3D-geprinte composieten met 60% vezels, minder dan 1% holtes
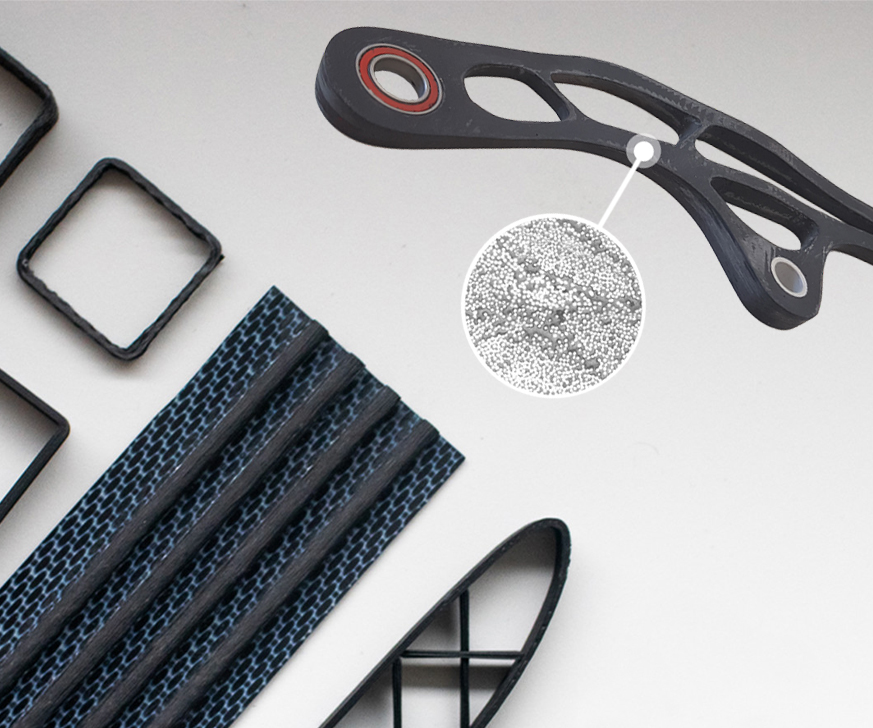
"Ons belangrijkste doel is om structurele continue vezelcomposieten voor de industrie te produceren", zegt Giovanni Cavolina, medeoprichter van 9T Labs (Zürich, Zwitserland). "Als je praat met mensen die CFRP-onderdelen (koolstofvezelversterkt polymeer) maken, geloven de meesten niet dat het mogelijk is om een superlaag gehalte aan lege ruimte of een goede interlaminaire afschuifsterkte (ILSS) tussen lagen te bereiken met continu 3D-printen van vezels." 9T Labs heeft echter een gepatenteerd nabewerkingsproces ontwikkeld dat holtes elimineert. "We kunnen nu continu vezelcomposieten 3D printen met een goede hechting tussen de lagen en een holte van minder dan 1 procent, wat concurreert met conventioneel vervaardigde composieten."
Begin bij ETH Zürich
9T Labs begon met een onderzoeksproject in het Laboratory of Composite Materials and Adaptive Structures (CMAS) van het Zwitserse Federale Instituut voor Technologie Zürich (ETH Zürich). Cavolina en 9T Labs mede-oprichters Martin Eichenhofer en Chester Houwink had een composietprintkop ontwikkeld, "die we op een robotarm hebben gemonteerd en roosterkernen hebben gemaakt voor ultralichtgewicht sandwichstructuren, bedoeld voor ruimtevaarttoepassingen", legt Cavolina uit.
