Continuous Fiber Manufacturing (CFM) met moi-composieten
Continu 3D-printen en depositie van vezels winnen aan kracht. Naarmate het aantal bedrijven dat het gebruikt en ontwikkelt, groeit, zal deze technologie ongetwijfeld de composietenindustrie vormgeven.
Ten eerste biedt het fabricage zonder mallen of gereedschappen. Ten tweede biedt het multifunctionele structuren (bijvoorbeeld elektrische geleidbaarheid, vormverandering, detectie). Ten derde opent het de deur naar een wereld van gehybridiseerde productie - bijvoorbeeld lamineren bovenop 3D-printen en frezen tijdens het printen - evenals een bijna eindeloos landschap van materiaalontwikkeling, van Nitinol-vormgeheugenlegering (SMA)-vezels tot geleidende nanocomposietoplossingen voor vloeibare depositiemodellering (LDM). Dat laatste is een hele wereld op zich waar ik in een volgende blog op terug zal komen.
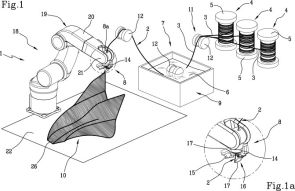
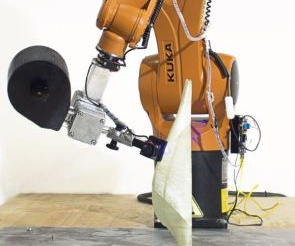
Patent WO2017085649A1 en Atropos-afdruksysteem. BRON:moi composieten.
Moi composieten werd in februari 2018 opgericht door materiaalingenieur en professor Marinella Levi, ontwerpingenieur Gabriele Natale en architect Michele Tonizzo. In 2013 begon professor Levi te werken met 3D-printen aan de Politecnico di Milano (Milaan, Italië). In 2014 had ze +LAB gevormd in de afdeling Scheikunde, Materialen en Chemische Technologie van de universiteit "Giulio Natta". Haar visie was om R&D, onderwijs en materiaalinnovatie te versmelten door ingenieurs, ontwerpers, onderzoekers en makers samen te brengen in een multidisciplinair, collaboratief 3D-printcentrum.
2014 Eerste tool voor het 3D printen van continue vezel thermohardende composieten 2015 Octrooi WO2017085649A1 2016 Partnerschappen met Owens Corning en KUKA Robotics,Atropos project- en printsysteem 2017 JEC Innovation Award, samenwerking met Autodesk,
James Dyson prijs runner-up,
Partnerschap met COMAU-automatisering
(Volledige tijdlijn)
"We zijn met moi composites begonnen omdat we commerciële onderdelen wilden produceren en betrokken wilden zijn bij internationale projecten", legt Michele Tonizzo uit. “We hebben ontdekt dat er veel markt is. We maken biomedische componenten en onderdelen voor maritieme, olie &gas- en ruimtevaarttoepassingen, voornamelijk met behulp van glasvezel. De CFM-technologie is in staat om unieke oplossingen te produceren die met traditionele methoden onmogelijk zouden zijn."
