Op maat gemaakte metalen gietstukken specificeren en bestellen:een gids
9 belangrijke overwegingen om het succes van uw op maat gemaakte metaalgietprojecten te garanderen
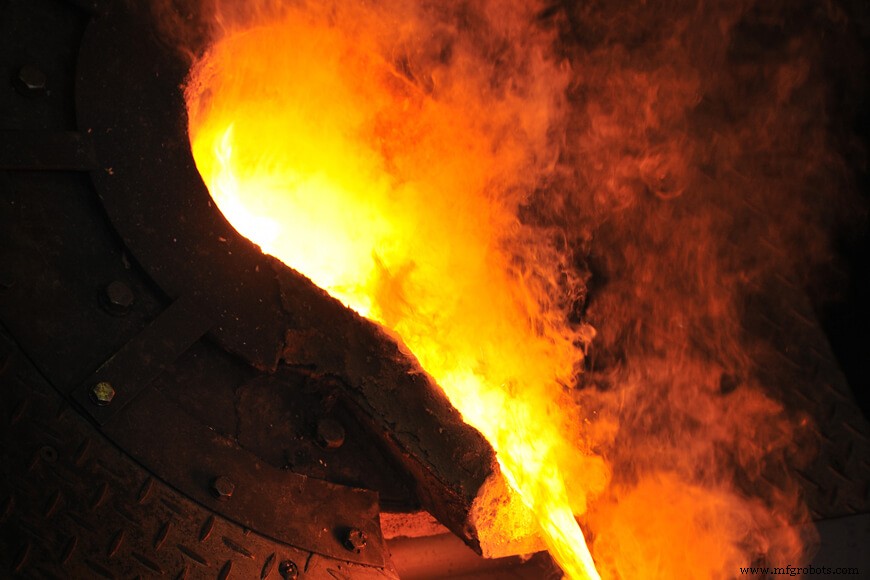
Metaalgieten is een proces waarbij vormen (gietstukken) worden geproduceerd door holtes in mallen te vullen met vloeibaar metaal. Producten van gegoten metaal bieden uitzonderlijke sterkte en duurzaamheid, waardoor ze nuttig zijn voor zware machinetoepassingen in industrieën die verband houden met landbouw, auto's, spoorwegen, huishoudelijke apparaten, bouwarchitectuur, scheepsbouw, olie- en gaswinning, waterverwerking, bosbouw en mijnbouw, om maar een weinig.
Het kwalificeren van een gieterij van een leverancier en het bestellen van metalen gietstukken kan een tijdrovende beproeving zijn, maar dat hoeft niet zo te zijn. Kostbare blunders kunnen worden voorkomen door inzicht te krijgen in het offerte- en castingproces. Duidelijke en gedegen communicatie met de leverancier gieterij zal resulteren in een goed ontworpen en economisch eindproduct.
Een offerte aanvragen
Het doel van het aanvragen van een offerte voor een gietstuk is om de optimale balans te vinden tussen ingekochte gietkosten, kwaliteit en levertijd. Hoewel het verleidelijk kan zijn om automatisch de laagste prijs te selecteren, kan dit leiden tot vertraagde levering of een gietstuk van mindere kwaliteit, die beide op de lange termijn duurder kunnen zijn.
Een slimme klant moet alle bepalingen van de ontvangen offerte afwegen, inclusief gereedschapsvereisten, toleranties en afwerkingstoeslagen, evenals eventuele uitzonderingen op tekeningen, specificaties en verwerkingsvereisten. Andere factoren, zoals minder machinewerk, verbeterde leveringsvoorwaarden en gieterijervaring en betrouwbaarheid van leveranciers, zijn bijzonder belangrijk om de werkelijke kosten versus waarde van het gietstuk te bepalen.
Er zijn ten minste negen belangrijke overwegingen waarmee rekening moet worden gehouden bij het aanvragen van prijzen voor metaalgieten bij een leveranciersgieterij:
- Voorlopig castingontwerp
- Aantal
- Specificaties
- Deugd
- Testen en inspectie
- Gewicht
- Patronen
- Bewerking
- Productie- en leveringsschema's
1. Voorlopig gietontwerp
Een gegoten metalen onderdeel moet zo zijn ontworpen dat het volledig kan profiteren van het gietproces. Voor een efficiënte en kostengevoelige productie moet het gietontwerp kiezen voor de eenvoudigste productiemethoden die zullen resulteren in de gewenste fysieke eigenschappen, eisen aan de netvorm en cosmetisch uiterlijk.
