Leonardo en CETMA:composieten verstoren voor lagere kosten en minder impact op het milieu
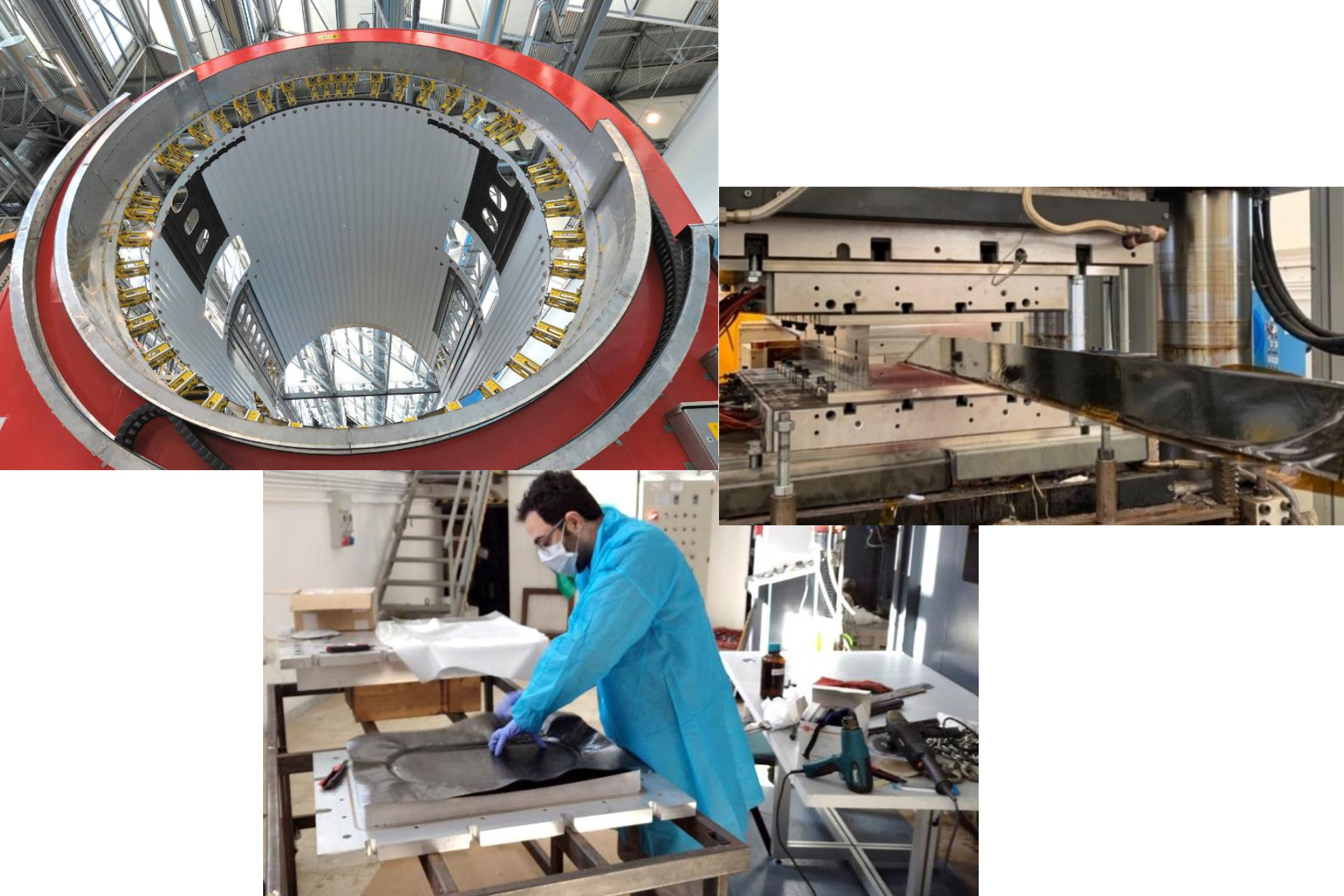
Deze blog is gebaseerd op mijn interview met Stefano Corvaglia, materiaalingenieur, hoofd onderzoek &ontwikkeling en IP-manager van de Leonardo Aerostructures Division (productiefaciliteiten van Grottaglie, Pomigliano, Foggia, Nola, Zuid-Italië) en Dr. Silvio Pappadà, onderzoeksingenieur en hoofd van programma's met Leonardo op CETMA (Brindisi, Italië).
