Nieuwe horizonten in het lassen van thermoplastische composieten
Deze blog hoort bij de sep 2018-rubriek “Lassen van thermoplastische composieten”. Het is een compilatie van afbeeldingen en details die niet in het gedrukte artikel pasten, inclusief een tijdlijn van ontwikkelingen in inductielassen en details over kwalificatie voor toekomstige commerciële vliegtuigen, evenals korte secties over reparatie, ontwikkelingen voor auto's en thermoset tot thermoplast (TS -TP) lassen.
Om nog maar eens te herhalen waarom gelaste assemblages van thermoplastisch composiet (TPC) van belang zijn voor zowel lucht- en ruimtevaartconstructies als lichtgewicht constructies voor auto's, vergelijkt u de twee onderstaande afbeeldingen van het Airbus A320-achterdrukschot. De bovenste afbeelding is de huidige versie gemaakt van aluminium. Let op het grote aantal klinknagels. Vergelijk dat nu eens met de gelaste TPC-demonstrator die Premium Aerotec presenteerde op de ILA-vliegshow van 2018 in Berlijn. Let op de afwezigheid van klinknagels. Voor composieten elimineert dit niet alleen het gewicht, de tijd en de kosten van bevestigingsmiddelen, maar ook de tijd en kosten van het plaatsen en boren van gaten, plus het reinigen en inspecteren van die gaten. Het betekent ook veel lichtere structuren zonder de laminaatpad-ups die nodig zijn om sneden door dragende vezels te compenseren.
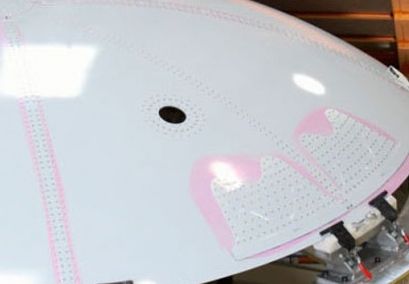
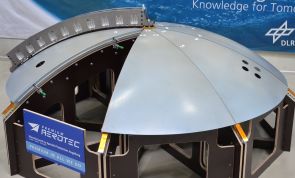
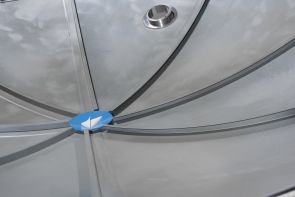
Een gelast thermoplastisch composiet A320 achterdrukschot (onder) biedt een oplossing zonder klinknagels in vergelijking met de huidige aluminium constructie (boven).
BRON:RUAG (boven) en Premium Aerotec (onder), DLR-centrum voor lichtgewicht productietechnologie (Augsburg, Duitsland)
"Een ander voordeel is dat inspectie voor gelaste constructies eenvoudiger is dan voor gelijmde assemblages", zegt Dr. Hans Luinge, directeur thermoplastische composieten R&D en productontwikkeling bij de TenCate-Toray Group, leverancier van TPC-materialen. “C-scan werkt goed en laat zien of er geen porositeit in het laminaat zit, wat betekent dat de las goed is. Voor verlijmde structuren kun je een kissing bond of moeilijk op te sporen verontreinigingen hebben.” Hoewel TenCate-Toray zelf geen lastechnologie ontwikkelt, ondersteunt het wel diverse industrie- en klantprojecten. "We optimaliseren onze materialen naar behoefte", zegt Luinge, "en proberen de ontwikkelingen in de goede richting te sturen op basis van onze langdurige deelname aan inspanningen zoals TAPAS en met partners zoals KVE Composites, de TPRC, tier-leveranciers en OEM's."
Ontwikkelingen inductielassen
KVE Composites ontwikkelt sinds 2001 inductielassen voor TPC's. In de eerste toepassingen werden koolstofvezelweefsel/PPS-laminaten gebruikt, waaronder liften en roer voor de zakenjets Gulfstream G650 en Dassault Falcon 5X.
