CosiMo:slim thermoplastisch RTM-proces gedemonstreerd voor challenge-simulator voor accubakafdekking
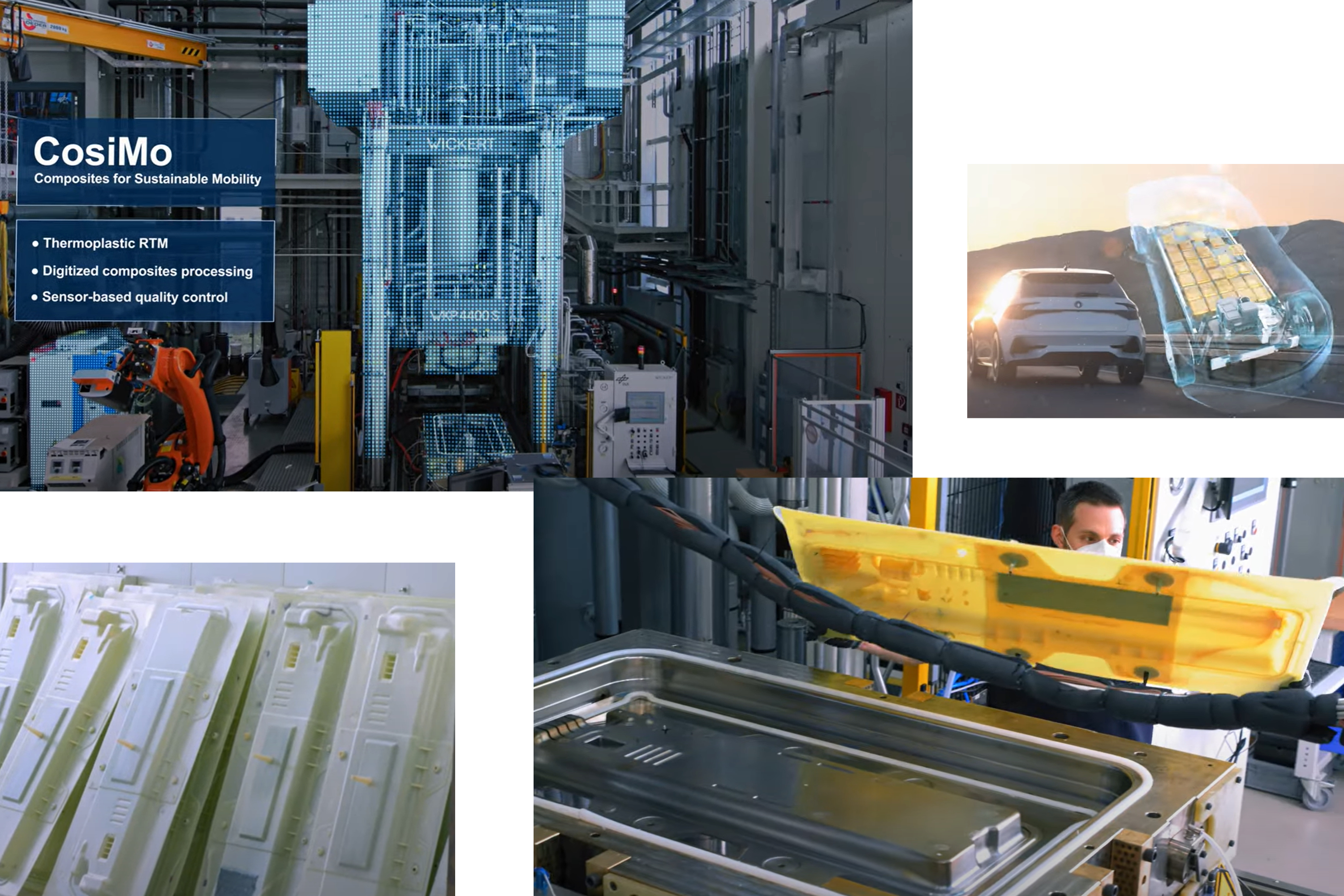
Het project "composieten voor duurzame mobiliteit" (CosiMo) werd in 2018 gelanceerd door Faurecia Clean Mobility (Nanterre, Frankrijk) om een slim thermoplastisch composiethars-transfergietproces (RTM) te ontwikkelen met behulp van een uitgebreid sensornetwerk inclusief gegevens van een intelligente mal. als machinegegevens van een injectiemachine en hete pers. Het project zal eind 2021 worden afgerond en CosiMo-partners hebben kennis en ervaring opgedaan met closed-loop besturing waarbij realtime sensorgegevens worden gecombineerd met materiaalparameters uit laboratoriumgegevens en simulatiegegevens. CosiMo wordt gefinancierd door het Beierse ministerie van economische zaken, regionale ontwikkeling en energie binnen het Campus Carbon 4.0-programma.
