Lasinspectie voor veiligheidskritische constructies
Er staat veel op het spel voor fabrikanten die auto-onderdelen produceren. Bestuurders en passagiers van auto's vertrouwen op laskwaliteit om stand te houden onder de omstandigheden waarvoor het is ontworpen. Eén onopgemerkte fout tijdens het fabricageproces kan een bedrijf kwetsbaar of erger maken, vooral wanneer het onderdeel in kwestie "veiligheidskritisch" is voor een assemblage.
Autostoelen staan bijvoorbeeld in direct contact met passagiers; daarom worden de stoellassen als veiligheidskritisch beschouwd. Deze classificatie dicteert een bepaald protocol voorafgaand aan de productie. Hoewel OEM-vereisten variëren, zijn ze meestal consistent met de praktijk in de industrie en worden ze geïmplementeerd met kleine verschillen, afhankelijk van het onderdeel, de installatie en de industriële apparatuur die wordt gebruikt. Dit zijn de basiselementen van een protocol:
Preproductieprotocol
- Parameters instellen - Vaststellen van lasparameters en verifiëren van hun aanvaardbaarheid. Dit kan worden gedaan door lassecties te snijden en te etsen om laspenetratie te verifiëren (15-20%).
- Vrijgaveproces - Een vast proces om de productie vrij te geven of goed te keuren zodra het bovenstaande is geverifieerd.
- Wijzigingsbeheer - Wijzigingen van essentiële variabelen voorbij bepaalde limieten vereisen hervalidatie via snij- en etstesten.
- Kwaliteitsborging - Willekeurige onderdelen kunnen uit de productie worden geselecteerd om te worden gesneden en geëtst met een door de OEM voorgeschreven frequentie.
Robotlassen heeft de kwaliteit van de onderdelen enorm verbeterd door lassen altijd op dezelfde locatie te plaatsen met geprogrammeerde lasparameters. Het naleven van de bovenstaande procedures helpt bij het produceren van een gelast kwaliteitsproduct. OEM's in de auto-industrie hebben zich gericht op veiligheidskritische lassen en dit heeft geresulteerd in een herziening van enkele belangrijke elementen:
Productieprotocol
- Beveiliging - Controleer of gekwalificeerd personeel toegang heeft tot apparatuur en of er geen wijzigingen worden aangebracht die de kwaliteit negatief beïnvloeden.
- Boogbewaking - Implementatie van een boogbewakingssysteem kan helpen om te verifiëren of het proces onder controle is en kan de frequentie van destructieve tests verminderen. Boogbewaking controleert of de lasparameters voldoen aan vastgestelde limieten. Lassen buiten de limieten worden gemarkeerd voor verdere inspectie.
- Traceerbaarheid - Houd wijzigingen en lasresultaten bij en behoud de mogelijkheid om de datum, tijd en het serienummer te loggen waar onderdeelwijzigingen hebben plaatsgevonden.
Bij Yaskawa Motoman nemen we de tijd om meer te weten te komen over de productie- en traceerbaarheidseisen van onze klanten. In de loop der jaren hebben we verschillende software- en I/O-verbeteringen voor onze controllers ontwikkeld waarmee fabrikanten betrouwbare, traceerbare lasinspecties kunnen uitvoeren.
Beveiligingsfuncties
Wachtwoordfunctie
Het standaard beveiligingssysteem met een wereldwijd wachtwoord op verschillende niveaus is handig voor meerdere technici om meerdere robotcellen binnen een fabriek te onderhouden. Wereldwijde wachtwoorden lopen echter het risico dat ze worden gedeeld door fabriekspersoneel, zonder controle over wat er wordt gewijzigd en door wie.
De wachtwoordfunctie van de DX-controller van Yaskawa creëert een database van gebruikers met wachtwoorden en veiligheidsniveaus. Gebruikers moeten inloggen om de robot te bedienen; de logfunctie registreert de gebruikersnaam en de aangebrachte wijzigingen.
