Expert Interview:Versterk CEO Josh Martin over zijn Digital Composite Manufacturing Technology
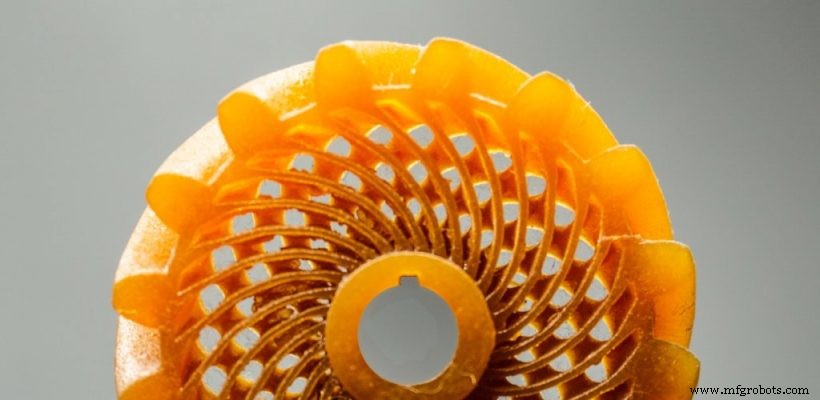
[Image credit:Fortify]
Fortify is een in Boston gevestigde startup die een nieuwe benadering van composiet 3D-printen heeft ontwikkeld. Deze benadering combineert magneetuitlijning van composieten met Digital Light Processing (DLP)-technologie, waardoor gebruikers hoogwaardige composietonderdelen kunnen produceren die anders onmogelijk te vervaardigen zouden zijn.
De technologie, genaamd Fluxprin t™ , drijft Fortify's Digital Composite Manufacturing (DCM)-platform aan. Het platform is er in de eerste plaats op gericht om bedrijven in staat te stellen duurzame gereedschappen zoals spuitgietmatrijzen en productie-onderdelen voor eindgebruik te produceren.
In het interview van vandaag worden we vergezeld door de CEO van Fortify, Dr. Joshua Martin, om meer te weten te komen over de opwindende technologie van Fortify en om te bespreken wat de groei van composiet 3D-printen stimuleert.
Kun je me iets over Fortify vertellen?
Fortify is een in Boston gevestigd bedrijf voor additieve productie dat het platform van de volgende generatie voor composietprinten op de markt brengt.
Bij Fortify richten we ons op het combineren van de prestaties die u krijgt van vezelversterkte materialen met de resolutie die u traditioneel zou hebben verwachten van fotopolymeertechnologieën zoals SLA en DLP.
We hebben het bedrijf opgericht omdat we het moe waren om te moeten kiezen tussen vorm en functie. Traditioneel is er een afweging gemaakt tussen het hebben van een prototype dat eruitziet als het echte werk, maar doorgaans slecht is in termen van prestaties, of een onderdeel dat een functioneel prototype is, maar ver verwijderd is van de pasvorm en afwerking van een productie -klaar materiaal.
Bij Fortify geloven we dat polymeerchemie alleen maar een klein deel van de vastgoedruimte kan bereiken die nodig is voor technische toepassingen. Binnen fotopolymeren zijn veel van de basismaterialen de afgelopen decennia niet echt veranderd. De afgelopen 25 tot 30 jaar is het vrijwel gebaseerd op dezelfde soorten chemie, hoewel de dingen de afgelopen vijf jaar of zo zijn versneld.
Fortify brengt een technologie op tafel die ons in staat stelt om de chemische processen met hoge resolutie te vullen met versterkende additieven, met het cruciale voordeel dat we de uitlijning van de versterkende deeltjes kunnen controleren.
Als je kijkt naar alle bestaande 3D-printtechnologieën, zijn op SLA/DLP gebaseerde platforms het verst gekomen wat betreft oppervlakteafwerking en nauwkeurigheid van onderdelen wanneer ze van de printer komen.
We hebben een techniek ontwikkeld waarmee we vezels magnetisch kunnen oriënteren in een vloeibaar medium. De onderdelen die we printen zijn in wezen de hoogste resolutie composieten die tot nu toe zijn geproduceerd. In vergelijking met andere vormen van additieve composieten, vertrouwt u doorgaans op afschuifkrachten om deeltjes uit te lijnen om de sterkte te optimaliseren. Afschuiving is echter niet altijd de gemakkelijkst gerichte kracht om te beheersen.