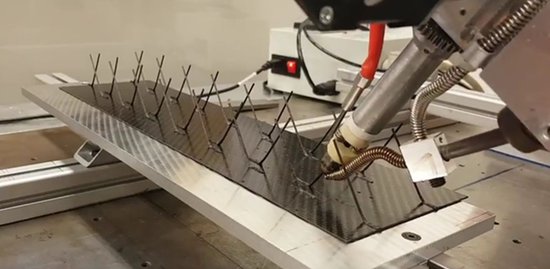
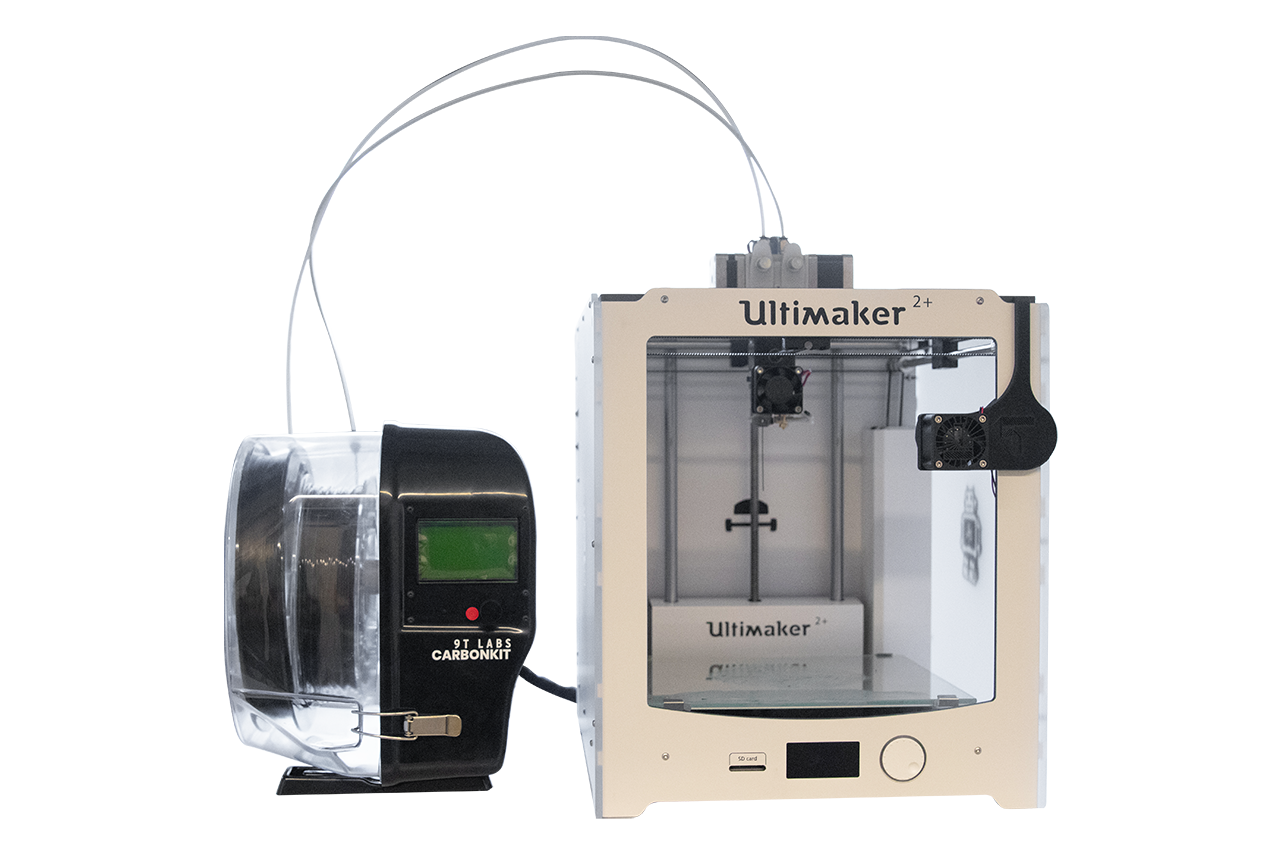
CarbonKit was een product met beperkte oplage waarmee kant-en-klare FDM-printers continue koolstofvezel konden gebruiken, maar was nog niet de juiste oplossing voor het produceren van kostenconcurrerende, industriële CFRP-structurele onderdelen. BRON | 9T Labs.
CarbonKit
Zo werd 9T Labs begin 2018 opgericht om het concept van 3D-printen van monolithische CFRP-laminaten te bewijzen die aan potentiële klantvereisten zouden kunnen voldoen. "Onze volgende stap was de CarbonKit", zegt Cavolina. Dit is het product dat voorkomt in CW ’s maart 2019 artikel “Continuous fiber 3D printing into production”. De CarbonKit transformeert Ultimaker of Prusa 3D-printers in een systeem dat kan printen met continue koolstofvezel. “Hiermee kunt u uw bestaande printers gebruiken in combinatie met onze printkop, filamenten en software om continue vezels te plaatsen, volgens het belastinggeval, met 50 procent koolstofvezelvolume-inhoud - niet 30 procent, wat de norm was in CFRP 3D-printen ”, voegt hij eraan toe.
