6 verschillende soorten gietprocessen die worden gebruikt in metaalgieterijen
Hier geven we een opsomming en bespreken we 6 verschillende soorten gietbewerkingen die vaak worden toegepast in metaalbewerkingsgieterijen. Kijk hier om de verschillende soorten gietprocessen, voor- en nadelen en toepassingen van elke giettechniek te specificeren.
Gieten is een metaalbewerkingsproces in de gieterij die vroeger gietstukken maakte die verschillende industrieën verbraken, van machinebouw, auto-onderdelen, ruimtevaartonderdelen tot alledaagse huishoudelijke producten.
Het gietproces werkt op het smelten van metaal, het gieten in de vormen en wachten op stolling. De verzamelde bepleistering kan ofwel direct in gebruik worden genomen of moet de verdere bewerkingsstappen doorlopen.
Metaalgieten is een zeer flexibel proces en kan complexe gevormde onderdelen fabriceren, ongeacht de metaalhardheid, maar alleen op de smelttemperatuur van het metaal. Men kan zeggen dat elk metaal dat kan worden gesmolten, kan worden gegoten.
Er zijn verschillende technieken om de metaalbewerking te verwerken en elke gieterij investeert en is gespecialiseerd in bepaalde vormen van gietverwerking. In dit artikel introduceren we de 6 verschillende soorten gietprocessen die vaak worden gebruikt in metaalgieterijen . Je gaat op zoek naar het antwoord op de manier waarop gietdelen worden verwerkt door verschillende soorten metaalgietmethoden en de voor- en nadelen van elke technologie.
1. Groen zand gieten
Wat is groen zandgieten?
De groene zandtechniek heeft zo'n lange traditie in de gietindustrie, maar wordt vandaag de dag nog steeds veel gebruikt vanwege zijn effectiviteit. Het groene zand gieten is een van de verschillende soorten gietwerk die het meest traditioneel is en de voorkeur heeft in de gieterij .
Bij deze gietverwerking is de zandvorm massaproductie. Elke zandvorm wordt één keer gebruikt en wordt gebroken om het bepleisterde materiaal te verzamelen.
Anders dan het gieten van harszand, heeft groen zand een natte inhoud. De term "groen" gaat niet over de kleur, maar over de vochttextuur in het zand. Het heeft het vermogen om zich op natuurlijke wijze te hechten, voornamelijk dankzij kleimiddelen.
Groene zandvorm samenstelling
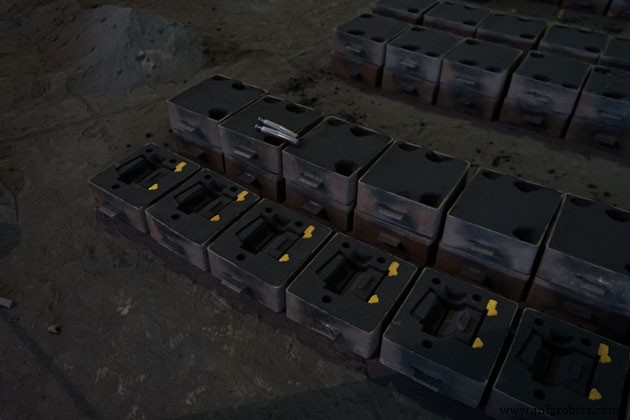
Om een groene zandvorm te maken, combineert de metaalgieterij de volgende componenten:
- Zand:kiezelzand (SiO2), chroomzand (FeCr2O4) of zirkoonzand (ZrSiO4) (ongeveer 75 tot 85%)
- Bentonietklei:(5 tot 11%)
- Water (2-4%)
- Anderen (3-5%)
Het groene zand gietproces
Het groene zand wordt verwerkt door deze stappen te volgen
- Stap 1 :Het zand mengen volgens een verhouding. Het is van groot belang dat dit de hechting van het zandmengsel bepaalt. Elke metaalgieterij volgt de bovenstaande verhouding, maar ze zullen een geheime mengformule hebben door andere middelen toe te voegen.