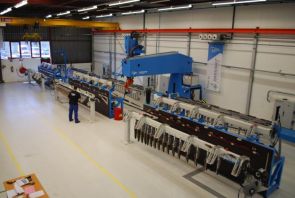
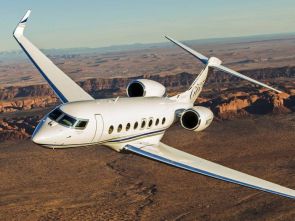
KVE Composites geholpen om GKN Fokker's productie van inductiegelaste liften en roer (links) voor de Gulfstream G650 (rechts) en Dassault Falcon 5X-vliegtuigen te ontwikkelen.
BRON:KVE Composites, GKN Fokker (links) en Gulfstream (rechts).
Andere inductiegelaste TPC-toepassingen zijn onder meer toegangsdeuren tot brandstoftanks geproduceerd door AVIACOMP S.A.S. (Launaguet, Frankrijk en nu onderdeel van Sogeclair Group) voor de Airbus A220-vleugel (voorheen Bombardier CSeries). (Aviacomp produceerde ook de stringers voor STELIA's gelaste TPC-romp, getoond op de Paris Air Show van 2017.)
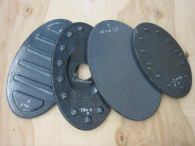
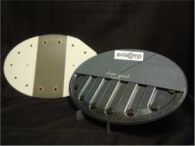
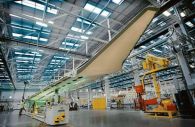
Aviacomp gebruikt inductie lastechnologie ontwikkeld door KVE Composites bij de productie van TPC-toegangsdeuren voor brandstoftanks voor het Airbus A220 narrowbody-vliegtuig.
BRON:Aviacomp, onderdeel van Sogeclair Group.
Deze algemene categorie toegangsdeuren is een kans voor TPC-lassen om kosten te besparen, zoals blijkt uit een ontwerp- en fabricagestudie uitgevoerd door KVE Composites. Zelfs kleinere vliegtuigen kunnen tot 60 van deze toegangspanelen hebben, allemaal verschillend van vorm en meestal gemaakt met een composiet sandwichconstructie met machinaal bewerkte honingraatkern. "Als je gelaste thermoplastische assemblage gebruikt, kun je alle verschillende toegangspanelen voor een vliegtuig maken met slechts $ 100.000 aan gereedschapskosten, wat een enorme besparing is", zegt KVE Composites-directeur Harm van Engelen. "We hoeven de kern niet te bewerken, we gebruiken gewoon 'lego-achtige' componenten - vlakke platen en gestempelde verstijvers - die aan elkaar zijn gelast om de verschillende vormen te vormen. Bovendien lijkt onze tooling meer op een lasmal, dus relatief lage kosten in vergelijking met wat ze tegenwoordig gebruiken. Alle toegangspanelen voor een vliegtuig zouden in één enkele lascel gemaakt kunnen worden.”
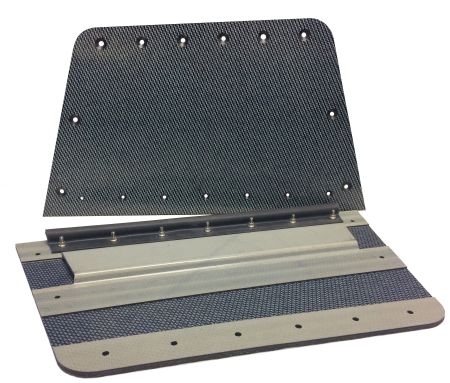
Gelaste thermoplastische assemblage voor overhangpanelen van vliegtuigen kan worden gemaakt met behulp van geautomatiseerde vorm- en lascellen en bespaar $ 100.000 aan gereedschapskosten. BRON:KVE Composites.