Cavolina legt uit dat hoewel de interesse in dit product vrij groot was, “we slechts aan 25 klanten hebben geleverd. We hebben dit product beperkt gehouden omdat we ons realiseerden dat het met slechts een eenstaps FDM [fused deposition modeling]-proces niet mogelijk is om structurele eindgebruiksonderdelen voor industriële lucht- en ruimtevaarttoepassingen te realiseren die ook qua kosten concurrerend zijn met de huidige technologieën."
Via de CarbonKit heeft 9T Labs echter waardevolle klantrelaties opgebouwd. "We kwamen erachter wat bedrijven verwachtten en nodig hadden, ook al waren deze onderdelen eigenlijk niet te produceren met de CarbonKit", legt hij uit. “In situ consolidatie is inderdaad mogelijk met FDM, maar daarvoor zijn veel complexere machines nodig die onbetaalbaar zijn. Dus hebben we een proces in twee stappen ontwikkeld met een post-print consolidatie.”
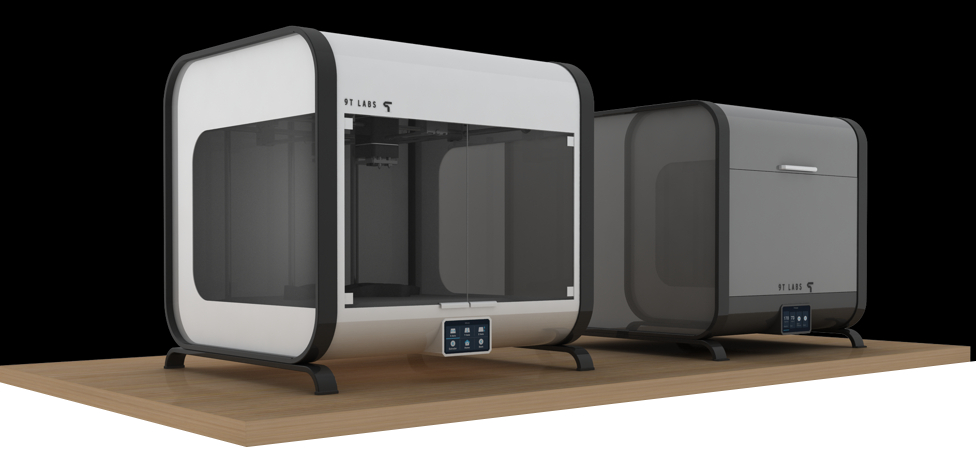
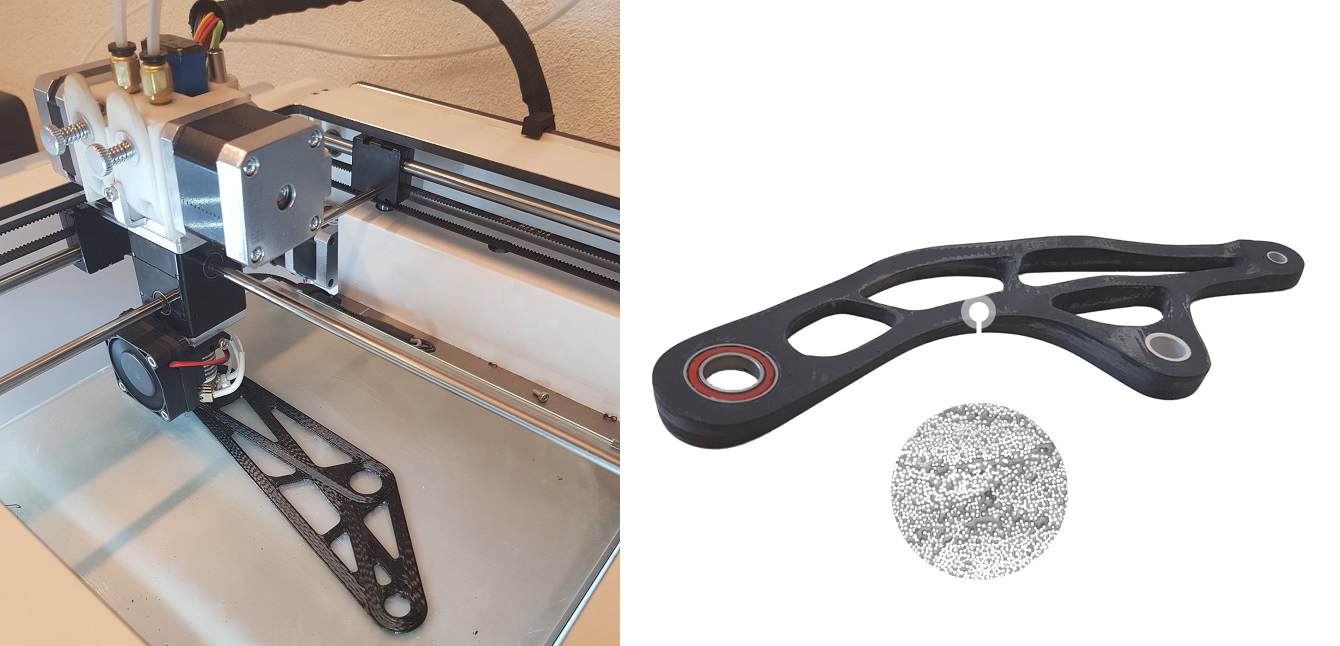
Met Red Series heeft 9T Labs 3D-geprinte CFRP-structuren bereikt met>50% vezelvolume en <1% holtes tegen een betaalbare prijs in vergelijking met de huidige productiemethoden voor composieten. BRON | 9T Labs.
