17 Hoofdstuk 7:Lean Manufacturing
DOELSTELLING
Na het voltooien van deze unit, zou je in staat moeten zijn om:
- Pas 5S toe in elke machinewerkplaats.
- Beschrijf het Kaizen-concept.
- Beschrijf het implementeren van Lean Manufacturing.
Lean 5S:
"5S" is een methode van werkplekorganisatie die uit vijf woorden bestaat:Sorteren, Op volgorde zetten, Shine, Standardize en Sustain. Al deze woorden beginnen met de letter S. Deze vijf componenten beschrijven hoe u artikelen opslaat en de nieuwe bestelling onderhoudt. Bij het nemen van beslissingen bespreken medewerkers standaardisatie, waardoor het werkproces duidelijk wordt bij de medewerkers. Door dit te doen, voelt elke medewerker zich eigenaar van het proces.
Fase 0:Veiligheid
Vaak wordt aangenomen dat een goed uitgevoerd 5S-programma de veiligheid op de werkplek zal verbeteren, maar dit is onjuist. Veiligheid is geen optie; het is een prioriteit.
Fase 1:Sorteren
Bekijk alle items op de werkplek en bewaar alleen wat nodig is.
Fase 2:rechttrekken
Alles moet een plaats hebben en op zijn plaats zijn. Items moeten worden verdeeld en geëtiketteerd. Alles moet zorgvuldig worden geregeld. Medewerkers hoeven niet steeds te bukken. Plaats apparatuur in de buurt van waar het wordt gebruikt. Deze stap maakt deel uit van de reden waarom lean 5s niet wordt beschouwd als "gestandaardiseerde opschoning".
Fase 3:Glans
Zorg ervoor dat de werkplek schoon en netjes is. Door dit te doen, wordt het gemakkelijker om je bewust te zijn van waar dingen zijn en waar ze zouden moeten zijn. Maak na het werken de werkruimte schoon en zet alles terug op de oude plek. Het schoonhouden van de werkplek moet worden geïntegreerd in de dagelijkse routine.
Fase 4:Standaardiseren
Standaardiseer werkprocedures en maak ze consistent. Elke werknemer moet zich bewust zijn van wat zijn verantwoordelijkheden zijn bij het volgen van de eerste drie stappen.
Fase 5:volhouden
Beoordeel en handhaaf de normen. De bovengenoemde stappen moeten de nieuwe norm worden in gebruik. Ga niet geleidelijk terug naar de oude manieren. Denk bij het deelnemen aan de nieuwe procedure na over manieren om te verbeteren. Bekijk de eerste vier stappen wanneer nieuwe tools of outputvereisten worden gepresenteerd.
Kaizen
Terwijl het lean 5S-proces zich richt op het verwijderen van afval, richt Kaizen zich op de praktijk van continue verbetering. Net als lean 5S identificeert Kaizen drie hoofdaspecten van de werkplek:M uda (afvalstoffen), M ura (inconsistenties) en M uri (belasting van mensen en machines). Het stapsgewijze proces van Kaizen is echter uitgebreider dan het lean 5S-proces.
Het Kaizen-procesoverzicht:
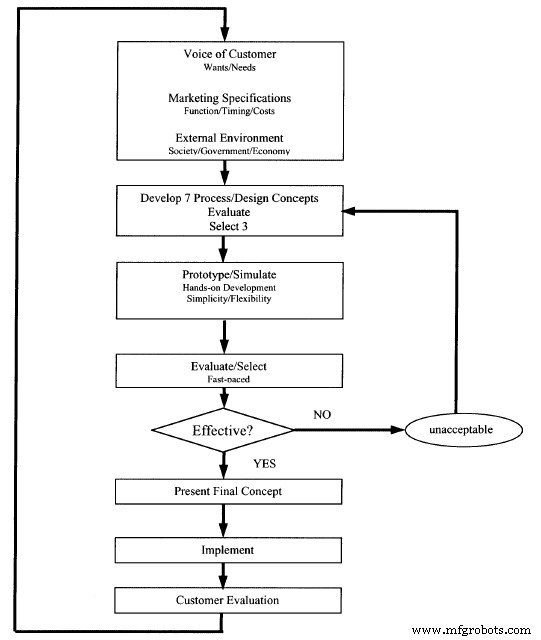
1. Identificeer een probleem.
2. Vorm een team.
3. Verzamel informatie van interne en externe klanten en bepaal doelen voor het project.
4. Bekijk de huidige situatie of het huidige proces.
5. Brainstorm en overweeg zeven mogelijke alternatieven.
6. Bepaal de drie beste alternatieven van de zeven.
7. Simuleer en evalueer deze alternatieven voor implementatie.
8. Presenteer het idee en de suggesties aan managers.
9. Voer de Kaizen-resultaten fysiek uit en houd rekening met de effecten.
Lean manufacturing verbetert naarmate de tijd verstrijkt, dus het is belangrijk om te blijven leren over het handhaven van normen. Het is van cruciaal belang om de normen te wijzigen en werknemers op te leiden wanneer ze nieuwe apparatuur of regels krijgen.