Er is software aan de DX200-controller toegevoegd om externe wachtwoordbesturing door PLC mogelijk te maken. Besturingstechnici kunnen logica implementeren om op fabriek/cel gebaseerde besturingselementen te gebruiken om gebruikers en aanmeldingen op afstand te beheren op basis van hun interne werknemersbadges of beveiligingssysteem.
Beveiligingsniveaus
- Bedrijfsniveau - Op dit basisniveau kan iedereen standaard een programma doorlopen of doorlopen, maar geen punten of lasinstellingen wijzigen.
- Niveau bewerken - Hiermee kan de gebruiker programma's maken en lasinstellingen wijzigen, maar heeft hij geen toegang tot parameters of gegevens van een hoger niveau.
- Beheermodus - Biedt volledige toegang tot parameters en onderhoudsfuncties.
- Veiligheidsniveau - Geeft toegang tot het instellen en beheren van de besturing, betrouwbare softwarelimieten en veiligheidslogica geïmplementeerd in DX-controllers (Functional Safety Unit – FSU).
Wat deze niveaus gebruikers toestaan te doen en toegang wordt bepaald door het systeem. Het niveau waarop het management de toegang regelt, verschilt per fabriekslocatie.
Logfunctie
Veel nieuwere robotcontrollers worden geleverd met een standaard logfunctie die wijzigingen bijhoudt die in het systeem zijn aangebracht op datum en tijd. Zo kan een dagdienstoperator zien of iemand van de nachtdienst een wijziging heeft aangebracht. De robot houdt een lokaal bestand bij van de laatste reeks wijzigingen, zodat een routinematige opslag van gegevens een historisch logboek van gebruikersactiviteit kan bijhouden. De robot kan ook wachtwoordbeveiliging gebruiken, waarbij gebruikers moeten inloggen om wijzigingen aan te brengen. Bij wijzigingen worden ook gebruikersnamen genoteerd.
Veiligheid opnieuw leren bewerkingsfunctie
Operation Level staat gebruikers niet toe om programmapunten te wijzigen, maar sommige bedrijven staan operators of technici van het eerste niveau toe om kleine wijzigingen aan te brengen voor onderdeelvariaties. Met Safety Re-Teach kunnen gebruikers op operationeel niveau geprogrammeerde punten wijzigen binnen een 3D-bereik dat wordt gedefinieerd door de beheermodus. Dit wordt normaal gesproken ingesteld op enkele millimeters en een manager kan de mate van hoekverandering voor de toorts of externe as beperken. Gebruikers op bedieningsniveau kunnen lasparameters niet wijzigen, dus essentiële lasvariabelen worden niet gewijzigd. Dit voorkomt herhaalde destructieve tests. Safety Re-Teach kan via een parameter worden ingeschakeld in de beheermodus op elke DX-controller.
Boogbewaking
Als robotleverancier die lassystemen integreert en voortbouwt op een joint venture met een lasbedrijf, heeft Yaskawa Motoman uitgebreide ervaring met boogbewaking. We hebben onze lasinterfaces ontworpen om boogbewaking te ondersteunen die fabrikanten van stroombronnen mogelijk hebben geïntegreerd.
De geïntegreerde functies van Miller Insight Centerpoint™ en Lincoln Electric Production Monitoring™ zijn toegankelijk via de robot-teach-hanger. WeldCube, van Fronius, communiceert rechtstreeks met de stroombron(nen). Yaskawa en Fronius werken eraan om het monitorresultaat te laten rapporteren in de statusbits van de lasser.
De uitdaging om te voldoen aan de "veiligheidskritieke" mandaten houdt ook in dat lasresultaten van stroombronboogbewaking duidelijk moeten worden gepresenteerd in een bruikbaar formaat. Het beste formaat is om monitorresultaten te markeren op een onderdeeldiagram op een HMI van een robotcel. Op die manier kunnen operators van lasstations gemakkelijk onregelmatigheden opsporen en snel reageren. De operators moeten de door het systeem gemarkeerde lassen visueel inspecteren, met monitorresultaten die buiten het bereik vallen, om te beoordelen of de lassen conform of niet-conform zijn.
Hoewel de robotcontroller de status van de boogmonitor lokaal op een HMI kan rapporteren, bieden de fabrikanten van stroombronnen ook software aan die is ontworpen om de resultaten van de boogmonitor op afstand te rapporteren, via een pc of cloudgebaseerde software.
