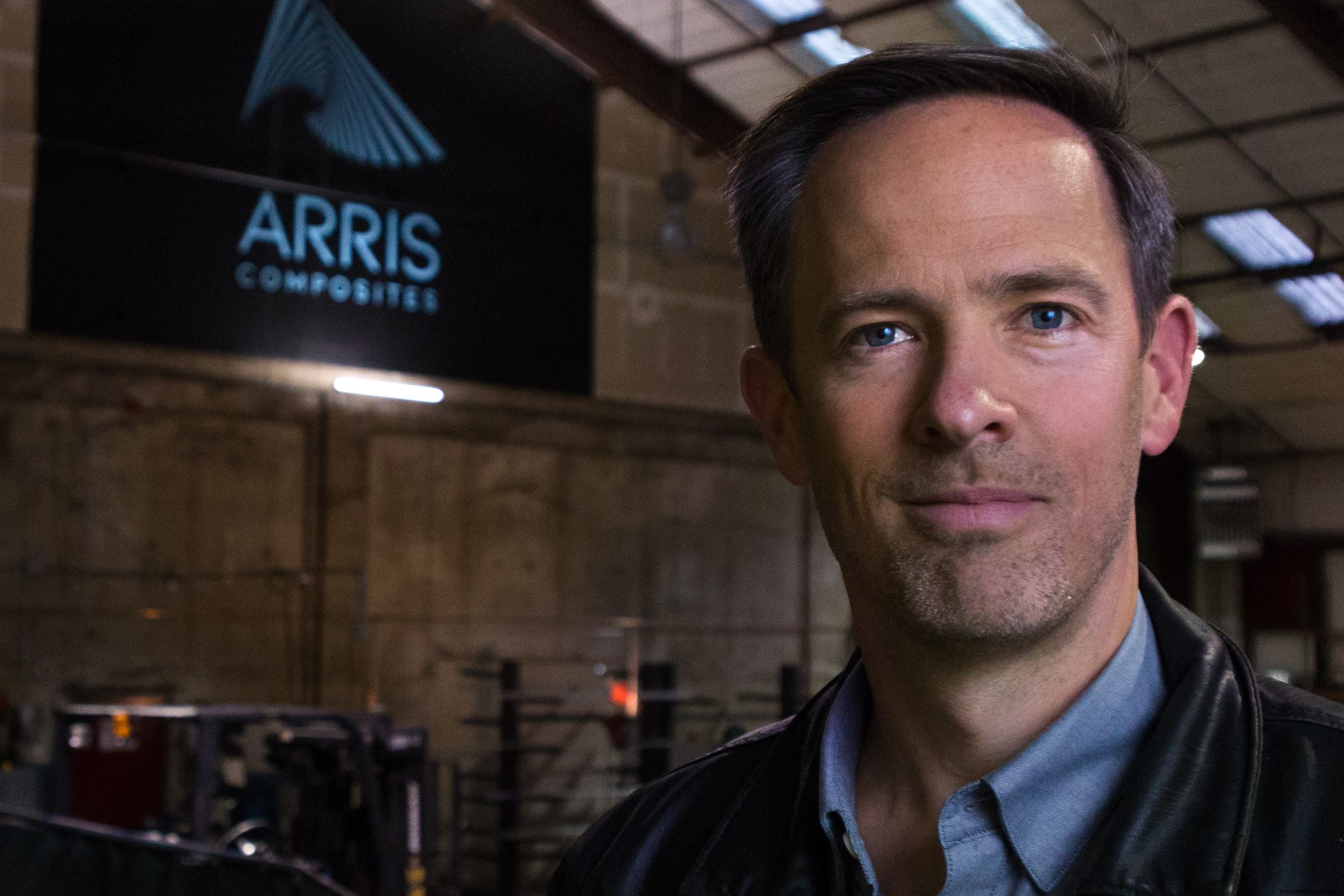
In deze aflevering van CW Talks:The Composites Podcast, host en CW hoofdredacteur Jeff Sloan praat met Ethan Escowitz, mede-oprichter en CEO van Arris Composites (Berkeley, Californië, VS). Ethan bespreekt hoe hij in aanraking kwam met composietproductie, de Additive Molding-technologie die de basis vormt van Arris' bedrijf, hoe deze is ontwikkeld, de toepassingen waarvoor deze het meest geschikt is en recente R&D die door het bedrijf is uitgevoerd.
Jeff en Ethan bespreken tijdens dit interview een technische paper die Arris presenteerde op CAMX 2020, getiteld "The Convergence of Composites and Topology Optimization, Ushering in the Next Era of Aircraft Lightweight Structures." Het papier schetst het werk dat Arris deed met Northrop Grumman om een samengestelde beugel te ontwikkelen ter vervanging van een metalen oude beugel.
Transcript van podcastinterview met Ethan Escowitz, opgenomen op 30 september 2020
Jeff Sloan (JS): Hallo allemaal en welkom bij CW Talks, de Composites Podcast. Ik ben Jeff Sloan, hoofdredacteur van CompositesWorld. Dit is aflevering 33 van CW Talks en mijn gast vandaag is Ethan Escowitz, mede-oprichter en CEO van het in Berkeley, Californië gevestigde Arris Composites. Ik zal met Ethan praten over de Additive Molding-technologie die Eris heeft ontwikkeld, waarop toepassingen worden gericht en hoe Additive Molding op de markt wordt ingezet. Ethan vertelt ook hoe hij zijn carrière als geoloog begon en in composieten terechtkwam. Hallo, Ethan en welkom bij CW Talks.
