Thermoplastische composietstructuur vervangt metalen op veiligheidskritieke rempedalen
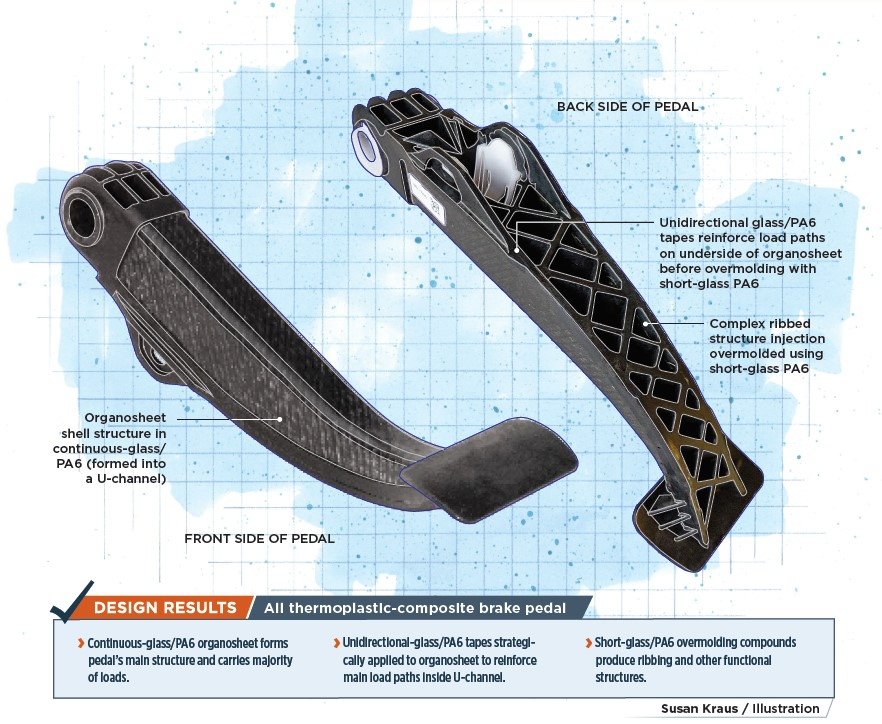
De auto-industrie heeft gaspedalen in de jaren negentig omgebouwd van metalen tot spuitgegoten thermoplasten van kort glas. Rempedalen - omdat het veiligheidskritieke componenten zijn met uitdagende vereisten voor stijfheid, sterkte en torsiebelasting - duurden echter veel langer om te converteren. Tier 1 automotive leverancier Boge Rubber &Plastics Group (Damme, Duitsland) zegt dat het de eerste leverancier is die voldoet aan de veeleisende OEM prestatie- en kostendoelstellingen voor rempedalen in thermoplastische composieten. Uniek ontwerp, drie verschillende materialen en een op maat gemaakt productieproces stellen het bedrijf in staat pedalen te produceren die sterker, stijver, lichter en goedkoper zijn.
Een niche vinden die telt
Boge is een ontwikkelaar en producent van producten voor trillingsdemping en aandrijflijn/chassismontage, evenals lichtgewicht plastic modules en pedaalkasten (inclusief combinaties van rem-, koppelings- en gaspedalen) voor de auto-industrie. Het produceert sinds 2008 auto-onderdelen in organoplaat van continue vezels met korte glas-overmolding-compounds. In 2018 voegde het unidirectionele (UD) thermoplastische tapes toe aan de mix. Door continue procesinnovatie werden de cyclustijd en -kosten verminderd en de omzet verhoogd.
"In 2015 kwam mijn baas naar me toe en zei:'Deze veranderingen die je hebt aangebracht zijn leuk, Daniel, maar het zou goed zijn als je een grotere markt zou kunnen vinden met productievolumes die er echt toe doen'", herinnert Dr.-Ing zich. . Daniel Häffelin, senior manager/hoofd van het lichtgewichtteam bij het Boge Global Innovation Center. Een team van ingenieurs van Boge ging de uitdaging aan en brainstormde over hoe de vezelefficiëntie kan worden verbeterd om de kosten te verlagen en meer omzet te genereren.