- Stap 2 :Zand in de vormmaker laden en op het patroon drukken om de vormholte te creëren. Tegenwoordig gebruikt de gieterij een apparaat om het zand te vormen.
- Stap 3 :Door het patroon te verwijderen, wordt een vormholte gemaakt die een vergelijkbare vorm heeft als het intent-gieten.
- Stap 4 :Aanbrengen van een coatinglaag op het matrijsoppervlak om de oppervlakteglans en hittebestendigheid te verhogen.
- Stap 5 :Giet het gesmolten metaal in de vormholte en koel af. Verzamel de ruwbouw en ga verder met bewerkingsstappen (indien nodig).
- Stap 6 :Deze stappen herhalen om voldoende mal te maken voor massaproductie.
Kenmerken voor het gieten van groen zand
Voordeel :
- Het is een zuinige en goedkope productie, vooral in kleine oplagen
- Vereist geen zeer hoogtechnologische investering in de fabrieksfaciliteit
- Vraag een castingbestelling voor gemiddeld en hoog volume aan
- Laat eventuele legeringen in de mal worden gegoten (zowel ferro als non-ferro materialen). Plus kan gebruiken voor bijna patroon en ontwerp
- Het zand kan worden hergebruikt nadat het gietstuk is verzameld. Het bespaart materiaalkosten voor de gieterij.
Beperkingen
- Beperk in gietgrootte. Het kan gietstukken maken met een gewicht van 1 tot 500 pond. Voor de grotere moet het worden overwogen andere gietmethoden.
- Het heeft niet de voorkeur om ingewikkelde castingdetails te casten
- Grote tolerantie waarvoor meer bewerkingsbehandelingen nodig zijn
- Maak zorgen over gietdefecten zoals blaasgat, porositeit, enz. Maar kan worden gecontroleerd door de technische tips van de gieterij.
Groene zandgiettoepassingen
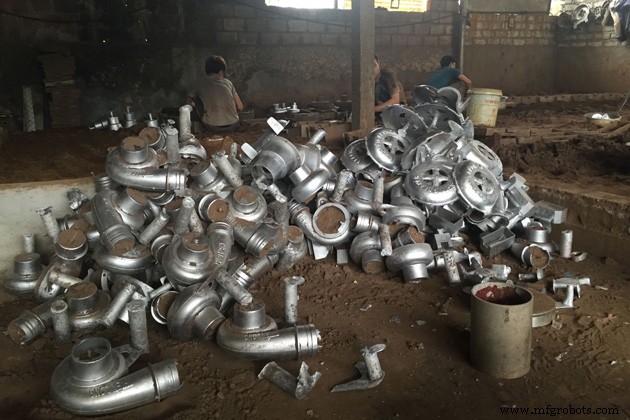
Groenzandgieten is erg populair bij een scala aan toepassingen. In Amerika wordt 42% van de gietstukken gemaakt door middel van het groene zandproces, terwijl gieten zonder bakken 40% kost (de tweede populaire gietmethode).
U vindt de onderdelen voor het gieten van groen zand, van decoratiestukken voor buiten zoals lantaarnpaal, bank, afvalbak; technische details, auto-onderdelen, ruimtevaart, pomphuis tot scheepsboeigewicht, enz.
Lees hier meer over groenzandgieten.
2. Furan hars zandgieten
Wat is zandgieten met furaanhars?
Andere veel voorkomende verschillende soorten gietprocessen in metaalgieterijen zijn furaanharszandgieten. In tegenstelling tot het groene zand dat voor een natuurlijke hechting zorgt, vertrouwt het gieten van furaanharszand op enkele katalysatoren en bindmiddelen om het zand te binden. Bij deze gietmethode worden het zand, furaanhars en katalysatoren met elkaar vermengd en wordt het zandmengsel zelfhardend door de chemische reactie.
