Koepeloven - Onderdelen, werkingsprincipe, toepassingen
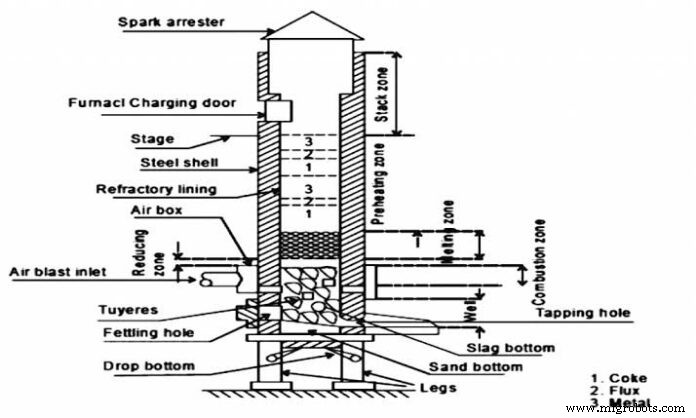
In dit artikel zullen we het hebben over Cupola Furnace, Delen van Cupola, Cupola oven diagram, Zones in Cupola, Cupola operatie.
De primaire doelstelling in de koepel is om ijzer van verlangen te produceren samenstelling, temperatuur en eigenschappen tegen het vereiste tarief op de meest economische manier. Bovendien heeft deze oven veel duidelijke voordelen ten opzichte van de andere typen, bijvoorbeeld eenvoud van bediening , continuïteit van de productie en verhoogde output gekoppeld aan een hoge mate van efficiëntie.
Verschillende soorten smeltovens worden gebruikt in verschillende gieterijen, afhankelijk van de hoeveelheid metaal die tegelijk moet worden gesmolten en de aard van het werk dat in de winkel wordt uitgevoerd. Alleen koepeloven gebruikt in gieterijen voor het smelten van een raffinage-ruwijzer samen met schroot wordt hieronder beschreven.
Delen van Koepeloven
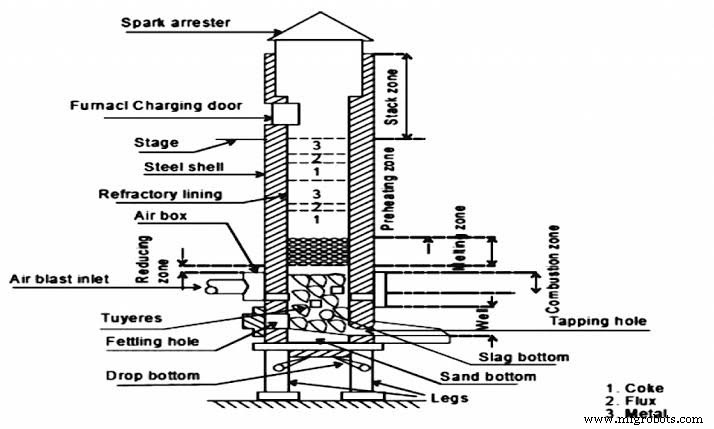
De koepeloven bestaat uit een verticale, cilindrische staalplaat, 6 tot 12 mm dik, en aan de binnenkant bekleed met zuur vuurvaste stenen of zuur. aanstampen van klei. De vuurvaste stenen of de gebruikte aandrukklei bestaan uitsiliciumoxide zuur (SiO2) en aluminiumoxide (Al2O3). De voering is over het algemeen dikker in het lagere gebied waar de aangetroffen temperaturen hoger zijn dan in het hogere gebied.
Het casco wordt ofwel op een metselwerkfundering ofwel op stalen kolommen gemonteerd. In een stalen kolomopstelling, gebruikt op de meeste moderne koepels, is de bodem van de schaal voorzien van drop-bottom deuren waardoor puin, bestaande uit cokes, slakken, enz. aan het einde van een smelt kan worden afgevoerd. In drop-bottom koepels is de werkende bodem opgebouwd met vormzand dat de drop-deuren bedekt.
Deze bodem loopt af naar het metalen tapgat dat zich op het laagste punt aan de voorkant van de koepel bevindt. Tegenovergestelde dit kraangat , en iets erboven, is nog een gat, het slakkengat , waardoor de slak kan worden verwijderd.
Een constant luchtvolume voor verbranding wordt verkregen door een gemotoriseerde ventilator. De lucht wordt van de blazer door een pijp genaamd windpijp (luchtinlaatinlaat) geleid, eerst naar een cirkelvormige mantel rond de schaal genaamd windbox en dan in de oven door een aantal openingen genaamd tuyeres die zijn aangebracht op een hoogte tussen 450 en 500 mm boven de werkbodem of het bed van de koepel.