"Organosheet is een geweldig product, maar je moet het op de juiste manier gebruiken, alleen waar het nodig is", legt Häffelin uit. “We hadden ons productieproces al heel lean gemaakt, dus we zouden niet veel winnen door te proberen de cyclustijden nog verder te verlagen. We redeneerden dat de beste manier om de kosten te verlagen, was om de hoeveelheid eindeloze vezels die we gebruikten te verminderen door die vezel efficiënter te gebruiken."
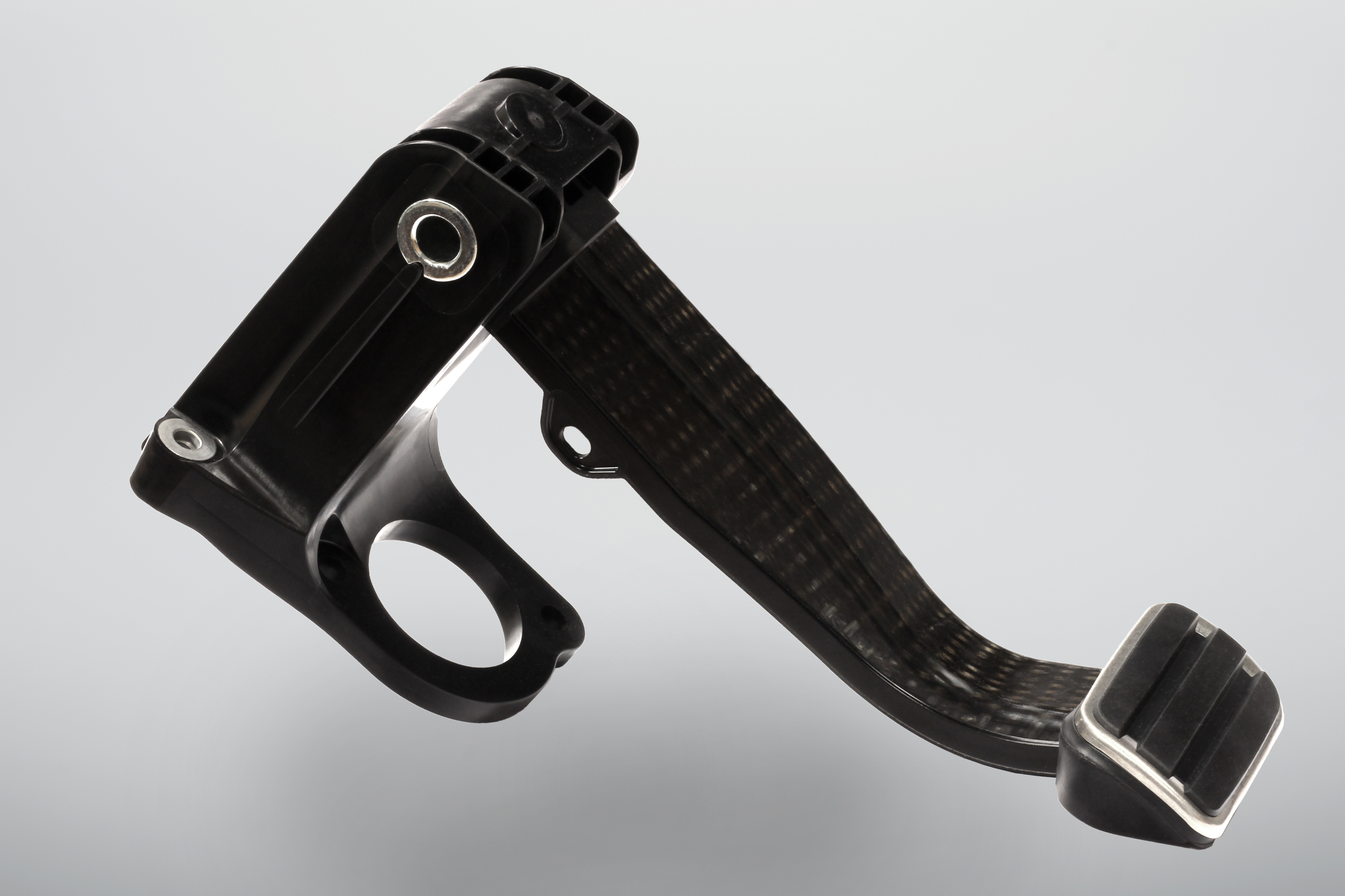
Gewoon pedalen kleiner of dunner maken zou ook niet werken omdat er praktische beperkingen zijn aan de grootte en vorm van het rempedaal, om nog maar te zwijgen van uitdagende prestatiespecificaties vanwege de veiligheidskritieke aard. Wat het meest logisch was, was het vinden van manieren om de vezeloriëntatie beter te beheersen om lokale eigenschappen te optimaliseren in delen van het onderdeel met de hoogste piekbelastingen, wat mogelijkheden bood om de wanddikte in minder kritieke gebieden te verminderen.
"We zochten een manier om vezels lokaal te 'sturen', zodat we ze precies daar konden plaatsen waar we ze nodig hadden om de stijfheid en sterkte te behouden", voegt Dr. Torsten Bremer, Chief Executive Officer van Boge Rubber &Plastics Group, toe. “We wisten dat dit in principe mogelijk was omdat we al hadden overwogen om pick-and-place-machines voor sportartikelen en medicijnen te gebruiken, maar ze waren te duur. Toen besloten we dat we een nieuw proces nodig hadden.”