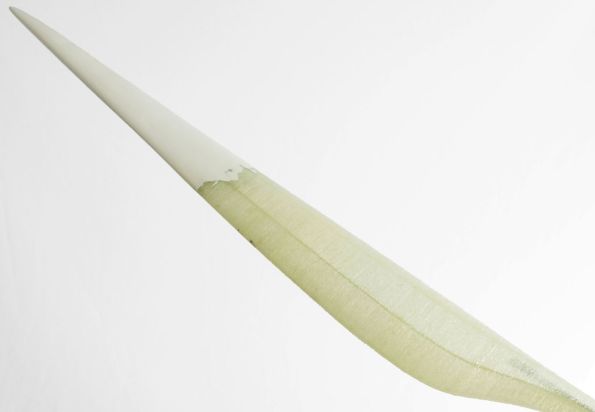
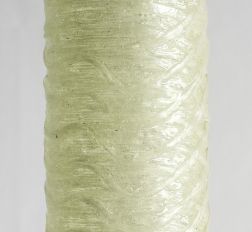
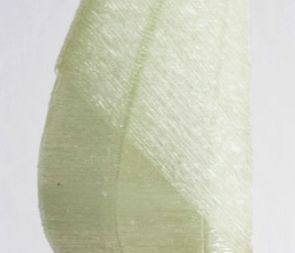
3D-geprint propellerblad met interne structurele truss met behulp van continue glasvezel (bovenkant). Dit project demonstreerde ook vezelplaatsing langs niet-lineaire curven (linksonder) en continu vezellaminaat met traditionele vezeloriëntaties (bijv. 0°,+45 °, -45°, 90°, rechtsonder). BRON:moi composieten
Assortiment harsen en vezels
Atropos toonde het vermogen om discontinue en continue vezelversterkte, thermohardende polymeren te printen, niet alleen laag voor laag, maar ook langs niet-lineaire curven. Het gebruikte ultraviolet (UV) licht om de polymeren op hun plaats uit te harden. “Momenteel kunnen we printen met UV-cure in epoxy, acryl en vinylester”, zegt Tonizzo. Hij merkt op dat acryl goed werkt voor architecturale onderdelen omdat het helder is en geen temperatuur vereist voor uitharding/nabehandeling. Vinylester wordt gebruikt voor scheepsonderdelen en epoxy voor olie- en gas- en ruimtevaartonderdelen.
"Voor sommige toepassingen is UV-uitharding slechts de eerste fase en daarna uitharden we met conventionele verwarming", merkt Tonizzo op. “We zijn niet gebonden aan UV-uitharding. We hebben geprint met niet-UV-uithardende polymeren en begrijpen dat we voor toepassingen met hogere eigenschappen verschillende matrixopties nodig hebben.” Ter referentie:de glasovergangstemperatuur (Tg) voor hun meest gebruikte hars, een vinylester, is ongeveer 140°C.
"We werken ook met koolstofvezel, maar niet met UV-uithardende harsen", zegt Tonizzo. Hij wijst erop dat zowel vezeltransparantie en kleur beïnvloeden UV-uitharding. “Het probleem met koolstof is dat het ondoorzichtig is en zwart. Dit is de slechtste combinatie. We willen de beste oplossing voor koolstofvezel als materiaal ontwikkelen, niet alleen de gemakkelijkste technologie die werkt. Er zijn veel andere opties voor uithardingsmaterialen die we kunnen gebruiken, dus we onderzoeken deze.”
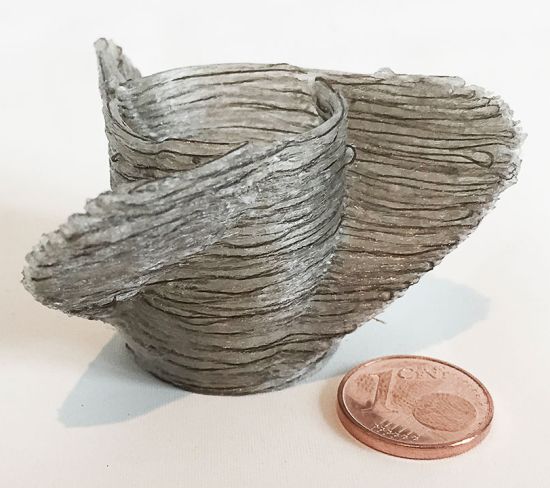
Moi-composieten kunnen print continu geleidende vezels voor elektrische/thermische functionaliteit, detectie, vormverandering, enz. BRON:moi composieten.
Moi composieten heeft continue glasvezels tot 2400 tex (207 yd/lb met een maximale diameter van 24 m per Owens Corning datasheet) geprint en test natuurlijke vezels. Het is ook bedrukt met basaltvezel. "We kunnen heel goed printen met UV-uitharding en basaltvezel omdat het eigenlijk wat transparanter is en meer bruin dan zwart", legt Tonizzo uit.
Vezels die elektrische stroom geleiden, kunnen ook worden gebruikt in de CFM-technologie. Ze kunnen naar behoefte in de te printen structuur worden geplaatst. Een van de projecten die op de +LAB-website worden vermeld, toont Nitinol-vezel, een legering in geheugenvorm. "Je zou dus structuren kunnen maken die van vorm kunnen veranderen", zegt Tonizzo. “Je zou het bijvoorbeeld kunnen gebruiken om andere vezels te ontlasten, zoals in voorgespannen beton.”
