DC diëlektrische sensoren voor de productie van industriële composieten
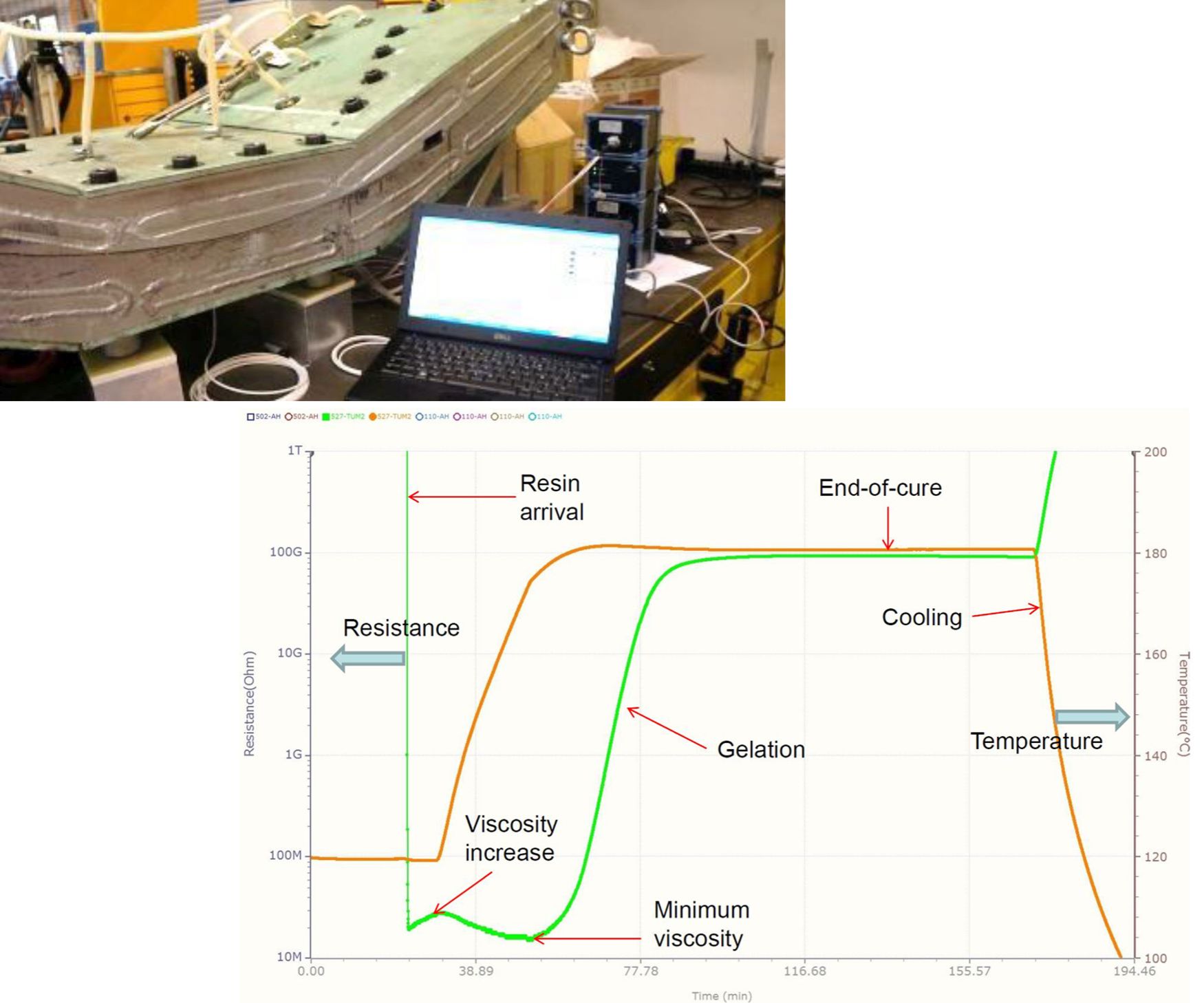
Omdat fabrikanten tegelijkertijd de kosten willen verlagen en de snelheid voor de productie van composietonderdelen willen verhogen, wordt het vermogen om in realtime in de vormprocessen te kijken en de harsstroom, viscositeit, temperatuur, druk en Tg/uithardingstoestand te controleren een onderscheidende factor. Synthesites (Ukkel, België) heeft dit vermogen ontwikkeld. Gebaseerd op resultaten gerapporteerd door het German Aerospace Centre (DLR, Stade) en het National Composites Centre (NCC, Bristol, UK), heeft deze technologie het potentieel om cyclustijden tot 50% te verkorten, met genezingsbeslissingen op basis van Tg en graad uitharding per hars en onderdeel versus conservatieve tijdsperioden op basis van generieke materiaalstudies. Het is in feite een vooruitgang in de richting van de productie van Composites 4.0, waarbij gegevens van sensoren worden gebruikt om processen en apparatuur te besturen, en ook om simulatie en ontwerp te verbeteren.
Ik heb voor het eerst gerapporteerd over Synthesites via het OPTO-Light-project (zie "Thermoplastische overmolded thermosets , 2-minuten cyclus, één cel"). In feite is de mogelijkheid om thermoplasten samen te voegen met thermoharders in OPTO-Light zonder laser-geablateerde oppervlakken werden mogelijk gemaakt door gebruik te maken van in-mold sensoren voor druk, temperatuur, gelijkstroomweerstand (DCR) en diëlektrische analyse (DEA). De DCR-sensoren werden geleverd door Synthesites en die voor DEA werden geleverd door Netzsch (Selb, Duitsland). Beide zijn diëlektrische sensoren die de elektrische eigenschappen van de hars meten. Ik zal de geschiedenis en verschillen in deze technologieën hieronder bespreken.
De technologie die Synthesites heeft ontwikkeld met een reeks commerciële klanten is indrukwekkend, waaronder de industriële productie van windbladen en de met hars doordrenkte vleugels voor de C-serie, nu Airbus 220. Het is ook gedemonstreerd voor een reeks materialen en processen, waaronder autoclaaf -uitgeharde prepreg, harsinfusie en hogedruk harstransfervormen (HP-RTM).

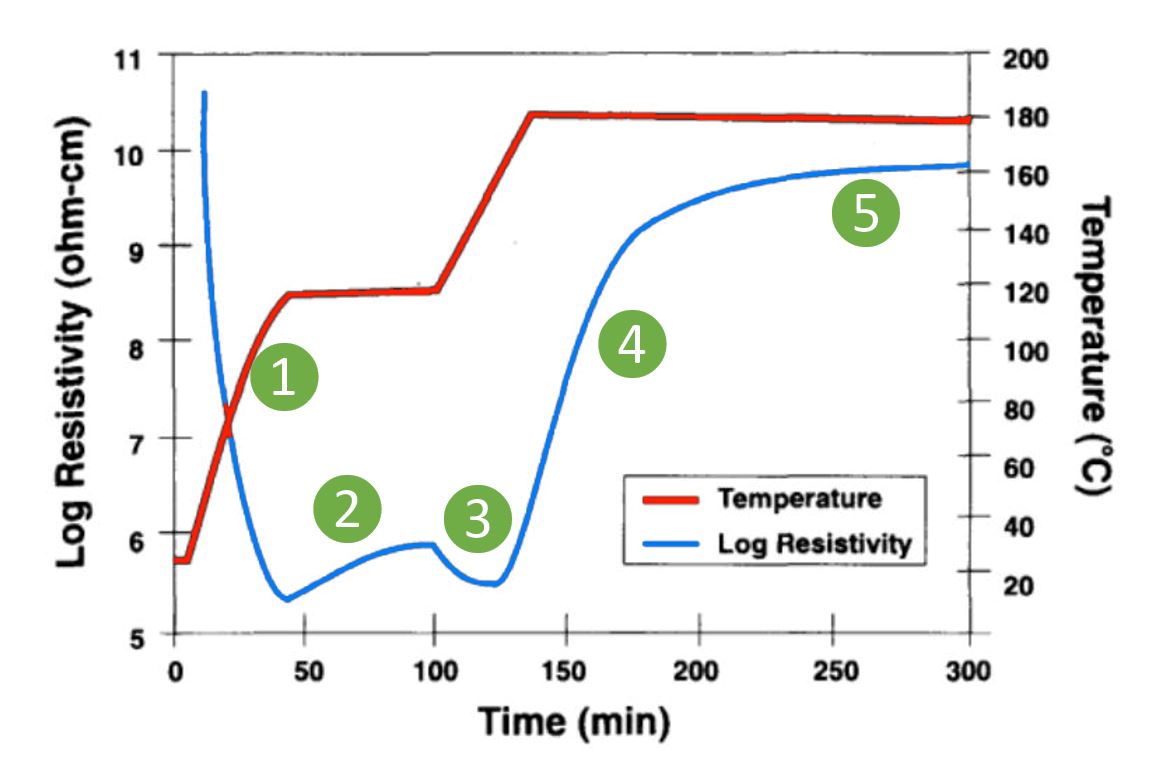
- Aanvankelijke afname in soortelijke weerstand weerspiegelt afname van harsviscositeit tijdens helling tot ≈120 °C.
- Tijdens deze verblijftijd bij 120°C neemt de soortelijke weerstand toe naarmate de harsviscositeit toeneemt als gevolg van harsreactie en verlies van vluchtige stoffen.
- De weerstand neemt weer af en bereikt een minimum als hars wordt verwarmd tot 177°C.
- De weerstand neemt dan snel toe naarmate de uithardingsreactie snel verloopt.
- Toename van de soortelijke weerstand vertraagt naarmate de uithardingsreactie vertraagt, bijna nul helling na 300 minuten als de uithardingsreactie bijna voltooid is.
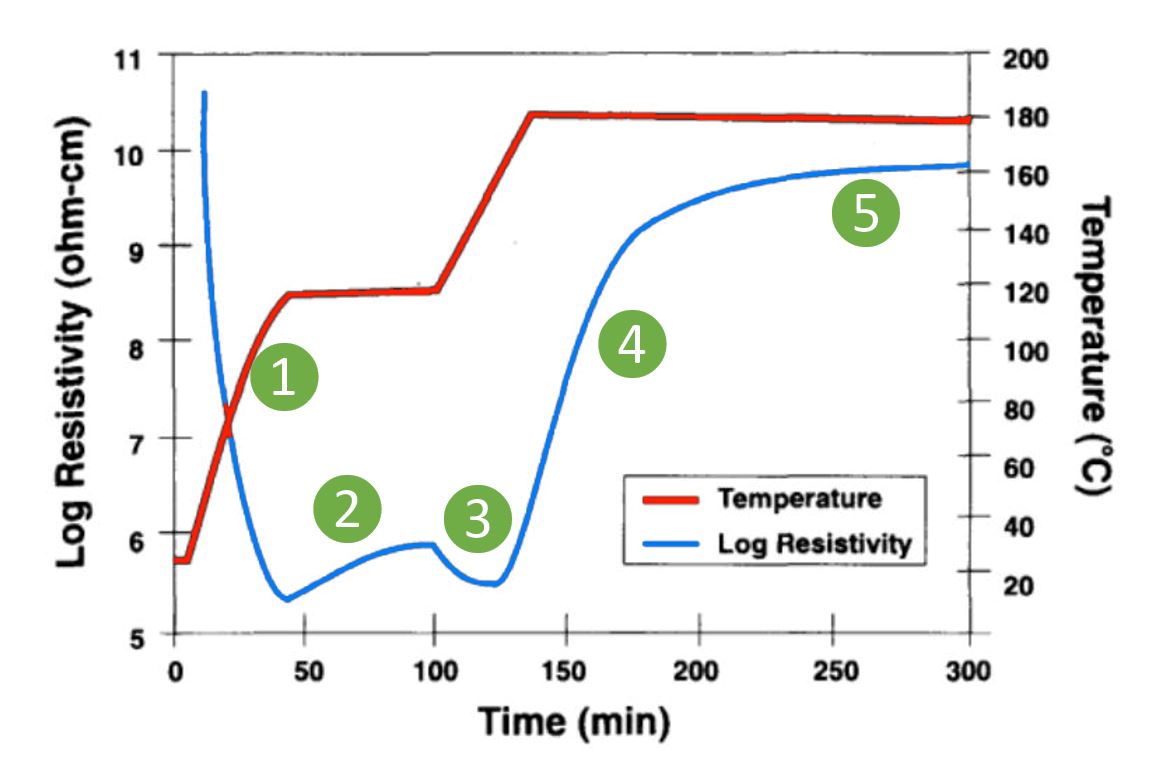
BRON | Niet-destructieve karakterisering van materialen VIII bewerkt door Robert E. Green, p. 385.
