De vorming van een leider in de thermoforming-industrie.

Hytech biedt oplossingen voor het thermovormen, embossing en trimmen van dunne film kunststoffen. Hun focus ligt voornamelijk op dunne film plastic onderdelen die een nauwkeurige grafische registratie vereisen. Er zijn ook niet-grafische toepassingen waarbij de Hytech-vormprocessen voordelen bieden ten opzichte van andere traditionele vormprocessen. Hun gepatenteerde technologieën worden gebruikt door OEM's in de automobiel-, huishoudelijke, medische, luchtvaart- en militaire industrie.
Ontwikkelen van gepatenteerde processen en geavanceerde thermoforming en Match Metal Trim Dies
Vandaag de dag heeft Hytech productiefaciliteiten die productiediensten en gereedschappen aanbieden in de VS en Europa en levert het procesontwikkeling en apparatuur vanuit het Amerikaanse hoofdkantoor in Phoenix, AZ.
Hytech vroeg Rogers waarom de koepel niet van plastic was gemaakt. Ze kwamen erachter dat niemand de koepel van plastic maakte. Dus het eerste wat ze deden was een gespecialiseerde thermovormtechnologie uitvinden voor het embosseren van een koepel in polyester en vervolgens miljoenen van deze koepels verkochten aan de Rogers Corporation en vervolgens tientallen miljoenen ervan aan Hewlett Packard verkochten voor hun financiële of wetenschappelijke rekenmachines. De productievoordelen (in vergelijking met de metalen koepels) op onderdelen zoals membraanschakelaars is dat je 100 plastic koepels in een enkele plaat kon leggen, terwijl je bij de metalen koepels alle 100 op de locatie moest kiezen en plaatsen.
Toen Hytech deze dome-lagen begon te verkopen aan makers van membraanschakelaars, zeiden de makers van membraanschakelaars:"Dit is echt geweldig, maar ik heb problemen met het embosseren van mijn overlays om over je domes te gaan." Dus vonden de oprichters van Hytech een andere vormtechnologie uit, hydroforming genaamd, waarbij ze de overlays in reliëf maakten. Op dat moment hadden ze een technologie om de overlay van een membraanschakelaar te embosseren en ze hadden een technologie voor het embosseren van de voelbare laag die onder de overlay gaat.
Match Metal Trim Die-proces:Hytech's voortdurende ontwikkeling en vooruitgang van gepatenteerde technologie heeft hen tot een wereldwijde expert gemaakt voor driedimensionale
overeenkomen met metalen sierlijsten voor dunne-film plastic.
Halverwege de jaren 90 kwam de technologie van in-mold decoratie (IMD) of in-mold-labeling (IML) of film-insert molding (FIM) langs die een plat zeefdrukplastic (meestal polycarbonaat) neemt en het vormt in de 3D-vorm van een spuitgietmatrijs. De decoratieve film wordt in de mal geplaatst, de mal wordt geïnjecteerd en wanneer de mal opengaat, wordt het onderdeel versierd.
Dit viel samen met de tijd dat Hytech de hydroforming- en polydome-processen had. Klanten kwamen naar hen toe en vroegen hen om plastic te embosseren voor deze nieuwe film-insert molding-technologie. Ze ontdekten al snel dat geen van hun processen geschikt was om iets dieper dan 1 mm te doen. Het voordeel van in-mold decoratie is dat je complexe 3D-onderdelen kunt maken met geregistreerde afbeeldingen. Dus ontwikkelden de oprichters, samen met een andere nieuw aangeworven ingenieur, Accuform − een hogedruk-luchtvormende technologie waarmee ze tot 50 mm tekendiepte kunnen doen met geregistreerde grafische afbeeldingen. Nu kunnen ze de positie, locatie en grootte van verschillende afbeeldingen behouden over complexe driedimensionale oppervlakken.
Dit resulteerde in Hytech bouwdelen voor de IMD industrie. Ze kwamen er al snel achter dat, hoewel ze gemakkelijk en continu de vormgereedschappen konden bouwen, ze worstelden met het bouwen van match-metal trim matrijzen. In die tijd bouwde niemand ter wereld driedimensionale snijgereedschappen van matchmetaal voor dunnefilmkunststoffen. Hytech moest die technologie dus zelf ontwikkelen.