Het demonstratiegedeelte, met een lengte van 1.100 millimeter en een breedte van 530 millimeter, is ontworpen door het onderzoekscentrum van Faurecia Clean Mobility in Augsburg, Duitsland. Het doel was om materiaal- en procesbeperkingen te onderzoeken, waaronder metaal- en schuimkern, complexe geometrie, verschillende radii en diktes variërend van 2,5 tot 10 millimeter. Niet-geweven glasvezels tot 1.000 gram/m² werden geleverd door de faciliteit van het Instituut voor Textieltechnologie (ITA) in Augsburg. Glasvezel non-crimp weefsels (NCF) en koolstofvezel unidirectionele tapes voor lokale versterking werden ook onderzocht. De glasvezelmaterialen maken het gebruik van gerecyclede vezels van end-of-life (EOL) composietonderdelen mogelijk.
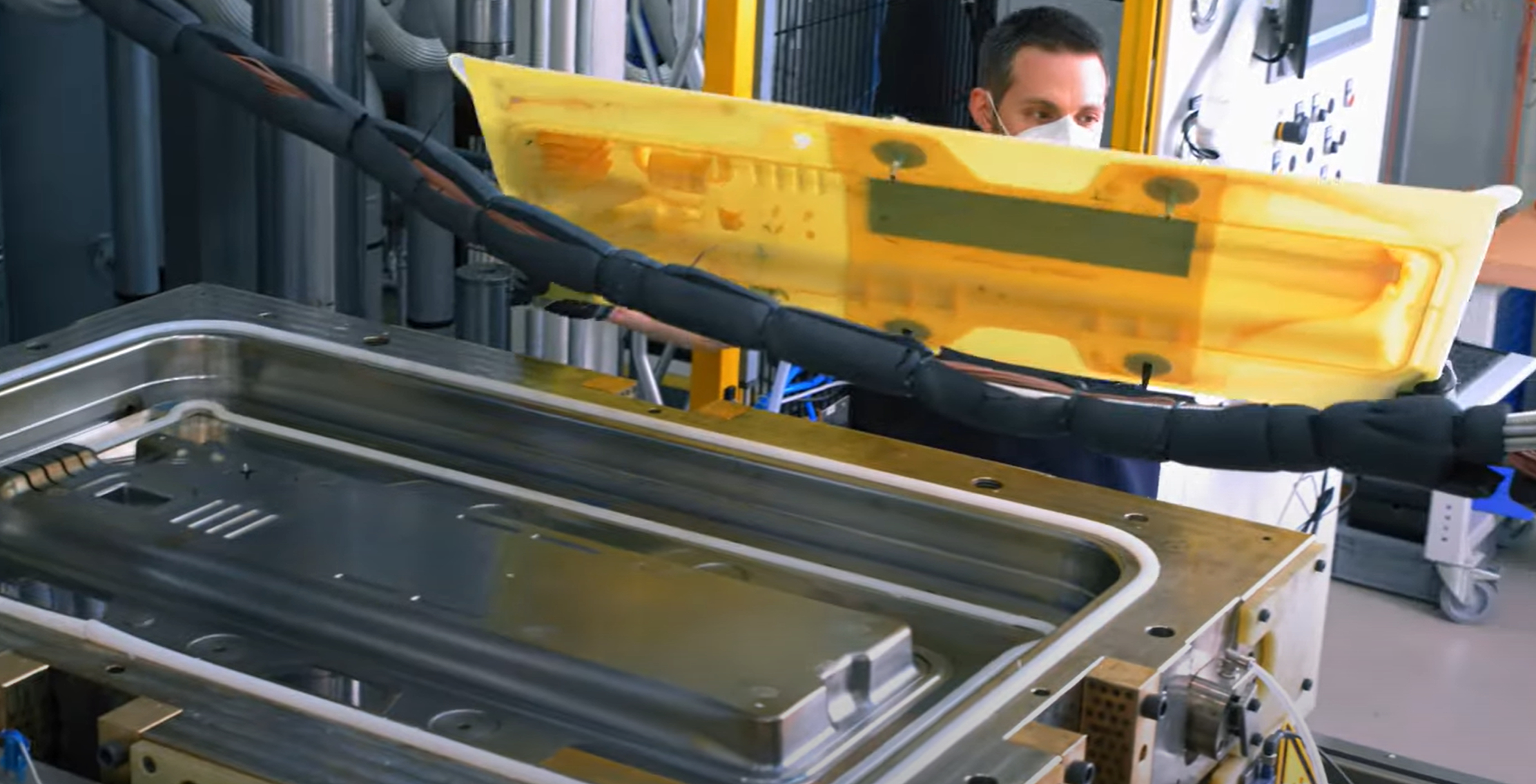