Lean
Beschouw een onderhoudsafdeling als het bedienen van interne klanten:de verschillende afdelingen en medewerkers in het bedrijf.
Lean verschilt van het traditionele westerse massaproductiemodel dat gebaseerd is op schaalvoordelen om winst te maken. Hoe meer u verdient, hoe goedkoper het product wordt, hoe groter de potentiële winstmarge. Het is gebaseerd op voorspellingen van klantbehoeften of het creëren van klantbehoeften. Het heeft moeite met het omgaan met ongebruikelijke veranderingen in de vraag.
Lean productie speelt in op bewezen klantvraag. Pull processing – de klant trekt aan de productie. In een massasysteem duwt de producent product op de markt, push processing.
Bouwen aan een langetermijncultuur die gericht is op verbetering.
Respect voor werknemers beter opgeleid en opgeleid, flexibeler
Lean is een filosofie die zich richt op het volgende:
- Voldoen aan de behoeften van de klant
- Continue, geleidelijke verbetering
- Voortdurend betere producten maken
- De inbreng van werknemers waarderen
- De langetermijnvisie bekijken
- Fouten elimineren
- Verspilling elimineren
Afval:te veel middelen gebruiken (materialen, tijd, energie, ruimte, geld, personeel, slechte instructies)
Afval:
- Overproductie
- Defecten
- Onnodige verwerking
- Wachten (tijd verspillen)
- Menselijke tijd en talent verspillen
- Te veel stappen of verplaatsing Overmatig vervoer
- Overmatige voorraad
Lean productie omvat het werken met leveranciers, onderaannemers en verkopers om het hele proces te stroomlijnen.
Het doel is dat de productie soepel verloopt en kostbare starts en stops worden vermeden.
Het idee wordt just-in-time genoemd:"produceer alleen wat nodig is, wanneer het nodig is en alleen in de benodigde hoeveelheid." Het productieproces moet flexibel en snel zijn.
Inventaris =precies wat je nodig hebt
In massaproductie =voor het geval dat. Extra benodigdheden en producten worden opgeslagen voor het geval ze nodig zijn.
Terminologie:
Procesvereenvoudiging - een proces buiten de productiestroom
Defecten – het massaproductiesysteem voert inspecties uit aan het einde van de productie om defecten op te sporen voordat ze worden verzonden. Het probleem is dat de middelen al zijn "uitgegeven" om het afvalproduct te maken. Probeer problemen onmiddellijk te voorkomen als ze zich voordoen, en voorkom ze dan. Inspectie tijdens de productie, in elke productiefase.
Veiligheid - gekwetste tijd is tijdverspilling
Informatie – de juiste informatie op het juiste moment nodig hebben (te veel, te weinig, te laat)
Principes:
Poka-yoke – foutbestendig bepalen van de oorzaak van problemen en vervolgens de oorzaak wegnemen om verdere fouten te voorkomen
Oordeelsfouten - problemen vinden na het proces
Informatieve inspecties – analyse van gegevens van inspecties tijdens het proces
Broninspecties – inspectie voordat het proces begint om fouten te voorkomen.
MEAN LEAN
Een van de termen die wordt toegepast op een eenvoudig kostenbesparende, banenbesparende interpretatie van Lean is Mean Lean. Vaak denken moderne managers dat ze het lean doen zonder het belang van werknemers en langdurige relaties te begrijpen.
Betrouwbaarheidsgericht onderhoud
Betrouwbaarheidsgericht onderhoud is een systeem voor het ontwerpen van een kosteneffectief onderhoudsprogramma. Het kan een gedetailleerd complex zijn, computer, statistisch gestuurd, maar in de basis is het vrij eenvoudig. De ideeën ervan kunnen worden toegepast bij het ontwerpen en bedienen van een PM-systeem en kunnen ook als leidraad dienen voor uw leerproces terwijl u onderhouds-, probleemoplossings-, reparatie- en energiewerk doet.
Dit zijn de kernprincipes van RCM. Deze negen fundamentele concepten zijn:
- Fouten gebeuren.
