Rockwell telt alle manieren waarop digitale 'reis' zijn vruchten heeft afgeworpen
Tom O'Reilly, VP, Global Business Development bij Rockwell Automation, spreekt met het tijdschrift Smart Manufacturing.
Tom, vertel ons alsjeblieft over het vijfjarenplan van Rockwell Automation om je faciliteit en leveranciersnetwerken te herstructureren en te komen tot de 'verbonden onderneming'.
Deze reis begon vijf jaar geleden. Terwijl we dit proces doorliepen, hebben we een proces van zes stappen in kaart gebracht dat illustreert wat we deden en hoe we deze dingen nu doen, en ook hoe we met klanten praten. De eerste stap is het begrijpen van de zakelijke behoeften. De tweede stap is bepalen waar de belangrijkste hiaten in de toeleveringsketen zitten. Vervolgens ook uw gereedheid bepalen:het beoordelen van uw huidige staat van uw productiefaciliteit en processen. De vierde is het ontwikkelen van implementatieplannen, vervolgens het projectmanagement doen terwijl u de implementatieplannen uitvoert, en vervolgens een continue verbeteringsfase.
Je had 20 verschillende planten om te coördineren. Welke lessen heeft het bedrijf geleerd dat het nu van toepassing is op klanten?
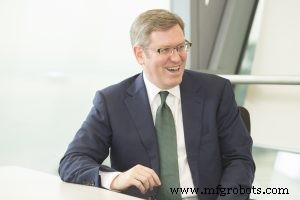
Het grootste probleem dat we ontdekten was het gebrek aan connectiviteit, met name tussen het ERP-systeem en de fabriek voor onze automatiseringssystemen. In veel gevallen beschikten we niet over de juiste gegevens. In sommige gevallen waren er geen gegevens. En in sommige gevallen waren er slechte gegevens. Wanneer u naar die gegevens kijkt en er analyses op uitvoert en het is onjuist of niet robuust genoeg, kan dit u tot de verkeerde beslissingen leiden. Een van de belangrijkste dingen, in de fase van het bepalen van de gereedheid, is het beoordelen van uw infrastructuurmogelijkheden. Dat was een belangrijke les geleerd. En we hebben er met onze klanten over gesproken.
Het tweede dat echt belangrijk is voor bedrijven die slimme productietrajecten willen ondernemen, is dat je eerst de waarde moet vinden. Kijkend naar de zakelijke behoeften, wat zijn de echte waardedrijvers? Wat zijn de echte grote problemen die u moet aanpakken - die de beste waar voor uw geld bieden? Soms zijn mensen alleen maar bezig met de technologie.
Ik heb gehoord dat Rockwell door die verandering een jaarlijkse productiviteitsverbetering van vier tot vijf procent toeschrijft. Hoe is dat mogelijk? En denk je dat de meeste fabrikanten dat kunnen verwachten?
Voor de meeste fabrikanten zou ik ja zeggen. Maar het hangt af van uw branche en uw huidige staat. Dus generaliseren is moeilijk. Als je kijkt naar hoe we het deden/doen, zijn hier enkele voorbeelden:voorraaddagen daalden van 120 naar 82. We verminderden onze CAPEX, wat we CAPEX-vermijding noemen, met 30 procent per jaar. Onze levering binnen onze supply chain ging van 80 procent naar 96 procent. Onze doorlooptijden werden zelfs met 50 procent verkort. En toen, voor klantenservice, ging onze gewenste datum voor levering aan de klant van 82 procent naar 98 procent. En wat betreft kwaliteit hebben we onze PPM (parts per million) met 50 procent verlaagd. Weet je, dit gebeurt niet allemaal op de eerste dag. Je moet je dus op de gebieden blijven concentreren en ze in de loop van de tijd blijven verdrijven. We denken dat we de kosten continu met vier tot vijf procent kunnen verlagen.
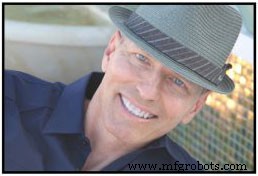
In uw MES-praktijk bent u' opnieuw met FANUC werken aan kansen over de hele wereld. Welk hoofdprobleem komt naar voren in dat soort samenwerkingen?
We hebben een geweldige samenwerking met FANUC die ongeveer zeven jaar geleden begon. Het is niet alleen rond MES. Met FANUC richten we ons voornamelijk op het gebied van aandrijflijnen in de auto-industrie. Het grootste probleem waarmee onze klanten werden geconfronteerd, en een van de drijvende krachten achter het partnerschap, was de integratie tussen de automatiseringssystemen en hun CNC of robots. Dus om onze klanten te helpen dat aan te pakken, hebben we de FANUC geholpen om EtherNet/IP voor communicatie te gebruiken. We bouwen voort op wat we add-on-profielen noemen binnen onze programmering. Het zijn in feite schermen die verschijnen zodat u de communicatie in de CNC automatisch kunt configureren. Daarom hebben we de integratie naadloos gemaakt en vooraf gebouwd, zodat het heel eenvoudig is om zowel de CNC's als robots met ons automatiseringssysteem te integreren.