Het verzamelde ruwbouw heeft een goede gladde oppervlakteafwerking en een hoge precisie.
Furanhars zandvorm samenstelling
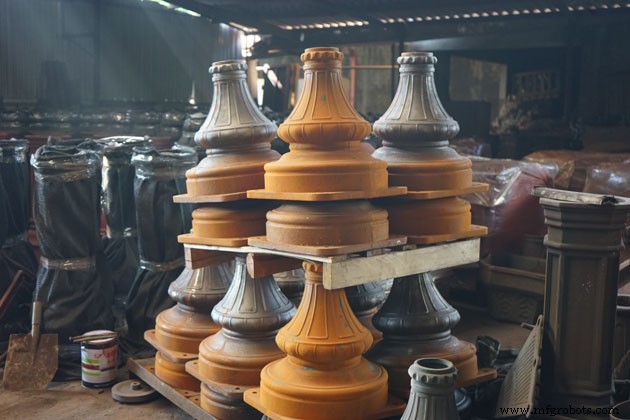
Bij het zandgieten van furaanhars wordt de mal gemaakt met de volgende formule:
- Zand:kiezelzand (SiO2) (40-60%)
- Furahars:0,7-1,3% afhankelijk van de gietmassa. Het is minder of zonder stikstof nodig, afhankelijk van de gietvereisten en de structuur van gietdelen.
Furaanhars speelt een belangrijke rol bij deze gietmethode. Het is een polymeerverbinding met 75% Furfurylalcohol + 11% Formaldehyde + 9% Ure + 5% Water. De verhouding van Formaldehyde en Ureum beïnvloedt de stollingstijd en de sterkte van het harsmengsel, terwijl Furfurylalcohol (FA) de hittebestendige eigenschappen van het mengsel beïnvloedt.
- Katalysator:stollingsmiddel en annexatiemiddelen (30-50%)
Het furaanhars zandgietproces
De processen voor het zandgieten van furaanhars worden toegelicht aan de hand van de volgende tabel:
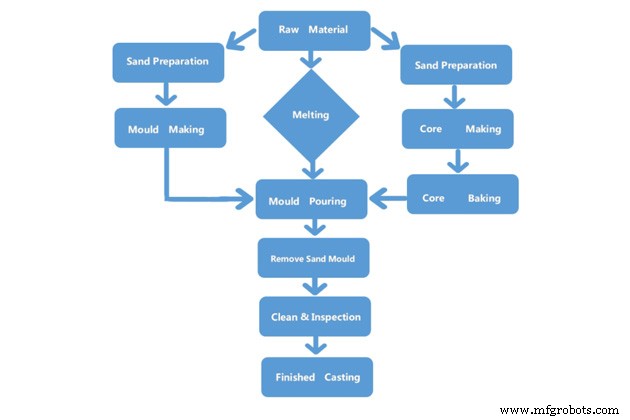
Furaanhars zandgieteigenschappen
Voordeel
- Strakke tolerantie en hoge precisie
- Het biedt een geweldige gladde afwerking van het oppervlak in vergelijking met andere gietmethoden
- Minimaliseer de gietfouten zoals zandgaten, luchtgaten en krimp
- Flexibel in gietmaat. Furanhars zandgieten kan grote stukken laten variëren van een dozijn kilogram tot enkele tonnen gewicht
Beperking
- Het is een duurdere methode dan andere gietprocessen
- Strenge eis voor grondstof
- Creëert milieuproblemen
Furaanhars zandgiettoepassingen
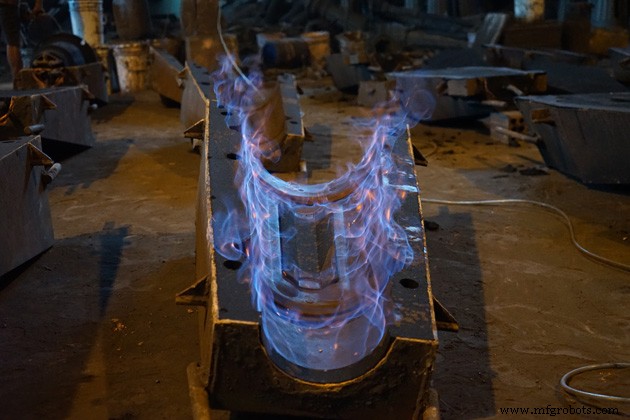
Met zijn uitstekende voordeel heeft de furaanharszandmantel vaak de voorkeur voor het gieten van ingewikkelde en gedetailleerde onderdelen die hoge precisie en nauwe tolerantie vereisen, zoals auto-onderdelen, details van landbouwmachines, ruimtevaartonderdelen, scheepsmotoren, enz.