Gebaseerd op het onderdeelontwerp van Faurecia Clean Mobility en het voorvormgereedschap vervaardigd in Augsburg, gebruikte het T-RTM-proces in CosiMo een KraussMaffei (München, Duitsland) 3K (driecomponenten) injectiemachine. Het proces is een afgeleide van een 2K-proces gepatenteerd door Tecnalia (Donostia-San Sebastián, Spanje) dat werd gedemonstreerd door KraussMaffei op de 2016 K-show in Düsseldorf, Duitsland. De 3K-injectiemachine werd gecombineerd met een 4400 kilo zware Wickert (Landau in der Pfalz, Duitsland) hete pers waarin een stalen RTM-tool was geïnstalleerd. De RTM-tool is vervaardigd door Siebenwurst in Dietfurt, Duitsland.
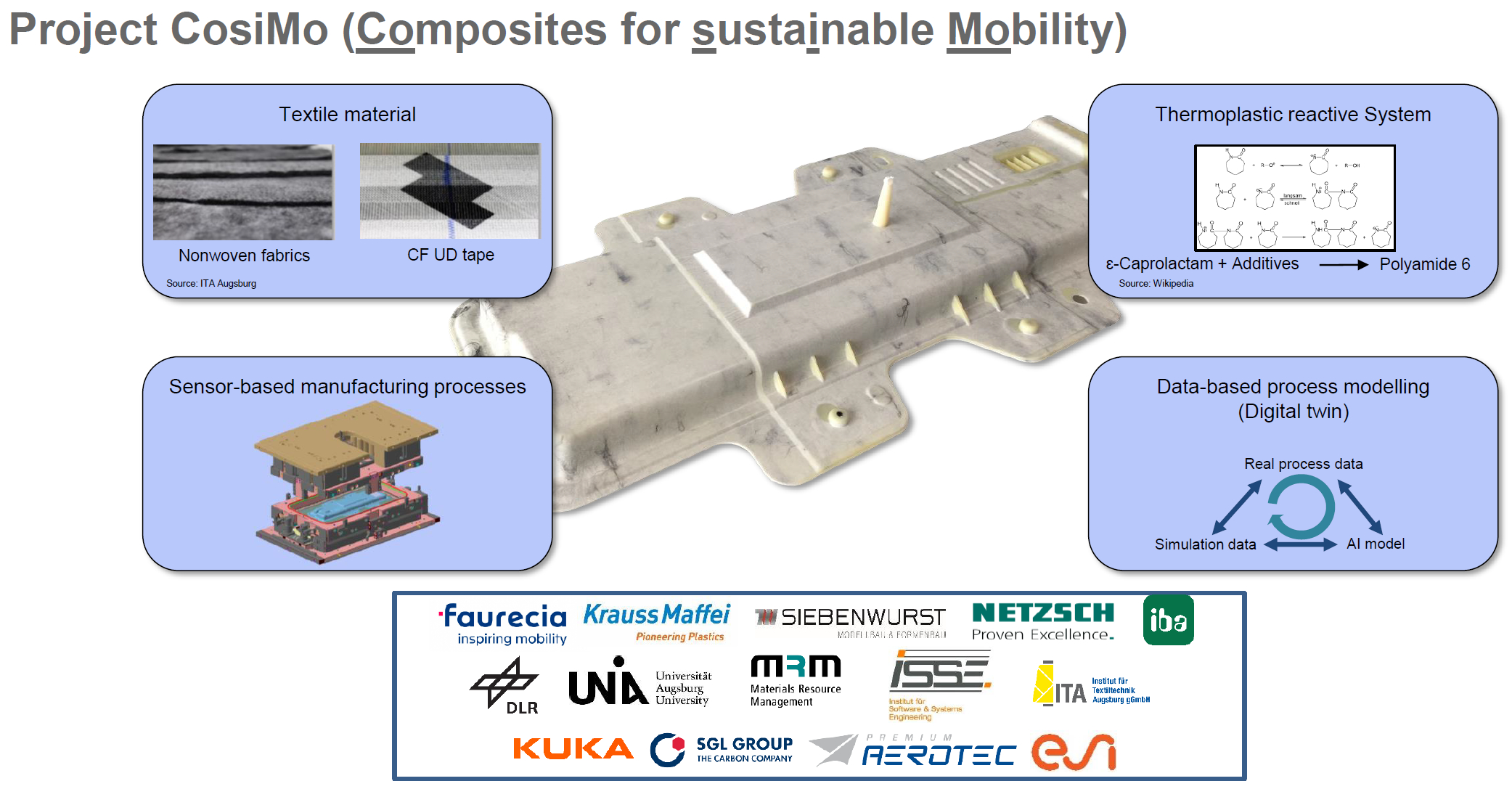
Het belangrijkste doel van het project was om volledige automatisering en sensorgebaseerde procesbesturing te onderzoeken voor een eenstaps T-RTM-proces met behulp van een sensorgestuurde RTM-matrijs en hete pers. Ongeveer 100 demonstratieonderdelen werden in dit project vervaardigd door het Duitse Lucht- en Ruimtevaartcentrum (DLR) Centrum voor Lichtgewicht Productietechnologieën (ZLP, Augsburg). "Deze onderdelen, gemaakt met verschillende versterkingen, waren van hoge kwaliteit en vertoonden een hoge reproduceerbaarheid", zegt CosiMo-productieprojectleider bij DLR ZLP, Jan Faber.
Als projectleider voor het werkpakket “HAP 3 – Intelligent Tooling” verzorgde DLR ZLP ook de belangrijkste interface tussen de basismateriaalkarakteriseringen in de werkpakketten “HAP 1 – Tailored Nonwovens” en “HAP 2 – Reactive Systems” en de “HAP 4 - Gegevensgestuurde procesbeheersing”.
