Expertinterview:James Hinebaugh van Expanse Microtechnologies
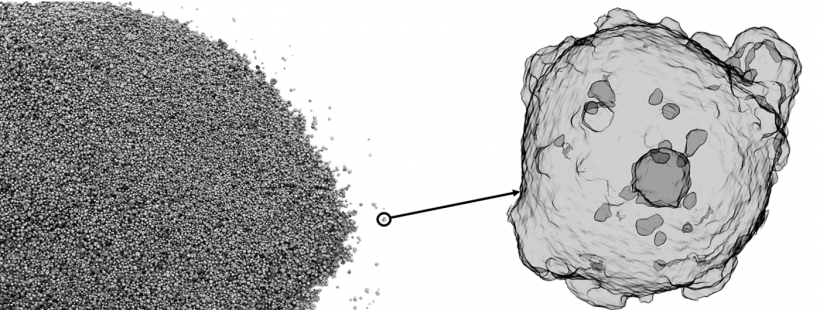
Materiaal- en onderdeelinspectie is een essentiële fase in het additieve fabricageproces - en toch is het niet zonder uitdagingen. Vooral voor toepassingen in de lucht- en ruimtevaart, de medische sector of de auto-industrie is het cruciaal om ervoor te zorgen dat een onderdeel perfect is, zonder verborgen gebreken. Problemen zoals porositeit, holtes en insluitsels, met name voor metalen onderdelen, kunnen echter gemakkelijk het verschil maken tussen een geslaagde of mislukte afdruk. Hoewel er verschillende methoden zijn om de kwaliteit van materialen en onderdelen te verifiëren, zijn er maar weinig in staat om problemen diep in het onderdeel zelf te detecteren.
X-ray CT-scantechnologie zou wel eens de oplossing kunnen zijn voor de inspectie van materialen en onderdelen voor additive manufacturing. Expanse Microtechnologies is een bedrijf dat fabrikanten helpt bij het optimaliseren van hun materialen, onderdelen en productieprocessen voor 3D-printen met behulp van haar gepatenteerde Microscale X-ray CT-technologie. We spraken met James Hinebaugh, president en medeoprichter van Expanse Microtechnologies, om te zien hoe de innovatieve technologie bedrijven kan helpen bij het perfectioneren van hun productieprocessen.
Kunt u ons iets vertellen over Expanse Microtechnologies?
Expanse Microtechnologies is een bedrijf dat fabrikanten helpt bij het beantwoorden van vragen over hun materialen en productieprocessen. We gebruiken geavanceerde inspectietools om kritische vragen op het gebied van additieve productie en andere geavanceerde productiegebieden te beantwoorden.
In de industrie heb je snelle onderzoeksbehoeften, wat betekent dat je niet kunt wachten tot er een onderzoeksovereenkomst wordt gesloten met een academisch laboratorium. Expanse Microtechnologies overbrugt de ruimte tussen de industrie en de academische wereld. Ons doel is om de instrumenten van academische laboratoria naar industriële klanten te brengen, waarbij we ons specifiek richten op een technologie genaamd Microscale X-ray CT.
Waarom besloot u het bedrijf mede op te richten?
We zijn geïnspireerd door de additive manufacturing-industrie. We zagen dat de industrie brandende vragen had, en toch waren er geen geweldige tools op de markt om bedrijven te helpen deze vragen te beantwoorden en hun productieprocessen te optimaliseren. Voor ons is CT de oplossing - we wilden onze CT-expertise gebruiken, toepassen op het gebied van AM en snelle maar zeer gerichte oplossingen bieden om bedrijven te helpen bij het beantwoorden van belangrijke productievragen.
Wat is Microscale X-ray CT en hoe werkt het?
Microscale X-ray CT stelt u in staat om interne en externe 3D-inspecties van geavanceerde materialen en onderdelen uit te voeren. U kunt ook een bijna eindeloos aantal geometrische kenmerken, defecteigenschappen karakteriseren en bepalen hoe goed het onderdeel is afgedrukt of vervaardigd. Dit soort technologie heeft een enorme leercurve, en daarom zijn er maar heel weinig servicebureaus die enige vorm van service voor CT bieden, en de meeste bieden niet dezelfde tools die je zou kunnen vinden als je een relatie zou beginnen met academisch onderzoekslab.
We hebben geavanceerde beeldverwerkingsmethoden ontwikkeld om bepaalde informatie uit 3D-beelden te halen. Aangezien deze afbeeldingen meerdere gigabytes groot kunnen zijn, is het onze taak om deze informatie op een begrijpelijke manier te presenteren, zodat onze klanten duidelijk kunnen zien waar hun problemen zitten.