In het begin besteedden ze de geharde stalen componenten uit aan leveranciers die ze produceerden met zinkvonken. Dit bracht Hytech ertoe te geloven dat ze moesten investeren in een zinkvonk en het werk in huis moesten halen. Dus, samen met de zinkvonk-EDM, investeerden ze ook in een draadvonken en alle nieuwe software en begonnen ze hun eigen trimgereedschappen te bouwen. Hoe goed ze ook waren in het proces, ze wisten dat het veel beter zou zijn als ze nog een tiende van de omtrek van het geharde staal konden halen. Ze wisten dat ze het niet konden doen op hun huidige bewerkingscentra omdat ze dat soort tolerantie niet aankonden. Hytech CEO, Fred Himmelein, legt uit:“In de loop der jaren zijn we beter en beter geworden en hebben we het maximale eruit gehaald hoeveel beter we konden worden. We konden gewoon niet de precisie krijgen, de tienden die we wilden. We wilden een speling hebben tussen de bijpassende gehard stalen componenten van +/- .0003” maar we konden daar gewoon niet komen met de zinkvonk-EDM- en VMC-apparatuur die we hadden. Dat heeft ons naar DATRON geleid.”
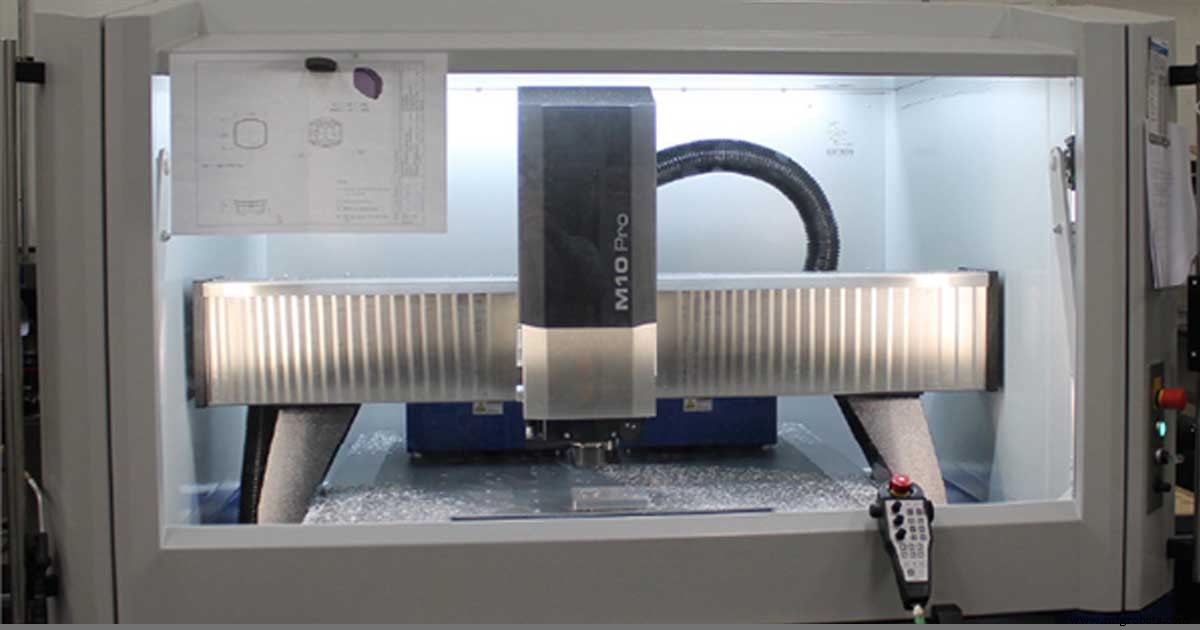
Onderzoek naar geavanceerde technologieën voor thermovormen en de perfecte oppervlakteafwerking
Het hoofd van de gereedschapswinkel van Hytech, Dave Blandino, deed zeer grondig onderzoek en analyse van beschikbare bewerkingscentra en presenteerde verschillende toonaangevende oplossingen aan het managementteam. Uiteindelijk werd besloten om een DATRON M10 Pro high-speed bewerkingscentrum aan te schaffen. Himmelein zegt:"Om een combinatie van redenen, zoals precisie, besturingssoftware (NC-programmering), de kosten van spindelonderhoud, de ondersteuning en de locatie van ondersteuning, heeft Dave het onderverdeeld in een matrix van ongeveer 10 of 12 elementen, en het liet ons duidelijk zien dat DATRON de juiste keuze was.”
