Aflevering 29:John McQuilliam, Prodrive Composites
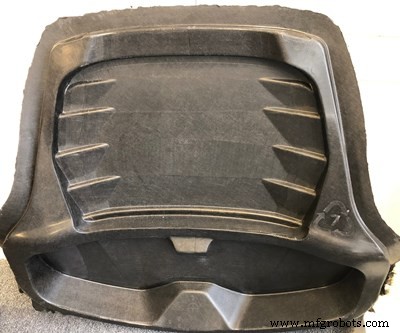
Voorbeeld van een tertiair onderdeel geproduceerd met behulp van het P2T-proces van ProDrive. CW foto | Scott Francis
In deze aflevering van CWTalks interviewt CW senior editor Scott Francis John McQuilliam, hoofdingenieur bij Prodrive Composites (Milton Keynes, VK), ontwerper en fabrikant van geavanceerde lichtgewicht composieten voor een breed scala aan toepassingen, waaronder auto's, motorsport, ruimtevaart, marine, defensie en andere specialistische sectoren.
John is een Formule 1-auto-ontwerper uit het VK die met tal van motorsportbedrijven heeft gewerkt. Hij trad in 2017 in dienst bij Prodrive als hoofdingenieur van hun composietdivisie. John bespreekt het primaire tot tertiaire (P2T) proces van het bedrijf, dat volgens het bedrijf recycling vereenvoudigt en composietmateriaal het potentieel geeft om drie of meer nuttige levensduur te bereiken.
Je kunt de volledige CW Talks beluisteren interview hierboven of bezoek:
- CW Talks:iTunes
- CW Talks:Google Play
Fragment uit de aflevering
CW: Hallo, John, en welkom bij CW Talks, de composieten-podcast. Ik geloof dat het in maart was, ik bezocht Prodrive Composites en kreeg een klein beetje van je P2T-proces te zien, wat staat voor primair tot tertiair.
JM: Dat is juist. De eerste fase is de fabricage van het primaire onderdeel, en dat is wat we momenteel doen voor het grootste deel van het werk. Dit zijn dus onderdelen die om welke reden dan ook nieuwe vezels, een speciale hars of een bepaald type thermohardende hars nodig hebben. Dus het zijn wat ik traditionele composietonderdelen zou noemen ... het zijn onderdelen waarvan we het ontwerp of de fabricage niet echt zouden veranderen, maar we zouden ze zeker veranderen om ze gemakkelijker recyclebaar te maken.
CW: Oke. En dat zijn typisch de meer hoogwaardige onderdelen?
JM: Ja. Dus ze zouden thermohardend zijn ... Wat we zouden doen, is gewoon het ontwerp ervan veranderen om het afvalmateriaal van het maken van de onderdelen en uiteindelijk het deel van het einde van zijn levensduur recyclebaar te maken, zodat we de koolstofvezels erin kunnen hergebruiken binnen die onderdelen. Dus de thermoplast komt binnen in de tweede fase ... de beginfase kan thermohardend of thermoplastisch zijn, maar het belangrijkste is dat het ons in staat stelt de vezels terug te winnen. Dus om de vezels van de primaire onderdelen terug te winnen, zoals eerder vermeld, veranderen we de ontwerpmaterialen in iets dat gemakkelijker is om de vezels van terug te winnen, dus waar we het echt over hebben is een verhoogd gebruik van niet-knijpstoffen, meer unidirectionele materialen, dingen waarbij het productieafval en de component wanneer ze door het vezelterugwinningsproces gaan, een betere opbrengst geven aan langere vezels van hoge kwaliteit.
CW: Kun je een klein beetje beschrijven van het terugwinningsproces dat plaatsvindt voor dat primaire onderdeel en wat dan het resulterende secundaire onderdeel kenmerkt?
JM: Ja. Het recycling- of terugwinningsproces voor de primaire onderdelen is dus een proces van het verbrandingstype. Dus het afval prepreg - de restanten prepreg - of de afgedankte delen gaan in een oven en alle hars wordt verbrand en laat de koolstofvezels achter. En die koolstofvezels worden door een reeks processen omgezet in een non-woven mat van consistente dikte en willekeurige oriëntatie - zodat het uiteindelijk in staat is om een quasi-isotopische plaque te maken.
CW: Is dit het proces dat ELG [ELG Carbon Fibre] voor u doet? Zijn ze bezig met de pyrolyse?
JM: Ja, ELG doet dat deel ervan. Dus sturen we ze onze afvalresten en enkele onderdelen en dan maken ze er weer een van de voorlopers van, een van de onderdelen die we gebruiken om onze secundaire onderdelen te maken.
CW: Kun je me iets vertellen over die secundaire delen en wat ze kenmerkt?
JM: Dus, de secundaire onderdelen, de versterking is voornamelijk gemaakt van de teruggewonnen koolstofvezels met een discreet gebruik van nieuwe vezels indien nodig in bepaalde gebieden. Maar het grootste deel van de versterking bestaat uit teruggewonnen vezels. En dan introduceren we een reactieve thermoplast. Dit is dus een vloeibare hars waarmee we, laten we zeggen, de versterkingen doordrenken. Dan is er een uithardingsproces en we krijgen een voltooid onderdeel en het proces wordt uitgevoerd bij relatief lage temperaturen, atmosferische druk en we krijgen op die manier een goed onderdeel.