- Niet alle fouten hebben dezelfde kans
- Niet alle storingen hebben dezelfde gevolgen
- Eenvoudige componenten verslijten, complexe systemen gaan kapot
- Goed onderhoud biedt de vereiste functionaliteit voor de laagst haalbare kosten
- Onderhoud kan alleen de inherente ontwerpbetrouwbaarheid van de apparatuur bereiken
- Onnodig onderhoud neemt middelen weg van noodzakelijk onderhoud
- Goede onderhoudsprogramma's worden continu verbeterd.
Onderhoud omvat alle acties die worden ondernomen om ervoor te zorgen dat componenten, apparatuur en systemen hun beoogde functies vervullen wanneer dat nodig is.
Een RCM-systeem is gebaseerd op het beantwoorden van de volgende vragen:
1. Wat zijn de functies en gewenste prestatienormen van de apparatuur?
2. Op welke manieren kan het zijn functies niet vervullen? (Wat zijn de meest waarschijnlijke storingen? Hoe waarschijnlijk is elk type storing? Zullen de storingen duidelijk zijn? Kan het een gedeeltelijke storing zijn?)
3. Wat veroorzaakt elke storing?
4. Wat gebeurt er bij elke storing? (Wat is het risico, gevaar enz.?)
5. Op welke manier doet elke mislukking ertoe? Wat zijn de gevolgen van een volledige of gedeeltelijke mislukking?
6. Wat kan er worden gedaan om elke storing te voorspellen of te voorkomen? Wat kost het om elke storing te voorspellen of te voorkomen?
7. Wat moet er worden gedaan als er geen geschikte proactieve taak kan worden gevonden (standaardacties) (er is mogelijk geen taak beschikbaar, of het is te duur voor het risico)?
Apparatuur wordt bestudeerd in de context van waar, wanneer en hoe het wordt gebruikt
Alle onderhoudsacties kunnen worden ingedeeld in een van de volgende categorieën:
- Correctief onderhoud - Herstel verloren of verslechterde functie
- Preventief onderhoud – Minimaliseert de kans dat de functie faalt
- Alteratief onderhoud - Elimineer een onbevredigende toestand door het systeemontwerp of het gebruik te wijzigen
Binnen de categorie preventief onderhoud kunnen alle uitgevoerde taken worden beschreven als behorend tot een van de vijf (5) hoofdtaken:
- Conditiegestuurd – Verleng het leven op basis van gemeten conditie in vergelijking met een standaard
- Tijdgestuurd – Vernieuw het leven ongeacht de conditie
- Failure Finding – Bepaal of er een storing is opgetreden
- Onderhoud – Verbruiksartikelen toevoegen/aanvullen
- Smering – Olie, vet of anderszins smeren
We doen onderhoud omdat we van mening zijn dat de betrouwbaarheid van de hardware met de jaren afneemt, maar dat we iets kunnen doen om de oorspronkelijke betrouwbaarheid te herstellen of te behouden die zichzelf terugbetaalt.
RCM is gericht op betrouwbaarheid. Het doel is om de inherente betrouwbaarheid van het systeem- of apparatuurontwerp te behouden, waarbij wordt erkend dat veranderingen in inherente betrouwbaarheid alleen kunnen worden bereikt door ontwerpwijzigingen. We moeten begrijpen dat de apparatuur of het systeem moet worden bestudeerd in de situatie waarin het werkt.
Lean productie implementeren
Analyseer elke stap in het oorspronkelijke proces voordat u wijzigingen aanbrengt
Lean manufacturing richt zich voornamelijk op kostenreductie en omzetstijging en het elimineren van activiteiten die geen waarde toevoegen aan het productieproces. Wat lean manufacturing eigenlijk doet, is bedrijven helpen om onder meer gerichte productie te bereiken door tools en technieken te introduceren die gemakkelijk toe te passen en te onderhouden zijn. Wat deze tools en technieken doen, is het verminderen en elimineren van verspilling, dingen die niet nodig zijn in het productieproces.
Productie-ingenieurs wilden de zes-sigma DMAIC-methodologie (Design, Measure, Analyse, Improve, Control) gebruiken - in combinatie met lean manufacturing - om te voldoen aan de eisen van de klant met betrekking tot de productie van buizen.
Productie-ingenieurs kregen de opdracht om een nieuwe proceslay-out van de buisproductielijn te ontwerpen. De doelstellingen voor het project waren onder meer:
- Verbeterde kwaliteit
- Verminderd afval
- Bezorging op het punt van gebruik
- Kleinere kavelgroottes
- Implementatie van een pull-systeem
- Betere feedback
- Verhoogde productie
- Individuele verantwoordelijkheid
- Verlaagde WIP
- Flexibiliteit dineren
Alvorens wijzigingen aan te brengen, analyseert het team elke stap in de oorspronkelijke lay-out van het buisproductielijnproces.