Lees hier meer over furaanhars zandgieten.
3. Verloren schuimafgietsel
Wat is verloren schuimgieten?
Het verloren schuimgieten is een soort verdampingspatroonproces dat vergelijkbaar is met investeringsgieten. In plaats van wax is het patroon gemaakt van foam in de lost foam methode.
In tegenstelling tot het zandgieten, kan dat patroon worden verwijderd en hergebruikt om andere mallen te maken. Het verloren schuimpatroon kan één keer worden gebruikt en wordt verdampt, wat leidt tot de gietdelen.
Niet zo populair als zandgieten, maar het verloren schuimgieten is een van de verschillende soorten gietprocessen die behoorlijk geweldige eigenschappen blijven die geschikt zijn voor massaproductie van kleine en middelgrote detailgietonderdelen.
Het verloren schuimgietproces
Het gietproces voor verloren schuim volgt deze stappen:
- Stap 1 :patroon maken. Het verloren schuimpatroon kan worden gemaakt met snijmachines of met de spuitgietmethode met polystyreenkralen . Het patroon kan een competitief patroon zijn (eenvoudig ontwerp) of een paar secties die vervolgens aan elkaar worden gelijmd om een replica van intent casting te vormen.
- Stap 2 :isolerende verfcoating om de duurzaamheid van het maloppervlak te verbeteren en te beschermen tegen erosie en breuk
- Stap 3: het schuimpatroon wordt in een kolf geplaatst die het ongebonden zand omgeeft en wordt verdicht.
- Stap 4: gieten van het gesmolten metaal, verdampen van het schuimpatroon en het vormen van de bepleistering
- Stap 5: het resterende zand reinigen en indien nodig verder bewerken.
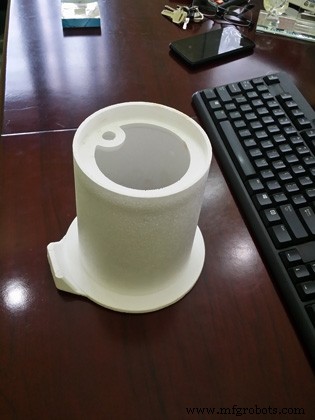
Verloren schuimgieteigenschappen
Voordeel
- Flexibel ontwerp
- Giet complexe vorm die ondenkbaar is in andere gietprocessen
- Hoge precisie en nauwe tolerantie
- Geen kerndefecten, geen schimmelverschuiving, uitstekende gladde oppervlakteafwerking
- Verkort de verwerkingstijd
- Verlaag de productie- en investeringskosten
Beperkingen
- Het is duurder dan andere methoden
- Het zal erg duur zijn voor het opzetten of kleine bestellingen
Verloren schuimgiettoepassingen
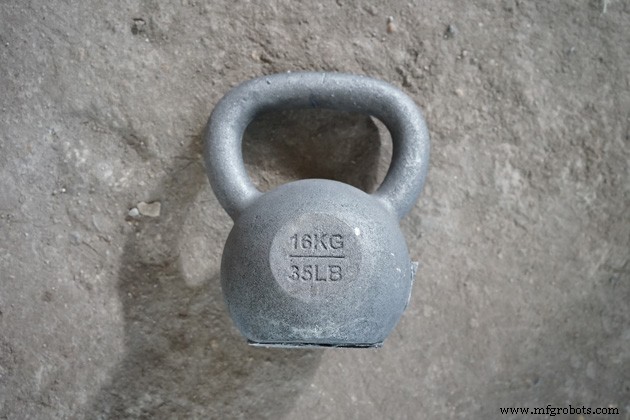
Het verloren schuimgietwerk beperkt zich niet tot enig ontwerp en type legering. Het is er vaak voor kiezen om complexe gietstukken te gieten die met andere methoden niet kunnen werken. Bijvoorbeeld auto-onderdelen, machine-elementen met hoge precisie, ingewikkelde kernproducten...