Sensornetwerk
Meer dan 70 sensoren werden geïntegreerd in de stalen RTM-tooling om procesparameters te bewaken tijdens harsinjectie en in-situ polymerisatie. Dit netwerk omvatte een verscheidenheid aan sensoren, waaronder gecombineerde druk-/temperatuursensoren van Kistler (Winterthur, Zwitserland), diëlektrische sensoren van Netzsch (Selb, Duitsland) en ultrasone sensoren ontwikkeld door de Universiteit van Augsburg. Deze laatste zijn gebaseerd op concepten van veelgebruikte commerciële piëzo-elektrische sensoren, maar aangepast voor de hoge temperaturen en in-mold integratie-eisen van de verwerking van thermoplastische composieten. Materiaal-, proces- en machinegegevens werden verzameld, verwerkt en vervolgens gepubliceerd op het machine learning-platform door een centraal data-acquisitiesysteem geleverd door iba AG (Fürth, Duitsland).
Processimulatie en optimalisatie
Het sensornetwerk maakte monitoring van harsstroom en polymerisatie mogelijk, evenals het volgen van onderdeelparameters in de complexe gereedschapsgeometrie. Procesparameters zoals temperatuur en druk werden gebruikt om realtime harsvul- en polymerisatiegedrag te analyseren.
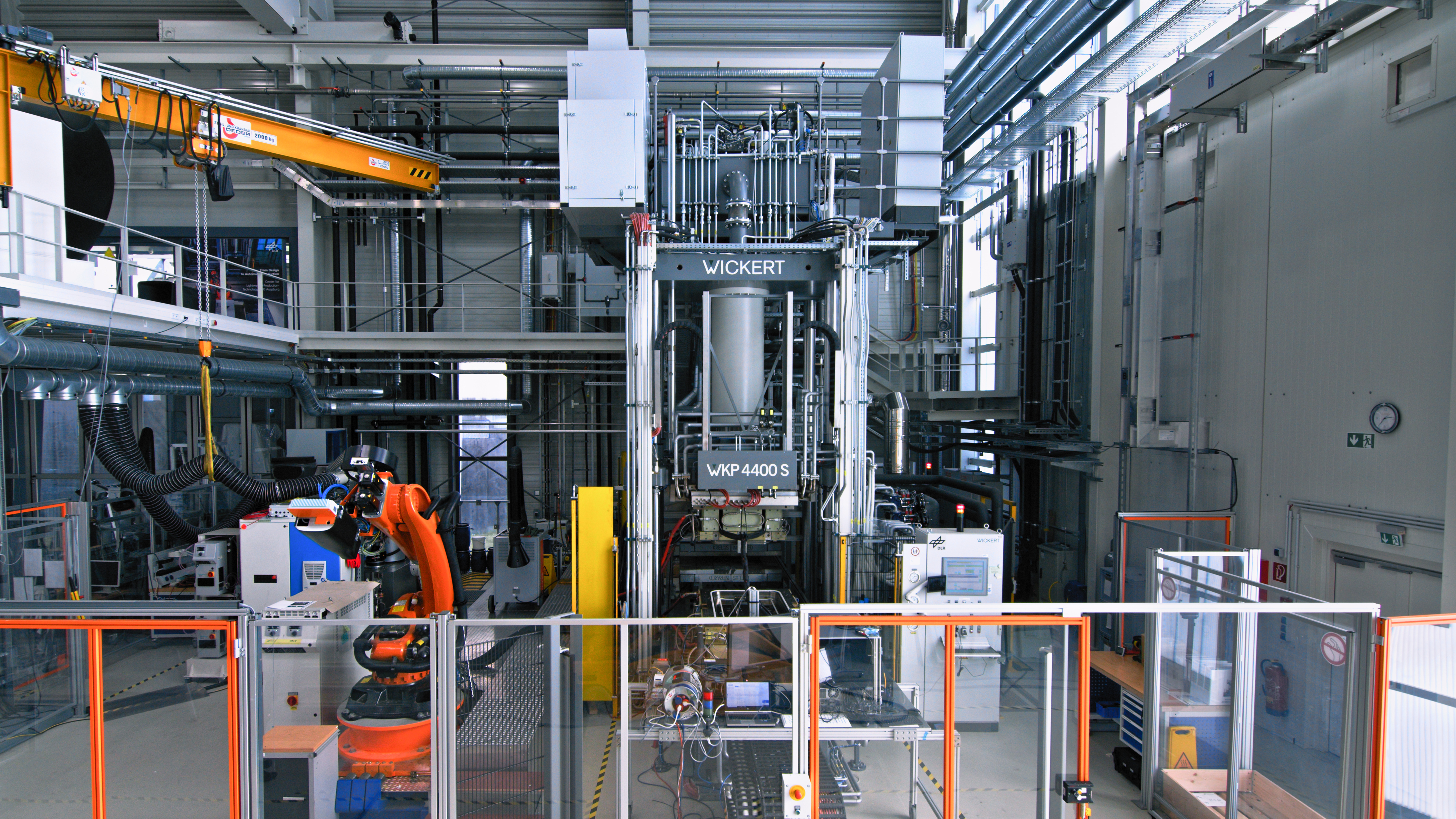
Procesparametergegevens van sensoren werden ook gebruikt om processimulatiemodellen te optimaliseren. Op basis van een eerder gedefinieerde fabricagedemonstrator werden subprocessen van de fabricage van onderdelen (bijv. simulatie van harsvulling) en kenmerken van de gepolymeriseerde component (bijv. simulatie van vervorming) gemodelleerd met ESI PAM-composietsoftware (ESI Group, Rungis, Frankrijk). DLR ZLP vergeleek deze simulatieresultaten met echte procesgegevens om het T-RTM-proces te optimaliseren, als onderdeel van de activiteiten van het HP3-Workpackage.