Maar de keuze om de DATRON aan te schaffen was niet alleen gebaseerd op deze matrix. Er was ook een runoff- of benchmarkingproces dat elke machinefabrikant moest voltooien - elk produceerde exact hetzelfde onderdeel voor een concurrerende vergelijking. Hoewel het vermogen om IMD-toepassingen van staal te frezen een van de parameters was, was de oppervlakteafwerking voor de vormende kant van hun bedrijf van het grootste belang in deze test. Dat komt omdat hun hogedrukvormtechnologie zo nauwkeurig is dat eventuele gereedschapsmarkeringen in het formulierblad te zien zijn, zelfs als ze zijn gezandstraald. Himmelein legt uit, "Je zou kunnen kijken naar een vormkern die we gaan vormen, het is gezandstraald en het ziet er prachtig uit en de afwerking ziet er geweldig uit, maar wanneer we het vormen, zie je een gereedschapsmarkering die je kunt het niet geloven.” In die tijd was veel van het werk dat ze deden zeer precieze driedimensionale bedrijfslogo's over de bovenkant van een gevormd onderdeel. Het is duidelijk dat het uiterlijk van elk logo van groot belang was voor de klant die ze voor het werk contracteerde. Himmelein legt uit, "Dat vormdeel is het inzetstuk dat in de spuitgietmatrijs gaat. Het is een gevormde applicatie of film die in de spuitgietmatrijs gaat en weer wordt gevormd, zodat wanneer de mal opengaat, het onderdeel wordt versierd. De cosmetica op deze onderdelen is absoluut essentieel en het is net zo'n strikte cosmetische vereiste als bij de fabricage.'
Hytech Tooling Manager, Dave Blandino, legt hun ervaring met de CNC-leveranciers en de concurrerende benchmarkingtest verder uit:“We hebben uitgebreid onderzoek gedaan en verschillende CNC-fabrikanten de kans gegeven om een onderdeel voor ons te snijden. Ik vroeg hen om een onderdeel voor me neer te zetten dat hun machine zou verkopen en niemand kwam in de buurt van het onderdeel dat DATRON produceerde. Ik heb onderdelen ontvangen van andere fabrikanten van gereedschapsmachines en de kwaliteit voldeed niet aan mijn verwachtingen. Maar binnen 2 weken nadat ik DATRON het model had gestuurd, vloog ik naar Duitsland, en niet alleen was de gastvrijheid geweldig, maar DATRON zette me een rol voor die ik echt niet had verwacht gezien het korte tijdsbestek. Het was verreweg de beste van wat alle CNC-leveranciers produceerden. Toen ik terugkwam in de Verenigde Staten en het DATRON-monster aan de andere verkopers liet zien, zeiden ze:'O, ze hebben dit gepolijst' en ik zei:'Nee, dat deden ze niet, dat is zo uit de machine!' maar dat deden ze niet geloof me. Het is een feit dat we elk onderdeel nauwgezet hebben geïnspecteerd op een RAM Optical comparator met een vergroting van meer dan 200, dus het is niet alleen wat je ziet met je ogen of een vergrootglas. Ons proces laat van alles en nog wat zien. Bij thermovormen, als je zelfs maar het kleinste merkteken van het gereedschap hebt, zal het in de film verschijnen. Het is dus uiterst belangrijk om de oppervlakteafwerking te hebben die de DATRON ons geeft.”
Afgezien van kwaliteit, is er een overeenkomstige kostenbesparing in verband met het elimineren van secundaire bewerkingen zoals handwerk, schuren en polijsten en Himmelein crediteert DATRON met een resulterende reductie van 90% in handtijd. Er zijn ook beperkingen aan het schuren, zoals Blandino uitlegt:“Je kunt altijd handwerk doen met schuurpapier, maar als je een gereedschap hebt dat meerdere holte, je gaat het onderdeel niet twee keer op dezelfde manier schuren. Als je 15 tot 20 gaatjes hebt, krijg je variatie en die variatie vertaalt zich in vormen, trimmen en vormen. Wat we in wezen doen, is het onderdeel van de DATRON verwijderen en we raken het niet aan en dat is ons doel. De onderdelen zijn klaar om direct vanaf de machine in onze gereedschapsassemblages te worden gemonteerd. Soms is een lichte parelstraaltextuur een eis van de klant, maar schuren of polijsten is niet nodig.”
