Best practices voor procesinstrumentatielijnen
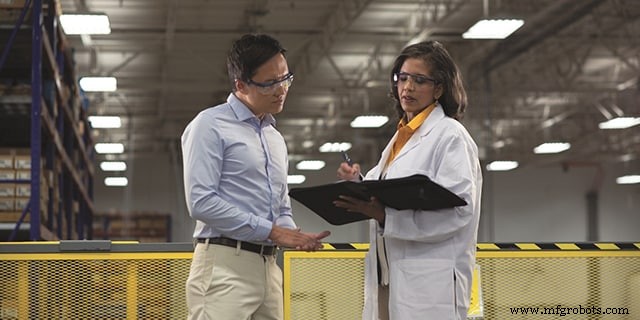
Procesmeting – beste praktijken voor impulslijnen
Chuck Erml, productmanager
Bij het meten van druk, flow of niveau binnen uw proces staan veiligheid en nauwkeurigheid altijd centraal. Van de kraan tot de transmitter, de nauwkeurigheid van de procesmeting hangt af van de juiste functie van elk onderdeel binnen de meetlus van de procesinstrumentatie. En hoewel ingenieurs en technici vaak het grootste deel van hun aandacht aan de zender besteden, is deze slechts zo nauwkeurig als de impulslijningangen die eraan worden geleverd.
Het is vaak moeilijk om te weten wanneer een procesinstrumentatielijn niet goed presteert. Als uw aandacht uitsluitend op de zender is gericht, wordt elke kans op succes ondermijnd als de impulslijn de oorzaak is van slechte prestaties.
Op de hoogte blijven van de mogelijke problemen binnen een procesimpulslijn, inclusief die met betrekking tot het algehele ontwerp en de lay-out, is noodzakelijk voor de nauwkeurigheid van uw uiteindelijke meting. Deze blogpost biedt zowel ingenieurs als technici bewezen best practices om het succes van hun procesimpulslijnen te beheren.
Een standaarddiagram van een impulslijn voor procesmetingen
Materiaalselectie
Voor elk van de basisbouwstenen in een procesinstrumentatielijn - procesinterfacekleppen (PIV's), impulsleidingen en spruitstukken - zijn er kritische keuzes in termen van materialen die de nauwkeurigheid kunnen beïnvloeden.
Procesmedia, omgevingscondities en systeemdruk/temperatuur bepalen vaak de legeringskeuze. Roestvast staal, of een hogere metaallegering, heeft in de meeste toepassingen sterk de voorkeur omdat het bestand is tegen corrosie. Veel industriële fabrieken blijven echter koolstofstaal gebruiken voor procesinterfacekleppen, leidingen en zelfs voor sommige verdeelstukken. In bepaalde toepassingen met weinig vocht is koolstofstaal acceptabel, maar voor de meeste andere toepassingen kan het een risico vormen. De afzetting die zich gewoonlijk op koolstofstaal opbouwt, kan losraken, stroomafwaarts stromen, vast komen te zitten in een klepzitting en een positieve afsluiting belemmeren. Het resultaat is een onnauwkeurige zenderkalibratie of een onnauwkeurige zenderwaarde. Als u koolstofstalen componenten in de instrumentlus gebruikt, moeten deze zeer nauwlettend worden gecontroleerd om ervoor te zorgen dat kalkaanslag de werking van de kleppen in het systeem niet beïnvloedt. U kunt leren hoe u het juiste corrosiebestendige materiaal voor uw specifieke toepassing selecteert met materiaalwetenschappelijke training van Swagelok.
Vereenvoudigd onderhoud door standaardisatie
Als uw doel standaardisatie van het ontwerp is, zijn er gevestigde best practice-configuraties die kunnen worden geïmplementeerd. Hoewel ingenieurs in de loop van de tijd een groot aantal ontwerpvariaties hebben ontwikkeld, zijn veel ervan niet ideaal voor betrouwbaarheid en nauwkeurigheid. Elk systeem heeft andere behoeften op het gebied van onderhoud en dit verhoogt de complexiteit voor onderhoudsteams.