1. Probeer daar het oorspronkelijke staatsproces te begrijpen, het probleemgebied, de onnodige stap en geen toegevoegde waarde te identificeren.
2. Nadat het proces in kaart was gebracht, verzamelde het lean-team gegevens van de Material Review Board (MRB)-bank om de belangrijkste soorten defecten te meten en te analyseren. Om het proces beter te begrijpen, deed het team ook een tijdstudie voor een productierun van 20 dagen.
In de oorspronkelijke staat bestond de buisleiding uit één operator en vier operaties, gescheiden in twee stations door een grote tafel met een duwsysteem. De tabel fungeerde als scheidingsteken tussen de tweede en derde bewerking.
Het eerste probleem dat werd ontdekt, was de ongebalanceerde lijn. Het eerste station werd ongeveer 70% van de tijd gebruikt. Operators op het tweede station waren veel tijd kwijt met wachten tussen de cyclustijden. Door stations één en twee te combineren, werd ruimte voor verbetering duidelijk met betrekking tot individuele verantwoordelijkheid, controle van de voorraad door de operator en onmiddellijke feedback wanneer zich een probleem voordeed. De tijdstudie en de indeling van de afdeling weerspiegelen deze bevindingen.
Een tweede probleem werd onderkend. Vanwege de processtroom liet de productiesnelheid het productieschema met twee stations niet toe. Omdat operators de machinecycli uit het oog verloren, wachtten machines op de aandacht van de operator. Operators probeerden ook onderdelen door het eerste station te duwen - het knelpunt in het proces - en gingen vervolgens door met het vervaardigen van de onderdelen bij de laatste twee bewerkingen. Doorgaans werden lange oplagen van WIP opgebouwd en werden kwaliteitsproblemen pas opgemerkt toen er een groot aantal defecte stukken waren geproduceerd.
De oorspronkelijke statusgegevens zijn afkomstig van de laatste 20 dagen vóór de wijziging. De teams analyseren elke stap in het origineel en brengen wijzigingen aan. De bevindingen van de tijdstudie over het oorspronkelijke proces vormden de basis voor het verkorten van de cyclustijd, het balanceren van de lijn, het ontwerpen van de Just In Time-kanbans en planning, het verbeteren van de kwaliteit, het verkleinen van de partijgrootte en WIP en het verbeteren van de doorstroming. De nieuwe procesgegevens zijn genomen vanaf een maand na implementatie. Deze vertraging gaf de machinebedieners de kans om te trainen en vertrouwd te raken met het nieuwe proceslay-outsysteem.
Met het U-vormige celontwerp; De onderdelen voldoen aan alle eisen van de klant. Tabel in het oorspronkelijke proces werd verwijderd, waardoor WIP bijna werd geëlimineerd. Met het verminderen van WIP en het verhogen van de productie.
Enkele van de concepten die werden gebruikt om het proces te verbeteren, waren onder meer totale werknemersbetrokkenheid (TEI), kleinere partijgroottes, planning, inventaris van gebruikspunten en verbeterde lay-out. Alle medewerkers en leidinggevenden van de afdeling zijn bij alle fasen van het project betrokken. Hun ideeën en suggesties werden meegenomen in het plannings- en implementatieproces om een bredere acceptatie van de veranderingen in het proces te krijgen. Er werden kleinere partijgroottes geïntroduceerd om het aantal geproduceerde onderdelen te minimaliseren voordat defecten werden ontdekt. Kanbans werden geïntroduceerd (in de vorm van material handling racks) om WIP te controleren en een pull-systeem te implementeren. En de celindeling verminderde het reizen tussen bewerkingen.
Operators werden gemachtigd om de lijn te stoppen wanneer zich problemen voordeden. In de oorspronkelijke staat waren de operators nog steeds bezig met het draaien van onderdelen wanneer een operatie werd onderbroken. Met kanban
controle, elimineerde de lay-out de mogelijkheid om WIP op te slaan, waardoor de operator de hele lijn moest afsluiten. De celindeling biedt uitstekende mogelijkheden om de communicatie tussen operators over problemen en aanpassingen te verbeteren, om een betere kwaliteit te bereiken.