We genereren een rapport van de CT-scan dat deze informatie op hoog niveau en toegang tot meer diepgaande gegevens biedt, zodat u correlaties kunt vinden tussen locaties in uw onderdeel en de defecten, evenals de vorm, grootte en de verdeling van die gebreken.
Waarom is röntgen-CT zo belangrijk voor het productieproces?
CT-scanning levert een driedimensionale set van informatie op die op geen enkele andere manier bereikbaar is. Net als bij een microscoop kunt u inzoomen op micron- en submicronniveau en belangrijke vragen beantwoorden. Bovendien kunt u vragen beantwoorden over interne ontoegankelijke functies van een onderdeel - wat anders onmogelijk zou zijn zonder het onderdeel te vernietigen.
Met CT-scanning kunt u duidelijk de doorsneden zien van uw onderdelen of testartefacten die u heeft vervaardigd. Het is alsof je je deel herhaaldelijk doormidden kunt snijden, met plakjes die slechts enkele microns van elkaar verwijderd zijn.
Dit creëert veel driedimensionale informatie die van cruciaal belang is om te begrijpen wat er in uw onderdeel gebeurt. De alternatieve benadering is om alleen een fysieke dwarsdoorsnede te nemen:maar hier moet je raden hoe het eruit ziet boven en onder het fysieke vlak of hopen dat dit een representatief vlak is. Met CT ziet u niet alleen die doorsnede, maar ook duizenden andere doorsneden en begrijpt u hoe de representatieve doorsnede er in werkelijkheid uitziet. We kunnen ook de correlaties zien; waar er bijvoorbeeld porositeit is, zijn er ook vaak oppervlaktedefecten en we kunnen dat terugkoppelen naar de parameters en het gereedschapspad dat we in de eerste plaats op de print hebben aangesloten.
Kunt u uitleggen hoe verschilt uw software van vergelijkbare software op de markt?
Onze software wordt op maat gemaakt. Dit betekent dat we veel vrijheid hebben om ons vertrekpunt en de vragen die moeten worden beantwoord te bepalen, zodat we het probleem vanuit elke gewenste hoek kunnen aanpakken.
Een voorbeeld:in het geval van oppervlakteruwheid ontwikkelen we een tool om een CT-scan te maken en eventuele contouren van het materiaal en onderdeel te matchen. We kunnen dan een contour vinden, die eruit halen en de ruwheid van die contour meten. Op dit moment zijn andere softwarepakketten hier niet op ingericht, omdat er niet veel vraag is naar oppervlakteruwheid van CT - maar in additive manufacturing wel. We kunnen die vraag zien, erop reageren en een tool maken om deze vragen te beantwoorden. Het kost ons twee tot drie weken van ontwikkeling om dit te doen en een herhaalbaar proces te creëren. Tegen die tijd is het klaar om te gaan.
Bij een groot commercieel softwarepakket heb je eerst die marktdruk en zekerheid nodig dat er voldoende marktpotentieel is om een gebruiksvriendelijk analysepakket te maken dat deze vragen kan beantwoorden voordat er iets ontwikkeld en vrijgegeven kan worden. De doorlooptijd voor deze maanden, zo niet jaren, terwijl het voor ons slechts een paar weken duurt om uit te zoeken hoe we een oplossing kunnen creëren en implementeren op basis van de specifieke behoeften van onze klanten.
Wat zijn de soorten bedrijven die u helpt?
We richten ons op vrijwel de hele toeleveringsketen van additive manufacturing. We werken bijvoorbeeld samen met poederfabrikanten, die poeders scannen om vast te stellen of er enige porositeit is of dat er interessante vormverdelingen en grootteverdelingen zijn die essentieel zijn voor het opbouwen van kwaliteit en sterkte-eigenschappen van de onderdelen.
In het geval van machinefabrikanten willen veel bedrijven bepaalde functies aan hun huidige machines toevoegen op het gebied van in-process monitoring of lokale controle van materiaaleigenschappen. Dat vergt veel iteratief testen, daarom ontwikkelen we aangepaste tools zodat ze de belangrijke statistieken kunnen bijhouden als dat nodig is.
We werken ook samen met servicebureaus, die vaak met nieuwe poeders te maken hebben, nieuwe machines proberen in gebruik te nemen of een beter idee willen hebben van hun herhaalbaarheid van de print, waar de porositeit vandaan komt en andere belangrijke vragen.