Bij elke offerteaanvraag moeten tekeningen worden gevoegd met de exacte afmetingen van het vereiste onderdeel.
Er zijn verschillende belangrijke componenten van ontwerp waarbij inzicht in gieterijprocessen en/of communicatie met leveranciersgieterijen helpt bij het bepalen van de meest kosteneffectieve ontwerpen vanuit het oogpunt van een gieterij.
Minimale coupedikte
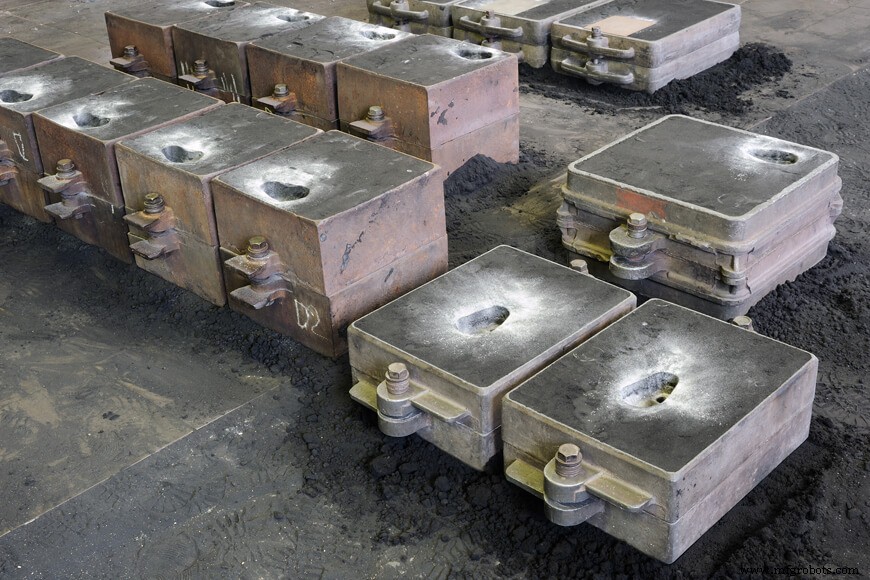
Elk gietstuk heeft een minimale dikte die wordt bepaald door zijn sterkte en stijfheid. Ontwerpen die dunner zijn dan de specificaties kunnen het project niet-castable maken. Om succesvol te zijn, moet het ontwerp van een gietstuk ervoor zorgen dat vloeibaar metaal de mal in de dunnere delen kan vullen.
Vloeibaar (gesmolten) metaal koelt uitzonderlijk snel af. Het kan te snel afkoelen om dunne delen binnen te gaan die ver weg zijn van de poort van de mal. In de regel mogen ontwerpen geen gebieden hebben die dunner zijn dan 0,25 in (6 mm) wanneer conventionele processen worden gebruikt. Investeringsgieten zorgt voor een grotere mate van vrijheid en de wanddikte kan dalen tot 0,030 in (0,76 mm).
Concept en kern
De term "concept" verwijst naar de tapsheid op de verticale vlakken van een patroon. Er is een trek nodig om het patroon uit de mal te halen zonder de malwanden te verstoren. Als u de beperkingen van deze hoeken negeert, zal de mal scheuren wanneer deze uit het gietstuk wordt verwijderd.
Verschillende factoren zijn van invloed op hoeveel diepgang nodig is voor elk gietstuk:het productieproces, de gietgrootte en of het gieten met de hand of machinaal wordt uitgevoerd, zullen allemaal de vereiste mate van diepgang veranderen. Voor machinaal gegoten gietstukken is minder diepgang nodig. Gietstukken geproduceerd met groene zandvormen hebben echter meer trek nodig dan normaal. De algemene vuistregel is om 3/16 inch diepgang per ft toe te staan (ongeveer 1,5 graden).
Een kern is een holle ruimte die in een gietstuk wordt gecreëerd door een stuk vormzand. Kernen zijn nodig wanneer de ruimtes of holtes niet alleen met het patroon kunnen worden gemaakt. Het gebruik van kernen kan de noodzaak van tocht elimineren, maar het gebruik ervan moet worden beperkt omdat ze de kosten van het gieten verhogen.