Lees hier meer over Lost foam casting.
4. Investeringscasting
Wat is investeringscasting?
Investeringsgieten of verloren was gieten is een geavanceerde gietmethode die wordt gebruikt om gecompliceerde en dunwandige vormen te gieten. Dit proces is vergelijkbaar met het verloren schuimgieten. In plaats van het schuimpatroon wordt het waspatroon voor eenmalig gebruik gevormd door de injectiemethode en vervolgens bedekt met meerdere lagen vuurvast materiaal.
Door het waspatroon te smelten, wordt een vormholte gecreëerd die klaar is om de metaalvloeistof in te gieten. Houd er rekening mee dat het patroon slechts één keer wordt gebruikt en dat voor elk gietstuk een patroon nodig is.
Deze methode heeft de kenmerken van het gieten van details met hoge nauwkeurigheid, dus het heeft vaak de voorkeur om producten voor de machinebouwindustrie te gieten, met name de productie van kleine details, hoge precisie, zonder bewerking of niet machinaal te bewerken.
Het proces voor het gieten van investeringen

- Stap 1 :Het masterpatroon en de mal maken
- Stap 2 :Injecteer de was in de mal om waspatronen te maken.
- Stap 3 :Patroondelen samenstellen
- Stap 4 :Schelpen maken
- Stap 5 :De-waxen door hitte
- Stap 6 :Het gesmolten metaal gieten
- Stap 7 :Verpletterend
- Stap 8 :Afsnijden
- Stap 9 :Afgewerkte gietdelen
Kenmerken voor het gieten van investeringen
Voordeel
Investment casting is een moderne casting-aanpak met veel voordelen.
- Vergeleken met zandgieten kan verloren-wasgieten betere complexe details, dunnere wanden en een hoge oppervlaktekwaliteit opleveren en machinale bewerkingen aanzienlijk verminderen. Veel afgewerkte gietstukken kunnen direct worden gebruikt.
- Het kan producten maken met een gewicht van enkele grammen tot een ton.
- Kan moeilijk te smelten legeringen gieten, zoals roestvrij staal, dun staal
- Het gietoppervlak is zeer nauwkeurig en glanzend
- Het gietstuk zal minder snel barsten of kromtrekken
Beperkingen
- Hoge arbeidsintensiteit
- Lange productiecyclus
- Matrijsproductiekosten zijn hoog
Aanvragen voor investeringsgieten
Complexe gietstukken, of in massaproductie om tandwielen te fabriceren; fietskoffers; motor schijf; reserveonderdelen in straalmachine … Gieten met gewicht van 0,02 ÷ 100kg; dikte tot 0,3 mm en gatdiameter tot 2 mm.
5. Spuitgieten
Wat is spuitgieten?
Spuitgieten is de methode voor het gieten van materiaal onder hoge druk en toegepast om non-ferro metalen en legeringen te gieten.
