4 manieren om een consistente snijdiepte te garanderen
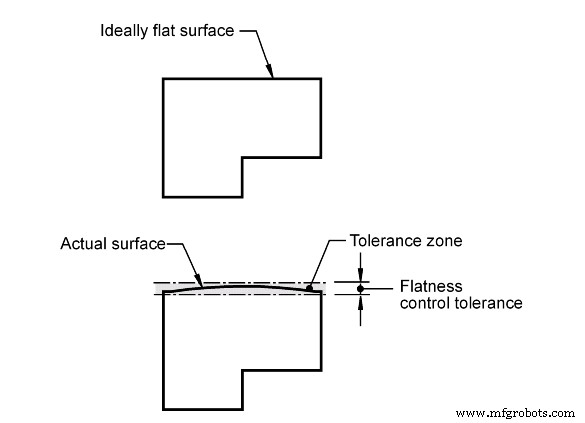
4 manieren om een consistente snijdiepte te garanderen (zelfs op oppervlakken die allesbehalve vlak zijn): Wat uw CNC betreft, is de wereld een en al zonneschijn en rozen:uw snijgereedschap buigt of verslijt nooit, uw opspanning is stijf en trillingsvrij en het oppervlak van uw werkstuk is perfect vlak. Echter, degenen onder ons met grijze materie hier in de echte wereld, weten dat de waarheid van de situatie allesbehalve perfect is - gereedschapslijtage, armaturen buigen, en dat oppervlak dat je gaat snijden is ongeveer net zo plat als de goede aarde zelf .
De video hierboven legt het allemaal uit!
Video met dank aan #rapiddtm – bezoek ze op Facebook!
Als je onze blog volgt, weet je al dat we hebben gesproken over hoe je kunt ruziën over het doorbuigen van gereedschap, en dat we enkele tips hebben gedeeld over de beste werkwijzen voor het vasthouden van werkstukken. Vandaag gaan we een paar trucjes bespreken die je kunt gebruiken om een consistente snijdiepte te behouden bij het graveren, markeren of frezen van oppervlakken die niet bepaald het voorbeeld zijn van vlakheid.
Vlakheid definiëren:
Simpel gezegd, de term "vlakheid" wordt gebruikt om een gebied tussen twee evenwijdige lijnen te beschrijven waarbinnen een oppervlak moet liggen. Deze specificatie werkt vaak in combinatie met andere dimensionale aanduidingen op de afdruk om het bereik van mogelijke locaties van een bepaald oppervlak te beschrijven:
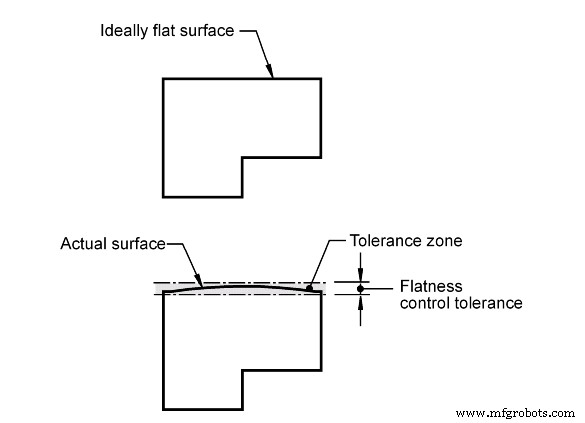
Afbeelding tegoed:http://www.engineeringessentials.com/gdt/flatness/flatness.htm
Zoals je je misschien wel of niet gerealiseerd hebt, is geen enkel oppervlak perfect vlak - er zijn zelfs maar heel weinig oppervlakken die zelfs maar in de buurt komen van perfecte vlakheid - en als het gaat om gefabriceerde onderdelen, kost vlakheid geld. Dus als het niet plat hoeft te zijn, of als de afdruk het niet als plat definieert, moet je aannemen dat het echt niet plat is. Afhankelijk van wat u met een bepaald oppervlak moet doen, zal de vlakheid (of het ontbreken daarvan) een sleutelrol moeten spelen in uw freesstrategie.