Dus zou je zeggen dat de integratie nu altijd een makkie is of is het in sommige omstandigheden nog steeds een uitdaging?
Het hangt af van wat je probeert te doen. Maar het is zeker veel gemakkelijker dan in het verleden. En dat zegt niet alleen Rockwell. Dat zijn onze klanten, zoals General Motors, die ons dat vertellen. Hun integratie en vervolgens de informatiestroom van beide systemen, of het nu FANUC of ons systeem is, naar het MES-systeem en vervolgens doorgaan naar het ERP, is veel eenvoudiger. Dus ik weet niet of ze zouden zeggen dat het een makkie is, maar ze zouden zeggen dat het veel gemakkelijker is.
Is dat gezamenlijke werk voornamelijk automotive? Welke andere markten zijn belangrijk in die relatie? En kun je alsjeblieft vertellen waar je in de wereld met hen samenwerkt?
De samenwerking kwam voort uit de behoefte aan integratie tussen CNC-robotica en automatiseringssystemen in de auto-industrie. Dus tot op heden was het meeste werk auto-motief. Een van de snelst groeiende gebieden van robotica is in de consumentenproductenindustrie. We werken dus vrij veel samen met FANUC over de hele wereld, voornamelijk voor robotica en consumentenproducten, in Noord-Amerika en Europa. Nu, het werk dat we met FANUC hebben gedaan, zou ik zeggen dat de belangrijkste markten Noord-Amerika, China, Europa, Japan en Korea zouden zijn. Dat komt omdat dit autohubs zijn waar de beslissingen worden genomen en/of de machines worden gebouwd.
Wat voor soort consumentenproducten?
Voedsel en drank of verpakte goederen.
En zijn die in verschillende landen?
Dat zijn meestal de meer ontwikkelde markten, waar ze kijken naar grotere kostenbesparingen, grotere efficiëntie, misschien zelfs grotere doorvoer zonder grotere kapitaaluitgaven:West-Europa en Noord-Amerika.
/P>
Welke landen zijn zeker grote groeimarkten in uw MES-praktijk?
Noord-Amerika is er één. Er zijn veel geavanceerde productie-initiatieven. En om concurrerend te zijn, moet u beginnen met het uitvoeren van de connectiviteit en de convergentie tussen IT en OT hebben. (We zeggen de Connected Enterprise.) MES is daarvoor een belangrijke enabler. We zien ook enkele opkomende markten, zoals China of India, die vanuit het oogpunt van productierijpheid eerder in hun ontwikkeling zijn. Maar ze erkennen dat om continu wereldwijd concurrerend te zijn, ze bijna een sprong voorwaarts moeten maken in hun ontwikkeling om wereldwijd concurrerend te worden.
Laten we het hebben over het FactoryTalk Cloud Gateway-platform, dat gaat over het verkrijgen van informatie uit productiefaciliteiten die uw automatisering gebruiken, om het in een cloudgegevensstructuur te krijgen waar het kan worden gecombineerd met bijvoorbeeld andere gegevens van derden en ERP-gegevens, en vervolgens business intelligence over de top te leggen om analyses voor uw klanten te doen om hen nieuwe zakelijke inzichten te geven.
Met de FactoryTalk Cloud Gateway werken we samen met Microsoft. We baseren het op de Microsoft Azure cloud. Maar de software is gebaseerd op onze jarenlange ervaring met implementaties op locatie, waarbij gebruik wordt gemaakt van de fabrieksmodellering van onze FactoryTalk VantagePoint met andere moderne web- en cloudgebaseerde technologieën. Het voordeel van het FactoryTalk Cloud Gateway-platform is dat we gegevens van meerdere industriële en zakelijke systemen kunnen streamen. En als we het combineren, kunnen we het contextualiseren, de gegevens betekenis geven en ze vervolgens presenteren in zeer gebruiksvriendelijke dashboards en rapporten, zodat niet-gegevenswetenschappers kunnen interpreteren wat er in het proces gebeurt en acties ondernemen om te optimaliseren.
Hoe belangrijk zijn cloudoplossingen zoals FactoryTalk Cloud wanneer u met bedrijven buiten de VS werkt? Heeft uw update van dat cloudplatform afgelopen najaar geholpen bij internationale partners en/of klanten?
We updaten ons cloudplatform sneller dan onze traditionele softwareproducten. Veel van onze wereldwijde klanten zijn geïnteresseerd in de geografische locatie van hun gegevens, gegevensopslag en de infrastructuur van Microsoft Azure is het beste gerelateerd aan transparantie en naleving van cloudgegevens. De acceptatie van het cloudplatform door een wereldwijd klantenbestand is dus verrassend hoog.
Wat doet u om fabrikanten ertoe aan te zetten FactoryTalk Cloud te gebruiken?
We proberen het heel gemakkelijk te maken. Zo is de configuratie van de dashboards en de connectiviteit met onze gateway heel eenvoudig. Met een paar eenvoudige stappen kunt u de gateway aansluiten op het besturingssysteem. De gegevens stromen automatisch naar de cloud, waarna u direct uw dashboards kunt instellen.