Het wordt gebruikt bij het gieten van onderdelen voor bulkorders omdat het voordeel van deze gietmethode de hoge productiviteit en het vereenvoudigde proces is dankzij de toepassing van een volledig geautomatiseerde lijn. Het verzamelde ruwbouw heeft een nauwe tolerantie, hoge precisie en een mooie glanzende oppervlakteafwerking.
Het spuitgietproces
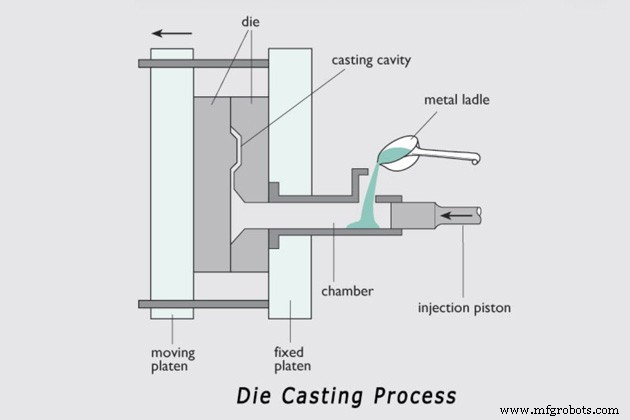
- Stap 1 :Het metaal smelten tot vloeistof
- Stap 2 :Het gesmolten metaal in de kamer gieten
- Stap 3 :Hogedruk piston injectiesysteem duwt de vloeistof in de mal
- Stap 4 :Wacht tot het gietstuk gestold is en verwijder dan de kern
- Stap 5 :De vergrendeling zal het object uitwerpen
- Stap 5 :verwijder het afvalmateriaal en ga verder met de volgend segment
Het hele gietproces van de spuitgietmethode vereist het gebruik van hogedrukzuigers en strakke persen om de duurzaamheid van het gietstuk te garanderen. Met het automatische lijnproces hangt de kwaliteit van het gietstuk af van vele factoren, zoals de samenstelling van het gesmolten metaal, het machinesysteem, de gietdruk, enz.
De spuitgieteigenschappen
Voordeel
- Strakke tolerantie en hoge precisie
- In staat om dunwandig gietwerk te gieten, zelfs 1 mm
- Hoogglans gietoppervlak
- Hoge consistentie in afmetingen en uniform ontwerp
- Verminder machinale bewerkingen
- Efficiëntie van hoog volumeproductie en geschikt voor bulkbestelling
- Volledig automatische regels die de arbeidskosten besparen
Beperkingen
- Dure gereedschapskosten
- Vereist een investering in machines
- Limiet in vormontwerp
Toepassingen voor spuitgieten
Spuitgieten wordt vaak gebruikt bij het gieten van kleine onderdelen, bulkorders zoals zuigers, krukassen, versnellingsbakken, enz. Het kan het gietstuk produceren dat vaak tot 5 kg weegt, maar er is ook een gietkoffer voor onderdelen met een gewicht tot 50 kg, maar de prijs is erg hoog.
De legeringen die bij het spuitgieten worden gebruikt, moeten uniform zijn, goede verdunningseigenschappen hebben wanneer ze gesmolten zijn en de samenstelling stabiel is om niet aan de mal te hechten, en een plastische sterkte hebben bij verhitting bij hoge temperaturen. Koper, aluminium en roestvrij staal hebben vaak de voorkeur in deze giettechnologie.
Bij het spuitgieten worden aluminiumlegeringen het meest gebruikt in vergelijking met alle andere legeringen. Alleen al in de VS is het spuitgieten van aluminium tot 2,5 miljard dollar per jaar waard. Vooral het gieten van aluminium is goed voor twee keer zoveel als alle andere methoden samen.
6. Permanente gietvorm
Wat is permanent gieten?
Permanent gieten, ook bekend als gieten van metalen gietvormen, is een gietproces waarbij een mal is gemaakt van metaal zoals spuitgieten. Het wordt gebruikt om een grote hoeveelheid gietstukken te produceren met behulp van een enkele herbruikbare mal. De mal kan vele malen worden hergebruikt vandaar de zogenaamde permanente vormmethode.