KVE Composites zet zijn ontwikkeling van TPC-lastechnologieën voort, zoals geïllustreerd in de onderstaande tijdlijnen. De hieronder getoonde productiecel voor 2019 is de Falko ATL-machine (automatische tape-legmachine), geproduceerd door Boikon (Leek, Nederland) met behulp van een ultrasone laseindeffector ontwikkeld door GKN Fokker. "Deze robotcel maakt een efficiënter proces en besturingssysteem mogelijk voor het volgende niveau van de productie van TPC-onderdelen in volume in vergelijking met de pick-and-place-methoden die tegenwoordig worden gebruikt", legt KVE Composites hoofd van R&D Maarten Labordus uit. “Je kunt bijvoorbeeld de huid- en riblaminaten volledig automatisch opleggen voor een regionaal jetregeloppervlak (dat ongeveer 60 mm x 3 m is), een consolidatie- en vormingsstap buiten de autoclaaf toepassen en vervolgens de assemblage voltooien in een aangrenzende lascel.” De Falko ATL-machine demonstreert ook een gesloten lusregeling die al door GKN Fokker is ontwikkeld voor ultrasoon lassen. "De machine kan het energieniveau naar behoefte regelen per materiaaltype, dikte en vorm, maar daarna is volledige smeltconsolidatie van de platte voorvorm vereist tijdens het gieten van het voltooide TPC-onderdeel", legt Arnt Offringa uit, hoofd van Aerostructures R&T voor GKN Fokker.
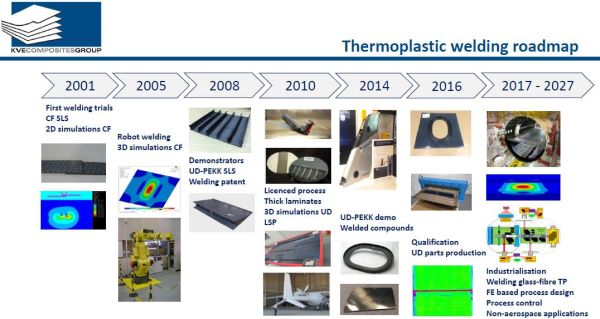
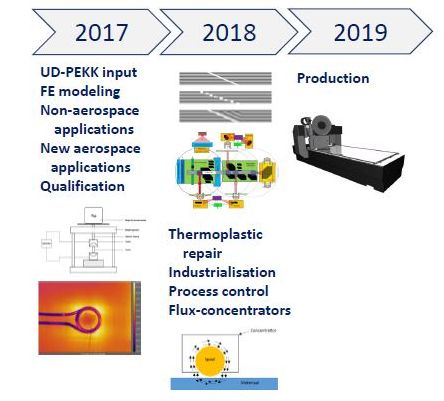
Kwalificatie
Hierboven weergegeven als een belangrijk ontwikkelingsinitiatief in 2017, kwalificatie van inductielasprocessen voor TPC-luchtstructuren is een voortdurende prioriteit. Volgens het abstract voor de aanstaande presentatie van KVE Composites op de 4 de Int. Conf. en tentoonstelling over thermoplastische composieten (ITHEC, 30-31 oktober 2018 in Bremen, Duitsland), heeft het lassen van thermoplastisch composiet (TPC) de afgelopen jaren een verschuiving gezien van polymeren zoals PPS en PEI naar duurdere polymeren zoals PEEK , PEKK en nu Low Melt PAEK (LM PAEK, lees meer in mijn blog "PEEK vs. PEKK vs. PAEK ..."), evenals in de richting van automatisch geplaatste UD-tapes en dikkere laminaten voor zwaarder belaste constructies. Als reactie daarop heeft KVE Composites getracht de gereedschappen en apparatuur, evenals op FEA gebaseerde simulatiemodellen te verbeteren en te standaardiseren.
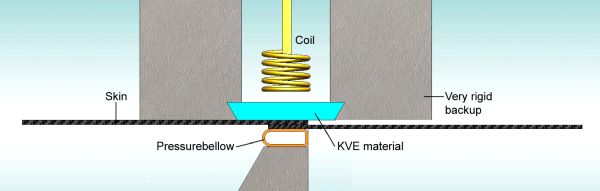
Gestandaardiseerde opzet voor kwalificatie van inductielassen met nieuwe materialen.