Ethan Escowitz (EE): Hoi Jeff, leuk om hier te zijn. Ik heb er met plezier naar geluisterd en ik vind het fijn om hier persoonlijk te zijn.
JS: Laten we het eerst hebben over Arris Composites. Ik zou graag willen dat je ons publiek iets vertelt over wat Arris Composites is, wanneer je het bedrijf hebt opgericht en waarom.
EE: Natuurlijk, dus laat ik dat achterstevoren nemen. We zijn begonnen in 2017. In de aanloop daarvoor had ik veel tijd besteed aan conventionele productie, het gieten, vormen, gieten van veel van de technologieën die veel van de producten maken die ons elke dag omringen, en dan vóór 2017, ongeveer een decennium daarvoor, was dat echt veel meer gericht op additive manufacturing, en zowel de composiet/metaal/kunststof ruimtes, en er was uiteindelijk begin 2017 een beetje een brug waar ik naar op zoek was , en hoe ik de voordelen die ik zag in de wereld van composietproductie met additieve fabricage kon benutten en deze kon combineren met de capaciteiten in grote volumes die zo efficiënt de producten produceren die ons elke dag omringen. Dus 2017, de video was echt waar we begonnen en het proces en enkele van de machine-elementen ontwikkelden. En, weet je, in de toekomst was een groot deel van het eerste jaar procesontwikkeling, een deel van de machineontwikkeling in 2018, we brengen productiesystemen, de vroege prototypes online. 2019 stond in het teken van het creëren van de robuuste en herhaalbare productie-elementen voor de systemen. En waar we echt aan hebben gewerkt, is het opschalen van de klantprogramma's waaraan we hebben gewerkt, parallel aan de ontwikkeling van onze technologie. Dus eigenlijk, om, denk ik, om je vraag op het hoogste niveau te beantwoorden, was het het combineren van de mogelijkheden in termen van prestaties van de uitgelijnde continue composieten, en enkele van de geometrieën die voorheen niet mogelijk waren en het opnemen van veel van de methoden die hadden ontwikkeld in de composietenwereld met betrekking tot verschillende materialen en lay-ups en dergelijke binnen geautomatiseerd productiesysteem.
JS: Oké, dus ik wil wat meer over jullie technologie praten, omdat ik weet dat wat je hebt ontwikkeld misschien technisch additieve fabricage is, hoewel ik denk dat het anders is dan wat we traditioneel beschouwen als additieve fabricage. Sterker nog, ik weet dat je je proces Additive Molding noemt. Wat ik zou willen doen, is dat je ons gewoon laat zien wat je proces is, en ik denk dat we hierin, als we dit posten, een paar video's kunnen opnemen die duidelijker laten zien hoe het proces werkt, maar misschien je kunt gewoon met ons praten over wat het proces is dat je hebt ontwikkeld.
EE: Natuurlijk, dus het is een stuk gemakkelijker om dit aan een samengesteld publiek uit te leggen, omdat de concepten zo bekend zijn, en het is ook de moeite waard om de naam Additive Manufacturing een beetje uit te pakken, omdat veel van de methoden, met name ATL, fundamenteel zijn hebben misschien een andere naam, maar zijn in veel opzichten hetzelfde proces als wat we additieve fabricage noemen. Dus, als we dat volgen, die gedachtegang een beetje, omdat sommige mensen ons additief zouden kunnen noemen, anderen misschien niet. Uiteindelijk schrijven we dat we echt profiteren van methoden die je kent, we kunnen tot op zekere hoogte door de geschiedenis van composieten kijken. Weet je, veel van de ambachtelijke en lay-upprocessen baanden de weg, ATL AFP begon te kijken naar elektromechanische manieren om vezeluitlijning te manipuleren. U weet dat opinieleiders zoals Fiber Forge begonnen te kijken naar geautomatiseerde preforming. En waar we toen echt naar keken, was hoe we deze complexe vezeluitlijningen in complexe delen konden maken. En in wezen produceert ons elektromechanische systeem deze bijna netvorm, complexe, continue vezel, voorgevormde assemblages, en dan vormen we ze in een nabewerkingsstap. Dus ik noem het een nabewerkingsstap. Weet je, in wezen is het een volledig soort, het is een volledig end-to-end geautomatiseerde productiecel. Maar als je gieten, nabewerking zou noemen, zou je het additieve fabricage kunnen noemen. Als je het voorvormen een voorgevormd proces noemt, zou je het een mal en mal in de preform-technologie kunnen noemen, het hangt er waarschijnlijk van af uit welke branche je komt.
JS: Oké, en dus, als je het hebt over nabewerking, wat bedoel je dan?
EE: Sorry, dus we hebben twee stappen in ons proces, één is de voorvormstap. En de tweede stap is de vormstap. Dus hebben we de naam additief overgenomen van de additieve fabricage van het maken van de preform-assemblage en het gieten van de vormstap, waar we de preform-assemblage consolideren
JS: Oké, en je vormt droge of prepreg-vezels rechtstreeks in een mal?
EE: Daarom gebruiken we thermoplastische composieten die vooraf geïmpregneerd zijn.
JS: En die worden automatisch, of in ieder geval met een soort van automatisering, in een mal gedeponeerd en vervolgens overgebracht naar een compressieproces.
EE: Ja, precies.
JS: En kun je de mallen of familie mallen groeperen? Ik denk dat het afhangt van de grootte van de preforms en de grootte van het onderdeel?