Ionengeleiding is omgekeerd evenredig met de harsviscositeit vóór gelering en met stijfheid na gelering (hoge ionenmobiliteit, lage harsviscositeit en lage stijfheid). De inverse van ionengeleiding, de soortelijke weerstand, houdt dus direct verband met veranderingen in viscositeit/stijfheid in de matrixhars.
Het is aangetoond dat een toename van de soortelijke weerstand correleert met een toename in Tg. Dit is de basis van gelijkstroomweerstand (DCR), wat gewoon DEA is met gelijkstroom (DC), en de beschrijving die aanvankelijk werd gegeven aan het proces dat Synthesieten ontwikkelden.
Zoals hierboven uitgelegd, is deze techniek voor het gebruik van gelijkspanning voor DEA gebaseerd op correlaties tussen soortelijke weerstand en uithardingstoestand. Deze werden in 1962 gerapporteerd door R.W. Warfield in "Properties of Crosslinked Polymers as Evidenced by Electrical Resistivity Measurements", Makromoleculare Chemistry, vol. 58. (Zie onderaan voor referenties die in deze sectie worden gebruikt.)
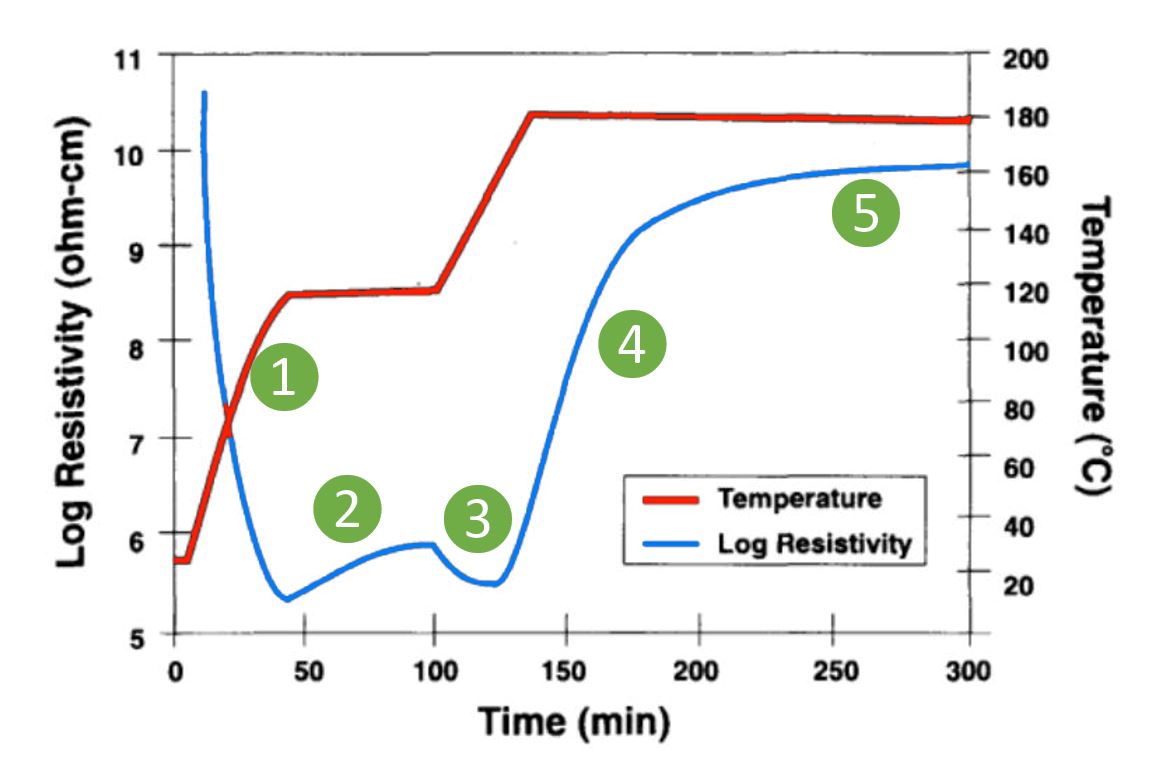
Geschiedenis van DEA- en AC- versus DC-sensoren
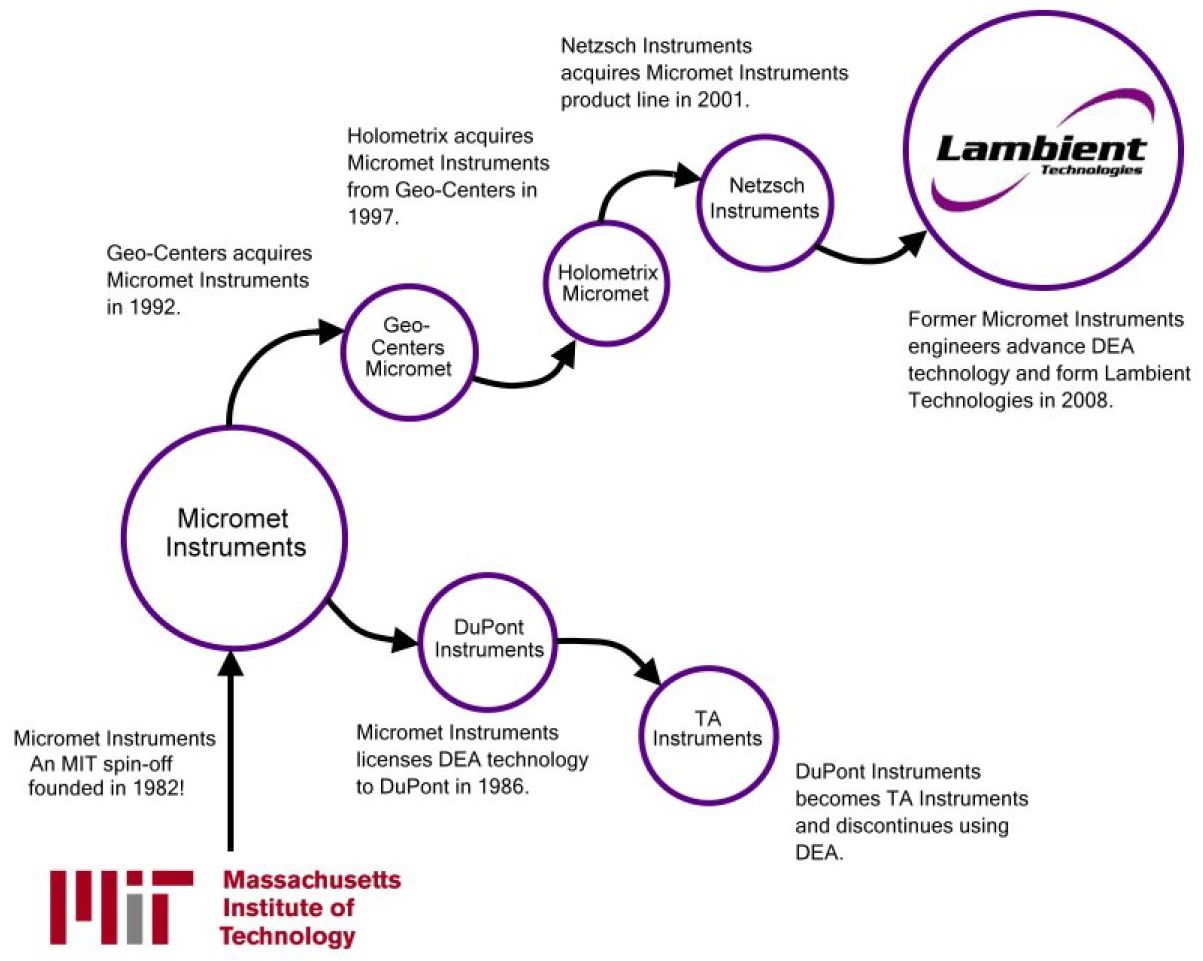
"Het idee van genezingsmonitoring is vrij oud", legt dr. Nikos Pantelelis, directeur van Synthesites, uit. “In de jaren tachtig werd de methode van diëlektrische detectie als volwassener beschouwd dan andere, zoals optische vezels. MIT (Massachusetts Institute of Technology) werkte eraan en probeerde het in productie te implementeren. Deze technologie is wat Netzsch vandaag heeft gekocht en gebruikt.”
Synthesites is opgericht in 2008. "We hebben onze technologie helemaal opnieuw ontwikkeld met behulp van elektrische sensoren met gelijkstroom, niet met wisselstroom", vertelt Pantelelis. "Voor ons is het nadeel van het gebruik van conventionele AC-diëlektrische sensoren de vereiste om de hars op een reeks frequenties te exciteren en vervolgens de impedantierespons voor verschillende signalen te meten. Het is niet alleen een uitdaging om al deze gegevens te verwerken, maar naarmate de hars verandert van vloeibaar naar vast, moet je je concentreren op verschillende signaalfrequenties om de juiste informatie te verkrijgen."
Pantelelis zegt dat Synthesites DC-sensoren een zeer lage geleidbaarheid en hoge weerstand kunnen meten, "wat nodig is om de transformatie van harsen tijdens uitharding te meten." Hij beweert dat het gebruik van conventionele DEA op slechts één frequentie om het eenvoudiger te maken geen nauwkeurige gegevens oplevert. “We hebben niet meerdere frequenties maar passen gewoon een constante spanning toe. Het nadeel is dat deze benadering erg smal is, wat betekent dat het goed werkt voor zeer specifieke toepassingen zoals harsuitharding, maar niet voor alles. Wanneer we echter de prestaties van onze apparatuur vergelijken met conventionele DEA, kan de onze het hele bereik van uitharding meten, zelfs bij lagere temperaturen. Bedrijven die instrumenten en diensten leveren buiten composieten, houden niet van onze aanpak omdat deze te weinig parameters heeft om af te stemmen.”
Dit is geen probleem voor Synthesites omdat het specifiek op composieten is gericht. "Onze aanpak werkt goed in een breed scala aan composietharsen en -processen, waaronder thermoharders, RTM, prepreg en zelfs reactieve thermoplasten zoals Elium." (Elium is de thermoplast met lage viscositeit van Arkema (Colombes, Frankrijk) die kan worden verwerkt met behulp van harsinfusie.)