Met de magnetische assemblage zijn we in staat om meerdere eigenschappen zoals sterkte, stijfheid en thermische geleidbaarheid in drie dimensies binnen elke voxel te regelen.
Is dit uw Digital Composite Manufacturing (DCM)-platform?
Ja. Het DCM-platform is alles waarmee we de glasvezelarchitectuur kunnen afstemmen om deze te optimaliseren voor prestaties. Dat omvat hardware, software en materialen.
De specifieke magnetische uitlijningstechnologie heet Fluxprint ™ , die meer betrekking heeft op het toepassen van magnetische velden op het bouwgebied om een magnetisch gevoelig materiaal te oriënteren.
Welke industrieën en toepassingen zijn het meest geschikt voor uw technologie?
We hebben een uitrolstrategie die ons in staat stelt om eerst te profiteren van de gereedschapsruimte, aangezien we werken aan bepaalde benchmarkingbehoeften voor de productie van onderdelen voor eindgebruik
Met betrekking tot gereedschap is ons concurrentievoordeel dat we kunnen bieden hetzelfde resolutieniveau dat u zou verwachten van een fotopolymeertechnologie, met het vermogen om temperaturen van bijna 300°C te weerstaan, met behoud van de beste sterkte en stijfheid in zijn klasse.
We zijn zeer goed in staat om te disrupten de spuitgietmarkt, waar de investeringen in tooling aanzienlijk zijn en de fabricage van tooling veel tijd kost. De spuitgietmarkt is de afgelopen tien jaar geprepareerd door andere oplossingen die het probleem met de prestatieresolutie nog niet helemaal hebben opgelost. We kunnen in een uur printen, terwijl het 10 weken kan duren om diezelfde tool conventioneel te kopen.
We zijn sterk in de markt omdat onze tools aanzienlijk meer schoten en cycli kunnen verwerken dan concurrerende oplossingen. We zullen binnenkort kunnen demonstreren hoe ze de productie van kleine volumes voor hoogwaardige toepassingen aankunnen.
Dat gezegd hebbende, hebben we verschillende actieve projecten die de productie van onderdelen voor eindgebruik zullen openen met behulp van het DCM-platform. . Onze technologie stelt ons in staat om fysieke eigenschappen te verbeteren die verder gaan dan sterkte en stijfheid, zoals het mogelijk maken van hoogwaardige onderdelen met certificeringen zoals FST (ontvlambaarheid, rook en toxiciteit).
Wij zijn van mening dat de toekomst van adoptie in de additieve ruimte afhankelijk is van het openstellen van het materiaalpalet voor toepassingen die momenteel kunnen worden aangepakt door de standaardsuite van polymeren. Kosten en doorvoer zijn natuurlijk noodzakelijk, en er zijn geen betere voorbeelden van het behalen van de juiste resultaten dan de op fotopolymeer gebaseerde technologieën.
Wat is uw mening over de huidige staat van composiet 3D-printen en hoe ontwikkelt de technologie zich?