EE: Ja, de vormmethoden met meerdere holtes die zijn geëvolueerd in voornamelijk spuitgieten, hebben de weg vrijgemaakt voor de snelle warmtewisseling die de grote rendabiliteit op schaal van onze methoden biedt. Het hangt dus zeker af van het volume van het programma dat u draait, hoeveel holtes u op een bepaald onderdeel wilt laten draaien. En zeker de grootte van de onderdelen speelt ook een rol. Veel onderdelen waar we aan zullen werken, waren eerder een aantal verschillende onderdelen die een assemblage waren. We hebben niet de beperkingen van het spuitgieten waar je hars door moet laten stromen, weet je, een complexe set lopers en in poorten en vervolgens hoe u op de juiste manier kunt vloeien zoals u zou doen bij spuitgieten en dan ook met verschillende benaderingen voor harsoverdracht, waar u weet, die dingen leiden tot complexiteit en gereedschapskosten en ontwerpoverwegingen en kwaliteitsoverwegingen met harsrijke gebieden. Dus het werken met de voorvorm om het materiaal door het holtevolume te verdelen, geeft ons een zeer, het geeft ons een grote homogeniteit van composietmateriaal door alle zones, en neemt veel druk en instelkosten weg bij het maken van nieuwe onderdelen. Maar dat ook, om terug te keren naar het oorspronkelijke maatpunt, onderstreept waarom grotere maten heel praktisch kunnen zijn, omdat we het materiaal over een groter gebied kunnen verdelen of zeker door meerdere holtes als dat is als dat een soort van de grootte-onderdeelklasse is waar we het over hebben over.
JS: Oké, en dus als je klein zegt en als je groot zegt, wat bedoel je dan wat betekenen die voor jou?
EE: Zeker wel. Dus we hebben klantonderdelen gemaakt voor draagbare elektronica met eigenschappen die je kent, tussen punt drie vijf en punt vier vijf millimeter met uitgelijnde continue vezels, en dan hebben we je grote acht voet lange spanten laten kennen, de methode?
JS: Oke. Je zei ook dat het materiaal dat we gebruiken thermoplastisch prepreg thermoplast is. Doe je die prepregging zelf, of is de grondstof die je nodig hebt al prepregged?
EE: Beide, dus impregneren doen we in eigen huis voor uiteenlopende toepassingen. En dan is er natuurlijk een geweldig ecosysteem van leveranciers waar we ook mee samenwerken. Weet je, een deel van de eer van wat we vandaag de dag kunnen doen, gaat naar de materiaalbedrijven die dit echt brede assortiment kostenbesparende materialen hebben gemaakt, zowel natuurlijk in de vezelruimte als in de harsruimte die we in ons systeem kunnen gebruiken, die variëren van goedkopere, je weet wel, goedkopere consumentenproducten, harssystemen, helemaal tot aan luchtvaartkwaliteit, vlucht, vlucht goedgekeurde harssystemen. En dan vergelijkbaar met de prestaties van alle vezels.
JS: Je zei dat sommige projecten waaraan je hebt gewerkt, geconsolideerde onderdelen of structuren hebben die eerder uit meerdere onderdelen waren gemaakt. Ik vraag me af of je daar de goede plek voor dit proces ziet, of dat je ook het volume noemde. Ik vraag me af, weet je, als je dit proces positioneert, en je kijkt naar goede toepassingen ervoor, hoe passen die in elkaar?
EE: Ja, het is een geweldige vraag waarvan ik denk dat er geen goed algemeen antwoord voor is. Het roept eigenlijk de vraag op van productarchitecturen en nieuwe productiemethoden. Dus gewoon in principe, gewoon om erover te praten, in principe voor een seconde, veel van de onderdelen die onze drop-in vervangingen zullen vervangen zoals ontworpen, of productarchitectuur, de beste manier om dat onderdeel te maken, is waarschijnlijk om het te maken en alle aangrenzende delen tegelijk. En dan elimineren we al die discrete fabricagestappen plus de montagekosten. En daar hebben we mooie voorbeelden van, die we bij klanten hebben kunnen doen. Maar soms heb je die speelruimte niet bij klanten, vooral niet rond sommige producten met een langere productlevenscyclus, en ben je niet in staat om zo snel te veranderen. Het is een van de redenen dat het werken met een consumentenproductruimte, consumentenelektronica, echt is waar we zijn begonnen, omdat we de productarchitectuur daar veel sneller kunnen veranderen en kijken naar deelconsolidatie en, en in afwijkingen die als we het hadden over over een voertuig zou veel langer duren, en parallel daaraan hebben we zeker samengewerkt met de, je weet wel, de voertuigindustrieën voor de verschillende kwalificatiestappen die daar nodig zijn. Maar we begrijpen dat we vooral kijken naar het laten vallen van vervangende onderdelen in die ruimtes. Wat betreft je maatvraag nu, weet je, in een groot multi-cavity gereedschap, kunnen we een heleboel kleine onderdelen maken, weet je, heel snel, weet je, parallel proces. Weet je, ik denk dat iedereen grote gereedschappen met meerdere holtes ziet opraken van onderdelen, weet je, we kunnen gewoon onderdelen opraken die sterker zijn dan titanium en een stuk lichter. Dus we kunnen veel zeer waardevolle, hoogwaardige, kleine onderdelen maken. En dan voor producten met grotere architecturen, het consolideren van de assemblage, dat zou eigenlijk een assemblagelijn van stappen kunnen zijn, in die situaties vaak, het consolideren van al die stappen, ook al is het misschien een groot en complex onderdeel dat eenmalig wordt gemaakt, dat die vaak de naald echt kunnen verplaatsen in sommige van die meer complexe productarchitecturen. Dus verschillende verschillende strategieën voor verschillende onderdeelklassen.