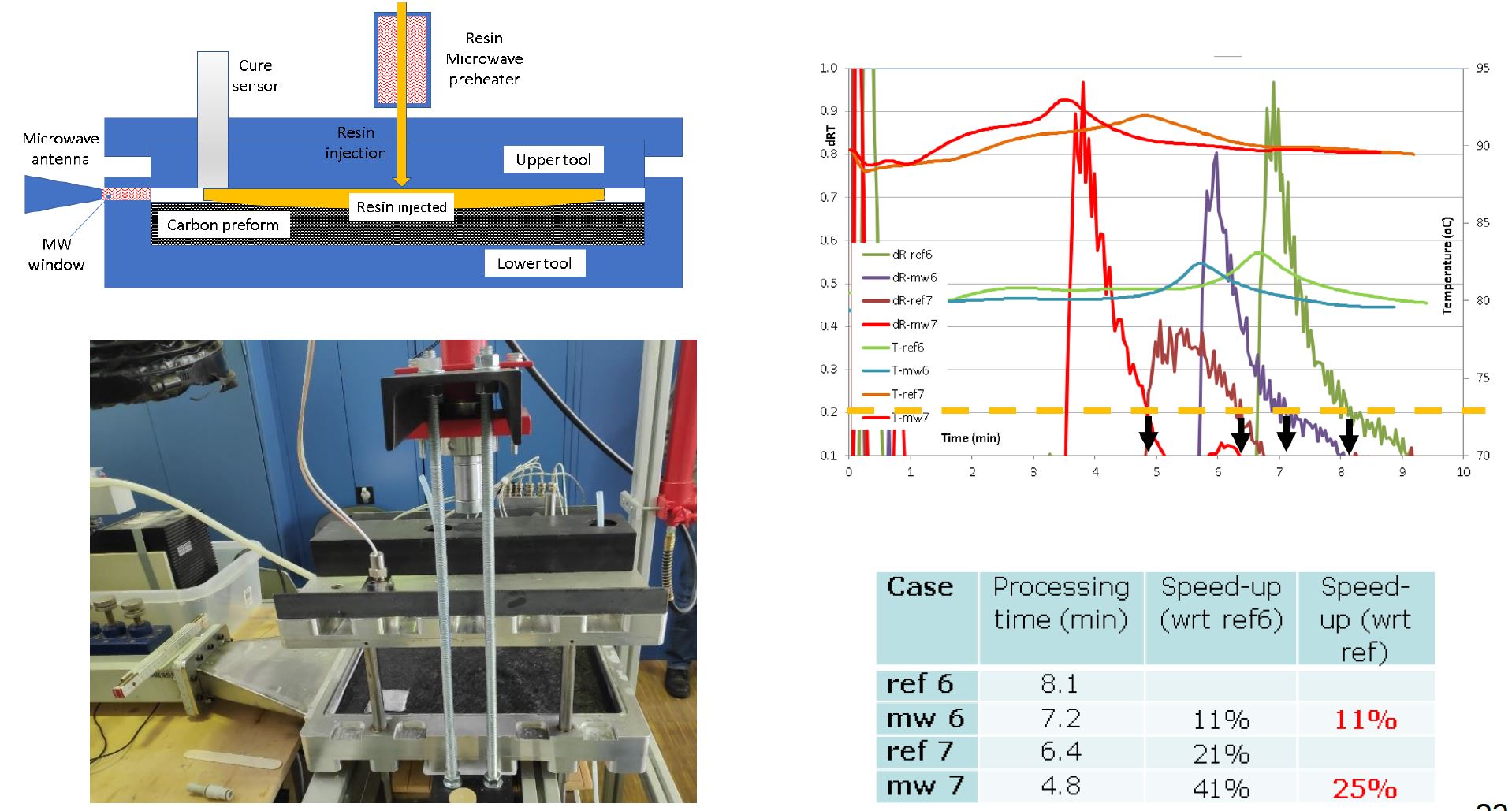
Als DEA met DC bekend was in de jaren zestig, waarom kregen AC-sensoren dan de voorkeur in de jaren tachtig en in de toekomst? "Dertig jaar geleden was de technologie voor DEA met behulp van DC-sensoren nog niet zo ontwikkeld", merkt Pantelelis op. “Maar we hebben onze aanpak verder ontwikkeld om zeer soepele en nauwkeurige metingen voor industriële productie te leveren. We hebben onze systemen gedemonstreerd en verder ontwikkeld met klanten zoals GE Aviation (Batesville en Ellisville, Miss., V.S.) en Bombardier, die grote onderdelen verwerken met vloeibare hars. Onze systemen worden ook elke dag gebruikt bij de productie van windbladen en hebben aangetoond dat ze geschikt zijn voor industriële productie van in de autoclaaf uitgeharde prepreg-laminaten."
Procesbeheersing
Pantelelis legt uit hoe Synthesites DC-sensoren slechts een onderdeel zijn van een geïntegreerd systeem om de verwerking en uitharding van composieten te bewaken. “We meten direct weerstand en temperatuur, en daaruit berekenen we online viscositeit, geleringsgraad en uithardingsgraad. We gebruiken duurzame in-mold sensoren maar ook poortsensoren en in-line sensoren voor harsinlaten, -uitlaten en aanvoerlijnen, evenals wegwerpsensoren op onderdelen. Je gebruikt de sensoren alleen waar je ze nodig hebt.”
De temperatuursensoren zijn platina-weerstandstemperatuurdetectoren (RTD's), die een veel hogere nauwkeurigheid (binnen 0,1°C) bieden dan thermokoppels, evenals een jarenlange stabiliteit ten opzichte van de meetafwijking die mogelijk is met thermokoppels. RTD's zijn standaarduitrusting in veel industriële toepassingen. Poortsensoren (zie procescontrolediagram hieronder) zijn binair en rapporteren de harsstroom als aan of uit, hoewel er een tweede versie is die ook viscositeit kan rapporteren. Synthesites heeft sensoren ontwikkeld voor gebruik met koolstofvezel zonder risico op galvanische corrosie, sensoren die door een vacuümzak kunnen worden gebruikt en gevormde in-mold-sensoren die passen bij de vormgeometrie.
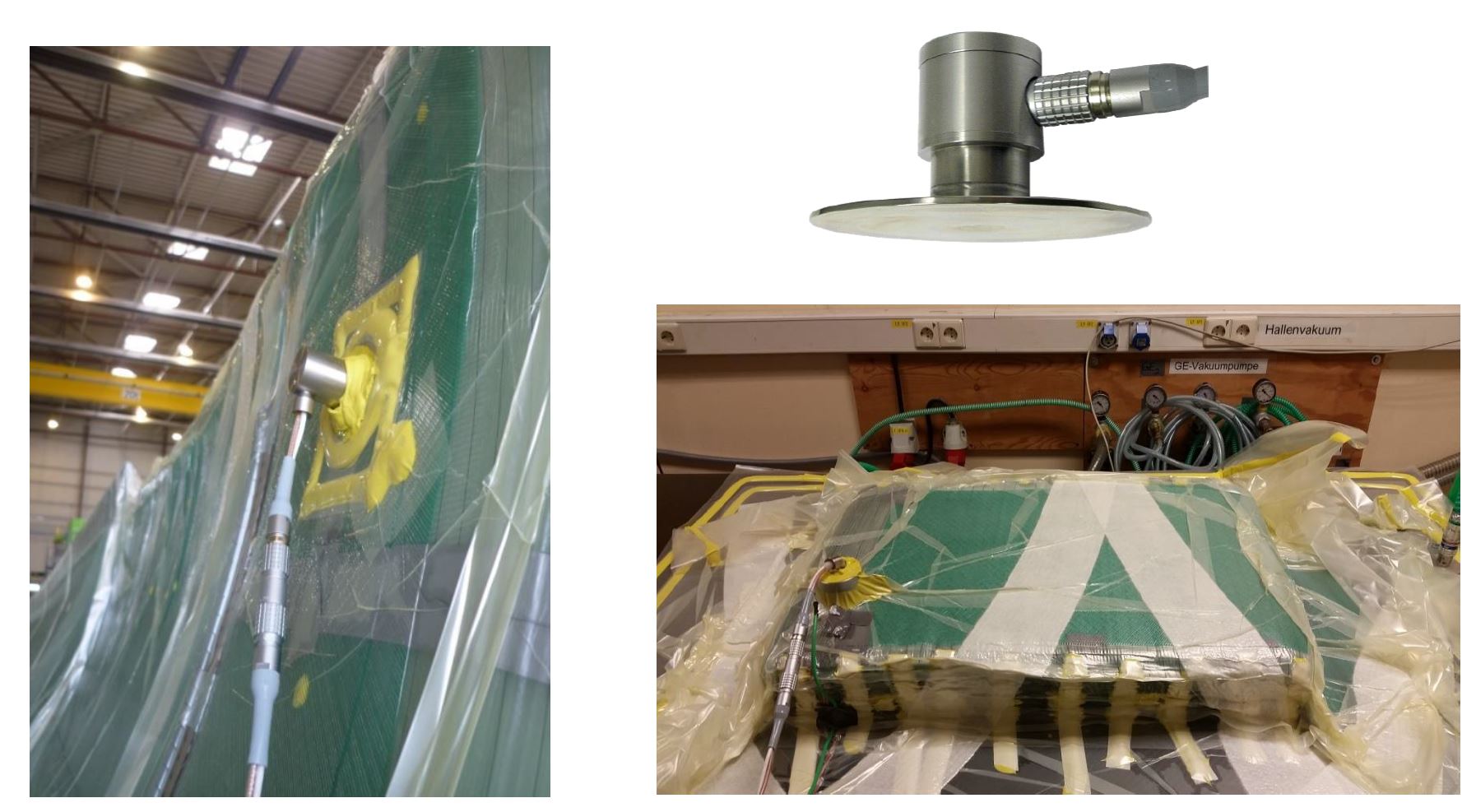
De volgende componenten zijn OPTIFLOW en OPTIMOLD data-acquisitie-eenheden. OPTIFLOW biedt in situ, realtime monitoring van harsaankomst en temperatuur voor het gieten van vloeibare composieten. Het verifieert en registreert de harsstroom en kan productieafwijkingen tijdens harsinfiltratie identificeren. OPTIMOLD gebruikt temperatuur- en harsweerstandsmetingen om berekeningen te maken en de toestand van de hars te bewaken, inclusief mengverhouding, chemische veroudering, viscositeit, Tg en mate van uitharding. Het kan worden gebruikt met prepreg- en vloeibare vormprocessen.
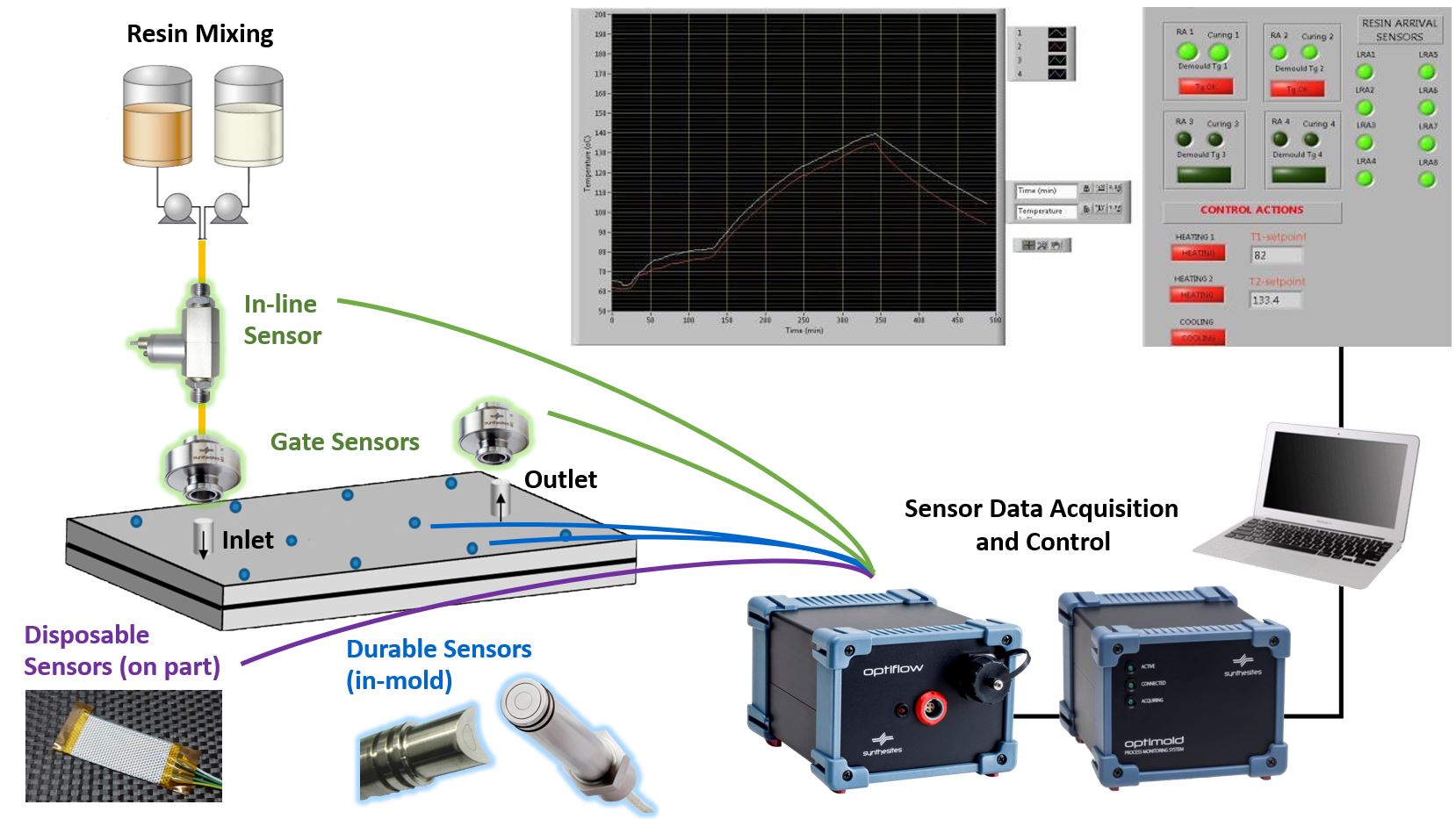
OPTIFLOW- en OPTIMOLD-units worden bestuurd door OPTIVIEW-software. “Deze software zorgt voor data-acquisitie en opslag en wordt gratis meegeleverd met onze apparatuur”, legt Pantelelis uit. “We bieden ook Online Resin State (ORS)-software aan, een meer geavanceerde optie die klanten extra kunnen kopen. Het verzamelt input, maakt online berekeningen en stuurt output voor intelligente procescontrole.”