Deze tuyeres zijn over het algemeen 4, 6 of 8 in aantal, afhankelijk van de grootte van de koepel en ze kunnen in een of meer rijen worden geplaatst. De totale oppervlakte van de blaaspijpen moet ongeveer een vijfde tot een zesde zijn van de dwarsdoorsnede van de koepel binnen de voering op het niveau van de blaaspijp. Meestal hebben blaaspijpen een afmeting van 50×150 mm of 100×300 mm. Er worden soms hulpblaaspijpen verschaft om het smeltrendement te verhogen.
In de straalpijp is een klep aangebracht om de luchttoevoer te regelen. Afhankelijk van de grootte van de koepeloven, het type gesmolten ijzer en de compactheid van de lading kan de luchtdruk variëren van 250 mm tot 400 mm water voor kleine en middelgrote ovens en van 400 mm tot 850 mm voor grote oven.
Soms wordt een volumemeter geïnstalleerd om het volume van de passerende lucht te kennen. De hoeveelheid lucht die nodig is om een ton ijzer te smelten hangt af van de kwaliteit van de cokes en de cokes-ijzerverhouding. Lange praktijk leert dat er ongeveer 800 tot 900 kubieke meter lucht nodig is om één ton ijzer in een koepeloven te smelten, aangenomen dat een verhouding van 10 tot 1 ijzer tot cokes wordt gebruikt. Voor een lagere verhouding zijn grotere luchtvolumes nodig.
Er is een vuldeur voorzien waardoor metaal, cokes en flux in de oven worden gevoerd, en deze bevindt zich 3 tot 6 m boven de blaaspijpen, afhankelijk van de grootte van de koepel. Een groot platform of podium omringt de koepel gewoonlijk op het niveau van ongeveer 300 mm onder de onderkant van de laaddeur.
De schil wordt meestal 4,5 tot 6 m doorgetrokken, boven de vuldeur om een schoorsteen te vormen. Aan de bovenkant van de oven voorkomt een conische dop, de vonkstop, dat de vonk naar buiten komt. De vonk die wordt gestopt, koelt de vonken af en laat alleen rook uit de opening ontsnappen. Soms kan een koepeloven worden uitgerust met een collector, fitter en neerslag om de luchtvervuiling tot een minimum te beperken.
Zones in Koepeloven
Op basis van verbrandingsreacties kan de gehele schacht van de koepel worden verdeeld zoals onder:
Smeltkroes zone:- Het bevindt zich tussen de bovenkant van het zandbed en de onderkant van de blaaspijpen. Hier wordt het gesmolten ijzer verzameld. Dit wordt ook wel de put . genoemd of haard .
Verbrandings- of oxidatiezone :- Het bevindt zich normaal 150 tot 300 mm bovenaan van de tuyeres. Alle zuurstof in de luchtstoot wordt hier verbruikt door de daadwerkelijke verbranding die in deze zone plaatsvindt. Zo komt er veel warmte vrij en wordt deze van hieruit aan andere zones geleverd.
Er ontstaat ook warmte door de oxidatie van silicium en mangaan. Door deze hoge temperatuur, met een temperatuur van 1550° tot 1850°C, komen gesmolten druppels gietijzer in de haard terecht. De chemische reacties die in deze zone plaatsvinden zijn:
C + O2 —–>CO2 + warmte
Si + O2 —–>SiO2 + warmte
2 Mn + O2 —–> 2 MnO2 + Warmte
Reductiezone:- Het strekt zich uit van de bovenkant van de verbrandingszone tot de bovenkant van het cokesbed. In deze zone vindt de reductie van CO2 tot CO plaats en daalt de temperatuur tot ongeveer 1200°C aan het cokesbed. Door de reducerende atmosfeer wordt de lading beschermd tegen eventuele oxiderende invloeden. De reactie die in deze zone plaatsvindt is:
CO2 + C (cokes) —-> 2 CO-Warmte
Smeltzone:- Het begint vanaf de eerste laag metaallading boven het cokesbed en reikt tot een hoogte van 900 mm. In deze zone wordt de hoogste temperatuur ontwikkeld voor volledige verbranding van de cokes en hier wordt dus ijzer gesmolten. De temperatuur in deze zone ligt rond de 1600°C. In deze zone vindt ook een aanzienlijke koolstofopname door het gesmolten metaal plaats volgens de volgende reacties:
3 Fe + 2 CO—–>Fe3C + CO2
Voorverwarmzone of oplaadzone :- Het begint boven de smeltzone en loopt door tot aan de onderkant van de laaddeur. De voorverwarmzone bevat koepellading als afwisselende lagen van cokes, flux en metaal en ze worden daar voorverwarmd op een temperatuur van ongeveer 1100°C voordat ze naar de smeltzone komen.