Het project ontwikkelde vervolgens geautomatiseerde en gesimuleerde datagestuurde procesbesturing op basis van machine learning-methoden. Het Institute for Software &Systems Engineering (ISSE, prof. Reif) binnen de Universiteit van Augsburg genereerde trainingsgegevens voor machine learning en ontwikkelde modellen voor kunstmatige intelligentie (AI) die de polymerisatiestatus voorspellen, evenals de tijd die nodig is voor polymerisatie, en mogelijke problemen tijdens harsinjectie, vul- en polymerisatiesubprocessen. Dit gebeurde in samenwerking met Kuka (Augsburg, Duitsland), een andere belangrijke partner in het project.
Een kinetisch model dat de voortgang van de polymerisatie beschrijft, is ontwikkeld door het Institute of Materials Resource Management (MRM) binnen de Universiteit van Augsburg. Netzsch was ook een belangrijke medewerker en droeg zijn kennis van thermohardende procesmonitoring over naar thermoplastische procesmonitoring om het vermogen van de voorspellende AI-modellen te helpen voorspellen wanneer de PA6-polymerisatie voltooid zou moeten zijn en wat de polymerisatiestatus zou zijn.
Fabricage en testen van onderdelen
Voor de productie van onderdelen werd het stalen gereedschap verwarmd tot 170°C en de reactieve caprolactamharscomponenten werden verwarmd tot 120°C. De preform werd in de mal geplaatst, die vervolgens werd gesloten. Na een korte pauze om de voorvorm op maltemperatuur te laten komen, werd het caprolactammonomeer geïnjecteerd, wat 20-25 seconden duurde. Processimulatie toonde aan dat in-situ polymerisatie 5,7 minuten na injectie nodig was voor een omzetting van 98,5%. Na deze tijd werd de pers geopend en het onderdeel uit de vorm gehaald bij 170°C.
