Hoe schroot in de productie te verminderen?
Van alle componenten waaruit de kostenstructuur van gefabriceerde goederen bestaat, zijn de materiaalkosten een van de duurste voor bijna elke industrie. Zonder grondstoffen en componenten zou er natuurlijk geen productie zijn. Maar als te veel materiaal wordt afgewezen vanwege slechte kwaliteit, kan dit een aanzienlijke impact hebben op de winstmarges van een bedrijf. Zelfs gereedschap alleen kan duur zijn!
In alle bedrijfstakken wordt afgekeurd materiaal schroot genoemd . Er zijn maar weinig dingen die de aandacht van het management trekken, zoals hoge uitvalpercentages. Het probleem is zo kritiek dat, net als het gebruik van arbeid en apparatuur, programma's om afval te verminderen bijna altijd deel uitmaken van de initiatieven voor continue verbetering van fabrikanten.
Fabrikanten moeten rekening houden met het uitvalpercentage in plaats van zich uitsluitend te concentreren op het creëren van maximale output, anders zal de winst een flinke deuk oplopen.
Maar wat valt er precies in de categorie "schroot" materiaal? En hoe kunnen managers actief aan de slag om de hoeveelheid geproduceerd schroot te verminderen? We onderzoeken het concept van schroot, hoe u uw schrootpercentage kunt berekenen en onderzoeken strategieën om schroot en herbewerking van uw bedrijf te verminderen.
Wat is schroot?
Productieschroot is het onbruikbare materiaal van een fabricageproces dat wordt weggegooid.
Schroot kan worden onderverdeeld in verschillende categorieën en wordt gebruikt als een algemene definitie voor al het afgewezen materiaal. Ten eerste is er schroot dat als grondstof wordt afgewezen. Het kan te wijten zijn aan bederf, of het kan te wijten zijn aan prestatiekenmerken die niet aan de specificaties voldoen, zoals treksterkte of breekpunt. Aan dit materiaal is geen extra bewerking of gedeeltelijke bewerking toegevoegd.
Ten tweede is er schroot dat gedeeltelijk is verwerkt. Veel gefabriceerde goederen worden geproduceerd in fasen van een productieproces, en het falen in een bepaalde stap kan betekenen dat het onderdeel moet worden afgekeurd. Dit is duurder dan het slopen van ruw materiaal, omdat het gedeeltelijk voltooide onderdeel wat arbeid met toegevoegde waarde heeft gehad.
Ten derde moeten afgewerkte producten worden gesloopt omdat ze niet aan de specificaties voldoen. Sommige kunnen worden herwerkt door arbeid toe te voegen om het onderdeel aan te passen of er iets anders van te maken. Anderen kunnen volledig worden gesloopt als er geen herbewerking kan worden uitgevoerd.
Dit is een voorbeeld van een schrootdeel. In dit geval zorgde een gereedschapsfout (de gebroken vingerfrees aan de onderkant) ervoor dat het onderdeel enigszins buiten de specificaties werd ontwikkeld. Omdat er geen manier is om dit onderdeel opnieuw te bewerken, moet dit onderdeel worden gesloopt, samen met het kapotte gereedschap.
Hoe schroot in productie te meten:schrootpercentage
Wat is het uitvalpercentage in productie?
Schraapsnelheid is een maatstaf voor de productiekwaliteit en output die fabrikanten helpt de efficiëntie van hun processen te begrijpen. Terwijl een laag uitvalpercentage suggereert dat een bedrijf met een hoog rendement produceert, kan een hoog uitvalpercentage betekenen dat de organisatie te maken heeft met kwaliteitscontroleproblemen en een lager niveau van operationele efficiëntie.
Hoe wordt productieschroot berekend?
Simpel gezegd, de formule voor het uitvalpercentage is gewoon een functie van het aantal onbruikbare eenheden gedeeld door het totale aantal geproduceerde eenheden. (In theorie is dit het tegenovergestelde van first-pass opbrengst, waarbij wordt gekeken naar het aantal bruikbare of geproduceerde kwaliteitseenheden gedeeld door het totale aantal geproduceerde eenheden).
Schrootpercentage =onbruikbare eenheden / totaal aantal geproduceerde eenheden
Door dollarwaarden toe te passen op deze schrootonderdelen kunnen fabrikanten een analyse van productieschroot uitvoeren om de volledige kosten van schroot te bepalen die het bedrijf maakt.
Er is ook een meer gecompliceerde (zij het nauwkeurige) methode voor het meten van het schrootpercentage, waarbij rekening wordt gehouden met extra soorten afval om een volledig beeld te krijgen van het gegenereerde schroot. Planning Master stelt voor om schattingen van deze verspillingen op te nemen om een nauwkeuriger afvalpercentage te genereren:
- Materialen
- Herwerktijd
- Energie
- Behandeling
- Afvoerkosten
- Kwaliteitsborgingskosten
Wat veroorzaakt afval in de productie?