Red Series, 2-stappen proces
Dat brengt ons waar 9T Labs vandaag staat. “We commercialiseren de Red Series, die bestaat uit twee units:een klassieke FDM-printunit met een gepatenteerde printkop en een aangrenzende Fusion Unit voor nabewerking”, legt Cavolina uit. “We realiseren geen volledige in-situ consolidatie tijdens het printen, maar printen en consolideren in een tweede proces. In wezen drukken we een voorvorm die in de Fusion-eenheid wordt geplaatst voor postconsolidatie met behulp van hoge temperatuur en druk om een vezelvolumegehalte van meer dan 50 procent te bereiken met minder dan 1 procent lege ruimten. Met dit 2-stappenproces wordt lucht- en ruimtevaartkwaliteit bereikt tegen een betaalbare prijs.”
De Red Series gebruikt voorlopig thermoplastische materialen. “We printen koolstofvezel met PEI, PEKK, PA (nylon) en hebben ook ervaring met PP”, zegt Cavolina. Is de Red Series een systeem met open materialen? "De enige manier om kostenconcurrerend te zijn, is door bestaande materialen te gebruiken met een nieuw productieproces", legt hij uit. “Als je vanaf nul met je eigen materiaal komt, sluit je uit dat je in serieproductie kunt gaan. Omwille van de veiligheid en betrouwbaarheid van de toeleveringsketen zullen seriefabrikanten voor hun materialen niet afhankelijk zijn van een klein bedrijf. Dus laten we onze klanten hun bestaande materiaalvoorraad gebruiken door ervoor te zorgen dat de materialen in ons systeem werken.” Hij legt uit dat 9T Labs de materialen test om er zeker van te zijn dat de grondstof aan bepaalde vereisten voldoet en de beste parameters voor printen bepaalt.
Hoe zit het met open-software? “Onze printsoftware wordt gecombineerd met structurele simulatiesoftware”, zegt Cavolina. “Als ingenieur is het geweldig om vezels te plaatsen waar nodig, maar hoe weet je zeker dat dit ook echt de plek is waar ze moeten worden geplaatst? Onze software geeft de vrijheid om te ontwerpen en vervolgens te kruisen met een structurele simulatie. De andere richting is om een vezelgeoriënteerde lay-up in een structurele simulatie te definiëren en deze vervolgens in onze software om te zetten in een printpad. We gebruiken een bestaande, beproefde en bekende partner voor de FEA die op de achtergrond draait. U kunt ook direct een onderdeel in CAD ontwerpen en dat bestand vervolgens uploaden naar ons programma. Daar bepaal je waar je de koolstofvezel wilt hebben en waar puur polymeer voldoende is.”