Drie factoren beïnvloeden de minimale diameter van een kern die in een gietstuk kan worden geplaatst:
- De dikte of diepte van het gebied waarin de kern wordt geplaatst,
- Hoe lang de kern is, en
- De gietmethode die de leveranciergieterij zal gebruiken.
Scheidingslijn
Afsteken in één vlak vergemakkelijkt de productie van patronen en de productie van de mal. Patronen met rechte scheidingslijnen (met scheidingslijnen in één vlak) kunnen gemakkelijker en tegen lagere kosten worden geproduceerd dan patronen met onregelmatige scheidingslijnen. Gietvormen die symmetrisch zijn, suggereren gemakkelijk de scheidingslijn. Een dergelijk gietontwerp vereenvoudigt het vormen en uitboren en moet waar mogelijk worden gebruikt. Ze moeten altijd worden gemaakt als "gespleten patronen" (gescheiden kop en slepen) die een minimum aan handwerk in de mal vereisen, de gietafwerking verbeteren en de kosten verlagen.
Kern
Een kern is een apart stuk (vaak gemaakt van vormzand) dat in de mal wordt geplaatst om openingen en holtes te creëren die niet alleen door het patroon kunnen worden gemaakt. Om de uiteindelijke kosten van het gieten te verlagen, moet het ontwerp alles in het werk stellen om het aantal benodigde kernen te elimineren of te verminderen.
De minimale diameter van een kern die met succes kan worden gebruikt in stalen gietstukken is afhankelijk van drie factoren:
De dikte van het metalen gedeelte rond de kern,
De lengte van de kern, en
De speciale voorzorgsmaatregelen en procedures die worden gebruikt door de gieterij van de leverancier.
De ongunstige thermische omstandigheden waaraan de kern wordt blootgesteld, nemen in hevigheid toe naarmate de metaaldikte die de kern omgeeft toeneemt en de kerndiameter afneemt. Deze toenemende hoeveelheden warmte van het zware gedeelte moeten via de kern worden afgevoerd. Naarmate de thermische omstandigheden toenemen, wordt het reinigen van de gietstukken en het verwijderen van de kern veel moeilijker en duurder.
De dikte van het metalen gedeelte dat de kern omringt, en de lengte van de kern, beïnvloeden beide de buigspanningen die in de kern worden geïnduceerd door opwaartse krachten en daarmee het vermogen van de gieterij van de leverancier om de vereiste toleranties te verkrijgen. Als de grootte van de kern groot genoeg is, kunnen vaak staven worden gebruikt om de kern te versterken. Naarmate de metaaldikte en de kernlengte toenemen, neemt natuurlijk ook de hoeveelheid wapening toe die nodig is om weerstand te bieden aan de buigspanningen. Daarom moet de kern met een minimale diameter ook groter worden om de extra versterking op te vangen.
De kosten voor het verwijderen van kernen uit gietholten kunnen onbetaalbaar worden wanneer de te reinigen gebieden ontoegankelijk zijn. Het gietontwerp moet voorzien in openingen die voldoende groot zijn om het verwijderen van de kern mogelijk te maken.
Minder toegankelijke plaatsen in het gietstuk maken het verwijderen van kernen moeilijker en tasten de economische haalbaarheid van de projecten aan. Gietstukken moeten altijd worden ontworpen met openingen die groot genoeg zijn om de kernen te kunnen verwijderen.
Gietstukken worden normaal gesproken geleverd met onbewerkte, als gegoten oppervlakken, tenzij anders aangegeven. Om te profiteren van het gietproces, moet de gieterij van de leverancier weten welke oppervlakken uiteindelijk moeten worden bewerkt (zie "8. Bewerking" hieronder voor meer details) en waar referentiepunten zich bevinden. De aanvaardbare maattoleranties moeten worden aangegeven bij het aanleveren van een tekening. Toleranties worden normaal gesproken overeengekomen tussen de leverancier en de klant.
Een nauwe samenwerking tussen de ontwerpingenieurs van de klant en de gieterij van de leverancier is essentieel om het gietontwerp te optimaliseren. Alle gietontwerpen moeten vóór productie worden gecontroleerd door een gieterijprofessional om de haalbaarheid van het gietproject te bepalen.
2. Hoeveelheid
Het aantal te produceren gietstukken of de lengte van de oplage moet duidelijk worden vermeld. De bestelhoeveelheid heeft een aanzienlijke invloed op de prijs, waarbij langere runs overeenkomen met lagere kosten per casting.