Bij de dagelijkse inspectie van het proces in de oorspronkelijke staat hebben de operators veel tijd besteed aan het wachten op een material-handling-persoon of als een material-handling. Met de U-vormige cel is levering aan het gebruikspunt beter voor de operator. De machinist plaatst dozen met grondstof op zes verrijdbare rollenwagens, waar het makkelijk te krijgen is. De zes dozen zijn genoeg voor een periode van 24 uur.
Om de insteltijden te verkorten, bevinden de gereedschappen die nodig zijn voor machinereparatie en -aanpassingen zich in de cel. De schroeven zijn niet gestandaardiseerd; gereedschappen worden opgesteld in volgorde van toenemende grootte om snel het juiste gereedschap te identificeren.
Drie maanden lang werd het proces gemonitord om te controleren of het in control was. Vergelijking van tijdstudies vanuit de oorspronkelijke staat en de geïmplementeerde lay-out toonde een toename van de productie aan van 300 naar 514 afgewerkte producten per ploeg. De nieuwe lay-out elimineerde dubbele handelingen tussen de tweede en derde operatie, evenals bij de inpakstap. Het verminderde ook in de loop van de tijd door het gemakkelijker te maken om alle vier de bewerkingen in een pull-systeemvolgorde te doorlopen. Aan de vraag van de klant werd voldaan door twee ploegen, waardoor de arbeidskosten daalden.
De resultaten van het herontwerp zijn als volgt:
- WIP verlaagd met 97%
- Productie steeg met 72%
- Het schroot is met 43% verminderd
- Machinegebruik verhoogd met 50%
- Benutting van arbeidskrachten met 25% gestegen
- De arbeidskosten zijn met 33% verlaagd
- Sigma-niveau verhoogd van 2,6 naar 2,8
This project yielded reduced labor and scrap costs, and allowed the organization to do a better job of making deliveries on time, while allowing a smaller finished-goods inventory. Daily production numbers and single-part cycle time served as a benchmark for monitoring progress towards the goal. Although the sigma level increase , the 43% reduction in defects, 97% reduction in WIP, and production increase of 72% contributed to the project objective.
Implementing lean is a never ending process; this is what continuous improvement is all
about. When you get one aspect of lean implemented, it can always be improved. Don’t get hung up on it, but don’t let things slip back to the starting point. There will always be time to go back and refine some of the processes.
Before Lean Manufacturing was implemented at Nypro Oregon Inc., we would operate using traditional manufacturing. Traditional manufacturing consists of producing all of a given product for the marketplace so as to never let the equipment idle. These goods them need to be warehoused or shipped out to a customer who may not be ready for them. If more is produced than can be sold, the products will be sold at a deep discount (often a loss) or simply scrapped. This can add up to an enormous amount waste. After implementing Lean Manufacturing concepts, our company uses just in time. Just in time refers to producing and delivering good in the amount required when the customer requires it and not before. In lean Manufacturing, the manufacture only produces what the customer wants, when they want it. This often a much more cost effective way of manufacturing when compared to high priced, high volume equipment.
Unit Test:
1. What is 5S?
2. Please Explain each “S” of the 5S.
3. Please Explain Kaizen concept.
4. What is the Pull processing?
5. What is the Poka-yoke?
6. What is the six-sigma DMAIC?
7. What is the objectives for a new process layout of the tube production line?
8. Before making changes, The Manufacturing engineers team do what first?
9. Please lists the results of the redesign.
10. The key to implementing lean new idea or concept is to do what?
CHAPTER ATTRIBUTION INFORMATION
This chapter was derived from the following sources.
- Lean 5S derived from Lean Manufacturing by various authors, CC:BY-SA 3.0.
- Kaizen derived from A Kaizen Based Approach for Cellular Manufacturing System Design:A Case Study by VirginiaTech, CC:BY-SA 4.0.
- Kaizen (image) derived from A Kaizen Based Approach for Cellular Manufacturing System Design:A Case Study by VirginiaTech, CC:BY-SA 4.0.
Industriële technologie
- Six Sigma en lean manufacturing vergelijken
- Voordelen van automatisering in lean manufacturing
- 5 productie- en onderhoudsblogs die u zou moeten lezen
- 6 verbeterpunten die elke consultant analyseert
- 5 Noodzakelijke Lean Manufacturing Tools [Infographic]
- 5 belangrijke voordelen van additieve productie die u moet overwegen
- Wat is lean manufacturing? Stroomlijnen met flexibele automatisering
- Top Lean Manufacturing Tools die D2C-fabrikanten nodig hebben
- De 8 verspillingen van Lean Manufacturing
- Verspilling verminderen in 3 eenvoudige stappen met Lean Manufacturing
- Hoe u Lean Manufacturing weer op het goede spoor krijgt