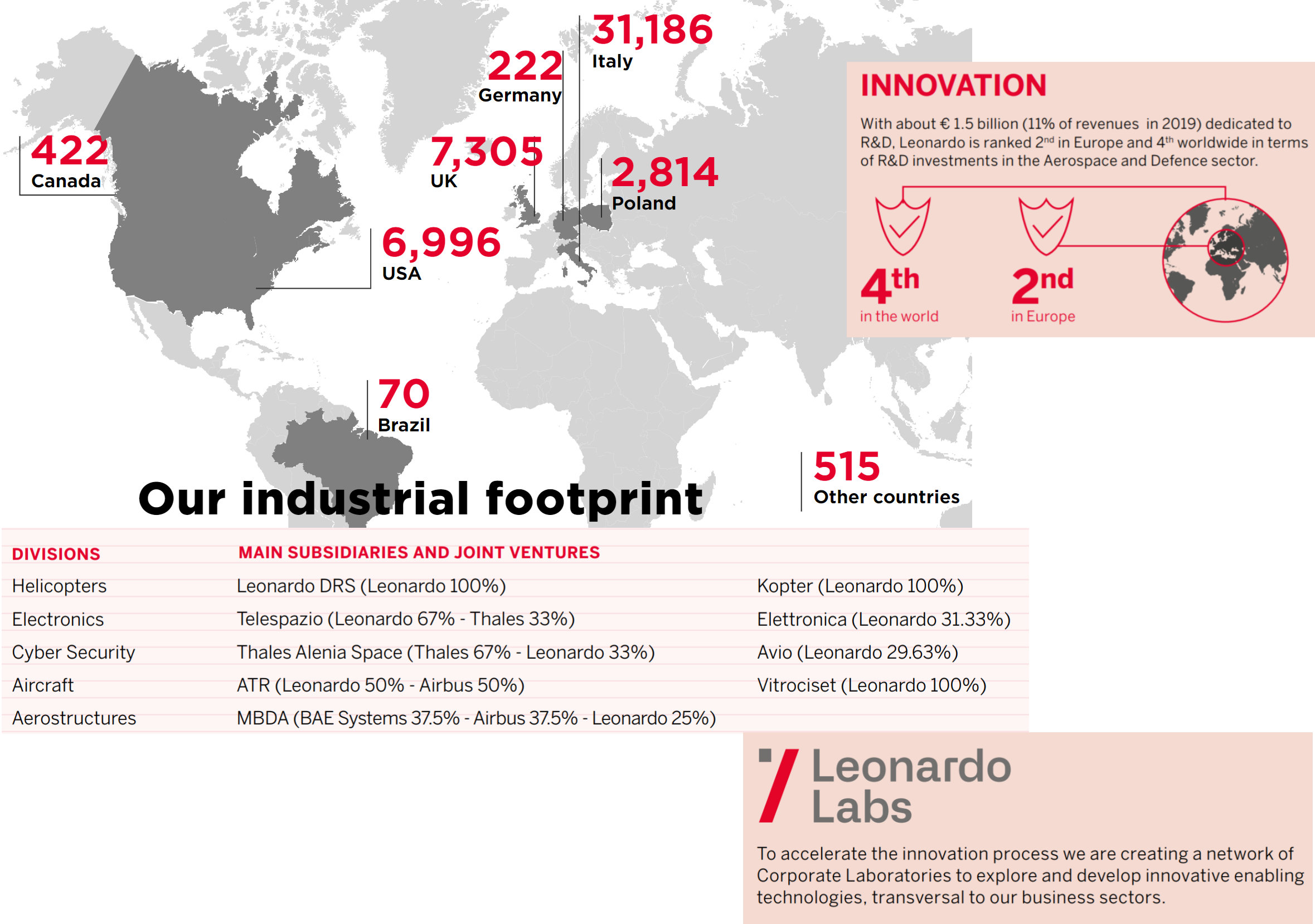
Leonardo (Rome, Italië) is een van 's werelds grootste spelers op het gebied van lucht- en ruimtevaart, defensie en veiligheid met een omzet van 13,8 miljard euro en meer dan 40.000 werknemers wereldwijd. Het bedrijf biedt op wereldschaal uitgebreide oplossingen voor lucht-, land-, zee-, ruimtevaart-, cyber- en beveiligingssystemen en onbemande systemen. Met ongeveer € 1,5 miljard (11% van de omzet in 2019) gewijd aan R&D, staat Leonardo op de 2e plaats in Europa en op de 4e plaats wereldwijd wat betreft onderzoeksinvesteringen in de lucht- en ruimtevaart- en defensiesector.
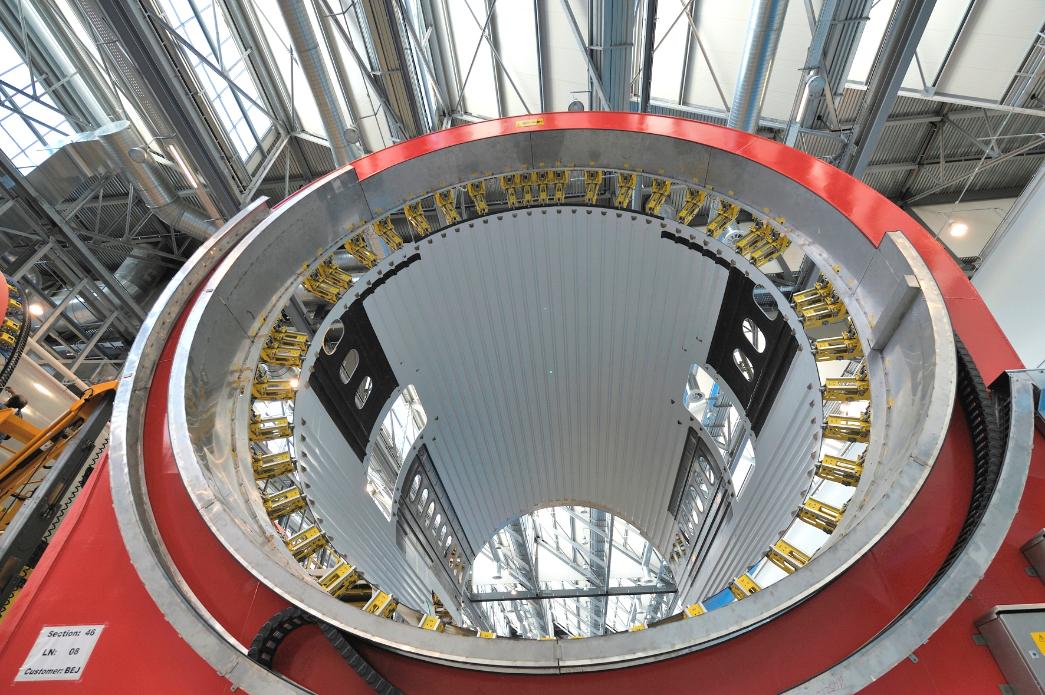
Via zijn Aerostructures Division levert Leonardo fabricage en assemblage van grote structurele componenten, waaronder rompen en empennages, in composieten en traditionele materialen voor 's werelds belangrijkste programma's voor burgerluchtvaart.