3D-printen als onderdeel van hybride productie
Atropos maakt gebruik van een Kuka robotarm met een bedrukte envelop van 0,5 x 0,5 x 0,5 m hoog. "We printen nu op een Comau-robot met een envelop van 1,0 x 0,5 x 0,8 m hoog, het systeem van de tweede generatie", zegt Tonizzo. "We hebben ook grotere robots met draaitafels gebruikt en volumes van 1,5 x 1,5 x 1 m hoog gebouwd en aangetoond dat onze technologie eenvoudig schaalbaar is."
Moi ontwikkelt ook een derde generatie, alles-in-één printkop met een systeem om druk uit te oefenen op de vezels, sensoren, snijmechanismen en freesgereedschap. Tonizzo zegt dat dit de kloof tussen 3D-printen en geautomatiseerde vezelplaatsing (AFP ). “3D-printen haalt niet de prestaties van AFP, maar CFM biedt meer flexibiliteit. We kunnen al printen met vezels met een dikte van 0,25 mm en hebben de mogelijkheid om bochten te maken en doorlopende vezels in de ideale positie te plaatsen”, voegt hij eraan toe.
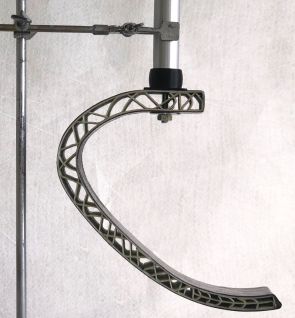
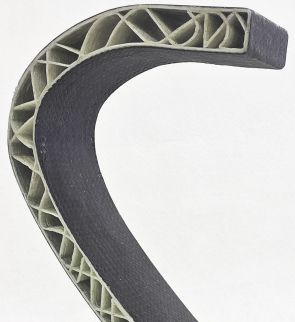
SuPeRIOR is een onderste ledematenprothese geoptimaliseerd voor minimaal gewicht, doorbuiging en kosten.
De 3D-geprinte structurele kern werd vervolgens gelamineerd met koolstofvezel en epoxyhars, gevolgd door VBO-uitharding. BRON:moi composieten.
"3D-printen moet worden gebruikt waar het het beste in is", zegt Tonizzo, "waaronder het optimaliseren van de workflow. U kunt bijvoorbeeld een interne kern 3D printen met ondersnijdingen en slimme vezelrichtingen. Je gebruikt dan gewone handlaminering bovenop en hardt alleen uit in een autoclaaf of met vacuümzak.” Hij beschrijft een onderdeel dat met een mal niet conventioneel te maken was. “We hebben de interne kern geprint en vervolgens in laminaat gewikkeld en in de autoclaaf gehard bij 110°C en 2 bar druk gedurende enkele uren. Het onderdeel kwam goed uit.” Dit onderdeel valt onder een geheimhoudingsverklaring, dus verdere details zijn niet beschikbaar, maar moi heeft de SuPeRIOR-prothese op een vergelijkbare manier geproduceerd, niet uitgehard in een autoclaaf maar alleen met vacuümzak (VBO). "Alle interne onderdelen maken gebruik van één continue glasvezel", legt hij uit, "maar het buitenste laminaat is met de hand gemaakt koolstofvezelweefsel en epoxyhars." Het hele ontwerp vermindert doorbuiging en vergroot de aanpassing, terwijl de kosten en productietijd aanzienlijk worden verlaagd.
Voxel-gebaseerde optimalisatiesoftware
Tonizzo legt uit dat het onderdeelontwerpproces het voxel-gebaseerde algoritme van Autodesk combineert met de algoritmen van moi voor stress- en padoptimalisatie. Dit is wat het geoptimaliseerde vezelpad voor de structuur produceert. De software werkt ook om het meest mogelijke pad te kiezen om te produceren. "Dit is een iteratief proces", zegt Tonizzo. “Het ontwerp is niet volledig geautomatiseerd zoals generatief ontwerp. Het heeft nog steeds ingenieurs nodig om keuzes te maken. Maar ik denk dat dit is hoe het zou moeten zijn:de ontwerper en de software gecombineerd, niet alleen AI alleen."