Idealiter zouden alle procesmeetsystemen moeten worden ontworpen met behulp van een consistente set criteria, waaronder het vaststellen van budgetten en vergoedingen voor uitvaltijd, onderhoud en nauwkeurigheid. Het optimale resultaat omvat vaak een hoge mate van standaardisatie. Vóór standaardisatie kan een raffinage-installatie bijvoorbeeld 30 verschillende configuraties hebben voor procesinstrumentatielijnen. Na standaardisatie kan dezelfde fabriek er slechts zes hebben, die elk dezelfde basiscomponenten bevatten:een zenderbevestiging, verdeelstuksysteem en isolatiekleppen. De belangrijkste variaties kunnen de leidingen zijn en het type isolatiekleppen (DBB's, Gage root, enz.) die op hun beurt afhangen van het medium, de temperatuur, de druk en de locatie van de zender of meter.
Met standaardisatie worden veel zaken eenvoudiger, waaronder onderhoud, installatie, training en diagnose. Ook de betrouwbaarheid wordt vergroot. Bovendien kan de faciliteit minder vervangende onderdelen in voorraad hebben, waardoor de overheadkosten worden verlaagd.
Procesinterfaceklep (PIV)
De procesinterfaceklep is de eerste klep van de proceslijn. Historisch gezien was de PIV naar keuze een enkele schuifafsluiter of kogelkraan. Beide worden vandaag de dag nog steeds gebruikt, vooral in de VS, maar de beste praktijk is een dubbele block-and-bleed-klep (DBB), die bestaat uit twee isolatiekleppen en een ontluchtingsklep ertussen.
De belangrijkste reden voor het gebruik van een DBB-klep is veiligheid. Als u de procesinstrumentatielijn voor onderhoud moet afsluiten, sluit u beide blokkeerkleppen en opent u de ontluchtingsklep. Als om welke reden dan ook de eerste blokklep zou lekken, zou de tweede blokklep druk- of vloeistofophoping in de procesinstrumentatieleiding voorkomen.
Een dubbele block-and-bleed-configuratie kan worden gefabriceerd en samengesteld uit drie afzonderlijke kleppen of kan worden gekocht als een enkele, op zichzelf staande eenheid, waardoor de grootte en het gewicht worden verminderd. Het innovatieve op zichzelf staande DBB-ontwerp is geschikt voor alle vloeistoffen, maar vooral voor die met een hogere viscositeit bij gebruik van kogelkranen.
Impulslijnen
Impulsleidingen verbinden de PIV-klep met het verdeelstuk en de zender. Hun doel - hetzelfde als bij alle componenten van procesinstrumentatie - is om de precieze procescondities naar de transmitter over te brengen. Bij het aanleggen van impulslijnen spelen drie hoofddoelen een rol:
- Voorkom corrosie, kalkaanslag of verstopping
- Verminder lekpunten
- Temperatuur binnen een bepaald bereik houden of vorstbescherming bieden
De eerste twee doelstellingen worden het best bereikt door buizen en hulpstukken te gebruiken die zijn gemaakt van een geschikte legering, zoals roestvrij staal, in tegenstelling tot koolstofstalen buizen en schroefdraadverbindingen. Roestvrijstalen buizen kunnen worden gebogen en gevormd, waardoor het aantal mechanische verbindingen wordt verminderd. Wanneer verbindingen nodig zijn, zullen twee-ferrule, mechanische-grip type buisfittingen niet achteruitgaan met thermische cycli of trillingen, in tegenstelling tot traditionele taps toelopende pijpschroefdraadfittingen.
Het derde doel – de temperatuur binnen een bepaald bereik houden – wordt bereikt door de impulsleidingen te verwarmen. U kunt uw impulsleidingen handmatig isoleren door ter plaatse te traceren of door buizen te kopen die al zijn geïsoleerd en in een polymeermantel zijn omhuld. Voorgeïsoleerde gebundelde buizen worden klaar voor installatie in opgerolde lengtes geleverd. Bij voorgeïsoleerde buisbundels is het belangrijk om de instructies van de fabrikant te volgen voor het afdichten van de isolatie bij het splitsen of snijden van de bundel.