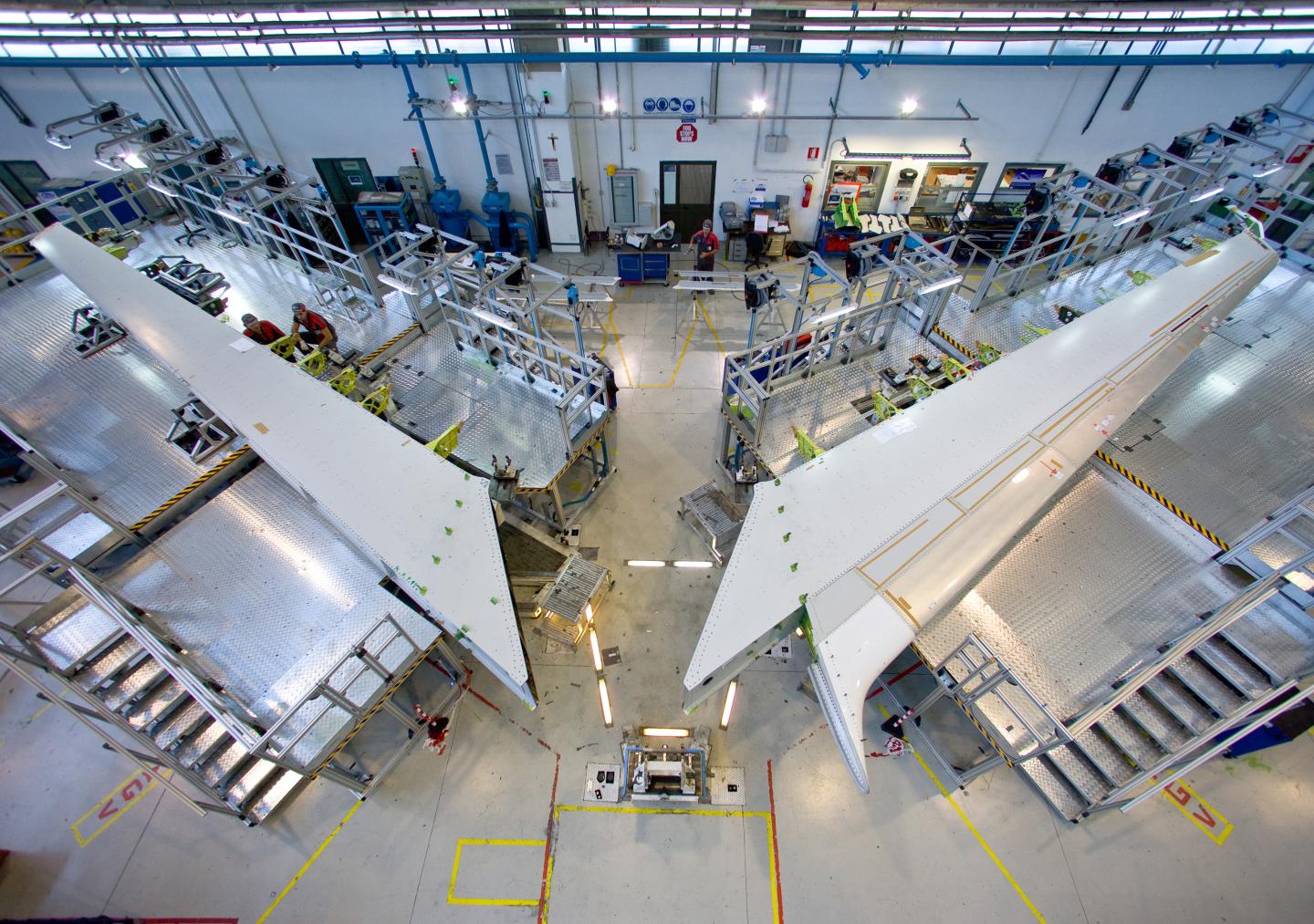
In composietmaterialen produceert Leonardo Aerostructures Division "vaten uit één stuk" voor de centrale rompdelen 44 en 46 van de Boeing 787 in de fabriek in Grottaglie, evenals de horizontale stabilisatoren in de Foggia-fabriek - in totaal ongeveer 14% van het 787-casco. De productie van andere composietstructuren omvat, in de Foggia-fabriek, de fabricage en assemblage van onderdelen voor commerciële vliegtuigen van ATR en Airbus A220. Foggia produceert ook composietonderdelen voor de Boeing 767 en voor militaire programma's, waaronder de Joint Strike Fighter F-35, Eurofighter Typhoon straaljager, C-27J militair transport en Falco Xplorer, het nieuwste lid van de Falco-familie van onbemande vliegtuigen geproduceerd door Leonardo.
Werken met CETMA
"We hebben veel lopende activiteiten met CETMA, bijvoorbeeld op het gebied van thermoplastische composieten en resin transfer molding (RTM)", zegt Corvaglia. “Ons doel is om de R&D-activiteiten in een zo kort mogelijke tijd klaar te hebben voor productie. In onze afdeling (R&D en IP-beheer) kijken we ook naar disruptieve technologieën met een lagere TRL [technology readiness level – dwz een lagere TRL is meer in de kinderschoenen en verder van productie verwijderd], maar we willen concurrerender zijn en onze klanten wereldwijd helpen .”