Miller Insight Centerpoint
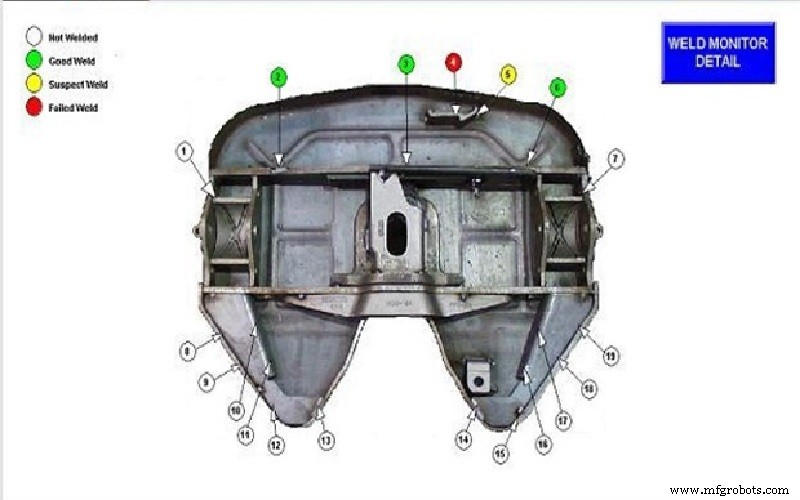
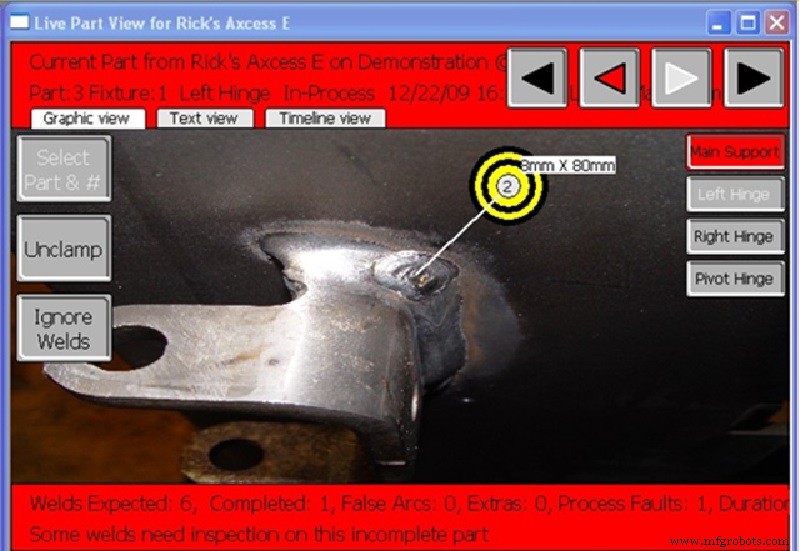
Traceerbaarheid
OEM's in de auto-industrie vragen hun leveranciers niet alleen om goede onderdelen te maken, ze vragen hen ook om kwaliteitssystemen te implementeren om "traceerbaarheid" te bieden die de lasresultaten van een onderdeel aan het serienummer koppelt. Het doel is om te kunnen herleiden tot een punt in de productie waarvan bekend was dat onderdelen conform waren, als een niet-conform onderdeel wordt gedetecteerd.
Om fabrikanten te helpen traceerbaarheid te bereiken, moeten de boogbewakingsgegevens van de lasstroombron en robotcontroller, plus alle onderdeelspecifieke gegevens die op afstand moeten worden geopend en uiteindelijk in de PLC moeten worden gelogd, worden vastgelegd en gekoppeld aan het serienummer van het onderdeel. Hoe deze mengelmoes van gegevens kan worden geharmoniseerd – en de moeilijkheid daarbij – hangt af van wat een fabrikant out-of-the-box kan integreren, zonder de interne beveiligingsprotocollen in gevaar te brengen.