JS: Oké, dus ik vraag me af vanuit het oogpunt van de klant, hoe vind je toepassingen die goed passen bij wat je doet? Heeft u klanten die naar u toe komen die een aantal opties hebben uitgeput en het gevoel hebben dat ze ten einde raad zijn en hopen dat u hun probleem kunt oplossen of bent u actief op zoek naar toepassingen die een past goed? En misschien is het antwoord beide.
EE: Ja, het zijn veel meer klanten die naar composieten kijken, voor veel van onze klanten vervangen we metaal. Weet je, we kijken zeker naar, je weet wel, toepassingen, of we kunnen composieten vervangen. En daar hebben we enkele, enkele voorbeelden van. Maar echt, dit is de grotere groep klanten die metaal vervangt. Dus ze maken wat ze maken op basis van wat ze hebben. Dus, weet je, er zijn al die ontwerpregels voor productie, die verantwoordelijk zijn voor de erfenis van productiemethoden die iedereen gebruikt voor hun product. Dus we werken met, weet je, veel Fortune 100-bedrijven die zeer geavanceerde verfijnde manieren hebben om te maken wat ze maken met bestaande metaalvormingstechnologieën, en het is zeer verfijnd en verfijnd. We introduceren de mogelijkheid om de composieten te gebruiken, vormen te kunnen bereiken en in productiesnelheden die niet zijn geassocieerd met composieten toen ze het in het verleden hebben onderzocht, wat dit het soort leuke gesprek opent, dat is , je weet wel, waar te beginnen. Dus we hebben veel meer, waar-moeten-we-gesprekken beginnen dan dat we doen, dit is mijn probleem dat op unieke wijze kan worden opgelost door jullie gesprekken. En degenen naar wie die gesprekken moesten beginnen, kijken vaak, waar kunnen we een aanzienlijk concurrentievoordeel ontsluiten op basis van dit product? Weet je, wat, welke functionele vereisten? Moet het kleiner? We willen er een andere vorm van maken, weet je, zijn het antennevensters of, weet je, een soort van ingebouwde elektronica of thermische oplossingen of gewoon, je weet wel, puur een sterkte-ding? En dan, en dan, weet je, wat is de waarde daarvan, in termen van dat product voor de klant. En dan proberen we meestal iets te vinden dat de naald echt beweegt, op de wenselijkheid voor hun eindklanten.
JS: U noemde zojuist een paar toepassingen en elektronica, u had het ook in het algemeen over auto's en ruimtevaart. Ik vraag me af of u ons enkele algemene voorbeelden kunt geven van toepassingen in de automobielindustrie of ruimtevaart waarbij dit proces goed past.
EE: Natuurlijk, dus in de auto- en ruimtevaart zijn er veel structurele beugels die complexer van aard zijn, en die niet zoveel composietinnovatie hebben gezien als veel van de, weet je, grotere, plattere 2D, 2,5 D-vormen. Dus 3D-printen met metaal heeft bijvoorbeeld enkele van de voor topologie geoptimaliseerde haakjes en vormen die met deze methoden kunnen worden vervaardigd, echt populair gemaakt. En ik denk dat de 3D-printruimte ook heeft bijgedragen aan de ontwikkeling van een aantal geweldige software om het ontwerp aan de kant van de klant, ook aan de OEM-kant, in staat te stellen applicaties echt in eigen handen te nemen. Veel van die structurele beugels hebben dus echt de ideale vorm. En ons vermogen om vezels uit te lijnen door die 3D-structuur die langs de laadpaden van het onderdeel loopt, heeft aanzienlijk gewicht bespaard ten opzichte van het 3D-printen van metaal en is zeer kostenconcurrerend. En weet je, die waren ergens tussen de 50 en 80%, gewichtsbesparingen en sommige van die toepassingen over het 3D-geprinte metaal. Dus de, weet je, hoewel lucht- en ruimtevaart een opwindende plek is om hierover te praten, omdat er daar zoveel aandacht is geweest, is het voor ons opwindend de mogelijkheid om de lagere kostendrempels te bereiken die vereist zijn voor auto's, maar ze zouden kunnen profiteren van al deze dezelfde topologie-geoptimaliseerde benaderingen van sommige van de structuren die ze maken. En met name de automobielindustrie is een plaats waar veel gestempelde stukken zijn die via assemblages tot complexe vormen worden samengevoegd. Elk van die onderdelen is erg goedkoop. Maar als je naar die totale assemblage kijkt en alles aan elkaar smeedt, is dat waar het heel interessant begint te worden en waar de meer geïntegreerde benadering van de productarchitectuur erg interessant wordt. En automotive bevindt zich ook in een interessante ruimte waar, weet je, het gebruik stijgt. Weet je, modellen veranderen. Uiteraard is er elektrisch en autonoom en verandert er veel in de productarchitectuur. En met het stijgende gebruik, waarbij de auto-industrie een beetje een pad volgt waar de lucht- en ruimtevaart een pad heeft gevolgd met totale benutting, worden de totale eigendomskosten steeds belangrijker voor sommige van deze voertuigen van de volgende generatie, en zijn ze echt voorstander van deze lichtgewicht architecturen. Dus, zo langdradig antwoord op, op de vraag van aero versus auto, maar weet je, hoe lang en kort het is, er zijn enkele goede drop-in vervangingen. Maar enkele van de meest opwindende dingen waar we naar kijken, zijn over een paar jaar aan de horizon in de auto.