Permanent vormgieten is geschikt voor grotere gietstukken dan spuitgieten, ongeveer 10 kg, het kan natuurlijk hoger zijn, 20 kg zelfs 50 kg, en de kosten zullen hoger zijn.
Het permanente gietproces
Het permanente vormgietproces omvat eenvoudig deze stappen:
- Stap 1 :gesmolten metaal in de mal gieten
- Stap 2 :laat afkoelen en stolt
- Stap 3 :de mal openen en het gietstuk verzamelen;
- Stap 4 :ga dan verder met bovenstaande processen om zoveel castings te maken als nodig is.
Met name de mal in dit proces is gemaakt van een metallisch materiaal op hoge temperatuur, zoals gietijzer, om de continue verwarming en koeling te kunnen verdragen terwijl het een groot volume inneemt.
Permanente vormgieteigenschappen
Voordeel
- Hoog nauwkeurig gietresultaat met nauwe tolerantie
- Mooie oppervlakteafwerking met minder gietfouten dan zandgieten
- Het gietstuk is een hoge sterkte, taaiheid en taaiheid
- De duurzaamheid van de mal is hoog.
- Door tijd te besparen bij het maken van matrijzen, verlaagt een hoge productiviteit de productiekosten.
Beperkingen
- Het is moeilijk om objecten te gieten die te complex zijn, met grote muren en gewicht
- Matrijsproductiekosten zijn hoog.
- Er is een mechanisme nodig om het gietstuk uit de mal te duwen, zodat ze soms een deuk in het gietstuk vormen.
Permanente toepassingen voor gietvormen
Deze permanente gietvorm wordt het meest gebruikt voor het gieten van aluminium, magnesium, koperlegeringen en grijs gietijzer vanwege het lage smeltpunt. Geschikt voor massaproductie met eenvoudige en kleine of middelgrote gietstukken zoals zuigers, tandwielblokken, keukengerei, details in werktuigmachines, vliegtuigwielen, pomponderdelen, etc. die niet zwaarder zijn dan 25kg. Voor objecten met een complexe interne vorm wordt het gebruik van een zandkern aanbevolen.
Samenvatting
De bovenstaande inhoud heeft de 6 verschillende soorten castingprocessen . opgesomd en geanalyseerd vaak gebruikt in de metaalgieterijen fabrikanten. Over het algemeen behoudt elk van deze giettechnieken zowel sterke punten als beperkingen. Afhankelijk van de gietvereisten en de projectvraag, zullen de gieterijen het gietproces overwegen dat past bij de toepassing.
Als een van de toonaangevende gietbedrijven en groothandel op de wereldmarkt, is VIC de zandgieterij met drie hoofdgiettechnieken:groenzandgieten, furaanharsgieten en verloren schuimgieten. Met deze drie verschillende soorten gietstukken zijn we in staat om alle gietstukken te vervaardigen, van het kleine, middelgrote, grote formaat tot een eenvoudig, ingewikkeld vormontwerp. Neem contact op met VIC-gieterij voor een OEM-project voor gietstukken via e-mail [email protected]
Productieproces
- Zandgieten:proces en kenmerken | Industrieën | Metallurgie
- 10 verschillende soorten patronen bij gieten
- Wat is metaalgieten? - Definitie, typen en proces
- Soorten zandgietapparatuur
- 4 veelvoorkomende soorten metaalgietprocessen
- Zandgietproces begrijpen
- Verschillende soorten elektrisch booglasproces
- Verschillende soorten apparatuur die worden gebruikt in het booglasproces
- Verschillende soorten hamers die op verschillende gebieden worden gebruikt:
- Verschillende soorten plaatbewerkingsprocessen
- Verschillende soorten spanen bij het snijden van metaal