Schroot kan door verschillende factoren worden veroorzaakt en is vaak het gevolg van slechte processen. Doorgaans belemmeren deze processen onderhoud, installatie, gereedschapskwaliteit en training.
Alle schroot verhoogt de kosten, en degenen die extra arbeid nodig hebben, drijven die kosten nog meer op. In complexe productieomgevingen zijn er veel factoren die uitval en nabewerking veroorzaken, waaronder:
- Onjuiste configuratie
- Slecht onderhoud van apparatuur
- Slecht onderhoud van het gereedschap
- Slechte gereedschapskwaliteit
- Operatorfout
- Trainingsproblemen
- Handmatige processen
- Communicatiefouten
- Inefficiënte procedures
- Slecht beheer van ontwerpwijzigingen/specificaties
Een Pareto-diagram voor afgekeurde onderdelen van MachineMetrics visualiseert waarom onderdelen werden afgekeurd. Dit kan kwaliteitsmanagers en leiders voor continue verbetering helpen om processen aan te passen om ervoor te zorgen dat de meest voorkomende oorzaken van uitval worden voorkomen.
6 manieren om afval en herwerk te verminderen
Veel methodologieën, zoals Lean en Six Sigma, zijn ontworpen om verspilling te helpen elimineren en processen in een bedrijf te verbeteren. Deze methodologieën geven bedrijven structuur en een proces voor het identificeren van manieren om afval te verminderen. Technieken voor het verminderen van schroot omvatten auditprocessen, analyse van de oorzaak en andere formele procedures om verandering te stimuleren.
Er zijn ook veel softwaresystemen die fabrikanten helpen bij het bewaken van hun processen om een hogere productkwaliteit en minder afval te garanderen.
Oplossingen voor machinebewaking kunnen nuttig zijn voor het vastleggen van nauwkeurige productiegegevens op machineniveau om nauwkeurig de hoeveelheid geproduceerd schroot te meten.
De sleutel tot het verminderen van schroot is buy-in van managers en leidinggevenden. Dit kan gebeuren als onderdeel van een breder initiatief voor continue verbetering of door het implementeren van een specifiek programma voor het verminderen van schroot. Hier zijn zes manieren om aan de slag te gaan:
1. Procesaudits uitvoeren
De OEE van veel fabrikanten is veel lager dan ze aannemen. Het is niet ongebruikelijk dat de werkelijke OEE in het bereik van 25-30% ligt, terwijl managers en leidinggevenden denken dat dit 20-30 punten hoger is. Dit komt omdat processen in de loop van de tijd veranderen en de controlemechanismen om deze wijzigingen te verwerken en aan te passen altijd handmatig zijn geweest.
Het uitvoeren van procesaudits is de eerste stap in elk proces voor het verminderen van schroot. Zonder het huidige proces te begrijpen zoals het zich voordoet, zou het identificeren van afvalpunten onmogelijk zijn.
Het meeste schroot zal verband houden met het afval dat is geïdentificeerd in de zes grote verliezen:
- Uitsplitsingen
- Instellingen en aanpassingen
- Kleine haltes
- Snelheidsreductie
- Opstartreductie
- Productie afwijzing
Voor elk type schrootverlies kan een hoofdoorzaakanalyse worden uitgevoerd en er kunnen proceswijzigingen worden doorgevoerd om het schroot te verminderen of te elimineren.
2. Verbeter communicatie en verandermanagement
Productie is een snel, luidruchtig en uitgebreid proces. Er is soms geen communicatie tussen stroomopwaartse en stroomafwaartse processen, en daardoor kunnen fouten worden verergerd. Hetzelfde geldt voor handgeschreven notities en tags, waar de kwaliteit van het handschrift, gebrek aan duidelijkheid en andere tekortkomingen van invloed kunnen zijn op de volgende productiefase.
Complexe stuklijsten (BOM's) zijn ook een boosdoener in communicatieketens op de productievloer. Als deze onderdelen moeten vergezellen, bestaat de kans op fouten die resulteren in schroot. Dit geldt op vloerniveau, waar de training van operator tot operator kan verschillen in de interpretatie van de stuklijst.
Het is ook waar wanneer wijzigingen in het ontwerp of de stuklijst niet zijn gecommuniceerd of vertraagd zijn vanwege handmatige processen. Nauwkeurige communicatie van wijzigingen naar de stuklijst is net zo belangrijk als het hebben van een duidelijke stuklijst voor alle productiefasen.
Casestudy:BC Machining heeft schroot vrijwel uitgeroeid als gevolg van slijtage van het gereedschap en aanzienlijk kortere omsteltijden, waardoor $ 72k per machine wordt bespaard.