Stapelzone :- De stapelzone strekt zich uit van boven de voorverwarmingszone tot de bovenkant van de koepel. Het voert de gassen die in de oven worden gegenereerd naar de atmosfeer.
Capaciteit van koepeloven
De output van een koepeloven wordt gedefinieerd als de tonnen gesmolten metaal die per uur van de warmte worden verkregen. Koepelcapaciteiten (afmetingen) variëren van 1 tot 15 ton (of zelfs meer) gesmolten ijzer per uur. De grootte hangt niet alleen af van de dwarsdoorsnede van de koepel, maar ook van de intensiteit van het cokesverbruik.
Maar de intensiteit van cokeconsumptie wordt bedoeld de tonnen cokes verbrand per m² van de dwarsdoorsnede van de koepel in tijdseenheid. Er is waargenomen dat 14 cm koepelvormige oppervlakte ongeveer 1 kg cokes per uur verbrandt. De diameter van de koepel varieert van 1 tot 2 m met een hoogte van 3 tot 5 keer de diameter.
Koepeloven werkt
De verschillende stappen die betrokken zijn bij de werking van de koepeloven zijn:
De eerste bewerking bij het voorbereiden van een koepeloven is het opruimen van de slak en afval op de voering en rond de blaaspijpen van de vorige run. Eventuele slechte plekken of gebroken stenen worden gerepareerd met een leemmengsel van vuurklei en kwartszand of ganister. De voorbereiding van de zandbodem in de koepel wordt gestart zodra het patchen van de bekleding is voltooid.
De onderste deuren worden omhoog gebracht en in deze positie gehouden door metalen steunen. Het bodemzand wordt door de laaddeur ingebracht en wordt goed rond de voering en over de kruising van de bodemdeuren geramd. Deze zandlaag wordt opgebouwd tot een hoogte van 100 tot 200 mm boven de gietijzeren deur.
Het oppervlak van de zandbodem loopt vanuit alle richtingen schuin af richting het tapgat, zodat het gesmolten metaal op elk moment volledig uit de koepel kan worden afgevoerd. Een opening met een diameter van ongeveer 35 mm is aangebracht voor het verwijderen van de slak, en een kraangat is gevormd rond een houten patroon met een diameter van ongeveer 20 mm. De koepel moet grondig worden gedroogd voor het bakken.
2. De koepel in brand steken
Bij het stoken van een koepeloven wordt op de zandbodem een vuur van aanmaakhout ontstoken. Dit moet 2,5 tot 3 uur voordat het gesmolten metaal nodig is, gebeuren. Bovenop het aangestoken hout is een bed van cokes gebouwd. Wanneer het hout goed brandt, wordt de cokes van bovenaf in meerdere porties in de put gedumpt om ervoor te zorgen dat de cokes ook begint te branden.
De cokes wordt toegevoegd tot een niveau iets boven de blaaspijpen en de luchtstoot wordt aangezet met een lagere blaassnelheid dan normaal om de cokes te ontsteken. Zodra rode vlekken over de bovenkant van het brandstofbed beginnen te verschijnen, wordt extra cokes in de koepel gebracht om een hoogte van 700 tot 800 mm boven de bovenste rij tuyeres te bereiken.
Het cokesbed moet goed heet zijn voordat het tot zijn uiteindelijke hoogte wordt afgewerkt. De hoogte van het cokesbed wordt bepaald met behulp van een meetlat die is voorbereid om de afstand van de drempel van de vuldeur tot de bovenkant van het cokesbed aan te geven. De laag cokes die op de zandbodem rust voordat de hitte begint, wordt bedlading genoemd. De hoeveelheid cokes in het bed is afhankelijk van de druk van de aan de koepel toegevoerde lucht.
De hoogte van de bedlading of het cokesbed is van groot belang voor de werking van de koepel; het beïnvloedt de temperatuur, smeltsnelheid en chemische samenstelling. Als andere zaken gelijk zijn, zal een laag bed koeler metaal opleveren dan een die hoog is.