BRON:KVE Composites
Om te helpen bij de rijping en kwalificatie van het inductielasproces met deze nieuwe composietlaminaten, heeft KVE Composites een gestandaardiseerde opstelling ontwikkeld voor het lassen van een enkele lap shear en ook van L- en T-pull-off testcoupons. Deze opstelling omvat:
- Een stijf frame om de belasting op te vangen van het uitoefenen van druk op het laminaat tijdens het lassen.
- Een lager gereedschapsblok dat onder het frame kan worden geplaatst om reproduceerbaar lassen van standaardpanelen mogelijk te maken.
- Een opblaasbare doorn (drukbalg in bovenstaande afbeelding) in het onderste gereedschapsblok die in slechts één richting kan uitzetten om het laminaat dat wordt gelast tegen een speciaal koellichaam ("KVE-materiaal" in afbeelding hierboven) samen te drukken om de warmte bij het lassen op te sluiten interface.
Door de onderste gereedschapsblokken te verwisselen, kan een verscheidenheid aan standaardcoupons worden gelast en vervolgens ultrasoon worden geïnspecteerd, waarna kleinere coupons kunnen worden gesneden en mechanisch getest. Deze gestandaardiseerde opstelling is al geïnstalleerd door:
- Thermoplastisch Onderzoekscentrum (TPRC, Enschede, Nederland)
- McNair Center aan de Universiteit van South Carolina (Columbus, SC, VS)
- Nederlands Lucht- en Ruimtevaartcentrum (NLR, Marknesse, Nederland).
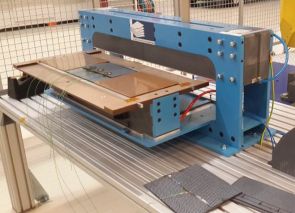

Gestandaardiseerd inductielassen opstelling bij KVE (links) en gelast UD-koolstofvezel/PEKK-monster met thermokoppels om de temperatuur bij laslijn (rechts) te registreren.
BRON:KVE Composites.
Reparatie
Een ander belangrijk ontwikkelingsgebied is het repareren van TPC-luchtstructuren. "We richten ons eerst op CF-weefsel/PPS-structuren die gekwalificeerd en vliegend zijn", zegt Labordus. "Het proces is in principe hetzelfde als dat voor reparaties van thermohardende composieten:verwijder het beschadigde materiaal, bereid dat gebied voor met een taps toelopende sjaal en bind het vervolgens vast in een prepreg-reparatiepleister. Labordus zegt dat een van de problemen is dat thermoplastische prepreg bij kamertemperatuur boardy is en niet plakt, "dus het is moeilijk om geometrie te matchen." Hij gelooft echter dat de robotreparatiesystemen die worden ontwikkeld door Airbus, Lufthansa en anderen een oplossing bieden.
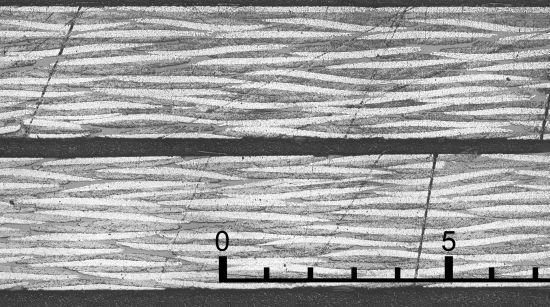
Als onderdeel van de voortdurende ontwikkeling van gelaste structurele thermoplastische composietreparaties, heeft KVE Composites inductiegelaste 2D lineaire conische verbindingen bereikt in CF-stof / PPS-laminaten met uniforme dikte en 90% van de oorspronkelijke materiaaleigenschappen.
BRON:KVE Composites.