“Vanaf het begin van onze samenwerking”, voegt Pappadà toe, “hebben we er altijd naar gestreefd de kosten en de impact op het milieu laag te houden. We hebben ontdekt dat thermoplastische composieten (TPC) een vermindering van beide bieden ten opzichte van thermoharders.”
Corvaglia merkt op dat "we samen met Silvio's team deze technologieën hebben ontwikkeld en enkele geautomatiseerde celprototypes hebben gebouwd om deze in productie te evalueren."
Continu persgieten (CCM)
“CCM is een goed voorbeeld van onze samenwerking”, zegt Pappadà. "Leonardo identificeerde enkele componenten gemaakt in thermohardende composieten en samen hebben we technologie onderzocht om deze in TPC te leveren, kijkend naar waar er grote aantallen onderdelen in het vliegtuig zijn, zoals verbindingsstructuren en rongen met een eenvoudige geometrie."
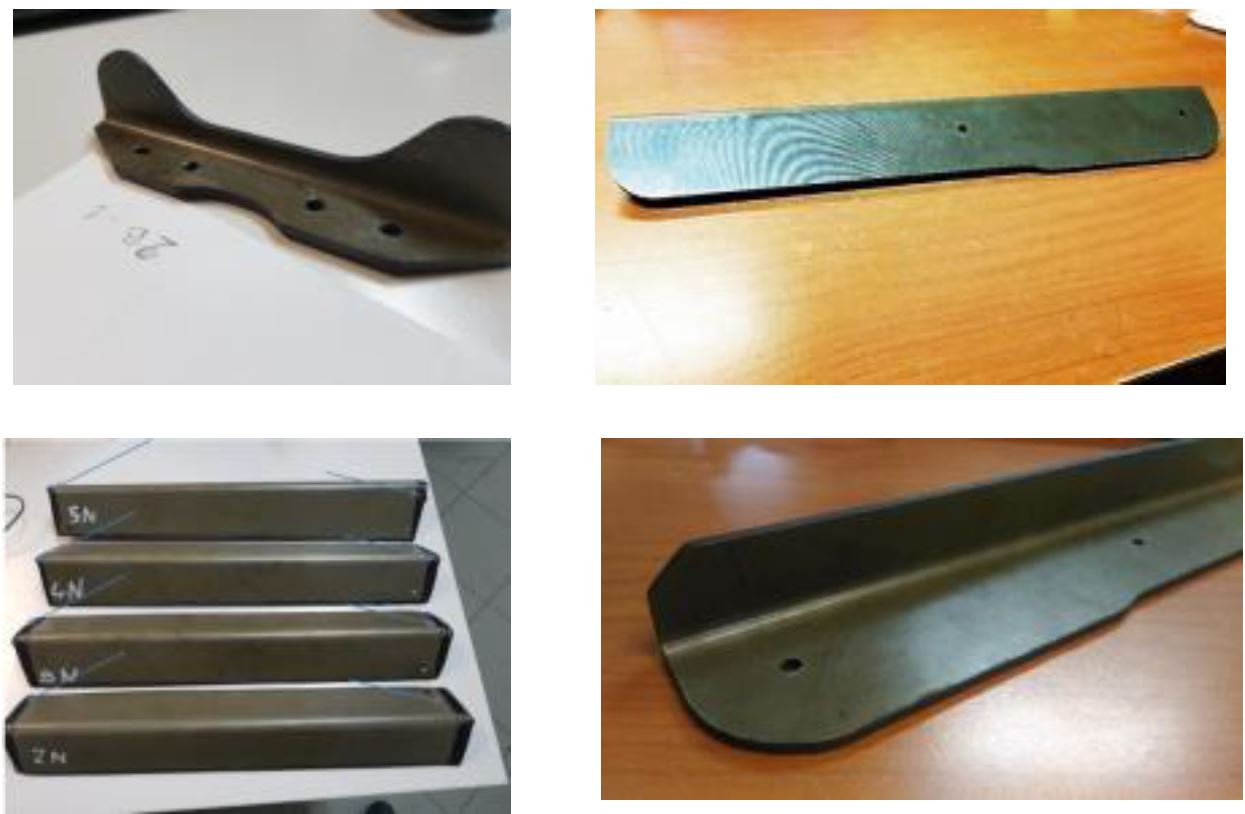
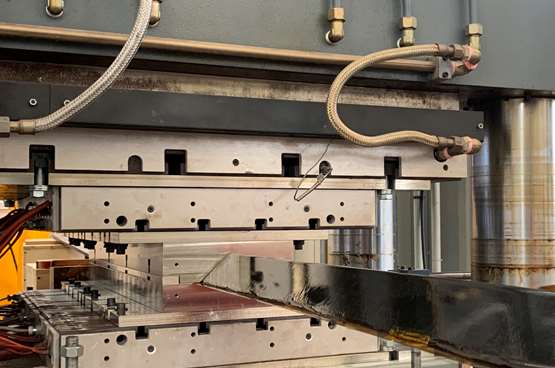
"We hadden een nieuwe productietechnologie nodig die wordt gekenmerkt door lage kosten en hoge tarieven", vervolgt hij. Hij wijst erop dat in het verleden afzonderlijke TPC-componenten werden vervaardigd met veel afval. “Dus we produceren netvormen op basis van niet-isotherm persgieten, maar met enkele innovaties (octrooien lopen nog) om afval te verminderen. We hebben hiervoor een volledig geautomatiseerde cel ontworpen, die een Italiaans bedrijf vervolgens voor ons heeft gebouwd.”