Verdeelstuk
Het verdeelstuk bestaat uit een set kleppen waarvan de lichamen zijn vervaardigd uit een enkel blok metaal, meestal roestvrij staal. Het verdeelstuk wordt op de zender gemonteerd en heeft een kritieke functie, waardoor isolatie voor kalibratie of onderhoud van de zender mogelijk is.
Vooral bij een spruitstuk is kwaliteit en betrouwbaarheid van belang. Tijdens kalibreren of normaal bedrijf staat tenminste één van de kleppen in het verdeelstuk in de afsluitstand. Als de uitschakeling niet volledig is, kan het resultaat een onnauwkeurige meting van de zender zijn.
Heeft uw faciliteit hulp nodig bij het identificeren van problemen binnen uw procesinstrumentatielijn? Ervaren veldingenieurs van Swagelok zullen uw faciliteit bezoeken, uw systemen evalueren en adviseren over verbeteringen die uw activiteiten zullen verbeteren.
The Close Couple Manifold – Een optie
Nu we de procesinstrumentatielijn in detail hebben bekeken, gaan we kijken naar een optie om het ontwerp verder te vereenvoudigen. Het is een elegant eenvoudige oplossing, als je toepassing het toelaat om het te gebruiken.
Impulsleidingen kunnen kostbaar zijn om te installeren en te onderhouden, met uitdagingen zoals verstoppingen, lekpunten, temperatuurregeling en corrosie. De optie – ook wel het “close couple” genoemd – elimineert de impulslijnen. De procesinterfaceklep en het verdeelstuk worden één eenheid en de transmitter wordt er rechtstreeks op gemonteerd. Vandaar dat het hele samenstel aan de proceslijn wordt bevestigd. Hoewel veel ingenieurs van deze oplossing houden, hebben close couple-installaties hun beperkingen.
Een beperking is de temperatuur. De reden voor de traditionele opstelling met impulsleidingen is om de zender te beschermen tegen de hoge temperatuur van de procesleiding. Als de procesleiding te heet is, kan de transmitter mogelijk niet werken op slechts enkele centimeters afstand in een nauw gekoppelde installatie.
Een tweede beperking is de toegang. Als u bij de zender moet komen voor kalibratie, moet deze toegankelijk zijn, daarom is het niet haalbaar om een hecht koppel op een proceslocatie van 50 voet in de lucht te monteren.
Het laatste obstakel zijn de initiële kosten. Nauwe koppeling vereist een investering vooraf, maar op de lange termijn kan de oplossing in het algemeen goedkoper zijn. Als u de mogelijkheid heeft om deze snelkoppeling te gebruiken, raden we u aan deze te gebruiken.
Conclusie
Als u nauwkeurige metingen op prijs stelt en investeert in een hoogwaardige transmitter, dan hebben uw procesinstrumentatielijnen hetzelfde aandachtsniveau nodig. De nauwkeurigheid van procesmetingen is net zo afhankelijk van de transmitter als van de kwaliteit van de componenten van de procesmeetlijn, inclusief hoe ze worden geïnstalleerd en onderhouden. Het standaardiseren van uw faciliteit op een kernset van instrumentatie-aansluitingen en het verwerken van impulslijndetails, samen met betrouwbare systeemcomponenten, zal de betrouwbaarheid en nauwkeurigheid van uw meting vergroten. Nauwkeurigere metingen zullen welkome dividenden opleveren in termen van tijd, efficiëntie en winstgevendheid van de fabriek.
Industriële technologie
- Best practices voor afsluiten van risicobeheer
- Vijf best practices in transporttelematica
- Hoe supply-chainmanagers best practices opnieuw evalueren
- Best practices van Tolerance Stacking
- Best practices voor het lassen van aluminium
- Best practices voor robotlassen
- Power Plane PCB:beste praktijken
- 5 best practices voor uw volgende virtuele sollicitatiegesprek
- Waarom profiteren van de best practices van het bedrijf?
- Best practices voor productiemarketing voor 2019
- Onderhoud van hydraulische olie:praktische tips