Zowel de OPTIFLOW- als de OPTIMOLD-systemen controleren continu of de sensoren zijn aangesloten en dat de meetwaarden binnen het bereik liggen. "Als u op deze sensoren vertrouwt voor procescontrole, is het absoluut noodzakelijk dat het systeem alarmeert als een sensor niet werkt of als de meetwaarden de voorgeschreven limieten overschrijden", zegt Pantelelis. Beide systemen hebben ook relaisuitgangen voor het aansturen van procesapparatuur. Toevoerleidingkleppen kunnen bijvoorbeeld open of gesloten zijn op basis van harsaankomstgegevens, en verwarmings-/koelapparatuur kan worden beheerd op basis van harsviscositeit. "Je kunt output van druksensoren in OPTIMOLD invoeren", merkt Pantelelis op, "en zo de druk in de mal regelen op basis van viscositeitsgegevens."
Metingen en typische gegevenscurves
De onderstaande schermafbeeldingen tonen OPTIMOLD-metingen van RTM-proeven (HP-CRTM) onder hoge druk bij NCC (Bristol, VK). De eerste set, van een eenvoudige proef bij 115 °C, laat zien hoe realtime metingen van elektrische weerstand en temperatuur van hars worden omgezet in geschatte viscositeit en Tg door ORS-software.
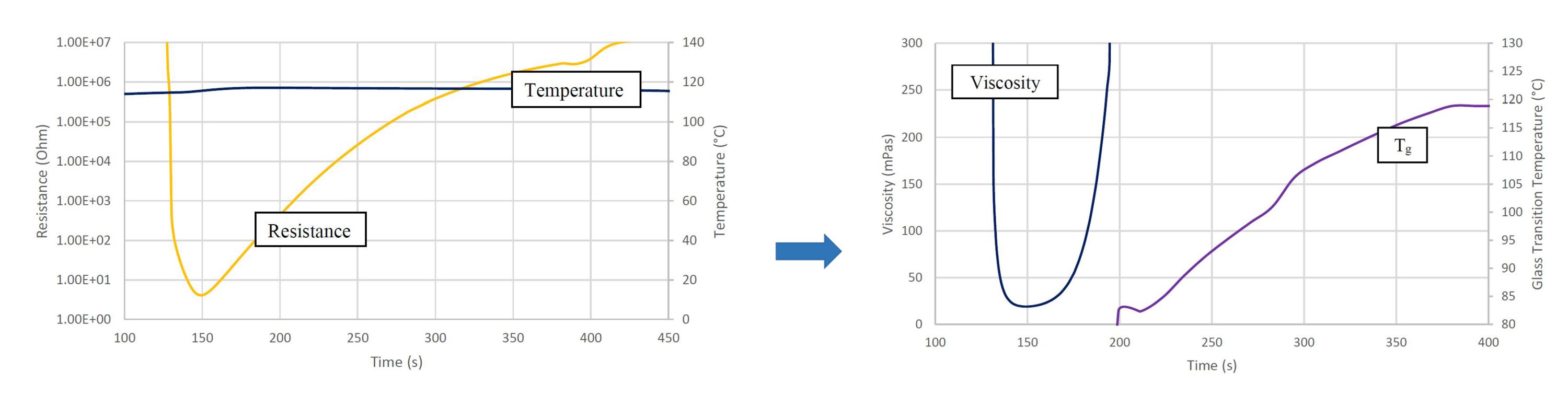
In de onderstaande grafieken, elektrische weerstand en temperatuur (bovenste grafieken) werden opgenomen op 110° (links) en 120°C (rechts). Onder de weerstand (R) en temperatuur (T) aflezingen zijn de grafieken met de berekende viscositeit en Tg bij 110°C (links) en 120°C (rechts) . Deze metingen waren van twee OPTIMOLD-sensoren in de bovenste malhelft (Sn.1 en Sn.2, onderste foto ) terwijl de caviteitsdruk werd geregistreerd met behulp van twee Kistler 6162A-druksensoren (Sn.3 en Sn.4).
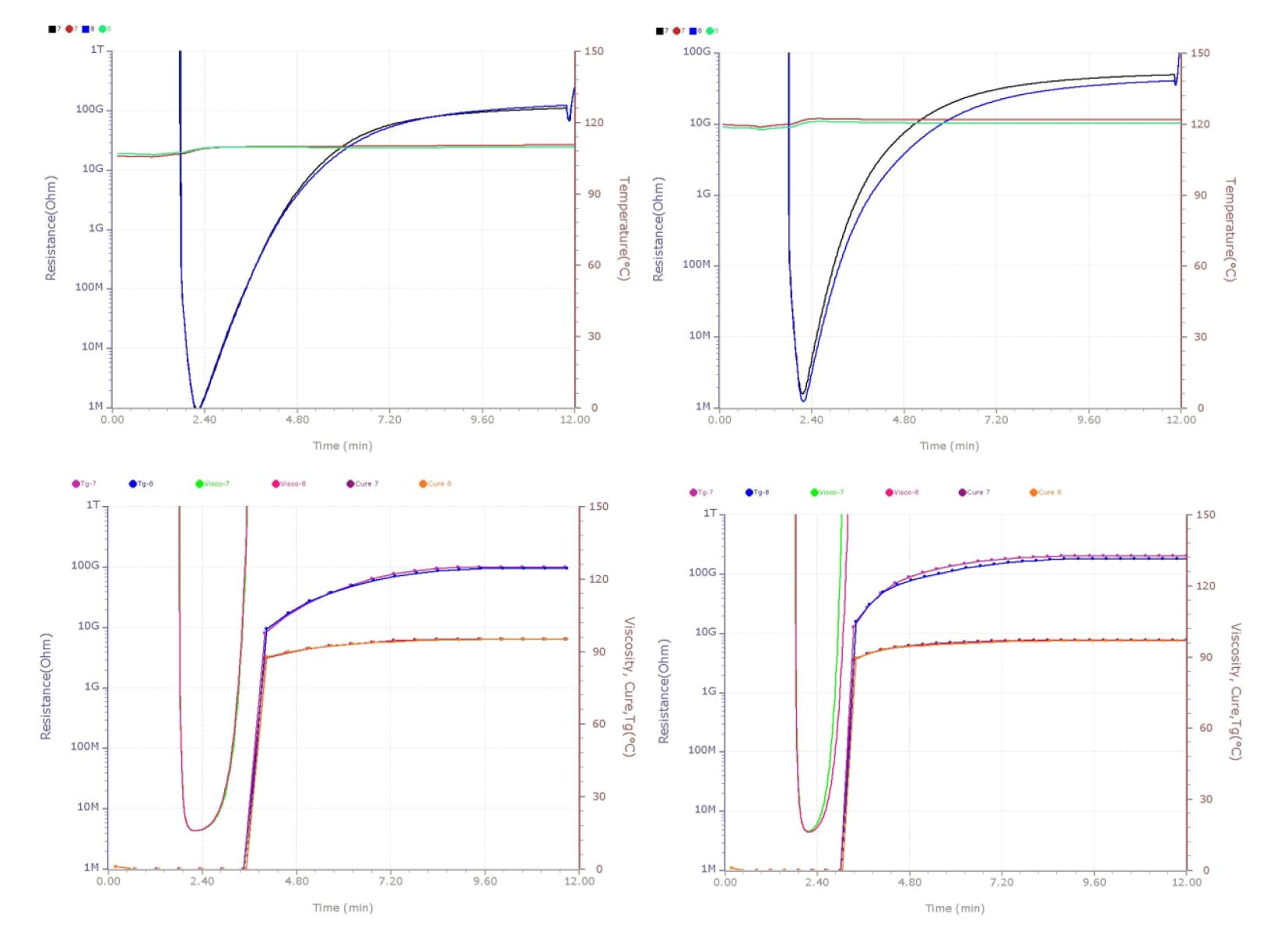
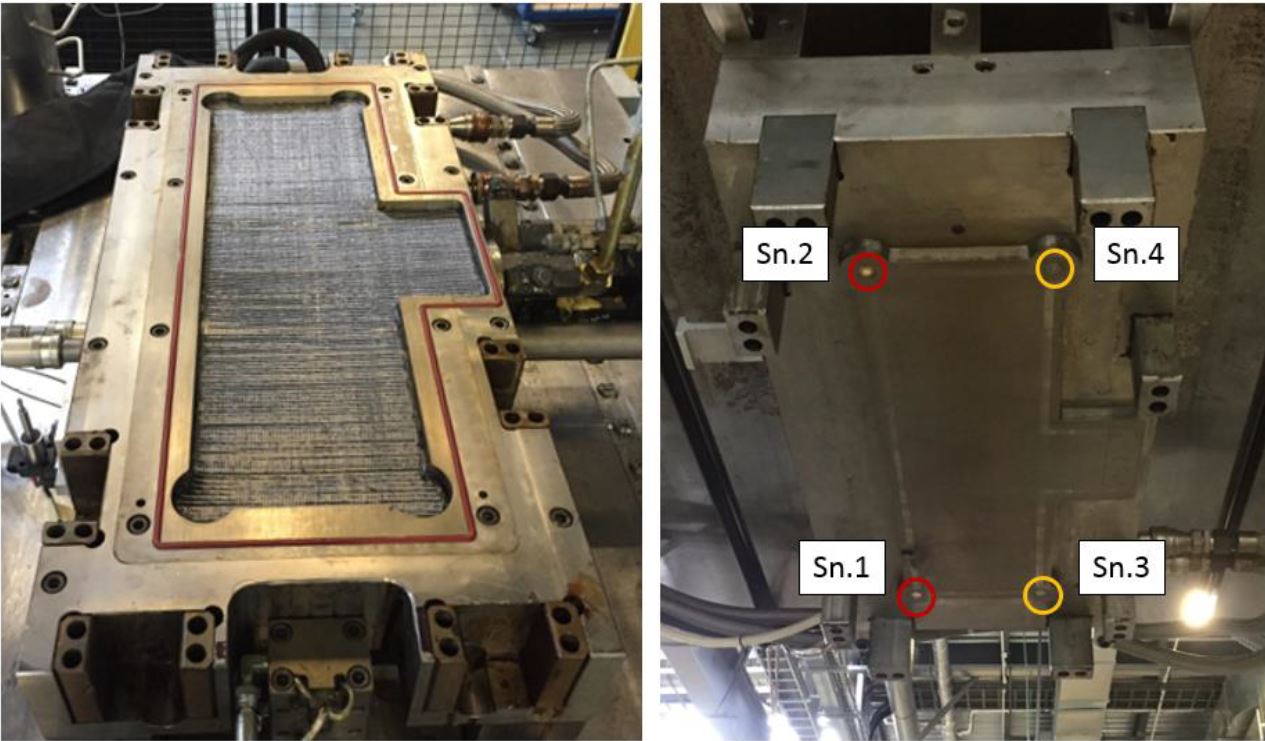
Alle gegevens die door de in-mold-sensoren en de pers- en injectieapparatuur worden geregistreerd, kunnen worden verzameld in een enkel logbestand, waardoor een gedetailleerd beeld ontstaat van het fabricageproces voor elk gecreëerd onderdeel.