Dergelijke systemen maken gebruik van metrologie om robotisch machinaal bewerkte taps toelopende sjaals nauwkeurig te meten en vervolgens een vooraf gemaakte patch te verbinden die robotisch taps machinaal is bewerkt om te matchen. "We willen inductielassen gebruiken om een thermoplastische patch aan de oorspronkelijke structuur te lassen", zegt Labordus, maar er moeten nog problemen worden opgelost. "Afhankelijk van de vorm van het onderdeel en de patch, vormen zich niet overal wervelstromen, dus we kunnen gebieden met koelte of oververhitting krijgen. KVE Composites heeft dit doorstaan en is erin geslaagd om een 2D lineaire conische verbinding te realiseren in CF-stof/PPS-laminaten met uniforme dikte en een perfecte las. "We zaten binnen 10% van de oorspronkelijke materiaaleigenschappen", zegt Labordus.
De volgende stap is het inductielassen van twee rechthoekige delen met elk een geschaafde rand en vervolgens het lassen van een taps toelopende patch aan een cirkelvormig/elliptisch gat met een taps toelopende sjaal, wat in wezen de methode is die wordt gebruikt voor reparaties van thermohardende composieten. "Als dat werkt, stappen we over op UD-laminaten gemaakt met PEEK en PEKK", zegt Labordus. Hij merkt op dat een systeem voor het gebruik van een inductiespoel om reparaties in het veld uit te voeren nog niet is aangetoond, "maar het kan in het laboratorium." Een ander probleem is hoe u druk uitoefent voor voldoende nauw contact tussen de reparatiepleister en het taps toelopende oppervlak. “Op dit moment is de druk die in de labtool wordt gebruikt 5 bar. Ik weet niet zeker of druk van alleen de vacuümzak voldoende is, maar met vlakker UD-materiaal kan 1 bar van alleen de vacuümzak goed zijn.”
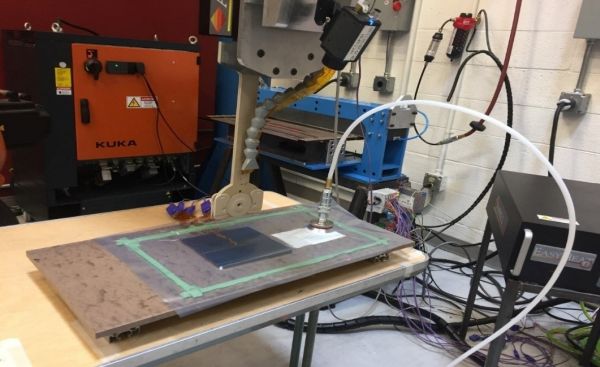
Inductielassen onder een vacuümzak - een mogelijke factor voor toekomstige reparaties van thermoplastische composieten in het veld - wordt ontwikkeld door Michel van Tooren en zijn team aan het McNair Center van de Universiteit van South Carolina. BRON:Michel van Tooren.
Dit werk bij KVE Composites wordt uitgebreid door Michel van Tooren, directeur van het SmartState Center for Multifunctional Materials and Structures, onderdeel van het McNair Center van de University of South Carolina (Columbia, SC, VS). "We lassen thermoplastische composieten inductief onder een vacuümzak, wat erg lijkt op hoe composietreparaties in het veld tegenwoordig worden uitgevoerd met een hete bonder en een warmtedeken", legt hij uit. “De vacuümzak gedraagt zich als zacht gereedschap voor het samendrukken van de twee delen. Je past inductiestroom toe en bereikt een smeltreparatie. U hoeft alleen de procesgrenzen en parameters te definiëren. In sommige opzichten is het gemakkelijker dan thermohardende reparatie, omdat u de reparatie indien nodig altijd kunt omsmelten, zelfs aan de andere kant van de wereld of na 20 jaar dienst. En het resultaat is geen lijmverbinding maar in plaats daarvan een samenhangend onderdeel, dus je elimineert alle problemen met lijmen en hoe je weet of je een goede hechting hebt bij een thermohardende reparatie.” Ook hij is van mening dat met de geautomatiseerde robotreparatietechnologieën die nu worden ontwikkeld, "inductielassen een reparatie relatief eenvoudig zou zijn."