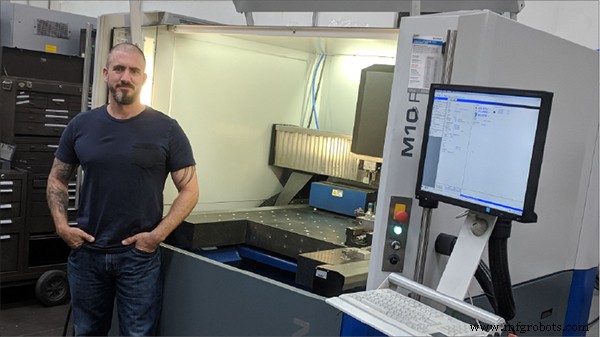
Hoge tolerantie vereist voor het produceren van Match Metal Trim Dies (Stempelstempels)
Dus nu gebruikt Hytech hun draadvonken om de A-zijde geharde stalen component te maken die hun vaste tolerantie vertegenwoordigt. Vervolgens fabriceren ze het onderdeel van gehard staal aan de B-zijde, het onderdeel dat past bij het stuk aan de A-zijde. Ze laten de matrijskern meestal tussen .0005” en .0008” zwaar en ze gebruiken de DATRON M10 Pro om een tiende per keer te nemen totdat het past. Himmelein zegt:"Dit is waar de DATRON echt uitblinkt, omdat we relatief snel een tiende tegelijk kunnen doen, de deur openen en alles gemonteerd laten en onze pasvorm testen en als het er niet is, sluiten we de deur en rennen we nog een tiende .”
De combinatie van de draadvonkmachine en de DATRON-machine heeft echt het verschil gemaakt voor Hytech Forming en ze zijn de wereldwijde expert geworden op het gebied van driedimensionale metalen sierlijsten voor dunne-film plastic.
Blandino legt uit, “Vroeger moesten we deze componenten uitbesteden aan winkels die de apparatuur hadden om dat aan te kunnen en sinds we de DATRON kochten, hebben we al dat werk in huis gehaald. We doen lichte afwerkingspassen om krappe toleranties te behouden op onze warmtebehandelde A2-stalen onderdelen. Deze onderdelen zijn gereedschapscomponenten die we hier ontwerpen en fabriceren. Een van de visies van ons bedrijf is trimmen. We houden van het thermovormen van dunne-film kunststoffen, maar de andere kant daarvan is dat we het plastic moeten bijsnijden als het eenmaal gevormd is en deze bijgesneden vormen moeten precies in de mal passen met nauwe toleranties van +/- een paar duizendsten van een inch. Maar om het trimmen daadwerkelijk te laten plaatsvinden, moeten de toleranties van de componenten die we bewerken +/- een paar tienden van een inch zijn. Dit zijn de componenten waarmee we onze snijmallen bouwen.”
Blandino crediteert de DATRON-technologie ook voor het toevoegen van flexibiliteit aan hun ontwerpproces. “Het heeft ons ook in staat gesteld om onze tooling veel efficiënter te ontwerpen. Vroeger was de enige apparatuur die we konden gebruiken om die nauwe toleranties te handhaven onze EDM-draad. Het probleem met EDM-draad is natuurlijk dat niet alles een doorgang is zak. Dus dat beperkte onze ontwerpflexibiliteit omdat we rond die beperking moesten ontwerpen. Met de DATRON kunnen we vrijer ontwerpen en dingen doen zoals we ze wilden doen.”
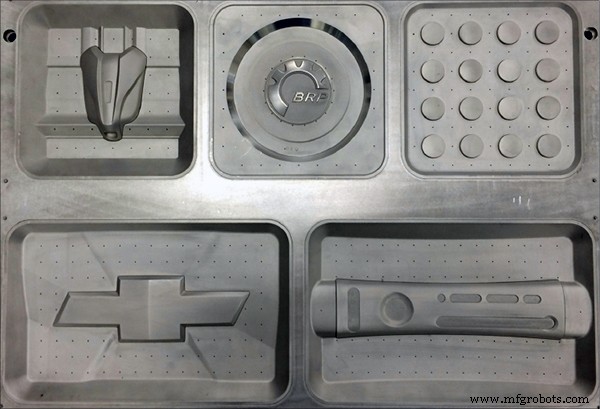
De DATRON M10 Pro is zo kritisch geworden voor de kwaliteit van hun eindproduct en Blandino zegt dat ze hieraan worden herinnerd wanneer de DATRON achterstand heeft met werk en ze gedwongen zijn om werk naar andere CNC-apparatuur te verplaatsen. “Zelfs met het handwerk kun je niet in de buurt komen van de oppervlakte afwerking die we op de DATRON krijgen. Bovendien hebben we een maximale spilsnelheid van 15k 12k en 10k op de andere CNC-apparatuur, dus we moeten onze feeds met een goede 100% verminderen. Vanwege de spiltrilling en speling op de kogelomloopspindel met onze andere bewerkingscentra, de afwerking die we moeten doen is zwaar schuren. Daarom pleit ik echt voor een tweede DATRON-machine. We gebruiken de andere bewerkingscentra als onze 'Op One-machine', waar we al het vlees van de rug en alle niet-kritieke oppervlakken ruw maken. Deze machines kunnen die taak goed aan.”