Verkorting van de uithardingstijd
"We hebben het potentieel om de uithardingstijd met meer dan 30% te verkorten, omdat de fabrikant de Tg in realtime kan zien, zodat ze kunnen beslissen wanneer ze de uithardingscyclus moeten stoppen", legt Pantelelis uit. “Ze hoeven niet te wachten om een langer dan noodzakelijke legacy-cyclus af te ronden. De legacy-cyclus voor RTM6 is bijvoorbeeld 2 uur bij 180°C voor volledige uitharding. We hebben gezien dat dit bij bepaalde geometrieën kan oplopen tot 70 minuten.”
Het doel is dan om het proces te stoppen zodra de genezing is voltooid? "Het gaat niet om volledige uitharding, maar om het bereiken van het uithardingsniveau dat elk onderdeel nodig heeft", zegt Pantelelis. “Volledige genezing duurt te lang. De sleutel is om te kunnen zien wanneer voldoende genezing is bereikt. Fabrikanten van windbladen hebben een streefwaarde Tg. Als ze dat bereiken, kunnen ze beginnen met afkoelen. Er is dus behoefte aan een sensor die in realtime zeer nauwkeurige Tg-metingen kan geven.”
Synthesites voltooide een demonstratieproject met Hutchinson (Parijs, Frankrijk) om een ophangingsblad voor auto's te produceren gemaakt met glasvezel/epoxy en RTM voor het door de EU gefinancierde ECOMISE-project (Enabling Next Generation COMmosite Manufacturing by In-Situ Structural Evaluation and Process Adjustment, 2013 -2016). Het doel van dit project was om de RTM-cyclus te optimaliseren op basis van realtime procesbewaking:
- De eerste verwarmingshelling zou worden geactiveerd door voltooiing van de harsinfiltratie op basis van sensoren.
- De tweede verwarmingshelling zou worden geactiveerd door voltooiing van de uitharding op basis van Tg-berekening.
- Afkoeling zou worden geactiveerd door voltooiing van de nabehandeling op basis van Tg-berekening.
Het Synthesites-systeem omvatte twee (2) in-mold sensoren voor uitharding (CS1, CS2), één (1) in-mold sensor voor harsstroom en temperatuur (Flow Sensor 1) en acht (8) wegwerp sensoren voor harsstroom/temperatuur — vier (4) ingebed in het testonderdeel en vier (4) bevestigd aan het gereedschapsoppervlak.
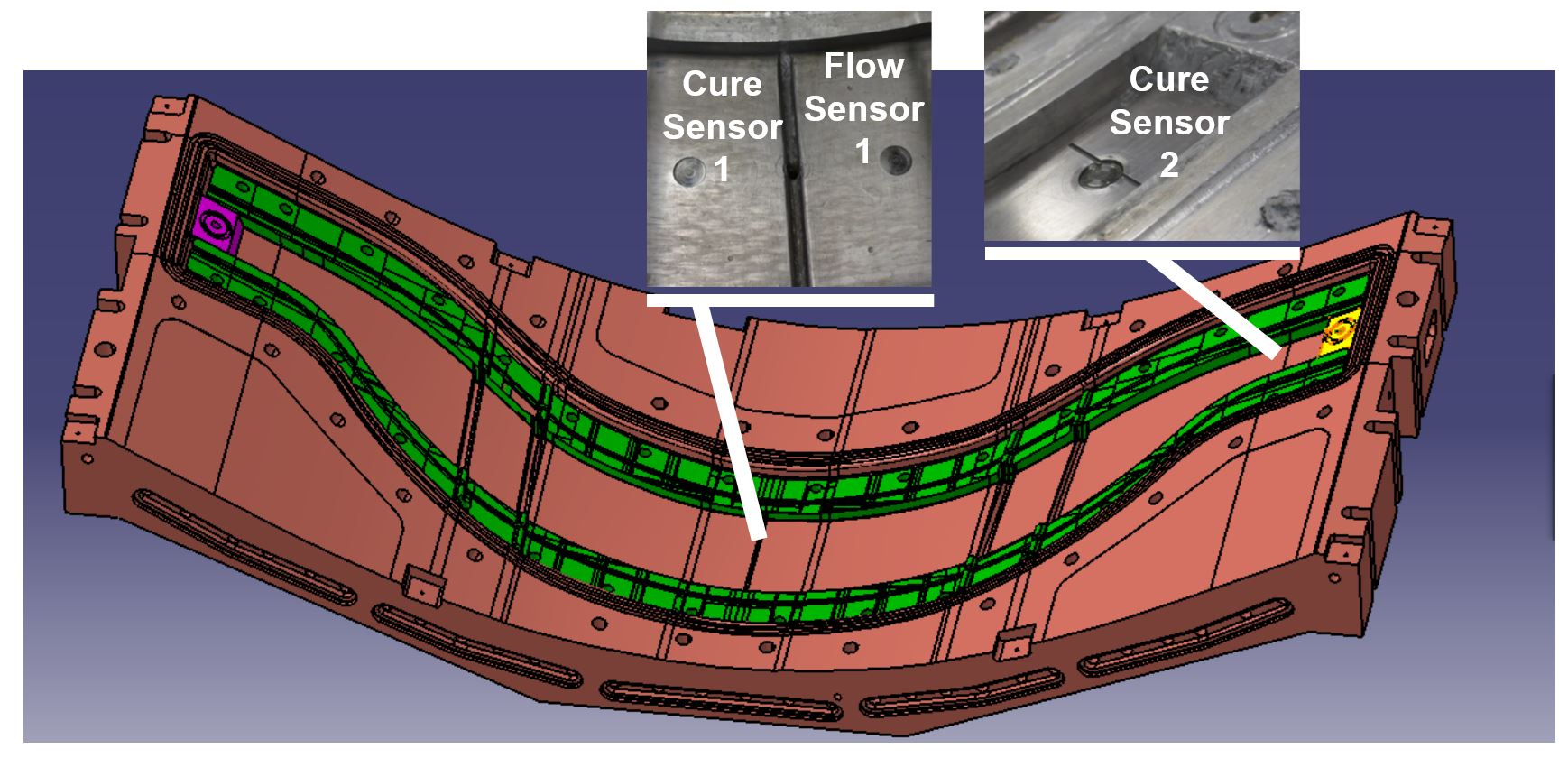
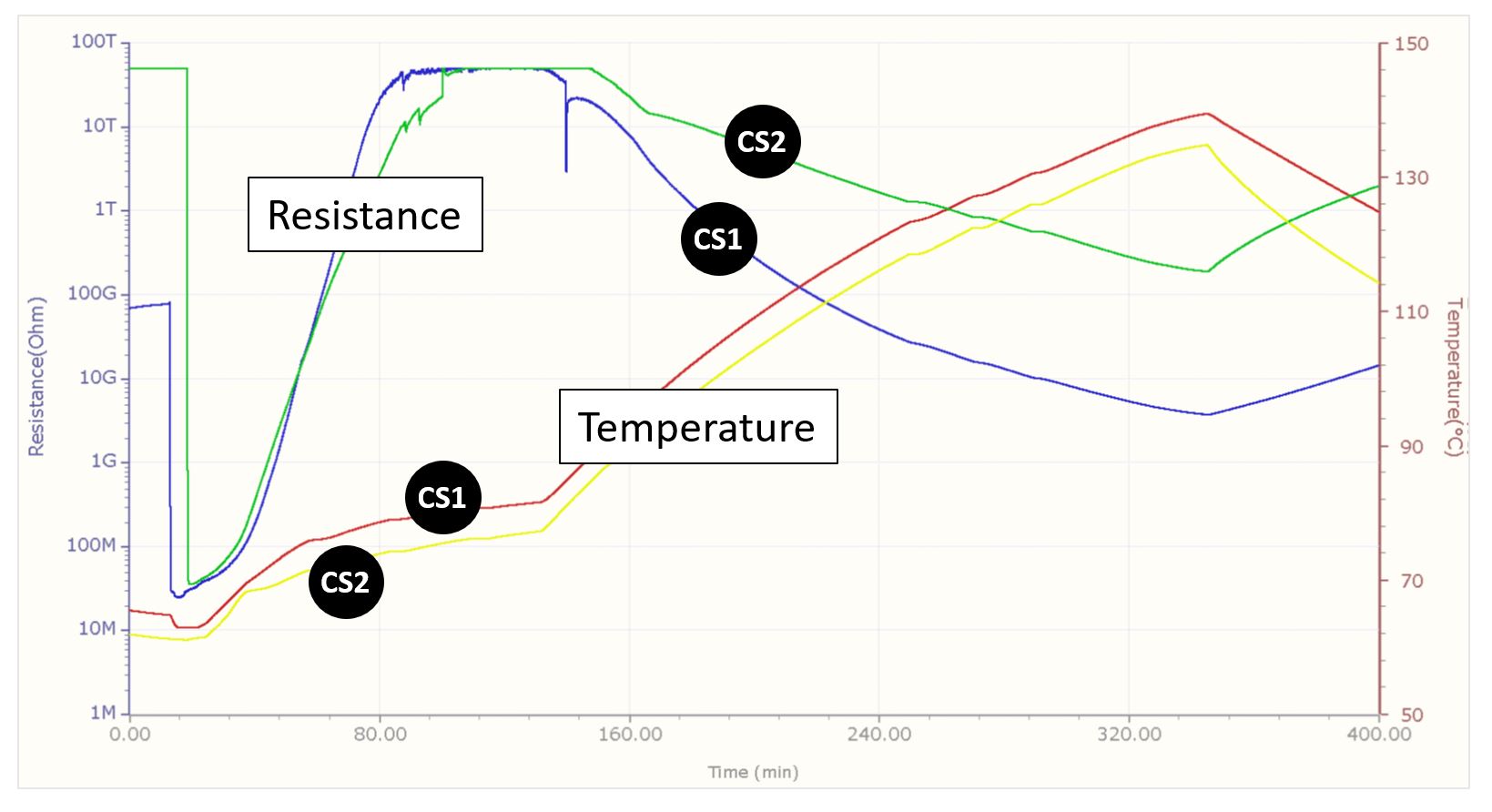
"OPTIMOLD- en OPTIFLOW-units kunnen via ethernet met elkaar worden verbonden, zodat alle sensoren in één Optiview-sessie kunnen worden opgenomen", legt Pantelelis uit. "Zo werden CS1 en CS2 aangesloten op twee OPTIMOLD-units, de in-mold flowsensor 1 en de acht disposable flowsensoren werden aangesloten op drie OPTIFLOW-units."
Dit systeem van sensoren, OPTIMOLD/OPTIFLOW data-acquisitie-eenheden en OPPTIVIEW/ORS-software werd vervolgens toegepast tijdens RTM-vormproeven om doelen vast te stellen voor verschillende procesfasen, waaronder harsinjectie/infiltratie en twee Tg-doelen. "Dit was een dik onderdeel gemaakt van unidirectionele vezels en Huntsman epoxyhars", zegt Pantelelis. "In dit geval hebben we stroomdraadsensoren gebruikt om de stroom binnen deze UD-lagen te controleren, die doorgaans dicht opeengepakt zijn en problemen kunnen veroorzaken tijdens harsinfiltratie."