Deze cel is in staat om de componenten te produceren die Leonardo heeft ontworpen, zegt Pappadà, "met een snelheid van één component per 5 minuten, 24 uur per dag werkend." Zijn team moest toen echter de productie van de preform uitzoeken. “In het begin hadden we een vlak lamineerproces nodig, want dat was op dat moment het knelpunt”, legt hij uit. “Dus ons proces begint met een blanco (plat laminaat), verwarmt dit in een infrarood (IR) oven en vervolgens in een pers om te vormen. Platte laminaten worden meestal geproduceerd met behulp van grote persen en hebben een cyclustijd van 4-5 uur. We besloten een nieuwe methode te onderzoeken waarmee we op een snellere manier platte laminaten kunnen produceren. Daarom hebben we een CCM-lijn met hoge productiviteit ontwikkeld bij CETMA met de ondersteuning van Leonardo-ingenieurs. We hebben de cyclustijd voor een onderdeel van 1 meter bij 1 meter teruggebracht tot 15 minuten. Belangrijk is dat het een continu proces is, dus we kunnen onbeperkte lengtes produceren.”
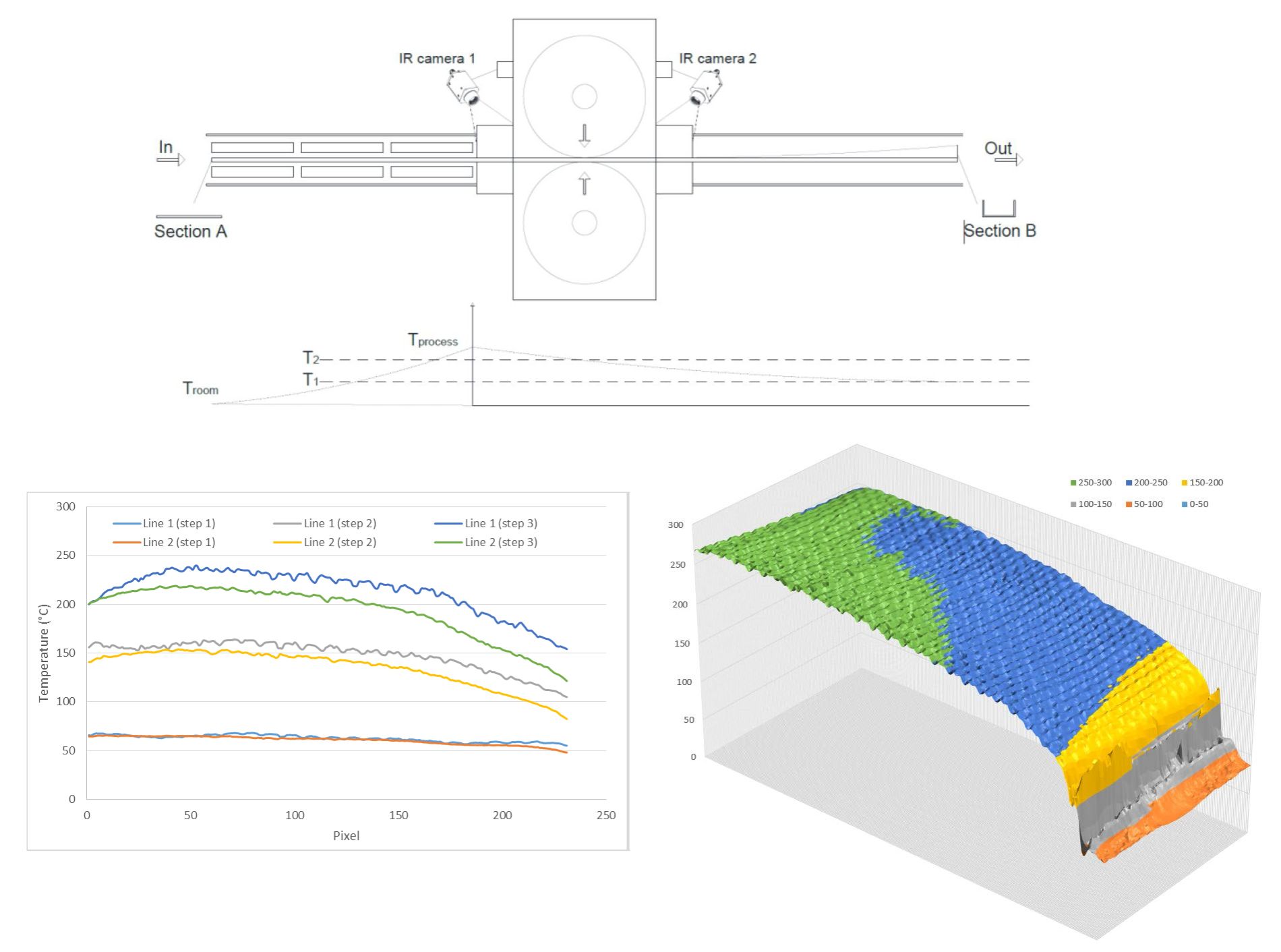
Maar hoe is dit nieuw in vergelijking met de CCM die al meer dan tien jaar door Xperion, nu XELIS (Markdorf, Duitsland) wordt gebruikt? "We hebben analytische en numerieke modellen ontwikkeld die defecten zoals holtes kunnen voorspellen", zegt Pappadà. “We hebben dit gedaan in samenwerking met Leonardo en de Universiteit van Salento (Lecce, Italië) om inzicht te krijgen in parameters en hun invloed op de kwaliteit. We hebben deze modellen gebruikt om deze nieuwe CCM te ontwikkelen, waar we een zeer hoge dikte maar ook hoge kwaliteit kunnen hebben. Dankzij deze modellen kunnen we temperatuur en druk optimaliseren, maar ook hoe deze toe te passen. Er zijn veel technologische aspecten die je kunt ontwikkelen om een uniforme verdeling van temperatuur en druk te krijgen; we moesten echter de impact hiervan op de mechanische prestaties en de groei van defecten in composietstructuren begrijpen."