Eindelijk hebben we klanten die producten op de markt proberen te brengen die alleen mogelijk zijn door middel van additive manufacturing. Dit kunnen bijvoorbeeld bedrijven zijn die medische implantaten maken - we hebben zelfs een klant die hele raketten probeert te printen met behulp van additieve technologieën! We willen heel graag met die bedrijven samenwerken, omdat zij degene zijn die we in de toekomst echt mogelijk willen maken - we willen ze de informatie geven die hen die controle geeft.
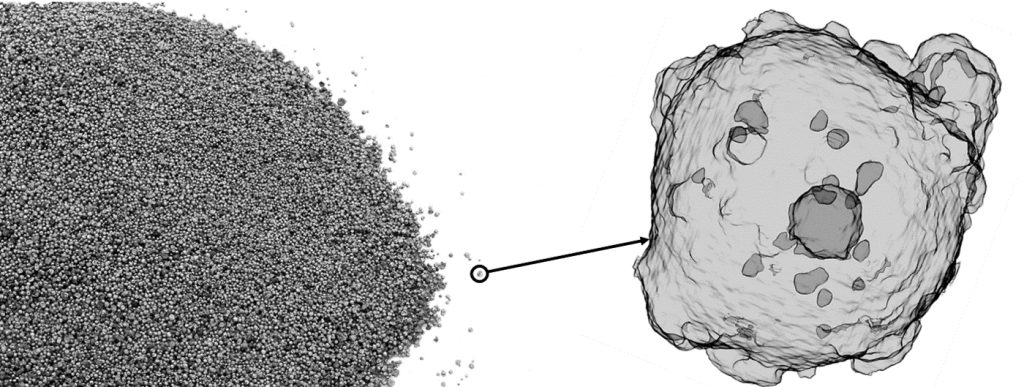
Wat zijn de belangrijkste uitdagingen waarmee deze klanten worden geconfronteerd?
Poeders zijn het belangrijkste aandachtspunt in deze hele toeleveringsketen van additieve productie. Begrijpen wat een goed poeder is dat zich goed verspreidt en goed afdrukt, is een belangrijke zorg voor bedrijven. Er zijn hier veel variabelen, niet alleen tussen de verschillende poeders, maar ook met verschillende machines. U hebt echt een gelijkmatige, uniforme poederlaag van dikte en dichtheid nodig om over poederbedprinttechnologieën te worden verspreid, anders heeft u te veel of te weinig poeder, wat respectievelijk gebrek aan fusie of oversmelting kan veroorzaken.
Het is belangrijk om te begrijpen 1) of er een ideale morfologie of een ideale grootte of morfologische verdeling is die goed kan samenwerken met een grote verscheidenheid aan overschilderers en printers, en 2) hoe we de defecten in poeders kunnen verminderen, zoals insluitsels en intradeeltjesporositeit die, studies hebben aangetoond dat ze vaak vast komen te zitten in een onderdeel en niet kunnen ontsnappen aan het onderdeel tijdens het printproces.
Een ander punt van belang, dat meer experimenteel is, is weten wat u moet doen met alle in-process bewakingsgegevens die al beschikbaar zijn op uw machine of beschikbaar zullen komen. CT zal een cruciale rol spelen bij het verwerken van die gegevens in een onderdeel tijdens het proces en bij het bouwen van inspecties. Universiteiten en machinefabrikanten hebben er veel belang bij om dit probleem op te lossen, maar wat zeker is, is dat veel hoogwaardige technologieën zoals machine learning en computervisie een sleutelrol zullen spelen. Dat is zeker iets dat ik in de gaten zou houden en we bereiden ons voor en werken samen met de juiste partners om voorop te lopen in dat onderzoek.
Kunt u een voorbeeld geven van een succesverhaal van een klant?
Een van onze klanten maakt een medisch hulpmiddel – een met titanium bedrukte wervelkolomklem die wordt geïmplanteerd in het lichaam. Ze hebben een zeer innovatieve oplossing gecreëerd die alleen mogelijk is door middel van additive manufacturing.
De eerste prototypes die ze printten, functioneerden echter niet goed. De onderdelen moesten flexibel worden bedrukt om tijdens het implantatieproces te kunnen worden aangepast, maar ze waren stijf gedrukt. Zonder te weten waar ze het deel doormidden moesten snijden, wisten ze niet waar de afdruk werd gegomd door extra materiaal of het oppervlak op twee tegenover elkaar liggende muren die elkaar raakten.
Binnen twee weken nadat ze ons het onderdeel hadden gestuurd, waren we in staat om het te scannen en de beelden te leveren die ze nodig hadden om te identificeren waar dit mechanische probleem zich voordeed. Hierdoor konden ze snel bepalen wat ze moesten veranderen aan hun productieproces. En dat was gewoon een kwestie van het buildbestand veranderen en de oriëntatie van de build heel licht veranderen om te voorkomen dat de punten die de binding maakten een ongewenste materiële verbinding hadden.