Multi-materiële toekomst, sterk marktpotentieel
Op een van de afbeeldingen van het door Atropos bedrukte propellerblad is een close-up te zien van een bijna geweven patroon. "Dit is niet echt geweven, maar het zal binnenkort mogelijk zijn", zegt Tonizzo. Hij verwijst me naar het sinusgolfproject op de +LAB-website. "De getoonde demonstrators zijn 3D-geprint in plastic met korte vezels en het LDM-proces [liquid deposition modeling] terwijl ze onderzoekers waren bij +LAB. De algoritmen die we toen gebruikten, zijn dezelfde die we nu ontwikkelen met continue glasvezel.”
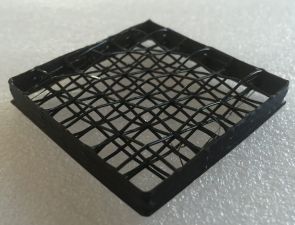
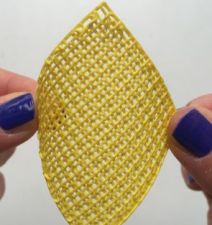
+LAB's Sine Wave demonstreert 3D-geprinte polymeer invulpatronen met een instelbare elastische respons. BRON:+LAB.
Het is duidelijk op de +LAB-website dat materiaalinnovaties en mogelijkheden voor dit soort drukwerk bijna eindeloos zijn. De vraag is wat de meeste kansen en mogelijkheden biedt voor veeleisende oplossingen. Ondertussen ondersteunen materiaalleveranciers de verdere ontwikkeling. Owens Corning is bijvoorbeeld geïnteresseerd om glasvezel te demonstreren met meer matrices, zoals keramiek en beton. Dit is uiteraard zeer interessant voor bouw- en constructietoepassingen en zou een aanzienlijk potentieel kunnen hebben in het licht van de huidige trends voor digitale fabricage en energiezuinig bouwen, offsite geprefabriceerde modules en verbeterde duurzaamheid via natuurlijke en gerecyclede materialen, die allemaal lichtgewicht benadrukken. "De Giulio Natta-afdeling van de Politecnico di Milano is betrokken bij een EU-project voor het printen van geopolymeren die zich als beton gedragen", voegt Tonizzo toe. “Ze worden na verloop van tijd vanzelf uitgehard, maar hebben de consistentie als klei tijdens het printen voor een betere vloei. We zullen zeker blijven werken op dit gebied, evenals met nieuwe polymeren en vezels.”
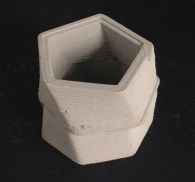
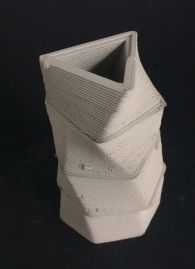
Moi-composieten is ook printen met geopolymeren, die zich gedragen als beton.
BRON:+LAB.
Ga je machines verkopen? “Ja, maar in de toekomst”, zegt Tonizzo. "Voorlopig produceren we onderdelen en brengen we de technologie naar de faciliteit van de klant, waarbij we onze knowhow, printkop en software gebruiken om on-demand onderdeeloplossingen te realiseren." Hij voegt eraan toe dat moi composites, na het afgelopen jaar te hebben gewerkt aan het verbeteren van de technologie met CFM-early adopters en het demonstreren van de businesscase voor veel verschillende onderdelen in verschillende markten, nu investeerders zoekt om CFM-machines en -processen verder op te schalen voor commerciële marktkansen.
Hars
- montage-armaturen voor 3D-printen met Markforged Composites
- Additive Manufacturing met composieten in de lucht- en ruimtevaart en defensie
- Beoordeling van een in beweging zijnde toeleveringsketen van composieten
- Het commercialiseren van UV-uithardende thermoharders voor continu 3D-printen met vezels
- Vraag en antwoord met Ethan Escowitz, CEO, Arris Composites
- Recycling van composieten - geen excuses meer
- Continue vezelproductie vervaagt de grens tussen 3D-printen en AFP
- Covestro lanceert Maezio thermoplasten met continue vezels
- 3D-print composieten met continue vezels
- Severstal investeert in robotica om geavanceerde composietproductie te automatiseren met Airborne
- GE Digital:operationele inzichten met gegevens en analyses