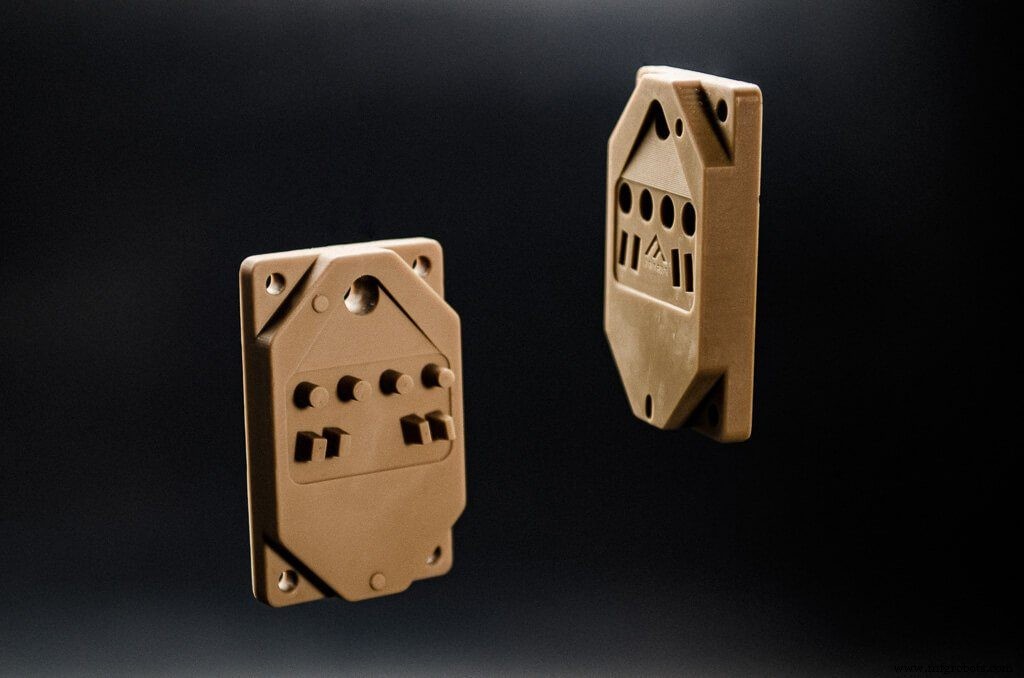
Wat interessant is, is dat als je kijkt naar de 3D-printindustrie van de afgelopen 10 jaar en de gebieden waarin bedrijven investeren, het erg asymmetrisch is.
Wat ik daarmee bedoel is dat er letterlijk miljarden dollars gaan naar polymere 3D-printbedrijven en metalen 3D-printbedrijven. Onlangs kondigde Carbon aan dat ze nog eens $ 260 miljoen aan financiering hebben ontvangen. Dat ene bedrijf alleen al heeft in ongeveer zes jaar meer dan $ 600 miljoen opgehaald.
In de composietruimte zijn er misschien vijf bedrijven die echt technologie beoefenen en onderdelen produceren in dit segment, zoals Markforged, Arevo, Continuous Composites en Impossible Objects. Maar alleen Carbon, dat een van de misschien wel 150 bedrijven is op het gebied van polymeer 3D-printen, heeft meer geld opgehaald dan alle composiet 3D-printbedrijven bij elkaar.
Als je kijkt hoe dit uitpakt, hebben aanzienlijk meer dollars naar polymeer 3D-printen en metaal 3D-printen versus composieten. Maar als je kijkt naar de marktkansen tussen kunststoffen, metalen en composieten, dan lijken ze erg op elkaar. Ze zijn allemaal wereldwijd meer dan $ 300 miljard.
Je hebt een enorme polymeermarkt, waar je bijvoorbeeld spuitgietverplaatsing hebt, en je hebt een enorme metaalmarkt met een verplaatsing van gesneden metalen, gegoten metalen en metalen spuitgieten voor sommige toepassingen.
Dan heb je deze enorme markt voor composieten, die bestaat uit handlayup, spuitgieten, vezelgevulde kunststoffen enzovoort.
Ze zijn allemaal enorm. Maar de investering aan de kant van 3D-printen gaat heel erg naar de oudere technologieën zoals de extrusie van thermoplasten en op licht gebaseerde processen.
Dat gezegd hebbende, de composietruimte is misschien wel het nieuwste segment in 3D-printen. Dit brengt uitdagingen met zich mee, maar er zijn ook veel kansen.
Wij zien het zo dat de meeste bedrijven in de composietindustrie tot nu toe gefocust waren op extrusie-gebaseerde technieken zoals FDM. Het probleem is dat dit in de eerste plaats enkele van de belangrijkste fouten van FDM niet echt omzeilt, wat een slechte oppervlakteafwerking en anisotropie zou zijn - waar je een materiaal hebt dat in de ene richting 10 keer sterker is dan in de andere.
Daar zullen zeer sterke toepassingen voor zijn, maar ik denk in de composietruimte, op zoek naar manieren om betere niveaus van isotropie, voorspelbaarheid, betere controle en prestaties te bereiken die niet alleen worden gedicteerd door het maximaliseren van kracht in een paar richtingen, zal de sleutel zijn.
Onze missie bij Fortify is om 3D-printen op een hoge doorvoerschaal mogelijk te maken, met materialen die doorgaans met traditionele middelen moeten worden gesneden of vervaardigd.