Met wie heb je samengewerkt om de gateway te bouwen?
De gateway-software is onze eigen ontwikkeling, maar is ontworpen om zeer uitbreidbaar te zijn met aangepaste adapters en applicaties. We zullen deze API's binnenkort aanbieden aan onze hele partnergemeenschap.
Welke andere platforms en applicaties biedt of bouwt u aan om waarde te creëren voor uw klanten in het buitenland?
Tijdens de Automation Fair afgelopen november hebben we FactoryTalk Analytics for Machines, FactoryTalk Analytics for Devices, de FactoryTalk TeamONE-applicatie aangekondigd, en veel hiervan zijn speciaal gebouwde applicaties. Zeer schaalbaar, gemakkelijk te gebruiken, eenvoudig te implementeren. We hopen dat door het produceren van deze modulaire toepassingen die zeer kosteneffectief zijn, mensen een stapsgewijze aanpak kunnen volgen, in plaats van te proberen de olifant in één hap op te eten.
Als u deze software gebruikt om storingen op te sporen en te verhelpen, wat zijn dan de twee of drie meest voorkomende storingen die worden gevonden en verholpen?
Een van de belangrijkste voordelen die we hebben gezien, is dat klanten onbekende problemen ontdekken. In een productiefaciliteit weten de operator of de mensen met de operationele technologie doorgaans waar ze uitdagingen hebben met betrekking tot prestaties, kwaliteit of doorvoer. Zodra klanten het systeem hebben ingevoerd en beginnen met het oplossen van die problemen, vinden ze vaak andere problemen waarvan ze zich vaak niet bewust waren. Ze kunnen bijvoorbeeld knelpunten hebben in upstream- of downstream-productieprocessen.
Net als iedereen zijn de klanten van Rockwell voorzichtig geweest met het adopteren van de cloud. Wat doet u om hen ervan te overtuigen dat dit het juiste moment is om het te introduceren? En zullen de ransomware-aanvallen van deze week de inspanningen om cloudadoptie te bevorderen bemoeilijken?
Ten eerste zijn de betrouwbaarheid en de mogelijkheden van cloudoplossingen enorm verbeterd. (Bovendien hoeven onze klanten hun eigen infrastructuur niet te onderhouden, en dat wordt voor veel van onze klanten steeds belangrijker.) Ten tweede is de schaalbaarheid van cloudservices bijna onmogelijk te reproduceren met on-premises mogelijkheden. Onze klanten kunnen klein beginnen en het veel sneller opschalen dan wanneer ze het zelf zouden bouwen en onderhouden. De beveiliging van cloudoplossingen is waarschijnlijk veel beter dan bij on-premise oplossingen. En dit, denk ik, speelt in op het tweede punt. Cloudservices worden veel vaker geüpdatet.
Wij geloven dat veel van de huidige ransomware [beïnvloed] wat mensen onbeheerde IT-middelen zouden noemen bij onze klanten - waar ze ze niet up-to-date hebben gehouden, of niet de juiste beveiliging hebben. Dat was of het beginpunt of het begin. Cloudservices zouden mogelijk een grotere preventie zijn. Dat is onze eerste gedachte. Het is duidelijk dat mensen bang zouden zijn om hier uit te komen en te proberen te begrijpen wat er is gebeurd. Maar onze eerste gedachte is dat dit misschien meer van onze klanten ertoe aanzet om meer gebruik te maken van de cloud.
Toen Rockwell fabrieken moest bouwen in Singapore en Mexico, hoe heb je de tribale kennis van productieprocessen bij Rockwell naar die markten overgebracht?
We hebben de vestigingen in Singapore en Mexico later op onze reis gedaan, dus we hadden ons zesstappenproces voor de implementatie van de Connected Enterprise in al onze vestigingen ontwikkeld - en dit bij ten minste 10 fabrieken uitgevoerd. Het is belangrijk om de beste materiedeskundigen te hebben voor specifieke aspecten van het proces die complex of uniek of zeer kritisch waren. We hebben die materiedeskundigen naar elke fabriek gebracht om ervoor te zorgen dat die processen op de juiste manier op gang kwamen. Ten slotte hebben we vastgesteld dat het erg belangrijk was om gestandaardiseerde systemen en architecturen te hebben voordat we aan de reis begonnen.
Automatisering Besturingssysteem
- Vijf manieren waarop Digital-Twin-technologie bedrijven door de pandemie heen helpt
- In het nieuwe logistieke landschap is er geen weg terug naar oude manieren
- Klanten helemaal van Noorwegen tot onze CNC-routerfabriek
- GE Digital:een doorlopend digitale transformatietraject
- Hoe heeft COVID-19 de digitale transformatie veranderd?
- Censornet:de toekomst van de maakindustrie veiligstellen
- De grote impact van Industrie 4.0 op de backoffice
- CS Ellis:Vier manieren om de supply chain te digitaliseren
- De opkomst van digitale platforms in de maakindustrie
- Rockwell Automation:digitale transformatie versnellen
- Automatisering en de toekomst van digitale productie?