Thermohard tot thermoplastisch lassen
Van Tooren ontwikkelt ook inductielassen om thermohardende en thermoplastische composieten te verbinden. “We introduceren thermoplast in een thermohardende composiet, maar alleen daar waar we willen lassen”, legt hij uit. “We enten op een nanodeeltje en doen een klein beetje kruispolymerisatie. Het resultaat is een eiland van thermoplast geïmplanteerd in en chemisch samengesmolten met de thermohardende composiet. Dan kan ik op het thermoplastische eiland lassen.” Nogmaals, de visie is alternatieve methoden voor het verbinden en monteren van composieten die het boren van gaten en de problemen die gepaard gaan met conventionele lijmverbindingen vermijden.
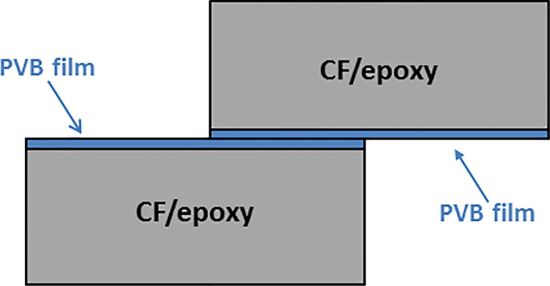
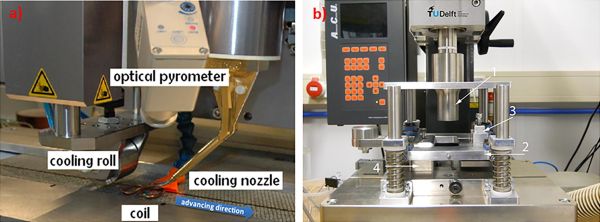
Schema van een TSC-TSC verbinding via PVB thermoplastische koppellaag voor het lassen (boven). Opstellingen (onder) voor inductielassen (links) en ultrasoon lassen (rechts).
BRON:"Hybride lassen van composieten op basis van CF/epoxy".
Het lassen van thermohardende composiet (TSC)-laminaten aan TPC-laminaten (of TS-TP-lassen) wordt door meerdere onderzoeksorganisaties nagestreefd. Irene Fernandez Villegas van de TU Delft - die in het gedrukte artikel wordt genoemd als leider in de ontwikkeling van continu ultrasoon lassen van TPC's - was co-auteur van een artikel uit 2017 met de titel "Hybrid lassen van koolstofvezelversterkte composieten op basis van epoxy" samen met Francesca Lionetto op de University of Salento (Lecce, Italië), Silvio Pappadà bij CETMA Composites (Brandisi, Italië) en anderen. De basis is als volgt:
- Polyvynilbutyral (PVB) is een semi-kristallijn, goedkoop thermoplastisch polymeer met een smelttemperatuur van 150-170°C, gekenmerkt door uitstekende binding en filmvormend vermogen en hechting op vele oppervlakken.
- PVB (Mowital, geleverd door Kurakay) werd gebruikt als een koppelingslaag, toegevoegd en samen uitgehard op een 14-laags koolstofvezelweefsel/epoxy TSC-laminaat (Hexcel 3501-6 prepreg met een vezelvolumegehalte van 58% en 180 °C genezen).
- Macromechanische vergrendeling tussen de PVB-koppelingslaag en de CF/epoxy-composiet werd bereikt door gedeeltelijke penetratie van de PVB-hars in de eerste laag van de TSC (meestal tussen de 10 en enkele honderden micron dik) tijdens co-curing en diffusie van de epoxymonomeren in de PVB thermoplastische film.
- Inductielassen en ultrasone lasprocessen resulteerden in voldoende sterke lasverbindingen, waarbij de resulterende CF/epoxy naar CF/epoxy-verbindingen gelast door de PVB-koppelingslagen met een overlap-afschuifsterkte van ≈25 MPa, wat binnen het typische bereik van sterktewaarden voor CF/epoxy lijmverbindingen.