Er zijn bijvoorbeeld veel materialen die traditioneel met de hand worden geassembleerd of die in een enorm blok worden gekocht dat erg duur is en vervolgens wordt bewerkt om het onderdeel te krijgen. We bouwen dit soort materialen in ons platform in, zodat u ze direct in 3D kunt printen.
Waarom heeft het zo lang geduurd voordat de industrie composieten zag als een geweldige kans voor 3D-printen?
Dat is een heel goede vraag. Ik denk dat veel daarvan te wijten is aan de volwassenheid van de koopmarkt. Met andere woorden, van 2000 tot 2014 bevond de industrie zich in een staat waarin er veel lager hangend fruit was om te grijpen.
Toen Formlabs de Form1 introduceerde, was het de eerste echte desktop 3D met hoge resolutie printer voor die prijs. Dat is wat hun branding kon vastleggen. Nu zijn er tien tot honderd bedrijven die hetzelfde proberen te doen.
Als je naar Markforged kijkt, brachten ze in 2014 de eerste composiet 3D-printer uit. Aan de andere kant bestaat FDM al tientallen jaren en bestaat SLA al sinds Chuck Hull het in de jaren 80 uitvond.
De industrie was niet per se klaar om composieten te gebruiken, omdat ze nog steeds aan het leren is hoe ze 3D-printen in het algemeen kan toepassen. Er zijn veel barrières op het gebied van ontwerp en benchmarking, die enige tijd in beslag nemen om op te lossen.
Er is een reden waarom composieten traditioneel alleen werden gebruikt voor zeer krachtige, zeer dure toepassingen zoals lucht- en ruimtevaartcomponenten of hoogwaardige recreatieve uitrusting zoals auto-onderdelen en fietsen.
Als je naar de Gartner-hypecyclus kijkt, zijn we nu op een punt beland dat toepassingen in de industriële ruimte echt voet aan de grond krijgen.
De algemene aanpak was om te proberen overal 3D-printen te krijgen. Nu is dit perspectief veranderd en veel meer gericht op specialisatie. De industrie als geheel wordt steeds meer gespecialiseerd om ervoor te zorgen dat de mogelijkheden voor technologie echt passen bij specifieke toepassingsbehoeften. Er is meer een gerichte inspanning om zeer specifieke problemen op te lossen, en dat is waar composieten echt nuttig zijn.
Als u meer in het algemeen over de AM-industrie denkt, hoe ziet u deze de komende vijf jaar evolueren?

Als u deelneemt aan het jaarlijkse circuit van brancheconferenties, kunt u meestal zien in welke richting alle bedrijven de branche echt willen inslaan.
Als we terugkijken naar vijf jaar geleden, begonnen we echt geruchten te horen over industrieel printen. Het doel was niet langer om 3D-printtechnologieën naar de consument te brengen, maar om ze naar high-end industriële omgevingen te brengen, waar we 'lights-out'-productie kunnen doen.
Bedrijven als Carbon hebben grote stappen gezet om dit mogelijk te maken, hoewel er nog een lange weg te gaan is. Ik denk dat een van de thema's waar we ons de komende vijf jaar op zullen richten, afkomstig is van hardware-, software- en materiaalinnovaties.
Om precies te zijn, als je kijkt naar wat de farmaceutische industrie heeft gedaan met batchgenealogie, begint dat te worden geïmplementeerd door het gebruik van machine learning.
Het idee is hoe u de digitale draad helemaal kunt volgen vanaf het batchnummer van uw grondstoffen via alle processen die het materiaal ervaart tijdens het printen tot na het testen en valideren. Dat is iets dat 3D-printen serieuzer moet nemen, omdat het vrij goed gedefinieerd is in de traditionele productieruimte.
Een andere manier om dit te zeggen is dat bedrijven zich de komende vijf jaar zullen moeten concentreren op het aantonen van hoge niveaus van herhaalbaarheid en betrouwbaarheid.
De reden waarom het prettig is om verschillende soorten conventionele materialen te gebruiken, is dat als u koudgewalst staal koopt, u weet wat u kunt verwachten op het gebied van eigenschappen en prestaties en hoe u ermee moet werken.
Het probleem met 3D-printen op dit moment is dat er nog steeds een groot scala aan variabiliteit is. Als u bijvoorbeeld twee dezelfde printers koopt en u drukt op beide twee weken achter elkaar af, dan verzamelt u alleen maar exemplaren om te testen.