De hoeveelheid benodigde onderdelen is geen onbelangrijke overweging; niet alleen bepaalt het projectverbruik van het onderdeel de soorten gereedschap die nodig zijn, maar het bepaalt ook het vermogen van specifieke gieterijen om aan de productievolumebehoeften te voldoen.
Veel gieterijen zijn gespecialiseerd in de productie van korte-termijn-kluswerk, terwijl andere zich richten op de productie van grote volumes. Als u uw behoeften in een vroeg stadium definieert, kunt u ervoor zorgen dat u met de juiste productiefaciliteiten communiceert.
3. Specificaties
Industriestandaardspecificaties bieden de gietklant de tools die nodig zijn om criteria vast te stellen voor bijna elke giettoepassing. Deze specificaties sluiten niet uit dat de technische medewerkers van de klant speciale eisen stellen. Afwijkingen van standaardspecificaties kunnen leiden tot misverstanden, hogere kosten en diskwalificatie van potentiële leveranciersgieterijen. Als een uitzondering wordt gemaakt op een bepaling in de hoofdtekst van een specificatie-eis (in tegenstelling tot het nemen van een uitzondering op een aanvullende eis van een specificatie), kan het resulterende gietstuk niet worden gehouden tot naleving van die specificaties.
De exacte te gieten metaallegering moet worden gespecificeerd met behulp van een internationaal erkende norm zoals ASTM. Gietstukken worden gemaakt van twee categorieën metalen:ferro (op ijzerbasis) en non-ferro (niet op ijzerbasis).
Gegoten staal is het meest voorkomende ferro-gietmetaal, maar er kunnen andere metalen worden gebruikt, afhankelijk van de gewenste fysieke eigenschappen, waaronder roestvrij staal, smeedbaar ijzer en nodulair gietijzer. Aluminium en koper zijn de meest voorkomende non-ferrometalen die worden gebruikt bij het gieten.

Mechanische eigenschappen kunnen worden geverifieerd door het gebruik van teststaven, afzonderlijk gegoten of bevestigd aan de gietstukken. De verkregen mechanische eigenschappen vertegenwoordigen de kwaliteit van het metaal, maar vertegenwoordigen niet noodzakelijk de eigenschappen van de gietstukken zelf, die worden beïnvloed door de stollingsomstandigheden en de afkoelsnelheid tijdens de warmtebehandeling, die op hun beurt worden beïnvloed door de dikte, grootte en vorm van het gieten . Het uithardend vermogen van sommige soorten kan de maximale grootte waarbij de vereiste mechanische eigenschappen worden verkregen, beperken.
Warmtebehandeling
Warmtebehandeling wordt gebruikt om de eigenschappen van specifieke legeringen te standaardiseren, homogeniseren en verbeteren. Voor veel legeringen is warmtebehandeling een routineproces dat wordt gebruikt om ervoor te zorgen dat de gespecificeerde minimale fysieke eigenschappen worden bereikt in de uiteindelijke gegoten producten. Temperatuurregelende apparaten en zelfs geavanceerde temperatuurregistratieapparatuur worden routinematig aangetroffen in moderne warmtebehandelingsovens om consistentie en kwaliteit van warmtebehandelingsstappen te garanderen.
In sommige gevallen kan een gespecialiseerde warmtebehandeling (zoals vlamverharding, uitharding, enz.) worden gespecificeerd als een aanvullend proces dat door de gieterij van de leverancier moet worden uitgevoerd.