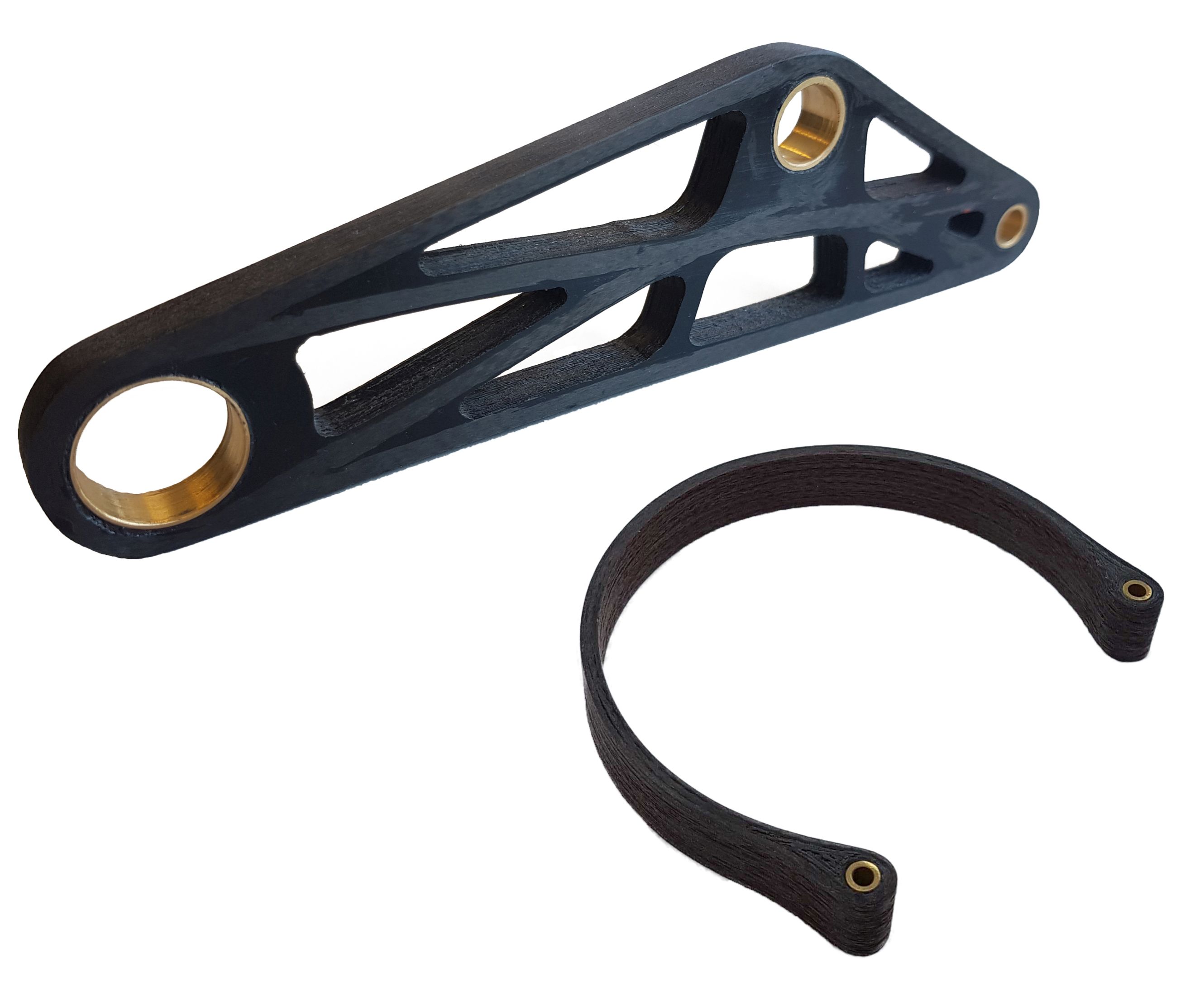
Deze CFRP-beugel en tuimelaar voor niet-ruimtevaarttoepassingen voldoen feitelijk aan de vereisten voor ruimtevaartlaminaat en zijn voorzien van meer dan 40 lagen - elke laag met een andere vezeloriëntatie om anisotropie te benutten en structurele onderdelen te optimaliseren die voorheen niet mogelijk waren. BRON | 9T Labs.