Dus heel snel hadden ze een oplossing voor hun volgende print, waarvoor ze geen enorme set nieuwe analysetools hoefden te ontwikkelen. Het enige dat nodig was, waren mensen die bekend waren met het additieve fabricageproces en de juiste inspectiemogelijkheden om hen te helpen. En we brachten ze heel snel naar hun volgende ontwerpfase.
Hoe ziet u additieve fabricage evolueren?
Ik ben verheugd dat het voor bedrijven steeds gemakkelijker wordt om AM in de toekomst te gebruiken. Op dit moment is het een zeer omslachtige technologie om aan de slag te gaan en een vroege afdrukkwaliteit te hebben op het niveau waar u dat wilt. Ik denk dat er momenteel een toetredingsdrempel is die niet alleen om de kosten gaat, maar ook om een aanzienlijke tijdsbesteding. Dus ik ben verheugd dat zaken als het slimme gebruik van CT, ontwikkelde in-process monitoring en het inzicht dat grote onderzoekslaboratoria ons verschaffen over het proces, deze barrières zullen wegnemen, de prijs van machines en poeders zullen verlagen en de tijdsinvestering zullen verminderen nodig zijn om additieve fabricage te gaan gebruiken.
Bovendien zijn er op dit moment strenge voorschriften van de FAA en FDA met betrekking tot onderdelen die worden geprint, of het nu gaat om ruimtevaart of medisch. Als u momenteel een onderdeel heeft dat is gekwalificeerd en goedgekeurd door de FAA, moet het onderdeel op dezelfde printer worden afgedrukt met exact hetzelfde materiaal zonder enige wijzigingen. Als er iets verandert, moet je bijna altijd terug naar af en je hele proces opnieuw kwalificeren.
We proberen dit probleem actief op te lossen door methoden voor het volgen van de machinekwaliteit te standaardiseren, door te helpen het afdrukgedrag van machine tot machine en van poeder tot poeder te vergelijken, zodat er een manier is om het herkwalificatieproces te verkorten. Dus als u een onderdeel op vijf nieuwe machines moet printen, kost dat niet vijf keer de oorspronkelijke kwalificatie-inspanning. Er moeten snelkoppelingen worden ontwikkeld zodat dit een meer vloeiende productietechniek in dit industriegebied kan zijn.
Enige laatste gedachten?
We willen graag twee belangrijke partners bedanken voor hun bijdrage aan ons succes. Een daarvan is met het laboratorium van de Universiteit van Waterloo Multi Scale Additive Manufacturing (MSAM), geleid door Ehsan Toyserkani en Mihaela Vlasea. Ze hebben ons kunnen laten zien wat er nodig is binnen additive manufacturing en hebben ons in staat gesteld om gebruik te maken van hun AM- en CT-apparatuur.
De tweede is met The Barnes Group Advisors, met wie we werken aan de ontwikkeling van standaardtools voor printen en CT-inspectie. De groep heeft expertise in het integreren van het additive manufacturing-proces in de productie, evenals de daaraan verbonden kwaliteits- en inspectie-eisen. De adviseurs van de Barnes Group weten dat CT een essentieel inspectie-instrument is om te begrijpen hoe onderdelen gemaakt moeten worden en hoe de kwaliteit van onderdelen in de loop van de tijd kan worden bijgehouden.
Ga voor meer informatie over Expanse Microtechnologies naar https://www.expansemicro.com
3d printen
- Interview met experts:Pat Warner, specialist in additieve productie van Renault Formula One Team
- Interview met een expert:professor Neil Hopkinson, directeur 3D Printing bij Xaar
- Interview met een expert:Dr. Alvaro Goyanes van FabRx
- Interview met een expert:Dr. Bastian Rapp van NeptunLab
- Expertinterview:Felix Ewald, CEO van DyeMansion
- Interview met een expert:Ibraheem Khadar van Markforged
- Interview:Dominic Parsonson van Fuji Xerox Australia
- Interview:Professor Ian Campbell van Loughborough University
- Interview met expert:CEO van PostProcess Technologies over het oplossen van het knelpunt in de nabewerking voor additieve productie
- Interview met experts:Sintavia President Doug hedges op het bereiken van serieproductie met 3D-metaalprinten
- Interview met experts:Brian Alexander van Solvay over de ontwikkeling van hoogwaardige polymeren voor 3D-printen