CW: Een deel van wat P2T mogelijk maakt, is dit harssysteem dat u hebt beschreven als een "reactieve thermische kunststofhars". Kun je iets meer uitleggen voor onze luisteraars wat je daarmee bedoelt?
JM: Dus reactieve thermoplast lijkt in sommige opzichten erg op een thermohardende hars. Dus we mixen het meteen voordat we het onderdeel maken. En er gaan twee of drie vloeibare componenten naar het mengsel. Elk daarvan is een vloeistof. En wanneer ze worden gecombineerd met de tijd en een beetje temperatuur, polymeriseren ze in feite tot een echte thermoplast. En het zijn de thermoplastische eigenschappen die latere recycling mogelijk maken. En het voordeel van het feit dat het een reactieve thermoplast is in plaats van een traditionele thermoplast, is het feit dat we effectief een thermoplast creëren terwijl we de versterkende vezels omringen, is dat het een zeer lage viscositeit heeft, zodat het kan worden gevormd in normale traditionele , moeten we zeggen, thermohardende processen. Het heeft niet de hoge temperatuur en de hoge druk nodig die je krijgt door ofwel een gesmolten thermoplast in een vezelvoorvorm te injecteren of een thermoplastische prepreg te nemen waarbij het thermoplast en de vezels al zijn gecombineerd en ze vervolgens opnieuw te monteren bij hoge temperatuur en druk , typisch in metalen vormen. We vermijden dus de complexiteit en de kosten van de vormgereedschappen die nodig zijn om thermoplasten boven het smeltpunt te verwerken en vermijden de moeilijkheden als gevolg van de hoge viscositeit van gesmolten thermoplast met vervorming en beweging van de versterking in de vormholte.
CW: En ik vermoed dat dat zich vertaalt in kostenbesparingen, tijdwinst en in feite nogal wat betekent voor de productie...
JM: Je hebt het, ja. De productiemethode is dus vergelijkbaar met wat we doen in de traditionele thermohardende industrie, maar de gereedschapskosten zijn veel lager dan nodig is voor het verwerken van een traditionele thermoplast. En dat is een groot voordeel voor de meeste van onze klanten. U wilt niet de eerste investering doen in thermoplastische vormgereedschappen - of vormgereedschappen alleen voor thermoplasten.
CW: Beschouwt u dit dus als een mogelijkheid voor meer grootschalige productie?
JM: We zijn zeker van mening dat het een motor is voor een hogere productie. Cyclustijden kunnen korter zijn dan hun traditionele thermoharding, omdat er geen verhoging naar een verwerkingstemperatuur, een wachttijd en vervolgens weer afkoelen nodig is voordat u de mal kunt omdraaien. We zien dus snelheidsvoordelen door dit proces te gebruiken in vergelijking met onze traditionele oven- of autoclaaf-uitgeharde componenten.
CW: En natuurlijk is een van de opwindende dingen dat je vanaf daar dit secundaire onderdeel opnieuw kunt recyclen. Dus wat kenmerkt dit tertiaire deel in de levenscyclus van dit materiaal?
JM: Dus ik zou zeggen dat het secundaire deel, dat een echte thermoplast is, kan worden hervormd in andere vormen en meestal in kleine stukjes wordt gesneden en vervolgens in de holte tussen de verwarmingsvorm wordt geplaatst en in een nieuwe vorm wordt geperst. Er zal dus een mogelijkheid zijn om alle overtollige secundaire onderdelen, al het productieafval van de secundaire onderdelen, te nemen en ze om te vormen tot een andere vezelversterkte kunststofcomponent of een vezelversterkte polymeercomponent.
CW: En vanaf daar zijn deze tertiaire delen niet per se het einde van de weg voor dat materiaal, zelfs dan...
JM: Dat klopt... Dus we denken dat deze tertiaire delen, omdat ze thermoplastisch zijn, bijna oneindig vaak kunnen worden hervormd. Het proces om ze te versnijden in vormpaletten, laten we zeggen vormstukken, heeft een uitputtingssnelheid op de vezel... dus sommige mechanische eigenschappen zouden afnemen, maar andere mechanische eigenschappen zoals de stijfheid, de thermische uitzettingssnelheid en de vervorming temperatuur zou goed behouden blijven. U krijgt dus nog steeds een vezelversterkte component van hoge kwaliteit - niet met de oorspronkelijke sterkte van een continue vezelcomponent of zelfs een relatief lange vezelcomponent - maar er zijn zeker nog steeds de voordelen op het gebied van stijfheid, thermische uitzetting en de vervormingstemperatuur die het zeer de moeite waard maken de tertiaire delen keer op keer opnieuw verwerken.
vezel
- Top 10 ontwikkelingen op het gebied van composietproductietechnologie
- Toen en nu:een korte geschiedenis van composietmaterialen
- Waar u op moet letten bij fabrikanten van composieten
- Composite fabricage:de fabricage van composietmaterialen
- Thermoplastische composieten bij Oribi Composites:CW Trending, aflevering 4
- AMRC en Prodrive werken samen om de productie van recyclebare composietcomponenten te bevorderen
- Hoogwaardige composieten in Israël
- Aflevering 17:Gino Francato, Sabic; Arno van Mourik, In de lucht; John OConnor, Siemens
- Aflevering 26:Achim Fischereder, Hexcel
- Nationale Composites Week:Duurzaamheid
- Nèos International vestigt nieuw hoofdkantoor, composietenfaciliteit in het VK