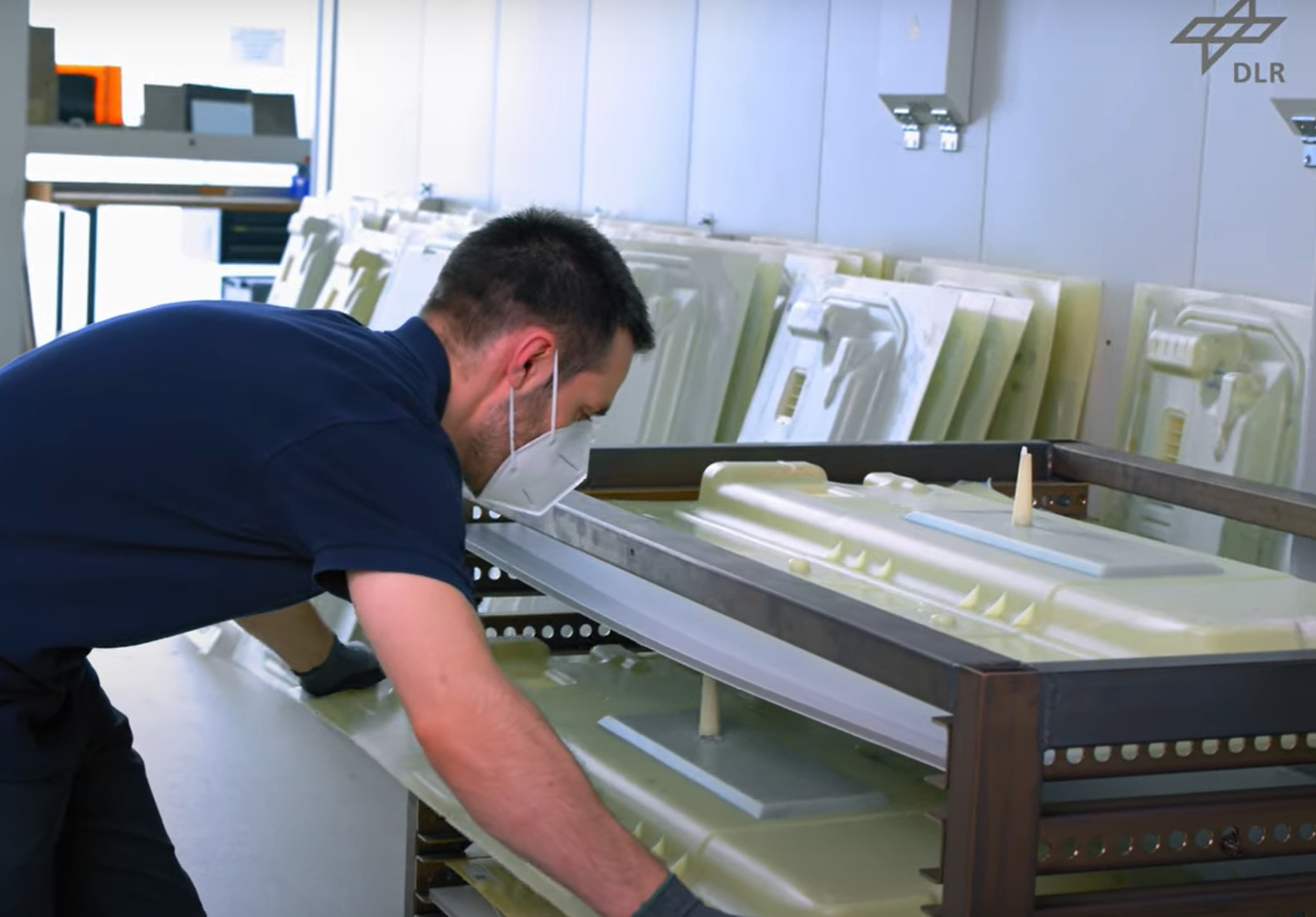
De polymerisatiegraad werd bevestigd via infraroodspectroscopie, reometrische gegevens en DEA-sensoranalyse van polymerisatie. Afgewerkte onderdelen werden geëvalueerd met behulp van niet-destructieve tests, waaronder microscopie, thermografie en luchtgekoppelde echografie. De kwaliteit van het onderdeel werd gecorreleerd met processensorgegevens en vergeleken met vergelijkbare glasvezel/thermoplastische onderdelen op de markt.