Als je al die exemplaren test, krijg je een grote wolk aan gegevens die in sommige gevallen alle kanten opgaat. De vraag is dus hoe een ingenieur verondersteld wordt enige mate van voorspelbaarheid uit te oefenen, vooral als ze de technologie op grote schaal willen gebruiken.
Dus een deel van het machine-leerproces is het introduceren van een hoog niveau van herhaalbaarheid en stelt de gebruiker in staat om gemakkelijker te voorspellen hoe de prestaties zullen functioneren.
Wat zijn enkele van de uitdagingen die de industrie moet overwinnen?
Op dit moment zijn er veel barrières om met 3D-printen het doel van Industrie 4.0 te realiseren. We hebben het bijvoorbeeld over gedistribueerde productie, bijvoorbeeld een hogere doorvoer, hoge herhaalbaarheid en lagere kosten per eenheid.
Om die doelen te bereiken, moet de industrie de machines minder als 3D-printers en meer als 3D-printers behandelen. productie-eenheden, en veel van de checks and balances hebben ingevoerd die een traditioneel productiesysteem zou hebben.
Als je naar de International Manufacturing Technology Show (IMTS) gaat, is het nederig, want er zijn ongeveer 140.000 aanwezigen, en ongeveer 90% van hen komt uit traditionele productie. 3D-printen is slechts een druppel op een gloeiende plaat.
Je krijgt een idee van hoe volwassen veel van deze traditionele systemen zijn. We komen daar in die zin dat AM-machines er nu uitzien en aanvoelen en hetzelfde niveau van inputs en outputs hebben als een traditioneel productiesysteem zoals een CNC.
Hoe lang duurt het voordat de industrie zover is dat ze meer is dan slechts een klein percentage van de totale productiemarkt? Of vind je dat de technologie bij wijze van spreken op zijn eigen manier moet worden gezien?
Ik denk dat het vergelijken van de omvang van de AM-industrie met de totale productiemarkt niet de beste manier is om ernaar te kijken, omdat de industrie niet alleen bestaat om spuitgieten of CNC te vervangen. Het zou jammer zijn als het doel gewoon dat was.
Er moet veel nadruk worden gelegd op de nieuwe soorten toepassingen en nieuwe soorten voordelen die alleen met additieven kunnen worden bereikt.
Dat is een groot deel van waar we naar uitkijken bij Fortify:de mogelijkheid om een verscheidenheid aan AM-technologieën te gebruiken om een onderdeel te creëren dat erg sterk is, een unieke geometrie heeft en ook een hoog niveau heeft van thermische geleidbaarheid. Dat zal nieuwe markten creëren.
Maar ik denk wel dat het enige tijd zal duren voordat we dit doel volledig hebben bereikt — hoewel het natuurlijk geen nulsomspel is.
Dit jaar kondigde Fortify een financieringsronde van $2,5 miljoen aan. Kunt u iets vertellen over wat deze investering in de toekomst voor Fortify betekent?
De financieringsronde die we in januari aankondigden, was een samenvatting van de financiering die al is afgesloten. De bedoeling is om ons systeem in wezen klaar te maken voor bètatests en het in handen te geven van gebruikers met wie we nu nauw hebben samengewerkt. We hebben zojuist een extra serie A van 10 miljoen dollar afgesloten, geleid door Accel Partners.
We willen het systeem gereed maken zodat onze klanten, die ons betalen om onderdelen te produceren voor hun huidige productiebehoeften, kan het ook echt gebruiken.
Onze eerste twee materiaalsystemen gaven ons goede feedback over de workflow tussen hardwaresoftware en materialen.
Dus de volgende stap is om de tooling-mogelijkheid te benutten en vervolgens te beginnen met het identificeren van en werken aan de productie van eindgebruiksonderdelen voor andere technische systemen.
Kunt u ons meer vertellen over uw samenwerking met chemiebedrijf DSM? Wat betekent deze samenwerking voor Fortify en uw toekomstige klanten?
DSM was de eerste partner op ons open materiaalplatform. Het idee achter dit platform is dat we niet alles willen bezitten als het gaat om materiaalformulering. We willen ons kunnen concentreren op de additieven, de hardwaresystemen en de softwarecontrole, zodat klanten meer dan één keuze hebben als het gaat om leveranciers.