"We werkten al samen met een Duitse OEM om manieren te vinden om volledig composiet rempedalen te maken die voldeden aan hun prestatie- en kostenvereisten", herinnert Burkhard Tiemann, executive vice president van de Boge Plastics &Rubber Group, productlijnleider - Plastics zich. "We zeiden tegen onze klant:'We zullen een nieuw proces ontwikkelen met behulp van UD-tapes en organoblad.' Ze zeiden tegen ons:'Als je de massa en de kosten verder kunt verminderen, zullen we het doen.' Dat was ons uitgangspunt. We hebben in 2015 een grote belofte gedaan dat we een volledig composiet rempedaal konden leveren dat goedkoper en lichter was en in grote hoeveelheden kon worden geproduceerd. Het heeft drie jaar geduurd om de details uit te werken en onze eerste producten te leveren.”
Vezelbekrachtiging
Composiet rempedalen moeten aan dezelfde prestatiespecificaties voldoen als pedalen van oud staal of aluminium. Dat omvat speciale vereisten voor storingsmodi met belastingen tot 3.000 Newton en staalachtige doorbuiging bij maximale belasting. Gezien deze vereisten en de beperkte beschikbare pakketruimte, vereist de hoofdschaalstructuur van het pedaal, die de maximale belastingen draagt, continue vezelversterking. Daarom besloot het team organoblad te gebruiken om de pedaalruggengraat te vormen. UD-tapes zouden dan worden gebruikt om plaatselijk de stijfheid/sterkte te vergroten en binnenmuren te versterken tijdens piekspanningen in het gebied van het onderdeel dat vervolgens tijdens het voorvormen in een U-kanaal zou worden gebogen. En in gebieden waar functionele geometrie zoals ribben nodig was, werd een overmolding-compound van gehakt glas gespecificeerd. Het team was van mening dat deze hybride benadering de vezelefficiëntie zou verhogen en tegelijkertijd het materiaalgebruik, de gemiddelde wanddikte en de cyclustijd zou verminderen.