Toepassingen
9T Labs streeft naar lucht- en ruimtevaart (voorlopig interieur), biomedische en industriële automatisering (bijv. verpakkingsmachines), evenals vrije tijd/luxe (bijv. motorsport, sportschoenen, brillen). Deze laatste markt, zegt Cavolina, "is waar je structurele composieten nodig hebt, maar de vereisten zijn niet zo streng als in de ruimtevaart." Hij citeert de hierboven getoonde tuimelaar. "Dit is een beugel voor een niet-luchtvaartconstructie die een structurele toepassing vertegenwoordigt die je op een geoptimaliseerde manier kunt produceren met onze technologie", legt hij uit. "Het komt van een aluminium onderdeel dat topologie is geoptimaliseerd om gewicht te besparen door koolstofvezels te oriënteren volgens het belastingsgeval. U kunt kosten besparen omdat u de hoeveelheid gebruikte koolstofvezel kunt verminderen in vergelijking met andere composietprocessen. Je kunt het niet op een andere manier maken, omdat het met andere methoden niet mogelijk is om elke vezel in hoge resolutie naar wens te oriënteren.”
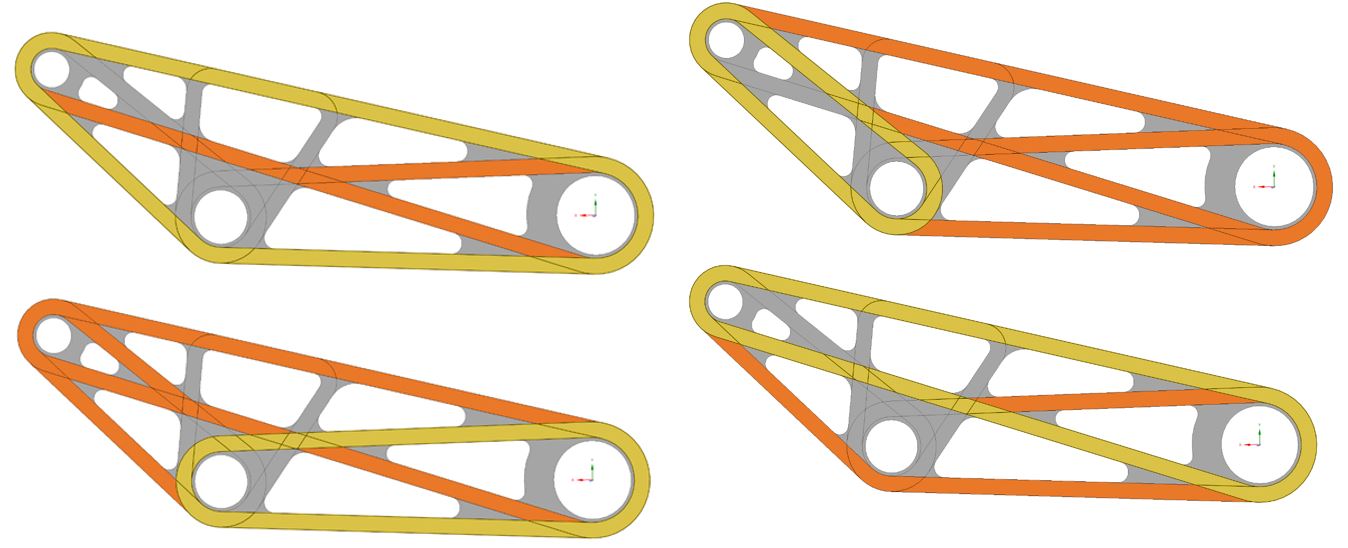
Vier verschillende doorlopende koolstofvezellay-ups worden afgewisseld over de dikte van de CFRP-beugel bedrukt met 9T Labs Red Series. BRON | 9T Labs.
Cavolina merkt op dat deze tuimelaar uit meer dan 40 lagen vezels en polymeer bestaat, "en we kunnen in elke laag een andere vezeloriëntatie hebben. We hebben vier verschillende lay-ups geprobeerd, niet beperkt tot quasi-isotroop. Deze vrijheid stelt ons in staat om de anisotropie van composieten te benutten om de eindgebruikstructuur verder te optimaliseren. Het zou niet mogelijk zijn om dit te doen met andere huidige productiemethoden.”
Hij wijst er ook op dat 3D-printen van CFRP een geautomatiseerd proces is in vergelijking met handlayup. "Onze technologie vermindert de handmatige arbeid drastisch via geautomatiseerde lay-up", zegt Cavolina. "Met onze technologie hoeft u alleen maar af te drukken, te consolideren en klaar."