Automobiel
Bijna alle bedrijven die in het artikel over thermoplastisch lassen zijn opgenomen, kijken naar zowel auto- als ruimtevaarttoepassingen. “Lassen helpt composieten concurrerend te maken ten opzichte van aluminium”, zegt Offringa van GKN Fokker. “Automotive kijkt ook naar lassen als een snel alternatief voor verlijmen. We hebben met verschillende automotive bedrijven gesproken over snelle verwerking van composieten.” Hij wijst erop dat carrosserieën van koolstofvezelcomposiet meestal thermohardend zijn, gebonden met een bepaalde lijmdikte. "Als je deze onderdelen zou kunnen maken met behulp van thermoplastische composieten en openingen tussen de componenten weg te werken door de assemblage te lassen, dan kun je een stijvere carrosseriestructuur maken, wat gewichts-, kosten- en prestatievoordelen oplevert.”
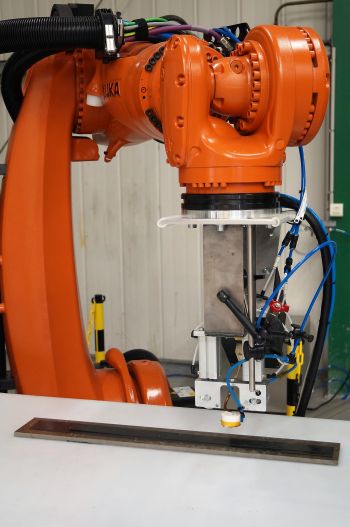
De dynamiek van samengestelde integriteit inductie lasproces setup.
BRON:Samengestelde integriteit.
Jérôme Raynal, business development manager voor Composite Integrity ziet ook potentieel. Zijn bedrijf werkte samen met STELIA Aerospace aan de ontwikkeling van het dynamische inductielasproces dat wordt gebruikt om CF/PEKK UD-tape stringers en romphuiden samen te voegen in de TP-demonstrator, onthuld op de Paris Air Show 2017. "We hebben resistief lassen ontwikkeld voor auto's met zowel polyamide [PA, nylon] als polypropyleen [PP] composieten", zegt Raynal. “Hiervoor hebben we verschillende technologieën. We kunnen bijvoorbeeld een metalen draad in een onderdeel inbedden, in contact brengen met een ander onderdeel en stroom injecteren. We kunnen ook een koolstofvezel resistieve patch op de lasinterface plaatsen om de benodigde laswarmte te genereren.” In één ontwikkeling werden twee componenten gemaakt van CF/PA gelast met behulp van een speciaal ontworpen resistieve patch gemaakt met hetzelfde polymeer en een glasvezelvlies om het aangrenzende laminaat elektrisch te isoleren en de energie op de laslijn te concentreren. Hoe zit het met metalen inzetstukken die heel typerend zijn in auto-onderdelen? "Onderdelen met metalen inzetstukken zijn geen probleem bij weerstandslassen, en bij inductielassen zou je een speciaal ontworpen spoel gebruiken of de elektromagnetische velden en stroom op een andere manier wijzigen", antwoordt Raynal. "Dit zou ontwikkeld moeten worden, maar het is vergelijkbaar met wat we al hebben aangetoond voor de geautomatiseerde productie van vliegtuigconstructies."