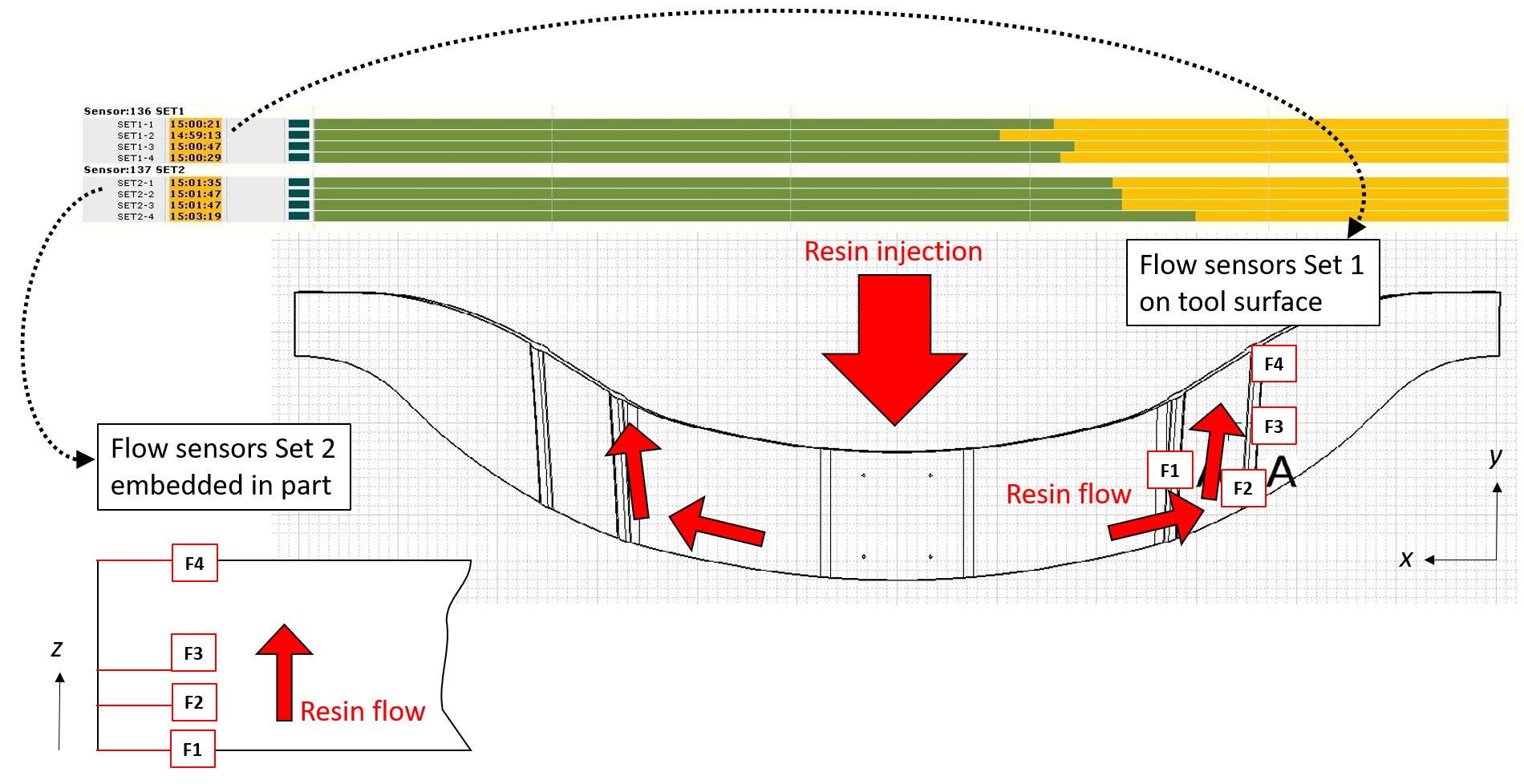
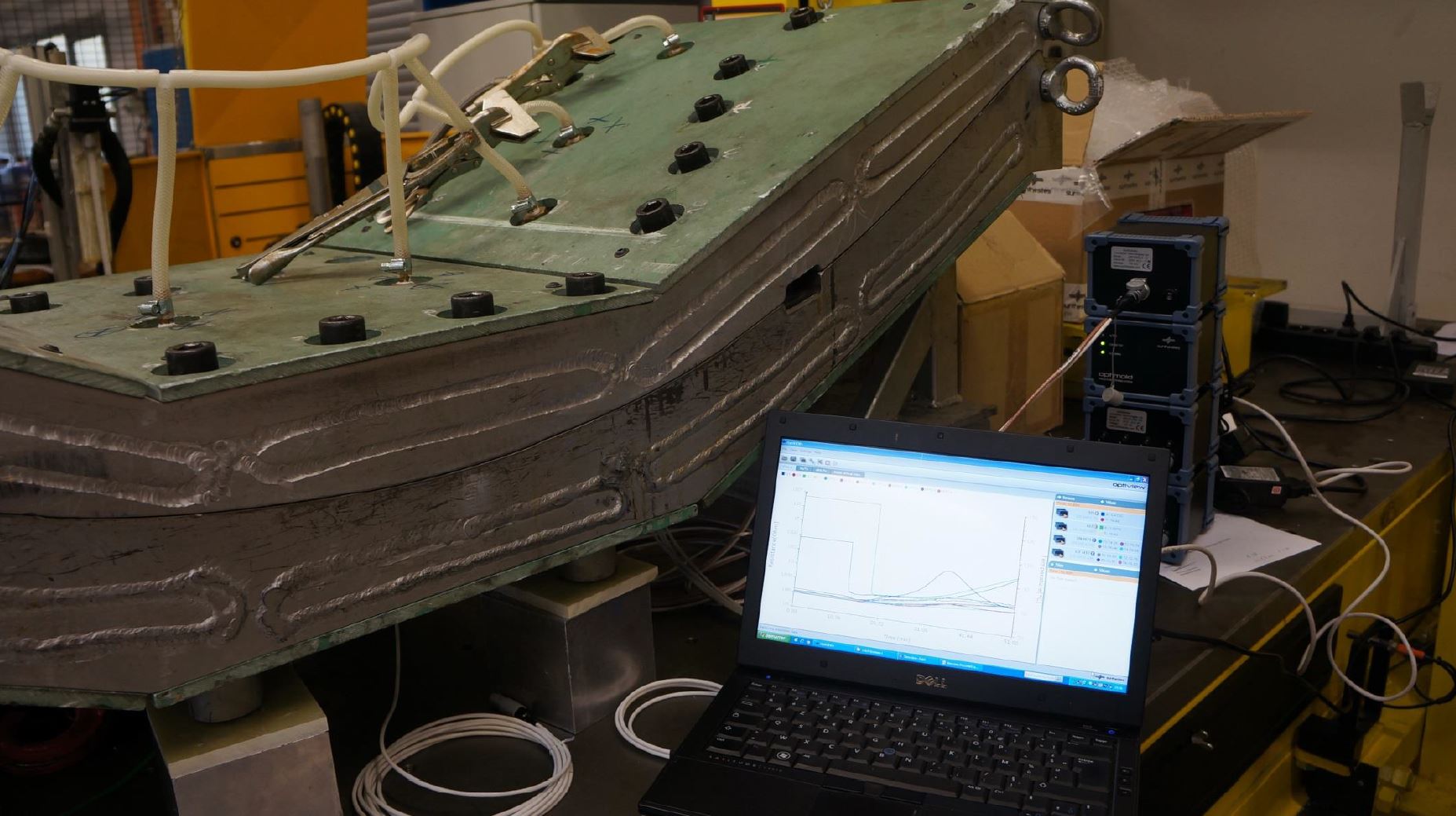
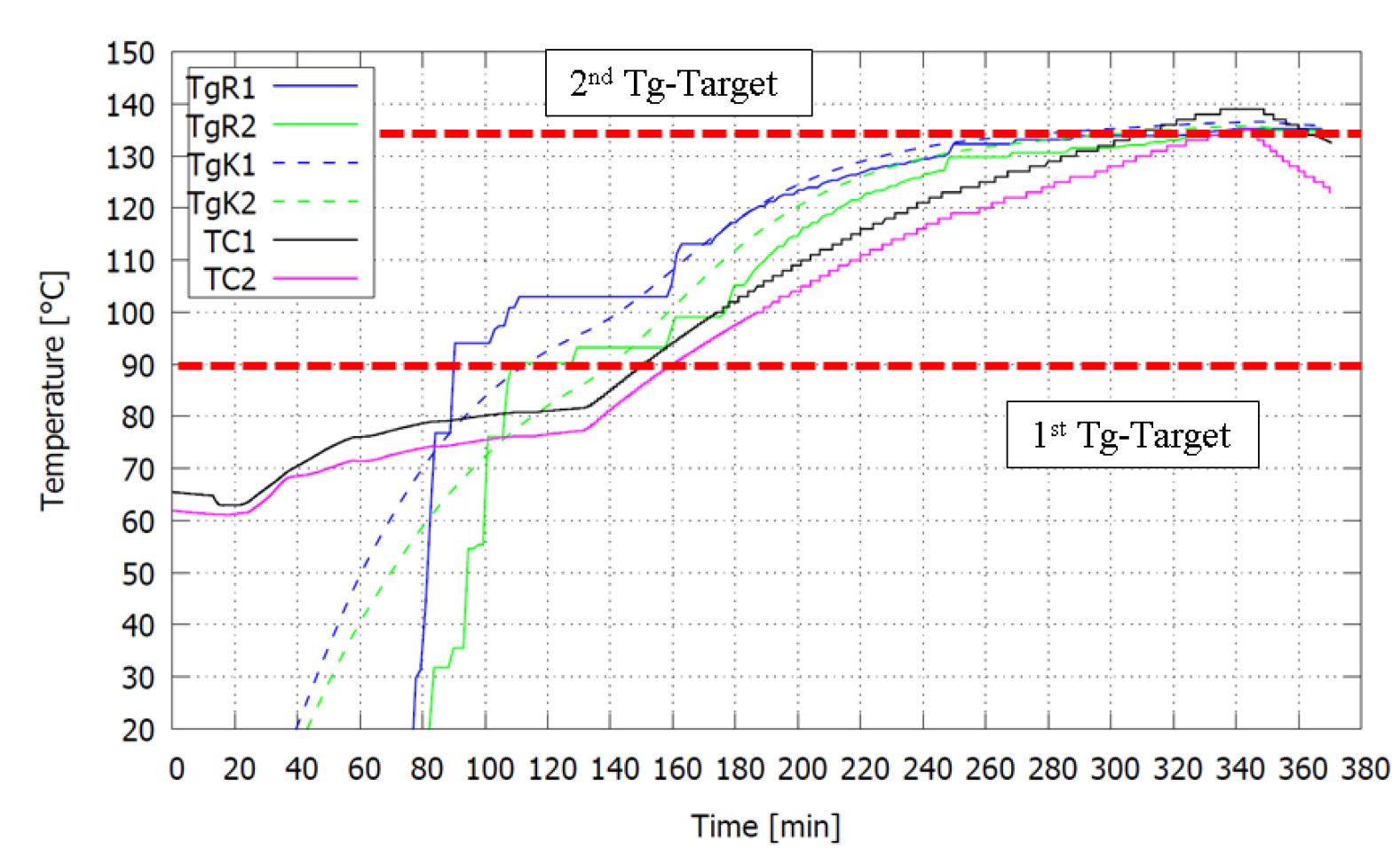
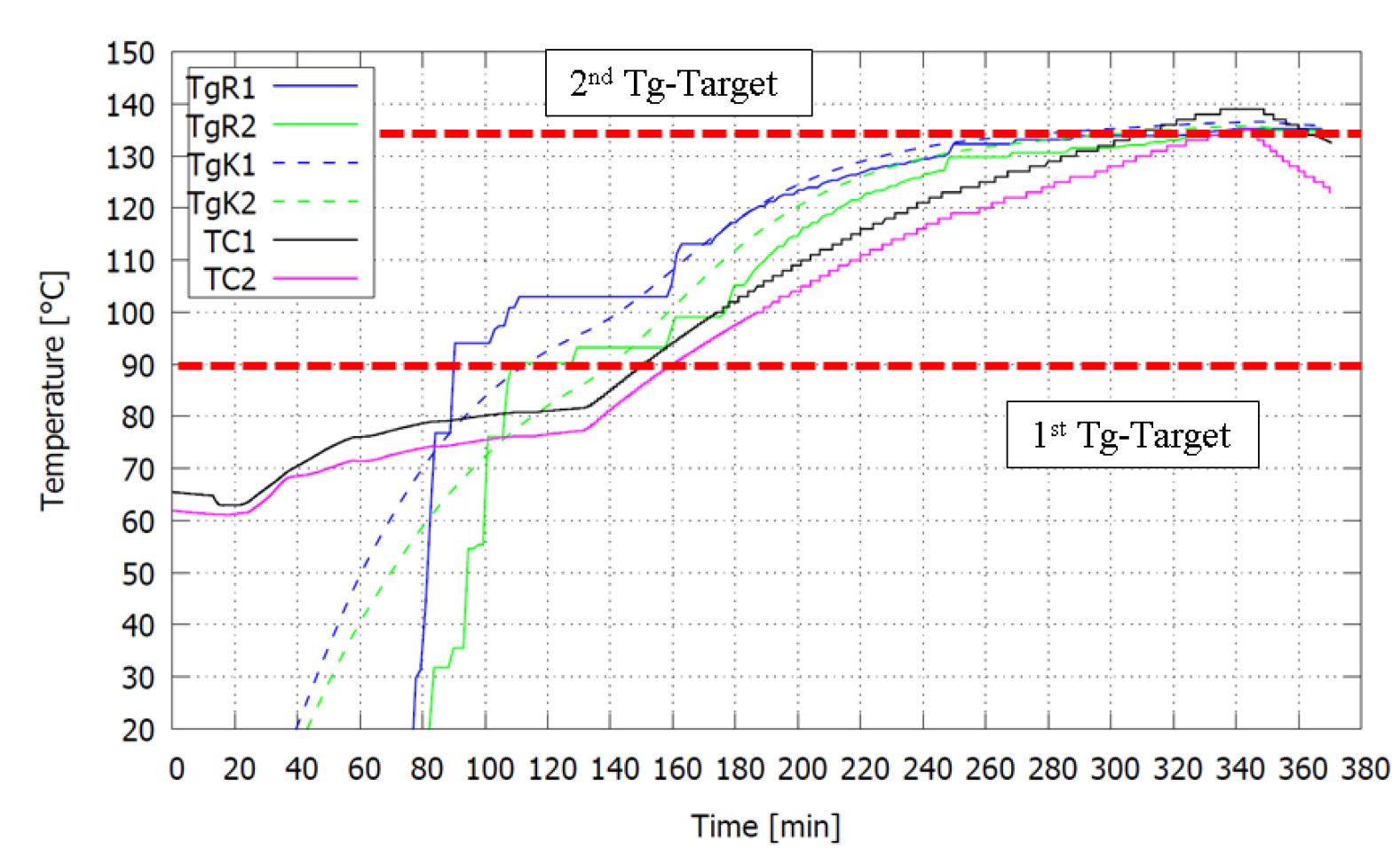
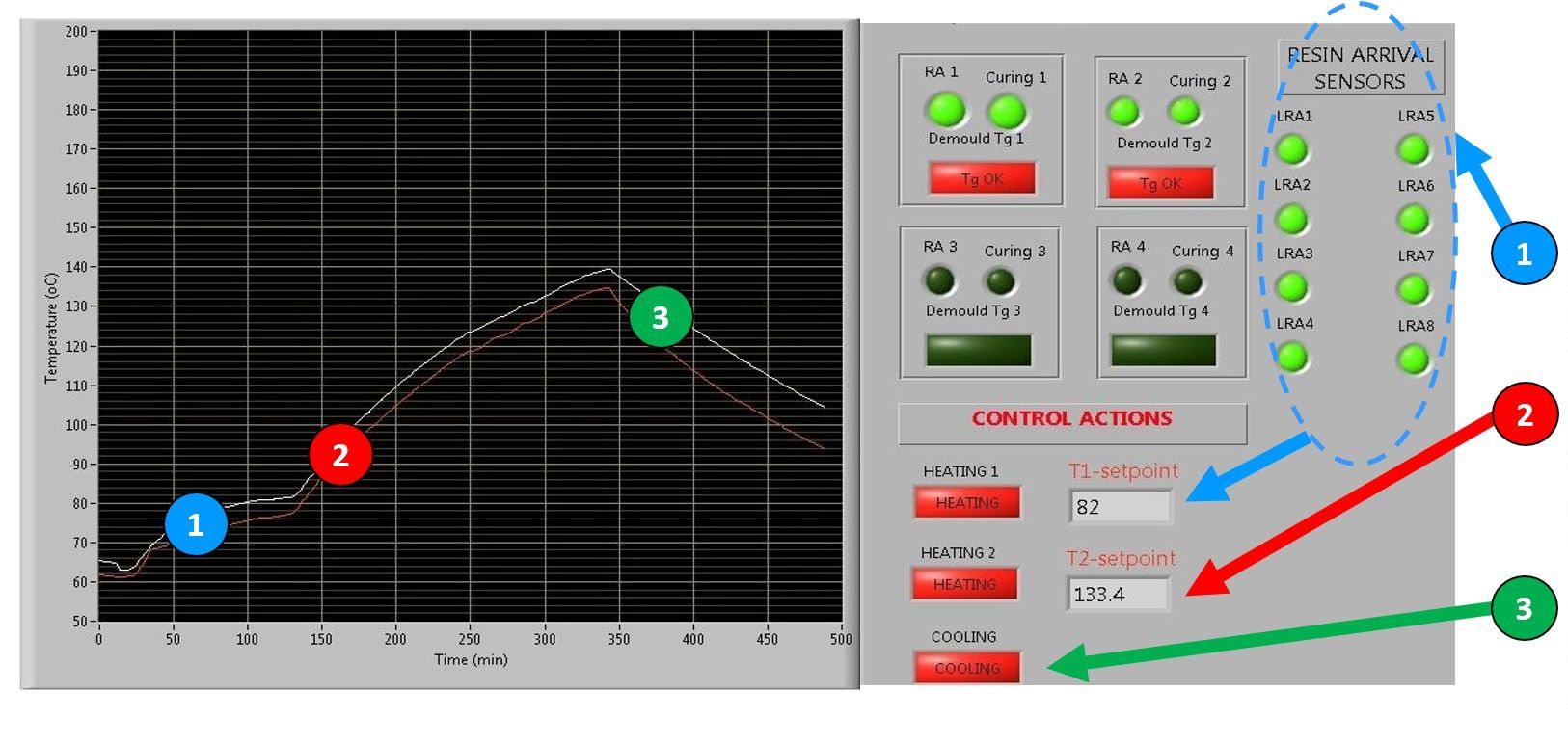
Met behulp van dit procescontrolesysteem kon het ECOMISE-project in Hutchinson de uithardingscyclus met meer dan 30% verminderen.
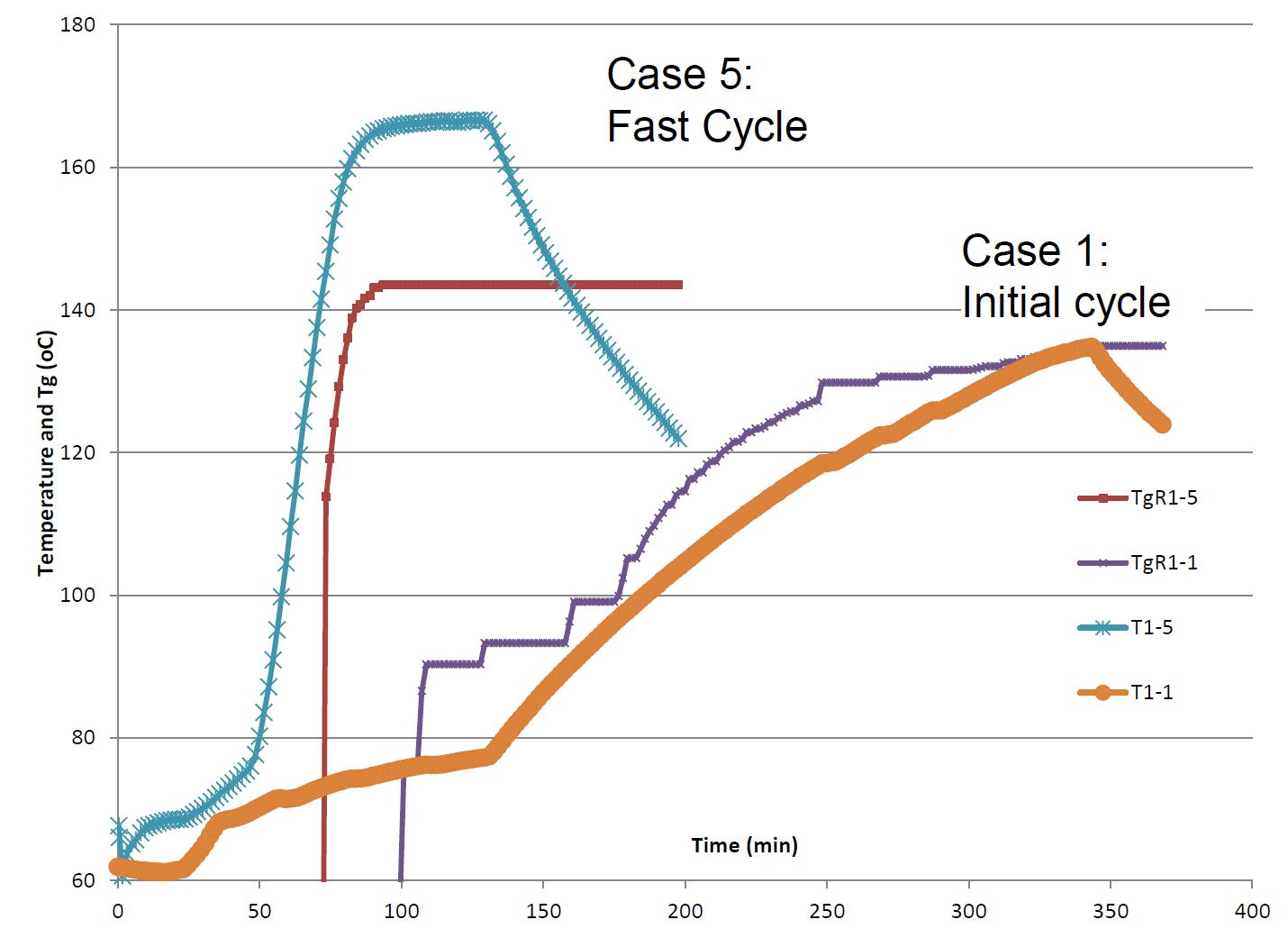
Kalibratie
Kalibratie is vereist voor online Tg-bewaking. Omdat metingen van de sensoren worden verzameld via OPTIMOLD-eenheden, vertaalt de ORS-software deze naar viscositeit en Tg op basis van de kalibratie voor die specifieke hars. "Deze kalibratie is werk dat vóór de verwerking wordt gedaan om de correlaties te leveren die de ORS-software zal gebruiken voor zijn berekeningen", legt Pantelelis uit. “We kalibreren door de hars in een rheometer te plaatsen en temperatuur en viscositeit te meten. Door de juiste formules toe te passen, bereken je vervolgens de bijbehorende weerstand en Tg. We ontwikkelen de kalibratie van harsen voor onze klanten op basis van hun normen en bestuderen de verschillende uithardingscycli van de hars. Deze kalibratiegegevens worden vervolgens gebruikt door de ORS-software bij het verwerken van die hars.”