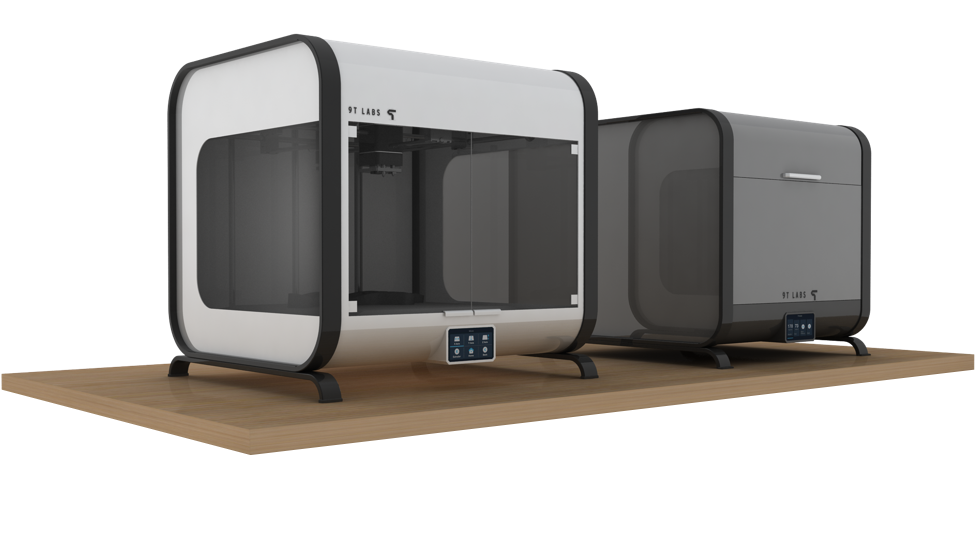
De Red Series print kleinere, complexe, monolithische CFRP-preforms die vervolgens worden geconsolideerd in een tweede stap voor schaalbare industriële serieproductie. BRON | 9T Labs.
Afdrukformaat, snelheid en volledige lancering van de rode serie
De Red Series is gericht op kleinere, monolithische onderdelen voor serieproductie binnen een printoppervlak van 350 millimeter bij 300 millimeter. “Hier zien we momenteel de hoogste toegevoegde waarde voor onze klanten”, legt Cavolina uit.
Hoe zit het met de afdruksnelheid? "We hebben het heel concreet over de productie in de komende 1-2 jaar van 4.000 tot 8.000 onderdelen per jaar voor verschillende klanten, bereikt met de Red Series twin-units", zegt Cavolina. "Omdat we de productie van complexe, gedetailleerde preforms hebben losgekoppeld van consolidatie, is het nu mogelijk om het productievolume snel op te voeren."
"We hebben veel tijd besteed aan het analyseren van de kostenstructuur van ons proces, inclusief apparatuur, arbeids- en materiaalkosten", reageert hij. “We hebben een betaalbare kostenstructuur voor apparatuur en hebben het voorvormproces geautomatiseerd. We gebruiken materialen die het meest betaalbaar en efficiënt zijn, en verminderen vervolgens de hoeveelheid materiaal die nodig is door de vezels per belastinggeval te oriënteren en structurele optimalisatie te gebruiken. We werken nauw samen met onze partners op het gebied van structurele en processimulatie en zien dat dit zal blijven groeien als een groot deel van het productiedoel om digitale twin-technologie te gebruiken om plug-and-play met 4.0-productielijnen en -cellen mogelijk te maken."
De Red Series wordt gelanceerd in 2020. “Nu evalueren we het via onze samenwerkingsprogramma's met productiepartners. We certificeren de onderdelen en processen met hen, dus ze hebben de eerste slots gereserveerd voor Red Series-machines en zullen deze gebruiken om hun eindgebruiksproducten te vervaardigen.
Hars
- Versterking van 3D-geprinte onderdelen met efficiënte glasvezelroutering:deel 1
- Een deel van de week — 3D-geprint statief met doorlopende, met koolstofvezel versterkte poten
- Recycling:continu-vezelversterkte thermoplastische composieten met gerecycled polycarbonaat
- Korte koolstofvezelverbindingen vergroten het bereik van thermoplastische composieten
- De kosten van 3D-printmaterialen met continue vezels verlagen
- TxV Aero Composites voldoet aan de AS9100-normen
- Hexcel werkt samen met Lavoisier Composites, Arkema
- Recycling van composieten - geen excuses meer
- Covestro lanceert Maezio thermoplasten met continue vezels
- Continuous Fiber Manufacturing (CFM) met moi-composieten
- 3D-print composieten met continue vezels