Pappadà vervolgt:“Onze technologie is flexibeler. Ook is CCM 20 jaar geleden ontwikkeld, maar er is geen informatie over omdat de weinige bedrijven die het gebruikten geen kennis en knowhow deelden. We moesten dus met niets beginnen, alleen met onze kennis van composieten en verwerking.”
"We werken nu met interne programma's en met onze klanten om onderdelen voor deze nieuwe technologieën te vinden", zegt Corvaglia. "Deze onderdelen kunnen opnieuw worden ontworpen en opnieuw worden gekwalificeerd om de productie te starten." Waarom? “Het doel is om een vliegtuig te hebben dat zo licht mogelijk is, maar ook qua prijs. We moeten dus ook optimaliseren met dikte. Maar we zouden kunnen ontdekken dat een onderdeel nog lichter kan worden of meerdere onderdelen met een vergelijkbare vorm kunnen identificeren, wat aanzienlijke kostenbesparingen kan opleveren."
Tot nu toe, herhaalt hij, is deze technologie in handen van enkelen. “Maar we hebben alternatieve technologieën ontwikkeld om deze processen nog meer geautomatiseerd te maken door geavanceerdere persvormen toe te voegen. We leggen er een plat laminaat in en er komt een deel uit, klaar voor gebruik. We zitten in de fase van het opnieuw ontwerpen van onderdelen en het ontwikkelen van platte versus gevormde CCM.”
"We hebben nu in CETMA een CCM-lijn die zeer flexibel is", zegt Pappadà, "waar we naar behoefte verschillende drukken kunnen uitoefenen om complexe vormen te bereiken. De lijn die we samen met Leonardo zullen ontwikkelen, zal meer gericht zijn op componenten die passen bij zijn specifieke behoeften. We denken dat we verschillende CCM-lijnen kunnen hebben voor platte panelen en L-stringers versus meer complexe vormen. Op deze manier kunnen we de apparatuurkosten lager houden in vergelijking met de grote persen die momenteel worden gebruikt om TPC-onderdelen met complexe geometrie te produceren.”
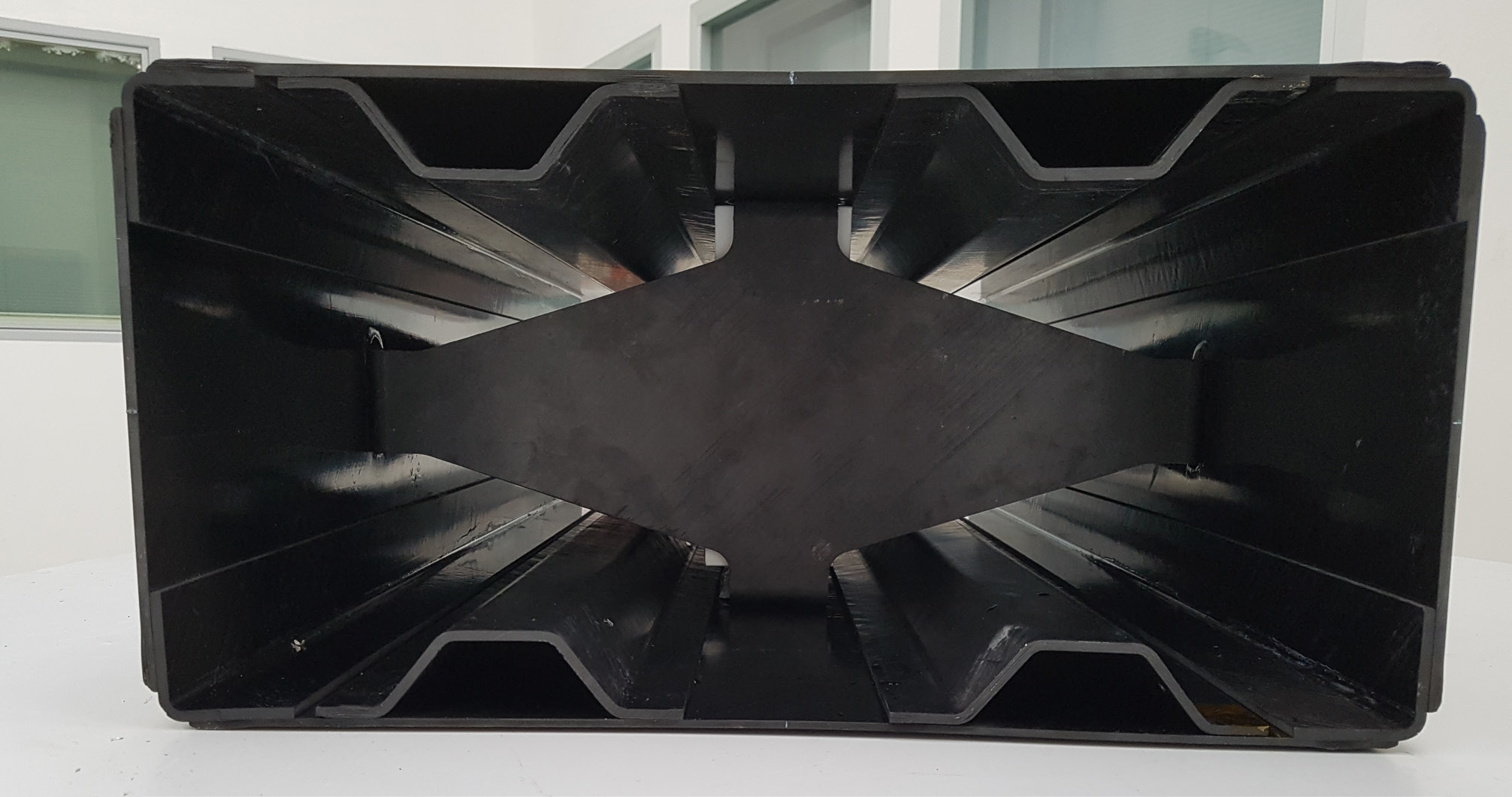
Inductielassen voor in-situ consolidatie
"Inductielassen is erg interessant voor composieten omdat het mogelijk is om de temperatuur heel goed af te stemmen en te regelen, heel snel te verwarmen en heel nauwkeurig te regelen", merkt Pappadà op. “Met Leonardo hebben we inductielassen ontwikkeld om TPC-componenten te verbinden. Maar nu denken we erover om inductielassen te gebruiken voor in-situ consolidatie (ISC) van TPC-tapes. Hiervoor hebben we nieuwe koolstofvezeltape ontwikkeld die zeer snel kan worden verwarmd door inductielassen met een speciale machine. De tape gebruikt dezelfde matrixmaterialen als commerciële tapes, maar met een andere architectuur die de elektromagnetische verwarming verbetert. We optimaliseren de mechanische prestaties, maar denken ook aan het proces en proberen aan verschillende behoeften te voldoen, bijvoorbeeld hoe we kosteneffectief kunnen verwerken met automatisering.”