Consistente snijdiepte Methode 1:Kwalificeer het oppervlak
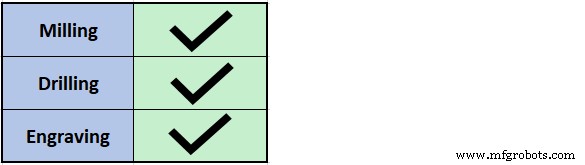
Als je in staat bent om dit te doen, is het kwalificeren van het oppervlak verreweg de gemakkelijkste en meest zekere manier om ervoor te zorgen dat het oppervlak waarop je gaat werken redelijk vlak en echt is. Het kwalificeren van een oppervlak is gewoon fancy machinistenpraat voor het vlakfrezen van het hele oppervlak, met een paar duizendsten per keer totdat het hele oppervlak redelijk uniform is in termen van vlakheid. Een kwalificatiepas is vaak de eerste stap die u ziet bij het bekijken van een freesproces op een werkvloer of online en dit heeft een aantal redenen, niet in de laatste plaats om de vlakheid van het betreffende oppervlak te garanderen.
Wanneer u begint met een stuk knuppel of ruw materiaal, is het kwalificeren van een oppervlak bijna altijd een optie en in het algemeen is dit gewoon een goede oefening van de machinist. Soms is het echter gewoonweg geen optie om het oppervlak te kwalificeren, zoals bij het werken met gegoten materiaal, een smeedstuk of met anderszins voltooide onderdelen die alleen moeten worden gemarkeerd of geserialiseerd. In deze gevallen zal een andere strategie moeten worden gevolgd om tot een goed resultaat te komen.
Consistente snijdiepte Methode 2:gebruik van een veerbelast graveergereedschap
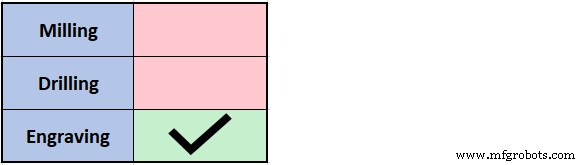
Als alles wat u hoeft te doen een eenvoudig graveer- of onderdeelmarkeringsproces is, en uw oppervlak een beetje "over de hele kaart" is, is een veerbelast graveergereedschap misschien precies wat de dokter heeft besteld. Veerbelaste gereedschappen zijn er in een paar verschillende varianten, waarbij de meest populaire versies een veerbelaste versie zijn van een traditioneel graveergereedschap met gespleten schacht en een veerbelaste "drag-graveerbit", ook bekend als een "schrijver"-gereedschap.
Geveerd graveergereedschap:dit gereedschap kan u helpen om in de marge te blijven bij eenvoudige graveertaken.
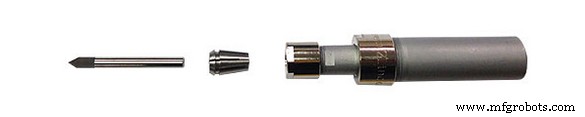
Verende graveergereedschappen bevatten een samendrukbaar mechanisch systeem tussen de spilinterface en het snijgereedschap. Deze gereedschapsassemblages hebben meestal een veerweg van 0,20" tot 0,40", zodat ze een vrij dramatische verandering in Z-hoogte kunnen absorberen terwijl ze toch een consistente neerwaartse druk op het werkstuk behouden. Veerbelaste graveerbits maken gebruik van een getipt graveergereedschap met gespleten schacht en kunnen als zodanig een verscheidenheid aan graveerbreedtes en -diepten produceren. Sleepgraveer- of schrijfgereedschap wordt letterlijk alleen over een oppervlak gesleept en is niet ontworpen om een roterend element in het proces op te nemen. Als resultaat zijn aftekengereedschappen echt alleen geschikt voor het markeren van zeer ondiepe onderdelen.