JS: En om duidelijk te zijn, u levert fabricage of diensten van onderdelen en structuren, u verkoopt deze technologie niet echt, klopt dat?
EE: Voor de consumentenproductruimte doen we de productie rechtstreeks. Voor andere industrieën zal ik het echter afzonderlijk hebben, de belangrijkste reden dat we de productie van onderdelen voor consumentenproducten op zich hebben genomen, is de manier waarop deze ruimte nu werkt, zoals u weet, behuizingsstructuren. Onze klanten willen deze laten afleveren bij een fabriek voor eindmontage. En we hebben de productiecapaciteit om aan die eisen te voldoen. Voor de meer gereguleerde productie-industrieën hebben we verschillende productiepartners waarmee we hebben gesproken over het online brengen van bronnen in het tijdsbestek van 2022. Maar we doen al het proof-of-concept werk met die klanten vandaag buiten onze faciliteit, oké.
JS: Je gooit datums weg die een paar jaar in de toekomst liggen, ik neem aan dat dit betekent dat je een stabiele financiering hebt om je door deze liquidatieperiode te helpen, denk ik.
EE: Voor consumentenproducten verzenden we vandaag productie-onderdelen. Dus, terwijl de meer gereguleerde industrieën, de verschillende kwalificatiehindernissen die daar nodig zijn, doorlopen en de productie opschalen op basis van de vereisten van de productieomgeving, dat een iets langere termijn inspanning is. Maar we hebben een zeer actieve NPI-faciliteit hier in Californië, waar we samenwerken met klanten. We zijn op dit moment echt een beetje een ontwerp- en productiebedrijf waar we heel nauw met hen samenwerken om te profiteren van wat mogelijk is. We hebben geavanceerde simulatiemogelijkheden in huis om onze klanten te helpen de functionele vereisten die ze hebben echt te realiseren. En hoewel er veel NPI-werk gaande is, verzenden we productieonderdelen naar klanten die in hun producten worden ingebouwd en op dit moment naar hun eindklanten worden verzonden. We hebben dus een goede relatie met ons durfkapitaalbedrijf, maar we zijn ook goed op weg naar winstgevendheid.
JS: U noemde NPI. Waar staat dat voor?
EE: Oh, nieuwe productintroductie. Dus op het gebied van consumentenproducten is het vrij gebruikelijk om een snellere productiefaciliteit te hebben, een faciliteit voor de introductie van nieuwe producten, waar u snel kunt inspelen op de eisen van de klant en aan de eisen van de klant kunt voldoen. echt efficiënt in productie.
JS: Ik wil een beetje terug in de tijd. Ik weet dat u eerder bij Arevo heeft gewerkt, dat eveneens in Californië is gevestigd, en een van de initiatiefnemers is van het gebruik van continue vezels in additive manufacturing. Ik vraag me af wat je werk bij Arevo was, en hoe kwam dat tot uiting in wat je een Arris hebt gedaan, of deed?
EE: Ja, ja, zeker. Het was. Het was erg vormend. Ik ontmoette de mede-oprichters van Arevo, Hemant, Wiener, Kunal en Riley in 2014, toen het echt het toppunt was van de 3D-printaandelen en waarschijnlijk de overijverige verwachtingen, en het was ook toen er veel nadruk lag op 3D-printen van metaal, en de manier waarop Arevo, die ze eigenlijk net hadden genoemd op basis van de uitdrukking 'een revolutie', was op zoek naar uitgelijnde vezels en dat te combineren met 3D-printen en alle voordelen van 3D-printen, om te profiteren van wat iedereen die naar zoiets zou luisteren, weet dat de composieten behoorlijk verbazingwekkend zijn. En als je alle voordelen van 3D-printen en de voordelen van composieten hebt, is het een opwindend vooruitzicht, plus de echte focus op de zeer hoogwaardige ruimte die de mogelijkheden vergroot. Dus ja, ik bedoel, het was in die begindagen erg spannend om met dat team te werken. Ik heb daar veel van de applicatie-ontwikkeling gedaan en veel van de samenwerkingen met klanten gedaan. En ik denk dat die tijd mijn overtuiging over de mogelijkheid van deze materialen echt heeft versterkt. En uiteindelijk, toen we aan het verhaal begonnen, ben ik echt met Arris op pad gegaan om te kijken hoe we ze voor iedereen toegankelijk kunnen maken, hoe, hoe kunnen we profiteren van de zeer efficiënte productiemethoden voor grote volumes, maar die op één lijn krijgen vezelmogelijkheden in een productiemethode, zodat deze materialen echt breed kunnen worden toegepast?
JS: Oké, Ethan, ik weet dat je een van de oprichters van Arris was, maar je bent niet de enige oprichter en dat je met anderen hebt samengewerkt om het bedrijf op te richten. Ik vraag me af of je me iets zou kunnen vertellen over met wie je hebt samengewerkt om het bedrijf te starten en wat je motiveerde.