Het team begon met intensief simulatiewerk om de glasvezellocaties tijdens de productie te optimaliseren. De basis voor het werk van Boge was gebaseerd op een door de overheid gefinancierd Duits onderzoeksprogramma uit 2011-2014 genaamd SoWeMa (Software, Tools, and Machine Development for a Fully Automatic and Closed Lightweight Manufacturing Chain).
"Het SoWeMa-onderzoek omvatte veel van de vragen die we een jaar later zouden stellen voor onze eigen onderneming", legt Häffelin uit. "Omdat ontwerp deel uitmaakt van de kernkennis van Boge, zijn we begonnen met de fundamenten van het SoWeMa-programma en hebben we onze eigen FE (eindige-elementen) simulatiemogelijkheden voor anisotrope lay-upstructuren gebouwd."
Een aandachtsgebied was gecombineerde topologie-optimalisatie voor de tape-lay-up en de ribstructuur. "We hebben een iteratiecyclus gemaakt om de plaatsing van tapes te optimaliseren en de ribstructuur dienovereenkomstig aan te passen, aangezien beide aan elkaar zijn gekoppeld over de stijfheid en sterkte van het onderdeel", vervolgt K. Siebe, FEA-ingenieur, CRRC Innovation Center. “Omdat de materiaalcombinatie van UD-tapes, organosheet en kortvezelige materialen uniek is en hun toepassing gebonden is aan een specifiek venster van vochtigheid en temperatuur, hebben we onze eigen materiaalkaarten gebouwd om nauwkeuriger te karakteriseren hoe deze materialen zich zouden gedragen tijdens fysieke tests. ”
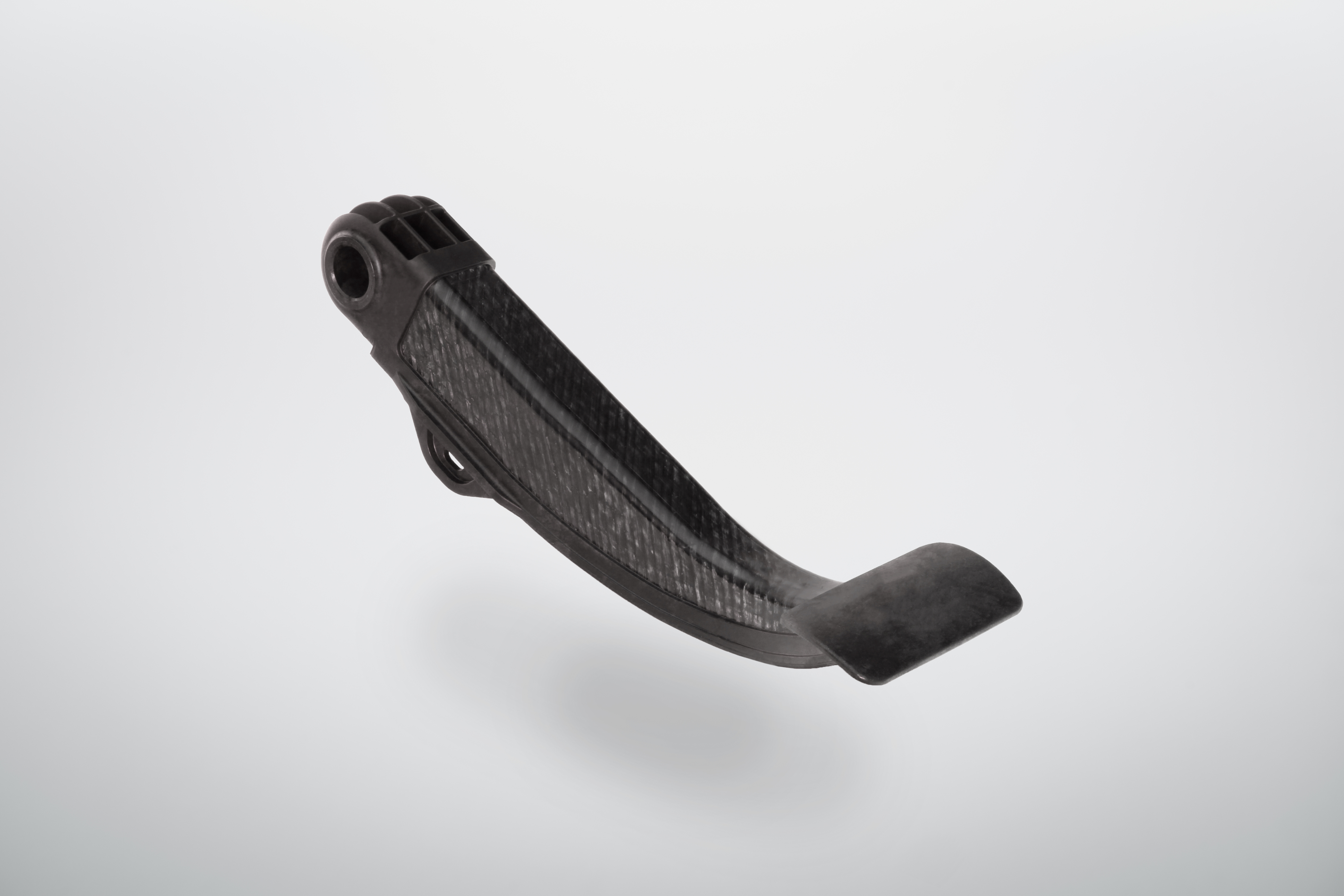