4. Degelijkheid
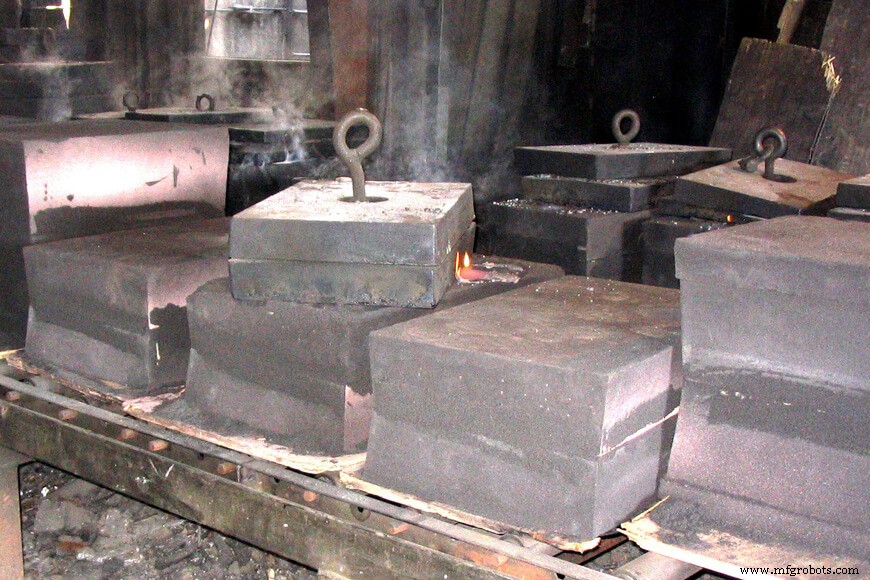
Degelijkheid van metalen componenten verwijst naar de mate van vrijheid van onzuiverheden en/of discontinuïteiten, zoals zandinsluitingen, slakinsluitingen, macroporositeit en krimp. Het is onmogelijk om een gietstuk zonder gebreken te produceren - alleen gietstukken met defecten in verschillende mate. De acceptatie of afwijzing van gietstukken wordt bepaald door onderzoek van onderdelen (in overeenstemming met internationaal erkende normen zoals ASTM) op basis van de formele technische vereisten van de klant; acceptatie- en afkeuringscriteria worden bepaald door een overeenkomst tussen de leveranciergieterij en de klant vóór productie. Deze criteria beïnvloeden zowel de gietkosten als de gebruikte productieprocessen.
5. Testen en inspectie
Na productie moeten alle gietstukken worden getest om er zeker van te zijn dat ze voldoen aan de vereisten van de specificaties. Gietstukken worden ook geïnspecteerd op maatnauwkeurigheid, staat van de oppervlakteafwerking, fysieke eigenschappen, interne degelijkheid en scheuren. In veel toepassingen is testen verplicht; aanvullende tests kunnen nodig zijn om ervoor te zorgen dat aan de materiaalspecificaties of andere algemene vereisten wordt voldaan.
Test- en acceptatiecriteria moeten voorafgaand aan de productie duidelijk worden gecommuniceerd en overeengekomen. Strengere testvoorwaarden zullen de totale kosten verhogen. Om kostenefficiënt te blijven, moeten de test- en acceptatievoorwaarden gebaseerd zijn op de precieze vereisten van elke toepassing.
Er zijn twee soorten tests die worden gebruikt om gietstukken te inspecteren:destructieve tests en niet-destructieve tests.
Destructief testen
Bij destructief onderzoek moet naast het benodigde onderdeel een apart proefgietstuk worden gegoten. Het proefgietstuk wordt vervolgens vernietigd om de interne degelijkheid (volume van insluitsels, krimp of aanwezig gas) visueel te bepalen. Destructief testen vertelt alleen de staat van het geteste stuk en garandeert niet dat andere niet-geteste stukken goed zullen zijn, maar het wordt in de praktijk veel gebruikt. Als het testgietwerk acceptabel is, kan de productie doorgaan in de veronderstelling dat gietstukken die op dezelfde manier zijn geproduceerd, hetzelfde niveau van degelijkheid zullen vertonen.
Niet-destructief testen
Niet-destructieve testmethoden worden toegepast op het gietstuk zelf om de interne en externe deugdelijkheid van het product te verifiëren zonder het product te beschadigen. Methoden omvatten visuele inspectie, dimensionale inspectie, inspectie van vloeibare kleurstofpenetratie (LPI), inspectie van magnetische deeltjes (MPI), ultrasone testen (UT) en radiografische inspectie (röntgenstraling).