EE: Zeker wel. Eric Davidson en Riley Reese waren dus kritisch bij de oprichting van het bedrijf en gaan nog bijna vier jaar door. Dus Riley, die door de jaren heen altijd met hem had samengewerkt, was de persoon waarvan ik wist dat hij de materialen en de materiaaleigenschappen en het composietkarakter van de onderdelen die ik maakte zou valideren. Dus hij was de eerste persoon die ik benaderde om dat te onderzoeken, om dat te valideren, om door te denken, na te denken over het pad naar schaalvergroting. En Eric, ik heb elkaar medio 2017 eigenlijk via een wederzijdse kennis leren kennen. En Eric had een zeer unieke achtergrond in die zeer sterke mechanische, maar had ook de composietmaterialen, en zijn vermogen om veel van de benchtop-tests te doen en de precisiemechanismen te ontwikkelen om R&D-labwerk mogelijk te maken, tot echt de nauwkeurigheid en het precisieniveau dat is nodig om uitstekende onderdelen te maken. En doe het echt in zijn eentje - iemand die net zo comfortabel achter een computer zit als achter de CNC-machine, maakte hem echt een ongelooflijk lid van het team bij het opschalen van de vroege ontwikkeling naar een robuuste methode die we vervolgens gingen gebruiken om schaal in de komende jaren.
JS: Ik wil nog verder terug in de tijd. Het viel me op dat je halverwege de jaren 90 afstudeerde aan de Universiteit van Vermont met een graad in geologie. En het is, ik denk dat het redelijk is om te zeggen dat dit geen typische opleiding is voor een composietingenieur. Hoewel het misschien typischer is dan we ons realiseren. We vragen ons af hoe je van dat punt tot dit punt bent gekomen en in de eerste plaats in composieten bent terechtgekomen?
EE: Ja, ik denk dat het de moeite waard is om snel uit te weiden dat het misschien een typische achtergrond is, omdat we meer composietingenieurs nodig hebben. Als je hiernaar luistert en probeert te beslissen wat je academisch moet doen om wat mechanische ervaring op te doen in composietmaterialen, zal er veel werk voor je zijn. Maar dat terzijde ja. Geologie is eigenlijk best grappig. Ik begon in de techniek en nam mijn wetenschappelijke vereisten. En echt de wetenschap, de wetenschappelijke methode, is een soort van wat me weghield van engineering. En composieten zijn, denk ik, achteraf gezien niet erg verschillend van composieten. Dus ik kan niet zeggen dat er goddelijke inspiratie was. Je weet wel, het weefsel van de aarde, de standaardwaarden, de voortplantingspunten van het falen, de laminering, de delaminatie. Het is een beetje komisch vergelijkbaar. Maar ja, ik denk dat het een beetje een omslachtig pad is, maar de wetenschap heeft me echt naar de R&D geleid, dat is wat ik echt leuk vond in de ruimte voor applicatieontwikkeling waar ik veel aan biz-ontwikkeling en applicatieontwikkeling heb gewerkt. En ik denk dat wat me misschien een beetje van de traditionele techniek heeft verwijderd, een deel van de creativiteit in de wetenschappen was, en, weet je, ik denk dat beide ongelooflijk belangrijk zijn. Het is duidelijk dat we mensen nodig hebben die processen verfijnen, maar we hebben ook de creativiteit nodig om te bedenken hoe je nieuwe methoden kunt gebruiken in, in de verschillende, weet je, productruimten die doorgaans alleen maar stapsgewijs vorderen. En met technische creatievelingen zijn technische incrementalisten allemaal zeer, zeer gezonde gebieden. En ja, ik denk dat het een beetje onderstreept dat, weet je, je tegenwoordig dingen over onderwijs hoort waar veel mensen niet zullen doen wat ze deden op school, ik denk dat ik daar een redelijk goed voorbeeld van ben.
JS: Waar of hoe werd u voor het eerst blootgesteld aan composietmaterialen en fabricage?
EE: Dus ik werd voor het eerst blootgesteld in de late jaren 80. Mijn eerste baan was werken bij een Gespecialiseerde fietsenwinkel. En we waren een wederverkoper, en ik herinner me dat het eerste DuPont driespaaks wiel binnenkwam. En het eerste metalen matrixframe dat het was, weet je, Specialized had dit innoveren of sterven. En dit, dit was een soort renaissance van, ze hadden in die tijd een aantal hele leuke innovaties. Zodat die ervaring in de fietsenwinkel is wat me ertoe bracht mijn opleiding in techniek te starten. Ik kwam pas terug op composieten toen ik aan een R&D-project werkte in waarschijnlijk rond 2012, waar ik werkte aan een eerste ontwikkeling van een composietcomponent voor wat een groot iconisch consumentenproduct werd dat me echt aanzette tot de mogelijkheden van hoe belangrijk een heel klein stukje materiaal kan zijn voor een product. Dat was, denk ik, een paar jaar voordat ik Arevo ontdekte en in Arevo heb ik dat echt uitgebreid en heb ik behoorlijk wat geleerd over de uitgelijnde uitgelijnde composieten en uitgelijnde continue composieten.
JS: En ik neem aan dat je ons niet kunt vertellen wat dat grote iconische consumentenproduct was.
EE: Juist.
JS: Niet verrast. Ik wil het nog even hebben over additive manufacturing. En ik weet dat wat je nu doet een beetje buiten wat wij, wat de wereld doorgaans beschouwt als additieve productie, ligt, maar ik denk dat je er nog steeds tegen kunt praten. Het landschap van additieve productie is volgens mij behoorlijk breed en gevarieerd in termen van materialen, en vooral als je begint te praten over discontinue of continue vezels. Ik vraag me af wat uw huidige beoordeling is van het landschap van additive manufacturing en wat ziet u als de grootste kansen en de grootste belemmeringen?