Boge specificeerde de laagstructuur en vezelarchitectuur voor elk materiaal op basis van simulatieresultaten en een bepaald pedaalontwerp. Lanxess Deutschland GmbH (Keulen, Duitsland) levert organoblad in vezelvolumefracties (FVF's) van 45-50%. UD thermoplastische tapes met FVF's van 55-60% werden geleverd door Celanese Corp. (Irving, Texas, U.S.). Short-glass injectiecompounds voor deze toepassing, met een vezelgewichtfractie van 40-60% (FWF), werden door meerdere bronnen geleverd. Alle materialen zijn zwart en hebben een polyamide 6 of 6/6 (PA6, PA6/6) matrix. Om aan de specificaties van de klant te voldoen, is PA6 de standaardhars voor alle drie de composietsoorten. Afhankelijk van de vochtigheids- en temperatuurniveaus tijdens de productie, evenals de beperkte ruimte en de pedaalgeometrie, kan Boge echter ook PA6/6 gebruiken voor de overmolding hars, aangezien de twee polymeren vergelijkbaar genoeg zijn om goed te hechten.
Drie-staps productie
Parallel aan het ontwerp werkte het team aan een productieproces in drie stappen. In de eerste stap wordt een op maat gemaakte vezelplaat gemaakt door voorgesneden en voorgeconsolideerde organoplaat te gebruiken als een stabiele basis waarop stroken UD-tape strategisch worden vastgehecht die zijn uitgelijnd met laadpaden om de schaalstructuur van het onderdeel te versterken. In de tweede stap wordt de plano verplaatst en achtereenvolgens verwarmd, geconsolideerd en gevormd/gedrapeerd. In de derde stap wordt het overgoten met een korte glassamenstelling om de geribbelde structuur te creëren.
Om snelle cyclustijden te bereiken, was robothandling een gegeven voor dit systeem. Een belangrijk proceskenmerk dat het team wilde toevoegen, was de flexibiliteit om tapes van elke lengte, in elke richting en in elke positie aan één kant van de organosheetschaal te plaatsen en deze tapes met een laser aan de schaal te hechten, zodat ze niet verschuiven. in de volgende stappen.