De nauwkeurigheid van de real-time Tg-berekeningen van de ORS-software is aangetoond in proeven door windbladproducent Carbon Rotec Composite Technology (Lemwerder, Duitsland). Tg online berekend door de ORS-software werd vergeleken met Tg gemeten direct na het uit de vorm halen door het uitvoeren van Differential Scanning Calorimeter (DSC). Voor isotherme verwerking was het gemiddelde verschil 1,61°C en voor niet-isotherme verwerking was het 2,15°C.
"Deze nauwkeurigheid is herhaaldelijk aangetoond in privéprojecten met andere klanten", zegt Pantelelis.
Vooruitgang voor industriële productie
Deze sensor- en datagestuurde procesbesturing is inderdaad een grote stap in de richting van volledig geautomatiseerde en intelligente Composites 4.0-productie. Hoewel het is aangetoond in ECOMISE en ook met het NCC in Bristol, wordt het nog niet gebruikt in de dagelijkse productie. "Het idee om de sensoren te gebruiken om Tg te zien en dan te beginnen met koelen, is inderdaad ontstaan in de productie van windbladen", meldt Pantelelis, "maar het is nog niet volledig geautomatiseerd. Het systeem geeft een alarm wanneer de beoogde Tg is bereikt, waarna de operator de uithardingscyclus stopt. De automatisering is eenvoudig en zal worden voltooid zodra de fabrikant de nauwkeurigheid van het systeem tijdens de pilotfase heeft gevalideerd.”