Hij wijst erop dat ISC erg moeilijk te bereiken is met TPC-tape tegen goede productiesnelheden. “Om dit voor industriële productie te hebben, moet je sneller opwarmen en afkoelen en heel gecontroleerd druk uitoefenen. Daarom hebben we besloten om inductielassen te gebruiken om alleen een klein gebied te verwarmen waar we materiaal consolideren, maar de rest van het laminaat koud laten.” Inductielassen dat wordt gebruikt voor assemblage heeft een hogere TRL, zegt Pappadà. “
Het gebruik van inductieverwarming voor in-situ consolidatie lijkt erg storend - iets wat geen andere OEM's of tier-leveranciers op dit moment openlijk doen. "Ja, dit is mogelijk disruptieve technologie", zegt Corvaglia. “We hebben de machine en de materialen gepatenteerd. We streven naar iets dat vergelijkbaar is met thermohardende composieten. Velen hebben AFP (automatische vezelplaatsing) met TPC geprobeerd, maar moeten een tweede stap doen voor consolidatie. Dit is een grote beperking in termen van geometrie, kosten, cyclustijd en grootte van onderdelen. We kunnen inderdaad de manier veranderen om luchtvaartonderdelen te produceren.”
SQRTM
Naast thermoplasten blijft Leonardo kijken naar RTM-technologieën. “Dit is een ander gebied waarop we met CETMA hebben samengewerkt en nieuwe ontwikkelingen hebben gepatenteerd op basis van een oudere technologie, in dit geval SQRTM. Dezelfde gekwalificeerde resin transfer molding (SQRTM) werd oorspronkelijk ontwikkeld door Radius Engineering (Salt Lake City, Utah, V.S.). "Het is belangrijk om een out-of-autoclave (OOA)-methode te hebben waarmee we materiaal kunnen gebruiken dat al gekwalificeerd is", zegt Corvaglia. “Het stelt ons ook in staat prepregs te gebruiken die bekende eigenschappen en kwaliteit hebben. We hebben met deze technologie een raamkozijn voor een vliegtuig ontworpen, gedemonstreerd en gepatenteerd.”
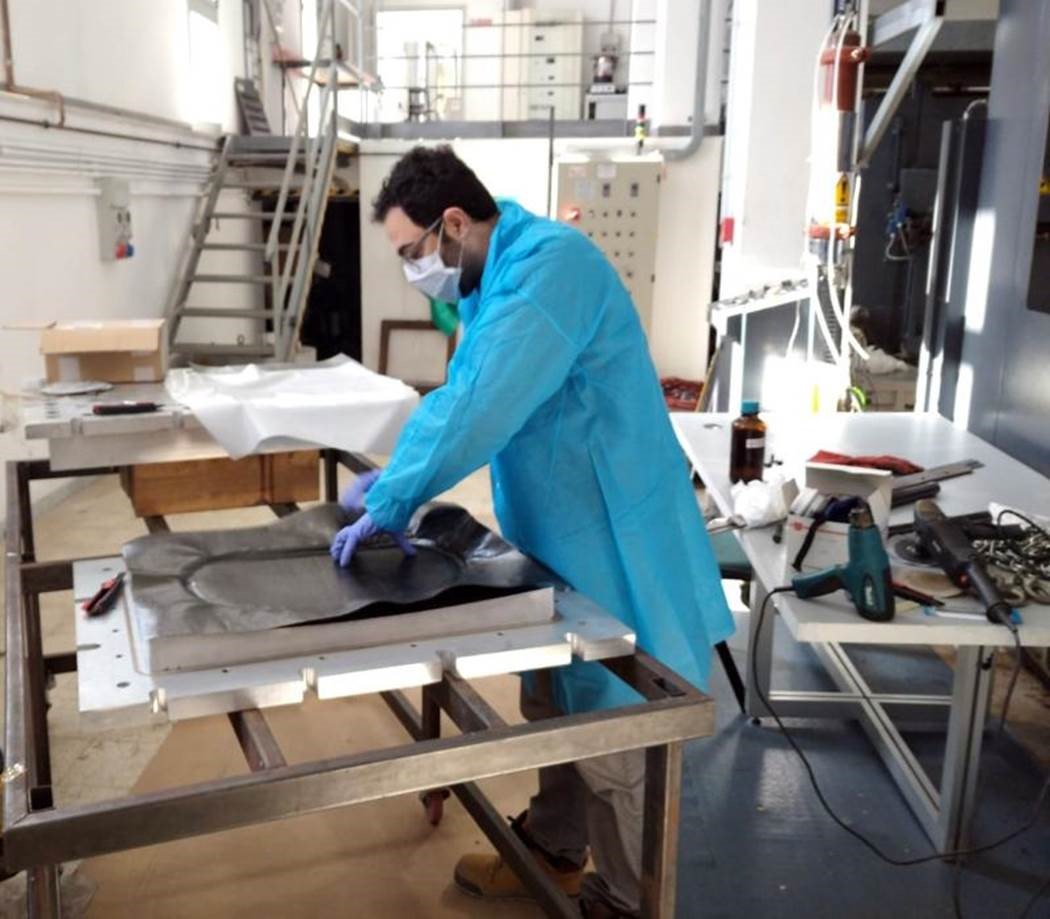
"Dit is ook oudere technologie, maar als je op internet gaat, kun je geen informatie over deze techniek vinden", merkt Pappadà op. “Belangrijk is dat we wederom analytische modellen gebruiken om de procesparameters te voorspellen en te optimaliseren. Met deze technologie kunnen we een goede harsverdeling hebben - zonder droge gebieden of harspooling - en een bijna nul leegtegehalte. We kunnen hoge structurele prestaties produceren omdat we het vezelgehalte kunnen controleren, en deze technologie kan worden gebruikt om complexe vormen te produceren. We gebruiken dezelfde materialen die gekwalificeerd zijn voor autoclaafuitharding, maar in plaats daarvan in een OOA-methode, maar u kunt ook besluiten om snel uithardende harsen te gebruiken om de cyclustijd tot minuten te verkorten.”