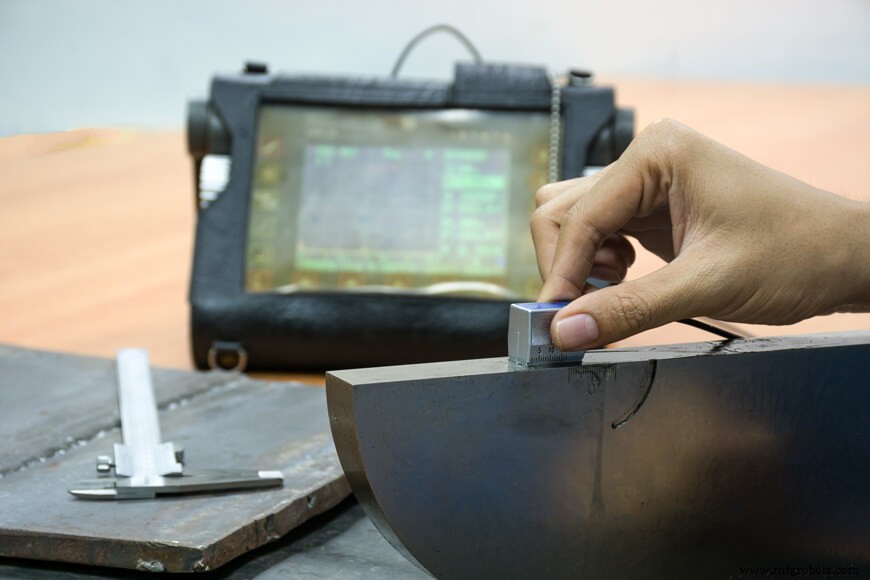
Nadat de inspecties zijn voltooid, worden de geïnspecteerde en geaccepteerde gietstukken soms ongewijzigd gebruikt en naar klanten verzonden, maar vaker worden ze verder verwerkt. Dit kan gespecialiseerde warmtebehandeling, schilderen, roestwerende oliën, andere oppervlaktebehandelingen (zoals thermisch verzinken) en machinale bewerking omvatten.
6. Gewicht
Een belangrijke kostencomponent voor elk gietstuk is materiaal. Hoe hoger het gewicht van het gietstuk, hoe hoger de materiaalkosten voor dat gietstuk zullen zijn. Hoe meer gedetailleerde gewichtsgegevens er aan een gieterij kunnen worden verstrekt over de onderdelen in kwestie, hoe nauwkeuriger en betrouwbaarder de prijsberekeningen kunnen worden gemaakt.
Gieterijen maken zich niet alleen zorgen over het netto (resulterende) gewicht van een gietstuk; ze maken zich vooral zorgen over het brutogewicht van het gietstuk. Het brutogewicht wordt gemeten door het gewicht van het gesmolten metaal dat nodig is om een mal te vullen die bestaat uit het resulterende gietstuk, en al het toevoermateriaal (poorten, stijgbuizen, enz.) dat nodig is om een degelijk gietresultaat van het gietproces te garanderen. De gietprijs van een gieterij wordt aanzienlijk beïnvloed door de gietopbrengst (de efficiëntie van het gietproces en het gewicht van het resulterende gietstuk gedeeld door het gewicht van het voedingsmetaal dat in de mal wordt gegoten) die ze behalen.
7. Patronen
Patronen zijn nodig om mallen te maken, en het maken van patronen is het proces en de handel voor het produceren van patronen. Aangezien patronen de vormen zijn voor de gietstukken, kan het gietstuk niet beter zijn dan de patronen waaruit het is gemaakt. Waar nauwe toleranties of gladde gietafwerkingen gewenst zijn, is het bijzonder belangrijk dat patronen zorgvuldig worden ontworpen, geconstrueerd en afgewerkt.
Het ontwerp van patroonapparatuur en de daaruit voortvloeiende kosten kunnen een grote bron van misverstanden vormen tussen de gieterij van de klant en de leverancier. De noodzaak om nieuwe patroonapparatuur te bouwen die past bij de productiemachines van een gieterij, ook al is er bestaande/oude apparatuur beschikbaar, een vereiste voor een volledig gesplitste kerndoos in plaats van een halve kerndoos, een behoefte om metalen patronen te produceren in plaats van houten patronen , en/of gemonteerde patroonbehoeften in plaats van los patroongebruik zijn slechts enkele van de vele discussiegebieden die van invloed zijn op de kosten van de apparatuur. Steevast komen de laagste gietkosten en de hoogste gietkwaliteit voort uit de meer geavanceerde patroonapparatuur, die de hoogste patroonkosten genereert.