Verdere ontwikkelingen en andere projecten
Een opmerking over de openingsafbeelding. Het toont een CAD-weergave van het geautomatiseerde proces ontwikkeld door het DLR Center for Lightweight Production Technology (DLR ZLP, Augsburg, Duitsland) met behulp van een ultrasoon lassen hoofd op een KUKA Quantec KR210 industriële robot om acht TPC-secties samen te voegen tot een achterste drukschot (RPB) voor een A320-type vliegtuig. In het bijbehorende gedrukte artikel over TPC-lassen besprak ik de ontwikkeling van DLR ZLP van een weerstandslassen methode die werd gebruikt op Premium Aerotec's A320 RPB-demonstrator die werd tentoongesteld op de ILA-vliegshow van 2018 in Berlijn. Volgens Lars Larsen, groepsmanager assemblage- en verbindingstechnologieën bij DLR ZLP:"Parallel aan het weerstandlasproces met behulp van een 'lasbrug', hebben we ook een robotaangedreven ultrasone laskop ontwikkeld. We hebben voorlopige tests uitgevoerd om de relevante lasprocesparameters te bepalen en in de komende maanden zullen we de integratie van die ultrasone laseindeffector in onze robot verfijnen. Ons doel is om één enkel industrieel proces te ontwikkelen voor het lassen van zowel de stringers van de vliegtuigromp als het achterste drukschot gemaakt van thermoplastische composieten.”
Andere projecten die ik deze keer niet kon behandelen, zijn EireComposites en haar deelname aan de Ybridio- en Innova-projecten, waarbij het potentieel voor lassen wordt nagestreefd om de kosten te verlagen en de automatisering te vergroten. Het bedrijf meldt inductielassen en weerstandslassen voor CF/PEEK-, CF/PEKK- en GF/PP-composieten en dat thermoplastisch lassen werd geëvalueerd voor de Bombardier CSeries (nu de Airbus A220) vleugel.
Tods Aerospace, nu onderdeel van Unitech Aerospace, nam deel aan een National Aerospace Technology Exploitation Program (NATEP), gesponsord door Rolls-Royce, waarin werd gekeken naar de ontwikkeling van een weerstandslastechniek waarbij geen metalen implantaten worden gebruikt. TenCate-Toray en het National Composites Centre (Bristol, VK) waren ook partners.
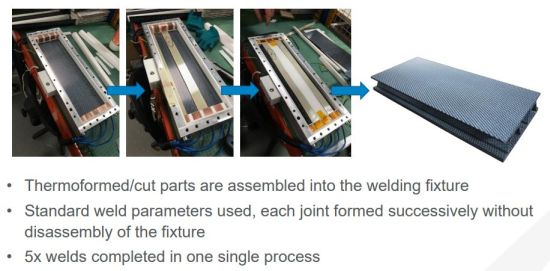
Deze procesdemonstrator onderzocht een methode voor het vervaardigen van met een hoed verstijfde TPC-structuren. BRON:Unitech Aerospace (begin bij Sectie 6, p. 39)
Blijf ons volgen, want ik ben van plan in de nabije toekomst de ontwikkelingen van Laser Zentrum Hannover (LZH) met laserlassen van thermoplastische composieten te bespreken.
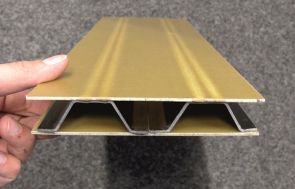
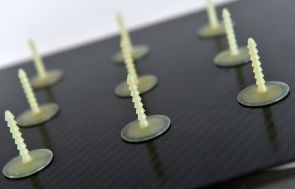
BRON:LZH Laser Zentrum Hannover eV
Hars
- Covestro verhoogt investeringen in thermoplastische composieten
- Thermoplastische composieten bij Oribi Composites:CW Trending, aflevering 4
- RECONTRAS-project valideert het gebruik van microgolven en laserlassen om recyclebare composieten te verkrijgen
- Salewas nieuwe wandelschoen met thermoplastische composieten
- Problemen oplossen met thermovormen van thermoplastische composieten
- Thermoplastische composieten:structurele bumperbeugel
- Toray Advanced Composites breidt mogelijkheden voor thermoplastische composieten uit
- Teledyne CML Composites investeert in verwerkingscapaciteit voor thermoplasten
- IRG CosiMo thermoplastische composieten consortium onthult nieuwe faciliteiten
- Thermoplastische composieten:schilderachtig uitzicht
- Thermoplastische composieten lassen