3. Recensie materiaal sourcing
De kwaliteit van een fabrikant hangt niet alleen af van de kwaliteit van het materiaal en de componenten die worden gebruikt om goederen te maken, maar ook van de kwaliteit van het materiaal dat wordt gebruikt in productiegereedschappen. In het eerste geval kan een strenge selectie van materialen, zoals treksterkte, legeringsconsistentie en productiemethoden van de leverancier, de kwaliteit van een bedrijf maken of breken wanneer die materialen in productie zijn.
In het laatste geval moeten stansmessen, freeskoppen en andere geharde gereedschapstypes gegarandeerd het materiaal snijden dat ze beweren te snijden. Als de prestatiekenmerken van het gereedschap inferieur zijn, kan dit tot uitval leiden.
Leveranciersbeheer, kwaliteitsaudits van leveranciers en certificering van materialen en gereedschappen helpen het afval op de werkvloer te verminderen. Wijzigingen in die materialen, zoals stuklijsten en kennisgevingen van ontwerpwijzigingen, moeten nauwgezet worden gecontroleerd wanneer ze worden geïntroduceerd.
4. Training herzien en verbeteren
Traditionele productie in industrieën zoals CNC-bewerking van precisieonderdelen was afhankelijk van jarenlange leertijd en training om een operator op snelheid te krijgen. Veel van wat operators wisten, was gebaseerd op intuïtie en 'gevoel'. Het probleem met deze methode is dat "voelen" niet altijd een goed genoeg hulpmiddel is om schroot te voorkomen.
Aan de andere kant legt het opleiden van nieuwe operators in dezelfde niet-gecontroleerde processen met ontoereikende processen voor wijzigingsbeheer en een slechte materiaalkeuze de last op de schouders van de operator, wat betekent dat de kans op uitval wordt ingebakken en vrijwel gegarandeerd.
Naast de bovenstaande stappen hebben operators toegang nodig tot realtime gegevens en machinestatus om beslissingen te nemen en actie te ondernemen. Door gebruik te maken van software zoals de conditie- en productiebewaking van MachineMetrics, worden operators nog steeds getraind in de bediening van de apparatuur en de vakmanschapsvaardigheden die nodig zijn om nauwkeurige onderdelen te produceren. Ze zijn ook getraind om proactief mogelijke afvalgebeurtenissen te monitoren en erop te reageren.
5. Documenteer de juiste dingen
Veel fabrikanten verdrinken in schriftelijke documenten van handmatige procedures. Maar als het gaat om de meest kritische aspecten van documentatie, ontbreken ze. Ontwerpiteraties voor actieve producten moeten altijd gedefinieerde en traceerbare toegang hebben. Dit omvat CAD- en CAM-tekeningen en andere technische specificaties.
Stuklijsten, kwaliteitsdocumenten (vooral die met betrekking tot naleving en regelgevende instanties) en andere kritieke items moeten strak gestructureerd zijn. Ze moeten ook deelnemen aan een auditproces om ervoor te zorgen dat ze worden voltooid.
6. Onderhoudsstrategieën evalueren
In plaats van "als het niet kapot is, repareer het dan niet", hebben preventieve onderhoudsstrategieën hun doel gediend. Maar bij het gebruik van preventieve methoden komt schroot nog steeds vaker voor dan wenselijk, en de meeste fabrikanten moeten nog verder gaan.
Dit komt omdat handmatige conditiebewaking veel arbeid, handmatige controle en meting van temperatuur, slijtage, slijtage en meer vereist. Gereedschapsslijtage en defecten worden mogelijk niet gedetecteerd met een handmatige strategie voor preventief onderhoud en gegevens kunnen worden weggelaten door fouten, vooroordelen of trainingsproblemen. Traditioneel onderhoud voorspelt geen subtiele, diep ingebedde gegevens zoals trillingen, olie- en smeerconsistentie, deeltjesinhoud en andere factoren.
MachineMetrics gebruiken om afval en herwerk te verminderen
MachineMetrics kan uw productieactiviteiten bewaken en automatiseren om uitval en nabewerkingen te verminderen en processen aanzienlijk te verbeteren. Het eersteklas machinegegevensplatform van MachineMetrics omvat productiebewaking, conditiebewaking, voorspellend onderhoud en procesoptimalisatie.
Hier zijn enkele manieren waarop MachineMetrics afval en herbewerking voor machinewerkplaatsen, spuitgietactiviteiten en andere discrete fabrikanten verlaagt:
Workflows, meldingen en instructies
Alle documentatie voor auditing en procesverbetering in de wereld zal tekortschieten als deze handmatig wordt gemaakt en beheerd. Met MachineMetrics kunnen workflows worden gebouwd en aan het systeem worden toegevoegd met behulp van een functie voor triggers en acties om veel fabrieksactiviteiten aan te passen en te automatiseren.