"Zelfs met de huidige prepreg hebben we de uithardingstijd verkort", merkt Corvaglia op. “In vergelijking met een normale autoclaafcyclus van 8-10 uur, kunnen we bijvoorbeeld 3-4 uur halen met SQRTM voor een onderdeel als een raamkozijn. Warmte en druk worden rechtstreeks op het onderdeel uitgeoefend en de massa om op te warmen is minder. Ook is het verwarmen van de vloeibare hars versus de lucht in een autoclaaf sneller en is de kwaliteit van het onderdeel uitstekend, wat vooral bij complexe vormen een voordeel is. Er is geen nabewerking, bijna geen lege ruimten en een uitstekende oppervlaktekwaliteit omdat het gereedschap het bestuurt, geen vacuümzak."
Visionaire, op technologie gebaseerde toekomst
Leonardo produceert innovatie in een grote en diverse reeks technologieën. Vanwege de snelle technologische evolutie beschouwt het investeringen in R&D met een hoog risico (lage TRL) als cruciaal om de nieuwe technologieën te ontwikkelen die nodig zijn voor toekomstige producten, die verder gaan dan de incrementele (korte termijn) ontwikkeling die het al in huidige producten ondersteunt. Een dergelijke combinatie van korte- en langetermijnstrategieën wordt gecombineerd in Leonardo's 2030 R&D Masterplan, een uniforme visie voor een duurzaam en concurrerend bedrijf.
Als onderdeel van dit plan lanceert het de Leonardo Labs, een internationaal netwerk van bedrijfs-R&D-laboratoria die zich toeleggen op geavanceerd onderzoek en technologische innovatie. Voor 2020 zal het bedrijf doorgaan met het openen van de eerste zes Leonardo-laboratoria in de gebieden Milaan, Turijn, Genua, Rome, Napels en Taranto en werft het 68 onderzoekers (Leonardo Research Fellows) aan met vaardigheden op de volgende gebieden:36 posities in kunstmatige intelligentie en autonome intelligente systemen, 15 in big data-analyse, 6 in high-performance computing, 4 in elektrificatie van luchtvaartplatforms, 5 in materialen en structuren en 2 in kwantumtechnologieën. Leonardo Labs zal de rol spelen van innovatieposten en generatoren van Leonardo's toekomstige technologieën.
Met name de technologieën die Leonardo in vliegtuigen commercialiseert, kunnen ook toepassingen hebben in zijn land- en zeedivisies. Blijf ons volgen voor meer updates over Leonardo en de mogelijke impact ervan op composieten.
Hars
- Ultralichte TPE-composieten voor schoenen
- PP schuim om duurzaamheid en kosten te verbeteren
- Grafeen- en polymeercomposieten voor toepassingen met supercondensatoren:een recensie
- Aanpassen van ultrasone sensoren voor procesoptimalisatie en controle van composieten
- OTOMcomposite ontwikkelt software voor de productie van Composites 4.0 met behulp van laserondersteunde tapeplaatsing en -wikkeling
- Herverwerkbare, herstelbare en recyclebare epoxyharsen voor composieten
- Combinatie van AC- en DC-diëlektrische metingen voor het bewaken van de uitharding van composieten
- Solvay composieten geselecteerd voor racecatamaran
- Consortium thermoplastische composieten streeft naar productie in hoog volume voor Automotive en Aerospace
- Milieu-impact van de productie van halfgeleiders en elektronica
- Draagbare gassensor voor gezondheids- en milieubewaking