EE: Dus ik denk dat ik me een beetje zal concentreren op composieten en daarin. Ik denk dat als je daar naar kijkt, en metalen en kunststoffen zijn zo'n verschillende ruimtes, en ik denk dat het de moeite waard is om even te pauzeren dat naarmate deze technologieën volwassen worden, er verschillende gereedschappen zijn voor verschillende taken. En ik denk dat iedereen dit begint in te zien. En misschien een beetje meer rationele verwachtingen van waar een tool voor zou kunnen worden gebruikt. Als we echt naar de composietenruimte kijken, denk ik dat recycleerbaarheid zeker bovenaan de lijst staat, als we dat willen, als we echt breed worden toegepast, moet hier een verstandige energiestroom aan worden gedacht van de, je weet wel, alles van de chemie tot de verwerking van het materiaal dat de economie daadwerkelijk beïnvloedt en of je zelfs kunt worden gebruikt om mee te beginnen, tot het einde van het leven en, en dan natuurlijk, recyclebaarheid. Weet je, deze hele cyclus is de reden waarom veel van de andere, meer efficiënte, volwassen legacy-technologieën bestaan en het gat hebben dat ze industrieën willen, omdat het niet alleen het winnen van een applicatie is, maar de totale levenscyclus. Ik denk dat een van de andere grote namen waar we het over hadden, het onderwijsstuk is. Om industrieën vooruit te helpen bij het adopteren van nieuwe dingen die je nodig hebt, heb je slimme mensen nodig met een goede opleiding en een goede achtergrond. En de juiste tools om de juiste dingen op de juiste plek te gebruiken. Dus ik denk dat ik denk dat dit de twee grootste uitdagingen zijn die ik zie.
JS: U noemde recycling, ik vraag me af, hoort u specifiek van uw klanten over de noodzaak om te worden gerecycled? Of recycleerbaarheid? Hoe erg is dat voor de mensen met wie u werkt en dient?
EE: Hoe groter, hoe groter de toepassing, des te belangrijker wordt de totale totale energiebeoordeling als de algemene economie van de hele levenscyclus. Hoe kleiner de aanvraag, hoe minder conversatie misschien, als we maar generaliseren. Maar veel van onze klanten werken zeer actief met ons en de materiaalbedrijven samen om verbetering op al deze gebieden te stimuleren. Er is op dit moment een heel gezonde vraag van het publiek. En ik denk dat er, weet je, het onderzoek is dat, weet je, veel van deze dingen kosteneffectief kunt doen, en met name rond harssystemen, waar veel van hen de prestaties aanzienlijk verbeteren, met schonere chemicaliën. Ze geven aan dat we op de goede weg zijn. Het is duidelijk dat de snelheid waarmee deze kunnen worden opgepikt echt van veel dingen afhangt, zoals, weet je, is het een zeer veeleisende industriële toepassing of ruimtevaart? Weet je, versus is het iemands mobiele telefoon? Rechts. Dus er is, er is, er is veel, veel spel in de, in dat in die beslissingen. Maar ik denk dat het algemene gevoel van consumentenproducten is dat ze echt snel in die richting proberen te gaan.
JS: U noemde onderwijs. We maakten er iets eerder grapjes over. Maar ik zou hier graag op terugkomen. Ik heb begrepen - en dit is de afgelopen jaren zo geweest - dat de hogescholen, zoals je weet, universiteiten, misschien zelfs wereldwijd, niet genoeg ingenieurs produceren die bekend zijn met composietmaterialen en -processen. Ik weet zeker dat dat aan het veranderen is - ik weet dat dat aan het veranderen is - maar er is nog steeds een grote vraag binnen de industrie naar goed opgeleide ingenieurs die de materialen en processen begrijpen, maar als dat al zo is, als dat niet altijd mogelijk is. I'm wondering what kind of traits you look for in an engineer. Aside from the, you know, sort of the nuts and bolts of engineering, I'm wondering what kind of traits you find are most helpful or beneficial in a composites manufacturing environment that that maybe aren't as sought after or as needed and other disciplines if there is in fact a difference?
EE: You know, there are such different roles in a in, in, you know, I just look at one end of the company to the other and the roles can differ so much that, you know, you need the very different personalities that might come with any specific discipline. You know, we need the very incremental methodic process developer that has, you know, really been, you know, some of the most important personalities in qualifying many of the critical applications that composites are used for today. You know, we also need some of the, you know creatives that have been attracted more to the newest flashiest things that come along to do the 3D-printed and new product architectures. And, and while you do need those, kind of, if I'm trying to stereotype two ends of the spectrum, you also need these technical program managers that have some some really solid technical backgrounds, whether it's mechanical engineering or material science, but also have a high degree of organizational sensibility. Making any change is, is maybe 80% people 20% technical. So, you know, we work with some amazing intrapreneurs, within big companies that, you know, we'd be lost without, without those really, really excellent communicators that have great technical backgrounds. Ultimately, if there is kind of one common thread, really just being able to effectively communicate, you know, wherever you fall on that spectrum, with the rest of that spectrum, is kind of one of the most common denominators among them all, though.
JS: And when you say effective communication, what does that mean to you?
EE: Yeah, that that's, that's a good question. You know, communications is, I've heard a definition that I won't do quite right that I like, it's 'communication is the meaning that the person receives.' I guess I would define it that way. However, you can use words or documents, or Slack, or email, or text, whatever it takes, if you can get the person that you're trying to get a message across to the meaning that is going to enable them to take what you have learned and build on it, then you're a great communicator.