3. De koepel opladen
Zodra het cokesbed tot de juiste hoogte is opgebouwd en overal gelijkmatig is ontstoken, worden afwisselende lagen ruwijzer, cokes en flux (kalksteen) vanaf de vuldeur geladen totdat de koepel vol is. Samen met het ruwijzer wordt ook geschikt schroot toegevoegd om de chemische samenstelling van het geproduceerde ijzer te regelen. Het aandeel van dit schroot is gewoonlijk 25 tot 50 procent van het totale gewicht van het gegoten metaal.
Wanneer naast ruwijzer veel staalschroot wordt gebruikt, wordt een kleine hoeveelheid, zeg 2 tot 4% ferromangaan, als deoxidator gebruikt. Het gewicht van de metaallading moet 10 tot 15 procent van de uuropbrengst van de koepel bedragen. Het doel van het toevoegen van vloeimiddel is om onzuiverheden in het ijzer te verwijderen en het ijzer te beschermen tegen oxidatie, het smeltpunt van de slak te verlagen en de vloeibaarheid ervan te vergroten voor gemakkelijke verwijdering. Naast kalksteen worden soms ook vloeispaat en natriumcarbonaat gebruikt als vloeimateriaal.
De benodigde hoeveelheid kalksteen kan 30 tot 40 kg per ton gesmolten ijzer bedragen of 25 gewichtspercenten van de geladen cokes. De verhouding tussen het gesmolten metaal en de geladen cokes hangt van een groot aantal factoren af. Het is dus niet mogelijk om definitieve aanbevelingen te doen voor deze verhouding die kan worden bereikt op verschillende soorten werk. Tabel 11.11 wordt alleen als richtlijn gegeven en toont goede gemiddelde praktijken in de branche. Meestal wordt het 10:1 gehouden. Dit betekent dat er 1 ton cokes nodig is om 10 ton ijzer te smelten.
4. Inweken van ijzer
Nadat de koepel volledig is opgeladen tot aan de laaddeur, moet de lading ongeveer 45 minuten in de hitte weken. De lading wordt langzaam verwarmd omdat de luchtstroom gedurende deze tijd op een lagere blaassnelheid wordt gehouden dan normaal (praktisch gesloten gehouden). Hierdoor raakt het strijkijzer doorweekt.
5. Luchtstoot
Aan het einde van de inweekperiode wordt de volledige straal ingeschakeld. Alvorens de ontploffing in te schakelen, worden de blaasopeningen en het tapgat gesloten gehouden. Nadat de explosie een paar minuten heeft geduurd, zeg ongeveer 10 minuten, begint gesmolten metaal zich op te hopen in de haard. Wanneer het metaal in de koepel begint te smelten, moet de laadsnelheid gelijk zijn aan de smeltsnelheid, zodat de oven tijdens de hele hitte vol blijft. Aan het einde van het smelten wordt het opladen gestopt, maar de explosie wordt voortgezet totdat al het metaal is gesmolten.
6. Tikken en slakken
De eerste keer tikken kan 40 tot 50 minuten nadat de volledige luchtstroom is ingeschakeld. Gedurende deze periode wordt er voldoende metaal opgevangen in de haard boven het zandbed. Wanneer slak zich ophoopt in de put, wordt het slakgat geopend en wordt de slak afgevoerd, bij voorkeur in een draaistel voor gemakkelijke verwijdering. Gesmolten metaal wordt opgevangen in pollepels en naar de vormen gebracht om te worden gegoten. Dezelfde procedure wordt herhaald totdat al het metaal is gesmolten en de bewerking voorbij is.
7. De koepel sluiten
Wanneer de operatie voorbij is, wordt de explosie uitgeschakeld en wordt de steun onder de onderste deur neergeslagen, zodat de bodemplaten openzwaaien. Hierdoor kunnen de koepelresten op de grond of in een emmer vallen. Ze worden vervolgens geblust en van onder de koepel verwijderd.
Over het algemeen worden koepels continu gebruikt, evenals hoogovens, maar worden ze alleen gebruikt gedurende de perioden die nodig zijn. Bij veel gieterijen is de smeltperiode niet langer dan 4 uur, maar koepels kunnen 10 uur of langer continu worden gebruikt.