Hoewel deze gereedschappen niet veel zullen helpen als het gaat om frees- of boortoepassingen, presteren ze zeer goed voor het markeren van onderdelen met een geringe tot gemiddelde diepte. Er zijn echter enkele nadelen aan dit type gereedschap:een gebruikelijke schachtmaat voor dit gereedschap is ¾”, wat voor sommige spindels te groot kan zijn. Omdat deze gereedschappen een mechanische assemblage zijn, zijn ze meestal beperkt tot maximaal 10.000 tpm. Deze beperking kan u ertoe dwingen uw voedingssnelheid te verlagen, waardoor uw cyclustijd toeneemt.
Dus als je gereedschap nodig hebt om duizend gegoten aluminium onderdelen te serialiseren, zal een veerbelast gereedschap waarschijnlijk de klus klaren. Als u echter van plan bent een frees- of boorproces te voltooien, of als de klus een diepe, brede of ingewikkelde/hoge kwaliteit gravure vereist, moet u wellicht andere methoden gebruiken om de klus te klaren.
Consistente snijdiepte Methode 3:gebruik van een tastsysteem om een onregelmatig oppervlak in kaart te brengen
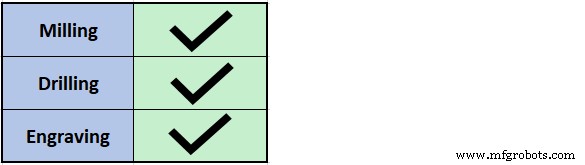
Bij het in kaart brengen van het oppervlak via touch-probing wordt meestal de machine een aantal basisgegevens gegeven over wat u wilt meten:grootte van het sondegebied, spoed van het sonderingsrooster, enzovoort. Van daaruit zal de machine het werkstuk zo vaak aanraken als nodig is om het gespecificeerde gebied tot de gewenste rasterafstand te tasten. Zodra de tastcyclus is voltooid, neemt de machinebesturing het snijbestand dat is geprogrammeerd om te worden gesneden op een vlak 2D-oppervlak en wijzigt het met de variatie in Z van het werkstuk die tijdens de meetcyclus is gevonden. Op deze manier zal de diepte automatisch variëren wanneer de frees het proces van frezen of graveren op het oppervlak uitvoert, zodat u een consistente snijdiepte krijgt, ongeacht de variatie in de Z-hoogte van het oppervlak.
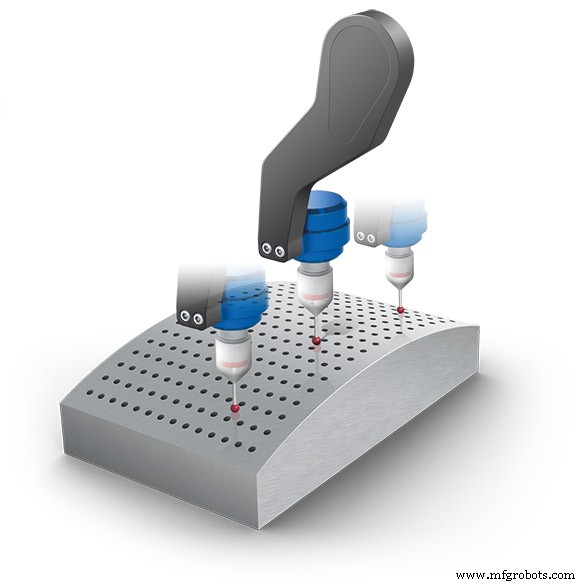
Niet alle CNC-machines bieden touch-probing en het in kaart brengen van oppervlakken is niet altijd een optie als dat wel het geval is. Maar als uw machine sondeer- en oppervlaktekartering heeft, is het geen slecht idee om er vertrouwd mee te raken - u weet nooit wanneer het van pas kan komen.
Consistente snijdiepte Methode 4:CMM-oppervlaktetoewijzing en beeldprojectie in CAM
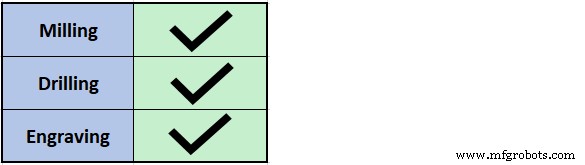
Wanneer al het andere faalt ... wanneer u het oppervlak niet kunt kwalificeren, wanneer een veerbelast gereedschap niet zal doen wat u nodig hebt en uw CNC-machine geen taster heeft, wanneer u een CMM hebt liggen die beschikbaar is voor gebruik en je vindt het niet erg om wat CAM-werk te doen, er is een laatste redmiddel.
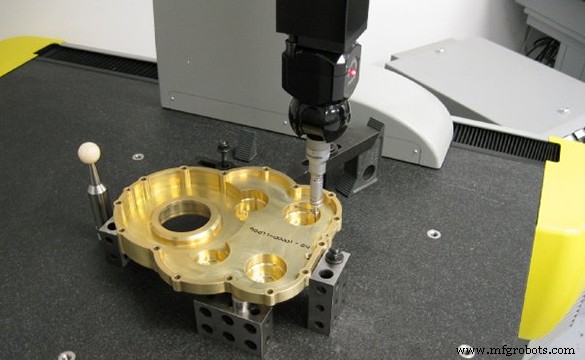
Foto hierboven met dank aan #rapiddtm – bezoek ze op Facebook!
Het gebruik van een CMM om een oppervlak in kaart te brengen om hoogte-onregelmatigheden te compenseren lijkt sterk op het doen op de CNC-machine zelf - maar zonder de luxe om het in kaart brengen, frezen en NC in één te integreren, wordt het proces veel arbeidsintensiever.
Dit proces is zo ingewikkeld dat alleen al hiervoor een heel artikel zou kunnen worden geschreven. In een poging om beknopt te zijn, zal ik het terugbrengen tot een stapsgewijze samenvatting:
- 1. Laad het werkstuk op de CMM
- 2. Meet handmatig zoveel punten als nodig is om volledige oppervlaktevariabiliteit binnen het werkgebied te realiseren
- 3. Exporteer de resulterende puntenwolk naar uw CAD-software
- 4. Maak splines die de gemeten punten verbinden om een 3D-oppervlaktekaart te maken
- 5. 3D-oppervlaktekaart exporteren naar CAM-software
- 6. Projecteer artwork/gefreesde features op het 3D-oppervlak
- 7. Genereer de benodigde gereedschapspaden en post het uitgesneden bestand naar uw CNC
- 8. Laad het werkstuk op de CNC en voer het onderdeel uit
Voor alle duidelijkheid: dit proces zou voor elke onderdeelrun 100% moeten worden herhaald. Zoals u waarschijnlijk kunt zien, kan het gebruik van deze methode gemakkelijk een klus klaren die in ongeveer een dag van begin tot eind zou worden gedaan met behulp van een tastsysteem in de machine, en het zou enkele dagen kunnen duren - simpelweg vanwege de vervelende aard van het gebruik van een CMM om het oppervlak in kaart te brengen.
Niets in deze wereld is perfect - maar het vermogen om met onvolkomenheden om te gaan om een goed resultaat te produceren, ongeacht wat een van de dingen is die goede machinisten onderscheidt van geweldige. Ik hoop dat de methoden die in dit bericht worden beschreven, u een voordeel zullen opleveren de volgende keer dat u wordt geconfronteerd met een werkstuk dat meer op een aardappelchip dan op een pannenkoek lijkt.
CNC machine
- Zes manieren om emissies in magazijnbeheer en distributie te verminderen
- Drie manieren waarop e-tailers de verzendkosten voor shoppers kunnen verlagen
- 8 manieren waarop u uw frees doodt
- Duiken in de diepte van de snede:perifere, sleuf- en HEM-benaderingen
- Hoe nauwkeurigheid en precisie bij CNC-frezen te garanderen?
- 5 manieren om de levensduur van het gereedschap te verlengen en de productiviteit te verhogen
- Oppervlakte-inspectie in handen geven van de machinist van de bewerkingsmachine
- Waterjet:de meest veelzijdige tool in de winkel
- Manieren om de levensduur van Punch te vergroten
- 5 effectieve manieren om de levensduur van ponsgereedschappen te verlengen
- Hoe de G76 draadsnijcyclus volledig te beheersen Aantal gangen en snedediepte uitgelegd