8. Bewerking
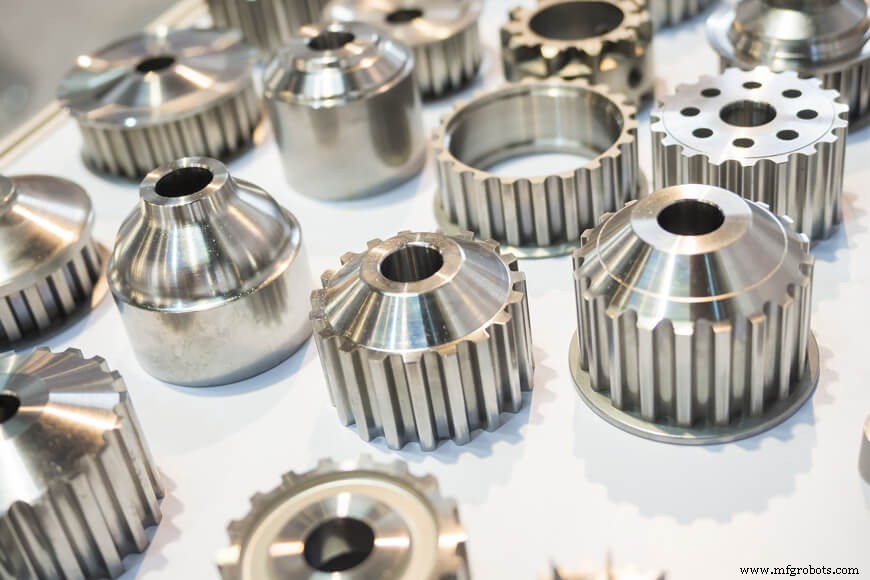
Het mechanisch verwijderen van extra onnodig materiaal wordt machinale bewerking genoemd en is een essentieel proces wanneer een hoge mate van maatnauwkeurigheid vereist is. Als zodanig moet een bepaalde hoeveelheid extra materiaal worden toegewezen voor bewerkingstoegift wanneer dat nodig is, vooral wanneer het gegoten onderdeel of product een nauwe tolerantie heeft.
Tolerantie verwijst naar de maatnauwkeurigheid die haalbaar is voor een bepaalde productiemethode. Vormuitzetting, stollingskrimp en thermische krimp hebben allemaal invloed op de tolerantie van het afgewerkte onderdeel in het groene zandgietproces. Bijgevolg zijn er limieten voor toleranties in een gegoten onderdeel. Daaropvolgende machinale bewerking wordt vaak toegepast wanneer een nauwere tolerantie vereist is.
Niet alle leveranciersgieterijen bieden machinale bewerking in huis, maar zij zijn verantwoordelijk voor het produceren van een gegoten product dat door machinale bewerking kan worden getransformeerd om aan de specifieke vereisten voor het onderdeel te voldoen. Om dit doel te bereiken, moet een nauwe relatie worden onderhouden tussen het engineering- en inkooppersoneel van de klant en de gietproducent. Bij een coöperatieve aanpak moeten de volgende punten in overweging worden genomen:
- Het gietproces, samen met zijn voordelen en beperkingen,
- Toeslag voor machinale bewerking (hoeveelheid materiaal die overblijft voor afwerking na ruw zagen) om opschonen van alle bewerkte oppervlakken te garanderen,
- Productontwerp met betrekking tot het toepassen van de klem- en spaninrichtingen die het onderdeel tijdens de bewerking vastzetten,
- Selectie van materiaalspecificatie en warmtebehandeling, en
- Aantal te produceren onderdelen.
Elk gietontwerp moet bij de eerste productie worden gecontroleerd om te bepalen of alle bewerkingsvereisten haalbaar zijn. Een methode om dit te bereiken is om een volledige lay-out van het gietstuk te maken en te controleren of er voldoende bewerkingsvoorraad is op alle oppervlakken die de bewerkingsprocedure vereisen.
Voor eenvoudiger ontwerpen is een volledige lay-out van het gietstuk misschien niet nodig. Maar in andere gevallen waar de machinale afmetingen ingewikkelder zijn, is het raadzaam het gietstuk grondig te controleren. Dit kan worden gedaan door richtpunten te bedenken en lijnen af te bakenen om alle bewerkte oppervlakken aan te geven, waardoor consistentie in alle productiefasen wordt gegarandeerd.