Tekenreeksvariabelen
Een truc is om een functie voor het maken van stringvariabelen van de robotcontroller te gebruiken om unieke identifiers te creëren als traceermechanisme. Er wordt een mix van variabelen gebruikt voor het opslaan van getallen of zelfs posities, en deze variabelen verschillen op basis van formaat en aantal cijfers. Tekenreeksvariabelen kunnen een combinatie zijn van tekens of getallen van maximaal 32 tekens. Deze kunnen worden opgeroepen om een bericht op de hanger weer te geven of voor ander gebruik.
In het geval van autoproductie hebben we deze gebruikt om serienummerinformatie te bevatten voor het specifieke onderdeel dat wordt geproduceerd. Besturingstechnici kunnen ethernetcommunicatie gebruiken om de waarden van een PLC of barcodelezer te "lezen" en we kunnen ze doorgeven aan andere apparaten.
Gelijktijdige I/O
Yaskawa Motoman gebruikt Concurrent I/O (CIO) om programmeerbare logische besturing uit te voeren en gegevens tussen de robot en de stroombron te communiceren. Terwijl het wordt gebruikt voor lasinstellingen, kan het ook worden gebruikt om boogbewakingsresultaten door te geven tussen de stroombron en de robot. Voor traceerbaarheid hebben we het gebruikt om de lasresultaten voor elke laslocatie samen te voegen en samen met het serienummer van het onderdeel naar de fabrieks-PLC te sturen voor een onderdeelrecord. We nemen ook het serienummer van het onderdeel en sturen het naar een stempelmachine die het serienummer graveert op onderdelen die de lasmonitor passeren.
Onlangs hebben we een systeem geleverd dat lasinspectiegegevens van de Lincoln Electric Production Monitor haalt en aan de operator presenteert in een grafische weergave van het onderdeel. Het markeert, in groen of rood, de monitorresultaten op elke laslocatie - op basis van binnen of buiten de limieten. CheckPoint™ monitoring (een externe software) is ontworpen om data op te slaan in de Cloud. De CIO gaf onmiddellijke toegang tot de resultaten van de productiemonitor, zodat deze aan de operator konden worden gepresenteerd terwijl het onderdeel werd geproduceerd.
Implementatie
Bij het omgaan met lasbewakingsgegevens moet rekening worden gehouden met productiecontrole, samen met de historische logging- en traceerbaarheidsvereisten. De gegevens die gaandeweg worden vastgelegd, worden in de hele organisatie op verschillende manieren gebruikt en er moet bij elke stap rekening worden gehouden met deze behoeften voor elke functie.
Terwijl het gebruik van lasbewakingsgegevens het voor operators op de vloer eenvoudig zou moeten maken om de kwaliteit van onderdelen te verifiëren, kunnen toezichthoudende medewerkers historische gegevens gebruiken om kwaliteitsplannen te beheren en problemen op te lossen. Beveiligingsfuncties maken het bijna onmogelijk om af te wijken van gevestigde protocollen en parameters, en boogbewaking levert real-time, grafische indicaties van lassen die verdere inspectie vereisen.
Met de PLC als eindbestemming worden onderdeelspecifieke lasgegevens gelogd, opgeslagen en traceerbaar. Het kan een aanzienlijke hoeveelheid werk vooraf vergen om tot volledige gegevensharmonisatie te komen; de resultaten zijn echter zelfverzekerde klanten en verbeterde kwaliteit die ook kunnen helpen de toekomst van uw bedrijf veilig te stellen.
Industriële robot
- Kritische temperaturen voor supergeleiders
- Waarom uitmuntende betrouwbaarheid essentieel is voor veiligheid
- NASA's 10 codeerregels voor het schrijven van veiligheidskritieke programma's
- Veiligheidstips voor CNC-machines
- Ontwikkelen van een nieuw tijdperk voor slimmere voedselveiligheid
- Een case voor het upgraden van verouderde vrachtwagens
- Strategieën voor een goede lasvoorbereiding
- 5 veiligheidstips voor het voorbereiden van zwaar materieel
- Inspecties zorgen voor veiligheid in huuruitrusting
- Veiligheidstips voor het lassen van brandstoftanks
- Lasinspectie begrijpen