Operators kunnen de daadwerkelijke operatie of taak zien en indien nodig om ondersteuning vragen. Deze waarschuwingen naar het juiste personeel worden vanaf de machine verzonden en gaan naar de juiste bron om het probleem aan te pakken, of het nu gaat om managers, onderhoud of kwaliteit. Ze worden verder geholpen door werkinstructies die hen helpen het uitgevoerde proces uit te voeren en te begrijpen.
Nauwkeurige documentatie
Met MachineMetrics behoort het handmatig verplaatsen van documenten tot het verleden. Wanneer er sprake is van schroot, kan het systeem een "waarom" aangeven, zodat operators, onderhouds- en kwaliteitsmanagers kunnen begrijpen wat er is gebeurd. Dit helpt om sneller naar de hoofdoorzaak te gaan om schroot in de toekomst te voorkomen.
Geautomatiseerde nauwkeurige documentatie helpt QA-teams ook bij het begrijpen van de KPI's, zoals 'first pass yield', zodat benchmarks kunnen worden vastgesteld of aangepast. Omdat de gegevens en analyse realtime zijn, kunnen managers en technici processen snel aanpassen om uitval en herbewerking te voorkomen.
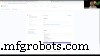
Conditiebewaking
Geavanceerde machinebewakingstechnologie en analysesoftware van MachineMetrics kunnen bedrijven helpen om over te stappen van preventieve naar voorspellende onderhoudsstrategieën om potentieel afval te identificeren en actie te ondernemen voordat het gebeurt.
Met geautomatiseerde conditiebewaking wordt de machinestatus in realtime bewaakt door machinediagnose te verzamelen. Dit geldt voor mechanische IIoT-sensoren die aan de machine zijn bevestigd en voor hoogfrequente gegevensdetectie die defecten aan onderdelen en gereedschappen voorspelt voordat deze optreden. Onderhoud kan worden gewaarschuwd zodra er zich problemen voordoen, zodat de apparatuur soepel werkt en geen defecte onderdelen levert.
Toolbewaking
Met gereedschapsbewaking kunnen instellingen worden bewaakt op een niveau dat verder gaat dan menselijke detectie. Dit omvat trillingen, temperatuur en andere variabelen die voorafgaan aan een gereedschapsfout.
De gegevens van deze gebeurtenissen worden geanalyseerd en gerapporteerd via intuïtieve dashboards en HMI's, zodat de machinist of onderhoudstechnicus echt zicht heeft op nauwkeurige machinecondities. In combinatie met hoogfrequente gegevensanalyse kan het personeel onopgemerkte problemen zien voordat ze zich voordoen.
Dit zorgt ervoor dat onnauwkeurige onderdelen, kapotte gereedschappen en andere kwaliteitsproblemen worden voorkomen en dat fabrikanten geen materiaal of gereedschap hoeven te verspillen.
Aan de slag met MachineMetrics
Het automatiseren van uw productieactiviteiten met het MachineMetrics Machine Data Platform biedt vele voordelen, waaronder de vermindering van uitval en nabewerking. Dankzij de inzichten die het platform biedt, kunnen operators en managers snel actie ondernemen zodra het gebeurt, of zelfs voordat het gebeurt. De informatie is gecontextualiseerd en beschikbaar gemaakt voor iedereen die het nodig heeft via waarschuwingen, meldingen en dashboards.
Met MachineMetrics kunt u processen optimaliseren en erop vertrouwen dat problemen proactief worden aangepakt met behulp van realtime gegevens en geavanceerde analyses. Uw documentatie is digitaal en direct toegankelijk in de meest actuele en nauwkeurige vorm om het gebruik van verouderde informatie te voorkomen.
Het gebruik van MachineMetrics om het schroot te verminderen, maakt deel uit van het brede scala aan voordelen van het platform. Bedrijven kunnen vertrouwen op nauwkeurige machine- en productiegegevens om problemen te analyseren, snellere analyse van de oorzaak te ontwikkelen en uitval en herbewerking te voorkomen op een niveau dat een paar jaar geleden nog ondenkbaar was.
Begin vandaag met het verminderen van afval
Boek een demoIndustriële technologie
- Hoe u de kosten van herbewerking in de productie kunt verlagen
- Hoe u de arbeidskosten van de productie kunt verlagen zonder het personeelsbestand te verminderen
- Hoe word je een digitale kampioen in productie
- Een data-analyseproject starten in de productie
- Hoe implementeer je een leerwerktraject in de productie
- Hoe draadloze energie de productie transformeert
- Hoe belangrijk is Philadelphia Manufacturing?
- Hoe het energieverbruik in de productie te verminderen?
- Partijtracking gebruiken in de productie?
- Hoe productiefouten te verminderen?
- 8 Effectieve manieren om productieafval te verminderen