9. Productie- en leveringsschema's
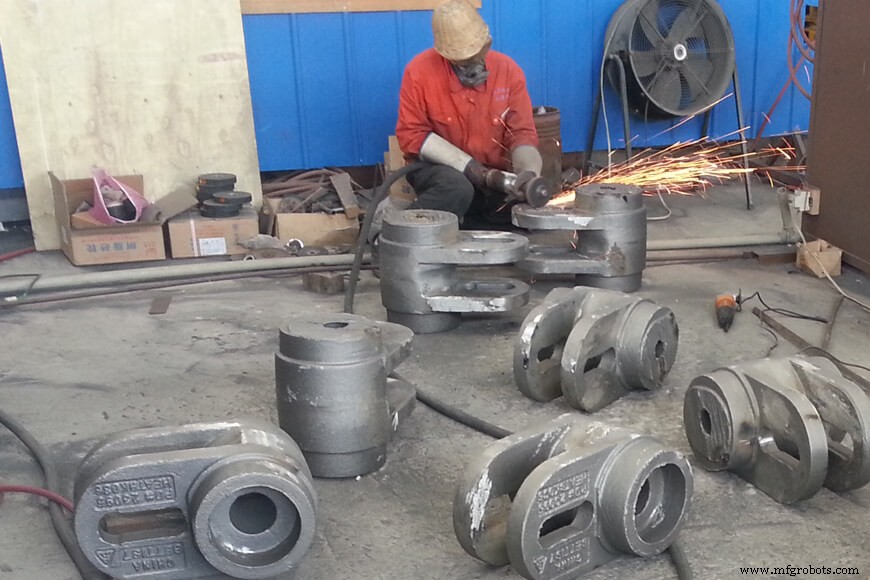
Communicatie over leverings- en vraagvereisten is essentieel om de juiste winkel te vinden die aan zowel de behoeften op korte als op lange termijn voldoet.
Naast alle andere overwegingen hierboven, is het absoluut noodzakelijk dat zowel klanten als leveranciers op de hoogte zijn van de behoeften van het productieschema. Als een klant bijvoorbeeld de levering van productieonderdelen binnen zes weken wil, zou dit het aantal gieterijen dat bereid of in staat is om een prijsopgave te doen voor dergelijk werk aanzienlijk beperken, laat staan dat de productie binnen zo'n strakke tijdlijn betrouwbaar kan worden uitgevoerd. Omgekeerd, als een klant geïnteresseerde gieterijen zoekt om hun gedetailleerde langetermijnbehoeften te beoordelen (bijvoorbeeld 600 stuks per jaar van onderdeel "x", geproduceerd in partijen van 150 stuks per bestelling, met initiële productieruns die niet eerder nodig zijn dan over zes maanden), dan zullen ze veel meer partijen vinden die geïnteresseerd zijn en in staat zijn om aan hun behoeften te voldoen.
Een offerteaanvraag dient ruim voor de gewenste leverdatum te worden gedaan. Vanwege de complexiteit van het metaalgietproces kunnen de doorlooptijden van projecten gemakkelijk oplopen tot 24 weken in de aanloop naar de volledige productie en levering zodra de gietstukken zijn besteld. Deze tijd kan commerciële overwegingen (financiële administratie), patroon- en toolingconstructie, bemonstering, inspecties, patroonwijzigingen, (volledige) productie-opzet, productie, postproductieprocessen en meer omvatten.
Gietstukken bestellen
Een gezamenlijke inspanning is essentieel voor het succesvol uitbesteden van een metaalgietproject - de gieterij van de leverancier moet worden betrokken vanaf de vroege stadia van het ontwerp tot aan de productie en de levering van het product.
Zodra de leveranciergieterij een offerteaanvraag heeft beoordeeld, werken ze samen met klanten om alle kosten te evalueren en productdoelen te bepalen. Een goede planning loont voor zowel de gieterij als de klant, aangezien gieterijexperts het project vóór productie evalueren en de beste materialen en methoden aanbevelen om tot de meest economische oplossing te komen.
Door gieterijen te voorzien van de meest nauwkeurige en gedetailleerde informatie over hun gietbehoeften, kunnen klanten veel feedback, vragen en - zodra de details zijn bevestigd - prijzen van geïnteresseerde partijen verwachten. Een goede voorbereiding stroomlijnt het bestelproces, bespaart tijd en verkleint de kans op productfouten.
Productieproces
- Zandgieten:proces en kenmerken | Industrieën | Metallurgie
- Dunne plaat gieten en rollen
- Wat is metaalgieten? - Definitie, typen en proces
- Definitie, typen en processen van metaalgieten
- Snelmetaalgieten:voordelen en toepassingen
- Precisie gietgids
- Een gids voor plaatwerkmeters en conversies
- Aangepaste legeringen maken van schroot en restanten
- Lintzaagmachine en productiviteit
- Wat is verloren was-metaalgieten?
- 4 veelvoorkomende soorten metaalgietprocessen