JS: So taking what's in your head and your ideas and putting them in a format that allows other people to readily accept it and adapt it.
EE: Yeah, making information actionable. That's one of the one of the big ones. There's, you know, it's the classic challenge of big company innovation, you know, there's so much great information in so many places, and if there's only somebody that could put those pieces together, there's lots of innovation that could occur. So, you know, the classic idea that I think that we think of when we think of communication might be closest to that project manager or program manager that I was talking about, who can pull everyone into a room and, you know, extract the best out of each individual and synthesize it all and, and lead the conversation and come out with some, some real kernels of value in this, this mastermind. But but I think it's, it's a lot more than that, you know, it's each one of the people around the table, that can take whatever it is that they have unique insights into based on their experience, or, or discipline and, and encapsulate that and that is as simple away as possible for the rest of the room to do you know, have an aha moment and understand how that might color their perceptions of everything else that they're working on.
JS: So that leads me to my next question. As you look over the next few years, how do you hope and expect that Arris will evolve and grow and what are your what are your goals and aspirations for the company?
EE: So we have really a focus on helping the customers that we're working with make these these previously unimaginable products. And our focus is helping them get big wins in their markets. We're very customer-centric in that respect, you know, their wins are our wins. So, as a result, we have a kind of daunting production pipeline that has a really a significant amount of scaling of our production capabilities that we're working on in the coming few years. So what we're really focused on is helping the customers get these products to market. Beyond that, though, the, you know, the new product architectures I think, are where the most exciting possibilities are for us. We talked about part consolidation, you know, the ability to put different materials into a single part and achieve not just shapes but part performance, it wasn't possible because you have this continuous fiber backbone, but you might have, you know, metal or ceramic or other materials that enable functionality that's, you know, typically beyond beyond composites. These areas, these products that typically aren't thought of as composite components or something consistent with a composite application is really when we look ahead is looking at ourselves as less of just a composite-specific company, but more of a product manufacturing platform that really can achieve the functions that a customer product requires. Just putting the best material in the best place with the continuous fiber composites just as the ideal backbone to hold it all together.
JS: You mentioned earlier, additional facilities and locations, what's your thinking there?
EE: So, our customers assemble their products in different places. So, we need to be able to deliver products based on their supply chain requirements. So that for for aerospace and consumer electronics and automotive looks very different. So we're working closely with our customers to make sure that we are consistent with their supply chain requirements and what's practical for high volume production.
JS: Ethan, I want to talk briefly about a paper that Arris presented at CAMX 2020, which occurred recently. This is of course, the virtual CAMX this year. The paper's title is 'The convergence of composites and topology optimization ushering in the next era of aircraft lightweight structures.' And I'll will post this paper with this interview so that our listeners can access it. But the paper basically describes work that Arris did with Northrop Grumman to take a metallic bracket and redesign it and optimize it for manufacture using the Arris Additive Molding process. And I'm wondering what you see as the implications for this and what it might mean for arrows going forward?
EE: Sure, so in the paper, we're equaling the stiffness of the 3D printed titanium at an 80% weight savings. And as I'm sure many listeners know, in any aircraft, you might have hundreds of brackets. So reducing this much weight really speaks to the ability to put these continuous composites into complex shapes. And this really clearly illustrates where the commercial value exists for aircraft manufacturers and owners. Obviously, as we we talked about earlier as well, brackets are not unique to aerospace, just the value of weight savings is is so extremely high in aerospace. It's where a lot of the innovation in a lot of shapes has started. So it is also quite exciting how that can be applied to all kinds of other structures and vehicles where energy efficiency would be beneficial by reducing weight.
JS: All right, Ethan, just a quick follow up to that. Do you expect this particular bracket that you developed with Northrop Grumman to to come to market and to be commercialized? Or is this just a demonstrate capability of your technology for the marketplace?
EE: Sure, well, I can't speak specifically to the Northrop Grumman bracket, brackets in general are a major application for us as our really new ability to run continuous column composites through complex 3D shapes really enables many of these bracket designs that have been pioneered by the 3D printing and metal 3D printing industry and using these higher stiffness-to-weight ratio materials that save weight in aerospace. And then using a scalable molding technology enables us to not only save weight in aerospace but also scale them for for use in automotive and other applications where there's more cost sensitivity.
JS: Alright, Ethan. Well, it's it's an interesting story and obviously a lot, a lot more to be told. So I wish you luck with Arris and hope that all goes well for you over the next few years. And I appreciate you speaking with me today here on CW talks.
EE: Yeah, my My pleasure. Great to great to connect, Jeff.
JS: Again, many thanks to my guest today Ethan Escowitz, co-founder and CEO of Arris composites. If you want to find out more about Arris, please visit arriscomposites.com. That's a-r-r-i-s-composites.com.
vezel
- Top 10 ontwikkelingen op het gebied van composietproductietechnologie
- Toen en nu:een korte geschiedenis van composietmaterialen
- Waar u op moet letten bij fabrikanten van composieten
- Composite fabricage:de fabricage van composietmaterialen
- Thermoplastische composieten bij Oribi Composites:CW Trending, aflevering 4
- Vraag en antwoord met Ethan Escowitz, CEO, Arris Composites
- Aflevering 34:Carmelo Lo Faro, Solvay Composite Materials
- Hoogwaardige composieten in Israël
- Aflevering 26:Achim Fischereder, Hexcel
- Nationale Composites Week:Duurzaamheid
- Nèos International vestigt nieuw hoofdkantoor, composietenfaciliteit in het VK