Deuren openen naar een nieuwe inkomstenstroom en een jaarlijkse stijging van 25% Opbrengst
CEO, Fred Himmelein, geeft DATRON de eer voor de kwaliteit die het Hytech heeft geholpen om te leveren aan een breed scala van industrieën, waaronder de automobielindustrie en de ruimtevaart. Himmelein is ook onder de indruk van de flexibiliteit van de DATRON en de andere ondersteunende processen die het heeft beïnvloed en verbeterd sinds de installatie. Ze hebben bijvoorbeeld een project dat ze al tien jaar voor een klant doen, waarbij ze .25-inch acryl snijden met een CO2-laser, wat uitstekend werk levert en een prachtig gepolijste rand produceert. Maar na een decennium besloot de klant dat ze van materiaal wilden wisselen en polycarbonaat wilden gebruiken om het risico op schade aan de onderdelen tijdens hun levenscyclus te verminderen. Omdat .25-inch polycarbonaat niet met een laser kan worden gesneden zonder dat het verbrandt en een gevaar voor de gezondheid oplevert, moesten ze een alternatief proces vinden. Dus deden ze een testsnede op de DATRON M10 Pro met behulp van een DATRON-vingerfrees die speciaal is ontworpen voor het frezen van acryl. Het resultaat was een grote overwinning voor zowel Hytech als hun klant. De DATRON sneed de onderdelen zelfs sneller uit polycarbonaat dan de laser ze uit acryl had gesneden, de oppervlakteafwerking was vergelijkbaar en de klant kon overschakelen naar het gewenste materiaal.
De DATRON M10 Pro is compatibel met een breed scala aan CAM-softwarepakketten en Hytech heeft in een aantal van deze pakketten geïnvesteerd en uitgebreide tests uitgevoerd om de prestaties en oppervlakteafwerking te maximaliseren. Blandino zegt:"We hebben waarschijnlijk meer softwaretests gedaan dan de meeste winkels. We gebruiken de contour smoothing van de DATRON-software, maar het is ook een combinatie van de dynamiek en de programmeerstrategieën die allemaal bijdragen aan een perfecte oppervlakteafwerking. We hebben wat getest met verschillende programmeersoftware, waaronder SolidCam, SOLIDWORKS, FeatureCAM, Fusion 360 en PowerMill en we vergelijken appels met appels met verschillende snijplotters, snelheden en feeds. We gebruiken dus een combinatie van wat de software te bieden heeft gecombineerd met wat DATRON te bieden heeft, en we kwamen met een formule voor de beste oppervlakteafwerking die je kunt bereiken met 3-assig frezen. Fusion heeft echt een goede basis voor DATRON en biedt uitstekende oppervlakteafwerkingen in combinatie met Dynamics en Contour Smoothing die de M10 te bieden heeft. Momenteel is onze primaire CAM
oplossing ligt bij Autodesk. Er wordt continu getest en de DATRON is een uitstekende aanvulling op de postprocessors van alle software.”
Ze moeten er de mond vol van houden, maar Hytech kan ons vertellen dat ze net een bestaande industrie betreden met een nieuwe manier om componenten te maken die uiterst nauwkeurig machinaal bewerkt moeten worden. Fabrikanten binnen die branche kwamen eigenlijk naar Hytech omdat ze een foto van hun DATRON M10 Pro op hun website hebben staan. Tijdens de laatste testronde voor deze industrie liep het onderdeel meer dan 200 uur. Dat komt omdat het onderdeel zeer kleine snijplotters nodig heeft die een kleine overstap maken om 3D-contouren uit te voeren en zelfs tientallen uren kunnen gaan zonder gereedschapswisseling. Met de machine die momenteel 24/7 draait, is het toevoegen en extra M10 Pro aanstaande. Deze nieuwe activiteit zal naar verwachting resulteren in een omzetstijging van 25% voor het bedrijf.
CNC machine
- Van CM naar EMS naar MSP:de evolutie van een industrie
- De voedingsindustrie heeft dit jaar wat veerkracht nodig
- Wat willen klanten in het tijdperk van Industrie 4.0 echt?
- Waarom moeten we eerlijk zijn tegen de klanten?
- CNC-bewerking in de auto-industrie
- Duurzaamheid:de uitdaging van Industrie 4.0
- Industrie 5.0:de nieuwe revolutie
- Industrie Spotlight:de mijnbouw
- Het Opportunity Kwadrant:vier delen voor het succes van Industrie 4.0
- Wat is de grafische industrie?
- Wat is de verfindustrie?