Een andere beslissing van het team was om de op maat gemaakte blank niet direct na de layup te preconsolideren, maar net voor het draperen/preformen en overmolding. Het team was van mening dat het materiaal sowieso tijdens het draperen/voorvormen opnieuw moest worden verwarmd en om kosteneffectief te zijn, moesten ze de totale cyclustijd in de buurt van 1 minuut houden. Daarom verwarmt en consolideert Boge de blanco net voor het draperen/preformeren met behulp van een snelle temperatuurstijging in combinatie met hoge druk om een sterke mechanische verbinding tussen tape en organoblad te creëren. De verwarming stopt en de temperatuur van het onderdeel begint te dalen als de nog hete, geconsolideerde plano in de draperende holte beweegt voordat deze opnieuw wordt bewogen en in een tweede holte wordt overgoten met ribben en andere functionele kenmerken. Sterke mechanische bindingen, met geverifieerde polymeerketenpenetratie, worden bereikt tussen alle drie de materialen. Er is geen nabewerking nodig.
Om te voldoen aan de kwaliteitseisen voor deze veiligheidskritieke onderdelen, heeft het team ook een snel, nauwkeurig en Industrie 4.0-conform systeem ontwikkeld dat gebruikmaakt van vision-, kracht-, tijd-, druk- en temperatuursensoren die het materiaal bij elke stap in het productieproces controleren. Het systeem slaat die gegevens vervolgens op en koppelt ze terug aan het unieke identificatienummer van elk pedaal. Dit zorgt voor 100% traceerbaarheid van alle betrokken materialen, ploegen en procesinstellingen.
Verwezenlijkingen tot nu toe
Boge's op maat gemaakte, volledig geautomatiseerde en op kwaliteit gecontroleerde proces maakte de stap van prototype naar grootschalige serieproductie in 2018. De huidige productiecel produceert ongeveer elke minuut een nieuw pedaal en kan tot 1 miljoen onderdelen per jaar produceren. De volledig composietpedalen gebruiken 33% minder organoblad dan eerdere ontwerpen en de nominale wanddikte daalde van 3 naar 2 millimeter. De pedalen zijn ook 50-55% lichter, maar voldoen aan of overtreffen de sterkte-eisen voor staal. De lichtere pedalen verbeteren het rijgevoel voor de consument en het hele systeem is aan het einde van de levensduur 100% recyclebaar. Met het huidige proces zijn composietpedalen vergelijkbaar met aluminium en iets duurder dan staal. Andere auto- en sporttoepassingen zijn in ontwikkeling.
Wat brengt de toekomst als autofabrikanten middelen verschuiven naar vlootelektrificatie? "Naarmate drive-by-wire [elektromechanische bedieningssystemen] en elektrificatie van de aandrijflijn steeds gebruikelijker worden, kunnen de gaspedalen verdwijnen, maar de rempedalen blijven bestaan", mijmert Häffelin. "We zullen echter waarschijnlijk meer elektronica-integratie zien, inclusief sensoren, in rempedalen. Dat zal de complexiteit van onderdelen aanzienlijk vergroten, waardoor composieten nog meer worden concurrerend dan metalen.”
Materiaalgebruik, processtappen en apparatuurcriteria worden in meer detail uitgelegd in CW ’s vervolgartikel van januari 2021, “Op maat gemaakt proces produceert elke minuut composiet rempedaal.”
Hars
- Lange vezelversterkte nyloncomposiet vervangt aluminium motorbehuizing
- Continu-vezelversterkte thermoplastische composiet volledig gemaakt van natuurlijke hulpbronnen
- Solvay breidt capaciteit thermoplastisch composiet uit
- Oribi Composites, Packard Performance-partner voor off-road powersports thermoplastisch composiet wiel
- Fraunhofer stelt geautomatiseerde Engel-productiecellen in gebruik voor R&D van thermoplastisch composiet
- Consortium streeft naar oplossingen voor thermoplastische composietstructuren van koolstofvezel
- INEOS Styrolution gaat productielocatie bouwen voor StyLight thermoplastisch composiet
- Xenia introduceert CF/PP thermoplastische composietverbindingen
- Thermoplastische composietbuis in opkomst in de diepzee
- NIAR's NCAMP kwalificeert TenCate thermoplastisch composiet
- TenCate viert assemblage van thermoplastisch composietconsortium in Brazilië