"Om dit doel te bereiken, hebben we een nieuw werkstation ontwikkeld waarmee de productie-operator toezicht kan houden op het geautomatiseerde proces, waarvoor geen input van zijn kant nodig is", vervolgt hij. "We hebben bij de fabricage van windturbinebladen gezien dat het gebruik van een enkel werkstation tijdens het uitharden van hars en lijm de cyclustijd met minstens 2-3 uur kan verkorten zonder in te boeten aan kwaliteit."
Hoewel Bombardier Belfast, nu Spirit AeroSystems, wel Synthesites-apparatuur gebruikt bij de productie van zijn met hars doordrenkte composietvleugel voor de C-serie, nu Airbus A220, is de procesbesturing niet geautomatiseerd. Synthesites werkte echter ook samen met Bombardier in ECOMISE, en die ontwikkeling wordt voortgezet. Een belangrijke prestatie waren sensoren die door de autoclaafwand werden gevoerd. Zoals uitgelegd in mijn blog van 2013, "C-Series composietvleugel":
Bombardier injecteert nadat de lay-up in de autoclaaf van 21,3 m lang en 5,6 m diameter is geplaatst, waardoor temperatuur en druk op het niveau kunnen worden gehouden dat nodig is voor verminderde viscositeit en bevochtiging - Cytec 890 is injecteerbaar bij 80˚C. . . Nadat de harsinjectie is voltooid, wordt tijdens de consolidatie positieve druk in de autoclaaf uitgeoefend, waardoor de gereedschapselementen sluiten, het natte laminaat verdichten en overtollige hars terug uit de harsinlaat wordt uitgeworpen in een speciaal ontworpen harsdump.
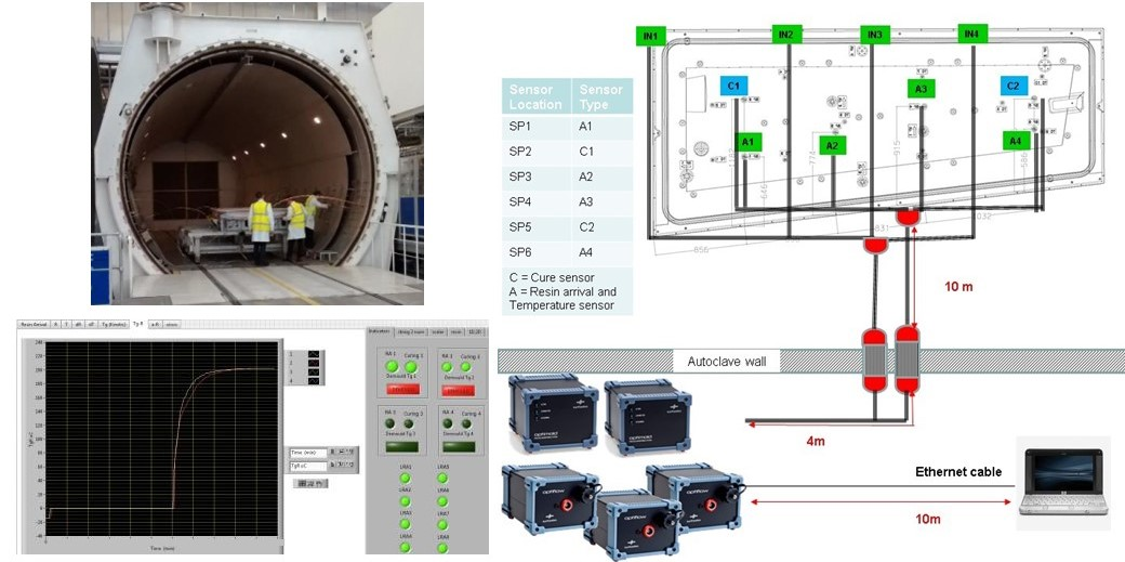
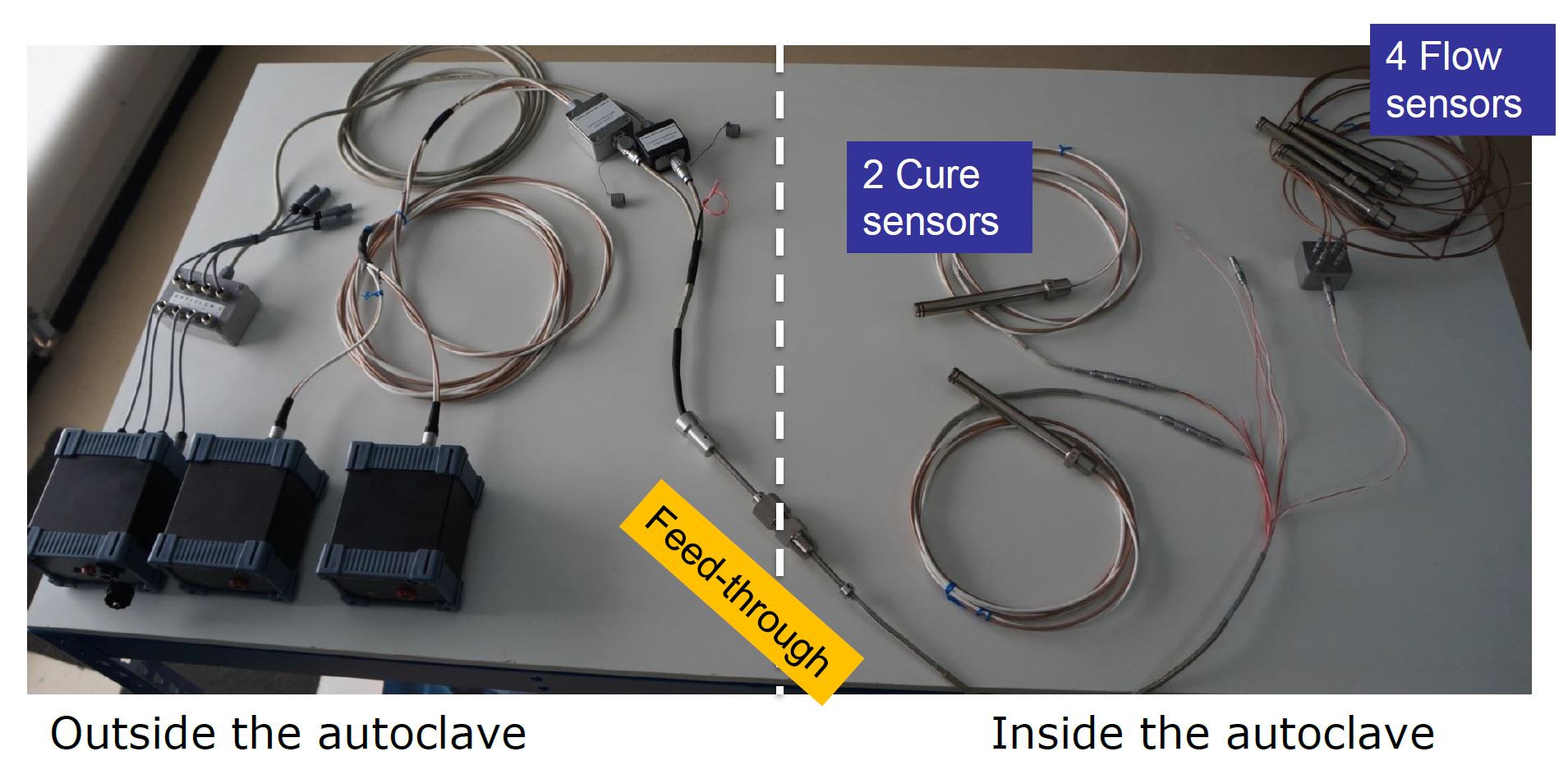
"Zoals de meeste fabrikanten in de commerciële lucht- en ruimtevaart, is het geïnteresseerd om de kwaliteit te waarborgen en de snelheid te verhogen", legt Pantelelis uit. De lay-out hieronder en de resultaten van ECOMISE waren voor een demonstrator, geen commercieel onderdeel. Het gebruikte twee OPTIMOLD-units met twee in-mold-uithardingssensoren en drie OPTIFLOW-units met vier in-mold flowsensoren en vier inline-sensoren bij de vacuümleidingen. "OPTIFLOW kan tot vier harsaanvoer en vier temperatuur-/weerstandssensoren bewaken", merkt Pantelelis op. “De doelstellingen van de demonstratie werden volledig bereikt. We hebben bewezen dat de sensoren, bedrading en systemen probleemloos kunnen werken onder de meest uitdagende ruimtevaartspecificaties. Het was interessant dat de harsaankomstmetingen grote verschillen lieten zien in vergelijking met de stroomsimulaties. Ook bleek uit de online Tg-monitoring dat de gevolgde genezingscyclus voor die specifieke demonstrator aanzienlijk korter had kunnen zijn.”
"We ontwikkelen nu een monitoringsysteem voor de bondlines", zegt Pantelelis, "voornamelijk voor de productie van windturbineschoepen, maar uiteindelijk voor elk bondingproces. Hoewel we het momenteel erg druk hebben met de windturbine-industrie, die probeert de kosten te verlagen, zien we steeds meer interesse vanuit de lucht- en ruimtevaartsector naarmate deze overgaat op het gieten van vloeibare composieten voor massaproductie. Fabrikanten willen meer inzicht krijgen in wat er precies gebeurt tijdens het gieten en hoe ze hun processen kunnen stabiliseren en optimaliseren.”
Ecomise- en Recotrans-projecten ontvingen financiering van de FP7- en Horizon 2020-onderzoeks- en innovatieprogramma's van de Europese Unie onder subsidieovereenkomst nr. NMP2-SL-2013-608667 en 768737, resp.
Referenties voor de sectie "Diëlektrische analyse (DEA), AC vs. DC" omvatten:
- “Real-time monitoring van UV-uitharding” door VINCENTZ, gepubliceerd in European Coatings Journal, uitgave 11/2003, p. 7.
- "Online procesbewakingssystemen - benchmark- en testonderzoek" door Reinhold Meier 1 , Swen Zaremba 1 , Florian Springl 1 , Klaus Drechsler 1 , Fabrice Gaille 2 en Christian Weimer 2 — 1 Institute for Carbon Composites, TU München, Garching, Duitsland. 2 Eurocopter Deutschland GmbH, Donauwörth. Stroomproces in composietmaterialen – FPCM 11, 9-12 juli 2012, Auckland, Nieuw-Zeeland.
- Niet-destructieve karakterisering van materialen VIII bewerkt door Robert E. Green, Proceedings of the 8 th Int. Symposium over niet-destructieve karakterisering van materialen, 16-20 juni 1997, Boulder, Colorado, V.S., gepubliceerd door Springer Science &Business Media, pp. 384-385.
Een andere nuttige referentie is "The Handbook of Dielectric Analysis and Cure Monitoring" door Huan L. Lee, uitgegeven door Lambient Technologies.
Hars
- Sensoren en processors komen samen voor industriële toepassingen
- Nieuwe ams-beeldsensoren voor industriële visie met hoge doorvoer
- BASF en Toray in leveringsovereenkomst voor productie van CFRT-tapes voor auto- en industriële toepassingen
- Ultralichte TPE-composieten voor schoenen
- Solvay composieten geselecteerd voor racecatamaran
- Hexion introduceert tweecomponenten epoxyoplossing voor de productie van composieten in de ruimtevaart
- LANXESS breidt productiecapaciteit voor continue vezelversterkte thermoplastische composieten uit
- Consortium thermoplastische composieten streeft naar productie in hoog volume voor Automotive en Aerospace
- Ultradunne, batterijvrije spanningssensoren voor industriële robotarmen
- Slimme sensoren:voor- en nadelen voor industriële machines
- Wat zijn de innovaties voor industrieel onderhoud?