Als het gaat om bedrijven als BASF, DSM, Mitsubishi en Henkel hebben elk hun unieke voordelen en unieke toepassingen binnen de additieve productieruimte. En we zouden graag met hen samenwerken op een manier die ons in staat stelt meer waarde te creëren dan wanneer we alleen de hele supply chain zouden beheersen.
Vooral met DSM kijken we naar manieren om een aantal van hun systemen te gebruiken die toepassingen in de ruimte onder de motorkap hebben. Ze hebben een redelijke mate van taaiheid, ze kunnen sterkte en stijfheid behouden bij misschien 100°C.
Bovendien kan het Fortify-technologieplatform veel hogere niveaus van sterkte, stijfheid, kruipweerstand en het kan presteren bij hogere temperaturen. Dit zou onze materiële partners in staat stellen hun bestaande klantenbestand oplossingen te bieden die niet noodzakelijkerwijs alles uit de technologie halen wat ze willen.
Voor Fortify is het geweldig omdat DSM een van de belangrijkste fotopolymeer is producenten ter wereld. We zijn verheugd om met hen samen te werken. Het is een geweldige groep mensen en samen kunnen we ver komen met onze technologieën.
Je hebt het model van open materialen aangeroerd. Denk je dat dit de toekomst is van 3D-printmaterialen?
Als je kijkt naar de computerindustrie in de jaren 80, was deze verticaal geïntegreerd. IBM zou bijvoorbeeld geheugens en processors maken en zou ook software en randapparatuur moeten bouwen.
Toen veranderde de industrie. Als je kijkt naar waar het nu staat, zijn er bedrijven die gespecialiseerd zijn in elk van deze segmenten:software, processors, geheugenchips enzovoort. De markt is gedecompartimenteerd.
In sommige opzichten volgt de 3D-printindustrie dat traject, waar traditionele bedrijven zoals Stratasys en 3D Systems de hardware bouwen, de software ontwikkelen en hun eigen materialen produceren, wat betekent dat je alleen binnen die supply chain.
Er zijn echter veel klanten die meer opties willen hebben. Ze willen kunnen kiezen welke materialen ze gebruiken en weten dat er een andere optie is.
Het zal enige tijd duren voordat het model voor open materialen in de hele branche is gestandaardiseerd.
Wat houden de komende 12 maanden in voor Fortify?
We schalen het team op om ervoor te zorgen dat we onze productmijlpalen kunnen bereiken. We nemen snel mensen aan en we willen het team verder uitbreiden om onze bètaprogramma's ergens begin tot midden 2020 te kunnen uitvoeren.
Dan kunnen we opschalen in termen van het verplaatsen van dit platform naar algemene beschikbaarheid.
We hebben het gevoel dat we ons in een positie bevinden waarin we de technologie kunnen leveren in 2021. We zullen hoogstwaarschijnlijk eind 2021 op zoek zijn naar wat meer kapitaal om een systeem te laten produceren voor eind 2021, begin 2022.
Er ligt heel wat spannend werk voor ons . We hebben al veel contact met klanten.
Als mensen geïnteresseerd zijn om in een vroeg stadium mee te doen, is er capaciteit om dat te doen. Maar we hebben nog veel werk voor de boeg om systemen in handen te krijgen van de mensen met wie we nu werken.
Ga voor meer informatie over Fortify naar: https://3dfortify.com
3d printen
- Interview met een expert:Dr. Bastian Rapp van NeptunLab
- Expertinterview:Felix Ewald, CEO van DyeMansion
- Interview met expert:Duncan McCallum, CEO van Digital Alloys over Joule Printing en de toekomst van Metal 3D Printing
- Expertinterview:James Hinebaugh van Expanse Microtechnologies
- Expertinterview:Nanoe CEO Guillaume de Calan over de toekomst van keramisch 3D-printen
- Interview met expert:CEO van PostProcess Technologies over het oplossen van het knelpunt in de nabewerking voor additieve productie
- Expertinterview:medeoprichter van Carbon, Philip DeSimone, over de overgang naar productie met hoog volume met 3D-printen
- Expert Interview:Jabil's Rush LaSelle over de toekomst van additieve productie
- Gebruikmaken van digitale technologie in de productie
- Bedrijfsprofiel:Productie- en technologie-expert SourceDay
- De opkomst van digitale platforms in de maakindustrie