Toekomstige ontwikkeling
Voor DLR ZLP is dit project volgens Faber een succes. "We hebben ons deel gecompleteerd en hebben veel kennis ontwikkeld over het gebruik van sensoren om volledig digitale closed-loop controle van composietverwerking te bereiken", zegt hij. “Voor industriële serieproductie zou niemand zoveel sensoren installeren en dat zouden we ook niet verwachten. Maar voor dit onderzoeksonderzoek was dit grote sensornetwerk zeer nauwkeurig en hielp het ons volledig inzicht te krijgen in het proces en het materiaalgedrag. We konden de lokale effecten in het proces zien als reactie op variaties in de dikte van het onderdeel of in de geïntegreerde materialen, zoals de schuimkern.”
Hij merkt op dat dit project veel kennis heeft gegenereerd en ziet in de toekomst potentieel om het toe te passen op langzamere RTM- en infusieprocessen, waar het risico op problemen met de kwaliteit van onderdelen historisch zeer hoog is geweest. Faber zal ook CosiMo-projectontwikkelingen en resultaten presenteren in "Sensor-based process monitoring of in-situ polymerization in T-RTM manufacturing with caprolactam" op woensdag 29 september tijdens het live en virtuele evenement, SAMPE Europe 21-conferentie, in Session 1, Kamer 1 – Automobiel.
DLR ZLP is ook een van de drie belangrijkste partners in het Augsburg AI (artificial intelligence) Production Network — opgericht in januari 2021 — dat ook de Universiteit van Augsburg en het Fraunhofer Institute for Foundry, Composites and Processing Technology (Fraunhofer IGCV) samenbrengt. Zoals uitgelegd door Dr. Markus Sause, directeur van het AI Production Network en ook een CosiMo-projectonderzoeker die ultrasone sensoren ontwikkelt:"We gaan deze blauwdruk van samenwerking die in het CosiMo-project naar voren is gebracht, uitbreiden naar een veel grotere schaal, AI-technologieën voor productie met een sterke focus op composieten. Onze nieuwe faciliteit van 5.000 vierkante meter in Augsburg zal in 2022 worden geopend en volgend jaar worden uitgerust met een verscheidenheid aan machines, zodat bedrijven demonstraties kunnen zien van wat AI kan doen voor echte processen in een productieomgeving.”
Faurecia Clean Mobility zal ondertussen intern de kennis uitbreiden die is opgedaan tijdens het CosiMo-project, dat volledig is afgestemd op de duurzaamheidsstrategie en ecologische transitie van Faurecia. Faurecia dankt ook het Beierse federale ministerie van Economische Zaken, Regionale Ontwikkeling en Energie, die dit onderzoeksproject financieel heeft ondersteund.
Hars
- Batterij
- TPE-verbinding gebruikt voor duurzame 'katoen' wattenstaafjes
- Thermoplastisch biomateriaal 'Fine-Tuned' voor medische toepassingen
- Medische kwaliteit TPE gebruikt voor bekroonde therapiebal
- Aanpassen van ultrasone sensoren voor procesoptimalisatie en controle van composieten
- Thermoplastische tapes blijven potentieel tonen voor composiet aerostructuren
- UBQ Materials heeft ISO-certificeringen toegekend voor van afval afgeleid thermoplast
- Polyscope Polymers wint JEC Innovation Award voor geleiderails van thermoplastisch composiet
- Thermoplastische deur een primeur voor autocomposieten
- Belangrijke overwegingen bij het uitbesteden van een assemblageproces voor het bouwen van dozen
- Dingen om te overwegen voor het assemblageproces voor het bouwen van dozen