Efficiëntie van Koepeloven
Het thermische of smeltrendement van een koepel in procenten wordt uitgedrukt als:
(Warmte gebruikt bij voorverwarmen, smelten en oververhitten) / (Potentiële warmte in cokes + warmte van oxidatie van Fe, Si, Mn + warmte in de luchtstoot) x 100
Het rendement van een koepeloven varieert van 30 tot 50 procent, afhankelijk van:
1. Cokesgehalte of cokesverhouding uitgedrukt als het omgekeerde van de metaal-brandstofverhouding in procenten,
2. Ontploffingssnelheid, en
3. Gemiddelde cola-grootte.
Luchtvereisten voor koepeloven
Voor volledige verbranding van de brandstof in de koepeloven is ongeveer 8,4 kubieke meter lucht nodig per kg cokes bij normale atmosferische druk en temperatuur. Als de verhouding tussen meel en cokes 10:1 is, wat als een bevredigend cijfer wordt beschouwd, zal de benodigde cokes per ton ijzer 1000/10 kg zijn, d.w.z. 100 kg. Het benodigde luchtvolume per ton gesmolten is dus>
Om lekkage enz. mogelijk te maken, is de toegevoerde lucht in het algemeen iets te veel, d.w.z. ongeveer 900 kubieke meter per ton ijzer.
Afmetingen van koepeloven
De hoofdafmetingen van een koepel worden gekozen op basis van empirische gegevens. Het dwarsdoorsnede-oppervlak A. van een koepel hangt dus af van de ontworpen uuropbrengst en wordt bepaald uit de formule
Waarbij d =koepeldiameter in de vrije ruimte, m, Q =ontworpen koepelopbrengst, ton per uur, Q2 =specifieke opbrengst per vierkante meter doorsnede, ton per uur. In de regel Q1 =6 tot 8 ton per uur.
De bruikbare hoogte van een koepel (afstand van de as van de hoofdblaaspijpen tot de onderkant van het laadgat) hangt af van de diameter en is ontworpen volgens de verhouding H:d =van 3 tot 5.
De hoogte van de koepeloven heeft rechtstreeks invloed op de smeltsnelheid , brandstofverbruik en de temperatuur en kwaliteit van gesmolten metaal . Als het te hoog is, kan de cokes worden geplet als de lading daalt; als het te laag is, wordt het metaal niet voldoende verwarmd, de trek wordt verminderd en de koepelopbrengst wordt verminderd.
De binnendiameter van de koepel bepaalt de hoeveelheid cola die wordt verbruikt en de hoeveelheid ijzer per tijdseenheid gesmolten. Gebleken is dat 14 cm? van de oppervlakte van het koepelplan verbrandt ongeveer 1 kg cokes per uur. Zo zal een koepel met een capaciteit van 3 ton per uur (3×100) of 300 kg cokes per uur nodig hebben, uitgaande van een metaal-brandstofverhouding van 10:1. De oppervlakte van de koepel zal dus gelijk zijn aan (14×300) of 4200 cm². De binnendiameter wordt dan:
Vierkante wortels van (4200×4 )/ π
=73 cm (ongeveer)
Koopaovenkosten
Als producten van uniforme kwaliteit gewenst zijn, moet er goed nagedacht worden over de koepelheffing. Meestal zijn er verschillende soorten ruwijzer en schroot beschikbaar voor de gieter. Om een gewenste samenstelling van het gegoten metaal te bereiken, moeten deze kwaliteiten worden aangepast en gecontroleerd. Aangezien de verschillende elementen in metaal chemische veranderingen ondergaan tijdens het opnieuw smelten, moet rekening worden gehouden met hun verlies of winst bij het aanvullen van de lading. Het verlies of de winst van verschillende elementen is als volgt.
5. Fosfor: Er is praktisch geen verlies of winst in het fosforgehalte.
Dit ging allemaal over de koepeloven, zijn zones, operaties en onderdelen. Ik hoop dat je het artikel leuk vond. Geef uw feedback in de opmerkingen hieronder.
Industriële technologie
- Gasklepstandsensor – Werkingsprincipe en toepassingen
- RVG-sensor – werkingsprincipe en zijn toepassingen
- Pulssensor:werkingsprincipe en zijn toepassingen
- Werkingsprincipe van de RTD-sensor en zijn toepassingen
- Wat is 3D-printen? Werkingsprincipe | Soorten | Toepassingen
- Koepeloven:principe, constructie, werking, voordelen, nadelen en toepassing:
- Schuurstraalbewerking - onderdelen, werkingsprincipe, toepassing
- Waterstraalbewerking - Werkingsprincipe, toepassingen, voordelen
- Ultrasoon bewerkingsproces - werkingsprincipe van onderdelen, voordelen:
- Hc06-gegevensblad: Inleiding tot pinout, functies, toepassingen en werkingsprincipe
- Werkingsprincipe van het spuitgietproces en zijn toepassingen: